Método de soldadura de collar para insertar tuberías de diferentes diámetros.
La forma más sencilla es cortar un tubo de pequeño diámetro en un tubo que obviamente sea grande. Para ello colocamos el primero perpendicular al segundo y dibujamos el contorno del tubo más pequeño sobre la superficie del más grande. Recortamos un círculo, insertamos un pequeño tubo en él y escaldamos el punto de inserción.
Si se van a insertar dos tubos del mismo diámetro, en el insertado realizamos el llamado. Los “pantalones” son segmentos que, en su parte más grande, deben tener una talla tres veces menor que el diámetro.
A continuación consideraremos el caso más difícil en términos de corte, cuando el diámetro del tubo insertado es ligeramente menor que el principal, por ejemplo, 89 mm o 76 mm y 100 mm, respectivamente.
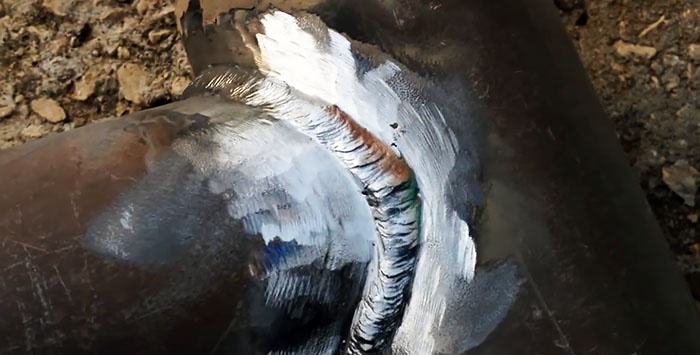
Para poder cortar y soldar un inserto de dos tubos metálicos de diferente diámetro debemos tener:
Usaremos la tecnología de corte de collar ampliamente utilizada, donde se forma el borde de un tubo redondo que se corta perpendicular al tubo principal.Seguiremos el siguiente orden al implementar este método.
Cortamos el borde del tubo soldado en ángulo recto.
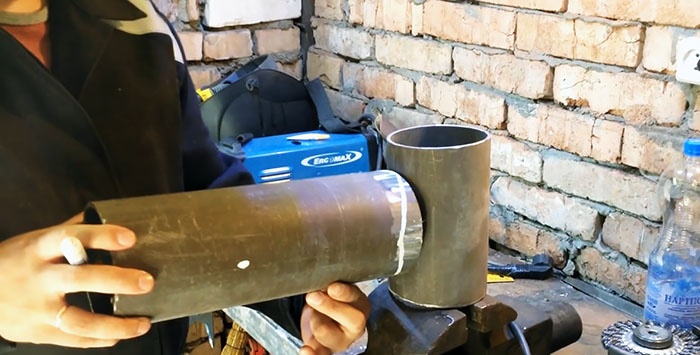
Marcamos cuatro puntos con un marcador, que son la intersección de dos diámetros mutuamente perpendiculares y el extremo de la tubería. Si todo se hace correctamente, estos puntos se ubican uniformemente en un círculo a 90 grados.
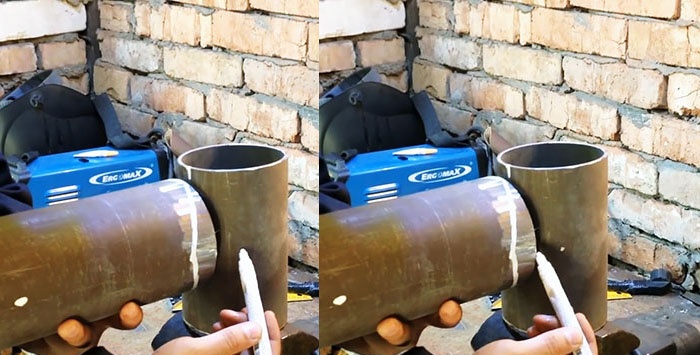
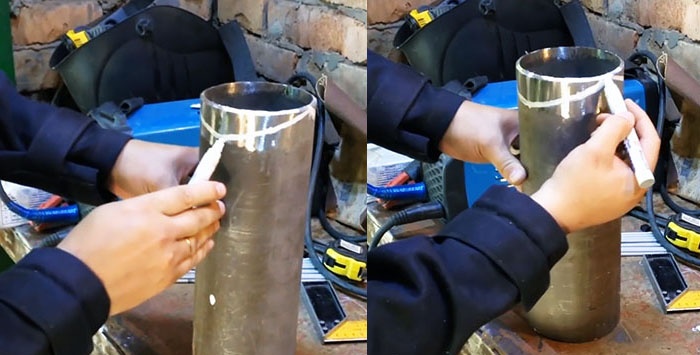
Colocamos el tubo con el extremo marcado contra la superficie lateral del principal y utilizamos una regla metálica o cinta métrica para medir el espacio más grande entre el extremo del primero y la generatriz del segundo. En nuestro caso resultó ser de 30 mm.
