Soldadura per fricció
La majoria dels processos de soldadura moderns es basen en l'entrada de calor externa, com ara una descàrrega d'arc. Però la calor es pot generar directament a la zona de soldadura a causa de la fricció entre les peces que es connecten.
L'energia tèrmica es pot obtenir fent girar una part mentre la segona està estacionària, o girant en sentit contrari. A més, les peces s'han de pressionar simultàniament les unes contra les altres amb una força constant o creixent de principi a fi. El procés acaba amb una aturada ràpida i alterada de la peça giratòria.
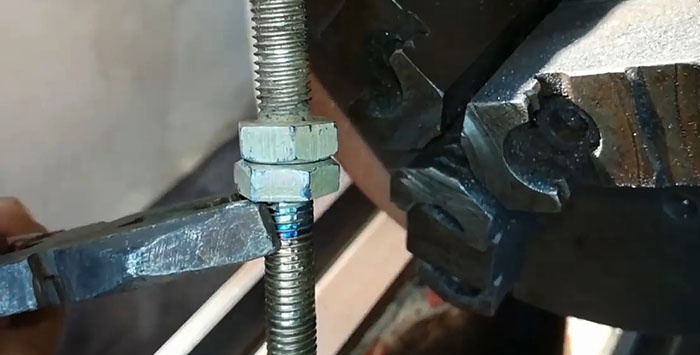
En comparació, per exemple, amb la soldadura elèctrica a tope, el procés basat en la fricció té una sèrie d'avantatges operatius:
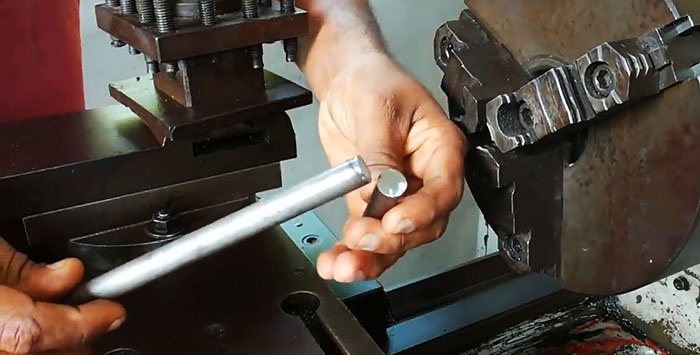
Al mandril i el capçal de la màquina subjectem una vareta metàl·lica, el diàmetre de la qual hauria de ser superior a 3,5 mm, però inferior a 200 mm. Poden ser tant d'acer, alumini, coure, bronze o diferents metalls:
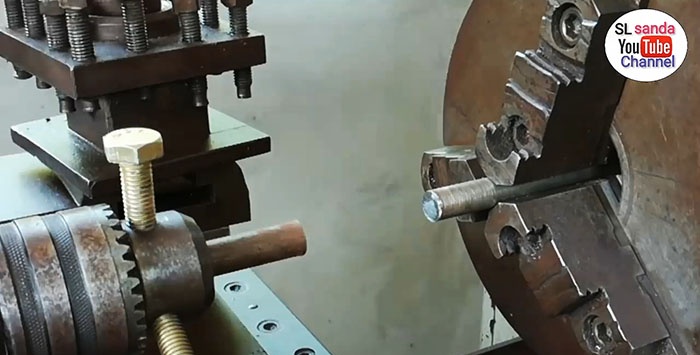
Les combinacions de materials poden ser molt diferents, fins i tot aquelles que no es poden soldar de la manera habitual. No hi ha restriccions en aquest sentit per a la soldadura per fricció.
En el nostre cas, fixem la vareta al capçal mitjançant tres cargols cargolats als forats del mandril, espaiats uniformement al voltant de la circumferència a 120 graus. Amb la seva ajuda, realitzem l'alineació respecte de la vareta subjectada al mandril apretant o afluixant un o un altre cargol.
Portem el capçal fins que les varetes s'aturin de punta a punta i el subjectem o subjectem amb la mà per tal d'augmentar la força de subjecció durant el procés de soldadura, que requereix la tecnologia d'aquest mètode de soldadura.
