Compresor de aire de una unidad ZIL y motor de lavadora.
Los propietarios de coches, motos y ciclistas a menudo tienen que inflar las ruedas; hacerlo manualmente es largo y tedioso. Un compresor de aire viene al rescate, que se puede ensamblar a partir de una unidad de automóvil en funcionamiento. Un motor de 300 vatios es excelente como motor; a menudo se utilizan para equipar lavadoras rotativas y automáticas. Consideremos en detalle el proceso de creación del dispositivo mencionado.
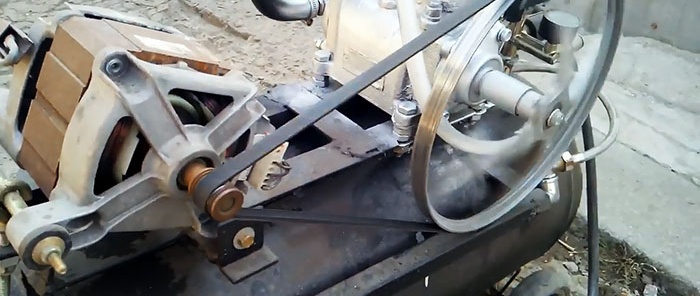
El proceso de fabricación de un compresor de aire requiere que un artesano tenga habilidades en metalurgia y plomería. Para el trabajo se necesitaron una serie de componentes y piezas: nuevos o usados:
Para realizar el trabajo necesitarás una herramienta de mecánico, un taladro con un juego de taladros y soldadura eléctrica. Algunas operaciones, por ejemplo, taladrar una polea, se encargan en un taller especializado.
La mayoría de los componentes fueron usados, fueron limpiados de contaminantes y, si fue necesario, reconstruidos. Las partes principales del compresor se fabricaron en el garaje y se ensamblaron en la siguiente secuencia:
La unidad del automóvil se monta en el bastidor del receptor mediante conexiones atornilladas.
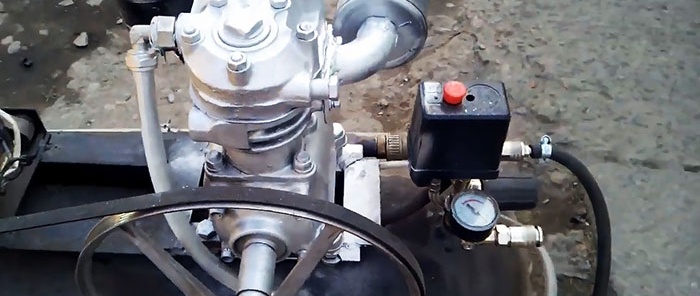
Junto a él se instala un accionamiento eléctrico para que las poleas queden en el mismo plano.
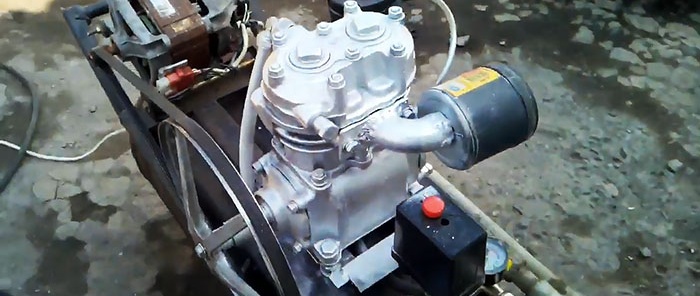
Delante del compresor en el bastidor montamos el sistema de control automático y lo reconfiguramos: encendiéndolo a una presión de 4 atm, apagándolo a 6 atm.
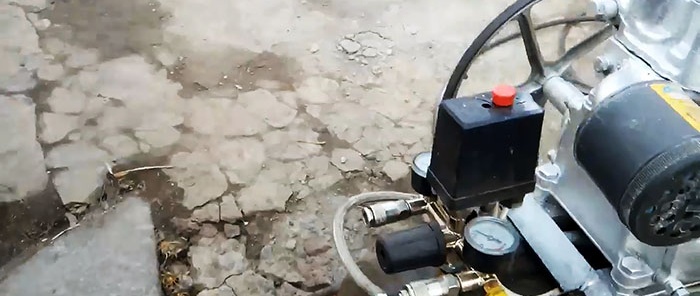
Perforamos un agujero en la tapa del cárter del compresor, cortamos una rosca y atornillamos un cuadrado. Le colocamos un tubo con un tanque de aceite y encima cortamos un respiradero a través del cual se exprimirá el aceite hacia el tanque de almacenamiento.
