Hvordan lage en stangekstruder for en 3D-printer billig ved å bruke tilgjengelige komponenter
Med aktiv bruk av 3D-printing brukes enorme summer på innkjøp av forbruksmateriell. I denne forbindelse er det fornuftig å lage dem selv fra knust ABS-plast og PET-flasker. For å gjøre dette må du lage spesialutstyr, hvorav det mest komplekse er ekstruderen.
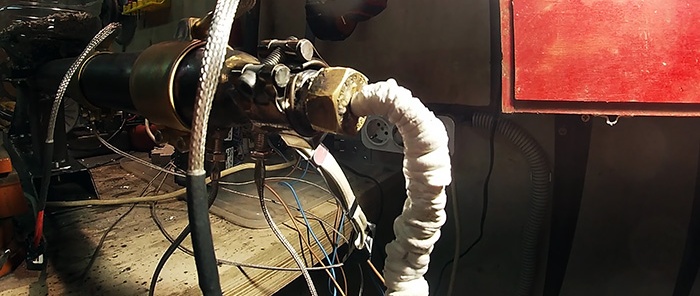
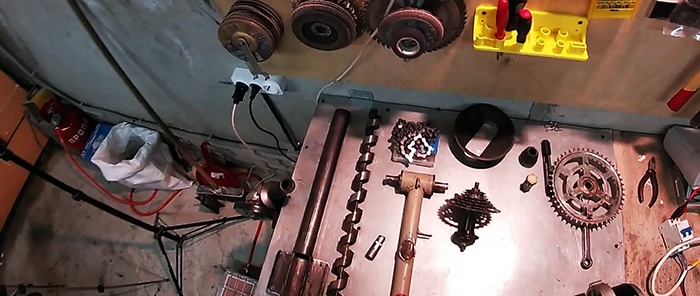
En spiraltrebor vil bli brukt som ekstruderskrue. Et vannrør er valgt for det. I den må du slipe av den interne sveisesømmen med en fil.Et langsgående kutt lages fra kanten av røret til en dybde på 60-80 mm, og en del av røret kuttes av langs det. Kinn av stålplate sveises til det resulterende sporet på venstre og høyre side. En lastetrakt for knust plast vil bli installert på dem. Den kan skrives ut på en 3D-printer.
En stålplate eller et massivt profilrør kan brukes som ekstruderbase.
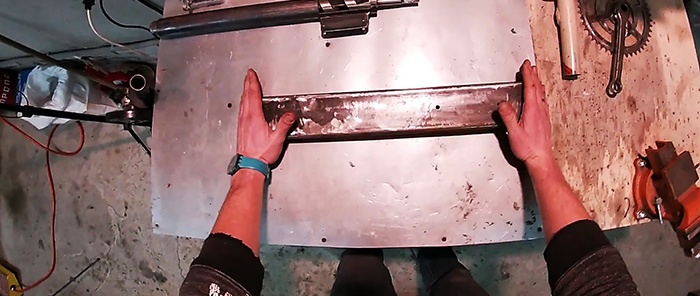
Et stativ er skrudd til basen for å sikre selve ekstruderen. Den er laget av et profilrør med knaster. Selve ekstruderhuset sveises til stativet, deretter settes en skrue inn i det.
