Kimpalan geseran
Kebanyakan proses kimpalan moden bergantung pada input haba luaran, seperti nyahcas arka. Tetapi haba boleh dijana secara langsung di zon kimpalan kerana geseran antara bahagian yang disambungkan.
Tenaga terma boleh diperolehi dengan memutarkan satu bahagian manakala yang kedua adalah pegun, atau berputar ke arah yang bertentangan. Selain itu, bahagian mesti serentak ditekan antara satu sama lain dengan daya yang berterusan atau meningkat dari awal hingga akhir. Proses ini berakhir dengan pemberhentian yang menjengkelkan dan pantas bahagian berputar.
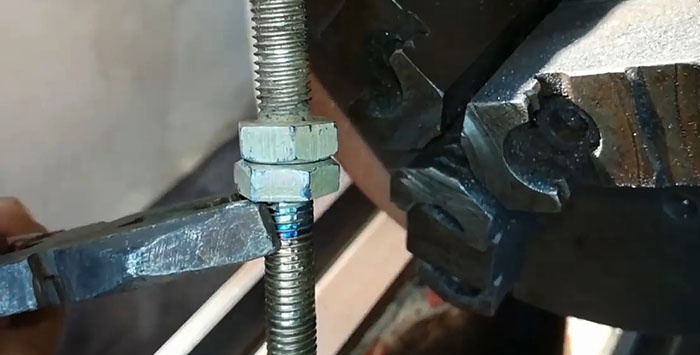
Sebagai perbandingan, katakan, dengan kimpalan punggung elektrik, proses berdasarkan geseran mempunyai beberapa kelebihan operasi:
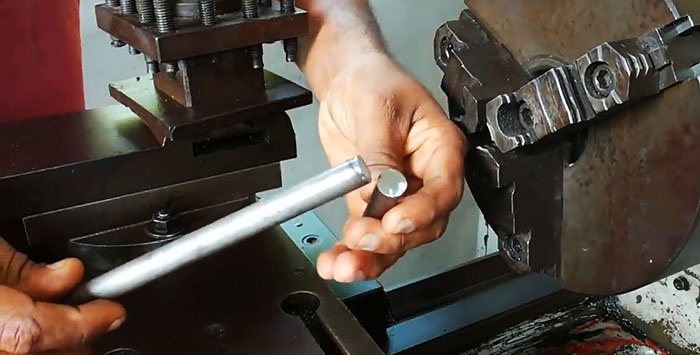
Dalam chuck dan headstock mesin kami mengapit rod logam, diameternya harus lebih daripada 3.5 mm, tetapi kurang daripada 200 mm. Mereka boleh menjadi keluli, aluminium, tembaga, gangsa atau logam yang berbeza:
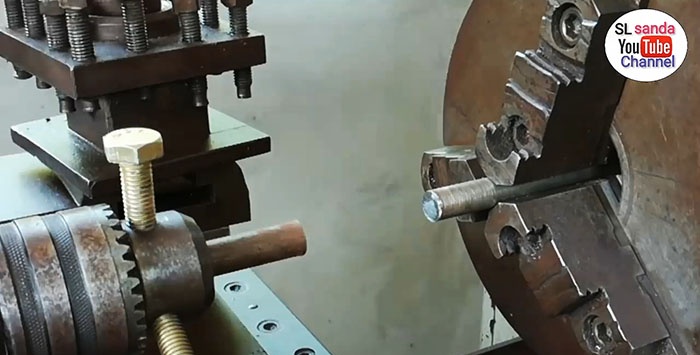
Gabungan bahan boleh sangat berbeza, malah yang tidak boleh dikimpal dengan cara biasa. Tiada sekatan dalam hal ini untuk kimpalan geseran.
Dalam kes kami, kami mengikat rod dalam headstock menggunakan tiga bolt diskrukan ke dalam lubang chuck, sama rata di sekeliling lilitan pada 120 darjah. Dengan bantuan mereka, kami menjalankan penjajaran relatif kepada rod yang diapit dalam chuck dengan mengetatkan atau melonggarkan satu atau satu lagi bolt.
Kami membawa headstock sehingga rod berhenti hujung ke hujung dan mengikatnya atau memegangnya dengan tangan untuk meningkatkan daya pengapit semasa proses kimpalan, yang diperlukan oleh teknologi kaedah kimpalan ini.
Kami menghidupkan mesin, akibatnya rod yang diapit di chuck mesin mula berputar. Dalam kes kami, rod yang dipasang di headstock tidak bergerak, tetapi pada dasarnya ia boleh berputar ke arah yang bertentangan, yang akan mengurangkan masa proses.