Encenem la màquina, com a resultat de la qual cosa la vareta subjectada al mandril de la màquina comença a girar. En el nostre cas, la vareta fixada al capçal està immòbil, però en principi pot girar en sentit contrari, la qual cosa reduiria el temps del procés.
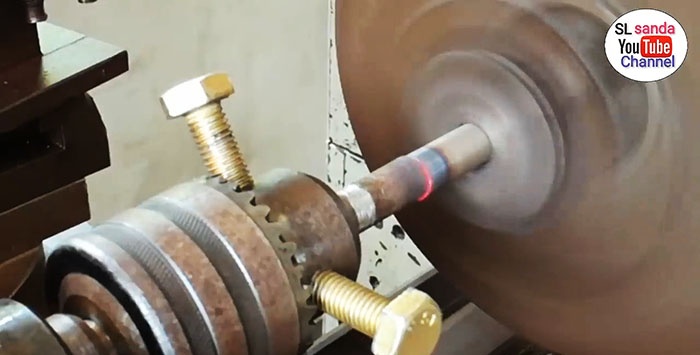
Aviat veurem colors tacats que comencen al punt de contacte de les varetes i s'estenen al llarg d'elles en direccions oposades, la qual cosa és un signe directe del ràpid escalfament del metall com a conseqüència de la fricció.
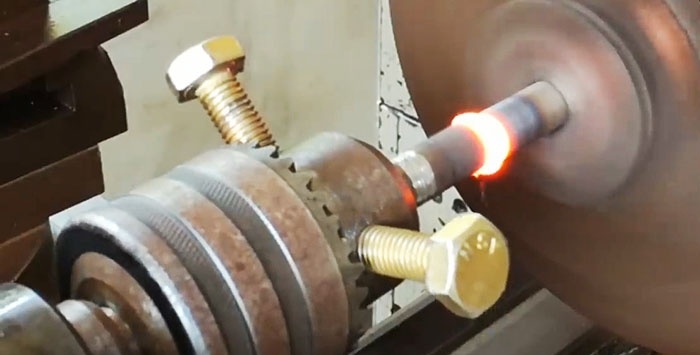
Al cap d'un altre temps, el metall de la zona de contacte brillarà brillantment i començarà a esprémer en forma d'anell més enllà de les dimensions de les barres.Aquest anell també contindrà rebava: escama, greix no cremat, inclusions sòlides no metàl·liques, etc.
En el moment de la brillantor més brillant al punt de contacte, la màquina s'ha d'apagar bruscament perquè el metall de les dues varetes s'enganxi. Al mateix temps, si el capçal no s'ha fixat, cal augmentar gradualment la pressió sobre ell per compensar el volum de metall desplaçat a la zona de contacte i obtenir una connexió més forta i de més qualitat.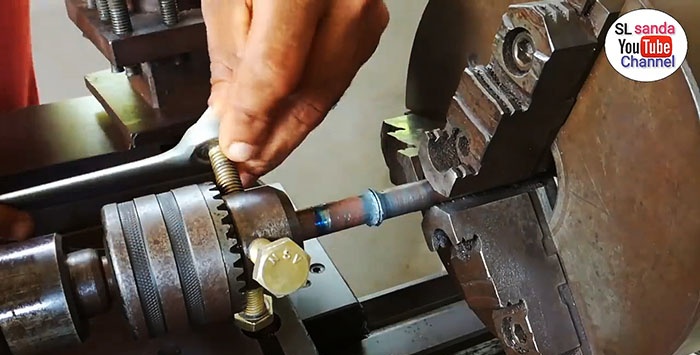
Després d'esperar fins que la brillantor s'aturi (i això és un senyal que el metall s'ha fixat completament), podeu afluixar els cargols de fixació i treure el capçal. Ara només queda comprovar la qualitat de la soldadura per fricció.
Per fer-ho, torneu a encendre la màquina i detecteu una lleugera desviació de la vareta soldada, conseqüència d'una alineació inexacta durant la instal·lació al principi. Aquest defecte es pot eliminar girant i eliminant la rebava extruïda a la zona de contacte.