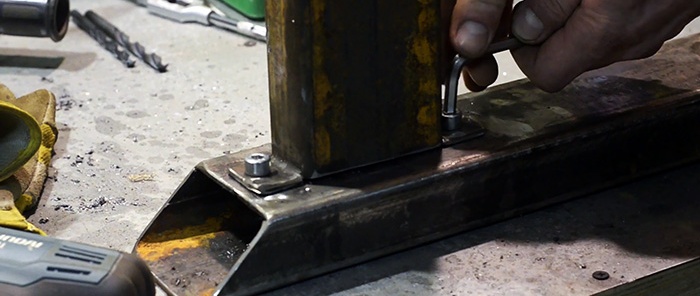
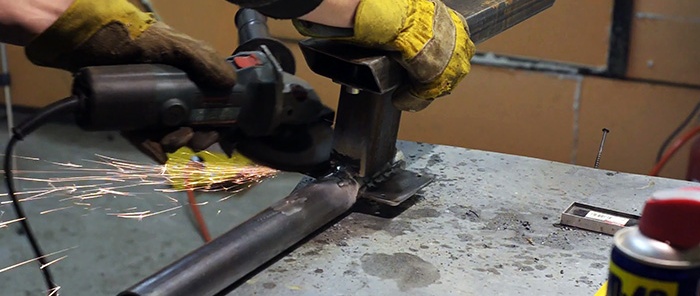
Deretter må du koble skruen til motoren gjennom en reduksjonsgirkasse.
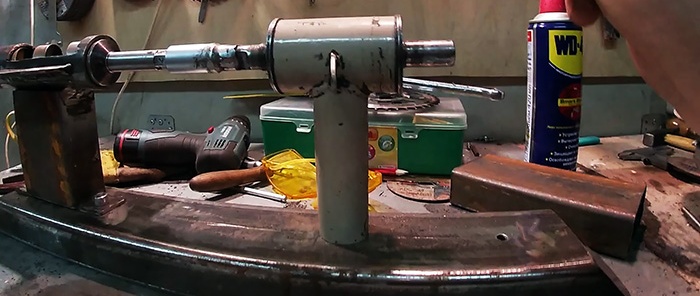
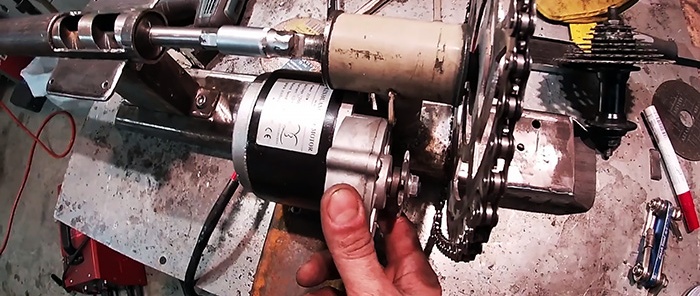
For å gjøre dette er en sykkelvogn koblet til den gjennom stikkontakten. Hodet sveises til vognen, deretter settes det på skruskaftet. Etter dette justeres vognen koaksialt med ekstruderen, og stativet sveises til sålen.
Deretter monteres drivsykkelhjulet på vognakselen. Deretter må du koble drivhjulet til det lille tannhjulet på navkassetten gjennom en rullekjede. Etter dette forbinder samme kjede det store tannhjulet på kassetten med tannhjulet på elmotorgiret. For å gjøre dette, er et annet profilrør sveiset til siden av rammen for å få plass til bøssingen og motoren. I dette tilfellet har drivhjulet 46 tenner, det lille har 11, det midterste har 30, og motorgiret har 9. Dermed vil girforholdet fra motor til drill være 1:140. For pålitelighet må alle stativer forsterkes med sveisekiler.
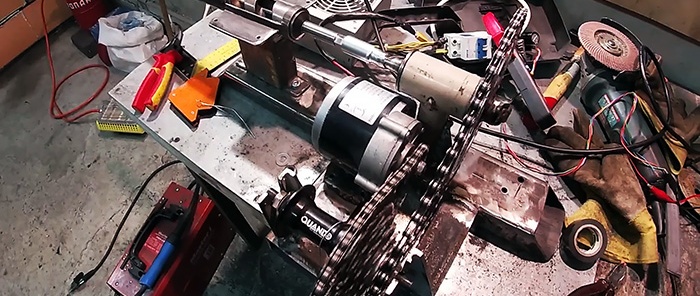
En adapter og et stykke 1/2-tommers rør er sveiset til utgangen av ekstruderhuset. Det skal være en tråd på kanten av røret for å installere dysen. Den bruker en rørleggerplugg med et 4 mm hull boret i midten.