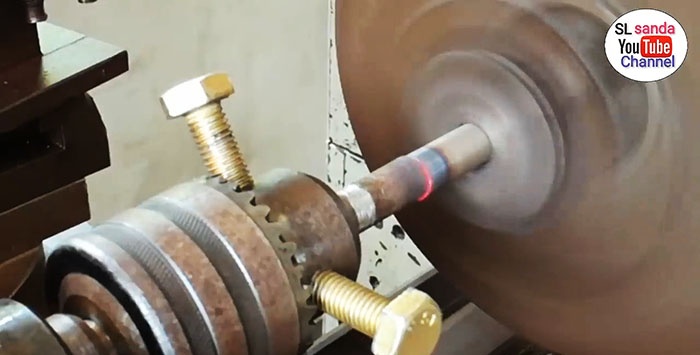
Tidak lama lagi kita akan melihat warna-warna ternoda bermula pada titik sentuhan rod dan merebak di sepanjang mereka dalam arah yang bertentangan, yang merupakan tanda langsung pemanasan cepat logam akibat geseran.
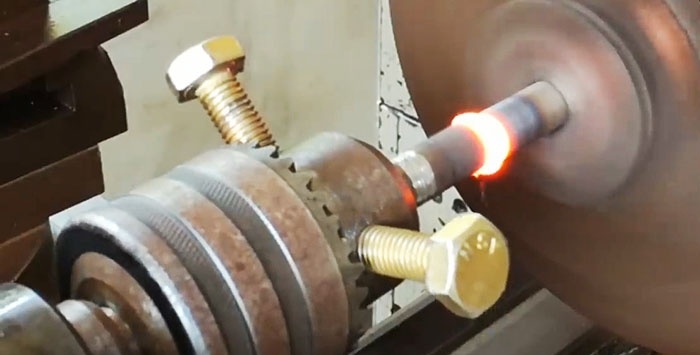
Selepas satu lagi masa yang singkat, logam dalam zon sentuhan akan bersinar terang dan mula diperah keluar dalam bentuk pembentukan cincin di luar dimensi rod.Cincin ini juga akan mengandungi burr: skala, gris tidak terbakar, rangkuman bukan logam pepejal, dsb.
Pada saat cahaya yang paling terang pada titik sentuhan, mesin mesti dimatikan secara mendadak supaya logam kedua-dua rod ditetapkan. Pada masa yang sama, jika headstock belum diamankan, perlu meningkatkan tekanan ke atasnya secara beransur-ansur untuk mengimbangi jumlah logam yang disesarkan di zon sentuhan dan mendapatkan sambungan yang lebih kuat dan berkualiti tinggi.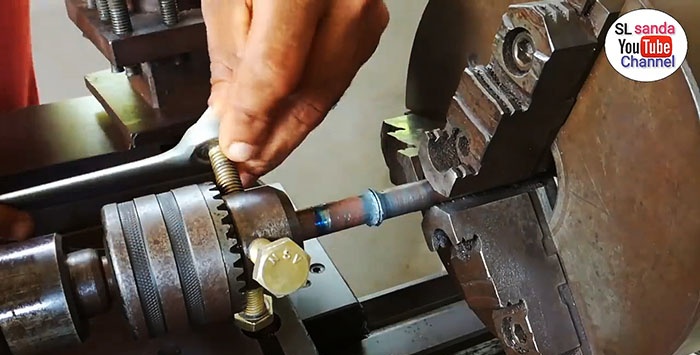
Selepas menunggu sehingga cahaya berhenti (dan ini adalah tanda bahawa logam telah ditetapkan sepenuhnya), anda boleh melonggarkan bolt pengikat dan mengeluarkan headstock. Sekarang yang tinggal hanyalah untuk memeriksa kualiti kimpalan geseran.
Untuk melakukan ini, hidupkan mesin sekali lagi dan mengesan sedikit kehabisan rod yang dikimpal - akibat daripada penjajaran yang tidak tepat semasa pemasangan pada mulanya. Kecacatan ini boleh dihapuskan dengan memusing dan mengeluarkan burr tersemperit di kawasan sentuhan.
