Drivhus med hjemmelavet ramme
Efter at jeg så forskellige præfabrikerede drivhuse købt hos forskellige detailforretninger, dannede jeg mig en sikker mening om disse strukturers skrøbelighed. Det, der især fik mig til at grine, var monteringen af tynde galvaniserede plader med skruer næsten direkte fra et børnebyggesæt. Min personlige grund ligger på en bakke, der er stort set ingen træer, ingen åben plads, så vinden er meget stærk, og drivhusets "fabriks" præfabrikerede struktur vil bestemt ikke modstå vindstødene. Senere, under installationen i blæsevejr, var jeg overbevist om, at min antagelse var korrekt; den i forvejen næsten fastgjorte polycarbonatplade, på grund af sin vinding, slap af som en fjer og smed stigen tilbage, der vejede 50 kg.
Opgaven var derudover at skaffe et drivhus med dimensioner på 3 meter bredt, 8 meter langt, med mulighed for at en person af gennemsnitshøjde kunne bevæge sig frit i det, dvs. op til 1,8 meter. Derfor besluttede jeg at lave et drivhus af polycarbonat med en ramme fra en metalprofil af mit eget design.
Rammen var hovedsageligt lavet af letvægts metalrør og vinkler. "Tag"-konstruktionen blev lavet af en rygtype, et almindeligt sadeltag, testet for pålidelighed.Højden på højderyggen vil variere alt efter vejrforholdene i dit område, jeg valgte en spærvinkel på 45 grader, så sneen ruller let af om vinteren. Under installationen blev spærene forstærket med en tværgående bjælke, forbundet med en trekant.
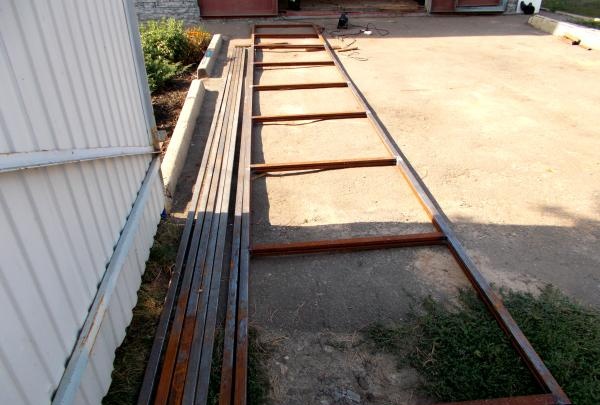
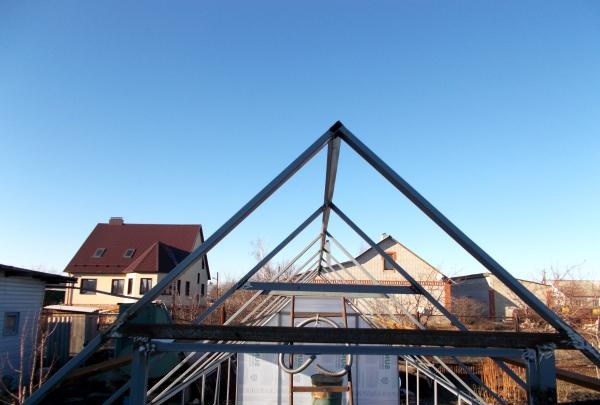
Standard polycarbonatplader har følgende dimensioner: tykkelse 4 mm, bredde 2,1, længde 6 meter. Jeg henleder opmærksomheden på kvaliteten af polycarbonat, jeg brugte den russiske producent Sunnex, lad os sige, at det er af gennemsnitlig kvalitet, der er et mere holdbart og tæt materiale, dette er mærkbart i afbøjning, struktur og vægt og ultraviolet transmission. Valget er dit, men du bør ikke spare for at undgå, at den knækker under belastning fra sne eller vind.