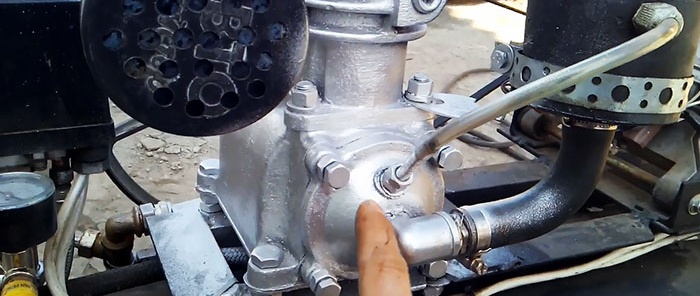
Soldamos un radiador de refrigeración por aire hecho de tubos de acero, que al mismo tiempo sirve como asa para el transporte. Por un lado le conectamos la salida del compresor, por el otro, conectamos el tubo de suministro de aire al receptor.
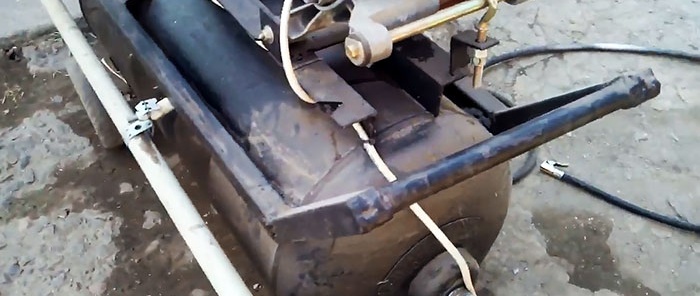
Giramos la línea de aire utilizando dos cuadrados.
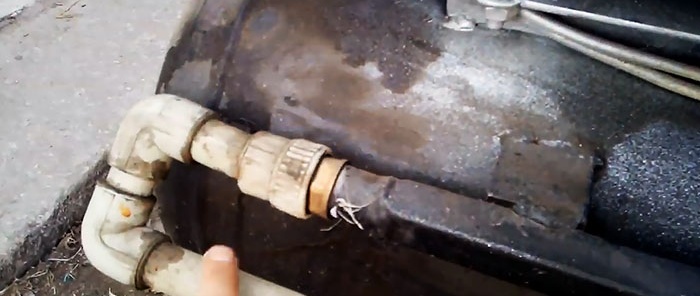
Instalamos una válvula de retención en la entrada del receptor.
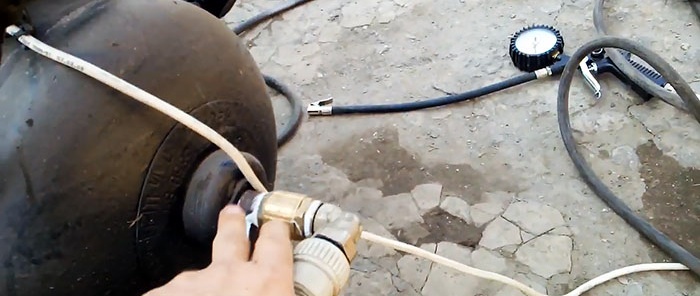
A la salida del receptor instalar una válvula y conectar una manguera flexible reforzada con rosca.
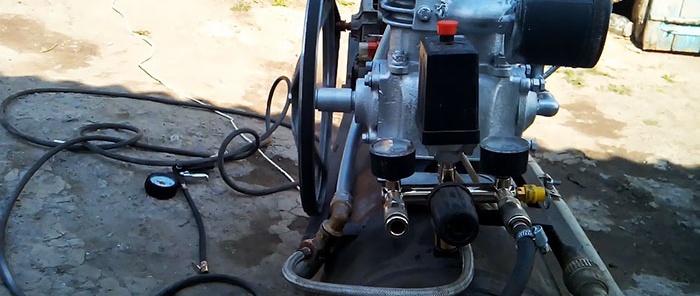
Instalamos un filtro de aire hecho de un frasco de plástico con una tapa con agujeros perforados en el tubo de succión del compresor.