Desde dos puntos opuestos en los extremos colocamos 30 mm a lo largo de la generatriz. Con un marcador, dibujamos dos líneas suaves en la superficie lateral de la tubería, que parten de un punto adyacente en el extremo, en direcciones opuestas, de modo que pasen por las marcas inferiores y converjan en el segundo punto al final.
Según las marcas realizadas, utilizando una amoladora con disco de corte, cortamos fragmentos en forma de dos segmentos redondeados idénticos. Limpiamos los recortes figurados al final del tubo para que no queden rebabas ni irregularidades.
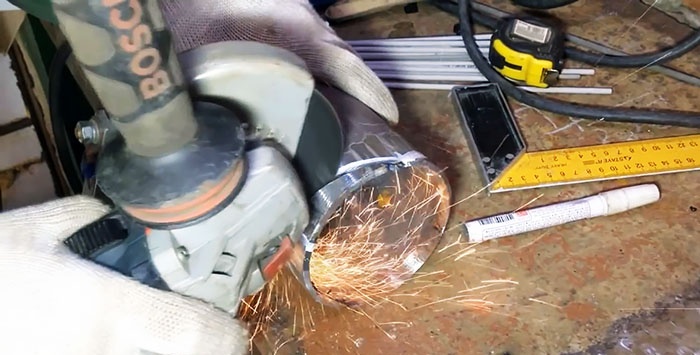
Probamos la tubería en su lugar y, si el ajuste es insuficiente, corregimos estos lugares con una amoladora y logramos una coincidencia más precisa de las superficies de las tuberías.
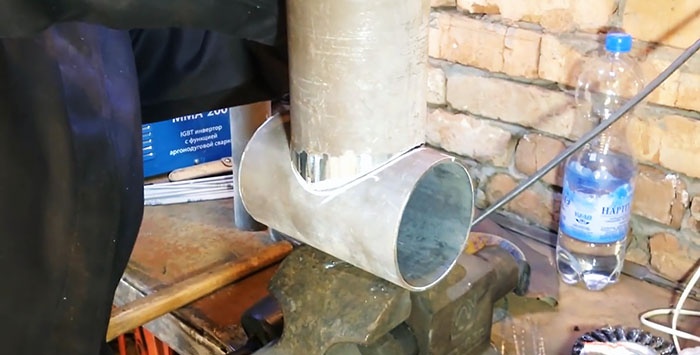
Con un marcador, transfiera el contorno exterior del tubo soldado a la superficie lateral del principal. Dentro de la línea cerrada resultante construimos una línea congruente, alejándose de la exterior por el grosor de la pared de la tubería. Es a lo largo de la nueva línea que haremos el corte.
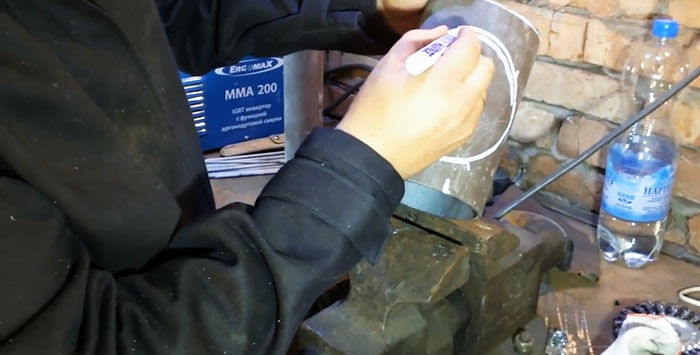
Con una amoladora, cortamos un círculo en la tubería de acuerdo con las marcas y procesamos los bordes para eliminar rebabas y redondeamos los bordes para soldar.
