Cómo montar una máquina para rectificar discos de freno a partir del motor de una lavadora en casa.
En los coches usados, a menudo se pueden sentir pulsaciones o vibraciones al pisar el pedal del freno. La causa de esto es la formación de costras de óxido en los discos de freno. Su presencia hace que la frenada sea menos eficaz y además va acompañada de un chirrido característico. Este problema se puede solucionar rectificando los discos, lo cual es muy fácil de hacer en una máquina casera. Una máquina de este tipo se puede soldar en su garaje o taller en tan solo 2 horas.
Materiales:
- Motor de lavadora;
- chapa de acero de 3 mm;
- esquina 20x20 mm;
- cubo de la rueda;
- Correa de transmisión;
- resorte de válvula;
- tubo de 25-32 mm.
Proceso de fabricación de una rectificadora de discos de freno.
Es necesario cortar una placa de chapa de acero que servirá como suela de la máquina. Sus dimensiones son individuales, ya que dependen del diámetro del disco y de la correa de transmisión disponible. Es necesario que haya suficiente espacio para montar el motor y el buje en la suela, procurando que el disco abrasivo no entre en contacto con la polea del motor.
Se inserta una varilla de acero de diámetro adecuado en el soporte estándar del motor de la lavadora. Luego se cortan 2 ojales y un puente de chapa o tira de acero, a partir de los cuales se suelda el soporte de fijación.
El motor debe instalarse verticalmente con el eje hacia arriba en la suela, colocando algo debajo para crear un espacio de 10 a 20 mm. A continuación se suelda el soporte a la placa desde abajo. Para evitar que se doble, debes cocinar el refuerzo para darle rigidez.
Se debe soldar un soporte al costado de la suela para instalar el cubo. Para hacer esto, puede usar el embrague de ajuste de la convergencia de la rueda. Tiene ranuras que permiten sujetar el buje. La tuerca de acoplamiento está soldada al tubo para extender la estructura.
A continuación, debe calcular la altura a la que se colocará el cubo en relación con la polea en el eje del motor eléctrico. Debe ser más bajo para que el disco adjunto quede al ras con la polea. El tubo está soldado verticalmente a la suela. Para evitar que se rompa, la conexión se refuerza con bufandas.
Se inserta un resorte de válvula entre el motor y su soporte. Para evitar que se caiga se puede soldar. El buje está atornillado lateralmente.
Ahora necesitas conectar el cable con el enchufe al motor eléctrico. Si hay 4 cableados, entonces usando métodos de prueba puede encontrar la combinación de dos de ellos que lo iniciará. No pasará nada malo, puedes atornillar el cable de forma segura y enchufarlo y enchufarlo a la toma de corriente. Si el motor no arranca, entonces debe conectarse a otro par de cables. El exceso de cableado está aislado.
El disco de freno está fijado al buje. La correa de transmisión se pasa entre ésta y la polea del motor. Si es demasiado corto, la resistencia del resorte puede doblar la delgada suela de acero. Para evitar que esto suceda, es posible que sea necesario reforzarlo soldando las esquinas en la parte inferior.
Con una carga en forma de disco, el motor no arranca, es necesario empujarlo ligeramente. Luego, después de la aceleración, se rectifica la superficie del disco de freno. Primero se utiliza papel de lija grueso P80 y luego se reduce el grano a P320. El resultado es un disco suave y sin rayones que frena suave y silenciosamente.
Ver el vídeo
Clases magistrales similares
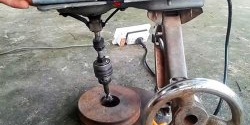
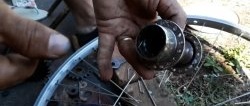
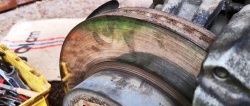
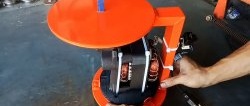
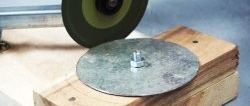
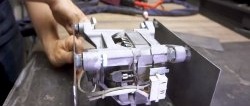
Particularmente interesante
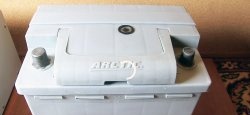
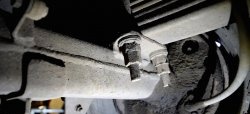
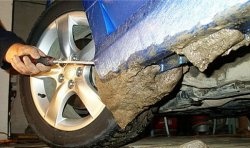
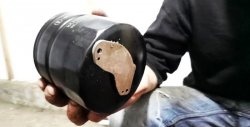
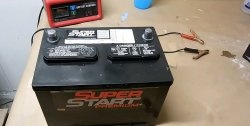
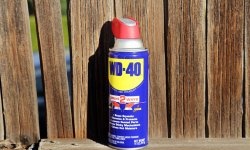