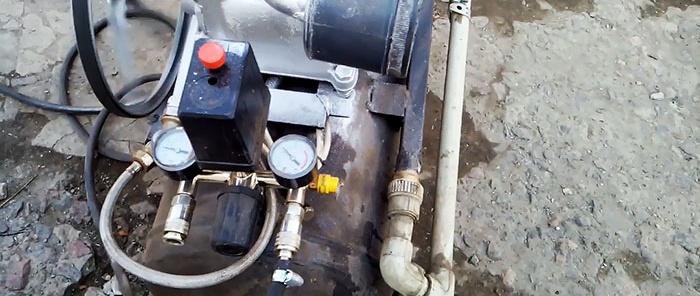
En el otro extremo de la manguera montamos una pistola para inflar neumáticos.
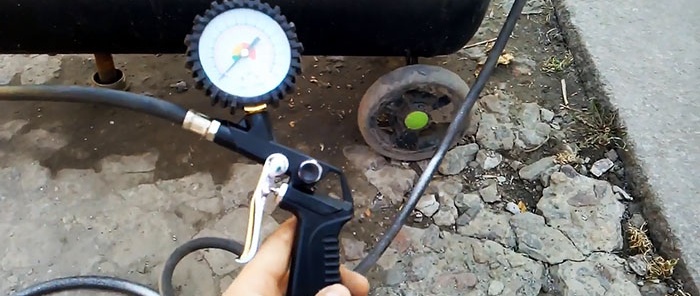
Como elemento filtrante se utiliza una esponja de espuma cortada a medida.
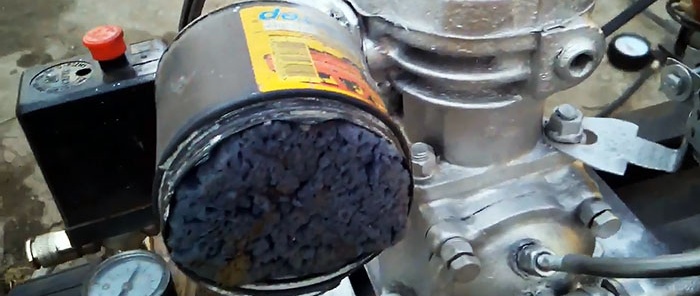
La relación entre las poleas motriz y conducida es de 1 a 13, lo que permite reducir las 13.000 rpm del motor eléctrico a 1.000 rpm en el compresor.
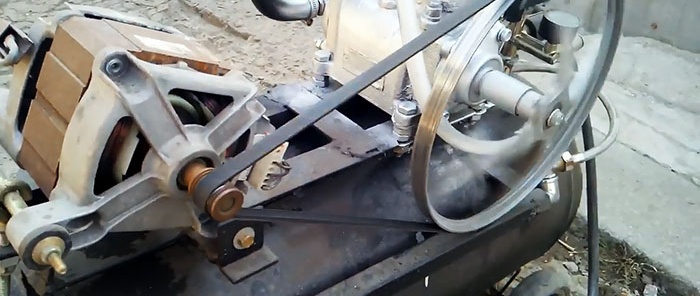
Esto asegura el funcionamiento normal de la unidad y un rápido aumento de presión en el receptor. Automático al llegar a las 6 atm. apaga el suministro de energía al variador y, a medida que aumenta el consumo de aire, el ciclo se repite.
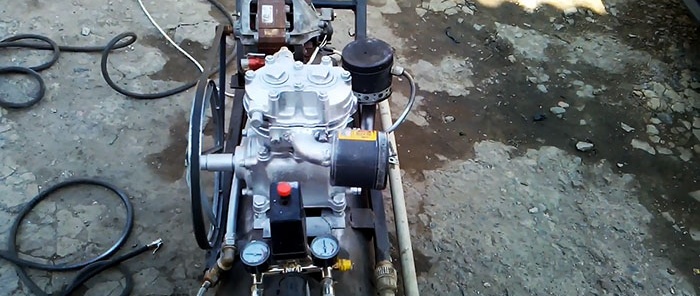
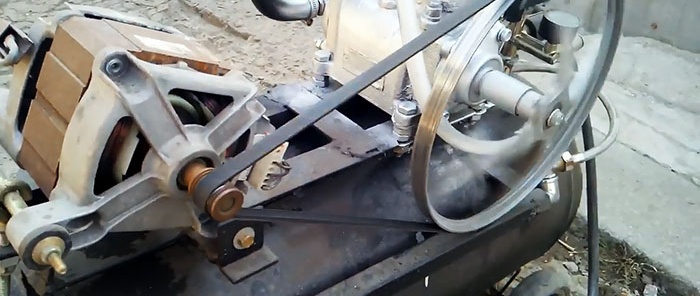
Materiales, componentes y herramientas utilizadas.
