Massivt bord og bænk
Specialdesignet spisestuesæt i valnød med rå kanter, LED-belysning, glasindsatser og metalben.
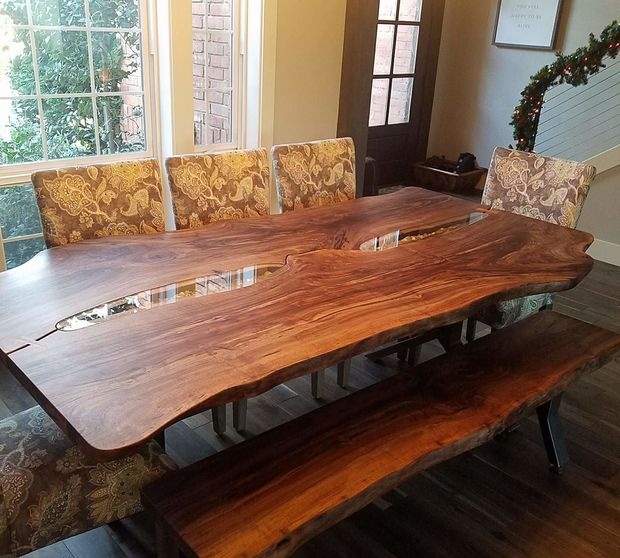
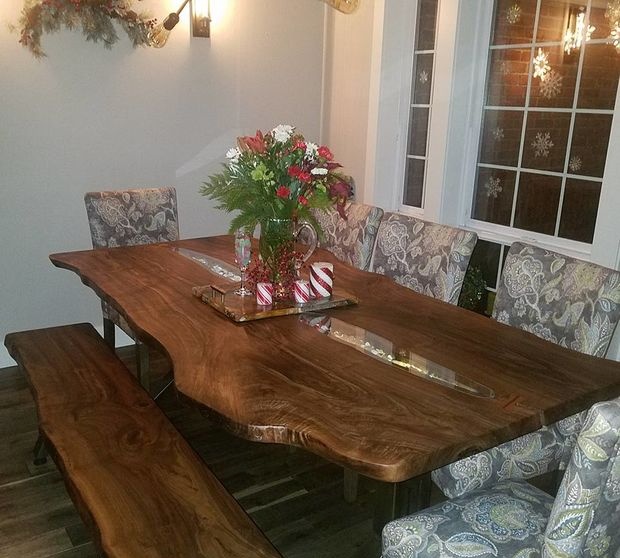
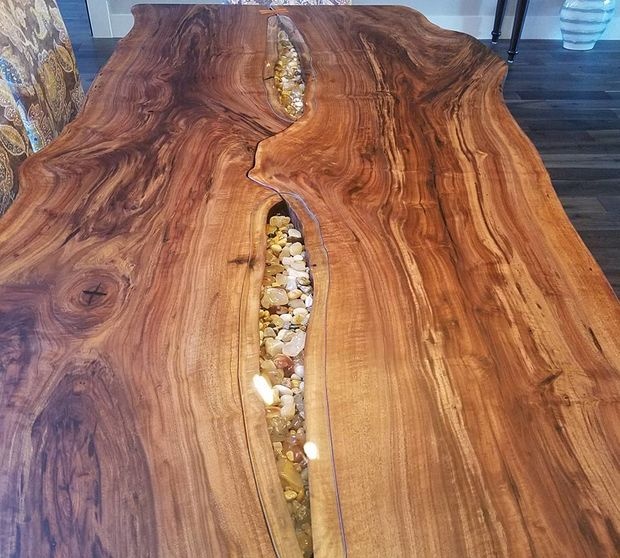


Det var meget sjovt at arbejde på bordet. Min kundes ordre var speciel (og interessant). Og som et incitament - budgettet. Hendes anmodning omfattede følgende punkter:
Jeg forsøgte at dokumentere hvert trin i processen, men deadlines var ret stramme, og nogle gange havde jeg ikke mulighed for at tage et billede. Beklager de manglende billeder; Jeg vil prøve at beskrive disse trin mere detaljeret...
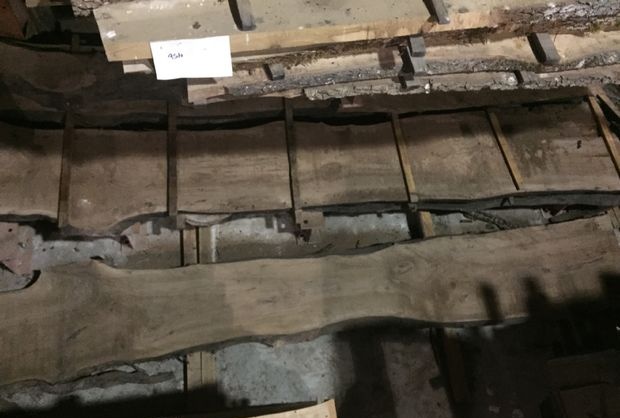
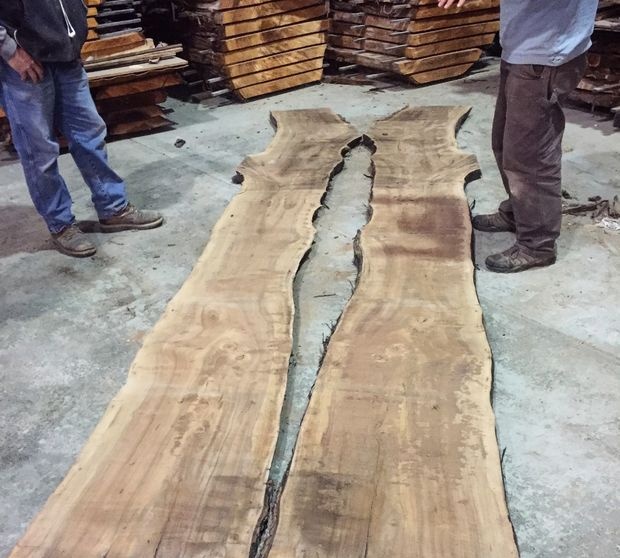
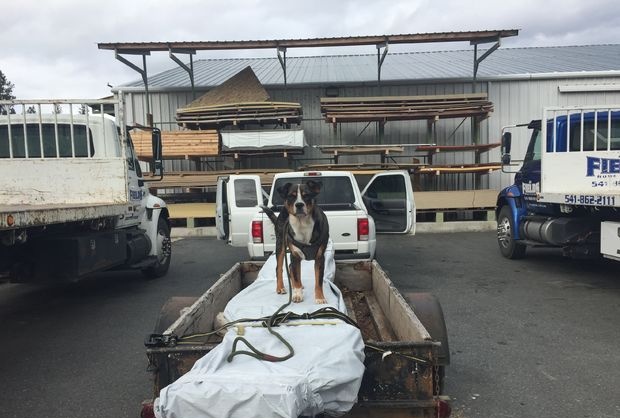
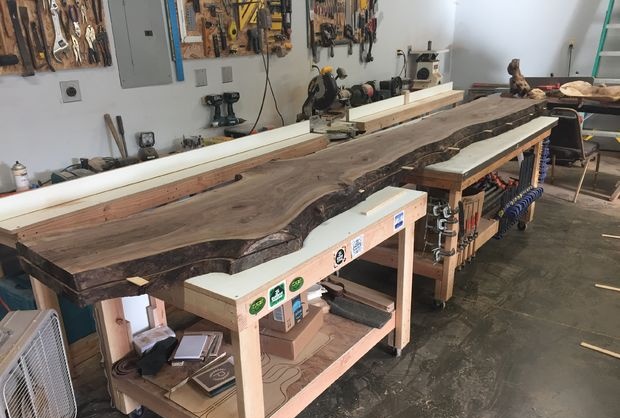
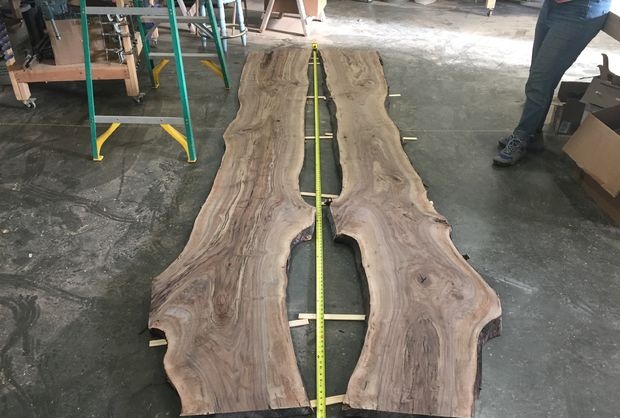
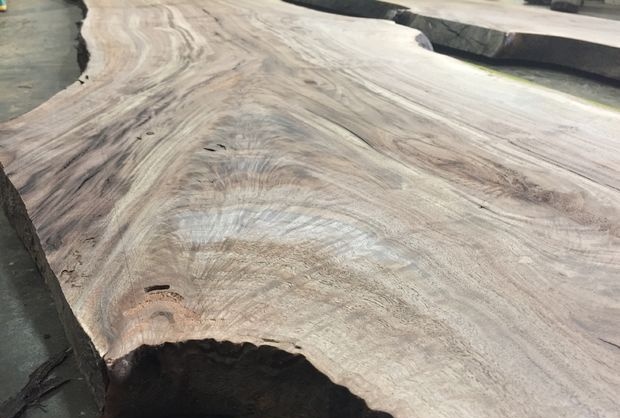
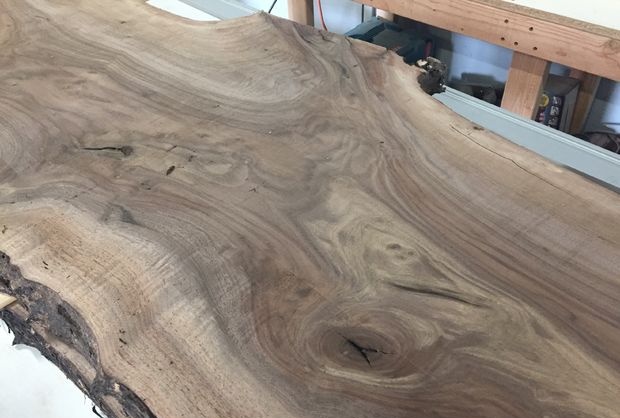
Jeg anser ikke denne fase for at være den vigtigste, men den kan vare ret lang tid.Meget tid, energi og benzin blev brugt på at besøge forskellige savværker og træværfter på jagt efter passende materiale. Dette virkede som noget af en bedrift i betragtning af breddekravene. Jeg skulle finde to brædder med rå kanter, og ved at placere dem side om side skulle den samlede bredde være de nødvendige 100 cm. Deres form skulle skabe hulrum for at kunne rumme kundens samling af agater. Brædderne skal have karakteristiske, udtalte mønstre. Der var også standardkrav: pladerne blev tørret i en ovn eller i et par år i luften, de havde et behageligt udseende, var flade uden unødvendige vridninger, vridninger eller snit (alt, der ville kræve at fjerne et lag af tykkelse) . Og prisen skal selvfølgelig være rimelig.
Søgningen begynder normalt med elektroniske rubrikannoncer i afsnittet "byggematerialer". Ofte tilbyder lokale håndværkere overskydende brædder til salg til rimelige priser. Butikker kan også sende annoncer i et forsøg på at tiltrække flere kunder. Jeg fandt et par anstændige muligheder i nærheden, men intet der passede til regningen. Bagefter besøgte jeg nogle lokale skovhuggere, der savede træstammer til planker. Disse fyre har ofte deres egne savværker og sælger brættet til en god pris, fordi de får træstammerne billigt eller gratis, og kvaliteten er ikke altid den højeste. Men denne mulighed virkede heller ikke, så jeg måtte videre til butikker og varehuse. Selvfølgelig er der allerede et valg her, men til en meget høj pris.
Jeg fandt endelig, hvad jeg havde brug for i en lokal butik. Ikke ligefrem i butikken. Det viste sig, at dens ejer har sit eget savværk og et lager fyldt med brædder med ukantede kanter.Han havde flere stakke nødder at vælge imellem. Her fandt jeg det jeg ledte efter. Brædderne havde den perfekte bredde, skåret af samme træstamme (symmetrien blev bibeholdt), tørret under de rigtige forhold i 3 år, pæne og flade, og prisen var forholdsvis billig. De kom med en bonus. Da de blev bearbejdet med et bredt plan, behøvede jeg ikke at slibe den ujævnt afskårne overflade. Jeg har ikke et 60 cm bredt fly...
Under søgningen sendte jeg billeder til klienten for at få hendes godkendelse. Vi besluttede os begge for disse to. Endelig kunne næste fase af projektet begynde!
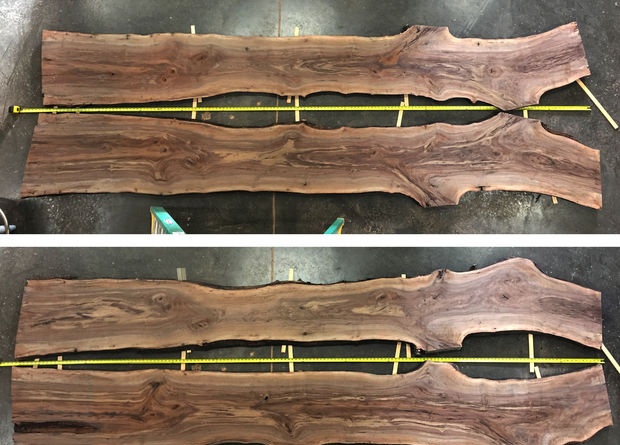
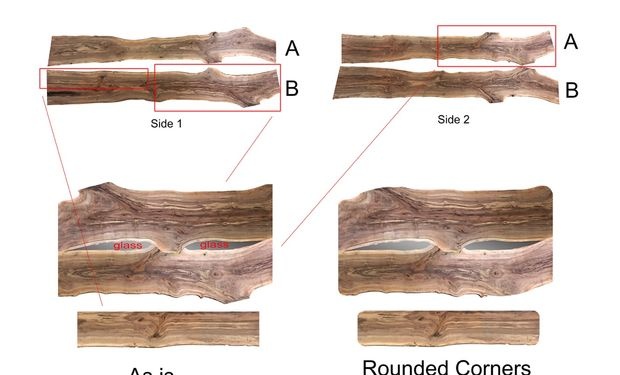
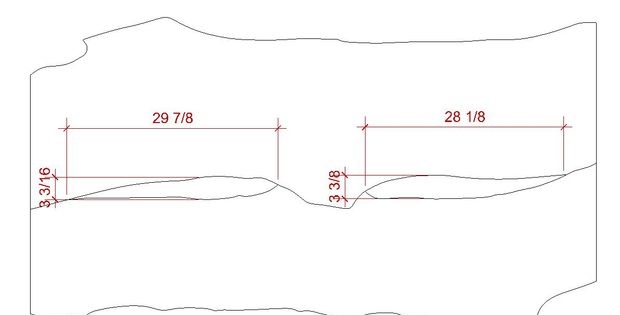
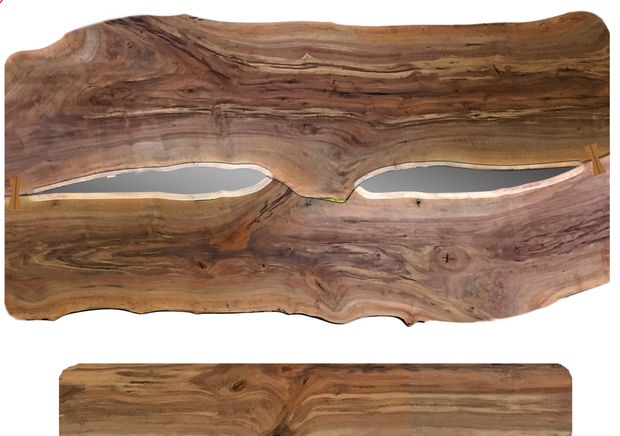
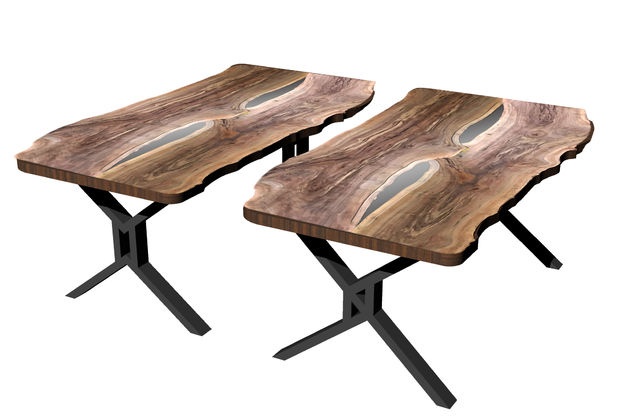
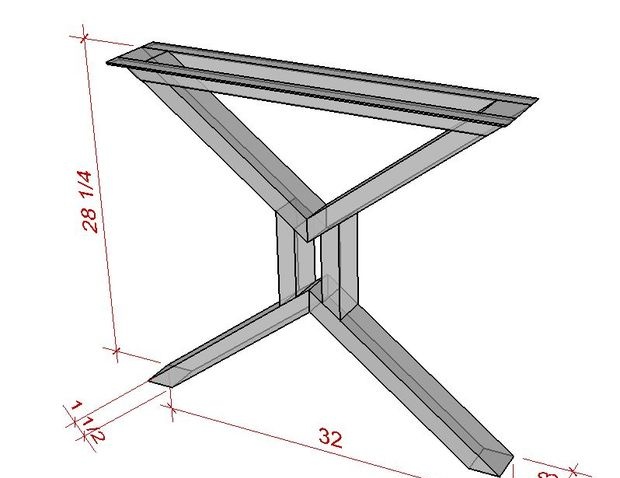
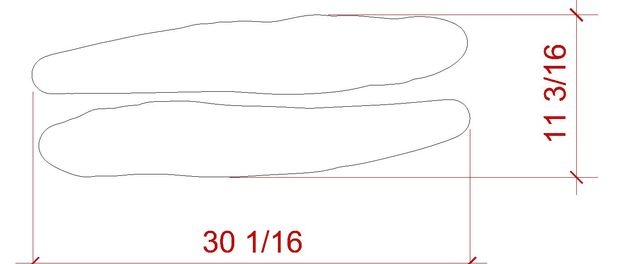
Før jeg henter et værktøj, starter næsten alle projekter, jeg laver, med et computerstøttet design (CAD). Dette er lidt sværere at gøre med rå kanter, da de er svære at replikere i CAD. Jeg løste problemet ved at installere en høj stige og tage billeder af brædderne i hele længden. Derefter importerede jeg billederne ind i programmet og sporede konturerne. Målebåndet var synligt på billedet for at hjælpe med at skalere grafikken mere nøjagtigt.
Efter at have designet de elektroniske modeller, overlejrede jeg dem med et rigtigt fotografi af overfladen af pladerne, så det ville være lettere for kunden at forestille sig, hvad jeg skulle lave. Da vi besluttede designet, designede jeg de forskellige elementer, og hvordan de ville interagere og knytte sig til hinanden.
Til dette projekt vektoriserede jeg forskellige projektioner af modellen til alle mulige formål. Jeg tegnede konturerne af de centrale hulrum og eksporterede dem til en DXF-fil, som jeg derefter sendte til et glasfirma for at få dem skåret de samme former ud til mig.Jeg brugte den samme fil til at lave en skabelon med omridset af hulrummet, hvorefter det vil være muligt at skære polycarbonatpladerne ud, som skal fastgøres på undersiden af bordpladen. Jeg skar skabelonerne og polycarbonatet på min hjemmelavede CNC-router. Jeg skar også en skabelon ud for at holde metalbenstykkerne på plads, så jeg kunne svejse dem ordentligt. Jeg har endda laserskåret profiler af forskellige metaldele, som vil hjælpe mig med at skære bendelene i den rigtige vinkel. Efter at have designet en komplet model i CAD, kan du begynde at arbejde, eller i det mindste bliver det meget nemmere at arbejde med.
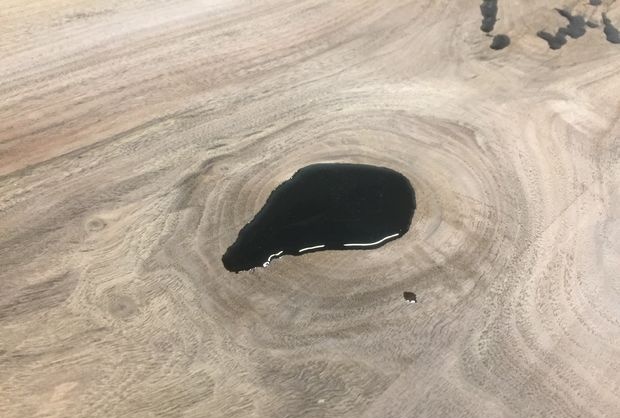
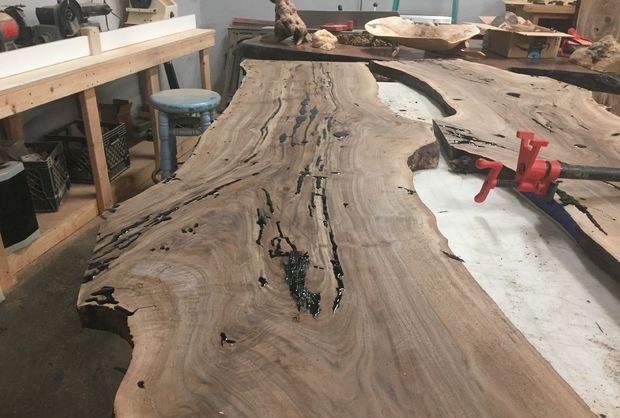
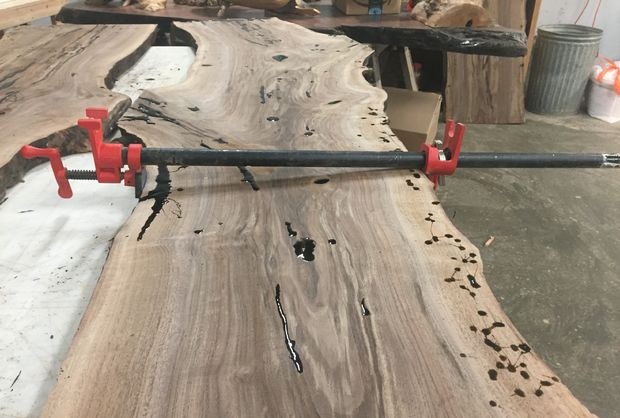

I de fleste tilfælde kan jeg godt lide at få alle knaster, revner og hulrum forseglet og fyldt med sort epoxy, især når man arbejder med valnød. Sort farve ser oftest naturlig ud og tilføjer nogle gange kontrast. Da der var ret dybe revner hist og her i brædderne, brugte jeg en harpiks med lang hærdetid; dette vil give det mulighed for at suge godt ind og hjælpe med at forsegle revnerne i stedet for at skabe en illusion af fyldning. Ulempen ved denne metode er, at du næsten altid skal påføre harpiksen en anden, og nogle gange en tredje gang. Nogle gange bruger jeg en harpiks med en hurtig hærdetid til efterbehandling. Jeg udfyldte alle hulrummene på begge sider af brædderne, så de kunne holdes sikkert på plads. Det er bedre at påføre epoxyharpiksen i en "dynge", så der ikke findes bobler under slibning (så de vil stige over brættets plan).
Efter at have fyldt alle hulrummene sleb jeg de udsatte dele af epoxyen ned med et P60 slibemiddel.
