Støbning af plastdele derhjemme. Så let som en pie
Fremstillingen af støbeprodukter ved hjælp af moderne materialer er blevet ret tilgængelig, ganske enkel og billig. Overvej muligheden for at bruge polyurethan til at hælde og silikone til at skabe formen.
Vil behøve
Til vores arbejde vil vi bruge ganske tilgængelige og billige materialer og produkter:
- silikone "ELASTOLUX-M" til fremstilling af forme;
- silikone "ELASTOFORM" til fremstilling af substratet;
- separator baseret på petroleum eller vaseline;
- bøjning til formen med en samlet vægt på 1 kg;
- støbning af polyurethan "UNIKAST 9" (base, del A);
- hærder (del B);
- præcisionsvægte;
- plastik glas.
Teknologi til støbning af polyurethanprodukter i silikoneforme
Først og fremmest skal du printe en mastermodel med et gating-system på en 3D-printer. Eller tag en færdig del, der skal gentages, lim tandstikker ind i rollen som sprues. Det vil være nødvendigt at lave en genanvendelig silikoneform.
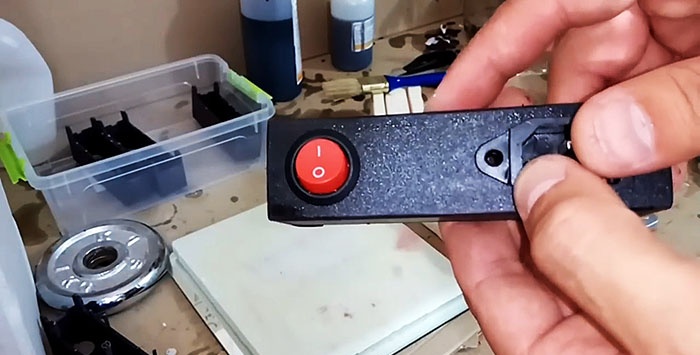
Til det bruger vi silikone, som er meget elastisk og tilstrækkeligt holdbart.Til et basissubstrat med en tykkelse på 10-15 mm er billigere to-komponent silikone af typen ELASTOFORM velegnet.
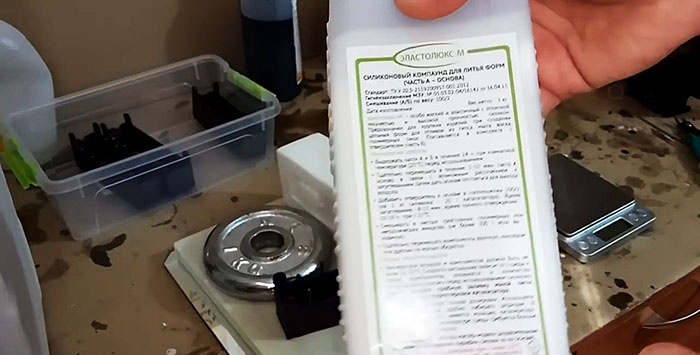
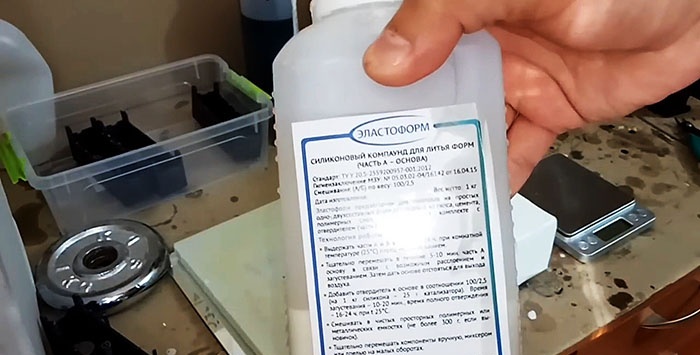
Lavet silikoneform.
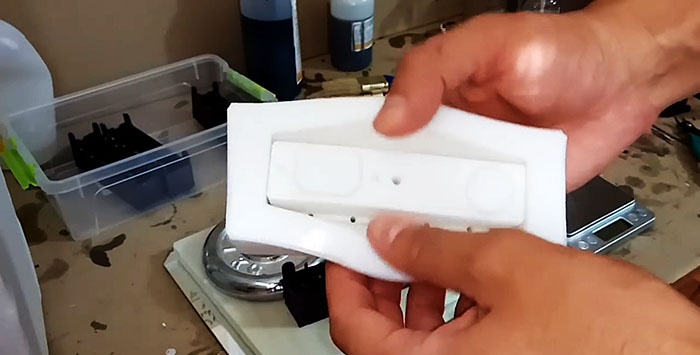
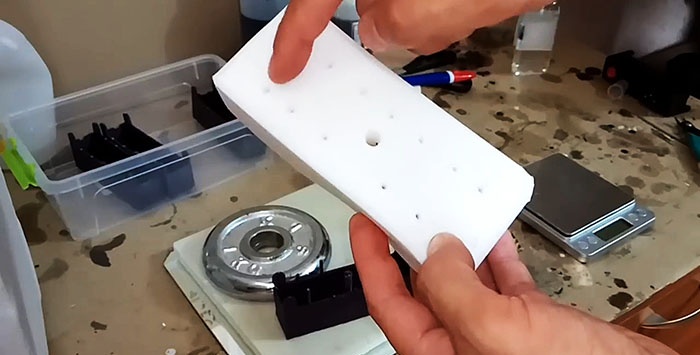
Hvordan fungerer støbeprocessen?
