Molinillo de motor de lavadora.
Las lavadoras suelen fallar sin que sus motores estén en pleno funcionamiento. Su potencia y velocidad real son muy adecuadas para el uso de este recambio en la fabricación de máquinas caseras. Resulta que un accionamiento eléctrico de este tipo también es una solución ideal para instalarlo en una amoladora casera.
Materiales usados
No hizo falta mucho para hacer:
- motor de máquina de escribir;
- su condensador de arranque original;
- parte de la cubierta de chapa de la máquina;
- 4 patas de goma de la lavadora;
- hoja de madera contrachapada;
- un trozo de tubo de 5 cm de paredes gruesas con un diámetro interior de 14 mm;
- 2 rodamientos idénticos;
- sellador de vidrio;
- chapa con una sección transversal de 8 mm;
- esquina 63x63 mm;
- tubo perfilado 40x40 mm;
- tubo perfilado 30x30 mm;
- tuerca extendida;
- fleje de acero con una sección transversal de 10 mm;
- amortiguador de gas para muebles;
- botón de encendido;
- tapones de plástico de 30x30 y 40x40 mm;
- pernos y tuercas M12, M10, M6 y M5.
El detalle principal de toda la estructura:
El proceso de hacer una amoladora a partir del motor de una lavadora.
Primero hice rodillos tensores.
Son de metal de fábrica. El nuestro será casero, de madera.Para su fabricación es adecuada la madera contrachapada resistente a la humedad, su espesor no es tan importante.
Necesitas hacer panqueques con él, que luego se pegarán formando un rodillo. Primero, instalo una broca para madera con un diámetro de 102 mm en el taladro. Corté 9 panqueques de madera contrachapada para el rodillo impulsor. El número de círculos depende del grosor de la madera contrachapada existente y del ancho de la cinta que se utilizará luego.
Ahora es necesario pegar los panqueques. Primero tendrás que lijarlas un poco para quitar las astillas de la corona. Engraso los lados de los círculos con pegamento PVA y formo un rodillo ancho de varias capas. Para un pegado normal, fijo la pieza de trabajo debajo de una prensa.
Mientras el rodillo impulsor se seca, puede hacer un rodillo impulsado. Utiliza una corona de 64 mm. Nuevamente, con un taladro, corté 9 panqueques de la misma madera contrachapada y los pegué bajo presión.
Para evitar que los rodillos se deslaminen después de secarse, les hice 2 agujeros laterales y además apreté todo con un par de tornillos en cada lado.
Equilibrio los rodillos en un torno, rectificando un poco las irregularidades y suavizando las piezas de trabajo.
Para asegurar el rodillo impulsor al eje del motor, necesita hacer un adaptador. Para ello se utiliza un trozo de tubo de paredes gruesas.
En la mayoría de los casos se necesitará un tubo con un diámetro interior de 14 mm. Para apretar el tubo en el eje del motor eléctrico, hago un agujero y corto una rosca M5. En el segundo extremo del tubo soldé un perno M12.
Amplié el orificio del rodillo impulsor para que se ajuste al tubo a la mitad de su profundidad. La parte estrecha restante contendrá la rosca del perno M12.
Debe instalar un par de cojinetes en el rodillo impulsado, uno a cada lado. Su tamaño no es tan importante, puedes utilizar cualquiera, siempre que tenga un diámetro interno adecuado.Preparo las carcasas de los cojinetes en un torno.
Para suavizar la superficie de los rodillos, decidí cubrirlos con pegamento para vidrio. Para ello, los fijo uno a uno en un torno y los recubro uniformemente en todo el perímetro y los extremos.
Ahora necesitas hacer un marco para instalar el motor eléctrico. Como base utilizo una chapa de metal con una sección de 8 mm. Recorté un rectángulo con lados de 220 por 310 mm.
Para montar directamente el motor necesitarás 2 esquinas. Estoy preparando piezas de 130 mm de largo. La curva 63 era ideal para el motor eléctrico.
Coloco la placa de acero sobre una superficie plana, instalo el ángulo y el motor, luego hago marcas para perforar los orificios de montaje con un taladro de 6 mm.
Para evitar que la esquina interfiera con el perno de fijación del rodillo impulsor en el futuro, debe seleccionar metal cerca del eje. La forma más sencilla es recortar un pequeño triángulo.
Monto los ángulos en el motor eléctrico usando cuatro tuercas M6 con una arandela de presión.
Instalo el motor con los soportes en su lugar, hago marcas y sueldo las esquinas a la base de la máquina.