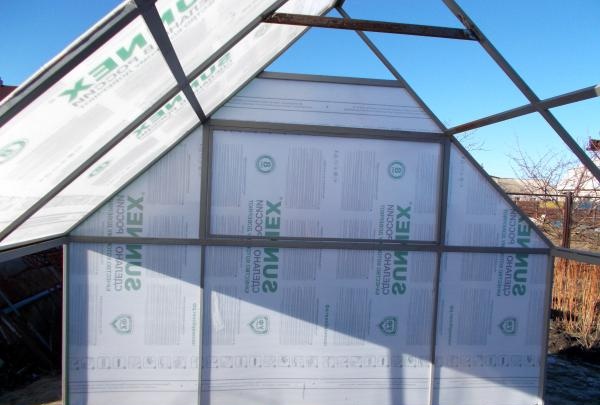
Konstruktion Traditionelt startede jeg med at lægge et lille fundament, da drivhuset i mit tilfælde skulle være solidt sikret, og også for at undgå skævheder. Jeg brugte tynde fundamentblokke og sveller i armeret beton. I svellernes "standard" huller placerede jeg bolte til kraftige fastgørelser af rammen rundt om hele drivhusets omkreds. Ved installation af hele rammestrukturen, svejset i dele, tjente disse fastgørelseselementer som en fiksering til den videre installation af det øvre gitter (der var dog nødvendige assistenter til at understøtte rammen i øjeblikket).
Caracas lavede det af et 20*40 mm metalprofilrør med et gitter på op til 1 meter, ellers kan polycarbonatet svigte om vinteren på grund af iskold sne. Jeg lavede de nederste ender af et 35*35 mm hjørne, så døren lukkede ved samlingen.
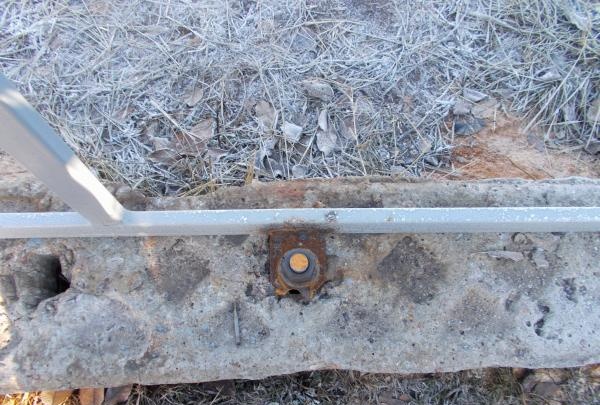
Ikke et uvigtigt punkt: vi designer rammen på en sådan måde, at vi skærer polycarbonatet mest økonomisk, nemlig vi laver sidevæggene 1,05 meter høje, idet vi tager højde for at skære arket i halve på langs. Spær 2,1 meter lange, så to hele plader kan fastgøres til taget og en ekstra plade kan skæres i stykker på 2 meter hver.
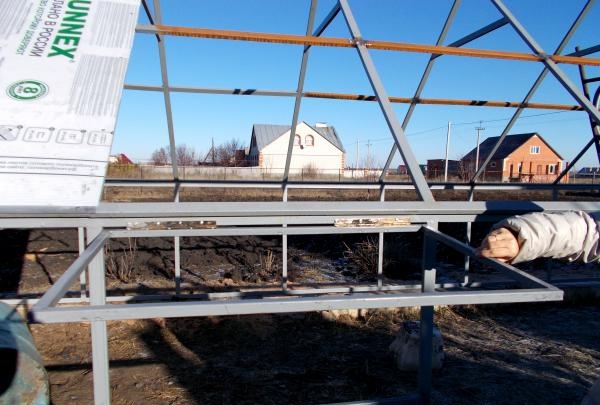
Udover døren sørgede jeg for to vinduer i drivhuset til ventilation, på læsiden for enden og siden af strukturen, svejset af en letvægts 20*20 mm profil. Jeg har installeret vinduerne på klaverhængsler; de er ret tynde og forstyrrer ikke polykarbonat, der passer tæt til rammen.