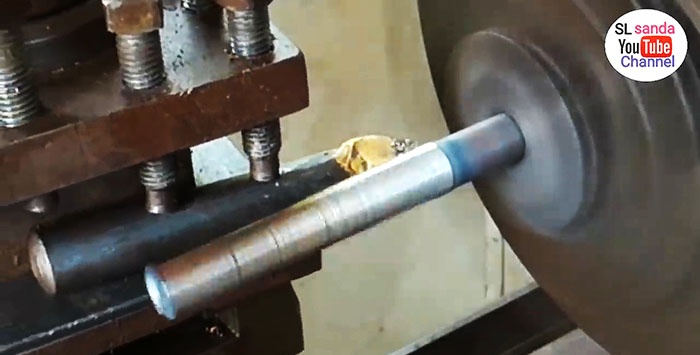
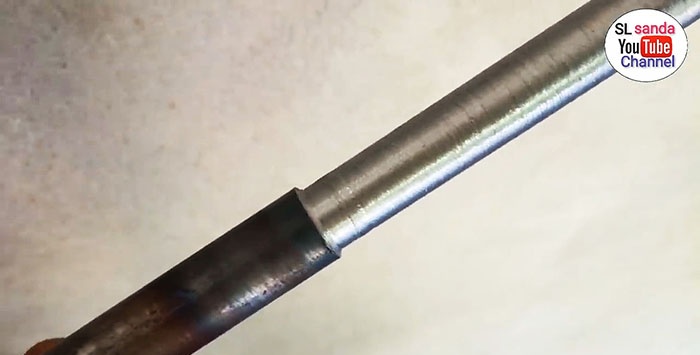
Penembusan logam yang lebih dalam menunjukkan bahawa tiada ciri yang kelihatan di kawasan kimpalan kedua-dua rod. Nampaknya ini bukan titik sentuhan antara dua batang, tetapi badan salah satu daripadanya.
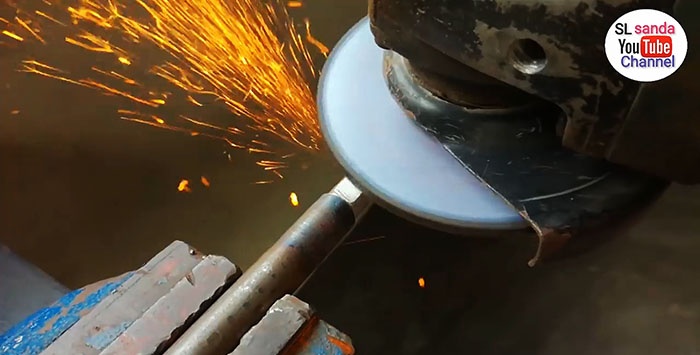
Kami menjalankan kawalan kualiti berikut bagi kimpalan geseran. Kami mengapit rod yang disambungkan dengan cara ini dalam naib dan menggunakan cakera pengisar untuk membuat "rak" di zon hubungan, dan sekali lagi kami yakin dengan kehomogenan logam, yang juga menunjukkan kualiti kimpalan.
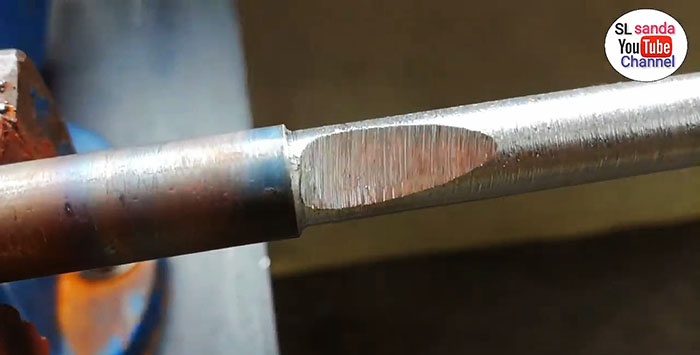
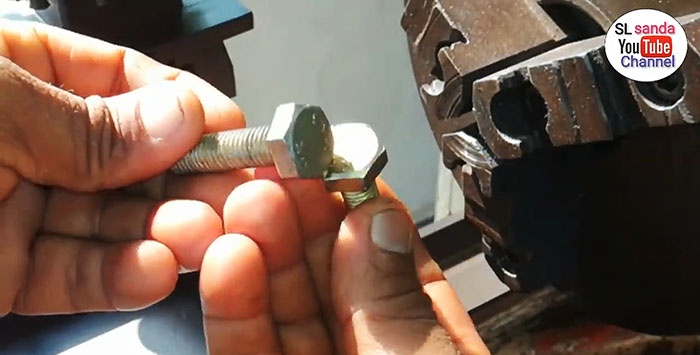
Kimpalan geseran boleh digunakan untuk menyambung kepala dan bolt yang dihasilkan secara besar-besaran. Prosesnya tidak berbeza dengan proses dengan rod: satu bolt diikat ke dalam chuck mesin, satu lagi ke dalam headstock.