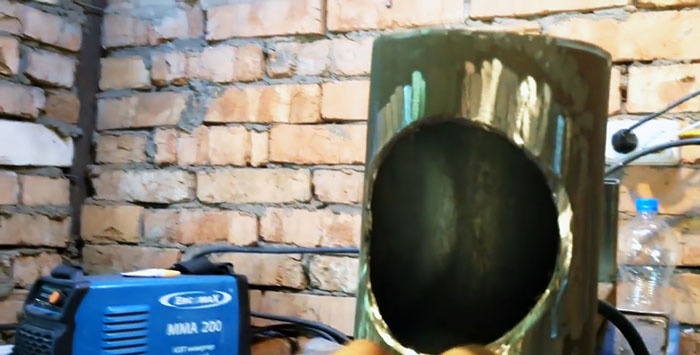
Antes de comenzar los trabajos de soldadura, utilice una escuadra para comprobar la perpendicularidad de las tuberías. El ángulo entre los generadores debe ser de 90 grados.Hacemos tachuelas en dos o tres lugares.
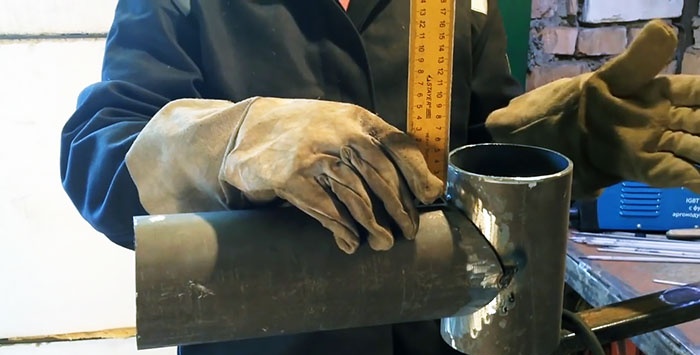
Comenzamos a soldar desde el punto de contacto inferior y realizamos dos pasadas mediante costura de hilo: raíz y refrentado. Esto asegurará la mejor calidad de la unión soldada.
Al soldar, es importante elegir la intensidad de corriente adecuada, que depende de la calidad de la electricidad suministrada y, en particular, del voltaje. Normalmente hablamos de 70-80 A. Cocinamos con un electrodo de tres milímetros UONI-13-55, intentando evitar que la escoria entre en el metal.
Habiendo pasado desde el punto inferior hasta la parte superior, nos detenemos y eliminamos la escoria con un martillo. Las deficiencias detectadas no son críticas, ya que pueden eliminarse durante la segunda pasada, la enfrentada.
Soldamos la otra mitad de la junta entre las superficies de la tubería de la misma forma. Luego procesamos ligeramente la primera costura, eliminando cuentas grandes y escoria.
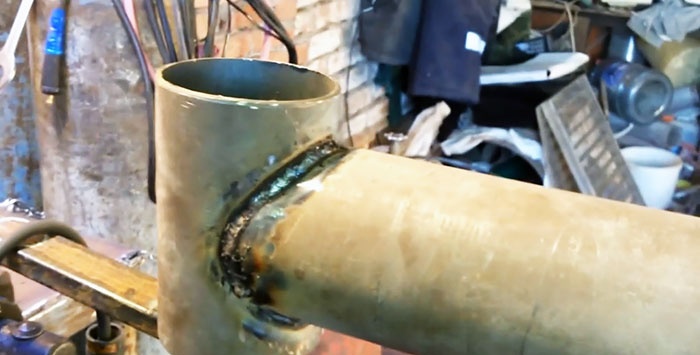
Comenzamos a aplicar la costura facial desde abajo, sosteniendo el electrodo en un ángulo de 45 grados a lo largo del camino y moviéndolo transversalmente a la primera costura, o "espina de pescado". A continuación soldamos la costura, sujetando el electrodo casi verticalmente a la superficie, y terminamos la primera mitad, colocando nuevamente el electrodo a 45 grados en el recorrido, y realizando movimientos circulares.