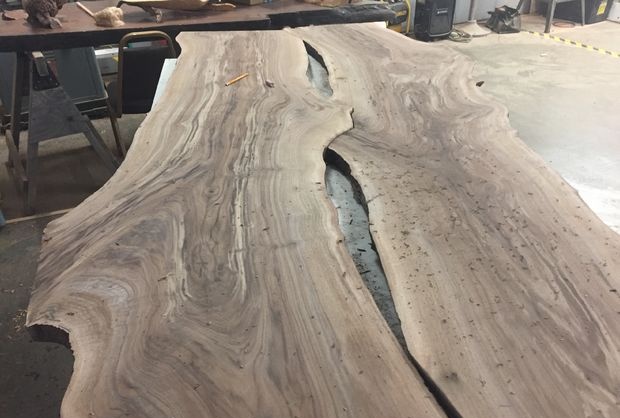
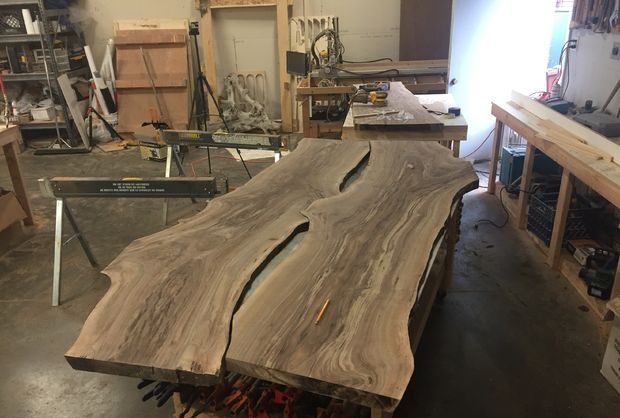
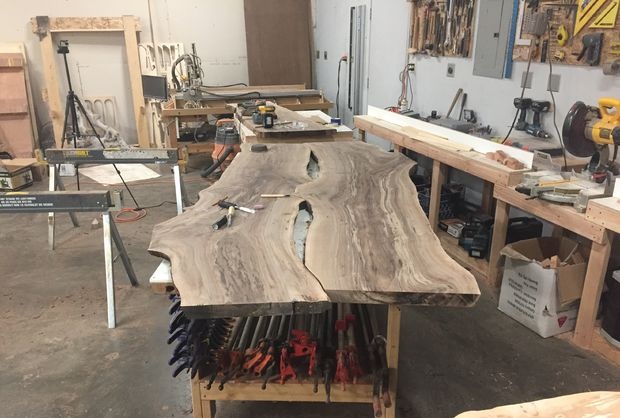
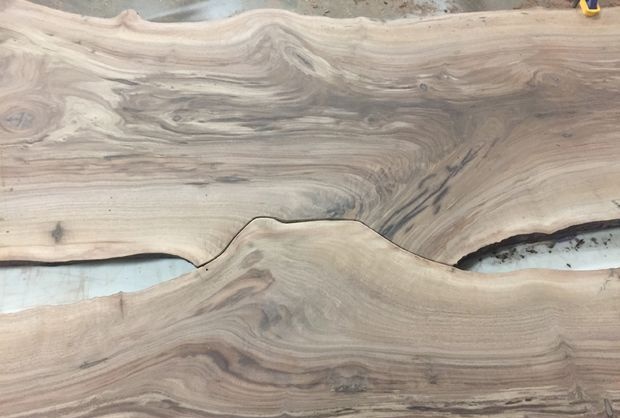
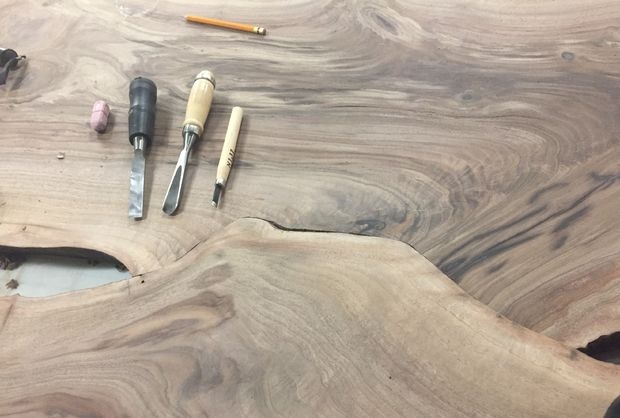
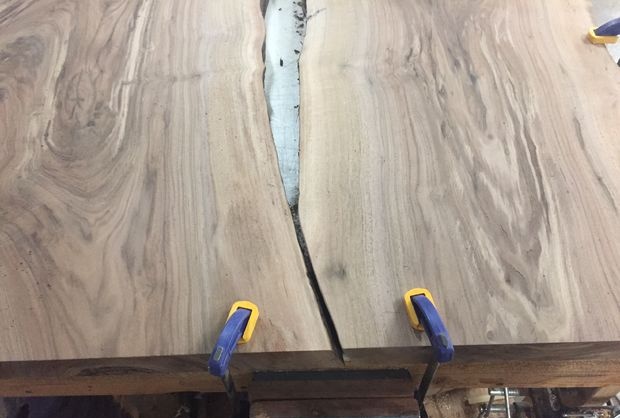
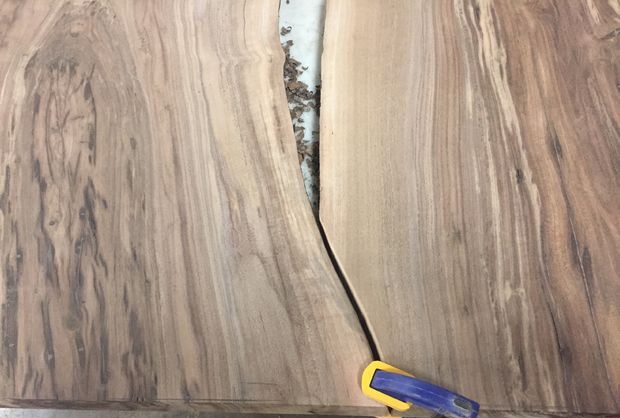
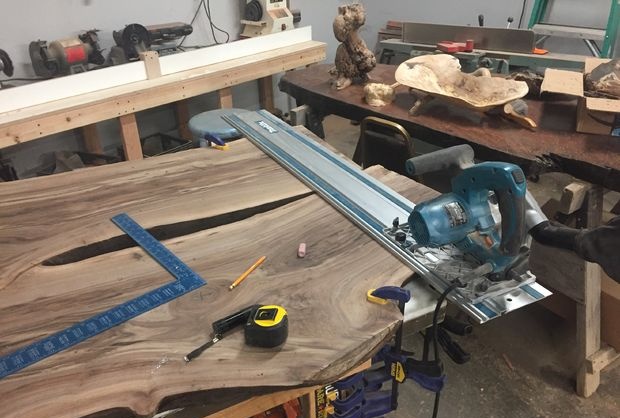
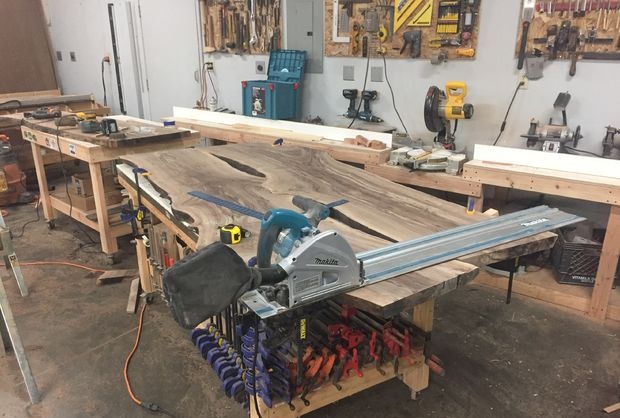
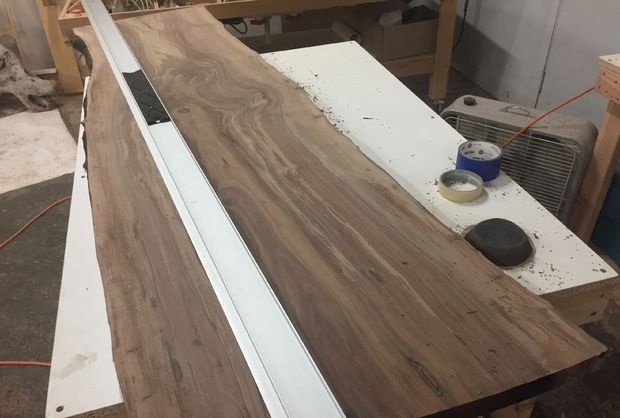
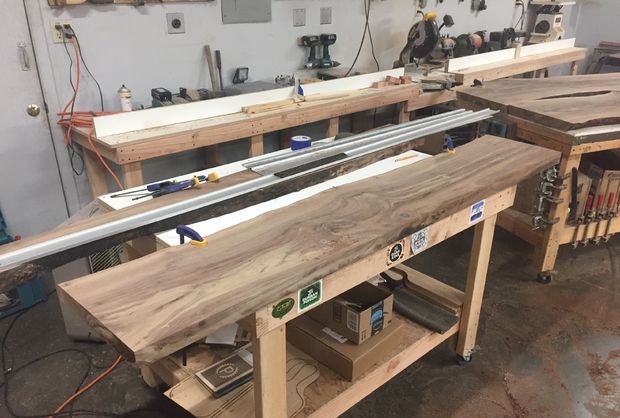
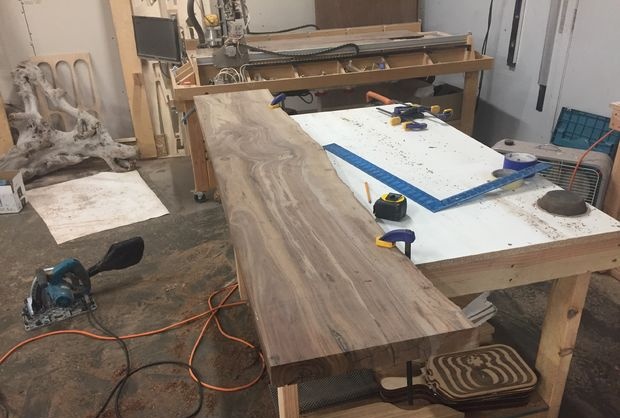
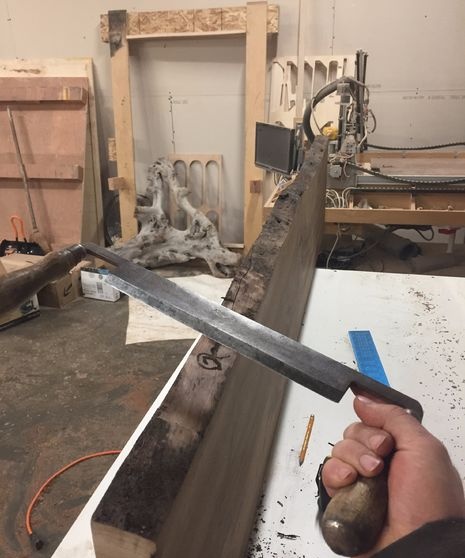
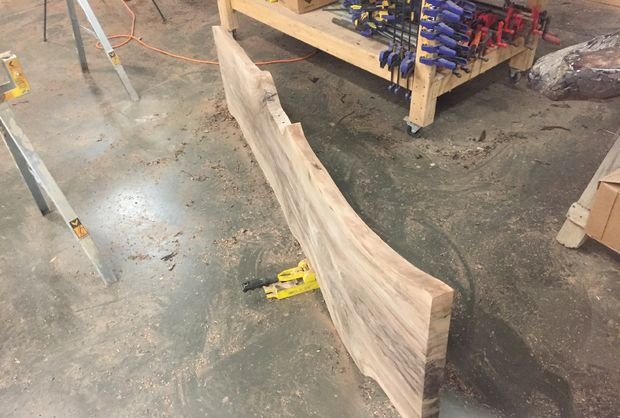
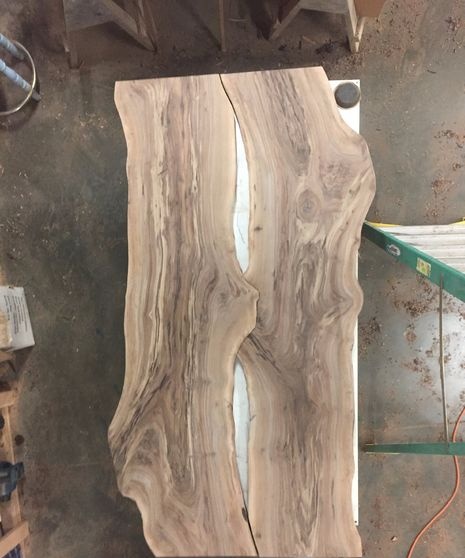
Desværre dokumenterede jeg ikke rigtig denne fase. I det væsentlige lagde jeg et bræt oven på et andet i den ønskede position og markerede det område, der skulle fjernes. Til selve arbejdet brugte jeg en stiksav, en vinkelsliber (med skæreskive og en klapskive) og eventuelt håndværktøj til træskærerarbejde. Der var meget fint arbejde og tilpasning på dette tidspunkt. Jeg efterlod en søm ca. 4 millimeter tyk langs hele længden mellem brædderne. Jeg troede, at bordet ville se mere udtryksfuldt ud på denne måde. På den negative side efterlader en sømløs pasform hjørner, hvilket ikke er et godt udseende. Tykkelsen af sømmen vil blive bibeholdt takket være svalehalenøglen. Jeg glattede derefter bordets kanter ud med en rundsav.
Under dette trin skrabede jeg de rå kanter fri af eventuel resterende bark på både bordet og bænken. Jeg gik så over dem med en vinkelsliber med klapskive for at få de ru kanter glattere.
På bænken skar jeg den ene rå side med en rundsav. Jeg aftalte med kunden, at bænken ville have den ene side lige.

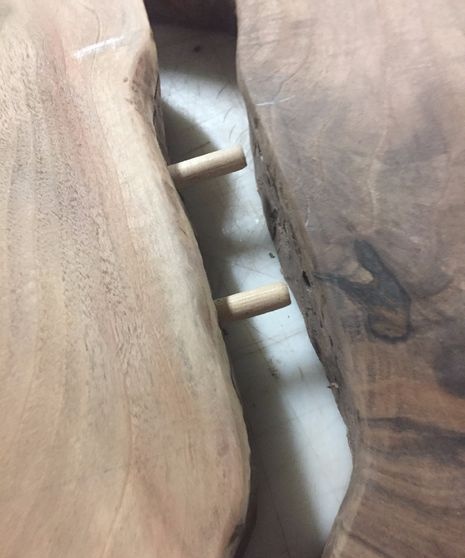
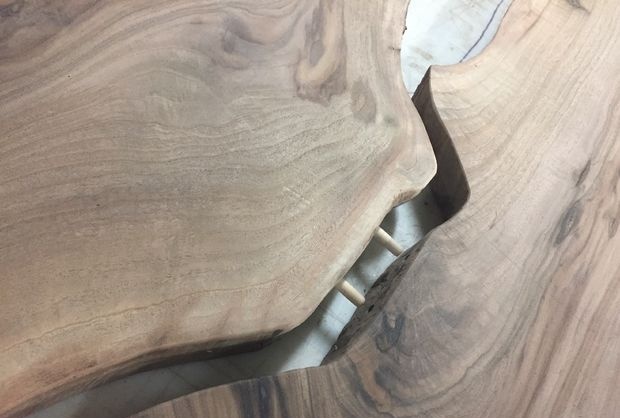
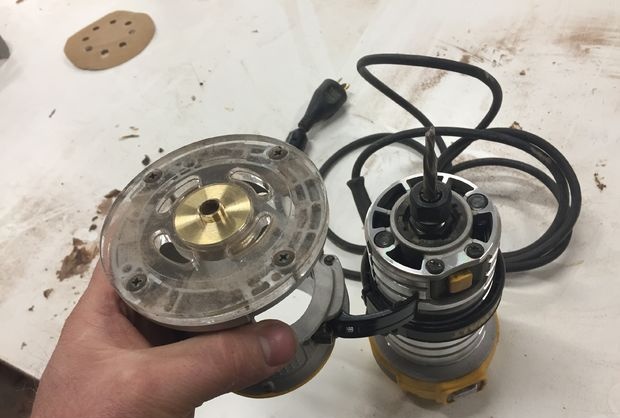
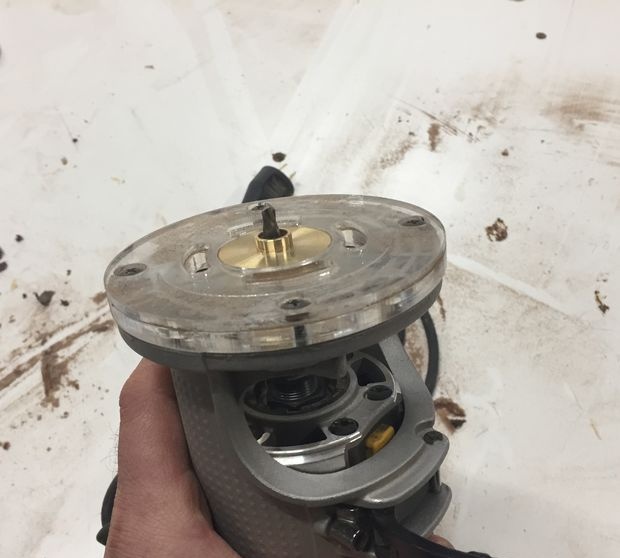
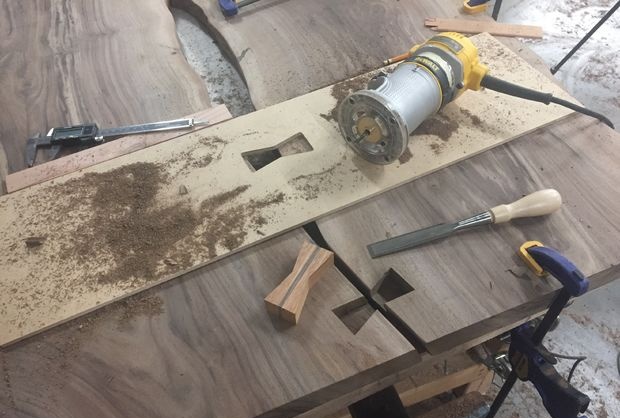
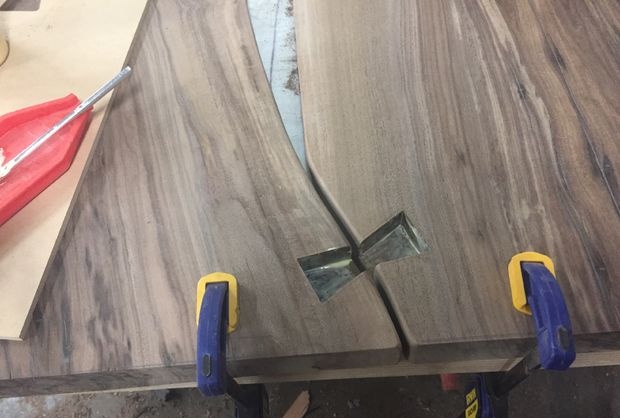
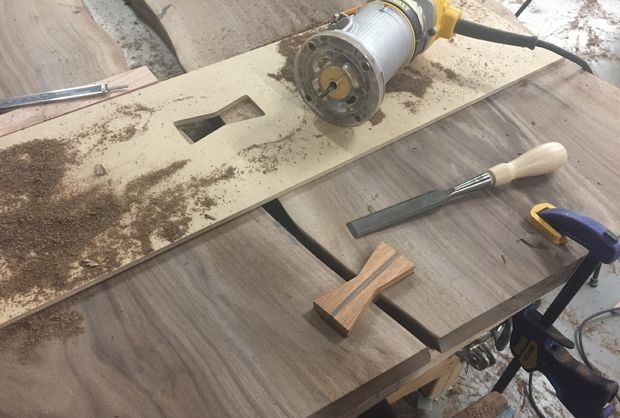
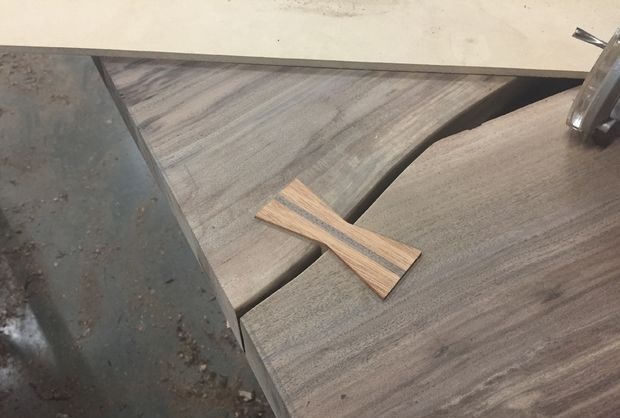
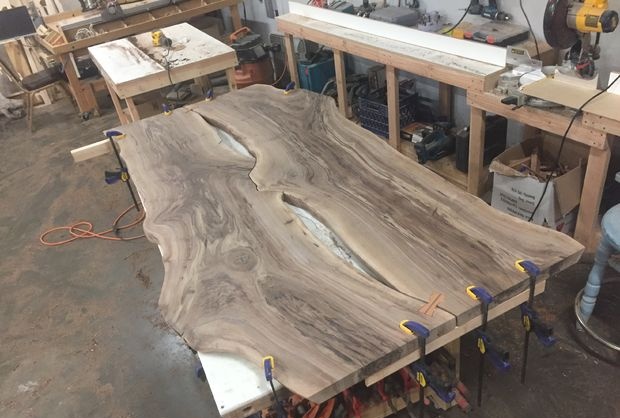
Jeg brugte dyvler til at forbinde de centrale dele. De tjener til at fastgøre to brædder i samme plan (i forhold til hinanden). Hovedbelastningen ved fastgørelse af bordpladen vil falde på bordets dyvler og ben. I modsætning til de dyvler, som jeg har set, lavede jeg disse med en tykkelse næsten lig med tykkelsen af brædderne.
Materialet til dyvlerne blev lavet ved at lime et ark valnød mellem to plader mahogni og en CNC-maskine skar formen ud. Jeg har også lavet en skabelon til at hjælpe dig med at skære dyvelåbningerne ud med en håndfræser.
Efter at have justeret sømmen mellem brædderne, fastgjorde jeg dem til bordet ved hjælp af klemmer. Så ved hjælp af en skabelon skærer jeg rillerne ud med en overfræser. Hvor overfræseren forlod rillen rundt, skulle jeg arbejde med en mejsel. Du kunne have lavet en afrundet svalehale, men jeg kan godt lide udseendet af lige hjørner.
Da svalehaleåbningerne var klar, prøvede jeg forsigtigt at indsætte svalehalen (for at sikre mig, at den ikke satte sig fast!) og begyndte at lime. Dyvlerne var lavet lidt tykkere end rillerne, så de blev slebet i plan med bordpladen.
Efter dette trin var afsluttet, sleb jeg alle overflader fra P60 til P180 korn. En sidste slibning med P220 korn blev udført umiddelbart før polering.
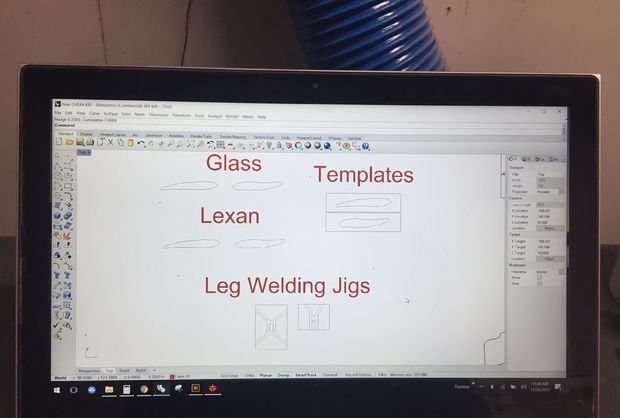
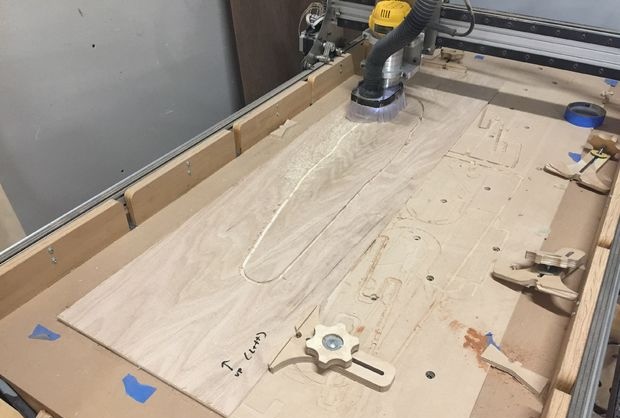
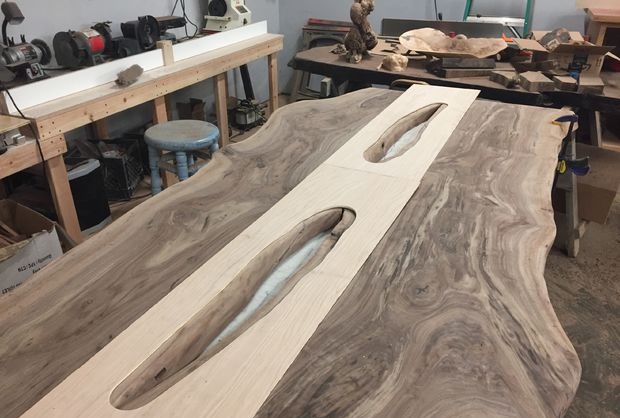
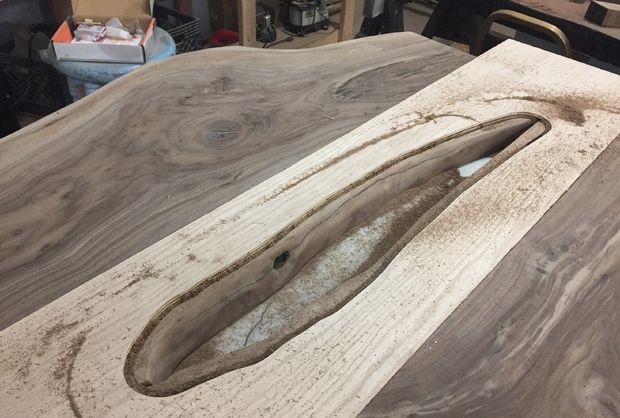
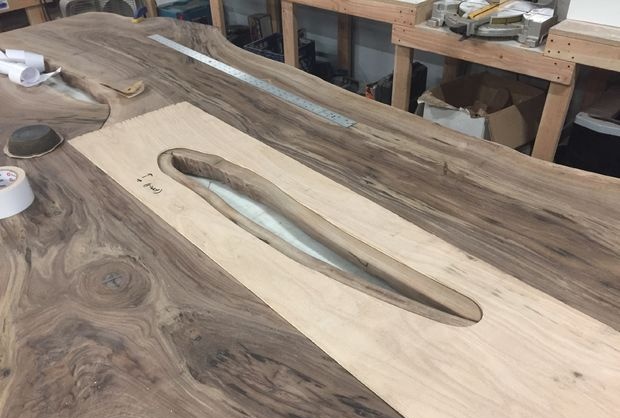
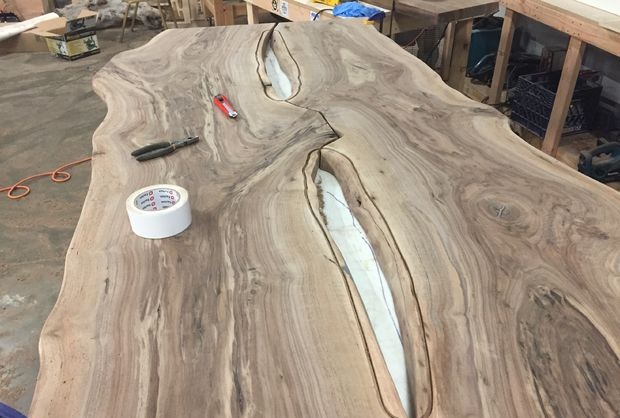
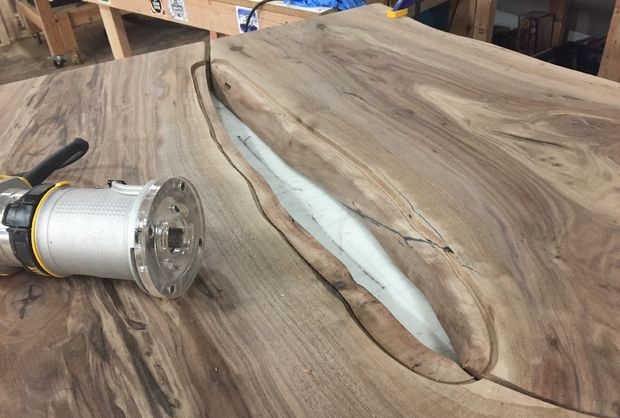
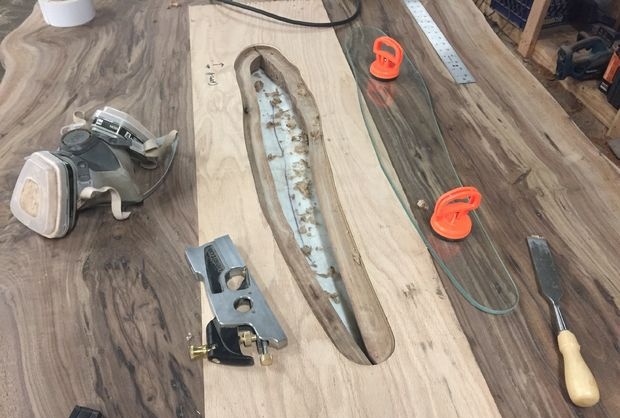
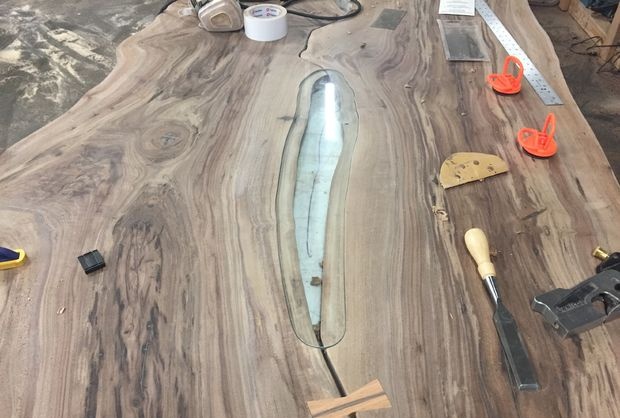
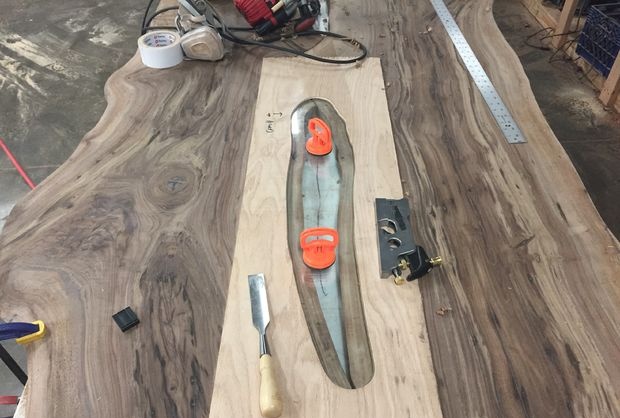
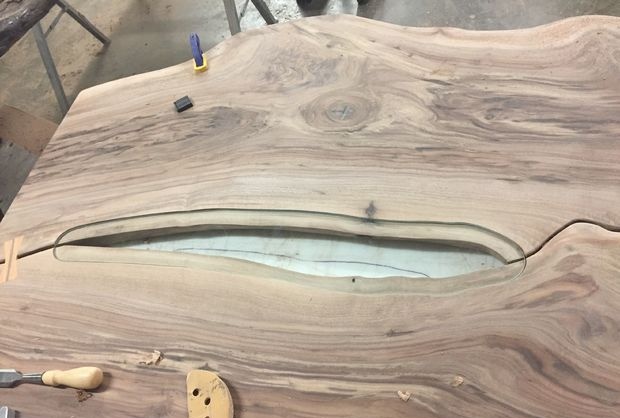
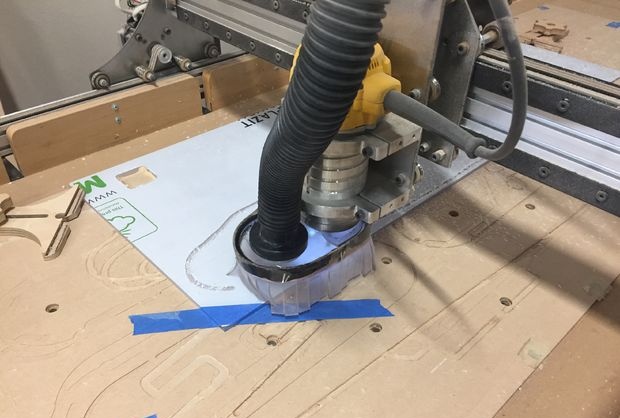
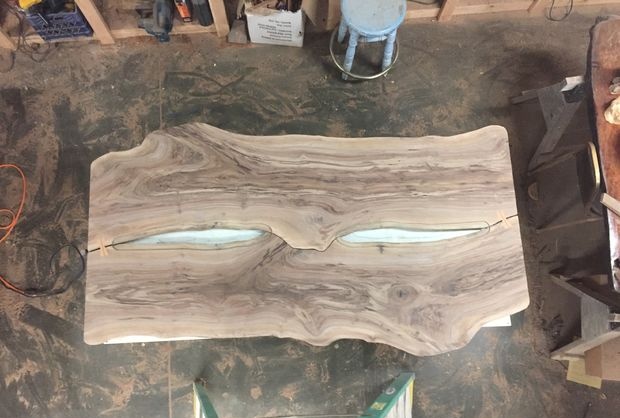
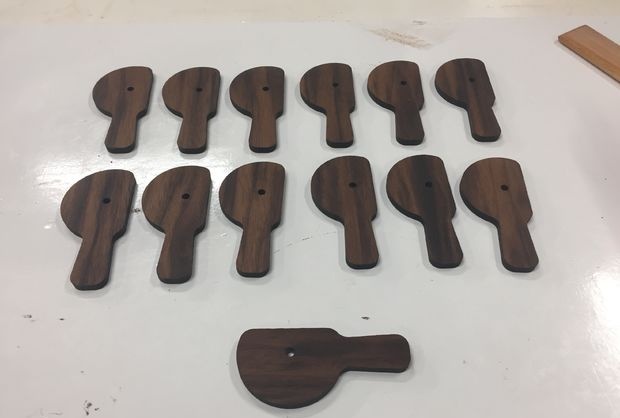
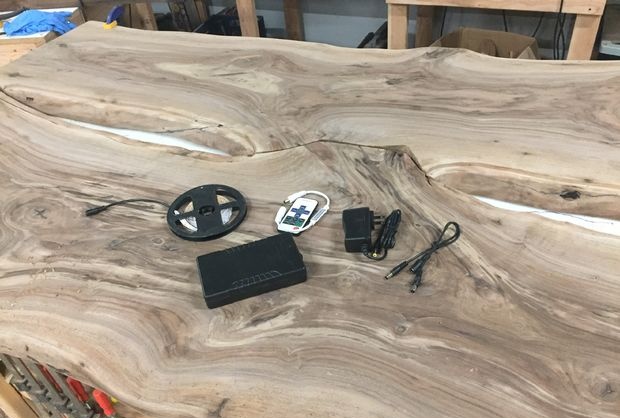
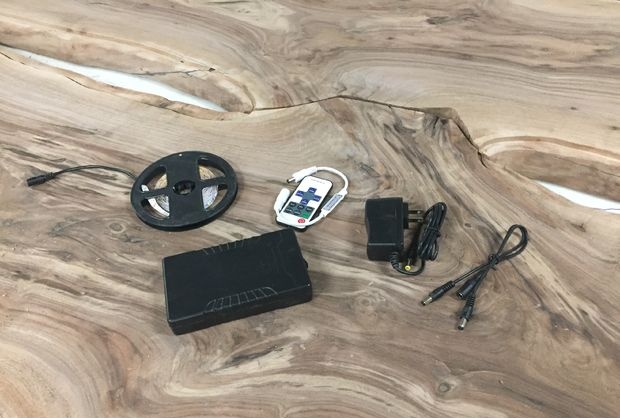
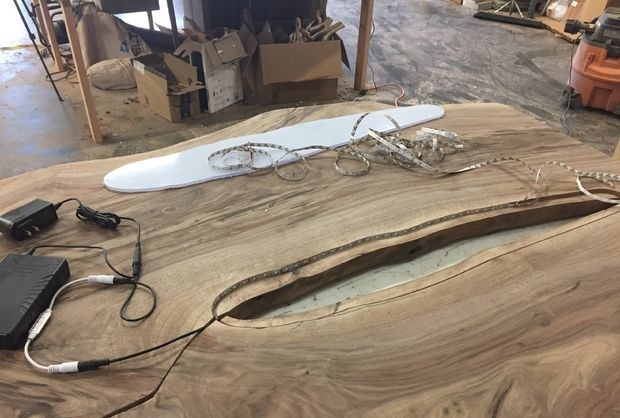
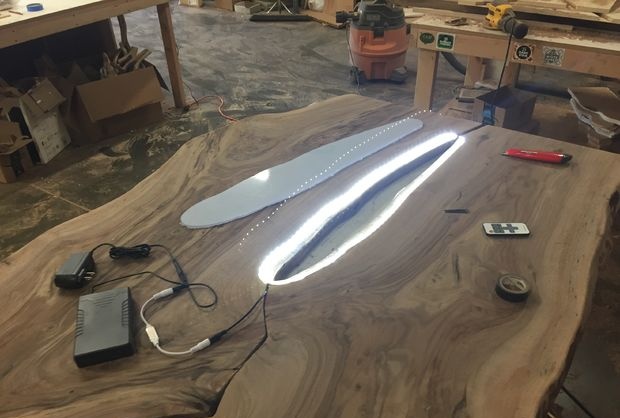
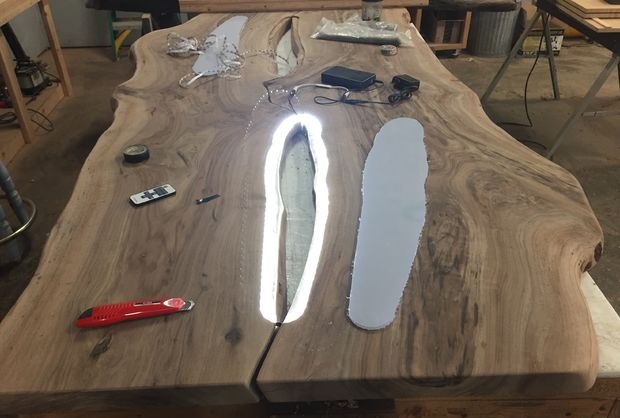
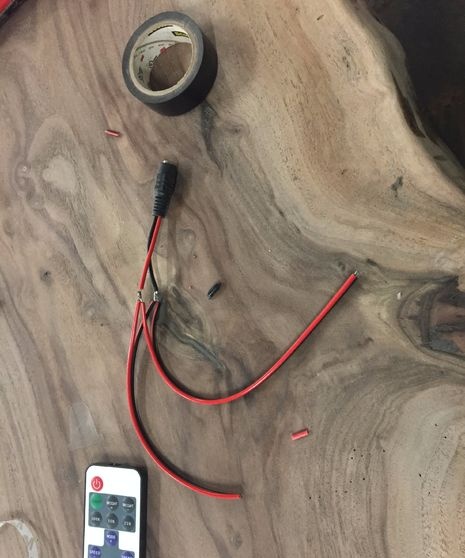
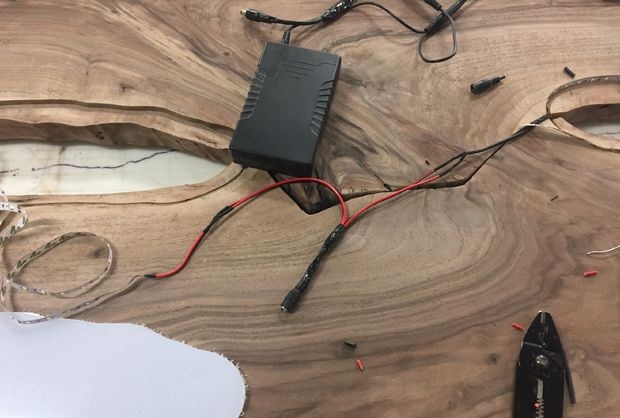
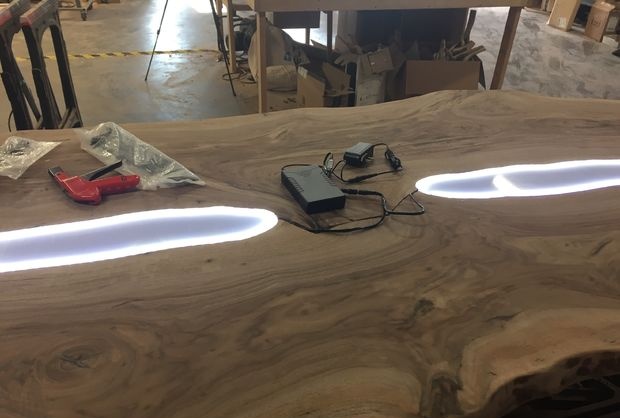
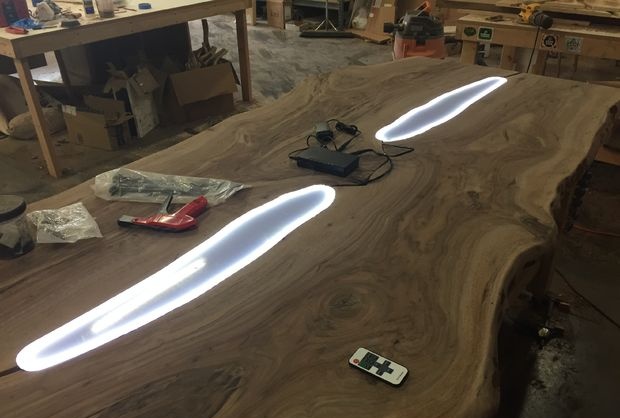
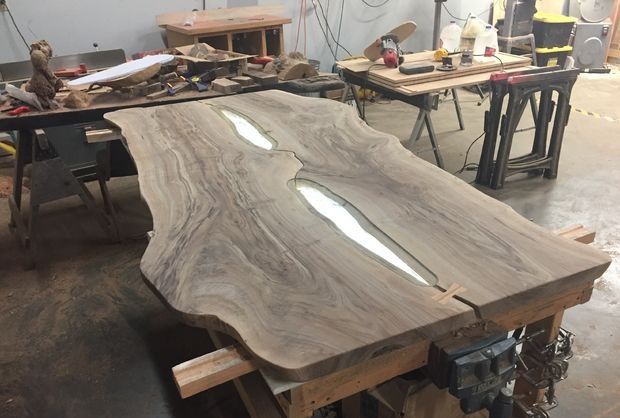
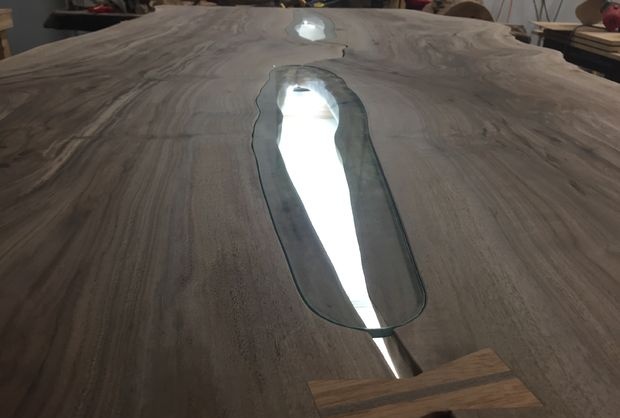
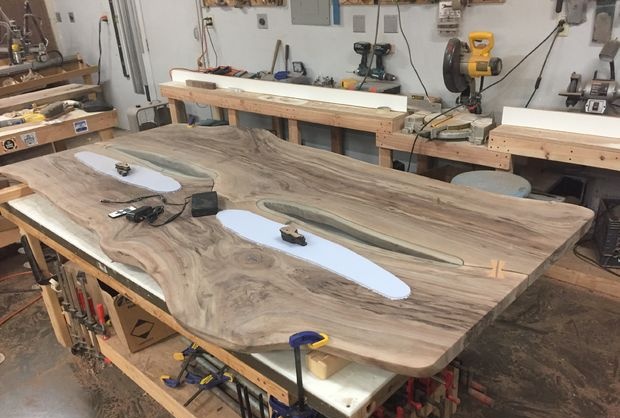
Jeg brugte CAD-modellen til at skabe glasindsatserne og polycarbonatpladen. Dobbeltklæbende tape er perfekt til midlertidig fastgørelse af emner på bordoverfladen. Jeg brugte så håndfræseren igen til at lave rillerne på begge sider af brædderne. For mere præcist arbejde brugte jeg en mejsel og en mejsel, indtil glasset lå fladt og fikseret uden at vakle. Glasset blev fjernet og sat i mange gange, hertil brugte jeg sugekopper.