Vi placerer silikoneformen på underlaget. Hvis det skal bruges gentagne gange, så smør det med jævne mellemrum med en separator baseret på petroleumsgelé.
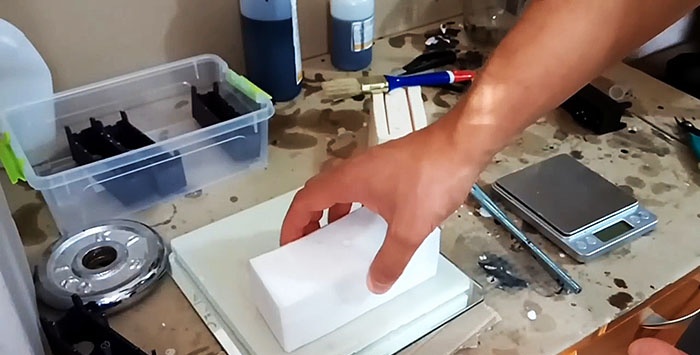
Vi presser silikoneformen ovenpå med en spredt belastning (tryk), der vejer op til et kilo. For at sikre, at støbematerialet hældes præcist og hurtigt, bruger vi en papirtragt. Herefter kan vi antage, at formen er klargjort til støbning.
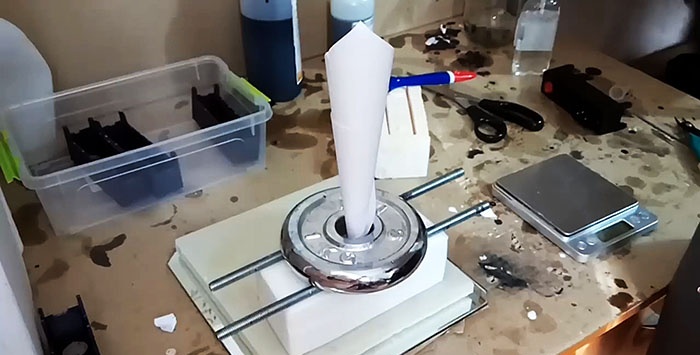
Til fyldning tager vi den billigste støbepolyurethan "UNIKAST 9" (del A) og hærder (del B), som vi blander i forholdet 1:0,6.
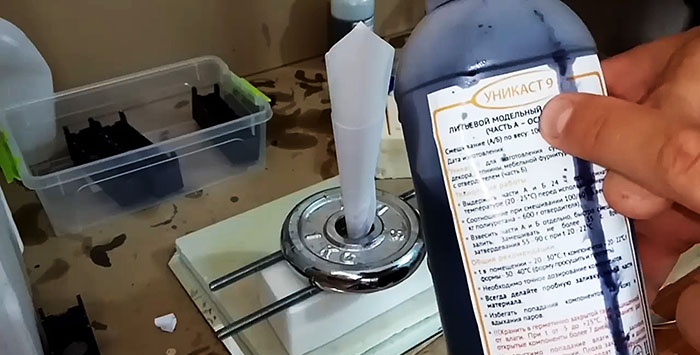
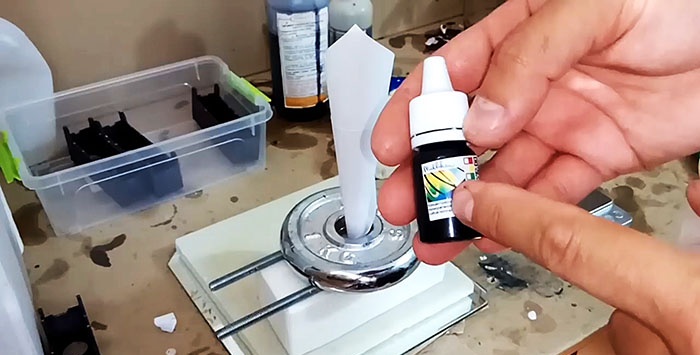
Til blanding af høj kvalitet har du brug for præcisionsvægte og en plastikkop. Du kan tilføje et hvilket som helst farvestof til basen, som sælges separat. For 1 kg polyurethan skal du bruge 90-100 dråber farvestof.