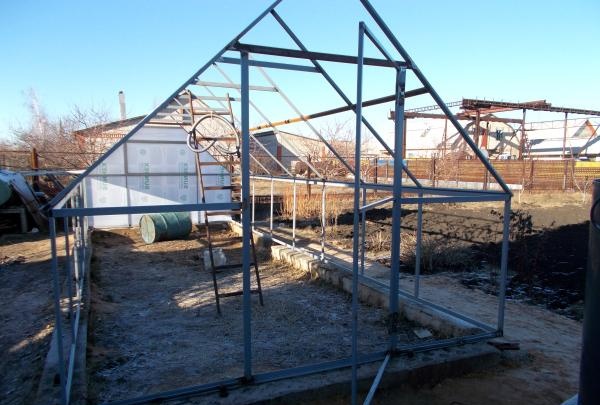
Alle samlinger og huller i polycarbonatet blev fyldt med silikone, og revnerne i bunden blev fyldt med polyurethanskum. Rammen blev slebet i svejsepunkterne, malet med anti-korrosionsmasse og maling.
Materiale til drivhusbyggeri:
- polycarbonat 2,1*6 m. – 5 ark;
- metalprofilrør 20*40 mm – 120 meter;
- metalprofilrør 20*20 mm – 18 meter;
- selvskærende skruer med en presseskive og en boremaskine - 1000 stykker;
- fundamentblokke (sovende) med en samlet længde på 22 meter;
- sand til at lægge fundamentet;
- fastgørelser og bolte til rammen;
- anti-korrosions maling;
- dør- og klaverhængsler, dørhåndtag;
- svejseelektroder 3 kg.
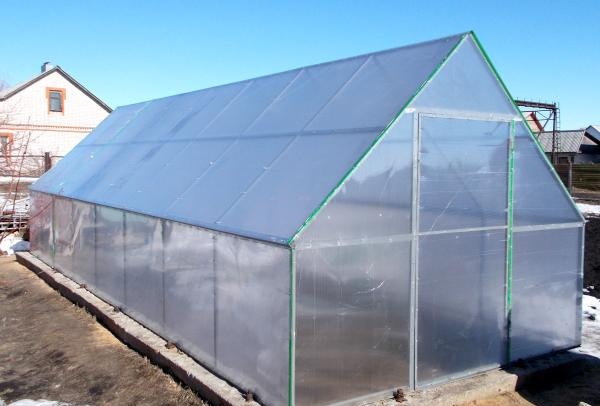
Fordele ved drivhuset: holdbar gavlkonstruktion; stiv fastgørelse af rammen; nødvendige geometriske dimensioner; Brugervenlighed; mulighed for økonomisk skæring af materiale; få led.
Ulemper: krydset mellem taget og rammens sidegear viste sig at være forstærket med to profiler, hvilket ikke er økonomisk rentabelt.
Opgaven var derudover at skaffe et drivhus med dimensioner på 3 meter bredt, 8 meter langt, med mulighed for at en person af gennemsnitshøjde kunne bevæge sig frit i det, dvs. op til 1,8 meter. Derfor besluttede jeg at lave et drivhus af polycarbonat med en ramme fra en metalprofil af mit eget design.
Rammen var hovedsageligt lavet af letvægts metalrør og vinkler. "Tag"-konstruktionen blev lavet af en rygtype, et almindeligt sadeltag, testet for pålidelighed.Højden på højderyggen vil variere alt efter vejrforholdene i dit område, jeg valgte en spærvinkel på 45 grader, så sneen ruller let af om vinteren. Under installationen blev spærene forstærket med en tværgående bjælke, forbundet med en trekant.