El proceso de fabricación de un compresor de aire requiere que un artesano tenga habilidades en metalurgia y plomería. Para el trabajo se necesitaron una serie de componentes y piezas: nuevos o usados:
- Compresor para camión ZIL-130 o ZIL-131.
- Motor eléctrico de potencia nominal 300 W, monofásico, voltaje 220 V.
- Poleas grandes y pequeñas.
- Receptor: cilindro de acero.
- Sistemas de control automático fabricados en China con manómetros.
- Accesorios de fontanería: tes de pinza, codos y válvula antirretorno.
- Tubos perfilados de acero, metal-plástico y plástico.
Para realizar el trabajo necesitarás una herramienta de mecánico, un taladro con un juego de taladros y soldadura eléctrica. Algunas operaciones, por ejemplo, taladrar una polea, se encargan en un taller especializado.
El procedimiento para fabricar y montar el compresor.
La mayoría de los componentes fueron usados, fueron limpiados de contaminantes y, si fue necesario, reconstruidos. Las partes principales del compresor se fabricaron en el garaje y se ensamblaron en la siguiente secuencia:
La unidad del automóvil se monta en el bastidor del receptor mediante conexiones atornilladas.
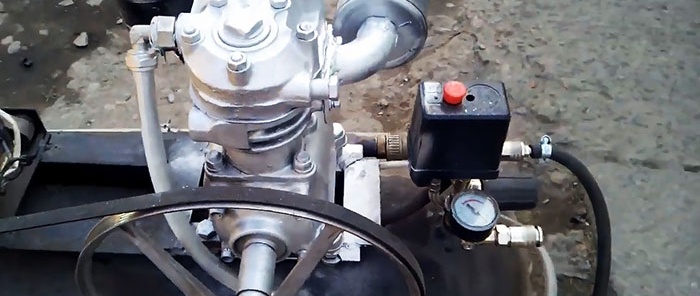
Junto a él se instala un accionamiento eléctrico para que las poleas queden en el mismo plano.
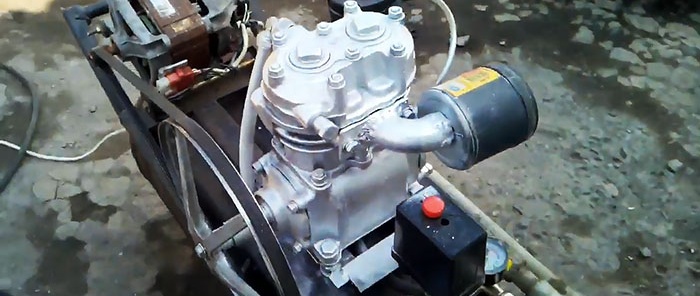
Delante del compresor en el bastidor montamos el sistema de control automático y lo reconfiguramos: encendiéndolo a una presión de 4 atm, apagándolo a 6 atm.
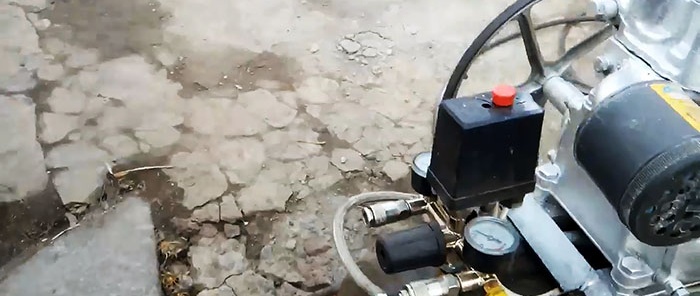
Perforamos un agujero en la tapa del cárter del compresor, cortamos una rosca y atornillamos un cuadrado. Le colocamos un tubo con un tanque de aceite y encima cortamos un respiradero a través del cual se exprimirá el aceite hacia el tanque de almacenamiento.