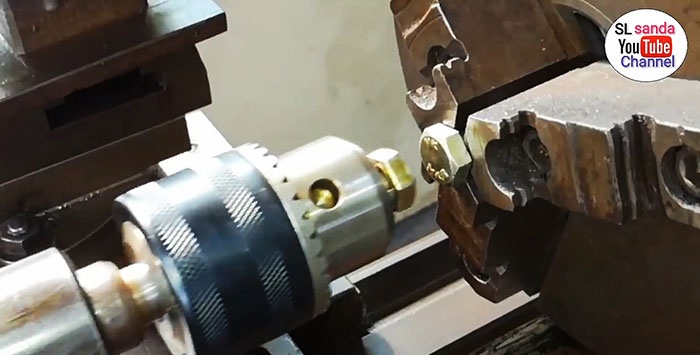
Dengan bantuan yang terakhir, bolt disentuh dengan kepala, dan mesin dimulakan. Ia juga perlu untuk meningkatkan daya pengapit dan menangkap momen kimpalan untuk mematikan pemacu dalam masa.
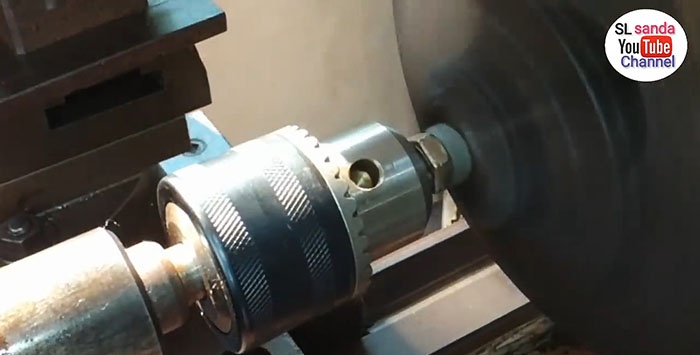
Kimpalan geseran boleh digunakan untuk menyambung bahan yang sukar atau mustahil untuk dikimpal dengan jenis lain: keluli dan aluminium, keluli austenit dan pearlitik. Ia juga boleh digunakan untuk menyambung bahan kerja plastik dengan mudah.
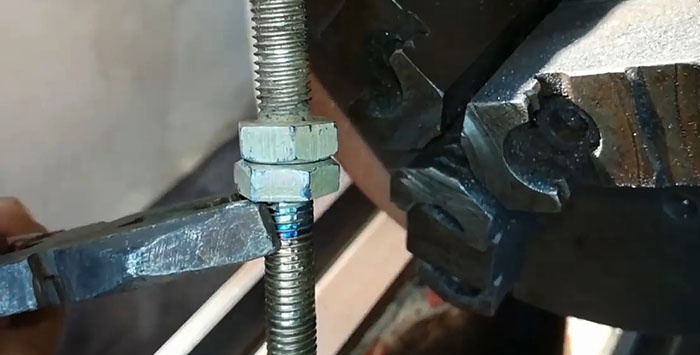
Pengiraan dan amalan menggunakan cantuman geseran menunjukkan bahawa kaedah ini lebih sesuai untuk bahan kerja yang diameternya terletak dalam julat 6-100 mm. Batang kimpalan dengan diameter lebih besar daripada 200 mm tidak menguntungkan dari segi ekonomi, kerana proses itu memerlukan lebih banyak kuasa (0.5 ribu kW) dan daya paksi (3 × 106 N). Ia tidak akan dapat menyambungkan rod dengan diameter kurang daripada 3.5 mm menggunakan kaedah ini kerana keperluan untuk menyediakan kelajuan tinggi (200 rpm) dan kesukaran untuk menentukan masa untuk mematikan pemacu.
Tenaga terma boleh diperolehi dengan memutarkan satu bahagian manakala yang kedua adalah pegun, atau berputar ke arah yang bertentangan. Selain itu, bahagian mesti serentak ditekan antara satu sama lain dengan daya yang berterusan atau meningkat dari awal hingga akhir. Proses ini berakhir dengan pemberhentian yang menjengkelkan dan pantas bahagian berputar.