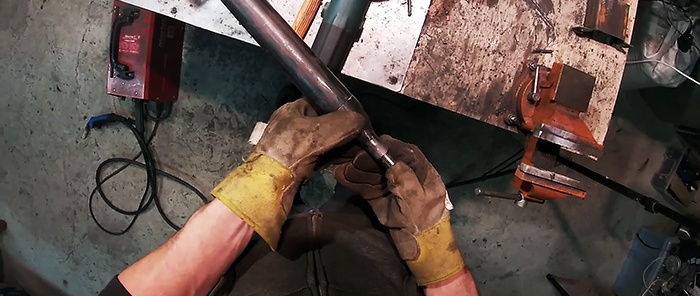
Deretter må du installere ringvarmere på toppen av ekstruderhuset. Hvis diameteren deres ikke stemmer overens, kan foringsrøret økes ved å vikle en stålstrimmel rundt den. Varmere er installert på ekstrudernesen, i midten og i begynnelsen av foringsrøret. Hver av dem er koblet til via en separat PID-kontroller. Deres termiske sensorer er skrudd til huset. For å gjøre dette, må du sveise muttere til den. Det er mulig at antall varmeovner må legges til etter testing.
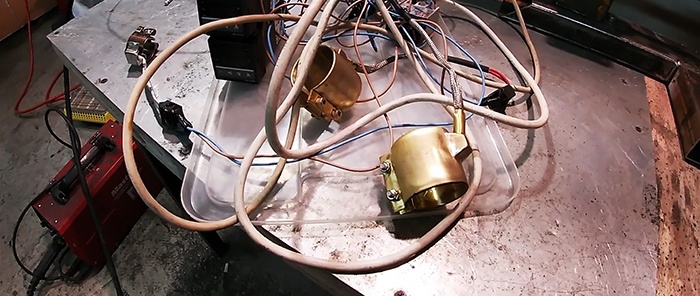
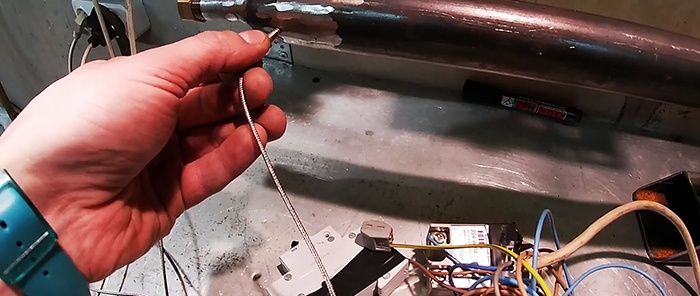
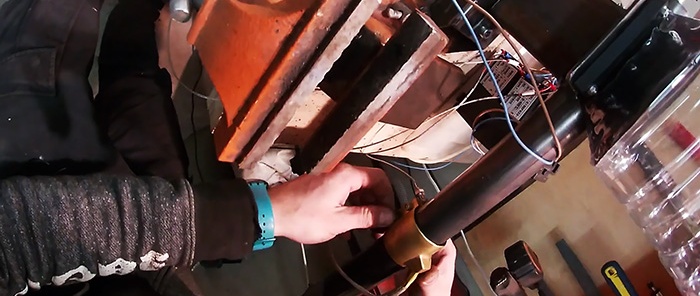
Deretter må du slå på oppvarmingen og justere temperaturen på varmeovnene. Til å begynne med, når du bruker ABS-plastbrikker, er den første satt til 120 °C, den andre 200 °C og den tredje 180 °C. Etter oppvarming starter rotasjonen av skruen. Du må sette den til ca 5 rpm.
