Full compressor from a refrigerator
Recently, compressors have gained popularity among tinkerers. They are made on the basis of almost any engine, calculating the power of the base unit depending on the number of consumers. For home workshops, do-it-yourself compressor units are in demand.
Refrigerator compressors often remain operational after the refrigerator itself breaks down or becomes obsolete. They are low-power, but unpretentious in operation. And many craftsmen make quite decent home-made installations from them. Let's see how you can do this yourself.
Required parts:
Tools:
Refrigerator compressors often remain operational after the refrigerator itself breaks down or becomes obsolete. They are low-power, but unpretentious in operation. And many craftsmen make quite decent home-made installations from them. Let's see how you can do this yourself.
Parts and materials
Required parts:
- 11 kg propane tank;
- 1/2" coupling with internal thread and plug;
- Metal plates, width – 3-4 cm, thickness – 2-4 mm;
- Two wheels with mounting platform;
- Refrigeration compressor from a refrigerator;
- 1/4 inch adapter;
- Brass check valve connector;
- Copper pipe connector ¼ inch – 2 pcs;
- Equipment for adjusting compressor pressure;
- Bolts, screws, nuts, fumlenta.
Tools:
- Welding inverter;
- Screwdriver or drill;
- Metal cutters with titanium coating;
- A turbine or drill with abrasive attachments;
- Metal brush;
- Roller for copper tubes;
- Adjustable wrenches, pliers.[list]
Assembling the compressor
Step one - preparing the receiver
We rinse the empty liquefied propane cylinder thoroughly with water. It is very important to remove all remaining explosive gas mixtures in this way.
We overlap the adapter by 1/4 inch into the end hole of the cylinder. We scald it on all sides by welding and seal it with a screw.
We place the receiver on wheels and supports. To do this, we take pieces of metal plates, bend them at an angle and weld them onto the body from the bottom. We weld wheels with a mounting platform to the corners. We mount a support bracket in the front part of the receiver.Step two - install the compressor
On top of the receiver we place mounting frames for the compressor made of metal plates. We check their position with a bubble level and scald them. We seat the compressor on the clamping bolts through rubber shock-absorbing pads. This type of compressor will have only one outlet through which air is pumped into the receiver. The remaining two, which suck in air, will remain untouched.Step three - attach the check valve and adapter to the equipment
We select a metal cutter of suitable diameter and use a screwdriver or drill to make a hole in the housing for the coupling. If there are protruding shapes on the coupling body, grind them down with a drill (you can use a regular electric sandpaper or grinder with a grinding disc for this).
Place the coupling in the hole and weld it around the circumference. Its internal thread must match the pitch and diameter of the mounting thread on the check valve.
We use a brass check valve for small compressors. We plug the pressure release outlet with a suitable bolt, since the control assembly already has a release valve.
To install a pressure switch or pressure switch with all the control equipment, we mount another 1/4-inch adapter. We make a hole for it in the center of the receiver, not far from the compressor.
We tighten the check valve with a 1/2-inch adapter.
We connect the compressor cylinder outlet and the check valve with a copper tube. To do this, we flare the ends of the copper tubes with a special tool and connect them with brass threaded adapters. We tighten the connection with adjustable wrenches.Step four - install the control equipment
The assembly of control equipment consists of a pressure switch (pressostat) with a control sensor, a safety valve or pressure relief valve, an adapter-coupling with external thread and several taps and pressure gauges.
First of all, we install the pressure switch. It must be slightly raised to the level of the compressor. We use an extension coupling with an external thread and screw the relay through the sealing tape.
Through the adapter we install a pressure regulation sensor with pressure gauges. We complete the assembly with a pressure relief valve and two taps for the hose outlets.Step five - connect the electrical
Using a screwdriver, we disassemble the housing of the pressure switch, opening access to the contacts. We connect the 3-core cable to the contact group, and distribute each of the wires according to the connection diagram (including grounding).
Similarly, we connect the power cable, equipped with a plug for a power outlet. Screw the relay cover back into place.Step six – revision and test run
To carry the compressor unit, we attach a special handle to the compressor frame. We make it from scraps of profile square and round pipes. We attach it to the clamping bolts and paint it in the color of the compressor.
We connect the installation to a 220 V network and check its functionality. According to the author, to obtain a pressure of 90 psi or 6 atm, this compressor needs 10 minutes. Using an adjusting sensor, the activation of the compressor after a pressure drop is also regulated from a certain indicator displayed on the pressure gauge. In his case, the author configured the installation so that the compressor would turn on again from 60 psi or 4 atm.
The last operation left is an oil change. This is an important part of the maintenance of such installations, because they do not have an inspection window. And without oil, such machines can work for only a short time.
We unscrew the drain bolt at the bottom of the compressor and drain the waste into a bottle. Turning the compressor on its side, fill in a little clean oil and screw the plug back on. Now everything is in order, you can use our compressor unit!Conclusion
Compressor equipment is considered low-power and practically household. It is unlikely that it will handle the work of several pneumatic tools at once. But it can be used for low-power devices, for example, for airbrushing or tire inflation. It's also a great way to reuse an unwanted refrigeration compressor and give it a second life in your home workshop.Watch the video
Similar master classes
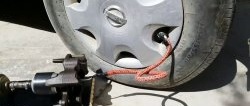
12V compressor from refrigerator compressor
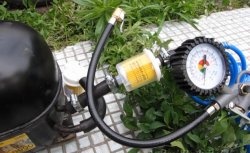
Refrigerator compressor for inflating tires
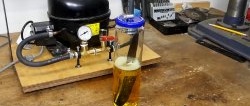
How to convert a refrigerator compressor into a vacuum pump
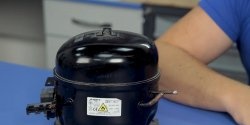
Piston compressors for refrigerators - types and principles of operation
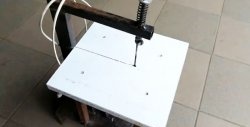
Jigsaw from a compressor from a refrigerator
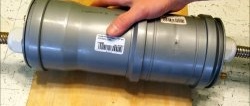
How to assemble a simple refrigerator for a distiller
Particularly interesting
Comments (11)