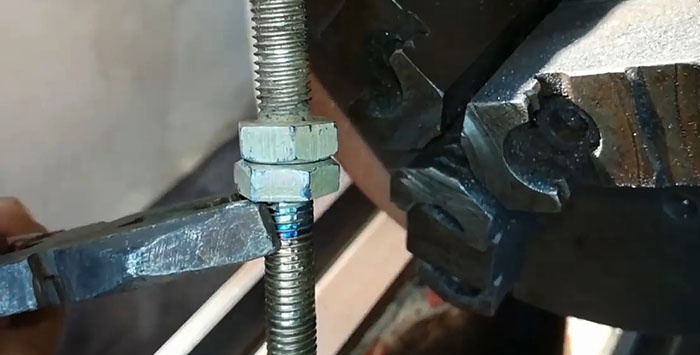
Sebagai perbandingan, katakan, dengan kimpalan punggung elektrik, proses berdasarkan geseran mempunyai beberapa kelebihan operasi:
- kos tenaga dikurangkan dengan banyak;
- sambungan yang dikimpal sentiasa boleh dipercayai, kerana ia hanya bergantung pada ciri termofizik produk yang dikimpal;
- tiada penyediaan khas diperlukan untuk sambungan yang akan disambungkan, kerana skala, karat, gris dan gris terbakar atau diperah menjadi kilat pada permulaan proses;
- kualiti sambungan tidak terjejas walaupun oleh pelanggaran keselarian bahan kerja sehingga sudut 6±1 darjah;
- ketiadaan faktor negatif dalam bentuk sinaran ultraviolet dan pelepasan gas berbahaya;
- kesederhanaan peralatan teknologi, mudah menerima penyelenggaraan rutin, mekanisasi dan automasi.
Proses kimpalan geseran pada mesin pelarik
Batang keluli kimpalan
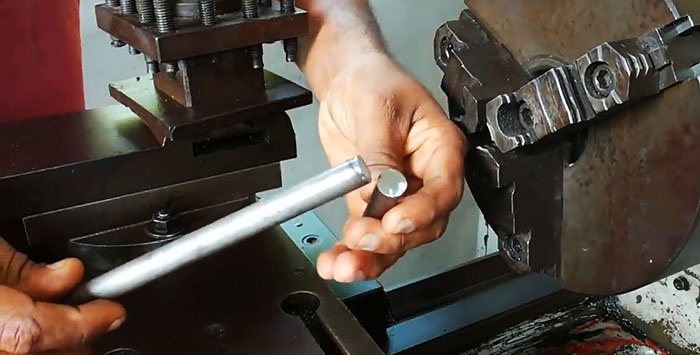
Dalam chuck dan headstock mesin kami mengapit rod logam, diameternya harus lebih daripada 3.5 mm, tetapi kurang daripada 200 mm. Mereka boleh menjadi keluli, aluminium, tembaga, gangsa atau logam yang berbeza:
- keluli dan aluminium;
- keluli dan tembaga;
- aluminium dan gangsa, dsb.
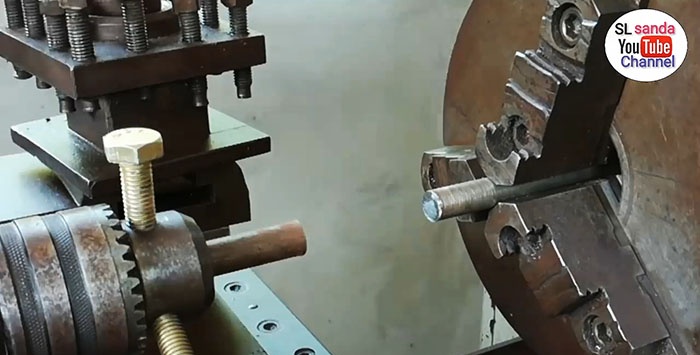
Gabungan bahan boleh sangat berbeza, malah yang tidak boleh dikimpal dengan cara biasa. Tiada sekatan dalam hal ini untuk kimpalan geseran.
Dalam kes kami, kami mengikat rod dalam headstock menggunakan tiga bolt diskrukan ke dalam lubang chuck, sama rata di sekeliling lilitan pada 120 darjah. Dengan bantuan mereka, kami menjalankan penjajaran relatif kepada rod yang diapit dalam chuck dengan mengetatkan atau melonggarkan satu atau satu lagi bolt.
Kami membawa headstock sehingga rod berhenti hujung ke hujung dan mengikatnya atau memegangnya dengan tangan untuk meningkatkan daya pengapit semasa proses kimpalan, yang diperlukan oleh teknologi kaedah kimpalan ini.
Kami menghidupkan mesin, akibatnya rod yang diapit di chuck mesin mula berputar. Dalam kes kami, rod yang dipasang di headstock tidak bergerak, tetapi pada dasarnya ia boleh berputar ke arah yang bertentangan, yang akan mengurangkan masa proses.