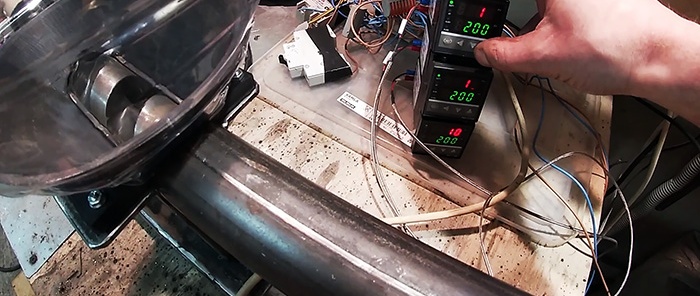
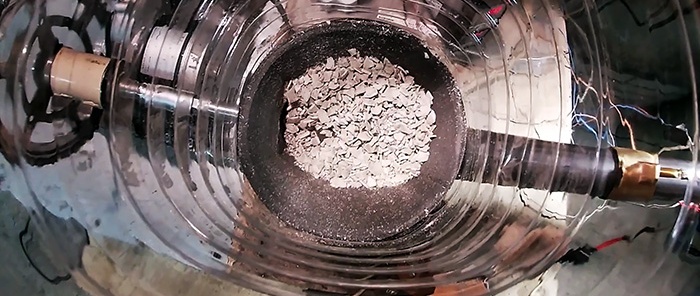
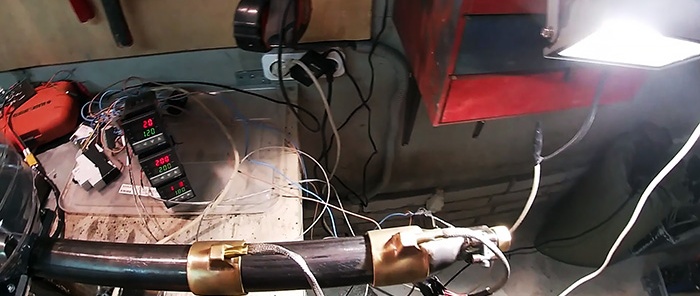
Etter å ha laget ekstruderen, må du sette sammen mange flere enheter for å organisere produksjonen av stangen, men de er gjort mye enklere. Som et minimum vil du også trenge et badekar for å avkjøle stangen, en mottaksvals og en vibrator for beholderen for uavbrutt tilførsel av plastflis til skruen.
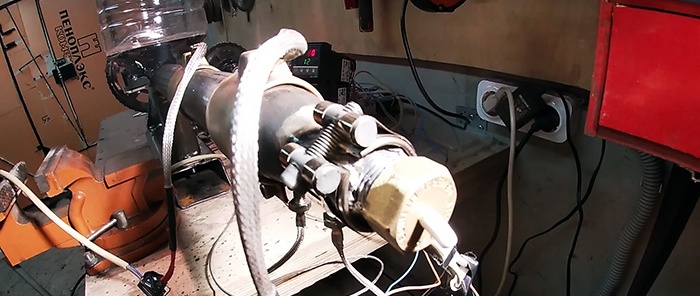
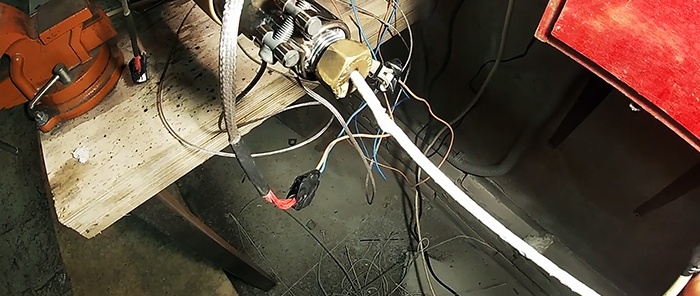
Se videoen for alle detaljer:
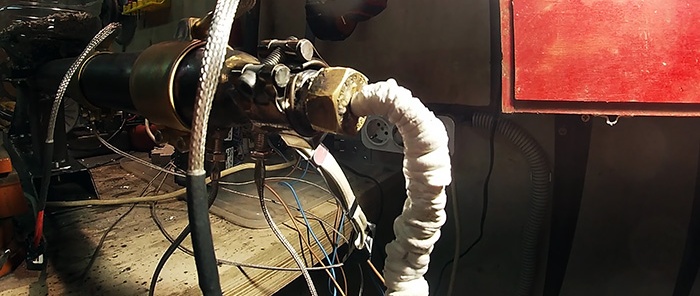
Materialer:
- spiralbor for tre 36 mm;
- stålrør med en innvendig diameter på 37 mm;
- adapter for rør med en diameter på 1/2 tomme;
- 1/2 tommers rør;
- 1/2" rørleggerplugg;
- Plate stål;
- sykkelvogn i huset;
- sykkel drev tannhjul;
- sykkel baknav med kassett;
- rulle kjede;
- elektrisk motor;
- profilrør;
- ringvarmere 320 W – 2-3 stk.;
- ringvarmer 70 W;
- PID-kontrollere for hver varmeovn;
- PWM regulator.