También comenzamos a aplicar la costura frontal desde el punto inferior y la llevamos hacia arriba, después de lo cual quitamos la escoria de la costura con un martillo.
Soldamos la costura frontal de la misma forma en la segunda mitad del contacto de las tuberías. A medida que avanzamos hacia arriba, reducimos la velocidad de soldadura para que la costura sea la misma en todas partes.
También eliminamos la escoria y limpiamos la costura con una amoladora. El resultado es una soldadura limpia y fiable.
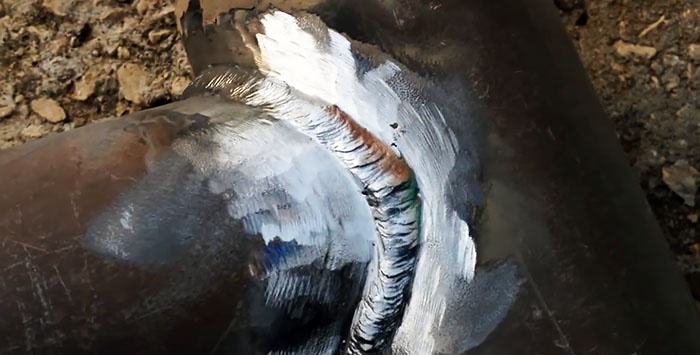
Si se van a insertar dos tubos del mismo diámetro, en el insertado realizamos el llamado. Los “pantalones” son segmentos que, en su parte más grande, deben tener una talla tres veces menor que el diámetro.
A continuación consideraremos el caso más difícil en términos de corte, cuando el diámetro del tubo insertado es ligeramente menor que el principal, por ejemplo, 89 mm o 76 mm y 100 mm, respectivamente.
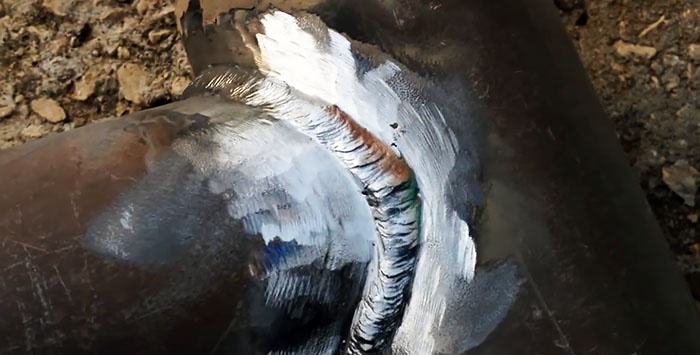
Necesitará
Para poder cortar y soldar un inserto de dos tubos metálicos de diferente diámetro debemos tener:
- tubos en bruto de dos diámetros diferentes;
- amoladora con muela de corte y rectificado;
- marcador;
- regla, cuadrado;
- maquina de soldar;
- martillo.
Algoritmo para el proceso de inserción de tubos redondos.
Usaremos la tecnología de corte de collar ampliamente utilizada, donde se forma el borde de un tubo redondo que se corta perpendicular al tubo principal.Seguiremos el siguiente orden al implementar este método.
Cortamos el borde del tubo soldado en ángulo recto.
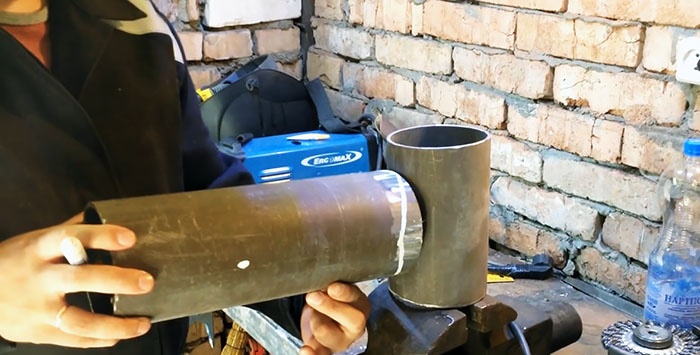
Marcamos cuatro puntos con un marcador, que son la intersección de dos diámetros mutuamente perpendiculares y el extremo de la tubería. Si todo se hace correctamente, estos puntos se ubican uniformemente en un círculo a 90 grados.