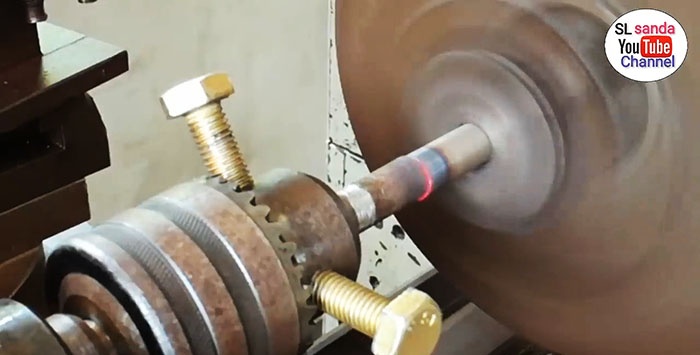
Tidak lama lagi kita akan melihat warna-warna ternoda bermula pada titik sentuhan rod dan merebak di sepanjang mereka dalam arah yang bertentangan, yang merupakan tanda langsung pemanasan cepat logam akibat geseran.
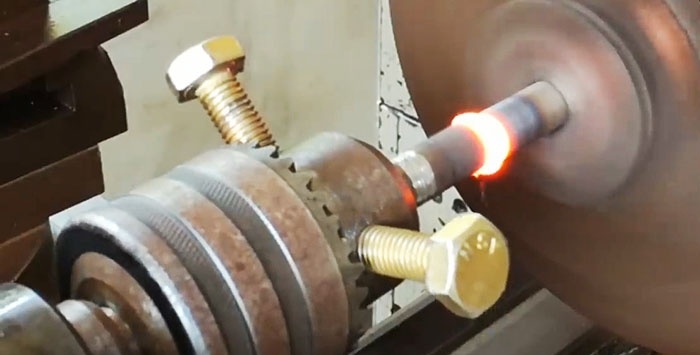
Selepas satu lagi masa yang singkat, logam dalam zon sentuhan akan bersinar terang dan mula diperah keluar dalam bentuk pembentukan cincin di luar dimensi rod.Cincin ini juga akan mengandungi burr: skala, gris tidak terbakar, rangkuman bukan logam pepejal, dsb.
Pada saat cahaya yang paling terang pada titik sentuhan, mesin mesti dimatikan secara mendadak supaya logam kedua-dua rod ditetapkan. Pada masa yang sama, jika headstock belum diamankan, perlu meningkatkan tekanan ke atasnya secara beransur-ansur untuk mengimbangi jumlah logam yang disesarkan di zon sentuhan dan mendapatkan sambungan yang lebih kuat dan berkualiti tinggi.
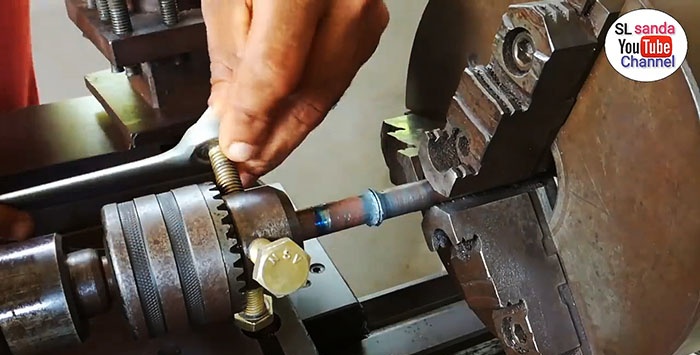
Selepas menunggu sehingga cahaya berhenti (dan ini adalah tanda bahawa logam telah ditetapkan sepenuhnya), anda boleh melonggarkan bolt pengikat dan mengeluarkan headstock. Sekarang yang tinggal hanyalah untuk memeriksa kualiti kimpalan geseran.
Untuk melakukan ini, hidupkan mesin sekali lagi dan mengesan sedikit kehabisan rod yang dikimpal - akibat daripada penjajaran yang tidak tepat semasa pemasangan pada mulanya. Kecacatan ini boleh dihapuskan dengan memusing dan mengeluarkan burr tersemperit di kawasan sentuhan.