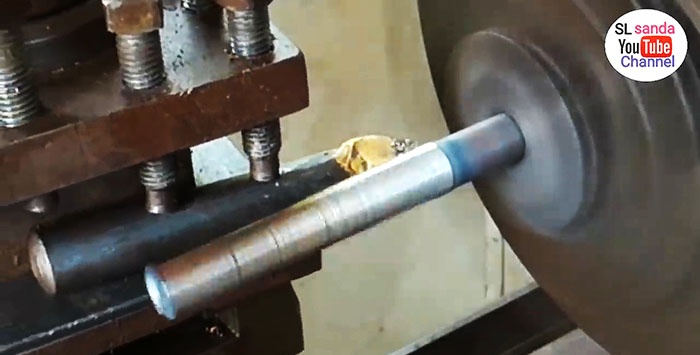
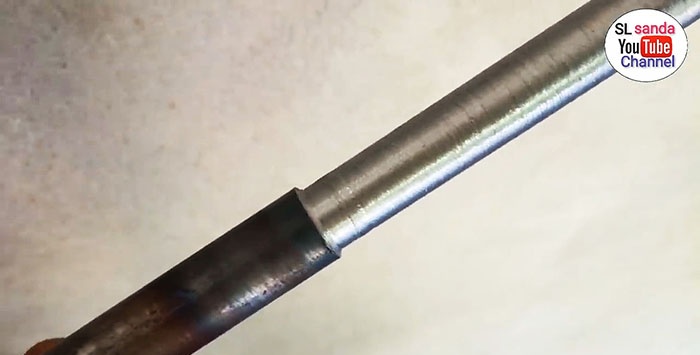
Una penetració més profunda del metall mostra que no hi ha cap característica visible a la zona de soldadura de les dues varetes. Sembla que aquest no és el punt de contacte entre dues varetes, sinó el cos d'una d'elles.
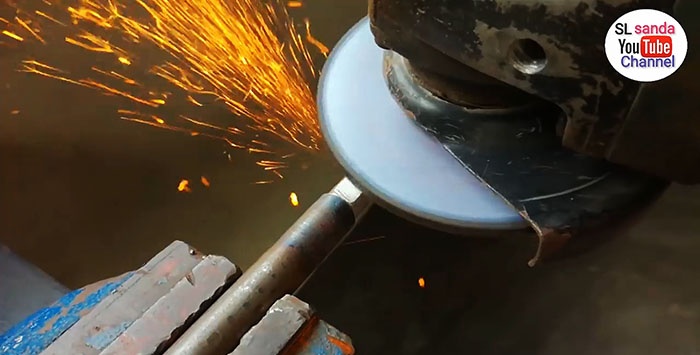
Realitzem el següent control de qualitat de la soldadura per fricció. Fixem les varetes connectades d'aquesta manera en un vici i utilitzem un disc de mòlta per crear un "prestatge" a la zona de contacte, i de nou estem convençuts de l'homogeneïtat del metall, que també indica la qualitat de la soldadura.
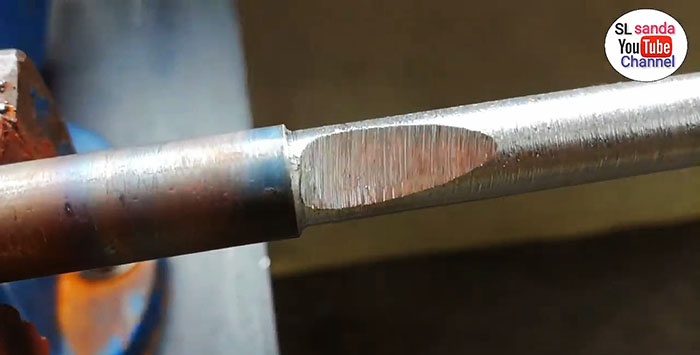
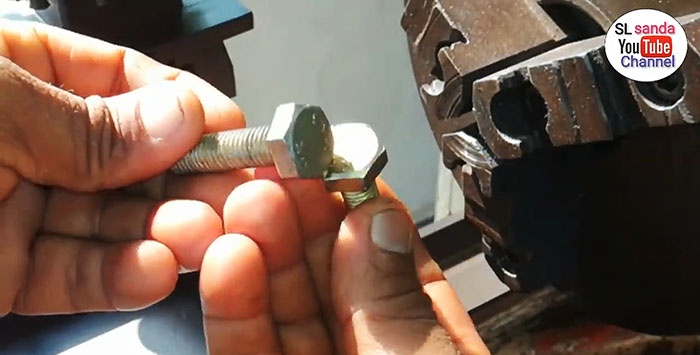
La soldadura per fricció es pot utilitzar per unir capçals i cargols produïts en massa. El procés no és diferent del procés amb barres: un cargol està subjectat al mandril de la màquina i l'altre al capçal.