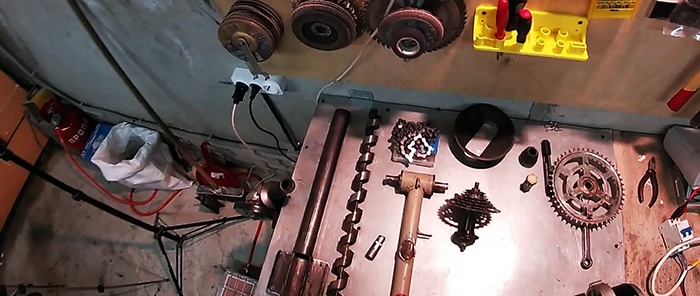
Produksjonsprosess for ekstruder
En spiraltrebor vil bli brukt som ekstruderskrue. Et vannrør er valgt for det. I den må du slipe av den interne sveisesømmen med en fil.Et langsgående kutt lages fra kanten av røret til en dybde på 60-80 mm, og en del av røret kuttes av langs det. Kinn av stålplate sveises til det resulterende sporet på venstre og høyre side. En lastetrakt for knust plast vil bli installert på dem. Den kan skrives ut på en 3D-printer.
En stålplate eller et massivt profilrør kan brukes som ekstruderbase.
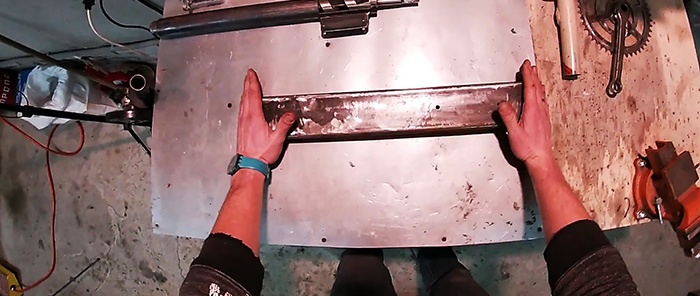
Et stativ er skrudd til basen for å sikre selve ekstruderen. Den er laget av et profilrør med knaster. Selve ekstruderhuset sveises til stativet, deretter settes en skrue inn i det.
