Do disco de freio: dispositivo de dobra multifuncional
Existem muitas opções de design para dobradores manuais de tubos, mas os mais produtivos são os dispositivos de alavanca. Ao contrário dos parafusos, eles dobram as peças instantaneamente, embora exijam algum esforço físico. Você pode fazer uma dobradeira não pior do que uma de fábrica em casa, usando peças de rodas de carros antigos como base.
O disco de freio deve ser preparado antes da soldagem, lixando sua superfície até obter metal descoberto.
O ideal é que o disco seja de aço ou ferro dúctil, pois são cozidos sem problemas. Ao usar um disco de um carro doméstico, provavelmente ele será feito de ferro fundido, não destinado à soldagem convencional. Então você precisará usar eletrodos especiais ou envolver o eletrodo de aço com fio de cobre para manter a soldagem forte.
Use uma lixa para chanfrar o anel externo do rolamento. Em seguida, é aplicado com o lado virado para o disco, centralizado com mandril e escaldado.
Devido à solidez do rolamento da roda, a área de soldagem é grande o suficiente para que não rompa sob carga como rolamentos pequenos. É melhor lixar a costura resultante.
Um braço dobrável precisa ser soldado a partir de uma tira de aço. Para fazer isso, 2 mandíbulas da mesma tira são soldadas em uma extremidade. A distância entre eles é de 14 mm. A alguma distância deles são feitos 2 furos, como na foto.
2 parafusos são inseridos neles e soldados. Um pouco mais adiante, o terceiro parafuso é soldado atrás da cabeça sem furo. É necessário que os parafusos fiquem no lado oposto da tira em relação às mandíbulas.
A alavanca resultante é estendida por uma enorme madeira redonda. Quanto mais longo for, mais fácil será dobrar o metal laminado.
Lubrificante é aplicado nos parafusos e tubos 2 mm mais curtos que seu comprimento são montados. Suas extremidades salientes são cobertas com arruelas e escaldadas. O resultado são 3 buchas rotativas.
Em seguida, a alavanca é aplicada ao anel interno do rolamento e soldada.
Em frente aos dois primeiros parafusos, os batentes das tiras são soldados ao disco.
Um batente de parafuso também é feito em frente às garras da alavanca.
Uma bucha também é colocada nele. Você precisa fazer 3 furos no próprio disco para parafusá-lo na mesa.
Agora se você colocar o reforço entre as mandíbulas e o batente e girar a alavanca, obterá uma curva com um pequeno raio. Se você usar buchas de flexão mais próximas da borda do disco, o raio de giro será mais suave.
A máquina pode trabalhar com uma variedade de metais laminados e dobrá-los em quase qualquer ângulo.O batente do parafuso mais distante já está fixado na mesa, pois o raio do disco não é suficiente, mas muito provavelmente a necessidade de tal dobra específica não aparecerá com frequência.
Materiais:
- disco de freio;
- rolamento de roda;
- tira de aço 40x10 mm;
- madeira redonda d20 mm ou mais espessa;
- Parafusos M14 – 4 peças;
- tubo com diâmetro interno de 14-15 mm;
- arruelas para o diâmetro externo do tubo – 3 peças.
Montando um dobrador de tubos
O disco de freio deve ser preparado antes da soldagem, lixando sua superfície até obter metal descoberto.
O ideal é que o disco seja de aço ou ferro dúctil, pois são cozidos sem problemas. Ao usar um disco de um carro doméstico, provavelmente ele será feito de ferro fundido, não destinado à soldagem convencional. Então você precisará usar eletrodos especiais ou envolver o eletrodo de aço com fio de cobre para manter a soldagem forte.
Use uma lixa para chanfrar o anel externo do rolamento. Em seguida, é aplicado com o lado virado para o disco, centralizado com mandril e escaldado.
Devido à solidez do rolamento da roda, a área de soldagem é grande o suficiente para que não rompa sob carga como rolamentos pequenos. É melhor lixar a costura resultante.
Um braço dobrável precisa ser soldado a partir de uma tira de aço. Para fazer isso, 2 mandíbulas da mesma tira são soldadas em uma extremidade. A distância entre eles é de 14 mm. A alguma distância deles são feitos 2 furos, como na foto.
2 parafusos são inseridos neles e soldados. Um pouco mais adiante, o terceiro parafuso é soldado atrás da cabeça sem furo. É necessário que os parafusos fiquem no lado oposto da tira em relação às mandíbulas.
A alavanca resultante é estendida por uma enorme madeira redonda. Quanto mais longo for, mais fácil será dobrar o metal laminado.
Lubrificante é aplicado nos parafusos e tubos 2 mm mais curtos que seu comprimento são montados. Suas extremidades salientes são cobertas com arruelas e escaldadas. O resultado são 3 buchas rotativas.
Em seguida, a alavanca é aplicada ao anel interno do rolamento e soldada.
Em frente aos dois primeiros parafusos, os batentes das tiras são soldados ao disco.
Um batente de parafuso também é feito em frente às garras da alavanca.
Uma bucha também é colocada nele. Você precisa fazer 3 furos no próprio disco para parafusá-lo na mesa.
Agora se você colocar o reforço entre as mandíbulas e o batente e girar a alavanca, obterá uma curva com um pequeno raio. Se você usar buchas de flexão mais próximas da borda do disco, o raio de giro será mais suave.
A máquina pode trabalhar com uma variedade de metais laminados e dobrá-los em quase qualquer ângulo.O batente do parafuso mais distante já está fixado na mesa, pois o raio do disco não é suficiente, mas muito provavelmente a necessidade de tal dobra específica não aparecerá com frequência.
Assista o vídeo
Master classes semelhantes
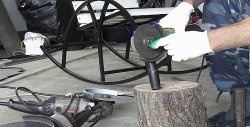
Como desparafusar facilmente a porca de uma rebarbadora se o disco estiver preso
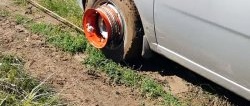
Como fazer um autoejetor para um carro a partir de um disco normal
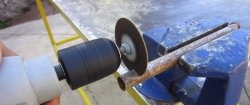
Acessório de corte para uma broca de um disco moedor
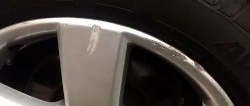
Como restaurar uma roda de carro danificada por um meio-fio
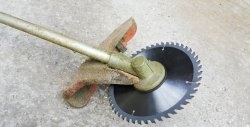
Como instalar uma lâmina de serra em um aparador
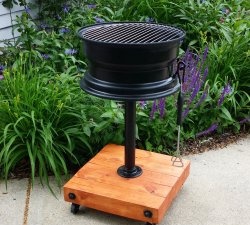
Braseiro feito de aro de roda sem solda
Particularmente interessante
Comentários (2)