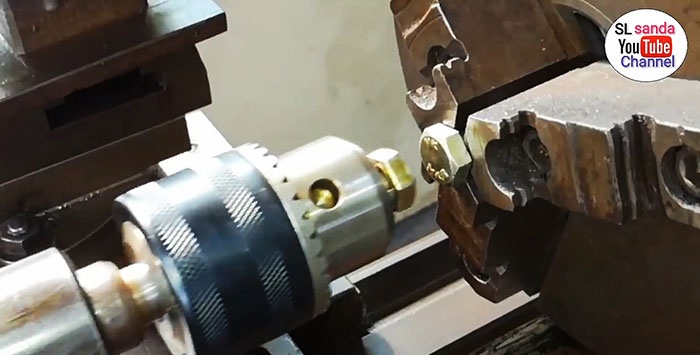
Amb l'ajuda d'aquest últim, els cargols es posen en contacte amb els capçals i s'engega la màquina. També cal augmentar la força de tancament i capturar el moment de la soldadura per tal d'apagar l'accionament a temps.
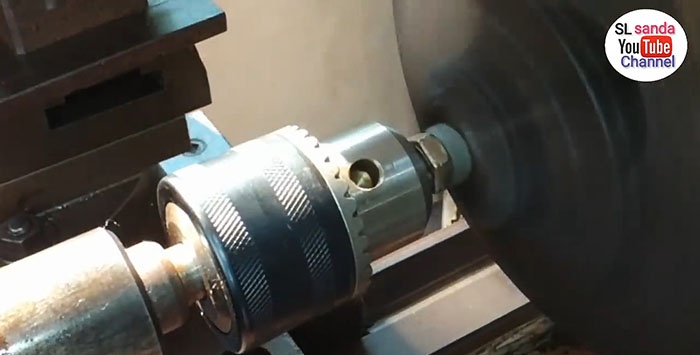
La soldadura per fricció es pot utilitzar per unir materials difícils o impossibles de soldar amb altres tipus: acer i alumini, acers austenètics i perlítics. També es pot utilitzar per unir fàcilment peces de plàstic.
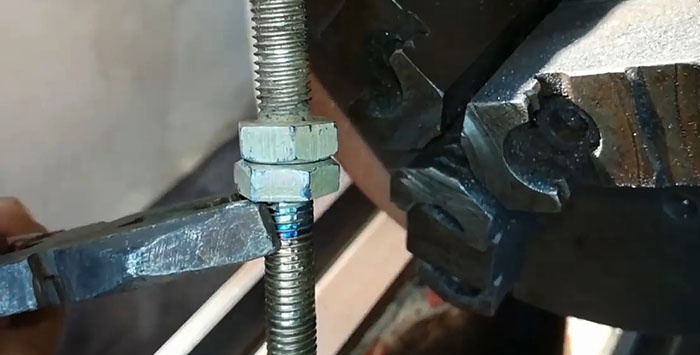
Els càlculs i la pràctica amb unió per fricció demostren que aquest mètode és més adequat per a peces el diàmetre de les quals es troba entre 6 i 100 mm. Soldar varetes amb un diàmetre superior a 200 mm no és rendible econòmicament, ja que el procés requerirà més potència (0,5 mil kW) i força axial (3 × 106 N). No es podran connectar barres amb un diàmetre inferior a 3,5 mm mitjançant aquest mètode a causa de la necessitat de proporcionar altes velocitats (200 rpm) i la dificultat de determinar quan apagar l'accionament.
L'energia tèrmica es pot obtenir fent girar una part mentre la segona està estacionària, o girant en sentit contrari. A més, les peces s'han de pressionar simultàniament les unes contra les altres amb una força constant o creixent de principi a fi. El procés acaba amb una aturada ràpida i alterada de la peça giratòria.