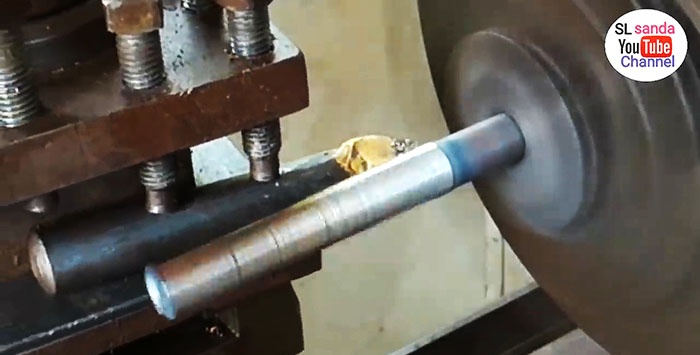
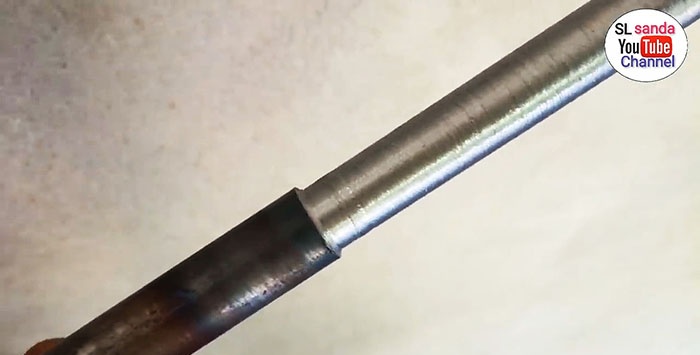
Penembusan logam yang lebih dalam menunjukkan bahawa tiada ciri yang kelihatan di kawasan kimpalan kedua-dua rod. Nampaknya ini bukan titik sentuhan antara dua batang, tetapi badan salah satu daripadanya.
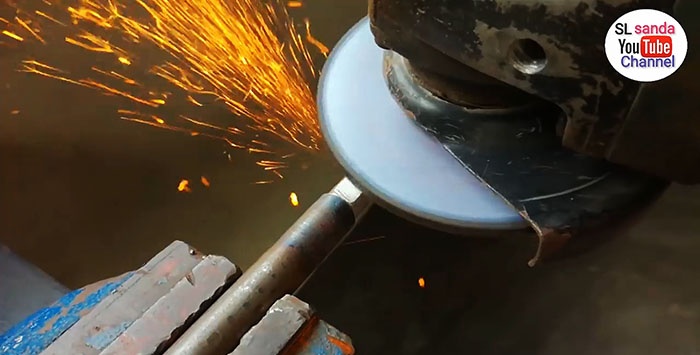
Kami menjalankan kawalan kualiti berikut bagi kimpalan geseran. Kami mengapit rod yang disambungkan dengan cara ini dalam naib dan menggunakan cakera pengisar untuk membuat "rak" di zon hubungan, dan sekali lagi kami yakin dengan kehomogenan logam, yang juga menunjukkan kualiti kimpalan.
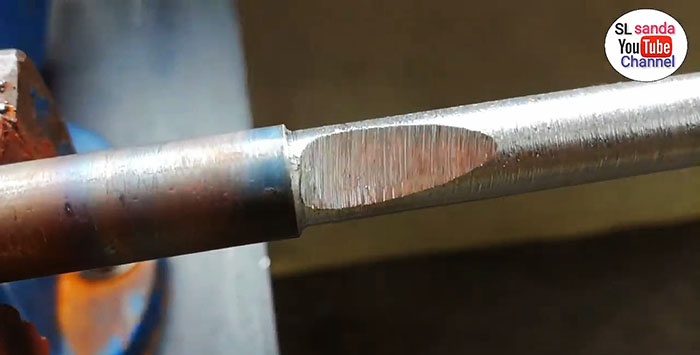
Sambungan bolt
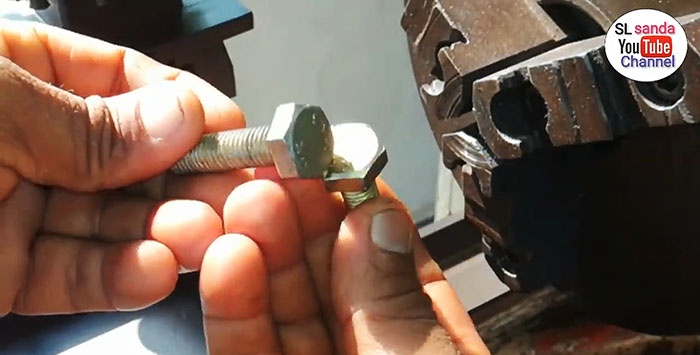
Kimpalan geseran boleh digunakan untuk menyambung kepala dan bolt yang dihasilkan secara besar-besaran. Prosesnya tidak berbeza dengan proses dengan rod: satu bolt diikat ke dalam chuck mesin, satu lagi ke dalam headstock.