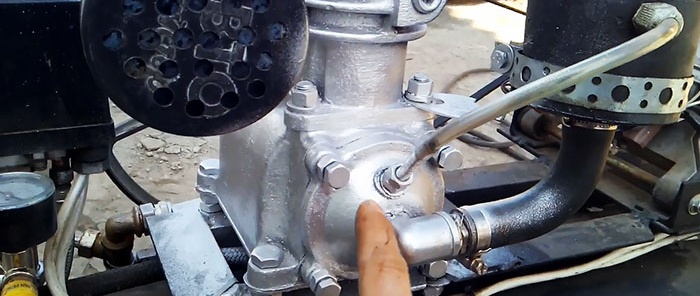
Soldamos un radiador de refrigeración por aire hecho de tubos de acero, que al mismo tiempo sirve como asa para el transporte. Por un lado le conectamos la salida del compresor, por el otro, conectamos el tubo de suministro de aire al receptor.
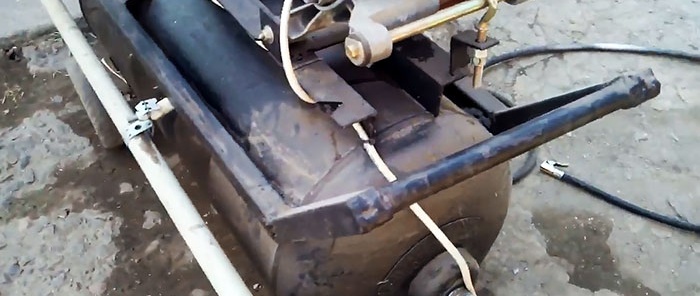
Giramos la línea de aire utilizando dos cuadrados.
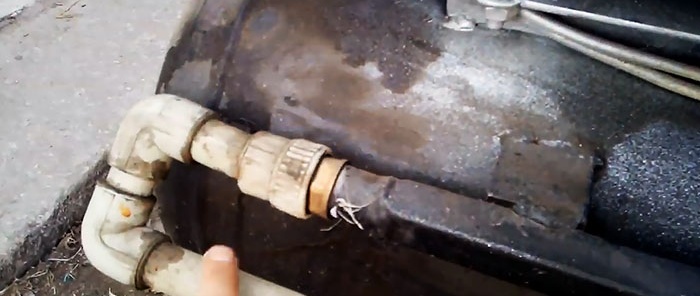
Instalamos una válvula de retención en la entrada del receptor.
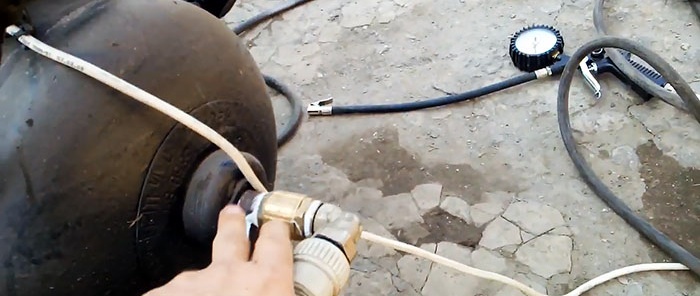
A la salida del receptor instalar una válvula y conectar una manguera flexible reforzada con rosca.
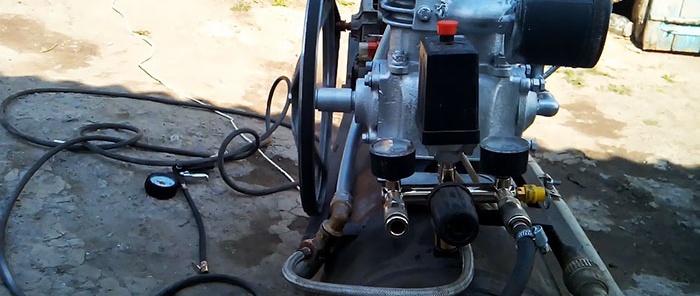
Instalamos un filtro de aire hecho de un frasco de plástico con una tapa con agujeros perforados en el tubo de succión del compresor.
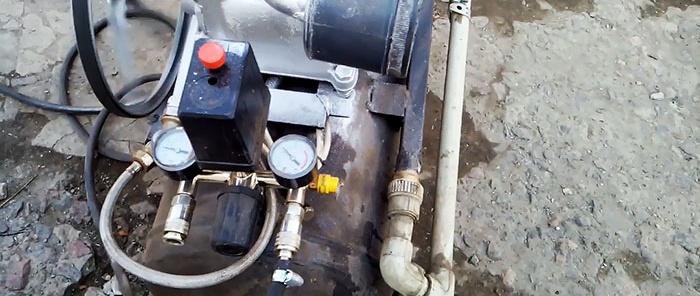
En el otro extremo de la manguera montamos una pistola para inflar neumáticos.