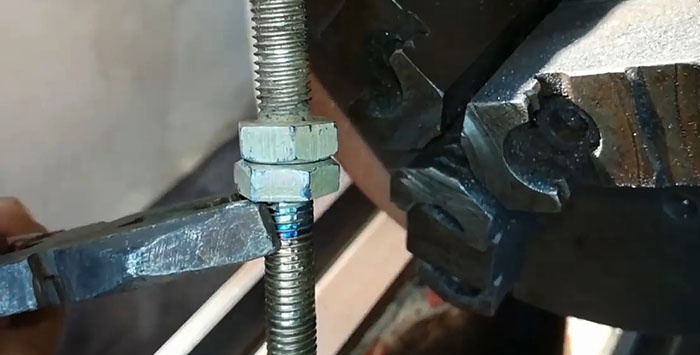
En comparació, per exemple, amb la soldadura elèctrica a tope, el procés basat en la fricció té una sèrie d'avantatges operatius:
- els costos energètics es redueixen molt;
- la junta soldada és sempre fiable, ja que només depèn de les característiques termofísiques dels productes que es solden;
- No es necessita cap preparació especial per connectar la junta, ja que l'escala, l'òxid, el greix i el greix es cremen o s'espremen en un instant al començament del procés;
- la qualitat de la connexió no es veu afectada fins i tot per la violació del paral·lelisme de les peces fins a angles de 6 ± 1 graus;
- absència de factors negatius en forma de radiació ultraviolada i emissions de gasos nocius;
- senzillesa dels equips tecnològics, fàcilment adaptables al manteniment rutinari, la mecanització i l'automatització.
Procés de soldadura per fricció en un torn
Soldar barres d'acer
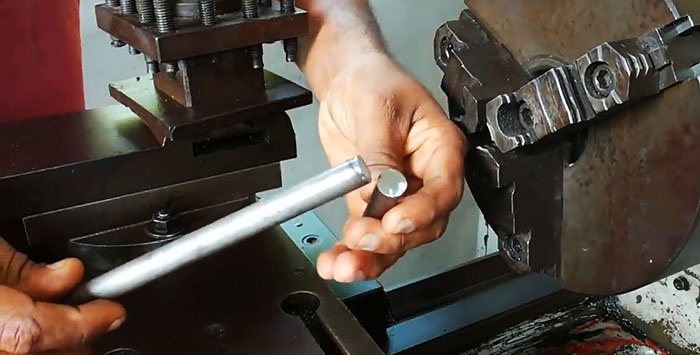
Al mandril i el capçal de la màquina subjectem una vareta metàl·lica, el diàmetre de la qual hauria de ser superior a 3,5 mm, però inferior a 200 mm. Poden ser tant d'acer, alumini, coure, bronze o diferents metalls:
- acer i alumini;
- acer i coure;
- alumini i bronze, etc.
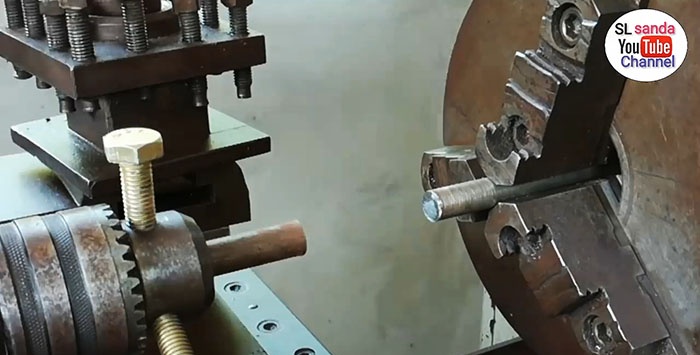
Les combinacions de materials poden ser molt diferents, fins i tot aquelles que no es poden soldar de la manera habitual. No hi ha restriccions en aquest sentit per a la soldadura per fricció.
En el nostre cas, fixem la vareta al capçal mitjançant tres cargols cargolats als forats del mandril, espaiats uniformement al voltant de la circumferència a 120 graus. Amb la seva ajuda, realitzem l'alineació respecte de la vareta subjectada al mandril apretant o afluixant un o un altre cargol.