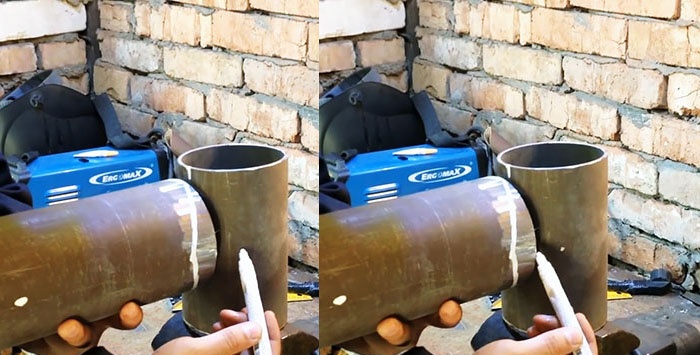
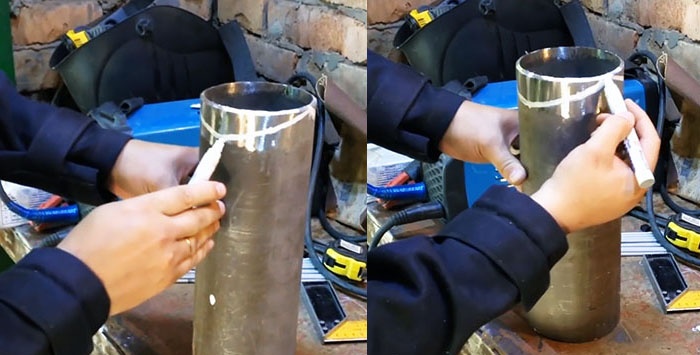
Colocamos el tubo con el extremo marcado contra la superficie lateral del principal y utilizamos una regla metálica o cinta métrica para medir el espacio más grande entre el extremo del primero y la generatriz del segundo. En nuestro caso resultó ser de 30 mm.
Desde dos puntos opuestos en los extremos colocamos 30 mm a lo largo de la generatriz. Con un marcador, dibujamos dos líneas suaves en la superficie lateral de la tubería, que parten de un punto adyacente en el extremo, en direcciones opuestas, de modo que pasen por las marcas inferiores y converjan en el segundo punto al final.
Según las marcas realizadas, utilizando una amoladora con disco de corte, cortamos fragmentos en forma de dos segmentos redondeados idénticos. Limpiamos los recortes figurados al final del tubo para que no queden rebabas ni irregularidades.
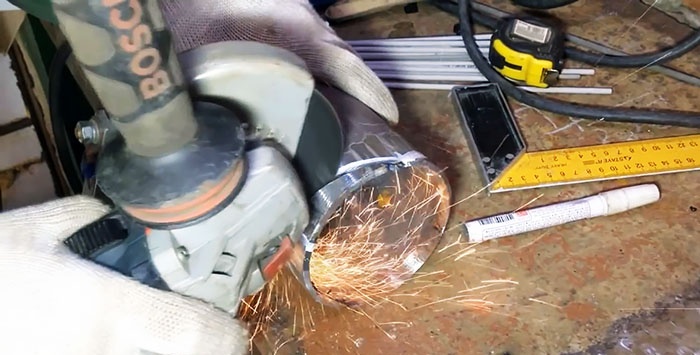
Probamos la tubería en su lugar y, si el ajuste es insuficiente, corregimos estos lugares con una amoladora y logramos una coincidencia más precisa de las superficies de las tuberías.