Corté un trozo de 300 mm de largo de un tubo perfilado de 40x40. Hago otra pieza del mismo largo, pero a partir de un tubo perfilado de 30x30 mm.
Ahora necesitas hacer un mecanismo para ajustar la cinta. Para empezar, tomo una nuez alargada y muelo su borde.
Lo sueldo a una fleje de acero con una sección transversal de 10 mm. Hago un agujero en la tira y corto una rosca M10 para el perno al que se fijará el rodillo accionado.
Luego soldé una pieza de trabajo en forma de L de un tubo cuadrado de 30x30 previamente cortado. Le soldé tuercas para asegurar la tira hecha. También aseguré la tuerca y el perno en la pared perpendicular del cuadrado opuesto a la cabeza del perno en el que se montará el rodillo impulsado.Apretando o desatornillando un perno corto, puede cambiar el ángulo del rodillo, ajustando así la máquina.
Coloco un tubo perfilado de 40x40 verticalmente sobre la plataforma de la máquina y lo soldo. Al mismo tiempo, pruebo el lugar para que el rodillo conducido quede opuesto al motriz, que a su vez está fijado al eje del motor.
Para garantizar una tensión suave de la cinta, es necesario instalar un amortiguador de gas para muebles entre un tubo vertical de 40x40 y un soporte de rodillo en forma de L de 30x30.
Hago una plataforma de soporte para la máquina con los materiales disponibles. Utilizando un pequeño trozo de tubo perfilado de 40x40 y un ángulo de 63º. Hice un corte en la tubería para aumentar el área de soldadura. Fijé la esquina con pernos, ya que será necesario quitarla para realizarle mantenimiento. Todos los espacios en blanco los hice sin dimensiones preliminares, simplemente ajustándolos a la ubicación.
Y ahora estoy preparando una mesa para apoyar las piezas que se están torneando. Para ello utilizo la misma chapa con una sección de 8 mm. Hice el ancho de la mesa de 80 mm.
Estoy preparando la base de la mesa. Para hacer esto, tomo un tubo de 40x40 con una longitud de 120 mm. Le hago un agujero, afilo el extremo en semicírculo y corto una rosca M10. Hago orejas pequeñas con chapa de metal. Actuarán como bucles. Soldé las orejas a la mesa.
Ahora corté un hilo en la suela de la máquina para 4 pies de goma suave para minimizar la vibración. Se pueden quitar de una lavadora rota. Inmediatamente corté un espacio en blanco de su cuerpo para hacer una carcasa protectora. Corté una tira de 130 mm de ancho en toda su longitud y luego la acorté localmente.
En un tornillo de banco, utilizando un martillo, bloques de madera y otros dispositivos, debe doblar la tira y perforar orificios de montaje para obtener una carcasa protectora completa. Todos los detalles están listos.
Teniendo a mi disposición todas las piezas necesarias, pinto los elementos de la máquina.
Es hora de montar. Todo está montado como un constructor. Tendrás que retocar un poco el botón, el condensador y la soldadura de cables. Incluso pude encontrar 2 tapones de plástico para el tubo de 30x30 y uno para el de 40x40, así que todo luce bien.
Como demostró la prueba, la potencia del motor es suficiente para el pleno funcionamiento de la máquina. Gracias al uso de un amortiguador de gas, puede instalar bandas abrasivas de varias longitudes en los rodillos, teniendo así la oportunidad de utilizar consumibles de fábrica en lugar de pegar la banda abrasiva usted mismo.
Ver el vídeo
Clases magistrales similares
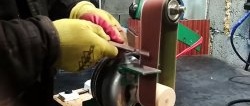
La amoladora más sencilla sin torno del motor de una lavadora.
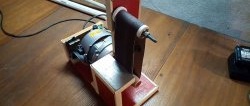
La amoladora más sencilla sin soldar ni girar desde el motor de una lavadora.
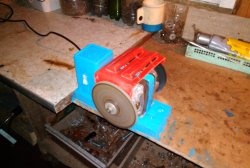
Afilador de motor de lavadora
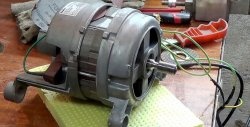
Potente cortadora de motor de lavadora.
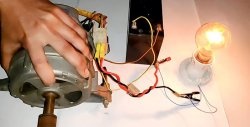
Cómo convertir el motor de una lavadora en un generador de 220 V
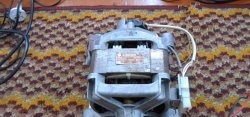
Cómo conectar el motor de una lavadora a 220 V
Particularmente interesante
Comentarios (7)