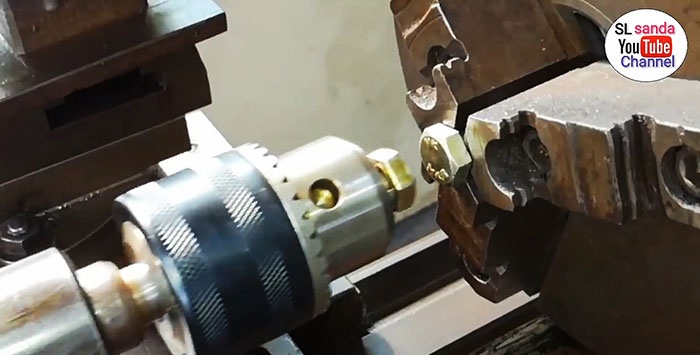
Dengan bantuan yang terakhir, bolt disentuh dengan kepala, dan mesin dimulakan. Ia juga perlu untuk meningkatkan daya pengapit dan menangkap momen kimpalan untuk mematikan pemacu dalam masa.
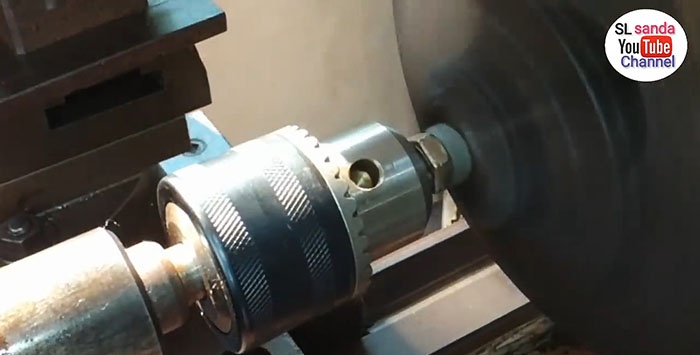
Kimpalan geseran boleh digunakan untuk menyambung bahan yang sukar atau mustahil untuk dikimpal dengan jenis lain: keluli dan aluminium, keluli austenit dan pearlitik. Ia juga boleh digunakan untuk menyambung bahan kerja plastik dengan mudah.
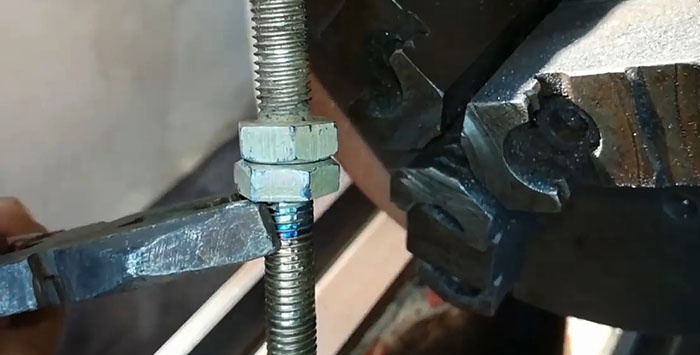
Pengiraan dan amalan menggunakan cantuman geseran menunjukkan bahawa kaedah ini lebih sesuai untuk bahan kerja yang diameternya terletak dalam julat 6-100 mm. Batang kimpalan dengan diameter lebih besar daripada 200 mm tidak menguntungkan dari segi ekonomi, kerana proses itu memerlukan lebih banyak kuasa (0.5 ribu kW) dan daya paksi (3 × 106 N). Ia tidak akan dapat menyambungkan rod dengan diameter kurang daripada 3.5 mm menggunakan kaedah ini kerana keperluan untuk menyediakan kelajuan tinggi (200 rpm) dan kesukaran untuk menentukan masa untuk mematikan pemacu.
Tonton video
Kelas induk yang serupa
Amat menarik
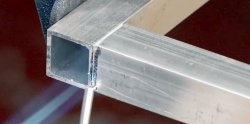
Cara mudah untuk memateri aluminium
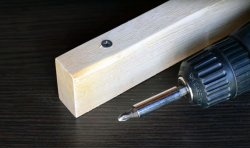
Bagaimana untuk memulihkan kelawar
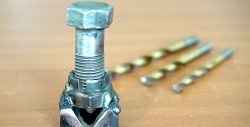
Alat mengasah gerudi
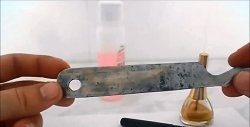
Cara Membuat Lubang pada Keluli Yang Dikeraskan Tanpa Menggerudi
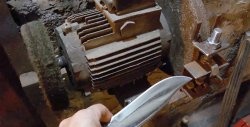
Peranti paling mudah untuk mengasah pisau pada 30 darjah
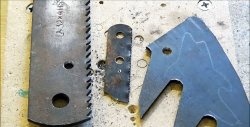
Bagaimana untuk menggerudi melalui mana-mana keluli berkelajuan tinggi dengan gerudi jubin
Komen (1)