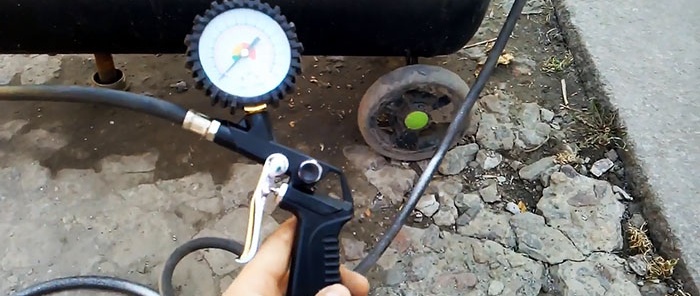
Como elemento filtrante se utiliza una esponja de espuma cortada a medida.
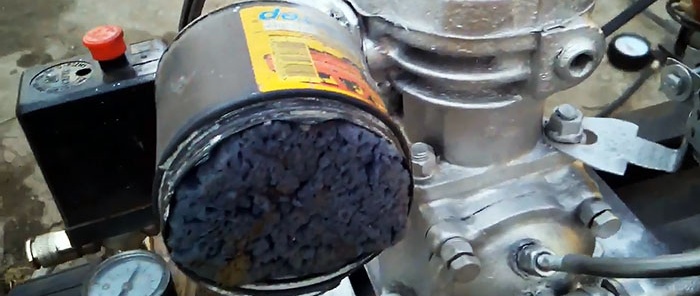
La relación entre las poleas motriz y conducida es de 1 a 13, lo que permite reducir las 13.000 rpm del motor eléctrico a 1.000 rpm en el compresor.
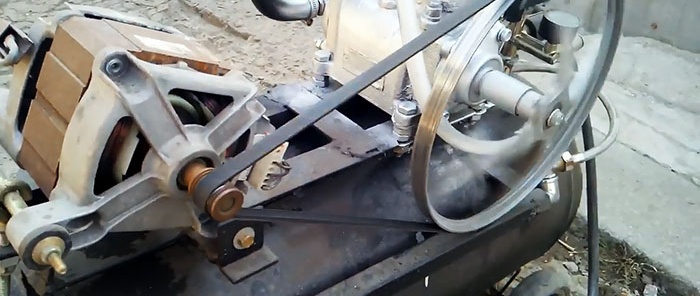
Esto asegura el funcionamiento normal de la unidad y un rápido aumento de presión en el receptor. Automático al llegar a las 6 atm. apaga el suministro de energía al variador y, a medida que aumenta el consumo de aire, el ciclo se repite.
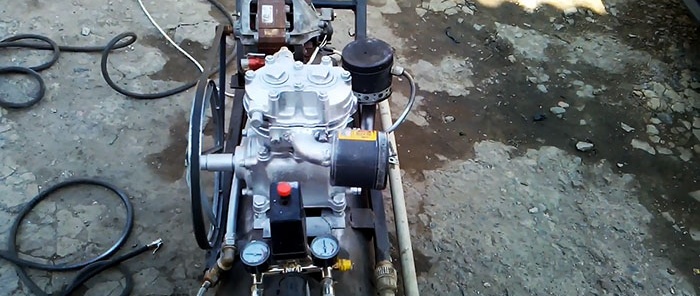
Ver el vídeo
Clases magistrales similares
Particularmente interesante
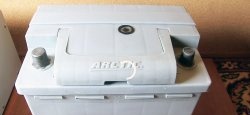
La forma más efectiva de restaurar tu batería
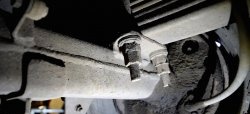
El lubricante penetrante más potente.
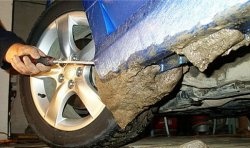
Una forma sencilla de eliminar la suciedad adherida a los revestimientos del guardabarros y
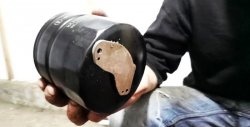
¿Vale la pena instalar un imán en el filtro de aceite?
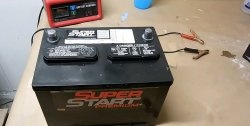
Cómo restaurar la batería de un coche con bicarbonato de sodio
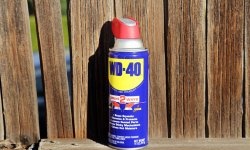
Usos inusuales del WD-40
Comentarios (1)