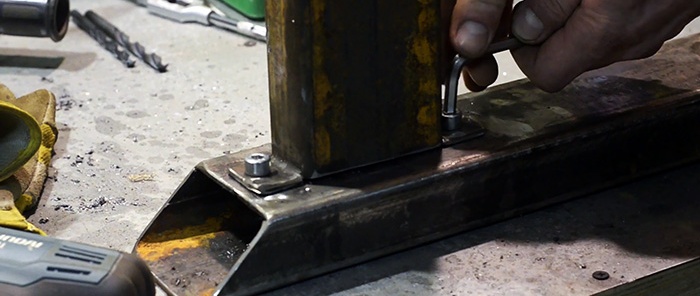
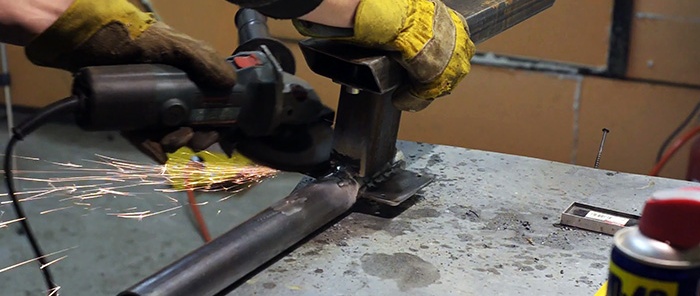
Deretter må du koble skruen til motoren gjennom en reduksjonsgirkasse.
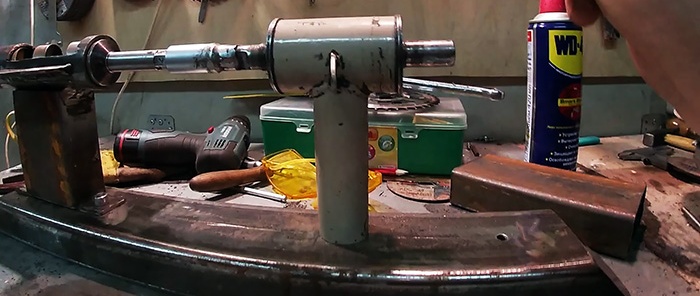
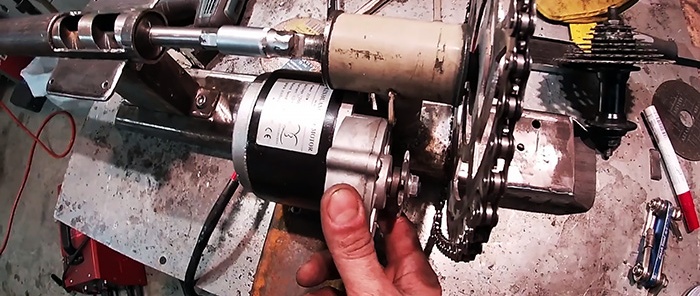
For å gjøre dette er en sykkelvogn koblet til den gjennom stikkontakten. Hodet sveises til vognen, deretter settes det på skruskaftet. Etter dette justeres vognen koaksialt med ekstruderen, og stativet sveises til sålen.
Deretter monteres drivsykkelhjulet på vognakselen. Deretter må du koble drivhjulet til det lille tannhjulet på navkassetten gjennom en rullekjede. Etter dette forbinder samme kjede det store tannhjulet på kassetten med tannhjulet på elmotorgiret. For å gjøre dette, er et annet profilrør sveiset til siden av rammen for å få plass til bøssingen og motoren. I dette tilfellet har drivhjulet 46 tenner, det lille har 11, det midterste har 30, og motorgiret har 9. Dermed vil girforholdet fra motor til drill være 1:140. For pålitelighet må alle stativer forsterkes med sveisekiler.
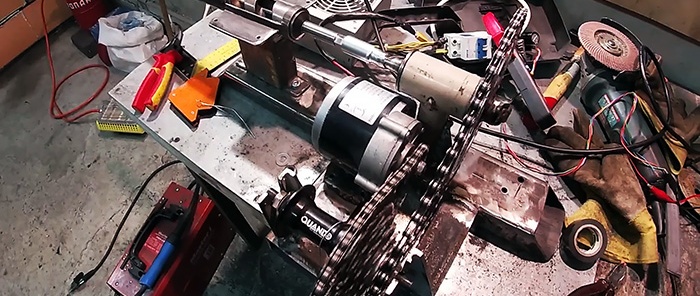
En adapter og et stykke 1/2-tommers rør er sveiset til utgangen av ekstruderhuset. Det skal være en tråd på kanten av røret for å installere dysen. Den bruker en rørleggerplugg med et 4 mm hull boret i midten.