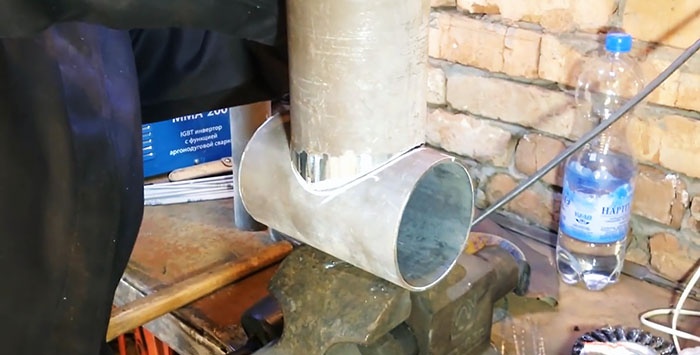
Con un marcador, transfiera el contorno exterior del tubo soldado a la superficie lateral del principal. Dentro de la línea cerrada resultante construimos una línea congruente, alejándose de la exterior por el grosor de la pared de la tubería. Es a lo largo de la nueva línea que haremos el corte.
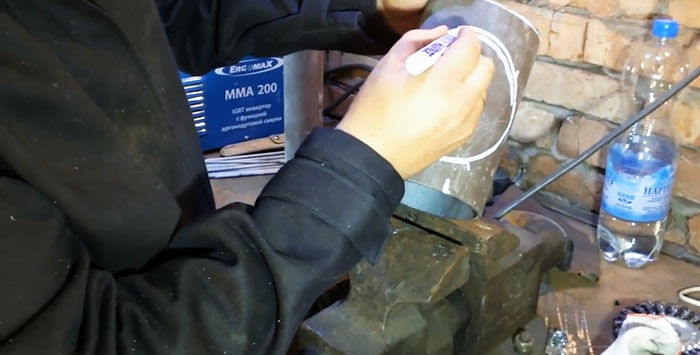
Con una amoladora, cortamos un círculo en la tubería de acuerdo con las marcas y procesamos los bordes para eliminar rebabas y redondeamos los bordes para soldar.
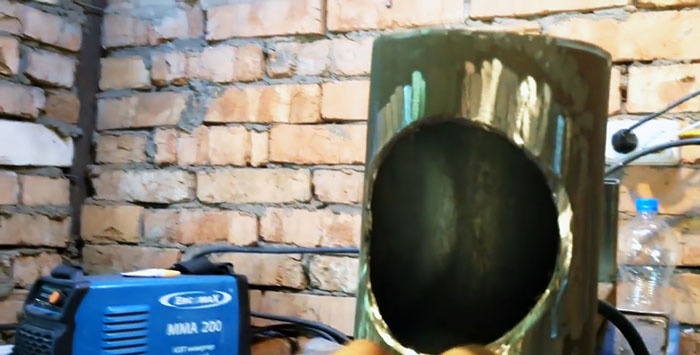
Antes de comenzar los trabajos de soldadura, utilice una escuadra para comprobar la perpendicularidad de las tuberías. El ángulo entre los generadores debe ser de 90 grados.Hacemos tachuelas en dos o tres lugares.
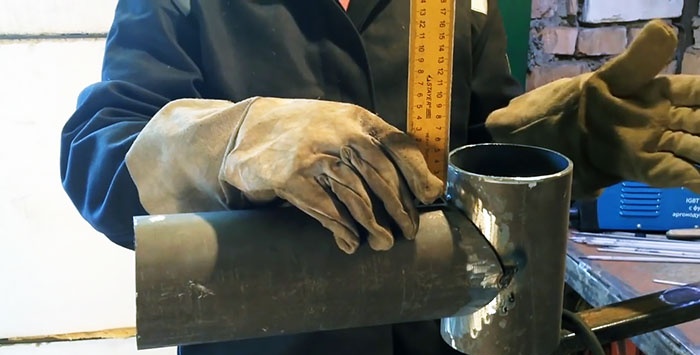
Comenzamos a soldar desde el punto de contacto inferior y realizamos dos pasadas mediante costura de hilo: raíz y refrentado. Esto asegurará la mejor calidad de la unión soldada.
Al soldar, es importante elegir la intensidad de corriente adecuada, que depende de la calidad de la electricidad suministrada y, en particular, del voltaje. Normalmente hablamos de 70-80 A. Cocinamos con un electrodo de tres milímetros UONI-13-55, intentando evitar que la escoria entre en el metal.
Habiendo pasado desde el punto inferior hasta la parte superior, nos detenemos y eliminamos la escoria con un martillo. Las deficiencias detectadas no son críticas, ya que pueden eliminarse durante la segunda pasada, la enfrentada.