Polycarbonatpladeindsatserne blev fremstillet ved hjælp af en CNC-maskine og en endefræser. Her skulle jeg tage en beslutning om, hvordan plastindsatserne sikres mere sikkert i bunden af bordpladen. Jeg ville have dem til at være nemme at fjerne, for eksempel at erstatte dem på grund af ridser. Jeg besluttede, at låseflag af valnød ville være det helt rigtige. Så jeg laserskar dem ud af det materiale, jeg havde.
Før jeg indsatte plastikken, skulle jeg finde ud af LED-belysningen. For en mere sofistikeret effekt besluttede jeg at placere LED-belysning rundt om plastikkens omkreds. Denne teknik hjælper også med at skjule ledningerne. Jeg købte en tynd LED-strimmel med en klæbende side, der nemt kan klæbes til den fordybning, jeg lavede tidligere omkring bunden af hulrummet. Jeg var nødt til at bygge to separate Y-formede elektriske kredsløb, der derefter ville føres ind i en separat lysdæmper. Lysdæmperen er tilsluttet batteriet på den ene side og til en 12-volt strømforsyning på den anden. Dette gør, at lamperne kan lyse både fra batterier og fra lysnettet. Ideen er, at husejere skal tilslutte opladeren, når de ikke bruger skrivebordet, så ledningerne kan gemmes væk, når de kommer i vejen. Ledningerne og batteriet blev fastgjort til bunden af bordpladen ved hjælp af klemmer og ankre. Jeg overvejede muligheden for at indlejre batteriet og ledningerne i træet, men besluttede til sidst, at det var bedre at lade være, da alle disse komponenter skal udskiftes på et tidspunkt. I slutningen af dagen skulle dette bord være et arvestykke, der vil overleve mig, kunden og LED-lysene. De siger, at LED-lamper kan holde ret længe, men hvis lysten melder sig, kan de udskiftes med noget lignende.
Efter at have prøvet plastikken og tjekket belysningen lagde jeg pladerne til side. Låseflag og plast kan påsættes efter polering.
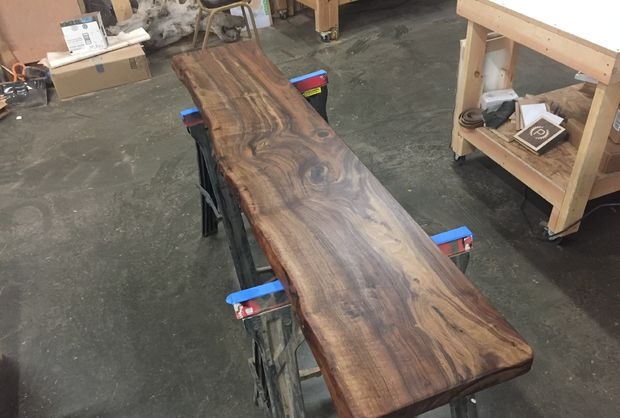
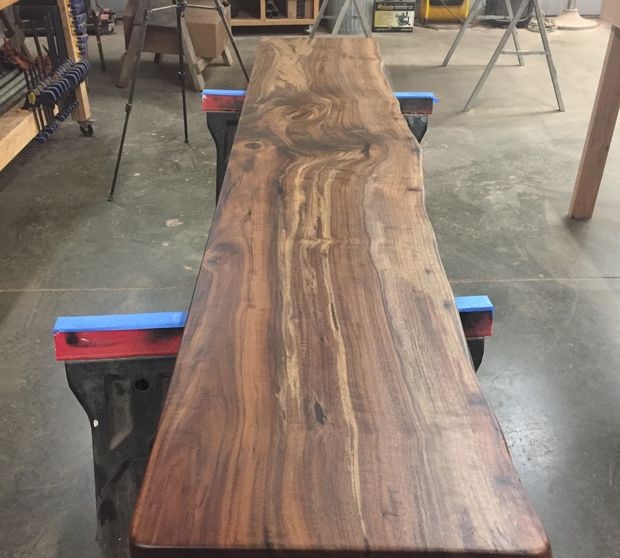
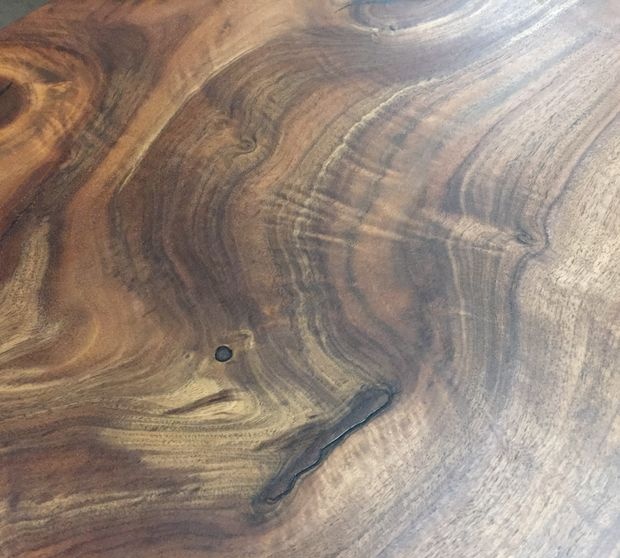
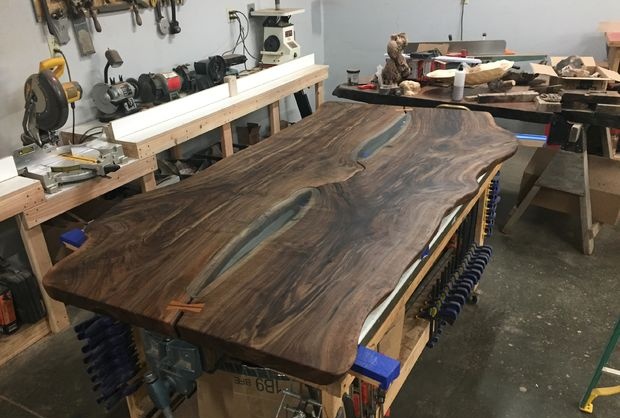
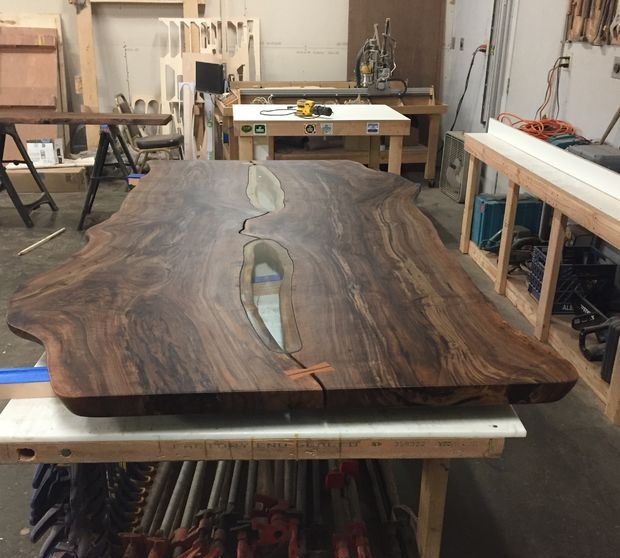
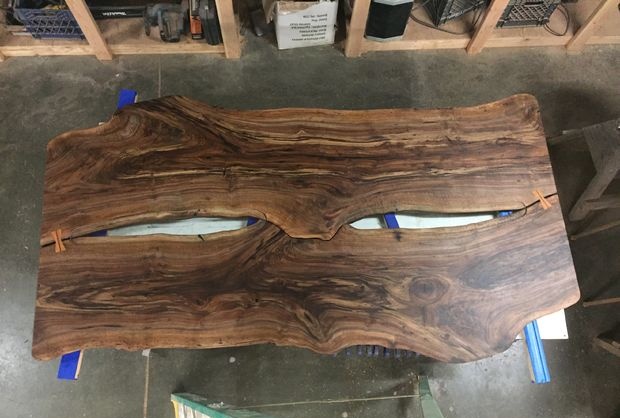
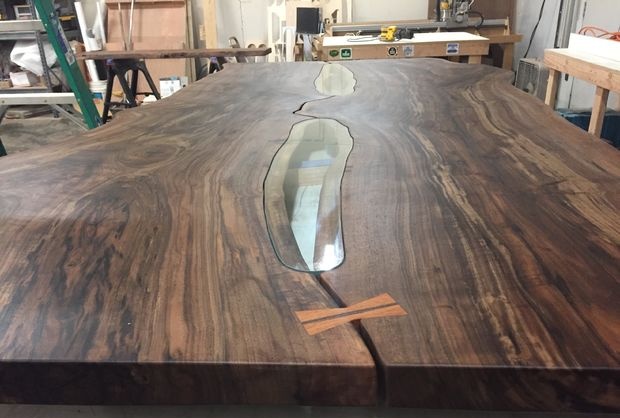
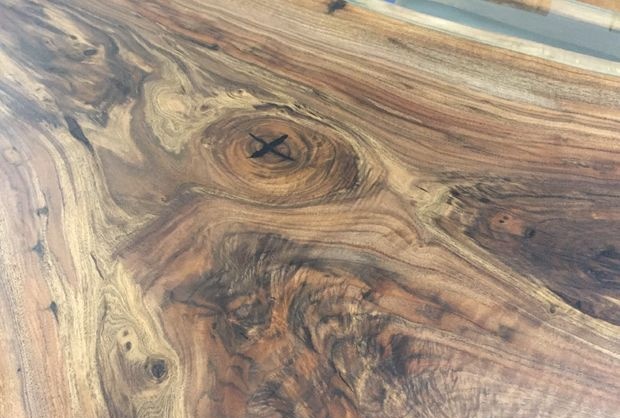
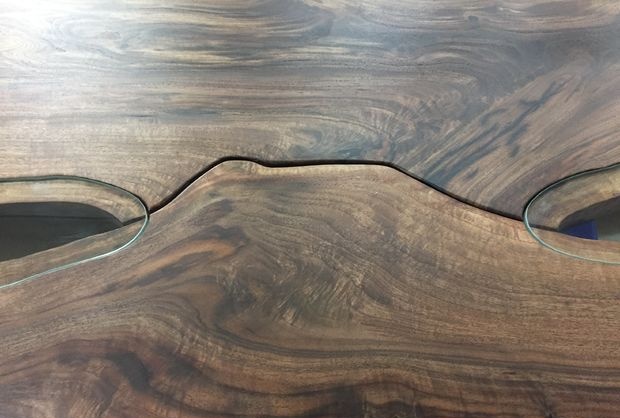
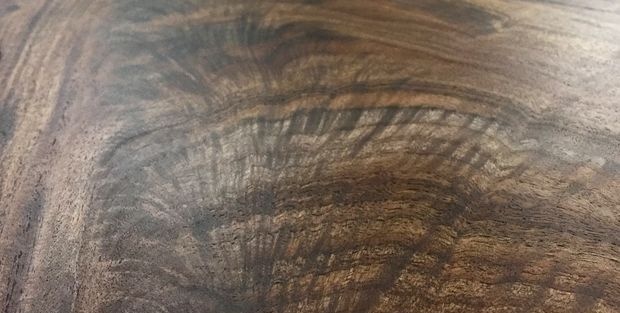
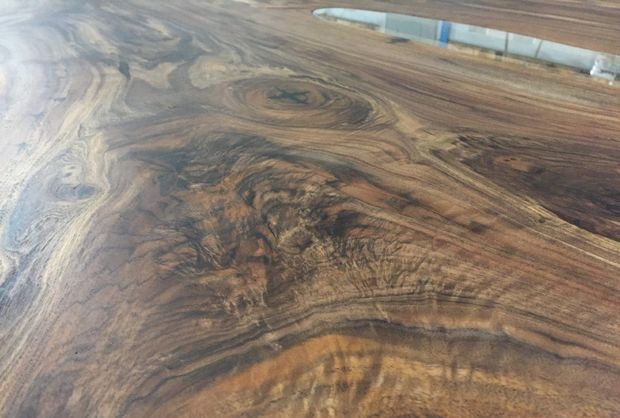
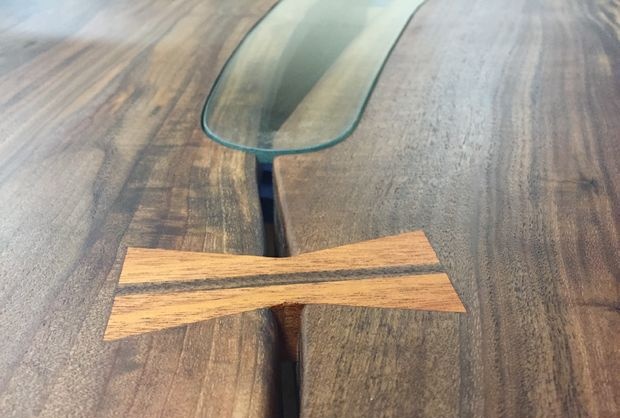
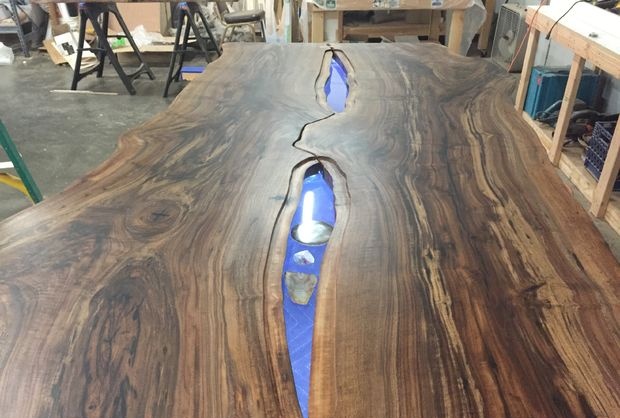
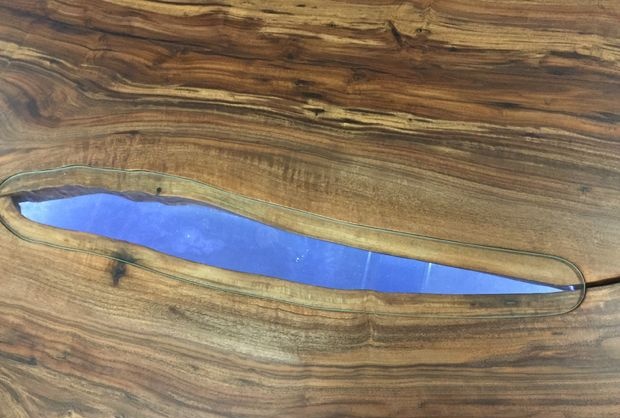
Kunden ønskede at bruge et poleringsmateriale, der ville bevare træets naturlige udseende, gøre det holdbart, men ikke ligne lak. Så jeg valgte OSMO PolyX. Dette produkt er designet til trægulve, men også til møbel det passer godt.Den har et lavt VOC-indhold og et højt faststofindhold, da det primært er sammensat af voks og naturlige olier. Det er nemt at anvende. For at opnå et godt resultat er to lag nok.
Jeg tog ingen billeder af denne proces, fordi jeg altid havde gummihandsker på med polerpasta. Inden jeg lagde lag, gik jeg igen over overfladerne og kanterne med en P220 korn.
Jeg brugte en spatel til at påføre OSMO jævnt på overfladen. Det var nemt for dem at fugte træet fuldstændigt og dække alle de små ujævnheder med pastaen. Jeg skulle bruge stof på kanterne. Efter fugtning fjernede jeg den resterende pasta med en fnugfri klud. På dette stadium er det vigtigt at bearbejde overfladerne grundigt, men helt fjerne overskydende. Jeg beklædte toppen, bunden og alle kanterne af bordet og bænken og lod dem tørre i en dag eller to, og så gjorde jeg det hele igen. Kun to lag er nok, og faktisk kan påføring af flere resultere i en uønsket blank effekt.
Som et resultat blev behandlingen af trædelene afsluttet, jeg lagde polycarbonatpladerne på plads og fastgjorde dem med flagklemmer.