Portem el capçal fins que les varetes s'aturin de punta a punta i el subjectem o subjectem amb la mà per tal d'augmentar la força de subjecció durant el procés de soldadura, que requereix la tecnologia d'aquest mètode de soldadura.
Encenem la màquina, com a resultat de la qual cosa la vareta subjectada al mandril de la màquina comença a girar. En el nostre cas, la vareta fixada al capçal està immòbil, però en principi pot girar en sentit contrari, la qual cosa reduiria el temps del procés.
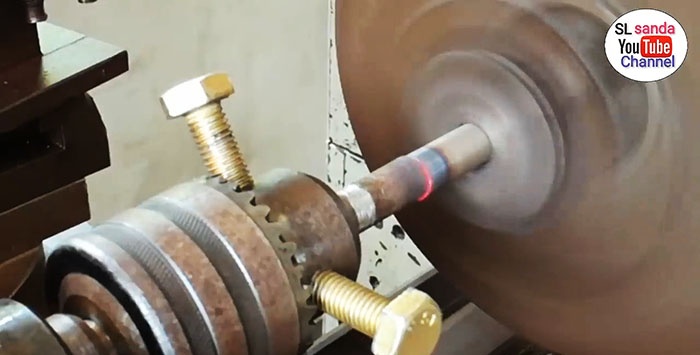
Aviat veurem colors tacats que comencen al punt de contacte de les varetes i s'estenen al llarg d'elles en direccions oposades, la qual cosa és un signe directe del ràpid escalfament del metall com a conseqüència de la fricció.
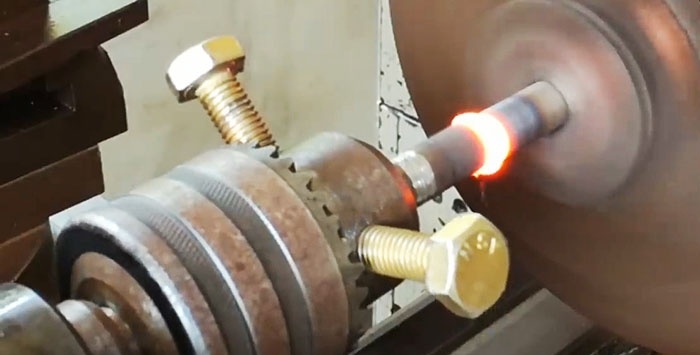
Al cap d'un altre temps, el metall de la zona de contacte brillarà brillantment i començarà a esprémer en forma d'anell més enllà de les dimensions de les barres.Aquest anell també contindrà rebava: escama, greix no cremat, inclusions sòlides no metàl·liques, etc.
En el moment de la brillantor més brillant al punt de contacte, la màquina s'ha d'apagar bruscament perquè el metall de les dues varetes s'enganxi. Al mateix temps, si el capçal no s'ha fixat, cal augmentar gradualment la pressió sobre ell per compensar el volum de metall desplaçat a la zona de contacte i obtenir una connexió més forta i de més qualitat.
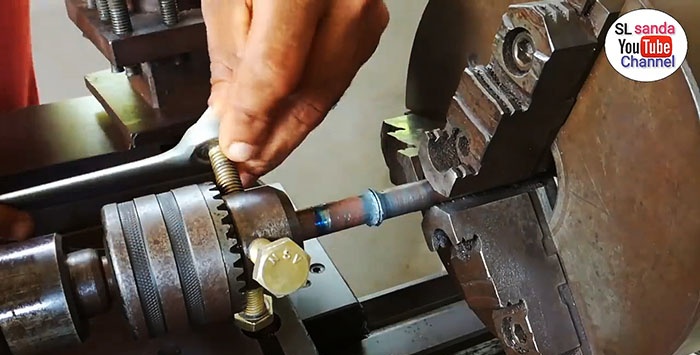
Després d'esperar fins que la brillantor s'aturi (i això és un senyal que el metall s'ha fixat completament), podeu afluixar els cargols de fixació i treure el capçal. Ara només queda comprovar la qualitat de la soldadura per fricció.
Per fer-ho, torneu a encendre la màquina i detecteu una lleugera desviació de la vareta soldada, conseqüència d'una alineació inexacta durant la instal·lació al principi. Aquest defecte es pot eliminar girant i eliminant la rebava extruïda a la zona de contacte.