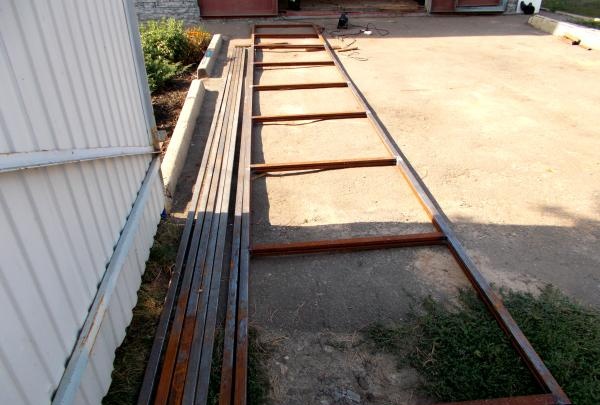
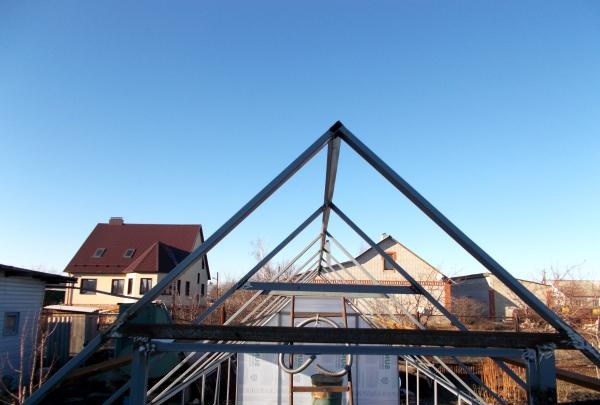
Standard polycarbonatplader har følgende dimensioner: tykkelse 4 mm, bredde 2,1, længde 6 meter. Jeg henleder opmærksomheden på kvaliteten af polycarbonat, jeg brugte den russiske producent Sunnex, lad os sige, at det er af gennemsnitlig kvalitet, der er et mere holdbart og tæt materiale, dette er mærkbart i afbøjning, struktur og vægt og ultraviolet transmission. Valget er dit, men du bør ikke spare for at undgå, at den knækker under belastning fra sne eller vind.
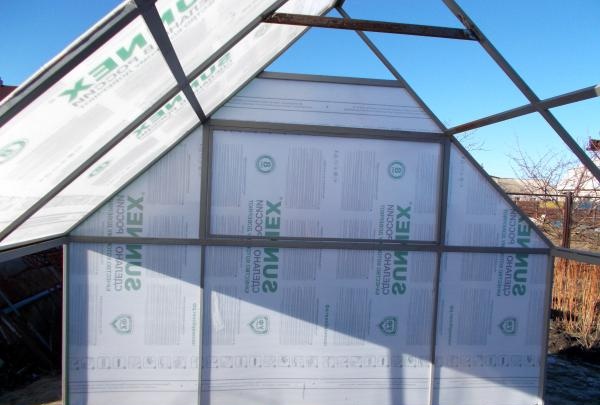
Konstruktion Traditionelt startede jeg med at lægge et lille fundament, da drivhuset i mit tilfælde skulle være solidt sikret, og også for at undgå skævheder. Jeg brugte tynde fundamentblokke og sveller i armeret beton. I svellernes "standard" huller placerede jeg bolte til kraftige fastgørelser af rammen rundt om hele drivhusets omkreds. Ved installation af hele rammestrukturen, svejset i dele, tjente disse fastgørelseselementer som en fiksering til den videre installation af det øvre gitter (der var dog nødvendige assistenter til at understøtte rammen i øjeblikket).
Caracas lavede det af et 20*40 mm metalprofilrør med et gitter på op til 1 meter, ellers kan polycarbonatet svigte om vinteren på grund af iskold sne. Jeg lavede de nederste ender af et 35*35 mm hjørne, så døren lukkede ved samlingen.
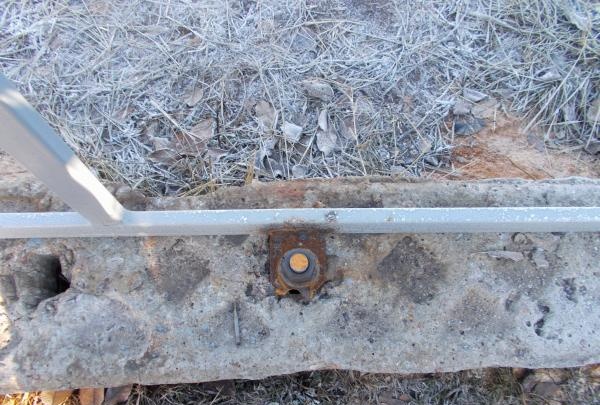
Ikke et uvigtigt punkt: vi designer rammen på en sådan måde, at vi skærer polycarbonatet mest økonomisk, nemlig vi laver sidevæggene 1,05 meter høje, idet vi tager højde for at skære arket i halve på langs. Spær 2,1 meter lange, så to hele plader kan fastgøres til taget og en ekstra plade kan skæres i stykker på 2 meter hver.