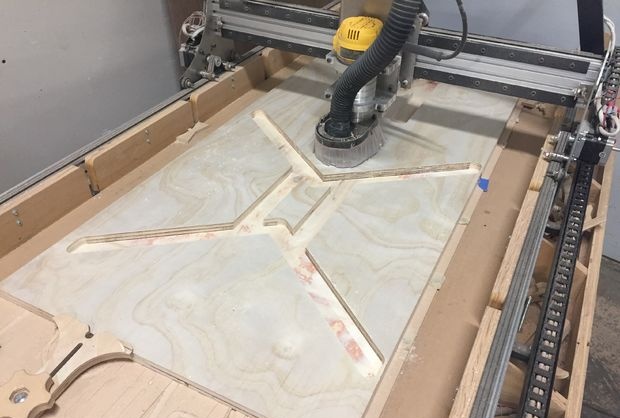
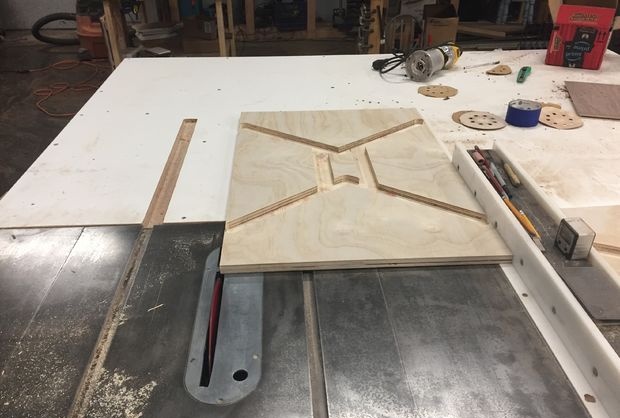
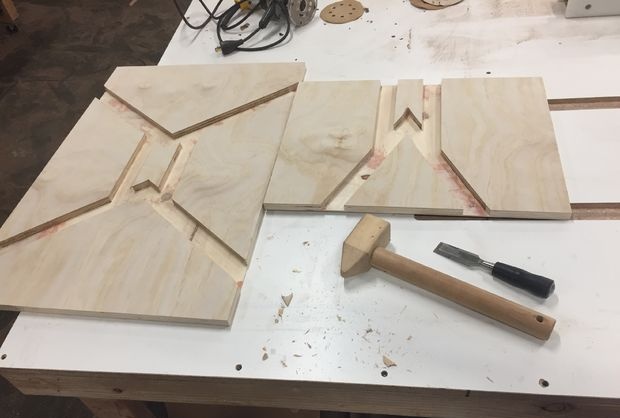
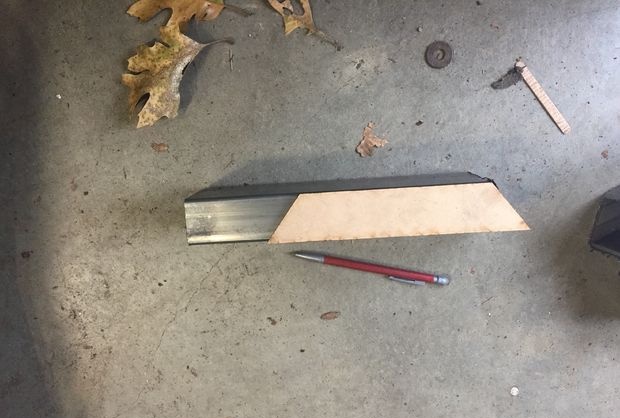
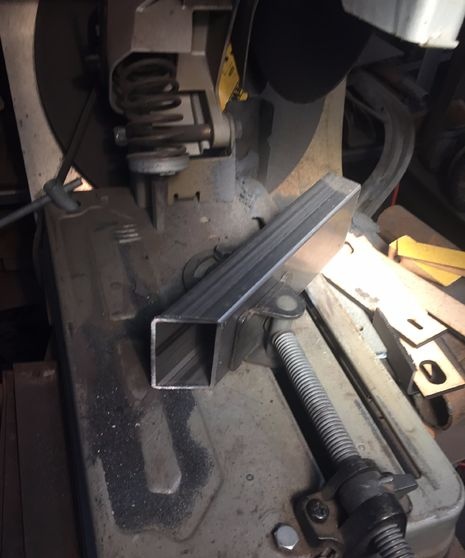
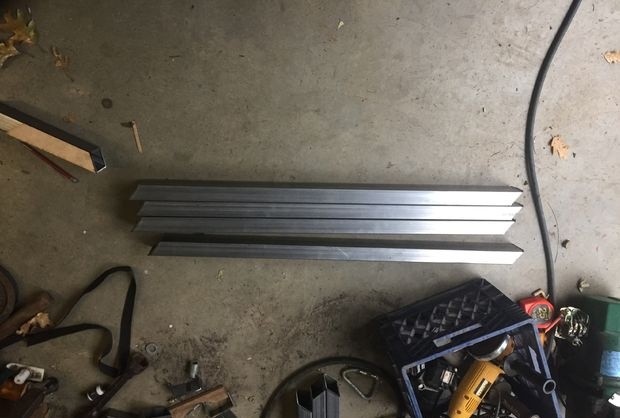
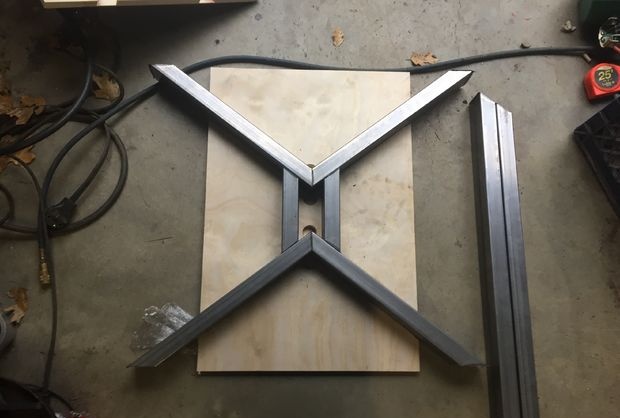
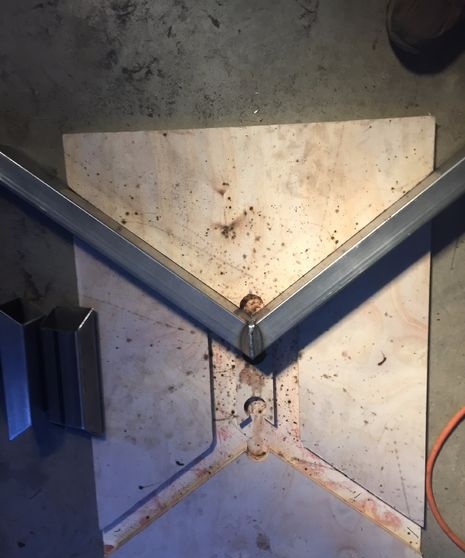
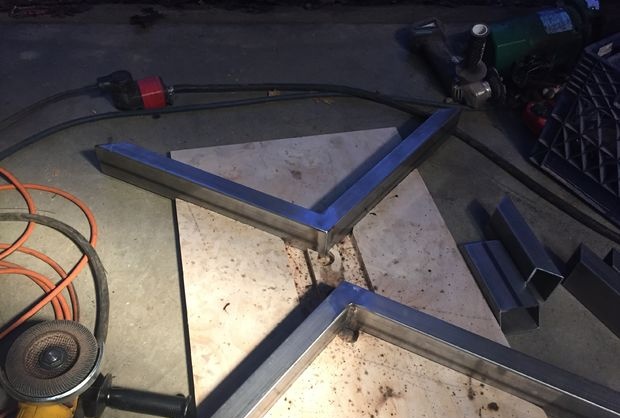
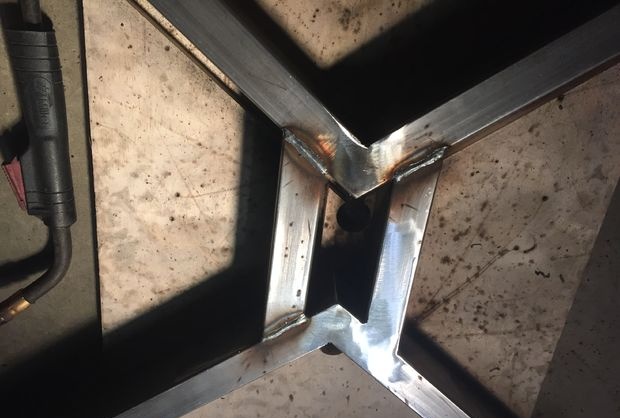
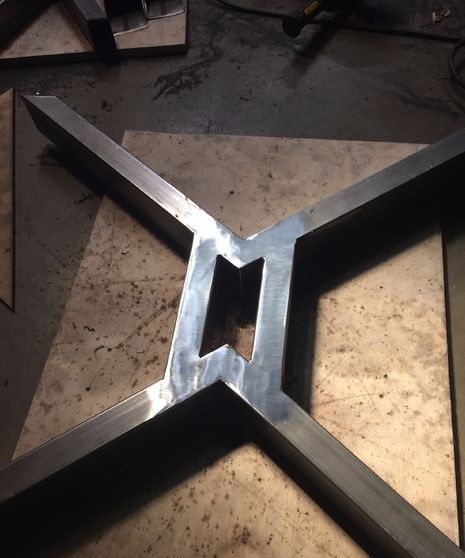

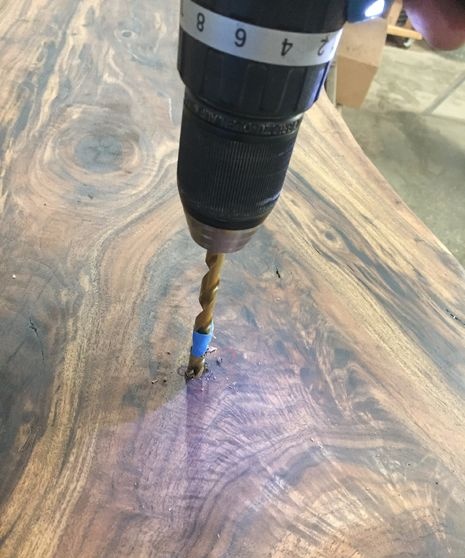
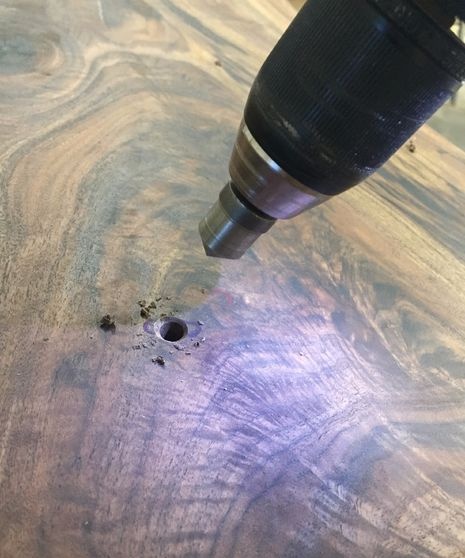
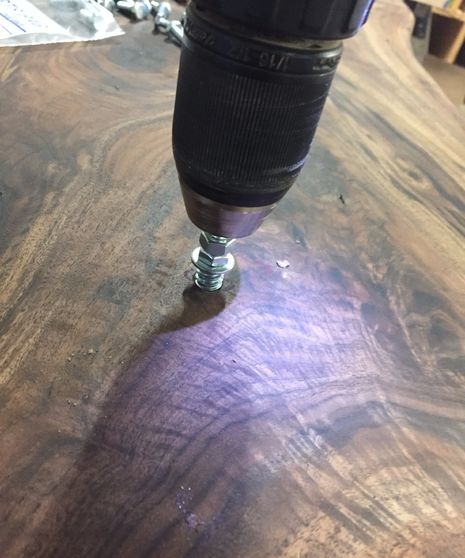
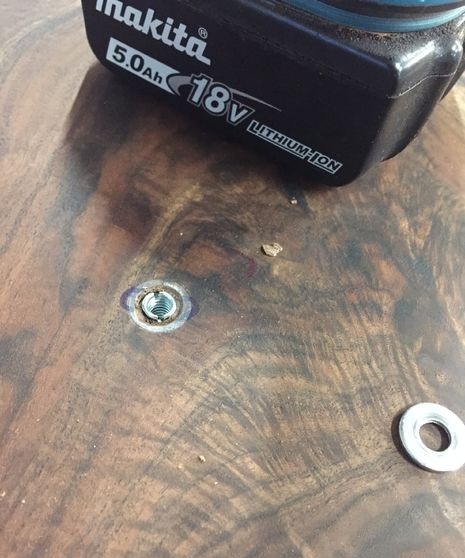
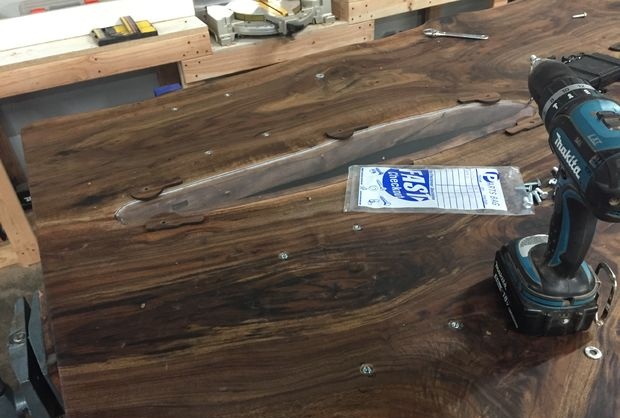
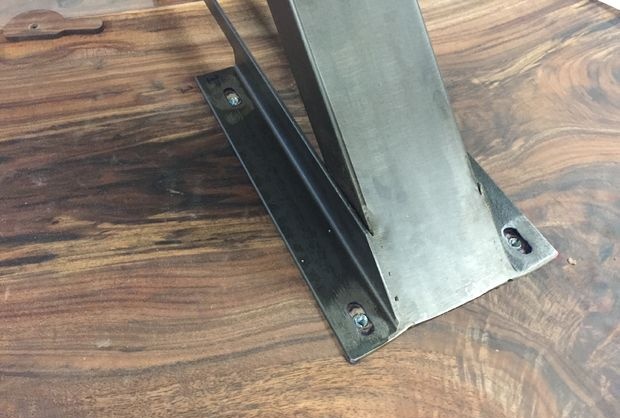
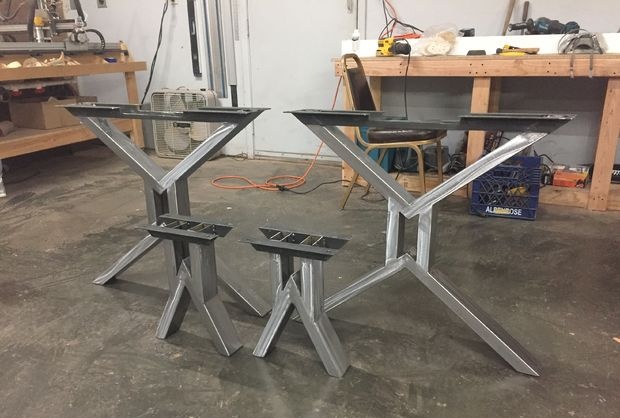
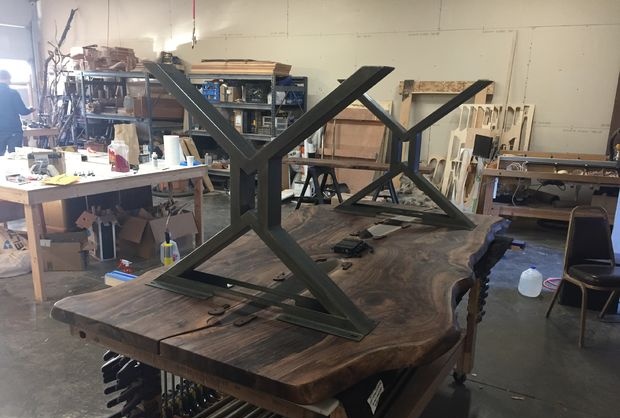
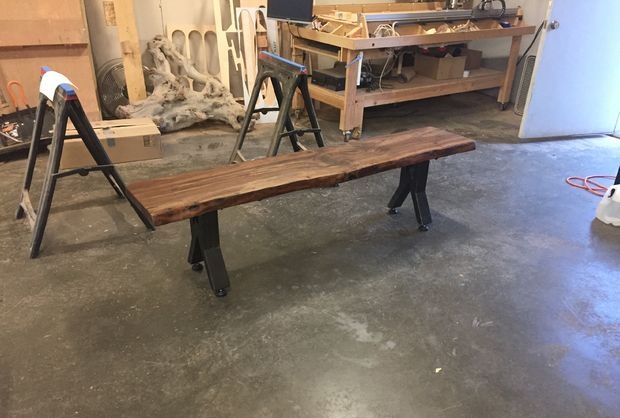

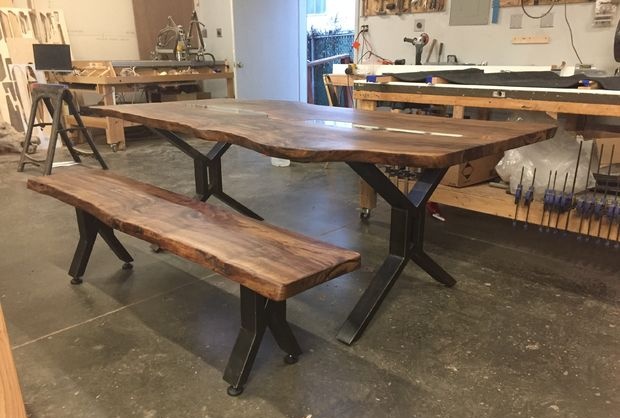
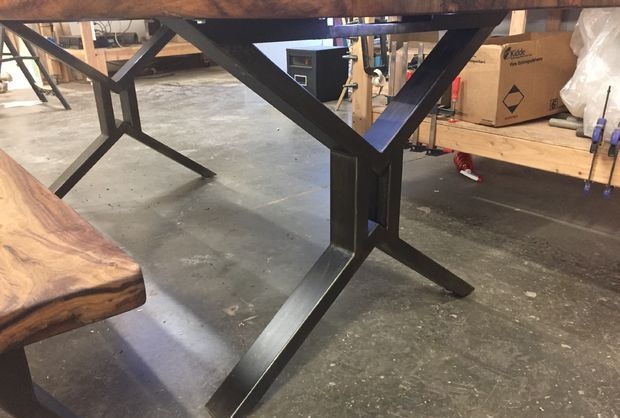
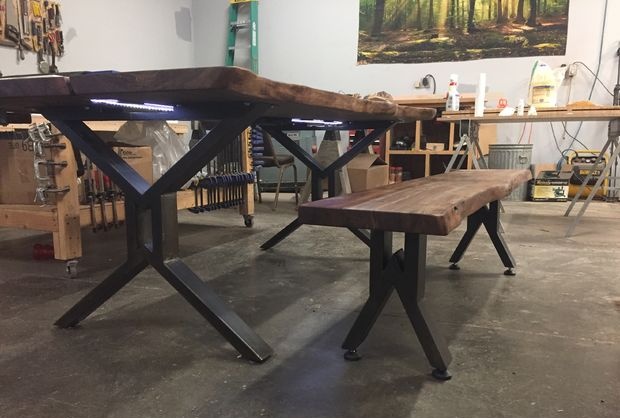
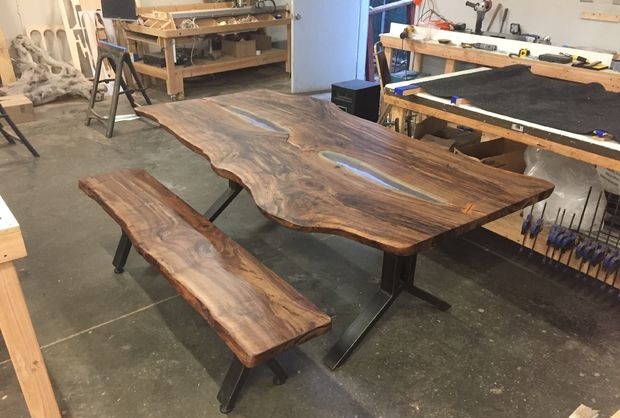
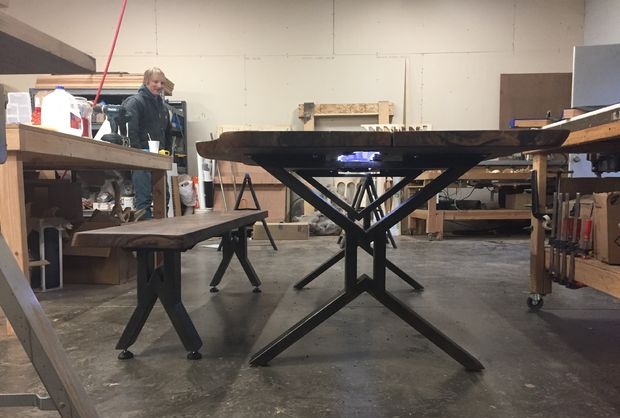
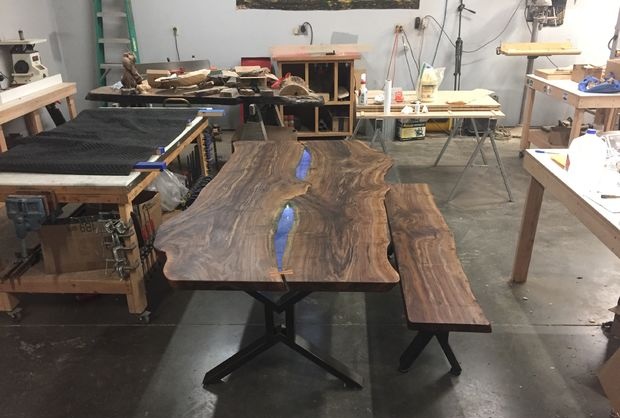
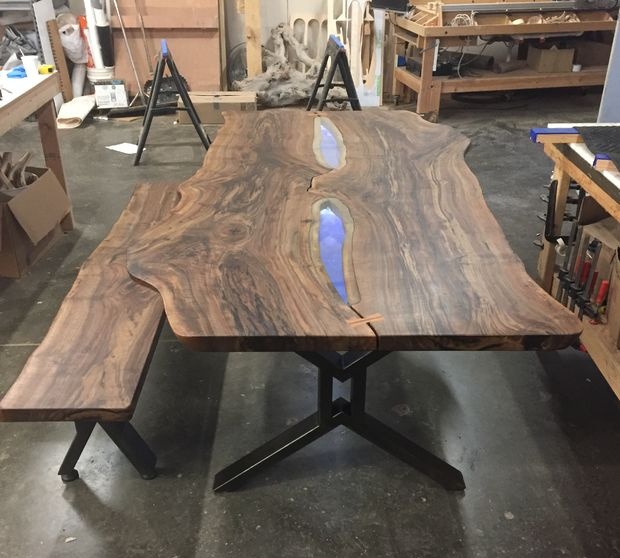
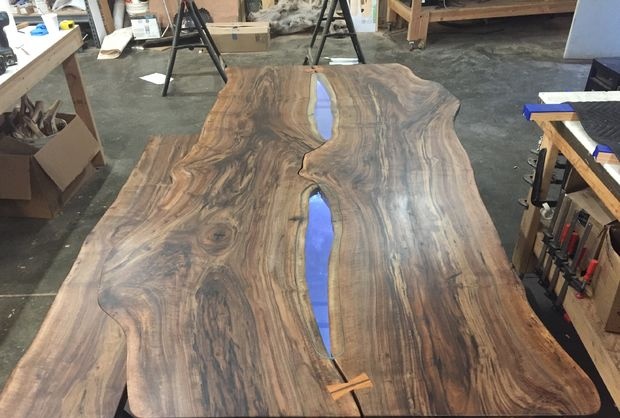
Benene var lavet af et rektangulært stålrør, der målte 3,8 x 7,6 cm og en jernvinkel på 3,8 x 3,8 cm. For at gøre processen lettere brugte jeg en laserskærer til at skære skabeloner ud for at holde de nødvendige komponenter på plads og et emne til at hjælpe med at sætte alt sammen i den rigtige vinkel. For lang tid siden var jeg en fremragende svejser, men der gik år, og uden tilstrækkelig øvelse havde jeg stadig funktionelle færdigheder, men jeg glemte, hvordan man svejser med dekorative sømme.For at udjævne denne ufuldkommenhed brugte jeg en vinkelsliber til at slibe det overskydende metal af og give overfladen et renere udseende.
Da svejsningen var færdig, sleb jeg alle metaloverfladerne med en vinkelsliber og en klapskive for at sikre, at de havde en ensartet tekstur og glans. Jeg skærer aflange huller i vinkelmetallet til at fastgøre bordpladen til, så hvis træet trækker sig sammen eller udvider sig, bliver der ikke problemer. Jeg svejste de nederste dele af benene med jernplader, så jeg så kunne bore huller i dem og installere højdejusteringsmekanismen.
Kunden ønskede, at benene skulle være sorte. Vi tænkte lidt over, hvordan vi bedst gør dette. I stedet for maling besluttede vi at bruge et stålblånende middel, så resultatet bliver mere holdbart og bedre skjuler ufuldkommenheder. Jeg brugte et produkt kaldet presto black. Påføring blev udført gennem en sprayflaske, indtil alle overflader var dækket af stoffet, og derefter blev dets virkning neutraliseret med en opløsning af bagepulver, så metallet ikke begyndte at oxidere (ruste). Efter at have fjernet blånemidlet tørrede jeg metallet med en kompressor og belagde overfladen med mat polyurethan for at forhindre, at det ruster undervejs.
Jeg brugte møbelmøtrikker og bolte til at fastgøre benene, hvilket gør det muligt at fjerne og montere benene igen og igen. Benene på bænken har jeg sikret med store træskruer, da den ikke er stor og kan flyttes uden at tage benene af.
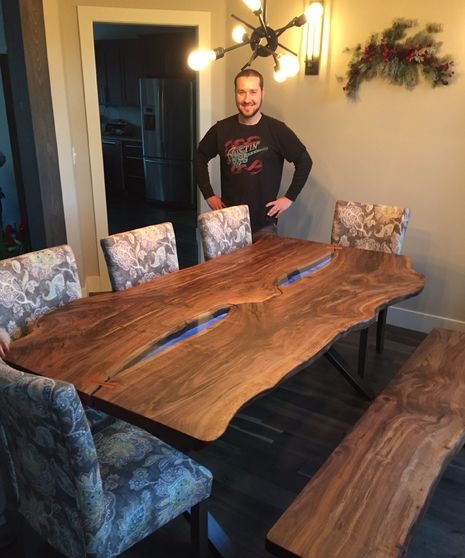
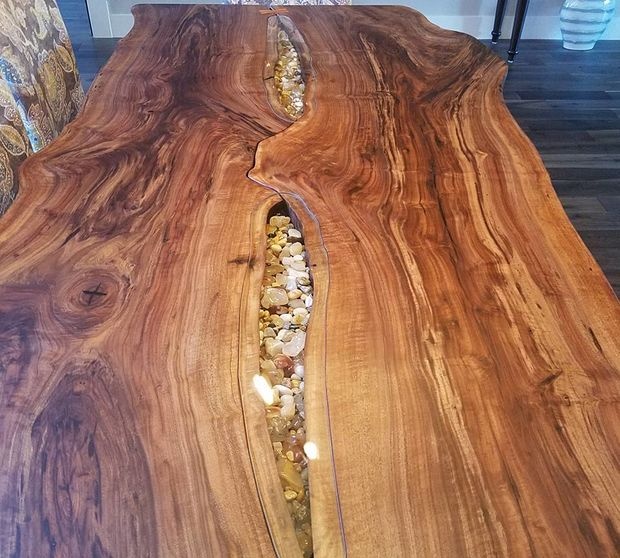
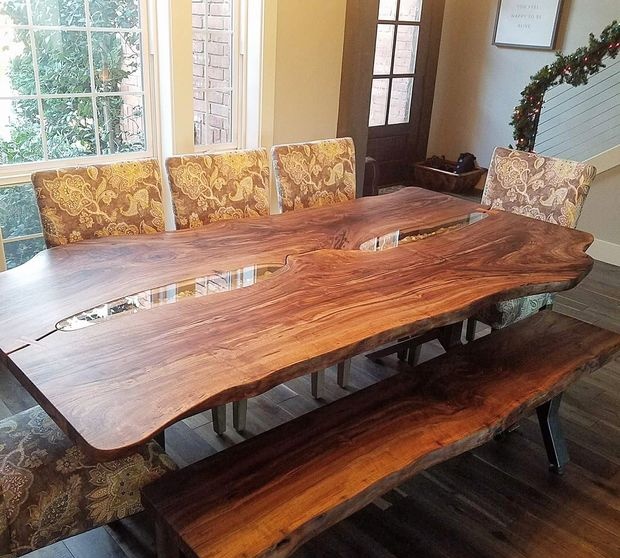
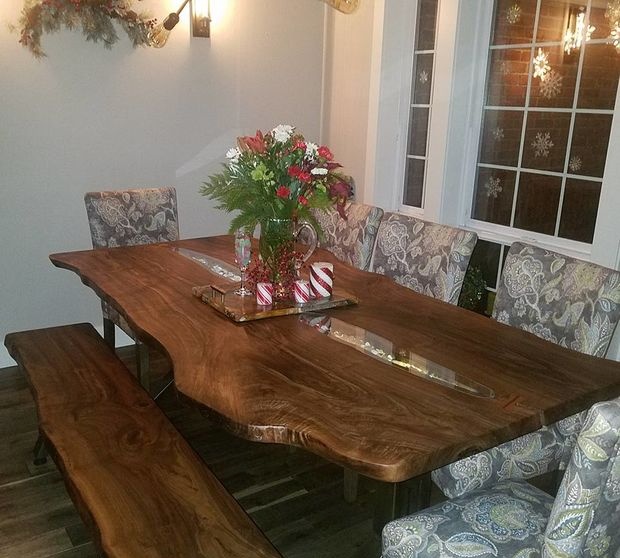
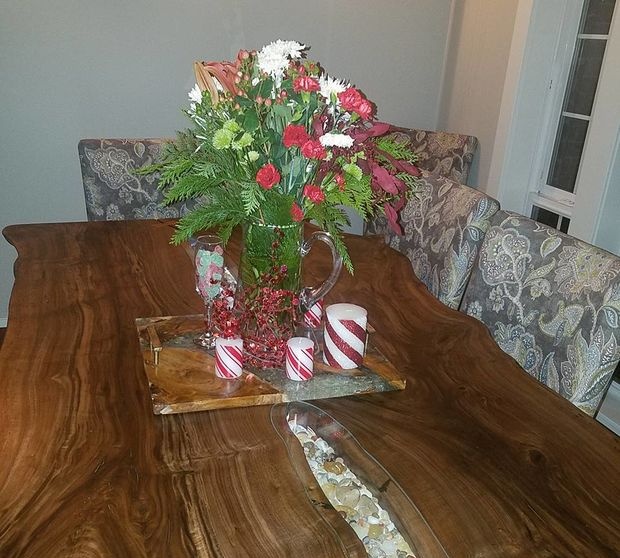
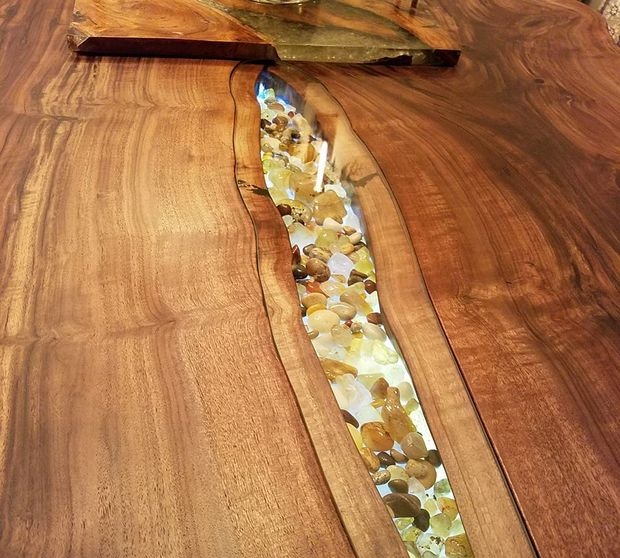
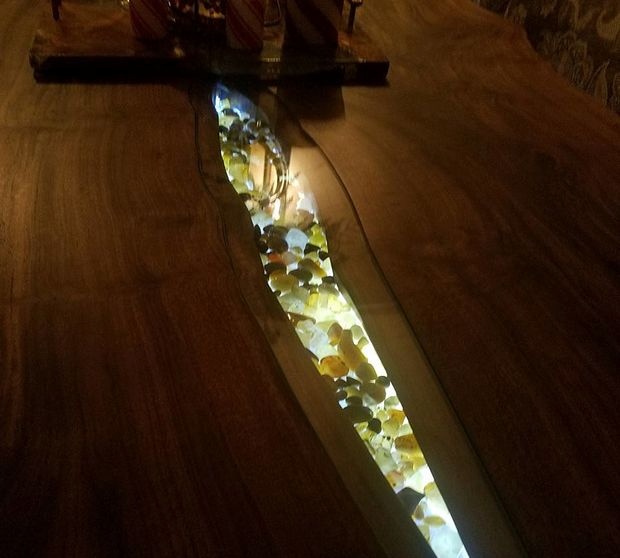
Kunden bor tre timer væk fra mig, så ved transport af bordet var det vigtigt at pakke det rigtigt. Jeg fjernede benene fra bænken og bordet og pakkede hver komponent for sig og forseglede den i plastikemballage.Det er vigtigt at pakke og pakke delene i den rækkefølge, de skilles ad, så når du sætter dem sammen igen, kommer de i den rigtige rækkefølge. Det bliver nemmere. For eksempel, da jeg ankom til en kundes hus, var det første, jeg skulle læsse af fra varevognen, bordpladen. Jeg stillede den på hovedet på gulvet i huset. De næste tilgængelige stykker var benene, som jeg satte fast på bordpladen. Så bænken, benene på bænken og så videre. Det kan virke som sund fornuft, men når du bliver revet med af pakning, er det nemt at glemme alt. Jeg filmede ikke denne proces, men jeg er sikker på, at det er ret nemt at forestille sig.
Kunden kunne rigtig godt lide spisestellet, og nu ligger hendes samling af agater i de oplyste fordybninger, i midten er der en buket til sæsonen, og rundt omkring er der et særligt udvalgt sæt stole. Det er på billedet. Et bord kan tilføje noget liv til et i forvejen sødt værelse. Jeg er glad for, at denne kreation kommer til et smukt hjem, hvor den vil blive beundret og plejet.
Tak for din opmærksomhed!