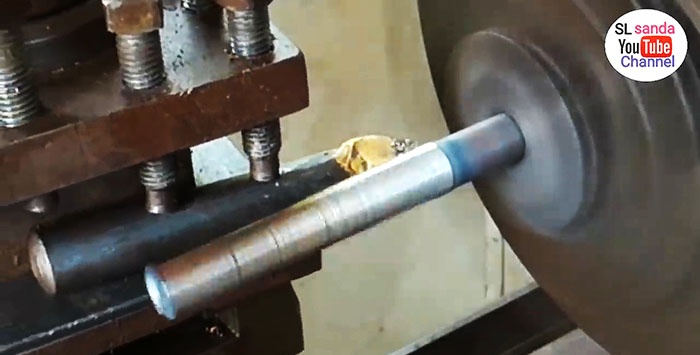
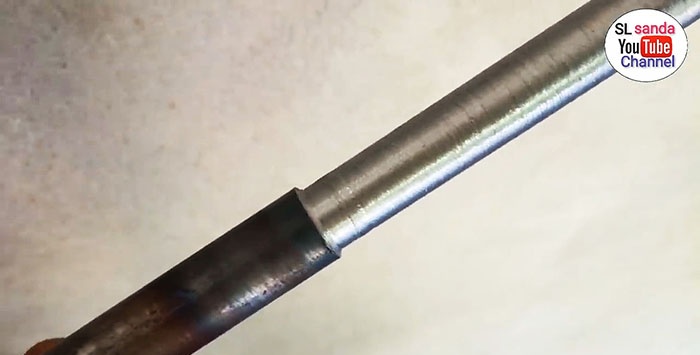
Una penetració més profunda del metall mostra que no hi ha cap característica visible a la zona de soldadura de les dues varetes. Sembla que aquest no és el punt de contacte entre dues varetes, sinó el cos d'una d'elles.
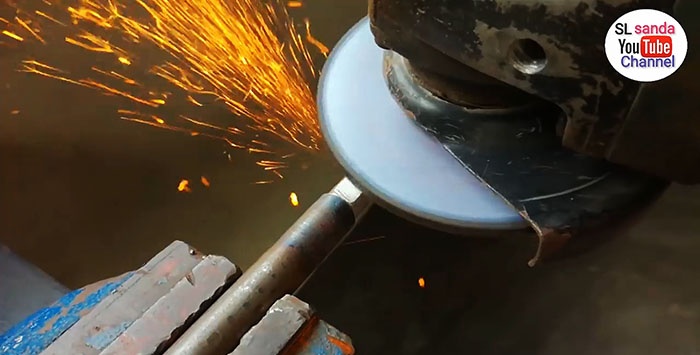
Realitzem el següent control de qualitat de la soldadura per fricció. Fixem les varetes connectades d'aquesta manera en un vici i utilitzem un disc de mòlta per crear un "prestatge" a la zona de contacte, i de nou estem convençuts de l'homogeneïtat del metall, que també indica la qualitat de la soldadura.
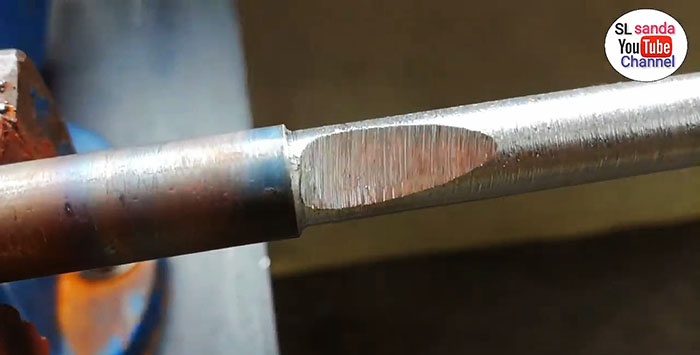
Connexió per cargol
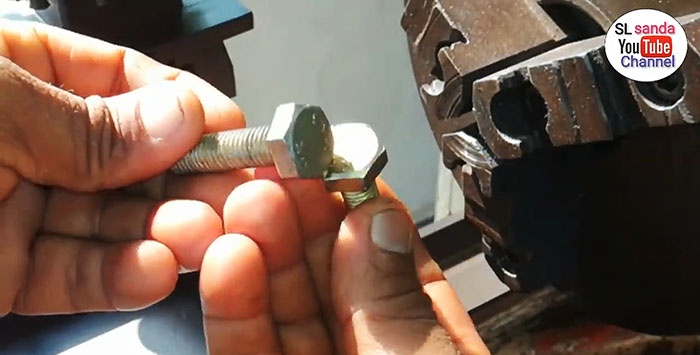
La soldadura per fricció es pot utilitzar per unir capçals i cargols produïts en massa. El procés no és diferent del procés amb barres: un cargol està subjectat al mandril de la màquina i l'altre al capçal.
