Como fazer um ventilador radial para uma coifa de oficina de compensado e motor de máquina de lavar
A purificação do ar numa oficina de carpintaria ou numa pequena oficina de processamento de pedra utilizando sistemas de aspiração industrial requer um investimento considerável. Para uma pequena instalação de produção, garagem ou oficina doméstica, a ventilação pode ser feita em algumas horas, gastando algumas dezenas de dólares. Quase todos os materiais e ferramentas podem ser encontrados nas prateleiras da maioria dos marceneiros.
O que você vai precisar
Para o projeto você precisa de:- motor elétrico de máquina de lavar: potência – 600 W com capacitor, com velocidade de rotação do eixo – 1600 rpm;
- quatro folhas de compensado com dimensões 400×400 mm e espessura 19 mm;
- um par de placas de compensado com dimensões 300×300 mm, espessura ~16 mm;
- compensado com 6 mm de espessura;
- aço laminado com espessura de 0,35 mm e dimensões 120x1100 mm;
- várias dezenas de parafusos metálicos;
- fita adesiva estreita;
- Parafusos M5 ou M6 com asas e arruelas.
- esmerilhadeira (rebarbadora) com rebolo de esmeril com granulometria de grão 80-100;
- lápis, régua e compasso;
- tesouras para cortar chapas metálicas;
- furadeira ou chave de fenda com brocas para metal e uma broca para parafusos auto-roscantes;
- fresadora manual de madeira, preferencialmente embutida na mesa;
- cortador de ranhura reta;
- lixa;
- macete de madeira ou borracha (martelo);
- cola e grampos para madeira;
- uma serra circular.
O processo de fabricação de um exaustor com materiais disponíveis
O eixo do motor está livre de porcas, polias, bujões, flanges e outros dispositivos. Um círculo com diâmetro de 250 mm é cortado em compensado medindo 400x400 mm usando uma fresadora manual para madeira usando uma mesa de fresagem universal.
No interior é feito um furo com diâmetro igual ao diâmetro do impulsor do motor (50 mm).
Um círculo com diâmetro 1-2 mm menor que o furo é cortado das sobras para que caiba livremente nele.
Os furos são feitos para a montagem do motor elétrico e, a seguir, alguns milímetros com um escareador ou uma broca grossa para esconder as cabeças dos parafusos. O motor é aparafusado ao compensado.
Um cilindro menor de tal altura é colado ao círculo para que juntos cubram o eixo do motor.
No interior é feito um furo com diâmetro igual à espessura do eixo. A estrutura é cuidadosamente pressionada no eixo através de um espaçador de madeira para não rachar ou danificar.
Dos restos de madeira compensada, duas “guitarras” idênticas são cortadas e uma segunda folha - o futuro corpo do purificador de ar.
Dois círculos são cortados em finas folhas de madeira compensada com um diâmetro um pouco menor do que antes - cerca de 230 mm.
Em um deles, ranhuras radiais cegas são fresadas com uma fresa de 6 mm e profundidade de 3-5 mm. Neste caso, 8 peças.
O resultado é uma turbina semelhante à usada em um aspirador de pó.
Usando uma serra circular manual ou estacionária, retângulos são cortados em compensado fino.Seu comprimento excede o comprimento das ranhuras em alguns milímetros, sua largura é de 58 mm.
As nervuras entre as bordas laterais, com as quais as peças são inseridas nas ranhuras, são retificadas em ângulo. Essas inclinações facilitarão a instalação das lâminas nas ranhuras. Ao lixar, tome cuidado para não colocar os dedos sob a lixa. As ranhuras são lubrificadas com cola de madeira e todas as peças são pressionadas nelas.
O segundo círculo é colocado coaxialmente com o inferior, e a estrutura é pressionada com um peso para colagem.
Após a secagem, uma entrada de ar com raio de 43 mm é perfurada no interior da base da turbina. No centro do segundo círculo com diâmetro de 230 mm, é feito um furo com uma coroa de diâmetro igual à espessura do cilindro menor no eixo do motor.
A estrutura é colocada no motor e aparafusada com parafusos através de furos pré-perfurados.
O motor dá partida e o compensado é nivelado com lixa ou esmeril como acessório, tomando os devidos cuidados. O círculo superior está colado nas lâminas. A estrutura é fixada com grampos. Uma rebarbadora com roda de esmeril ou esmeril se adapta a ela.
Se as lâminas se projetam fortemente além dos círculos, elas precisam ser cuidadosamente aparadas com um serrote com uma margem de alguns milímetros.
O motor é acionado com uma ferramenta cifrada para alinhar as bordas e centralizar a turbina para minimizar a vibração.
O mesmo é feito para nivelar a superfície superior. Na “guitarra” superior é feito um furo igual ao diâmetro do círculo com o motor elétrico para que fique bem encaixado. Uma entrada de ar com raio de 43 mm é recortada na “guitarra” inferior.
De um pedaço de chapa de aço é cortada uma tira de 110 mm de altura, de circunferência igual à “guitarra” com margem.
A largura é dobrada no comprimento mostrado.
A uma distância de 10-15 mm da borda ao longo do comprimento da chapa, os locais onde os parafusos são aparafusados são perfurados a cada 40-50 mm.
Eles são projetados na borda oposta da tira usando um quadrado ou equivalente. Para evitar lacunas ao longo do perímetro de contato entre o metal e o compensado, é colada fita adesiva. O metal é parafusado na parte inferior da base.
Na parte inferior da tampa, 4 furos com um diâmetro de 5-6 mm são perfurados a uma distância de ~ 7-8 mm da borda e parafusos M5 ou M6 são aparafusados neles. Utilizando pedaços de madeira com 81 mm de altura, a tampa é instalada no lugar.
Em seguida, é aparafusado com parafusos de metal. O excesso de metal é cortado.
O bloco com o motor é inserido no lugar. Arruelas são colocadas nos parafusos e asas são aparafusadas para fixar o bloco dentro do dispositivo. O design pode ser testado. Após uma inicialização bem-sucedida, conecte-se ao duto de ar para remover o ar sujo e a ferramenta por meio de adaptadores.
Não se preocupe se o dispositivo precisar ser desmontado algumas vezes para aplicar uma segunda camada de selante entre o compensado e o metal e lixar adicional para eliminar a vibração. É aconselhável fazer uma carcaça protetora do motor em madeira ou chapa de aço e isolar seus contatos antes da primeira partida.
Assista o vídeo
Master classes semelhantes
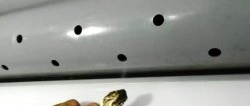
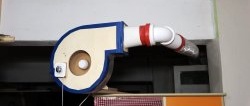
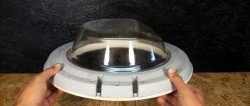
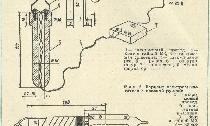
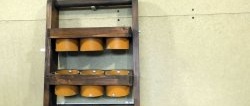
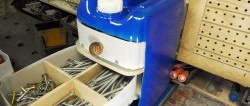