Originalartikel på engelsk
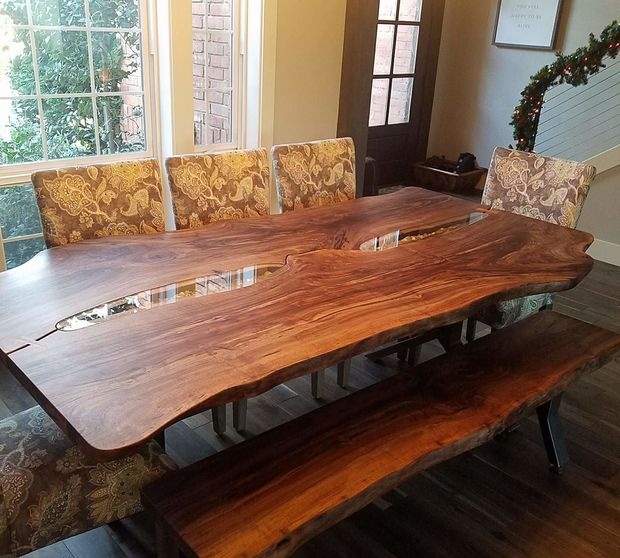
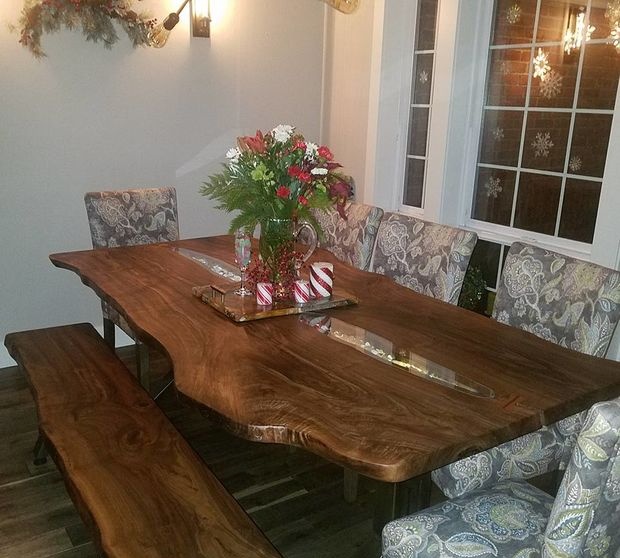
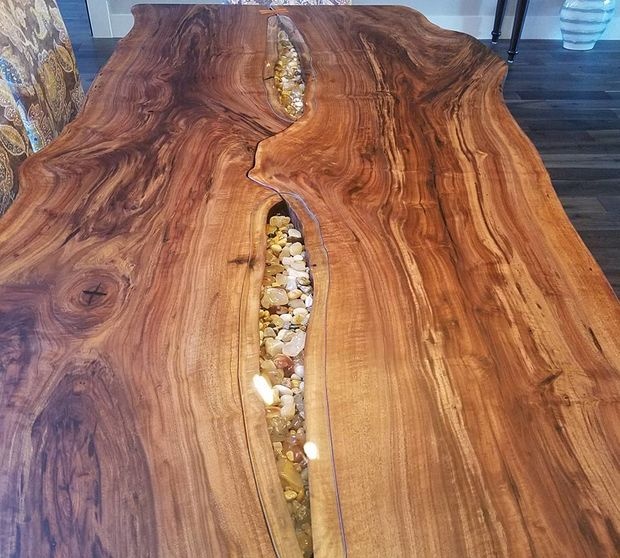


Det var meget sjovt at arbejde på bordet. Min kundes ordre var speciel (og interessant). Og som et incitament - budgettet. Hendes anmodning omfattede følgende punkter:
- - Bordplade med uskårne kanter på begge sider, bestående af to separate valnøddebrædder.
- - Masser af mønstre og kontraster.
- - Hulrum i midten til agatopsamling.
- - For at oplyse agaterne skal der være LED-belysning i hulrummet.
- - Hulrummene er dækket af aftagelige glasindsatser.
- - Bordplade mål 100 cm bred og 210 cm lang.
- - Specialfremstillede stålben (sorteret).
- - Én bænk i lignende stil.
- - Produktionstiden er ikke mere end en måned.
Jeg forsøgte at dokumentere hvert trin i processen, men deadlines var ret stramme, og nogle gange havde jeg ikke mulighed for at tage et billede. Beklager de manglende billeder; Jeg vil prøve at beskrive disse trin mere detaljeret...
Søg efter materiale
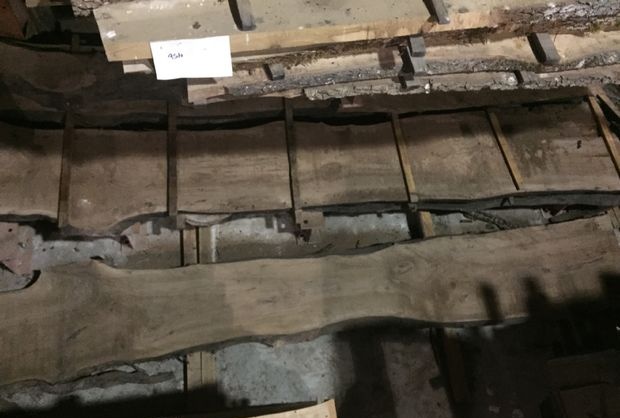
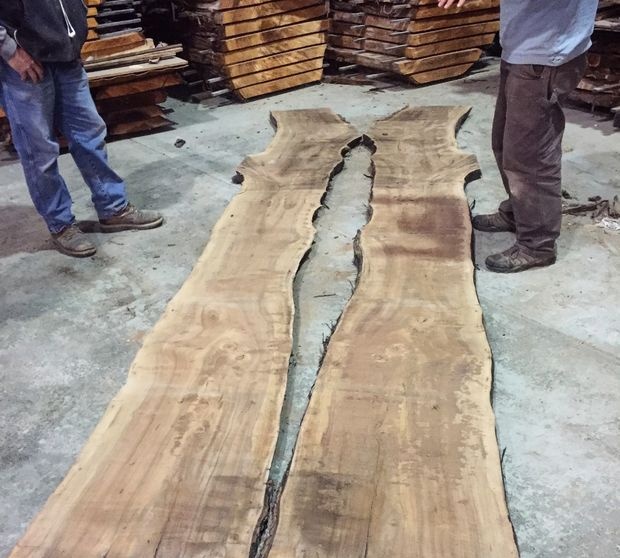
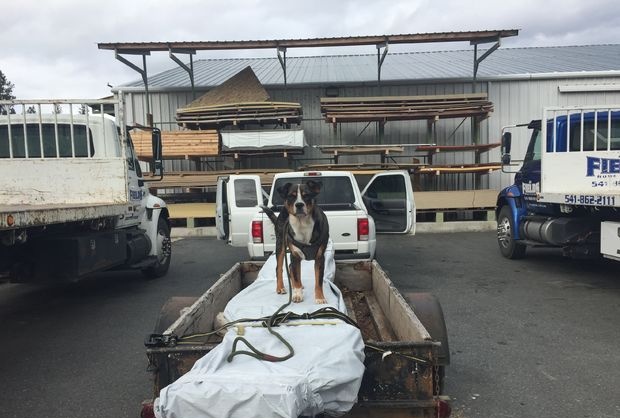
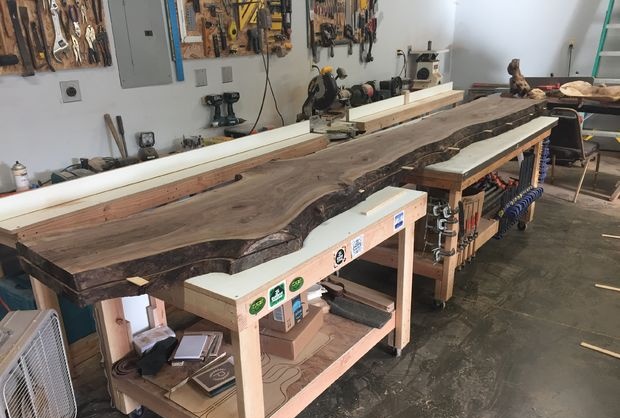
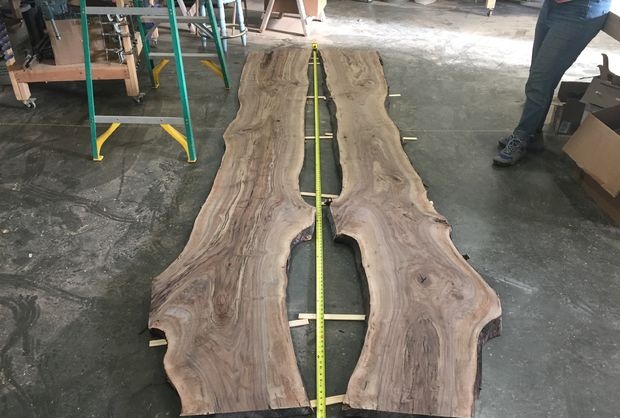
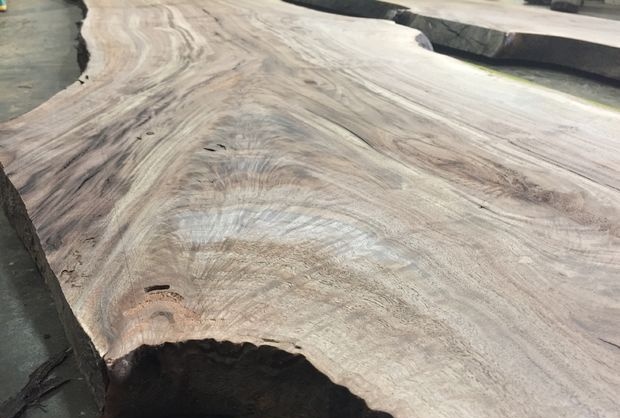
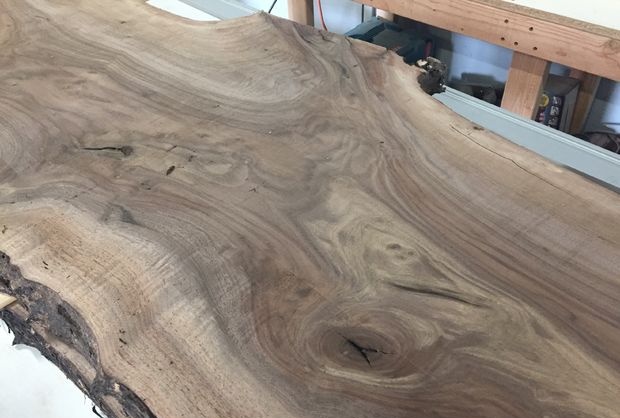
Jeg anser ikke denne fase for at være den vigtigste, men den kan vare ret lang tid.Meget tid, energi og benzin blev brugt på at besøge forskellige savværker og træværfter på jagt efter passende materiale. Dette virkede som noget af en bedrift i betragtning af breddekravene. Jeg skulle finde to brædder med rå kanter, og ved at placere dem side om side skulle den samlede bredde være de nødvendige 100 cm. Deres form skulle skabe hulrum for at kunne rumme kundens samling af agater. Brædderne skal have karakteristiske, udtalte mønstre. Der var også standardkrav: pladerne blev tørret i en ovn eller i et par år i luften, de havde et behageligt udseende, var flade uden unødvendige vridninger, vridninger eller snit (alt, der ville kræve at fjerne et lag af tykkelse) . Og prisen skal selvfølgelig være rimelig.
Søgningen begynder normalt med elektroniske rubrikannoncer i afsnittet "byggematerialer". Ofte tilbyder lokale håndværkere overskydende brædder til salg til rimelige priser. Butikker kan også sende annoncer i et forsøg på at tiltrække flere kunder. Jeg fandt et par anstændige muligheder i nærheden, men intet der passede til regningen. Bagefter besøgte jeg nogle lokale skovhuggere, der savede træstammer til planker. Disse fyre har ofte deres egne savværker og sælger brættet til en god pris, fordi de får træstammerne billigt eller gratis, og kvaliteten er ikke altid den højeste. Men denne mulighed virkede heller ikke, så jeg måtte videre til butikker og varehuse. Selvfølgelig er der allerede et valg her, men til en meget høj pris.
Jeg fandt endelig, hvad jeg havde brug for i en lokal butik. Ikke ligefrem i butikken. Det viste sig, at dens ejer har sit eget savværk og et lager fyldt med brædder med ukantede kanter.Han havde flere stakke nødder at vælge imellem. Her fandt jeg det jeg ledte efter. Brædderne havde den perfekte bredde, skåret af samme træstamme (symmetrien blev bibeholdt), tørret under de rigtige forhold i 3 år, pæne og flade, og prisen var forholdsvis billig. De kom med en bonus. Da de blev bearbejdet med et bredt plan, behøvede jeg ikke at slibe den ujævnt afskårne overflade. Jeg har ikke et 60 cm bredt fly...
Under søgningen sendte jeg billeder til klienten for at få hendes godkendelse. Vi besluttede os begge for disse to. Endelig kunne næste fase af projektet begynde!
Designudvikling og godkendelse
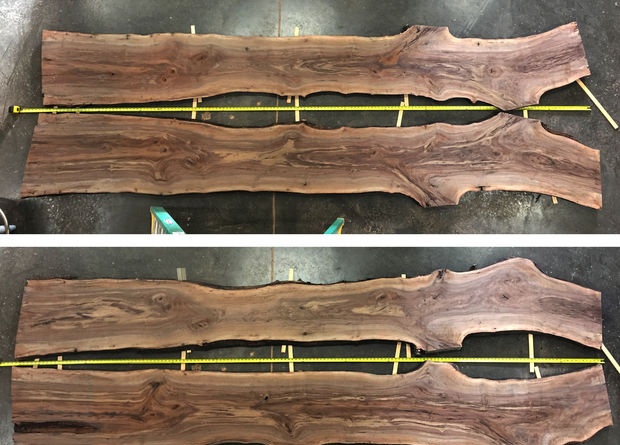
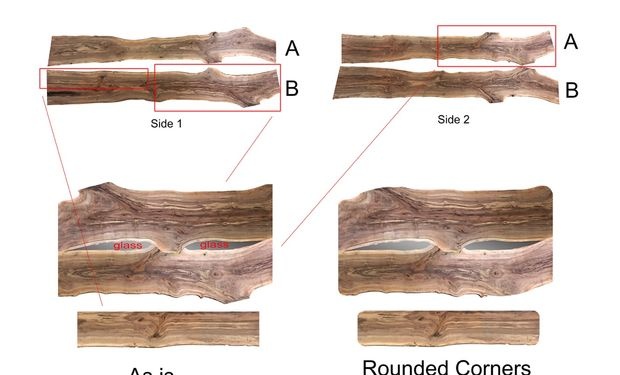
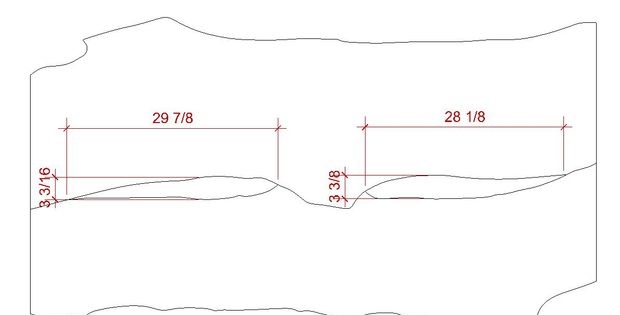
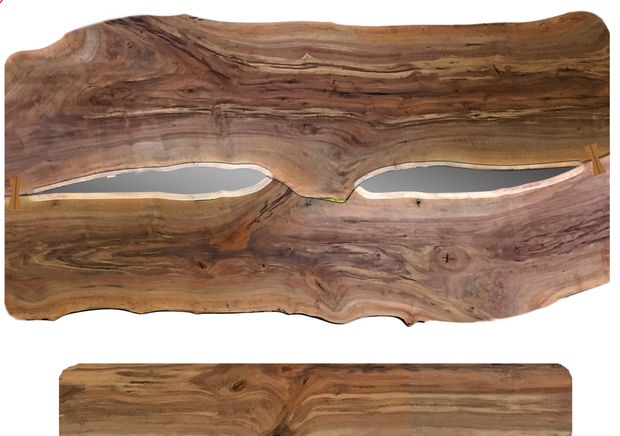
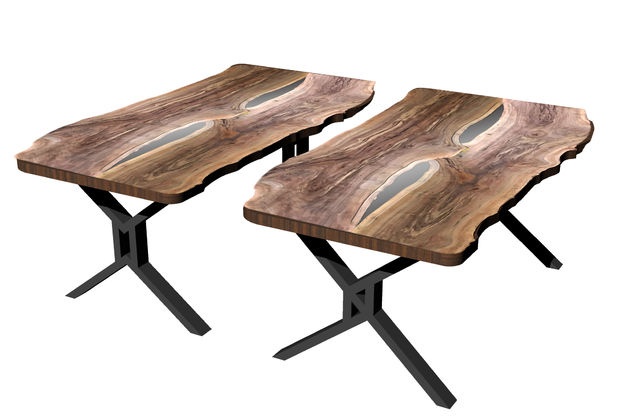
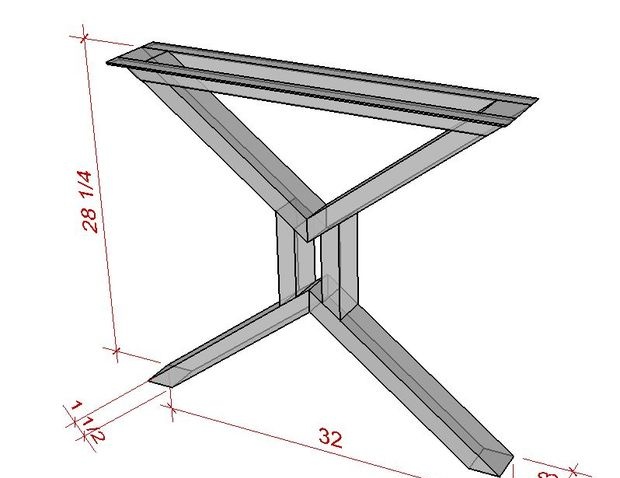
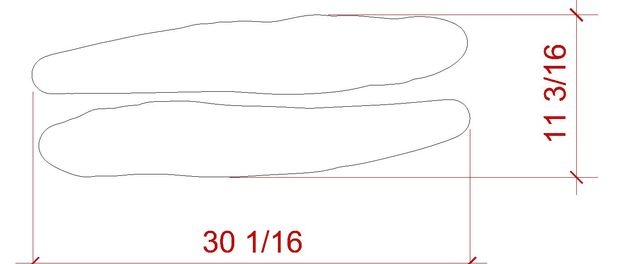
Før jeg henter et værktøj, starter næsten alle projekter, jeg laver, med et computerstøttet design (CAD). Dette er lidt sværere at gøre med rå kanter, da de er svære at replikere i CAD. Jeg løste problemet ved at installere en høj stige og tage billeder af brædderne i hele længden. Derefter importerede jeg billederne ind i programmet og sporede konturerne. Målebåndet var synligt på billedet for at hjælpe med at skalere grafikken mere nøjagtigt.
Efter at have designet de elektroniske modeller, overlejrede jeg dem med et rigtigt fotografi af overfladen af pladerne, så det ville være lettere for kunden at forestille sig, hvad jeg skulle lave. Da vi besluttede designet, designede jeg de forskellige elementer, og hvordan de ville interagere og knytte sig til hinanden.
Til dette projekt vektoriserede jeg forskellige projektioner af modellen til alle mulige formål. Jeg tegnede konturerne af de centrale hulrum og eksporterede dem til en DXF-fil, som jeg derefter sendte til et glasfirma for at få dem skåret de samme former ud til mig.Jeg brugte den samme fil til at lave en skabelon med omridset af hulrummet, hvorefter det vil være muligt at skære polycarbonatpladerne ud, som skal fastgøres på undersiden af bordpladen. Jeg skar skabelonerne og polycarbonatet på min hjemmelavede CNC-router. Jeg skar også en skabelon ud for at holde metalbenstykkerne på plads, så jeg kunne svejse dem ordentligt. Jeg har endda laserskåret profiler af forskellige metaldele, som vil hjælpe mig med at skære bendelene i den rigtige vinkel. Efter at have designet en komplet model i CAD, kan du begynde at arbejde, eller i det mindste bliver det meget nemmere at arbejde med.
Klargøring af brædder (udfyldning af revner, fiksering af knaster, slibning)
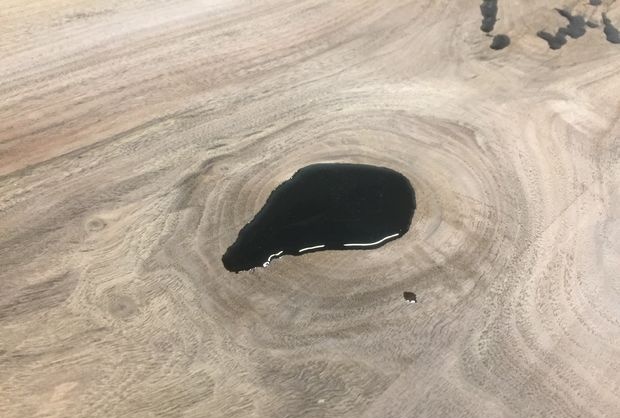
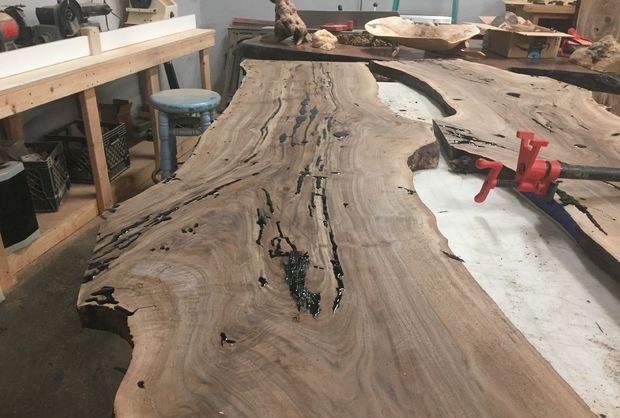
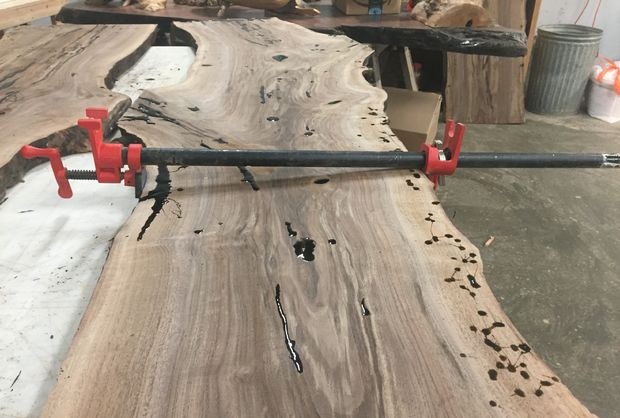

I de fleste tilfælde kan jeg godt lide at få alle knaster, revner og hulrum forseglet og fyldt med sort epoxy, især når man arbejder med valnød. Sort farve ser oftest naturlig ud og tilføjer nogle gange kontrast. Da der var ret dybe revner hist og her i brædderne, brugte jeg en harpiks med lang hærdetid; dette vil give det mulighed for at suge godt ind og hjælpe med at forsegle revnerne i stedet for at skabe en illusion af fyldning. Ulempen ved denne metode er, at du næsten altid skal påføre harpiksen en anden, og nogle gange en tredje gang. Nogle gange bruger jeg en harpiks med en hurtig hærdetid til efterbehandling. Jeg udfyldte alle hulrummene på begge sider af brædderne, så de kunne holdes sikkert på plads. Det er bedre at påføre epoxyharpiksen i en "dynge", så der ikke findes bobler under slibning (så de vil stige over brættets plan).
Efter at have fyldt alle hulrummene sleb jeg de udsatte dele af epoxyen ned med et P60 slibemiddel.