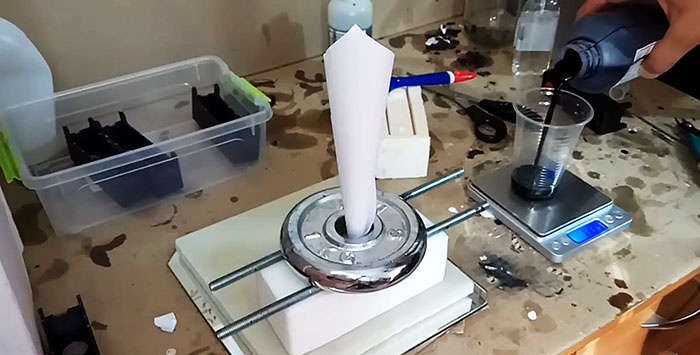
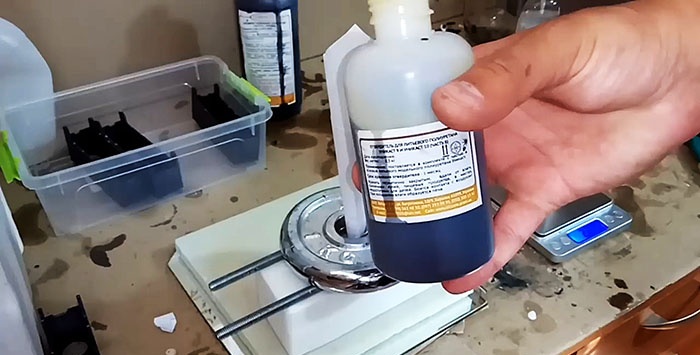
Hæld 22 gram flydende polyurethan og 13,2 gram hærder i et glas på en vægt og rør grundigt i 30 sekunder, ikke mere, da det allerede vil begynde at hærde. Ved omrøring vil vi mærke, at glasset varmes op, hvilket betyder, at polymerisationsprocessen er begyndt. Blandingen er klar til at hælde.
Vi hælder blandingen uden afbrydelse, indtil flydende polyurethan kommer ud af indløbene. Primær hærdning vil tage omkring to minutter, og fuldstændig hærdning vil tage 10-15 minutter, men det er bedre at holde fyldet i formen i 20-30 minutter.
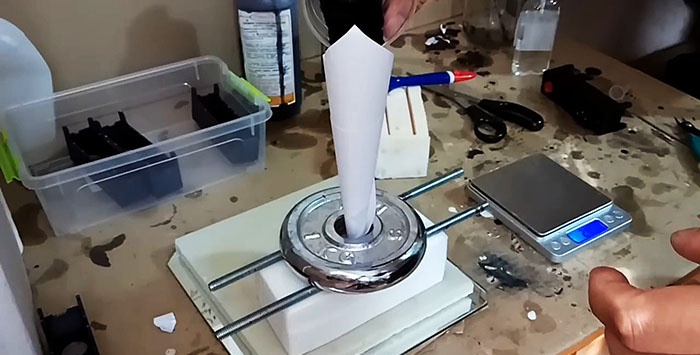
Efter en halv time begynder vi at fjerne polyurethanstøbningen fra silikoneformen.
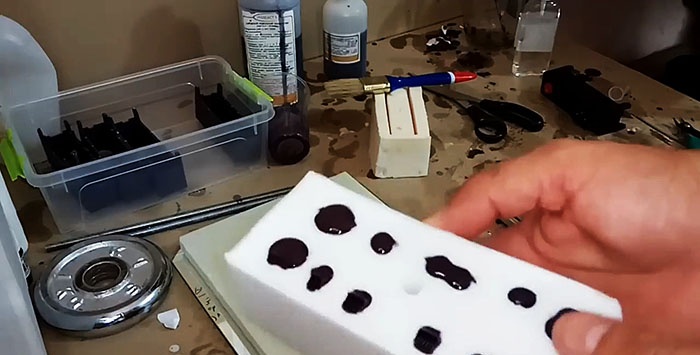
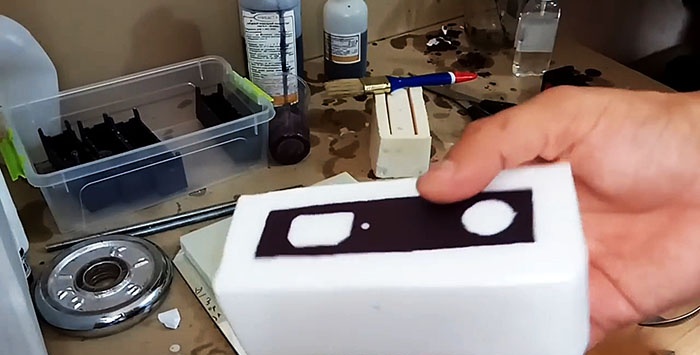
Vi brækker først papirtragten af med overskydende polyurethan frosset i den, derefter det overskydende, der stikker ud fra indløbene, sammen med "benene". Dette vil gøre det nemmere for os at fjerne det støbte produkt fra formen.