Soldamos la otra mitad de la junta entre las superficies de la tubería de la misma forma. Luego procesamos ligeramente la primera costura, eliminando cuentas grandes y escoria.
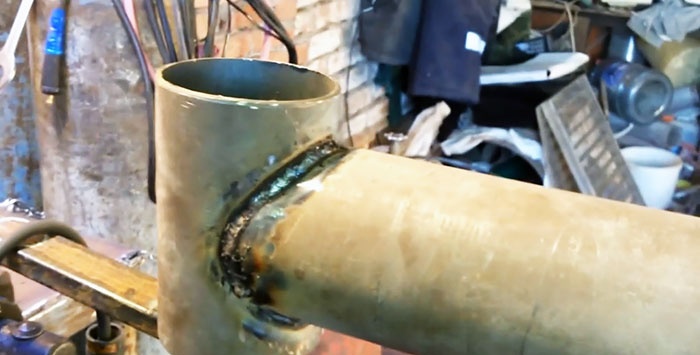
Comenzamos a aplicar la costura facial desde abajo, sosteniendo el electrodo en un ángulo de 45 grados a lo largo del camino y moviéndolo transversalmente a la primera costura, o "espina de pescado". A continuación soldamos la costura, sujetando el electrodo casi verticalmente a la superficie, y terminamos la primera mitad, colocando nuevamente el electrodo a 45 grados en el recorrido, y realizando movimientos circulares.
También comenzamos a aplicar la costura frontal desde el punto inferior y la llevamos hacia arriba, después de lo cual quitamos la escoria de la costura con un martillo.
Soldamos la costura frontal de la misma forma en la segunda mitad del contacto de las tuberías. A medida que avanzamos hacia arriba, reducimos la velocidad de soldadura para que la costura sea la misma en todas partes.
También eliminamos la escoria y limpiamos la costura con una amoladora. El resultado es una soldadura limpia y fiable.
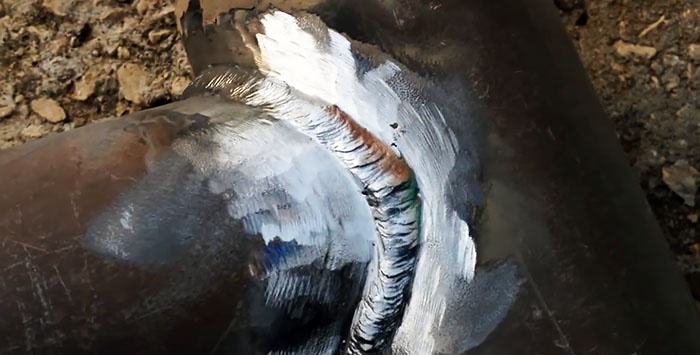
Ver el vídeo
Clases magistrales similares
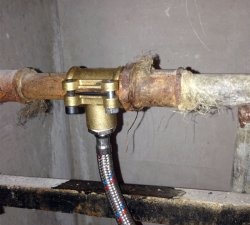
Cómo hacer un corte sencillo en un tubo de acero.
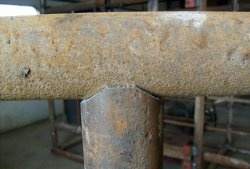
Cómo hacer una montura de tubería de alta calidad para roscado en ángulo
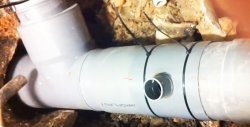
Cómo hacer una curva en un tubo de PVC.
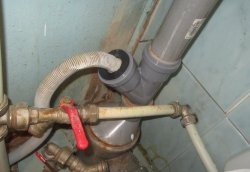
Instalación de una lavadora en un elevador de PVC
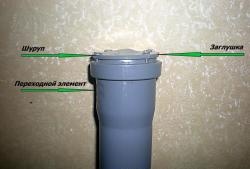
Cajas hechas de tubos de plástico.
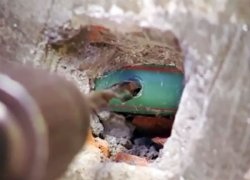
¿Rompiste una tubería de propileno? Dos tecnologías de reparación
Particularmente interesante
Comentarios (0)