Formning af samlinger
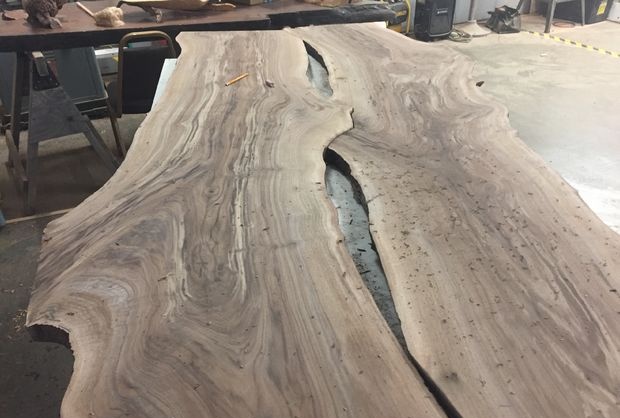
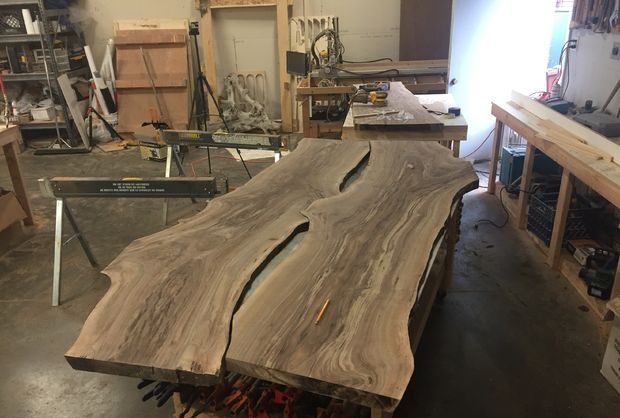
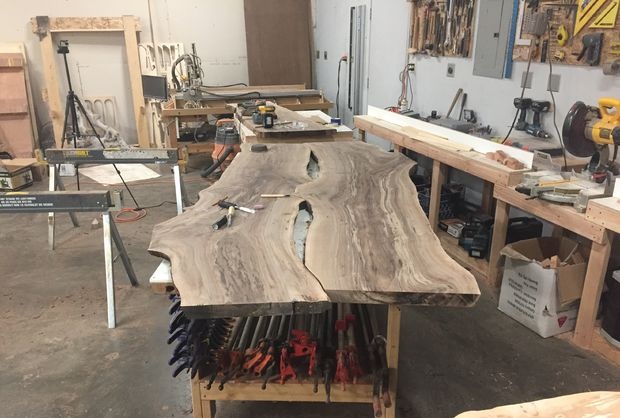
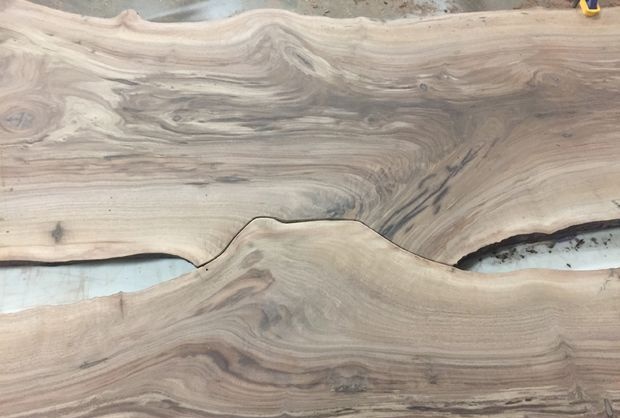
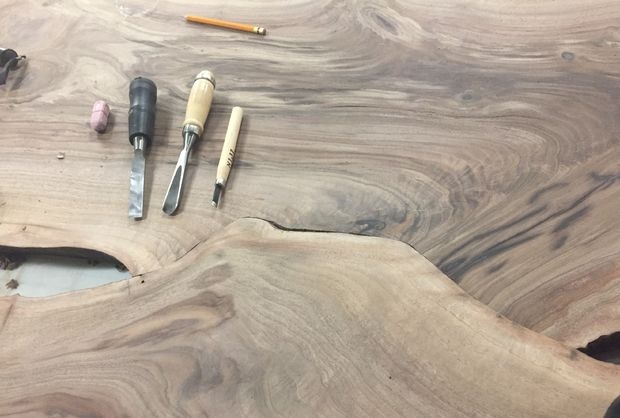
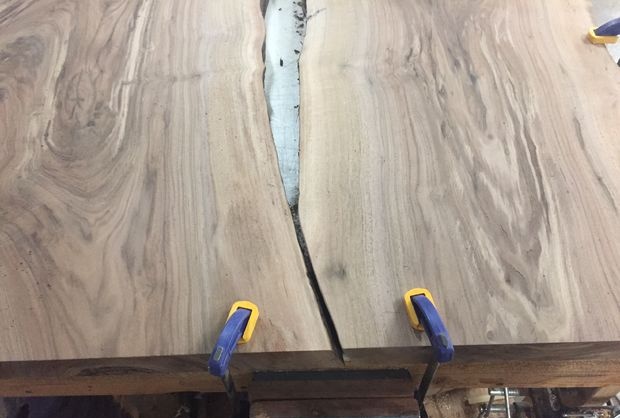
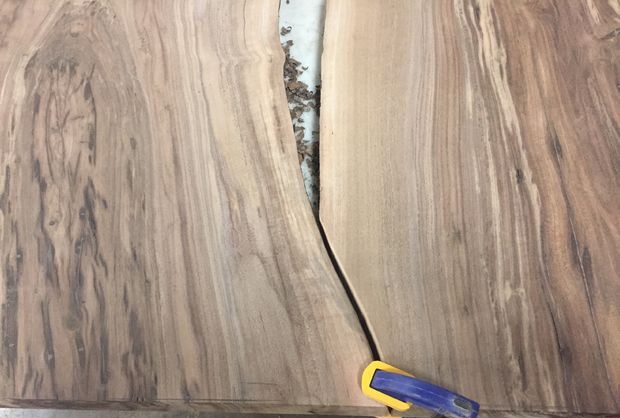
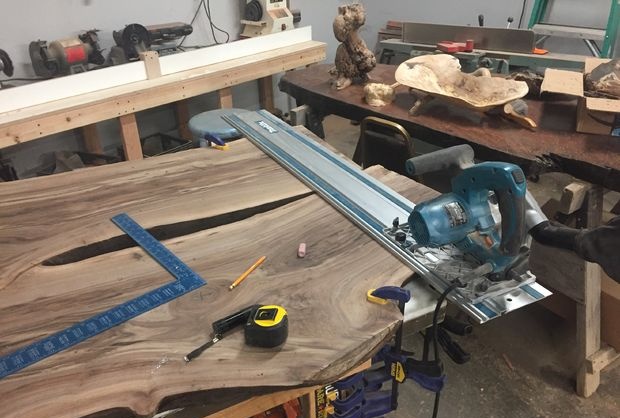
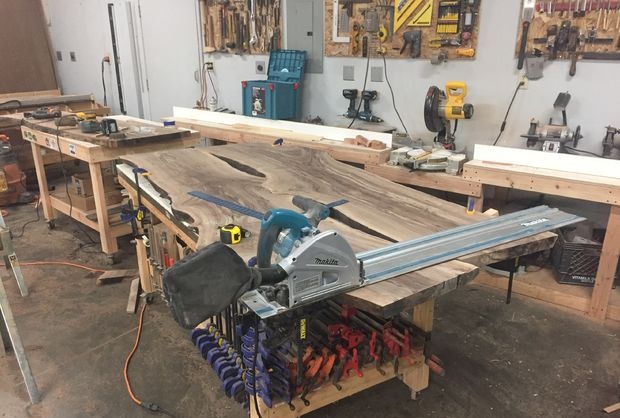
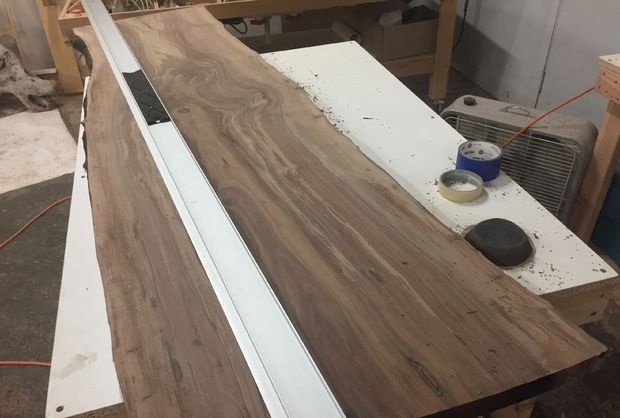
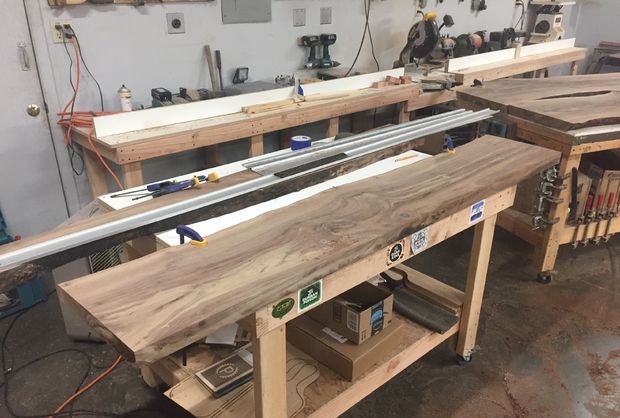
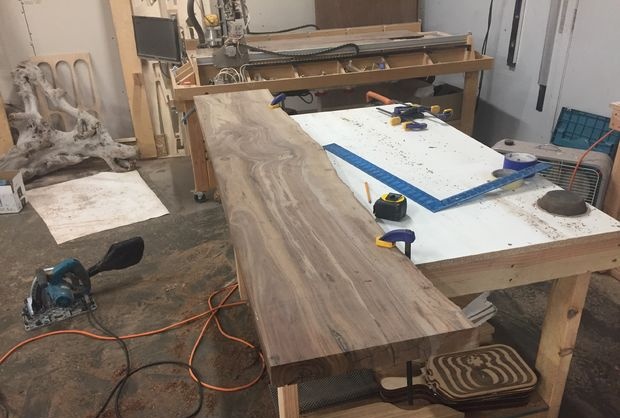
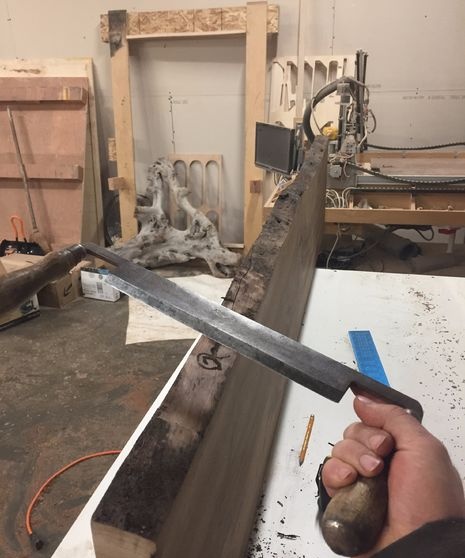
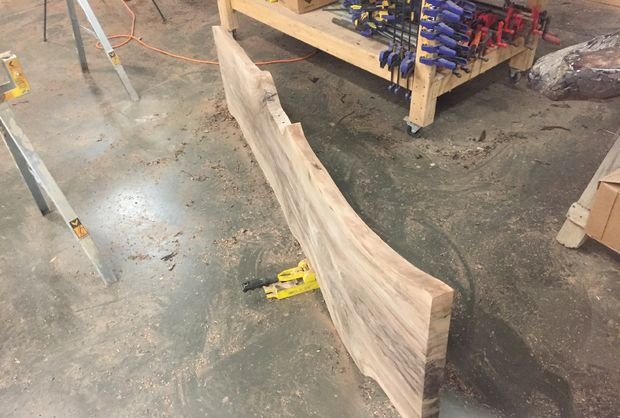
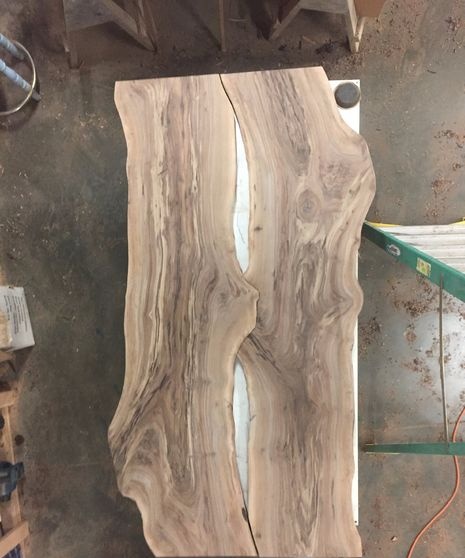
Desværre dokumenterede jeg ikke rigtig denne fase. I det væsentlige lagde jeg et bræt oven på et andet i den ønskede position og markerede det område, der skulle fjernes. Til selve arbejdet brugte jeg en stiksav, en vinkelsliber (med skæreskive og en klapskive) og eventuelt håndværktøj til træskærerarbejde. Der var meget fint arbejde og tilpasning på dette tidspunkt. Jeg efterlod en søm ca. 4 millimeter tyk langs hele længden mellem brædderne. Jeg troede, at bordet ville se mere udtryksfuldt ud på denne måde. På den negative side efterlader en sømløs pasform hjørner, hvilket ikke er et godt udseende. Tykkelsen af sømmen vil blive bibeholdt takket være svalehalenøglen. Jeg glattede derefter bordets kanter ud med en rundsav.
Under dette trin skrabede jeg de rå kanter fri af eventuel resterende bark på både bordet og bænken. Jeg gik så over dem med en vinkelsliber med klapskive for at få de ru kanter glattere.
På bænken skar jeg den ene rå side med en rundsav. Jeg aftalte med kunden, at bænken ville have den ene side lige.
Forbindelse af brædder ved hjælp af dyvler og dyvler

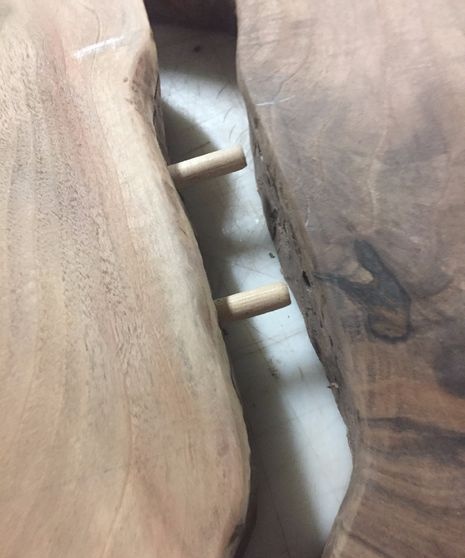
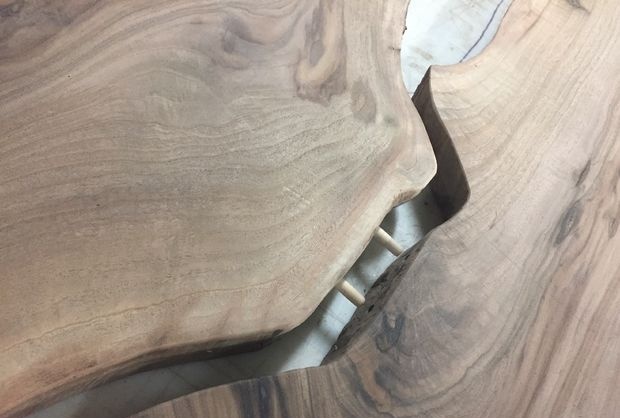
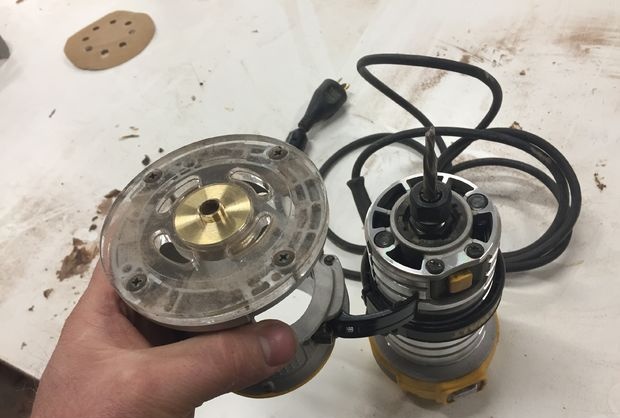
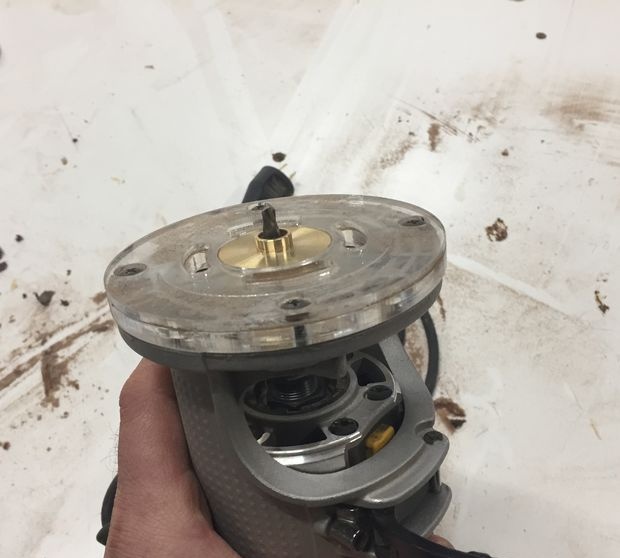
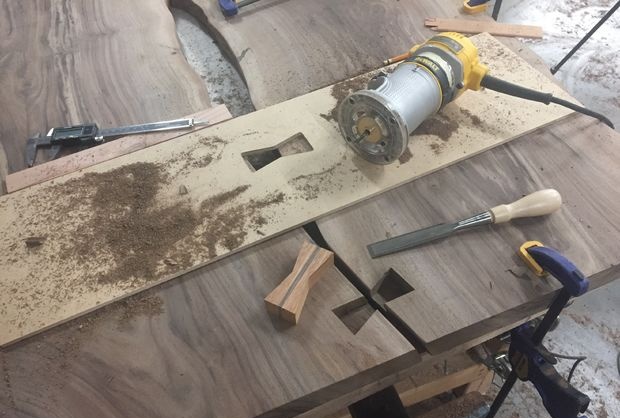
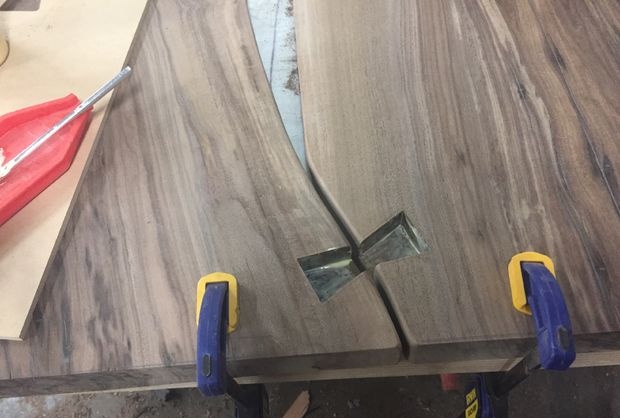
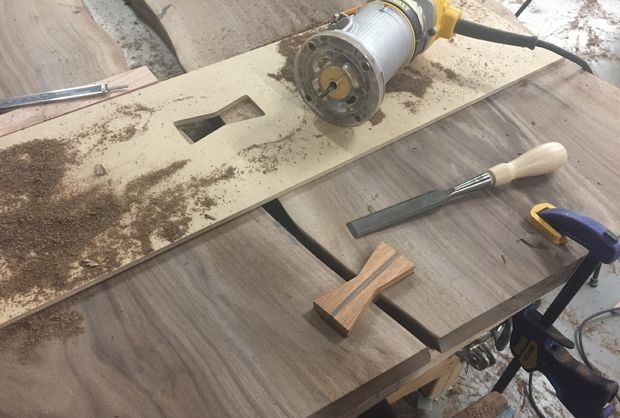
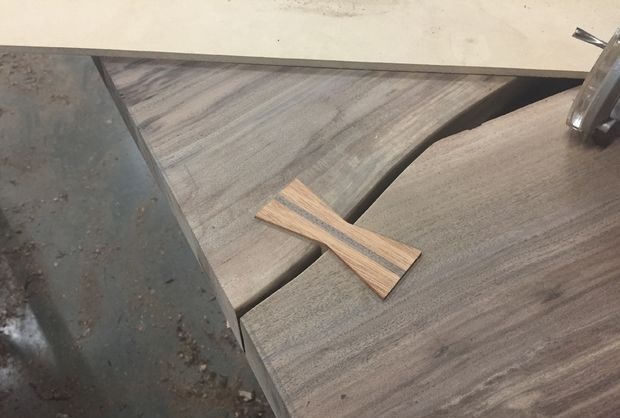
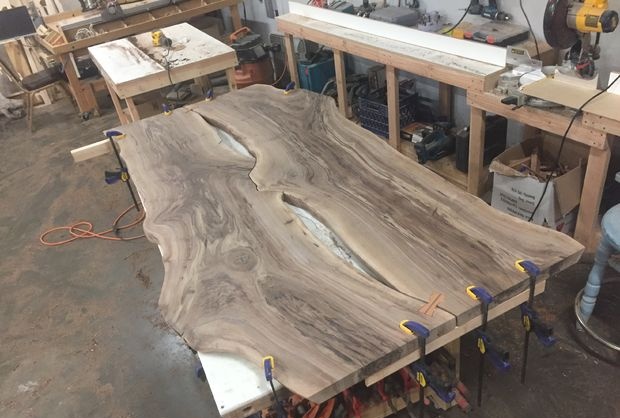
Jeg brugte dyvler til at forbinde de centrale dele. De tjener til at fastgøre to brædder i samme plan (i forhold til hinanden). Hovedbelastningen ved fastgørelse af bordpladen vil falde på bordets dyvler og ben. I modsætning til de dyvler, som jeg har set, lavede jeg disse med en tykkelse næsten lig med tykkelsen af brædderne.
Materialet til dyvlerne blev lavet ved at lime et ark valnød mellem to plader mahogni og en CNC-maskine skar formen ud. Jeg har også lavet en skabelon til at hjælpe dig med at skære dyvelåbningerne ud med en håndfræser.
Efter at have justeret sømmen mellem brædderne, fastgjorde jeg dem til bordet ved hjælp af klemmer. Så ved hjælp af en skabelon skærer jeg rillerne ud med en overfræser. Hvor overfræseren forlod rillen rundt, skulle jeg arbejde med en mejsel. Du kunne have lavet en afrundet svalehale, men jeg kan godt lide udseendet af lige hjørner.
Da svalehaleåbningerne var klar, prøvede jeg forsigtigt at indsætte svalehalen (for at sikre mig, at den ikke satte sig fast!) og begyndte at lime. Dyvlerne var lavet lidt tykkere end rillerne, så de blev slebet i plan med bordpladen.
Efter dette trin var afsluttet, sleb jeg alle overflader fra P60 til P180 korn. En sidste slibning med P220 korn blev udført umiddelbart før polering.
Indsættelse af glas, polycarbonat og LED-belysning
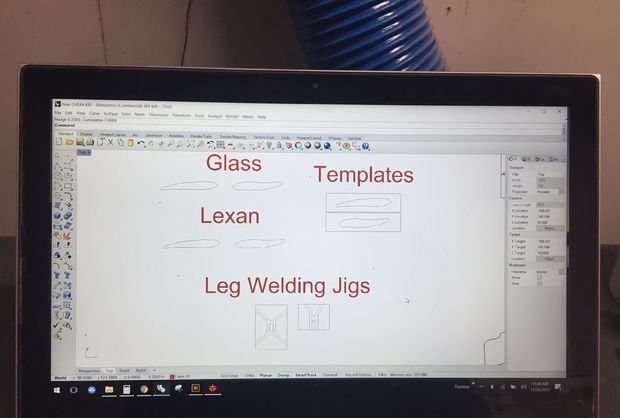
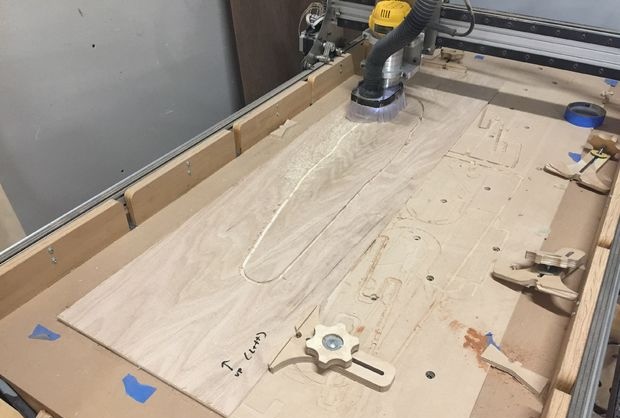
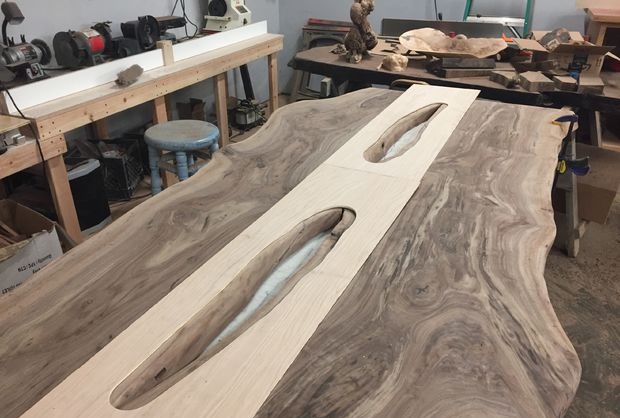
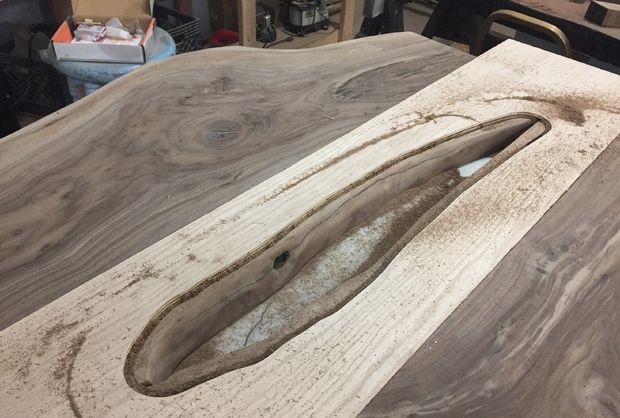
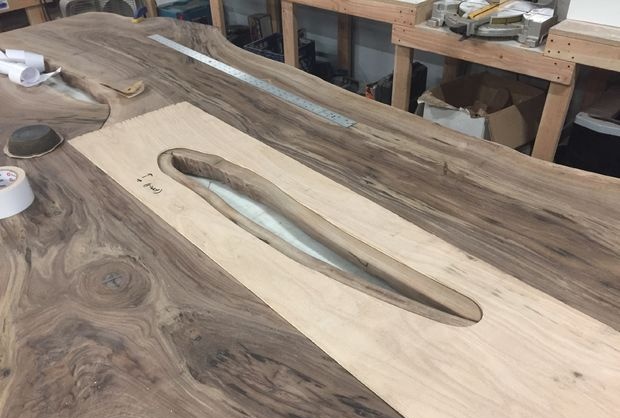
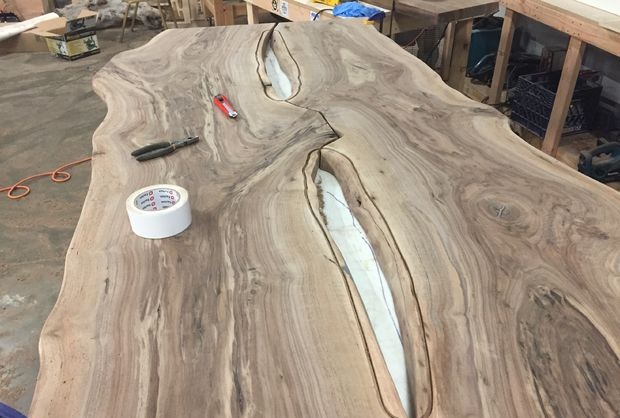
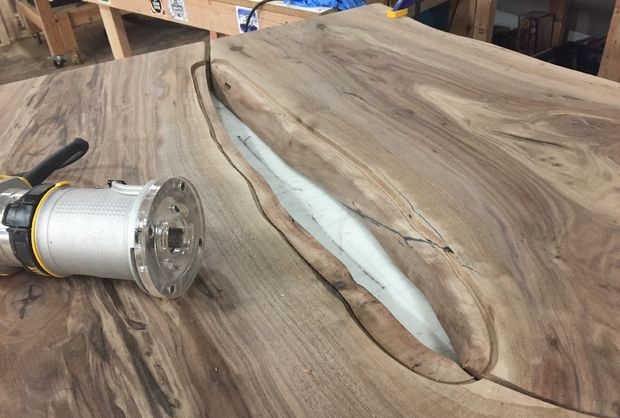
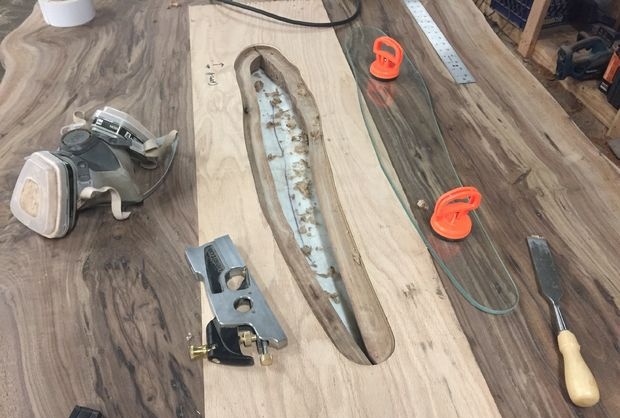
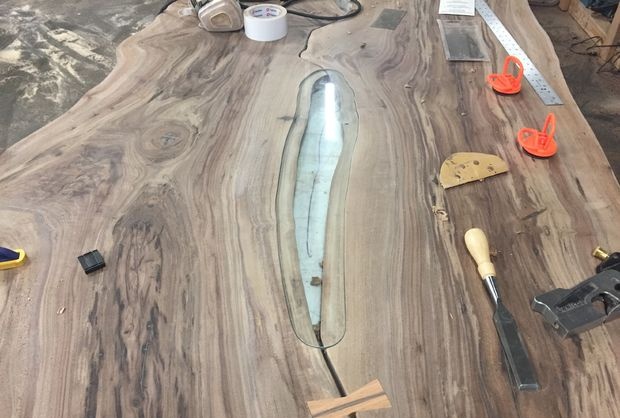
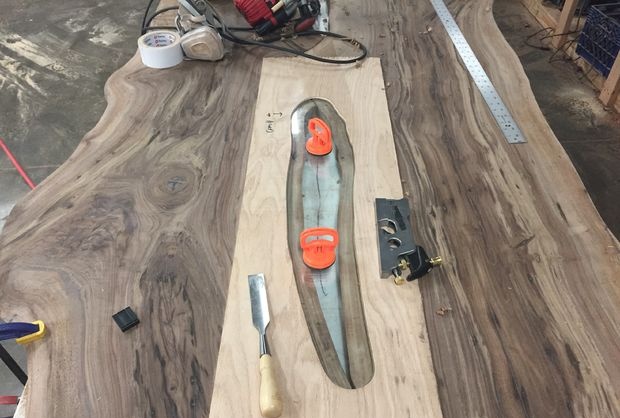
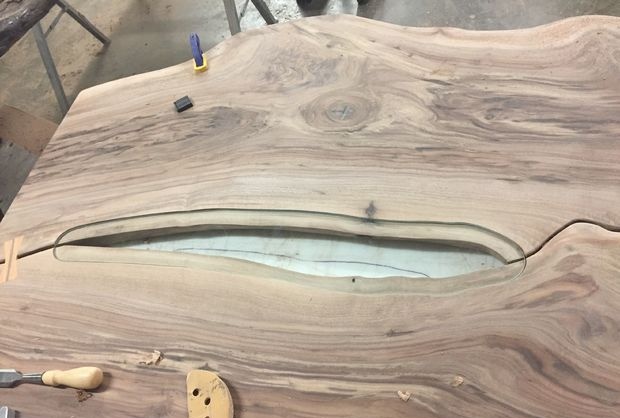
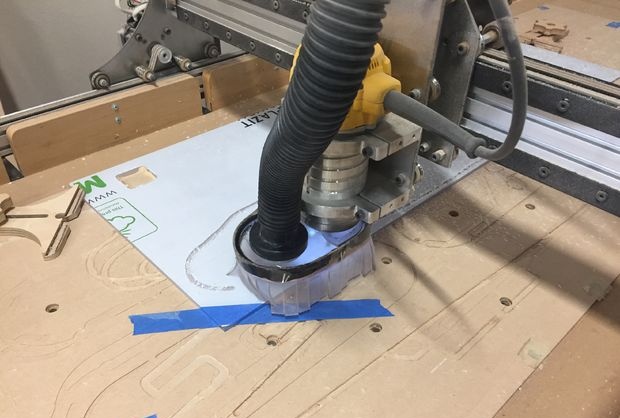
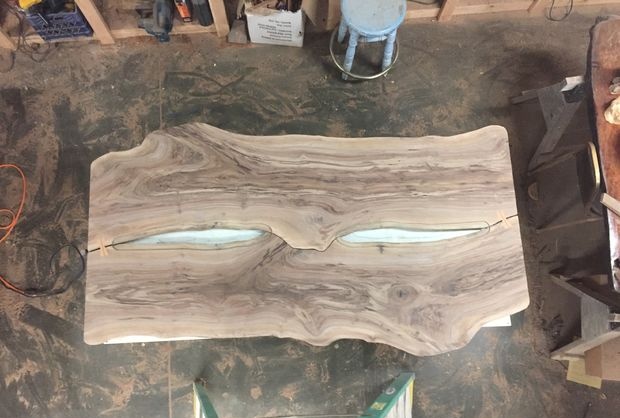
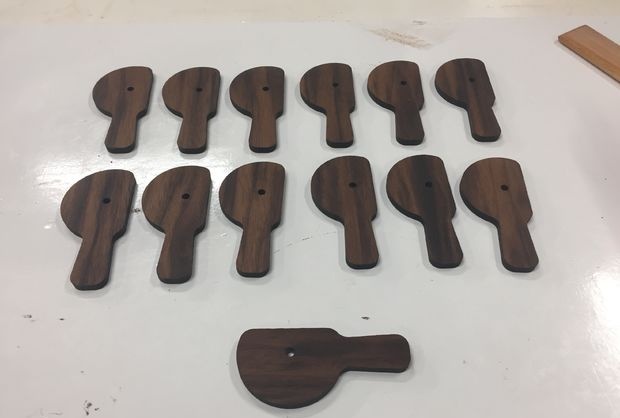
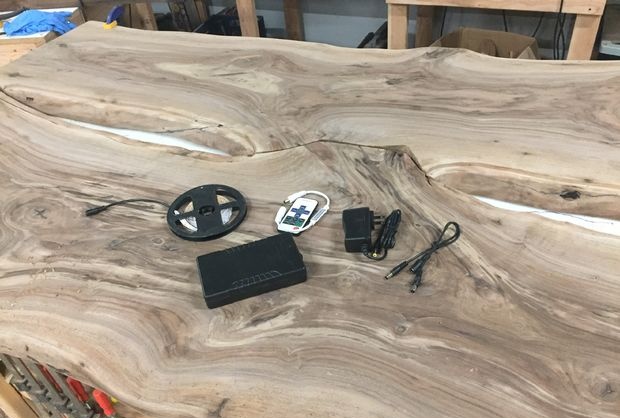
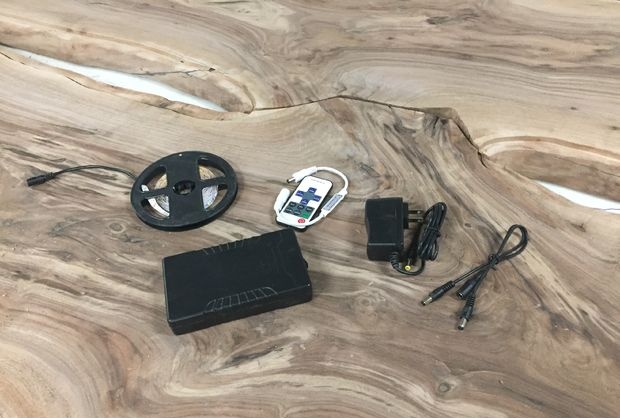
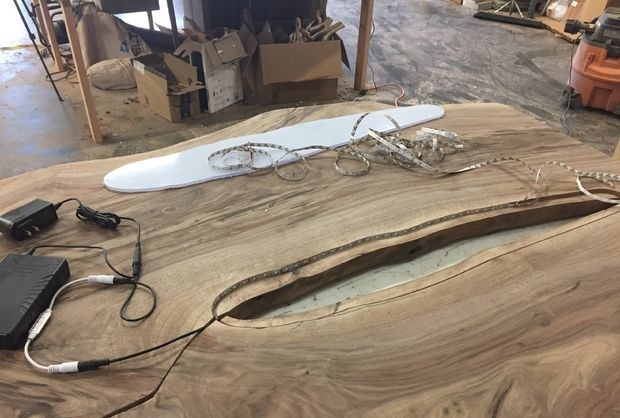
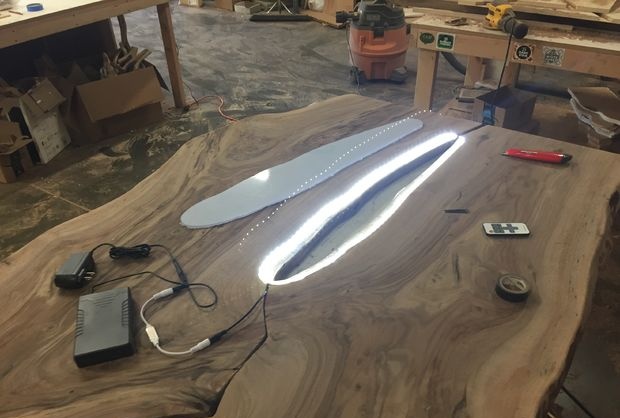
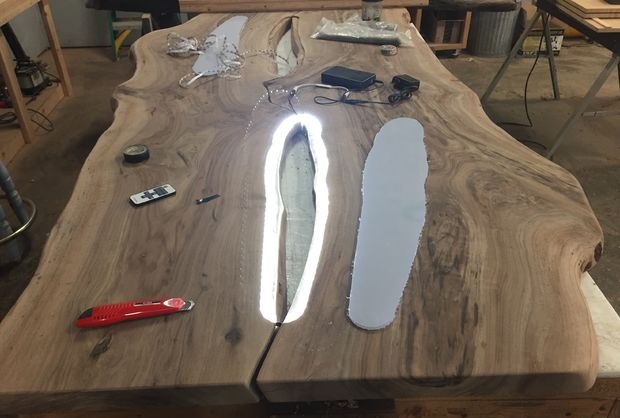
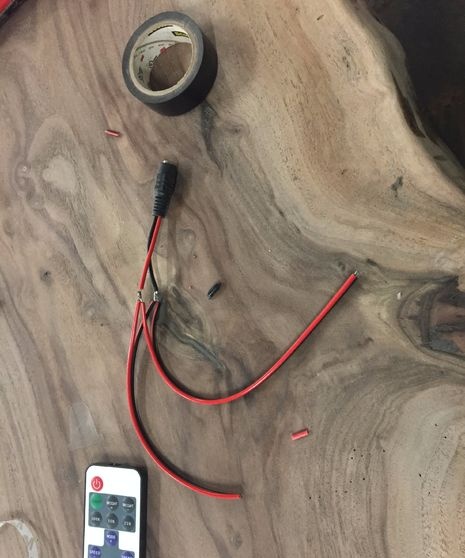
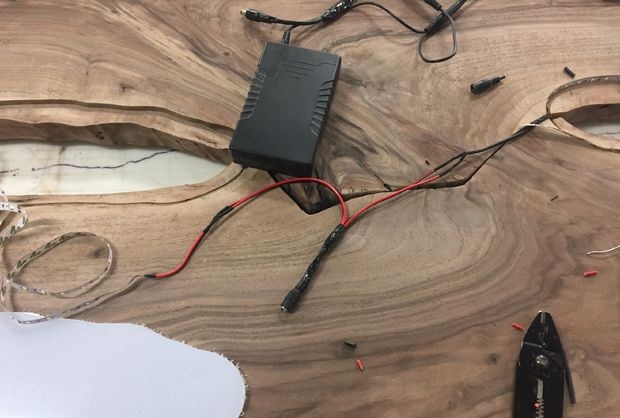
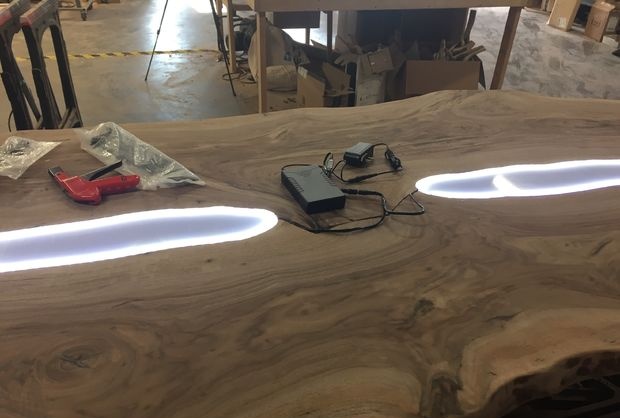