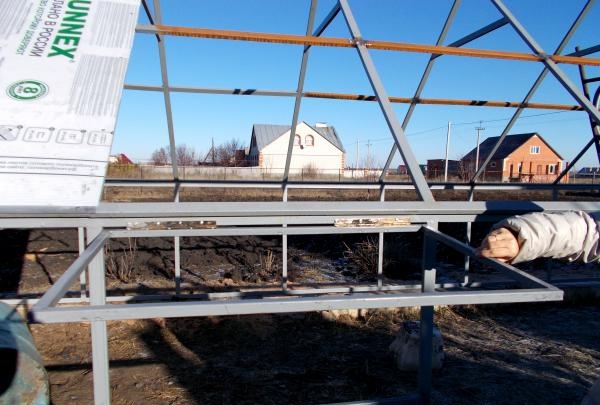
Udover døren sørgede jeg for to vinduer i drivhuset til ventilation, på læsiden for enden og siden af strukturen, svejset af en letvægts 20*20 mm profil. Jeg har installeret vinduerne på klaverhængsler; de er ret tynde og forstyrrer ikke polykarbonat, der passer tæt til rammen.
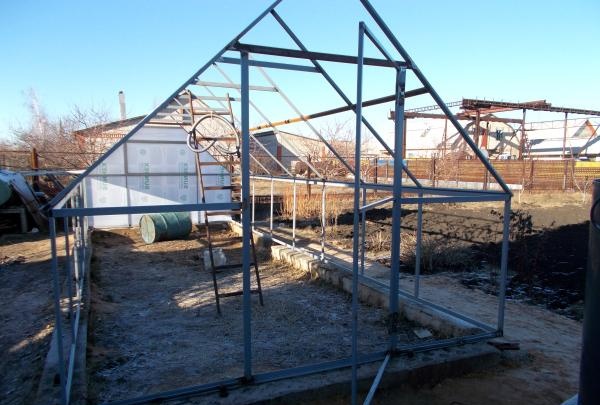
Alle samlinger og huller i polycarbonatet blev fyldt med silikone, og revnerne i bunden blev fyldt med polyurethanskum. Rammen blev slebet i svejsepunkterne, malet med anti-korrosionsmasse og maling.
Materiale til drivhusbyggeri:
- polycarbonat 2,1*6 m. – 5 ark;
- metalprofilrør 20*40 mm – 120 meter;
- metalprofilrør 20*20 mm – 18 meter;
- selvskærende skruer med en presseskive og en boremaskine - 1000 stykker;
- fundamentblokke (sovende) med en samlet længde på 22 meter;
- sand til at lægge fundamentet;
- fastgørelser og bolte til rammen;
- anti-korrosions maling;
- dør- og klaverhængsler, dørhåndtag;
- svejseelektroder 3 kg.
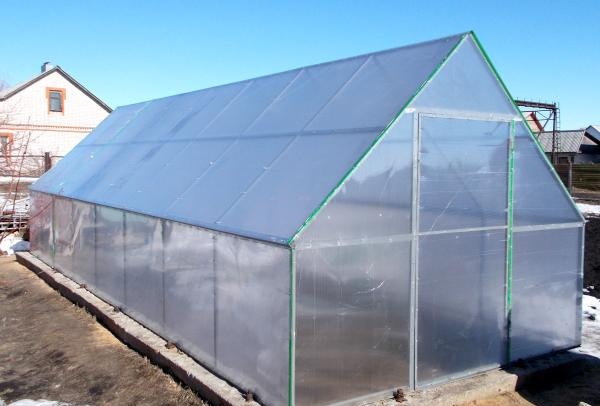
Fordele ved drivhuset: holdbar gavlkonstruktion; stiv fastgørelse af rammen; nødvendige geometriske dimensioner; Brugervenlighed; mulighed for økonomisk skæring af materiale; få led.
Ulemper: krydset mellem taget og rammens sidegear viste sig at være forstærket med to profiler, hvilket ikke er økonomisk rentabelt.
Lignende mesterklasser
Særlig interessant
Kommentarer (0)