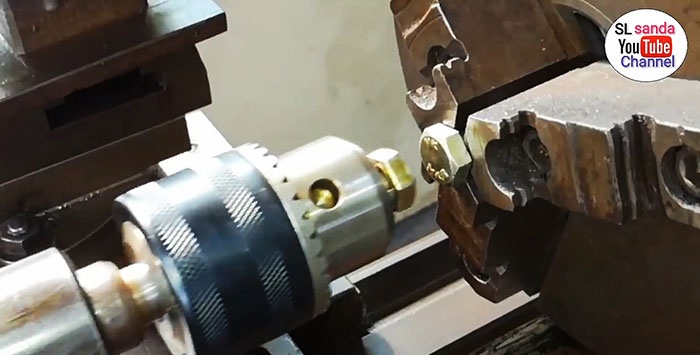
Amb l'ajuda d'aquest últim, els cargols es posen en contacte amb els capçals i s'engega la màquina. També cal augmentar la força de tancament i capturar el moment de la soldadura per tal d'apagar l'accionament a temps.
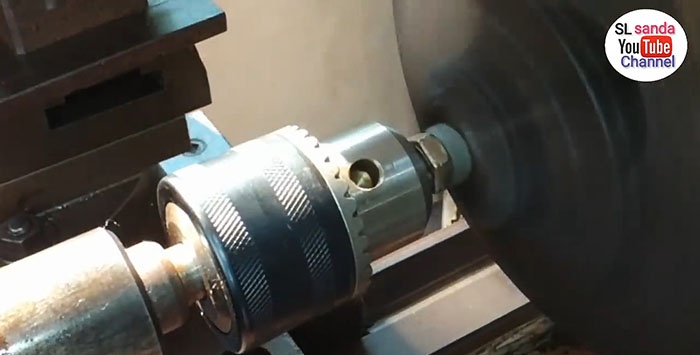
La soldadura per fricció es pot utilitzar per unir materials difícils o impossibles de soldar amb altres tipus: acer i alumini, acers austenètics i perlítics. També es pot utilitzar per unir fàcilment peces de plàstic.
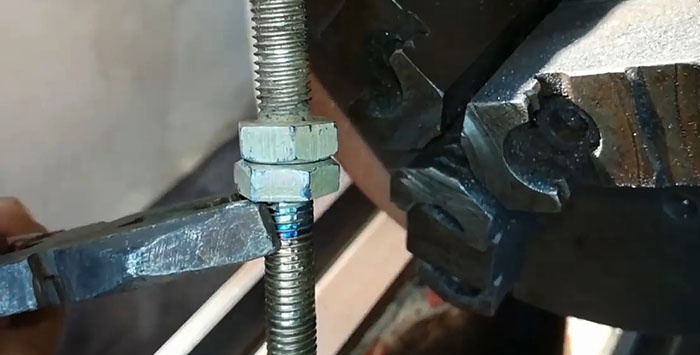
Els càlculs i la pràctica amb unió per fricció demostren que aquest mètode és més adequat per a peces el diàmetre de les quals es troba entre 6 i 100 mm. Soldar varetes amb un diàmetre superior a 200 mm no és rendible econòmicament, ja que el procés requerirà més potència (0,5 mil kW) i força axial (3 × 106 N). No es podran connectar barres amb un diàmetre inferior a 3,5 mm mitjançant aquest mètode a causa de la necessitat de proporcionar altes velocitats (200 rpm) i la dificultat de determinar quan apagar l'accionament.
Mira el vídeo
Classes magistrals similars
Particularment interessant
Comentaris (1)