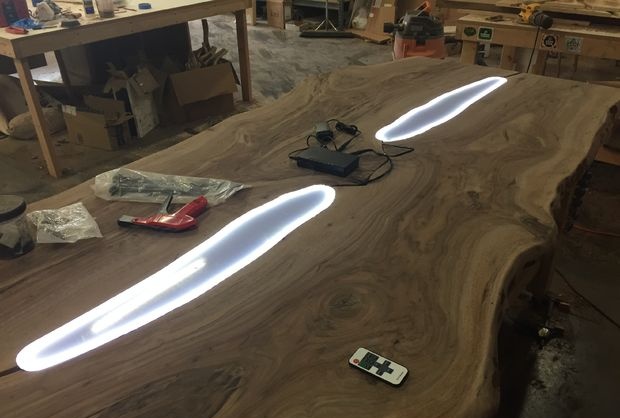
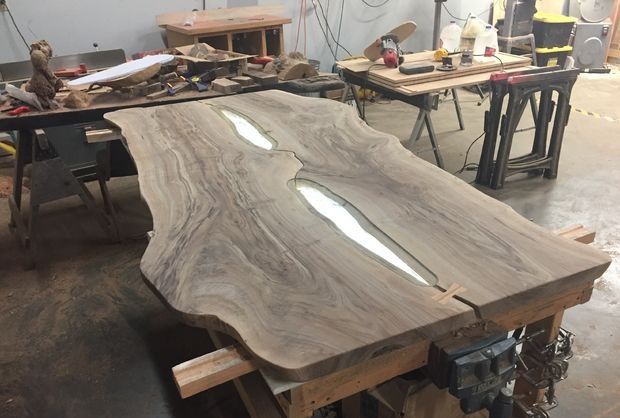
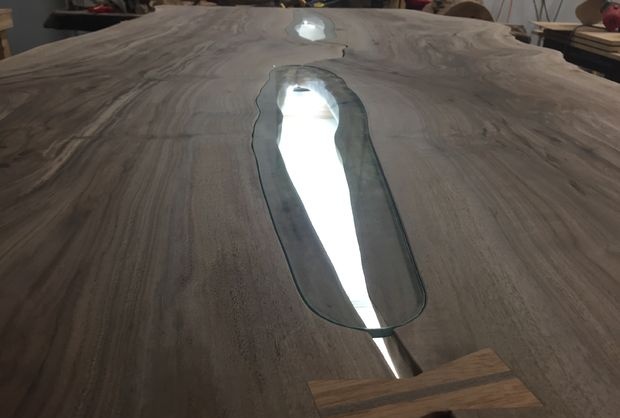
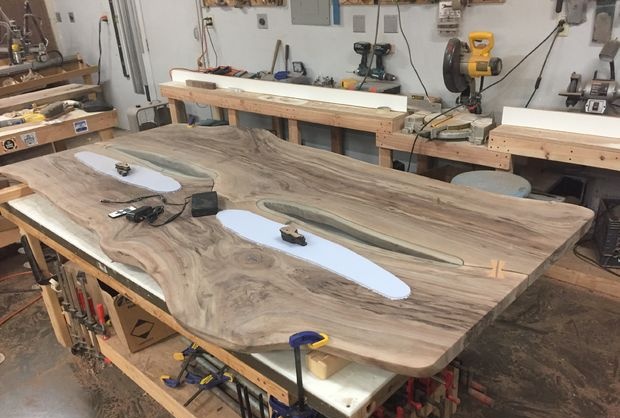
Jeg brugte CAD-modellen til at skabe glasindsatserne og polycarbonatpladen. Dobbeltklæbende tape er perfekt til midlertidig fastgørelse af emner på bordoverfladen. Jeg brugte så håndfræseren igen til at lave rillerne på begge sider af brædderne. For mere præcist arbejde brugte jeg en mejsel og en mejsel, indtil glasset lå fladt og fikseret uden at vakle. Glasset blev fjernet og sat i mange gange, hertil brugte jeg sugekopper.
Polycarbonatpladeindsatserne blev fremstillet ved hjælp af en CNC-maskine og en endefræser. Her skulle jeg tage en beslutning om, hvordan plastindsatserne sikres mere sikkert i bunden af bordpladen. Jeg ville have dem til at være nemme at fjerne, for eksempel at erstatte dem på grund af ridser. Jeg besluttede, at låseflag af valnød ville være det helt rigtige. Så jeg laserskar dem ud af det materiale, jeg havde.
Før jeg indsatte plastikken, skulle jeg finde ud af LED-belysningen. For en mere sofistikeret effekt besluttede jeg at placere LED-belysning rundt om plastikkens omkreds. Denne teknik hjælper også med at skjule ledningerne. Jeg købte en tynd LED-strimmel med en klæbende side, der nemt kan klæbes til den fordybning, jeg lavede tidligere omkring bunden af hulrummet. Jeg var nødt til at bygge to separate Y-formede elektriske kredsløb, der derefter ville føres ind i en separat lysdæmper. Lysdæmperen er tilsluttet batteriet på den ene side og til en 12-volt strømforsyning på den anden. Dette gør, at lamperne kan lyse både fra batterier og fra lysnettet. Ideen er, at husejere skal tilslutte opladeren, når de ikke bruger skrivebordet, så ledningerne kan gemmes væk, når de kommer i vejen. Ledningerne og batteriet blev fastgjort til bunden af bordpladen ved hjælp af klemmer og ankre. Jeg overvejede muligheden for at indlejre batteriet og ledningerne i træet, men besluttede til sidst, at det var bedre at lade være, da alle disse komponenter skal udskiftes på et tidspunkt. I slutningen af dagen skulle dette bord være et arvestykke, der vil overleve mig, kunden og LED-lysene. De siger, at LED-lamper kan holde ret længe, men hvis lysten melder sig, kan de udskiftes med noget lignende.
Efter at have prøvet plastikken og tjekket belysningen lagde jeg pladerne til side. Låseflag og plast kan påsættes efter polering.
Polering
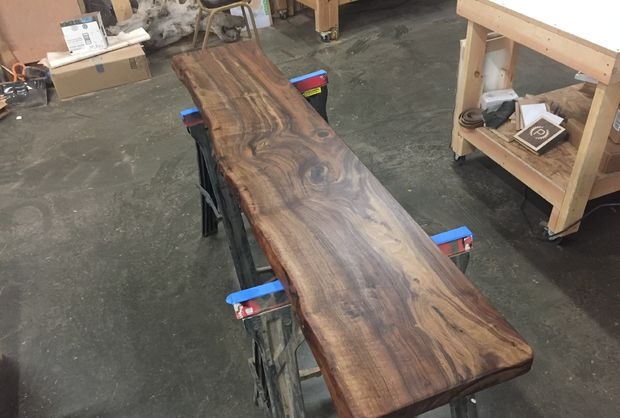
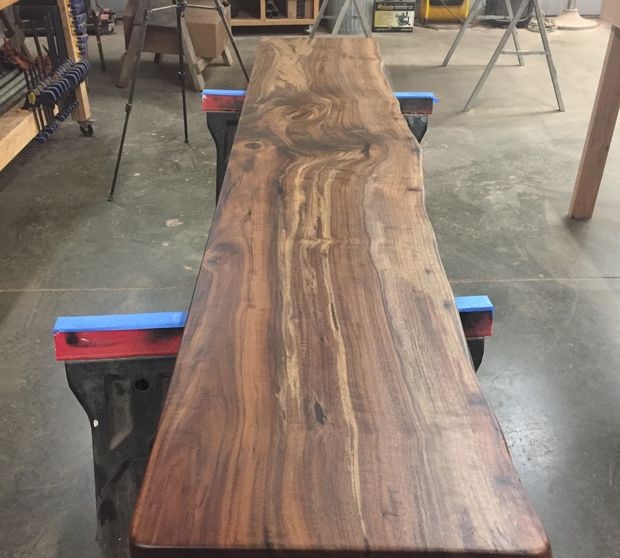
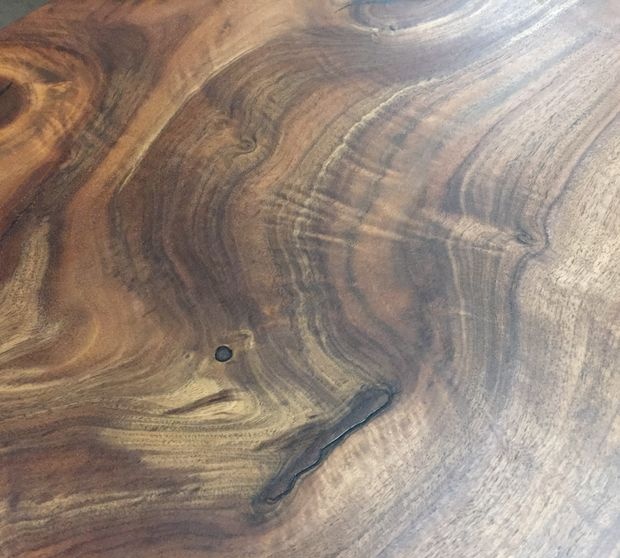
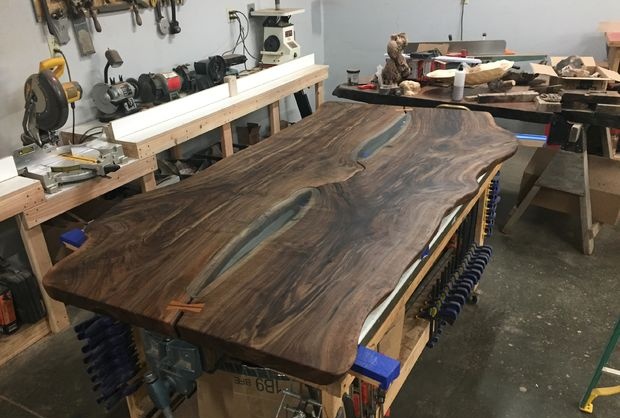
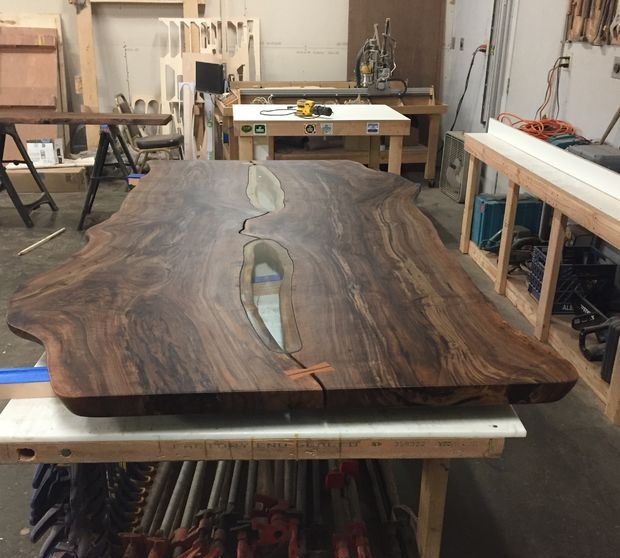
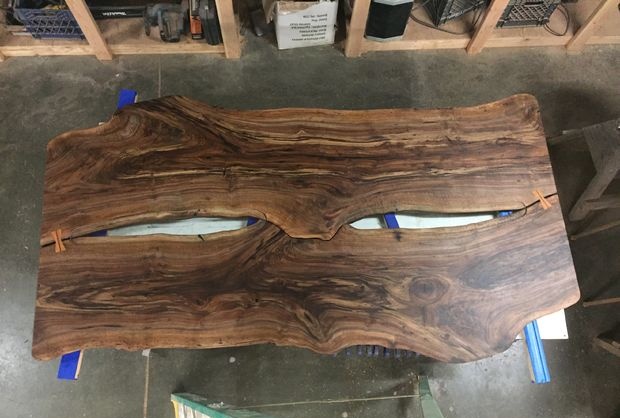
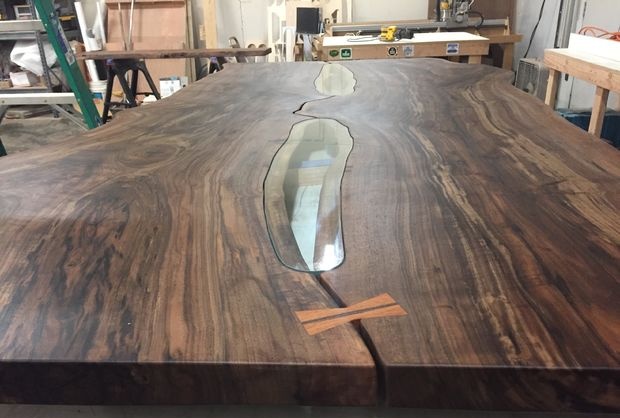
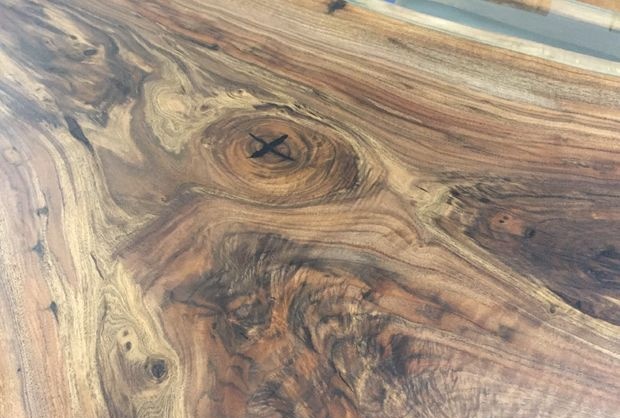
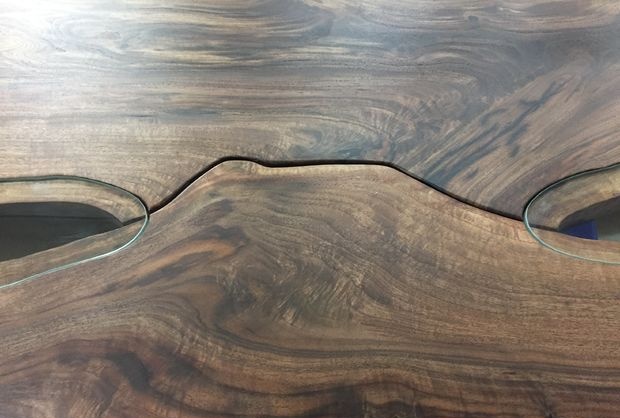
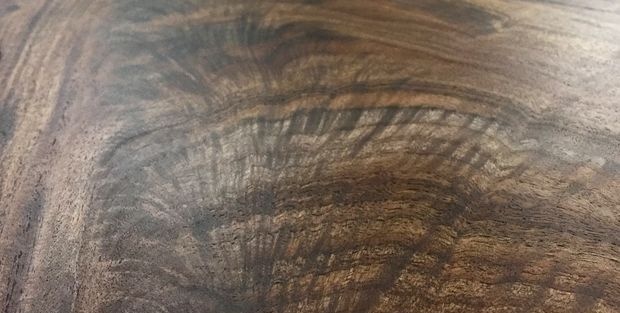
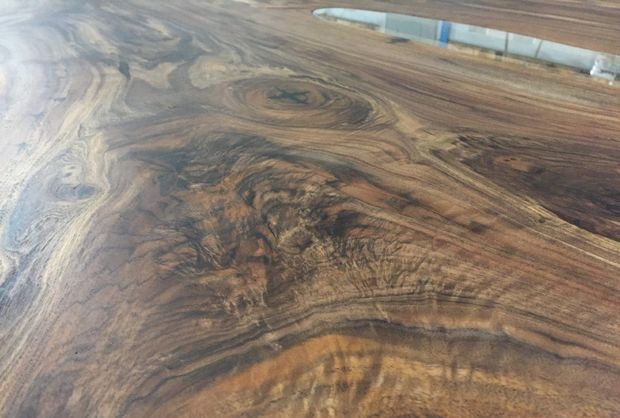
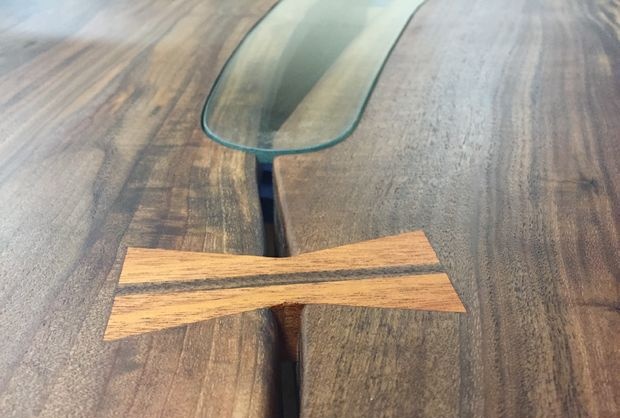
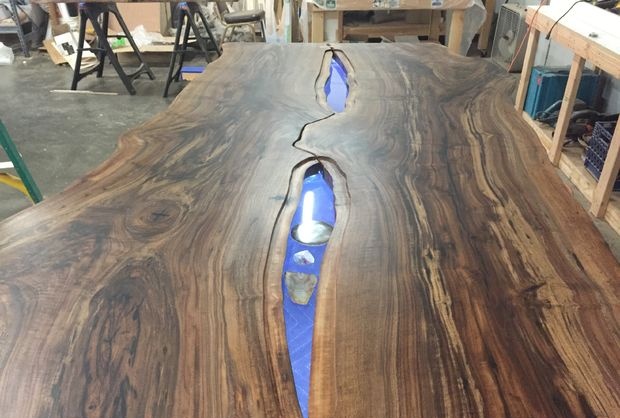
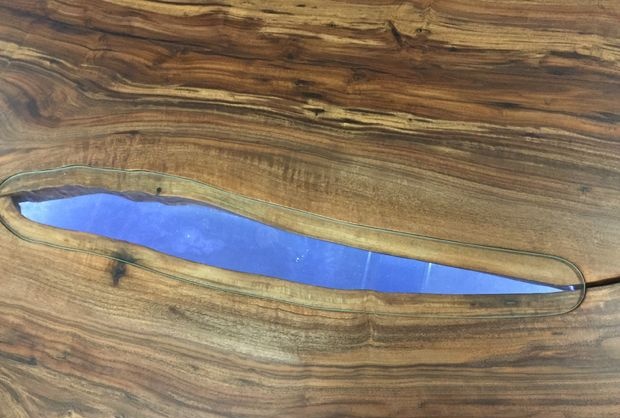
Kunden ønskede at bruge et poleringsmateriale, der ville bevare træets naturlige udseende, gøre det holdbart, men ikke ligne lak. Så jeg valgte OSMO PolyX. Dette produkt er designet til trægulve, men også til møbel det passer godt.Den har et lavt VOC-indhold og et højt faststofindhold, da det primært er sammensat af voks og naturlige olier. Det er nemt at anvende. For at opnå et godt resultat er to lag nok.
Jeg tog ingen billeder af denne proces, fordi jeg altid havde gummihandsker på med polerpasta. Inden jeg lagde lag, gik jeg igen over overfladerne og kanterne med en P220 korn.
Jeg brugte en spatel til at påføre OSMO jævnt på overfladen. Det var nemt for dem at fugte træet fuldstændigt og dække alle de små ujævnheder med pastaen. Jeg skulle bruge stof på kanterne. Efter fugtning fjernede jeg den resterende pasta med en fnugfri klud. På dette stadium er det vigtigt at bearbejde overfladerne grundigt, men helt fjerne overskydende. Jeg beklædte toppen, bunden og alle kanterne af bordet og bænken og lod dem tørre i en dag eller to, og så gjorde jeg det hele igen. Kun to lag er nok, og faktisk kan påføring af flere resultere i en uønsket blank effekt.
Som et resultat blev behandlingen af trædelene afsluttet, jeg lagde polycarbonatpladerne på plads og fastgjorde dem med flagklemmer.