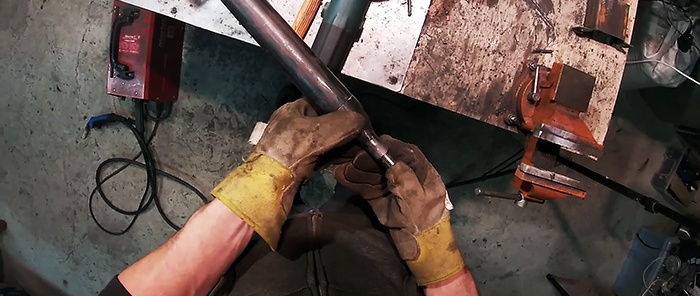
Deretter må du installere ringvarmere på toppen av ekstruderhuset. Hvis diameteren deres ikke stemmer overens, kan foringsrøret økes ved å vikle en stålstrimmel rundt den. Varmere er installert på ekstrudernesen, i midten og i begynnelsen av foringsrøret. Hver av dem er koblet til via en separat PID-kontroller. Deres termiske sensorer er skrudd til huset. For å gjøre dette, må du sveise muttere til den. Det er mulig at antall varmeovner må legges til etter testing.
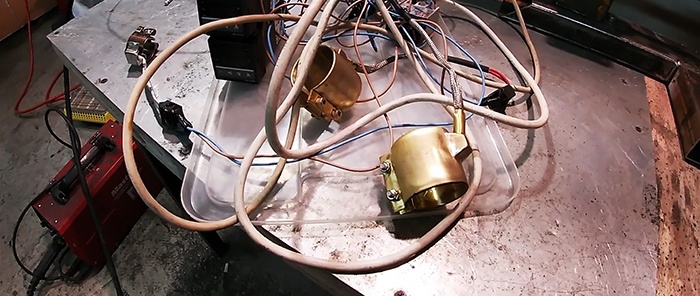
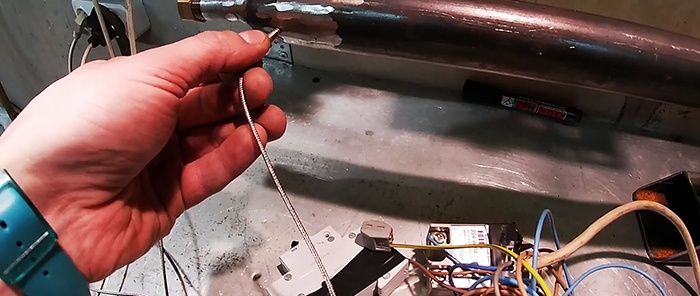
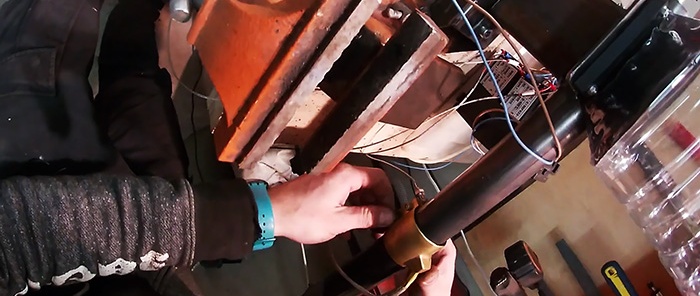
Deretter må du slå på oppvarmingen og justere temperaturen på varmeovnene. Til å begynne med, når du bruker ABS-plastbrikker, er den første satt til 120 °C, den andre 200 °C og den tredje 180 °C. Etter oppvarming starter rotasjonen av skruen. Du må sette den til ca 5 rpm.