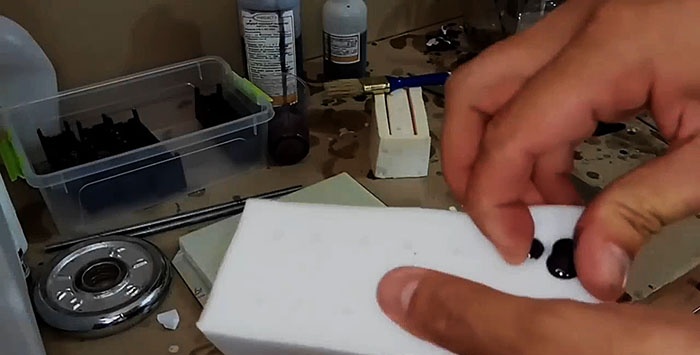
Derudover er silikoneformen meget fleksibel, hvilket også gør det nemt at fjerne støbningen fra den uden besvær.
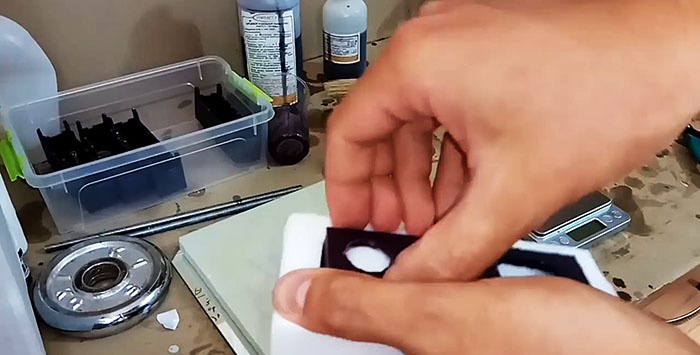
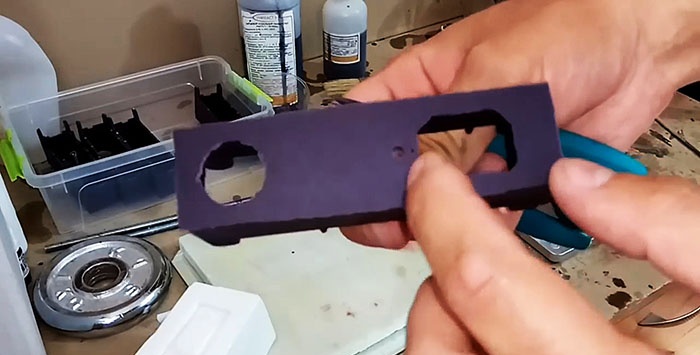
Tilbage er kun at bearbejde hullerne let, brække af eller skære indløbene af og bore hullerne med et bor. Efter dette er det støbte produkt praktisk talt ikke forskelligt fra masterformen.
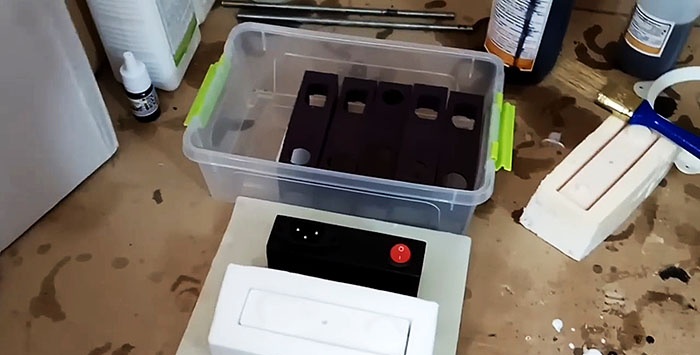
Sammenligning af støbemetode og 3D-print
Casting sammenlignet med 3D-print er en hurtig proces. At printe sådan en boks på en 3D-printer vil det tage 4,0-4,5 timer. I dette tilfælde viser 3D-modellen sig ofte at være defekt, og alt skal startes forfra. Støbeprocessen tager maksimalt 30 minutter. Det næste punkt er billighed. Casting er mere end 3 gange billigere end 3D-print.