Oprettelse af ben og montering af dem
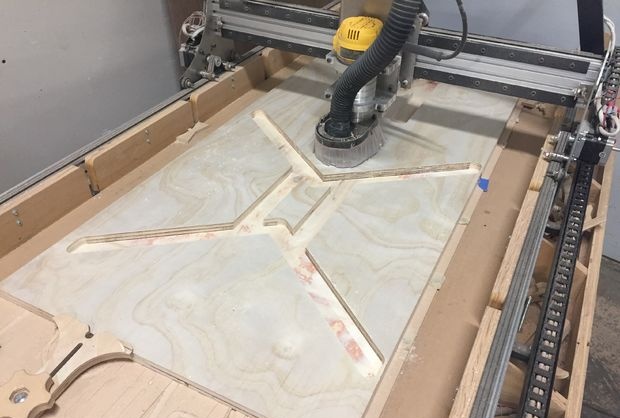
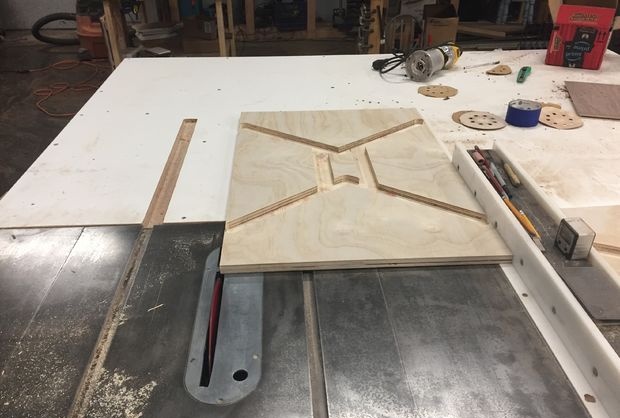
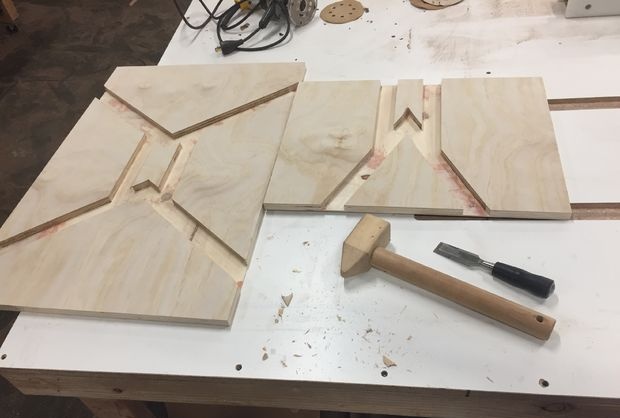
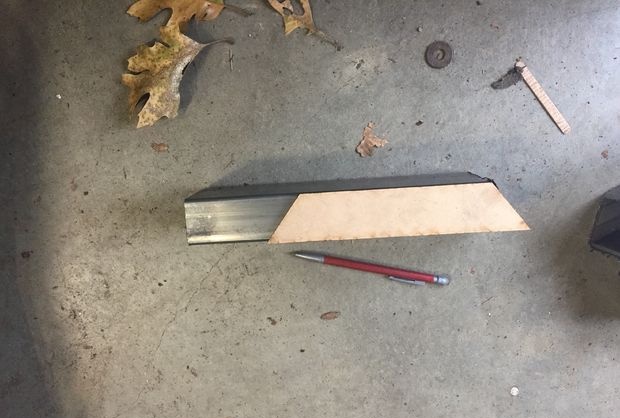
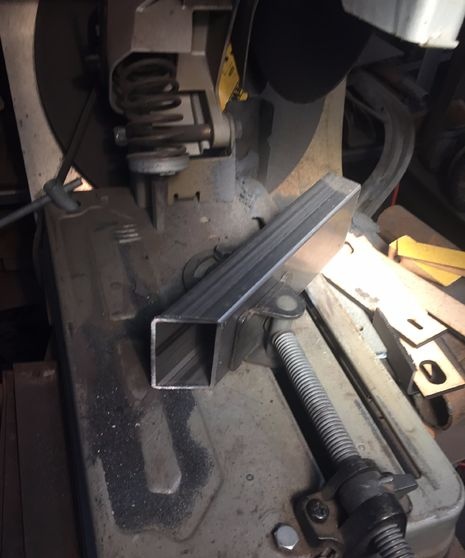
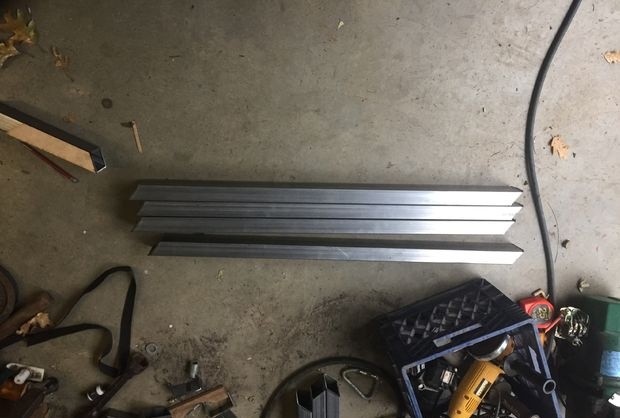
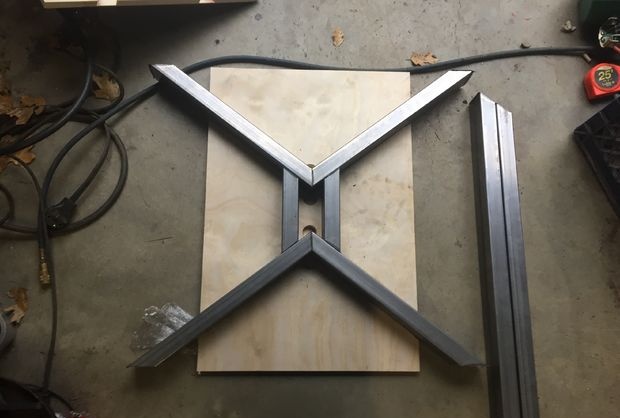
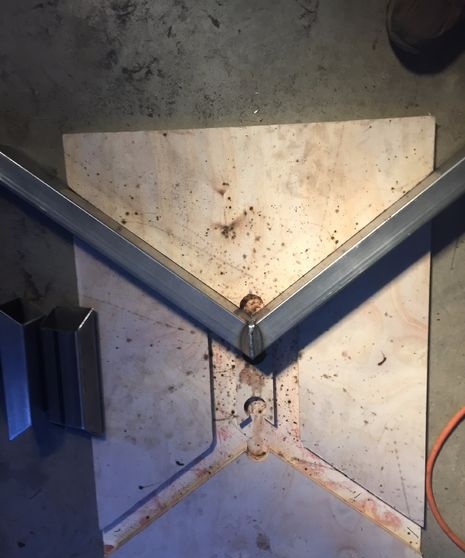
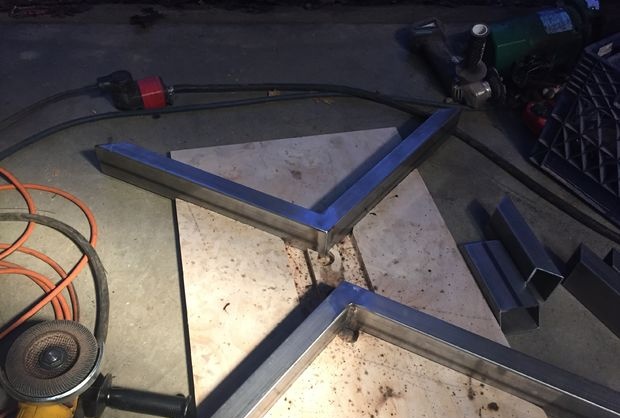
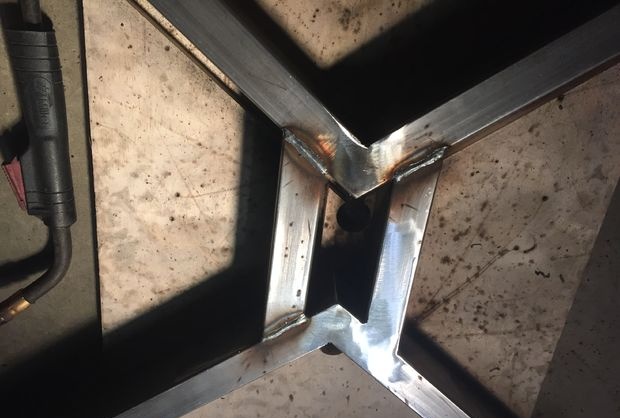
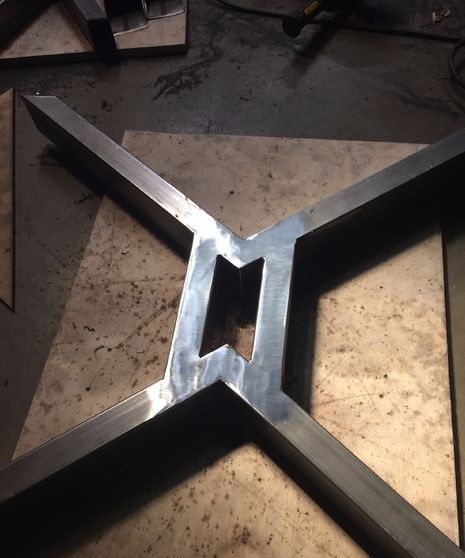

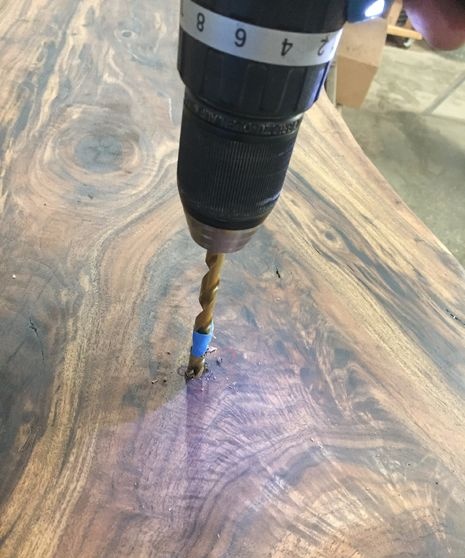
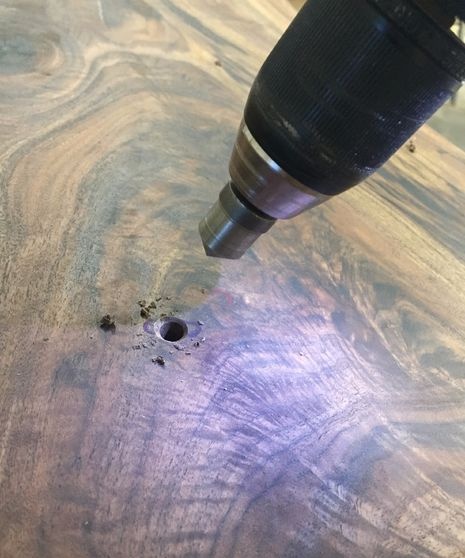
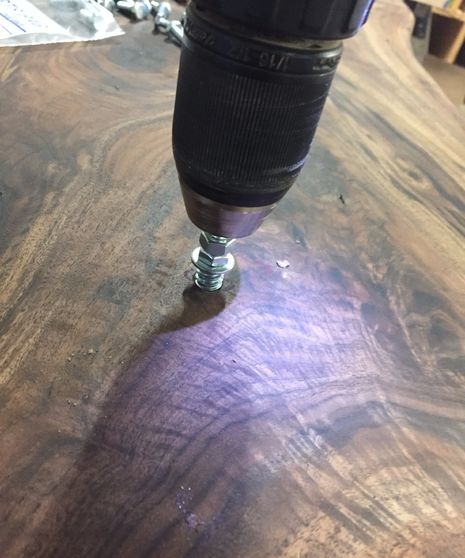
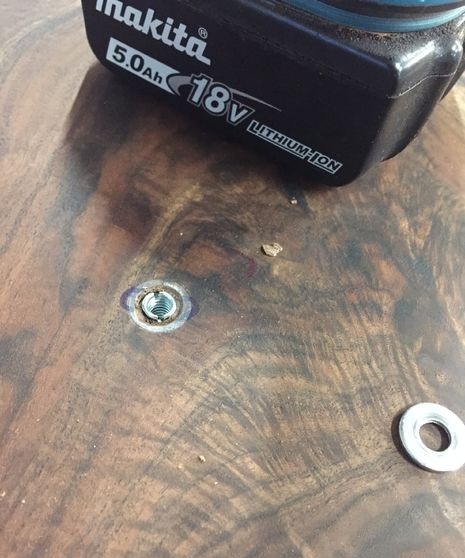
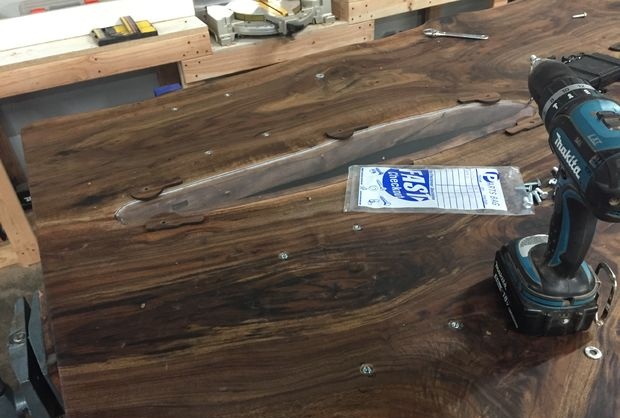
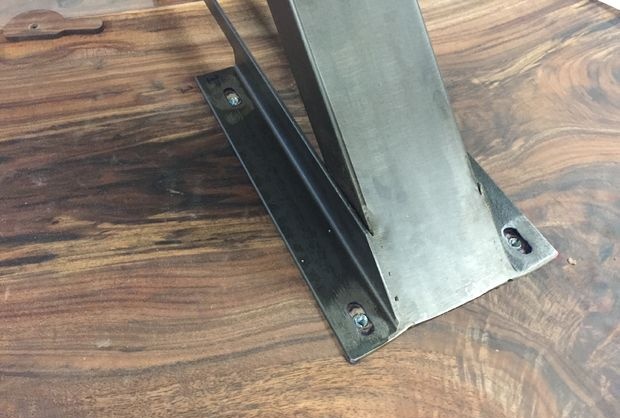
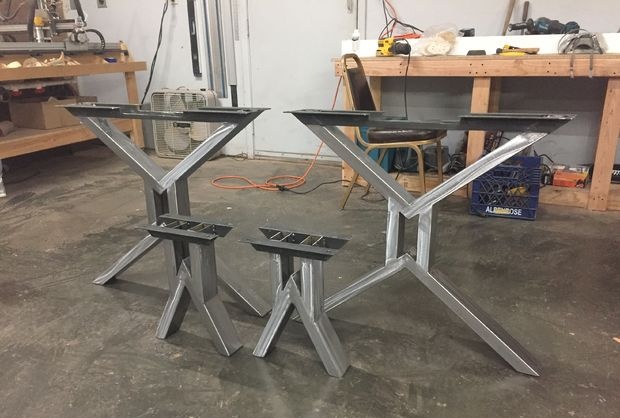
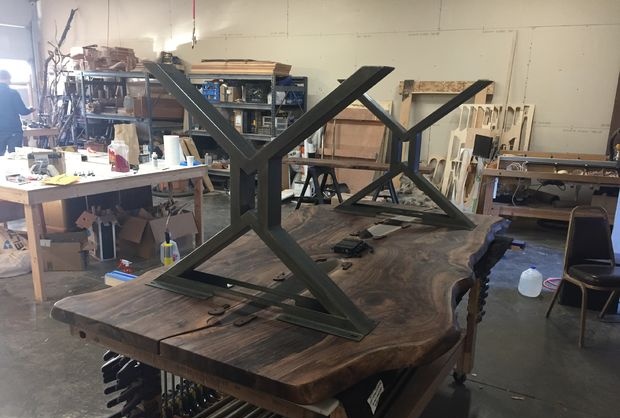
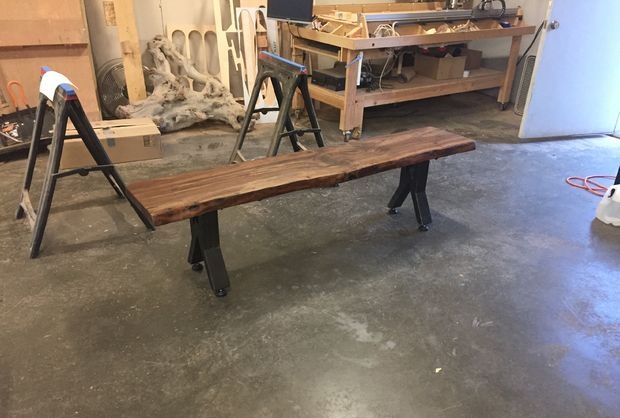

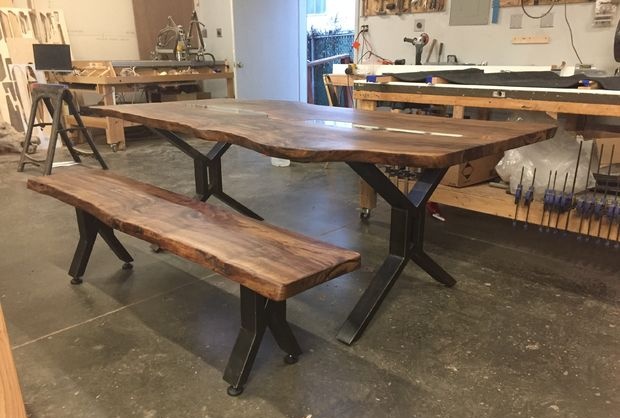
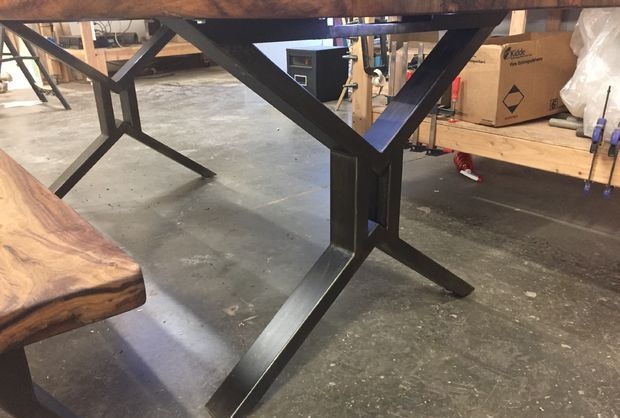
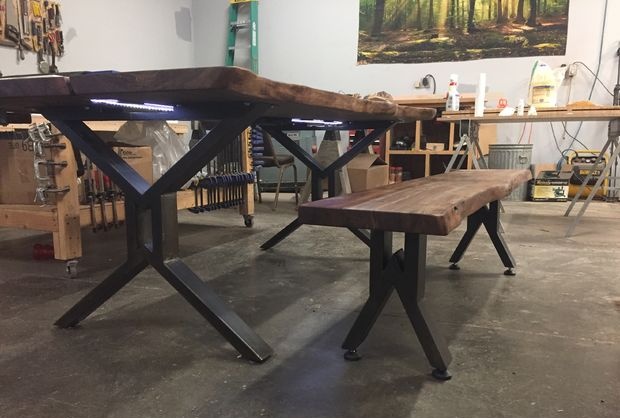
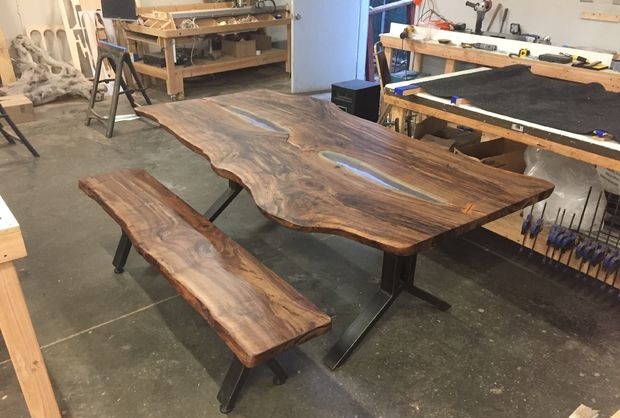
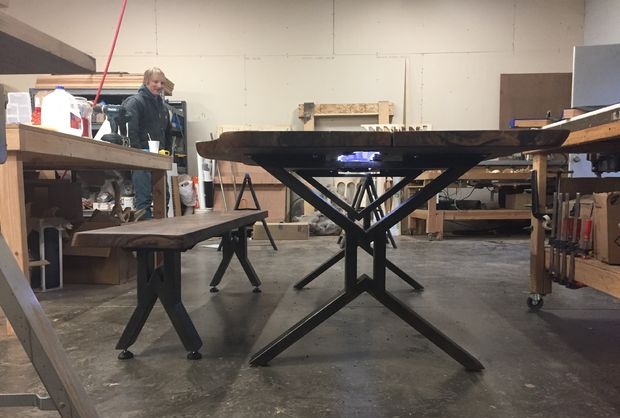
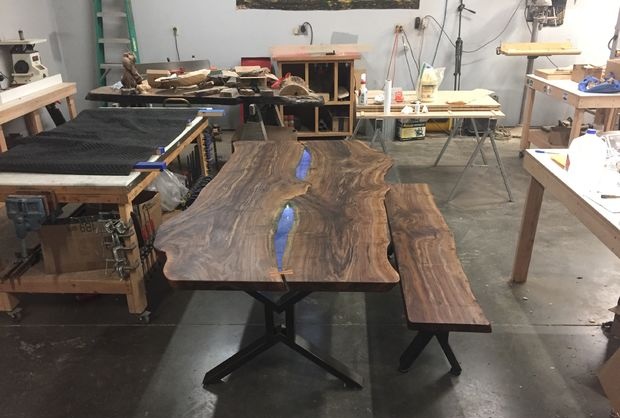
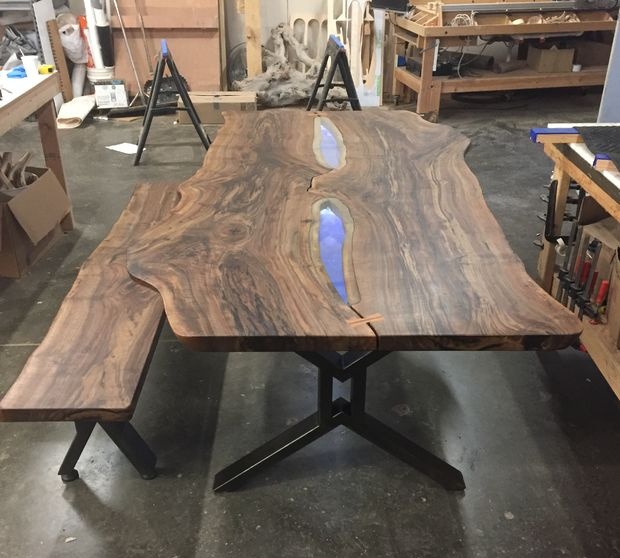
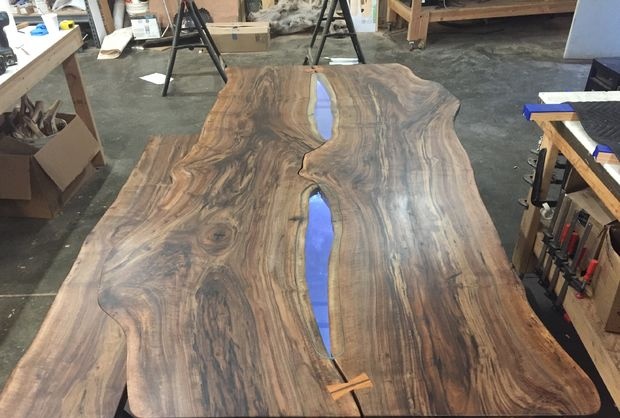
Benene var lavet af et rektangulært stålrør, der målte 3,8 x 7,6 cm og en jernvinkel på 3,8 x 3,8 cm. For at gøre processen lettere brugte jeg en laserskærer til at skære skabeloner ud for at holde de nødvendige komponenter på plads og et emne til at hjælpe med at sætte alt sammen i den rigtige vinkel. For lang tid siden var jeg en fremragende svejser, men der gik år, og uden tilstrækkelig øvelse havde jeg stadig funktionelle færdigheder, men jeg glemte, hvordan man svejser med dekorative sømme.For at udjævne denne ufuldkommenhed brugte jeg en vinkelsliber til at slibe det overskydende metal af og give overfladen et renere udseende.
Da svejsningen var færdig, sleb jeg alle metaloverfladerne med en vinkelsliber og en klapskive for at sikre, at de havde en ensartet tekstur og glans. Jeg skærer aflange huller i vinkelmetallet til at fastgøre bordpladen til, så hvis træet trækker sig sammen eller udvider sig, bliver der ikke problemer. Jeg svejste de nederste dele af benene med jernplader, så jeg så kunne bore huller i dem og installere højdejusteringsmekanismen.
Kunden ønskede, at benene skulle være sorte. Vi tænkte lidt over, hvordan vi bedst gør dette. I stedet for maling besluttede vi at bruge et stålblånende middel, så resultatet bliver mere holdbart og bedre skjuler ufuldkommenheder. Jeg brugte et produkt kaldet presto black. Påføring blev udført gennem en sprayflaske, indtil alle overflader var dækket af stoffet, og derefter blev dets virkning neutraliseret med en opløsning af bagepulver, så metallet ikke begyndte at oxidere (ruste). Efter at have fjernet blånemidlet tørrede jeg metallet med en kompressor og belagde overfladen med mat polyurethan for at forhindre, at det ruster undervejs.
Jeg brugte møbelmøtrikker og bolte til at fastgøre benene, hvilket gør det muligt at fjerne og montere benene igen og igen. Benene på bænken har jeg sikret med store træskruer, da den ikke er stor og kan flyttes uden at tage benene af.
Levering og montering
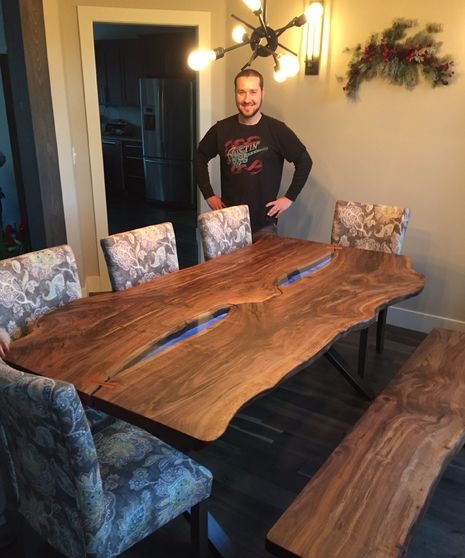
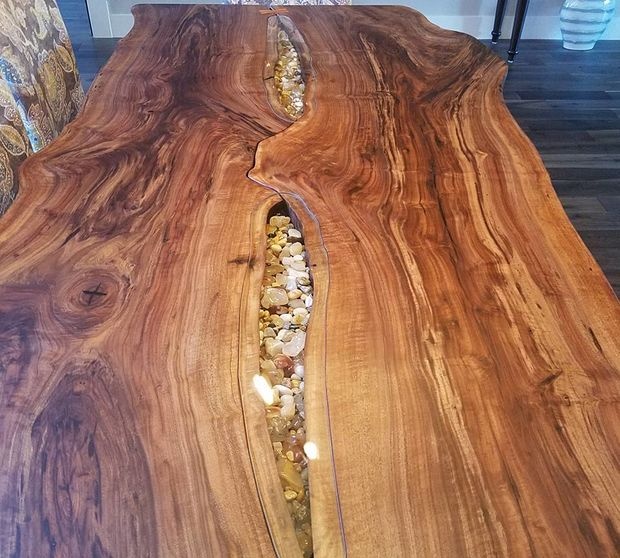
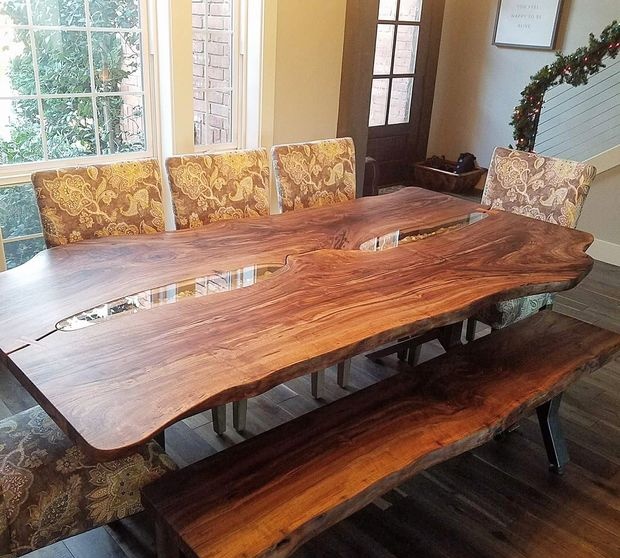
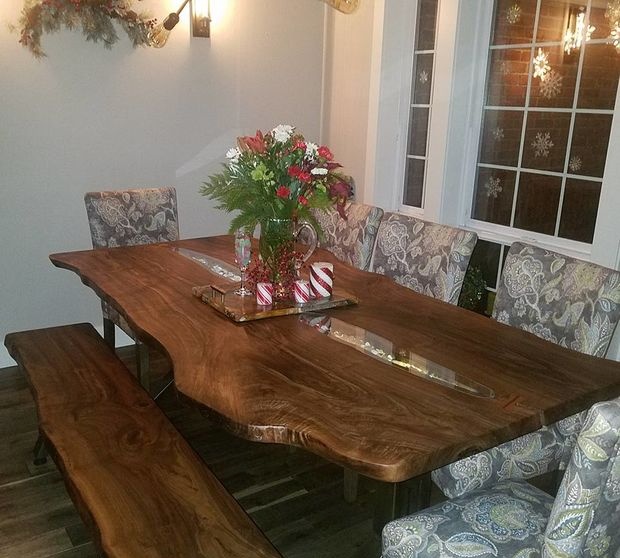
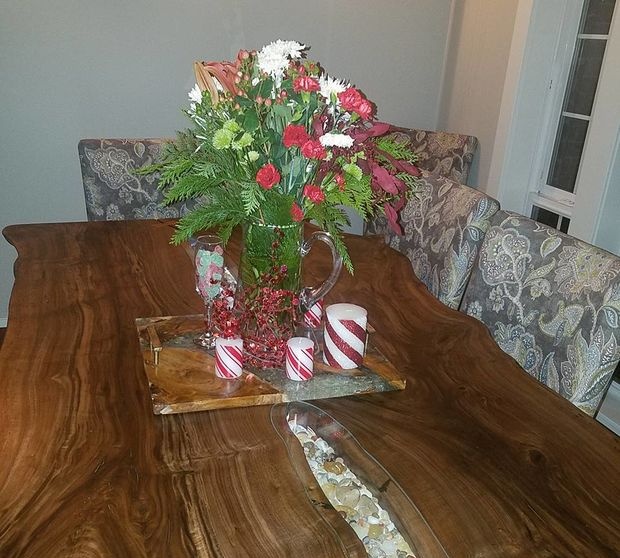
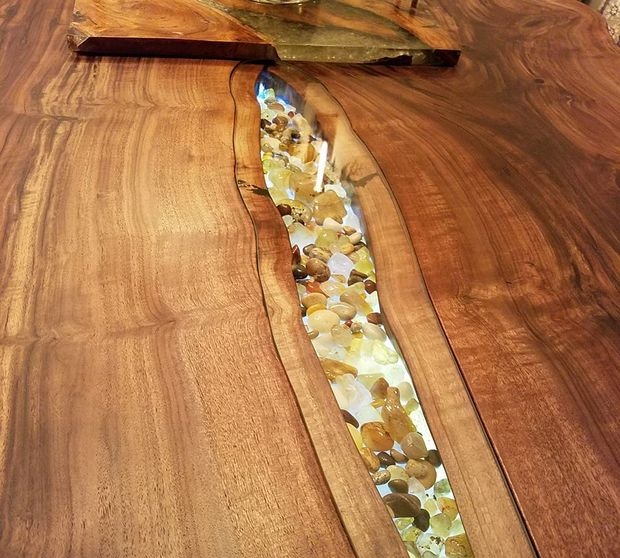
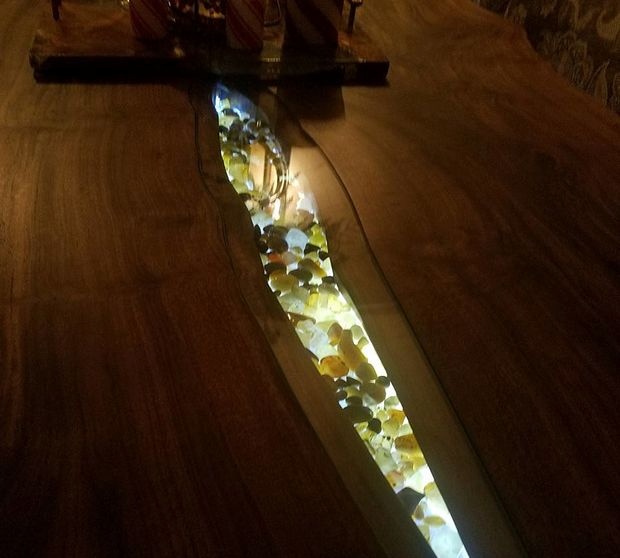
Kunden bor tre timer væk fra mig, så ved transport af bordet var det vigtigt at pakke det rigtigt. Jeg fjernede benene fra bænken og bordet og pakkede hver komponent for sig og forseglede den i plastikemballage.Det er vigtigt at pakke og pakke delene i den rækkefølge, de skilles ad, så når du sætter dem sammen igen, kommer de i den rigtige rækkefølge. Det bliver nemmere. For eksempel, da jeg ankom til en kundes hus, var det første, jeg skulle læsse af fra varevognen, bordpladen. Jeg stillede den på hovedet på gulvet i huset. De næste tilgængelige stykker var benene, som jeg satte fast på bordpladen. Så bænken, benene på bænken og så videre. Det kan virke som sund fornuft, men når du bliver revet med af pakning, er det nemt at glemme alt. Jeg filmede ikke denne proces, men jeg er sikker på, at det er ret nemt at forestille sig.
Kunden kunne rigtig godt lide spisestellet, og nu ligger hendes samling af agater i de oplyste fordybninger, i midten er der en buket til sæsonen, og rundt omkring er der et særligt udvalgt sæt stole. Det er på billedet. Et bord kan tilføje noget liv til et i forvejen sødt værelse. Jeg er glad for, at denne kreation kommer til et smukt hjem, hvor den vil blive beundret og plejet.
Tak for din opmærksomhed!
Originalartikel på engelsk
Lignende mesterklasser
Særlig interessant
Kommentarer (1)