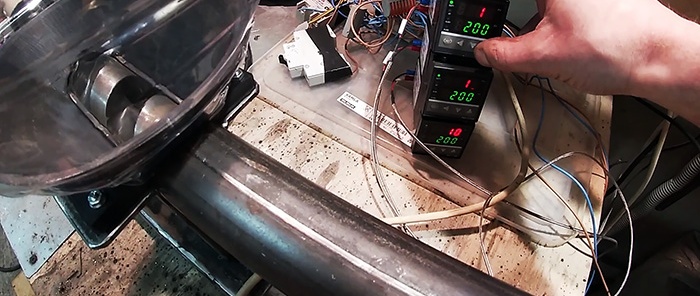
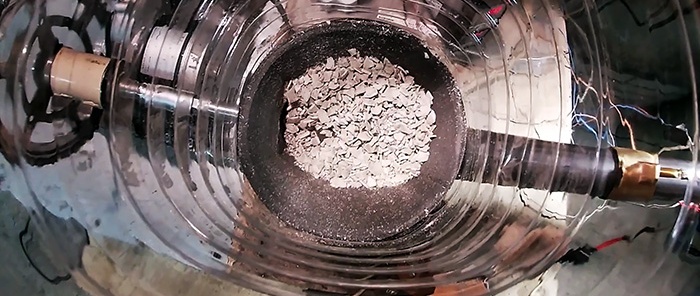
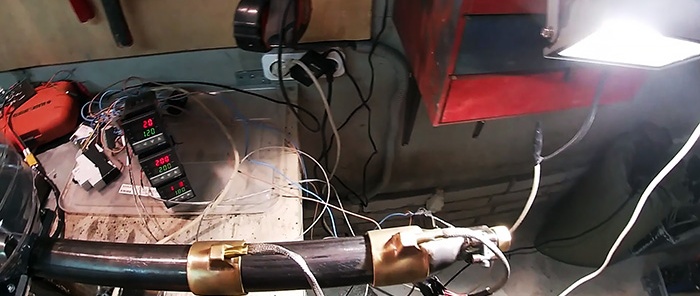
Etter å ha laget ekstruderen, må du sette sammen mange flere enheter for å organisere produksjonen av stangen, men de er gjort mye enklere. Som et minimum vil du også trenge et badekar for å avkjøle stangen, en mottaksvals og en vibrator for beholderen for uavbrutt tilførsel av plastflis til skruen.
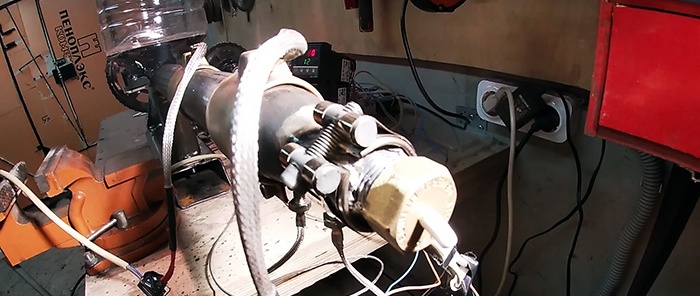
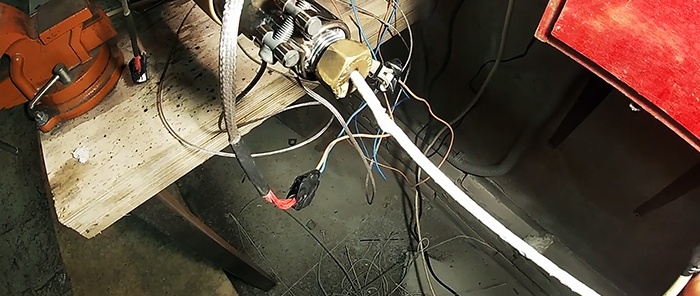
Se videoen
Se videoen for alle detaljer:
Lignende mesterklasser
Spesielt interessant
Kommentarer (0)