Sürtünme kaynağı
Çoğu modern kaynak işlemi, ark deşarjı gibi harici ısı girdisine dayanır. Ancak bağlanan parçalar arasındaki sürtünme nedeniyle doğrudan kaynak bölgesinde ısı üretilebilir.
Isıl enerji, bir parçanın sabit iken ikinci parçanın döndürülmesiyle veya ters yönde döndürülmesiyle elde edilebilir. Ayrıca parçaların baştan sona sabit veya artan bir kuvvetle aynı anda birbirine bastırılması gerekir. İşlem, dönen parçanın sarsılması ve hızla durmasıyla sona erer.
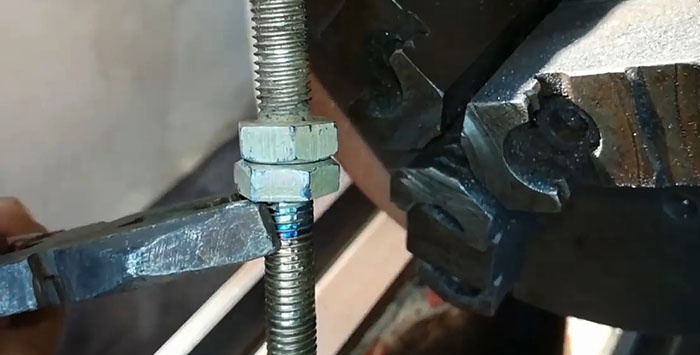
Örneğin elektrikli alın kaynağıyla karşılaştırıldığında, sürtünmeye dayalı işlemin bir takım operasyonel avantajları vardır:
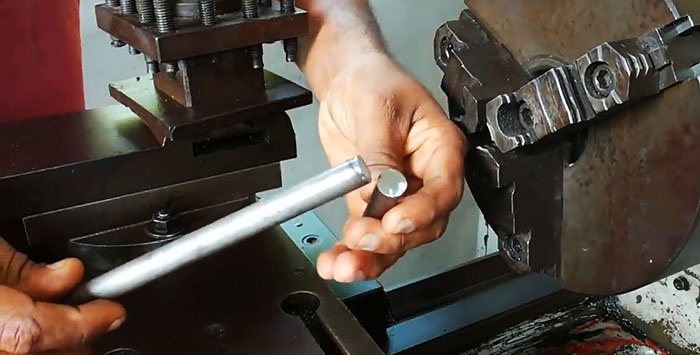
Makinenin aynasına ve mesnetine, çapı 3,5 mm'den fazla, ancak 200 mm'den az olması gereken metal bir çubuğu kelepçeliyoruz. Hem çelik, alüminyum, bakır, bronz hem de farklı metaller olabilirler:
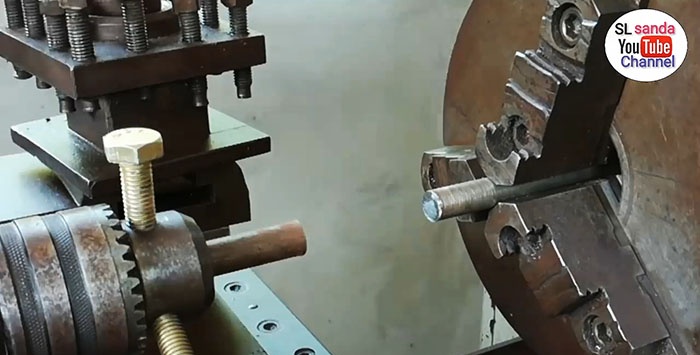
Malzeme kombinasyonları, olağan şekilde kaynak yapılamayanlar bile çok farklı olabilir. Sürtünme kaynağında bu konuda herhangi bir kısıtlama yoktur.
Bizim durumumuzda, aynanın deliklerine vidalanmış, çevre etrafında 120 derecelik eşit aralıklarla yerleştirilmiş üç cıvatayı kullanarak çubuğu mesnete sabitliyoruz. Onların yardımıyla, bir veya daha fazla cıvatayı sıkarak veya gevşeterek aynaya kenetlenen çubuğa göre hizalama yapıyoruz.
Bu kaynak yönteminin teknolojisinin gerektirdiği kaynak işlemi sırasında bağlama kuvvetini arttırmak için mesneti çubuklar uç uca kadar getirip sabitliyoruz veya elle tutuyoruz.
Makineyi açıyoruz, bunun sonucunda makine aynasına kenetlenen çubuk dönmeye başlıyor. Bizim durumumuzda, mesnete sabitlenen çubuk hareketsizdir ancak prensipte ters yönde dönebilir, bu da işlem süresini kısaltacaktır.
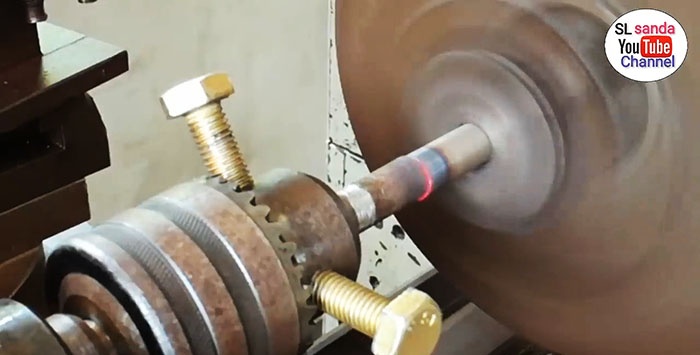
Yakında çubukların temas noktasında başlayan ve bunlar boyunca zıt yönlere yayılan kararmış renkleri göreceğiz; bu, metalin sürtünme sonucu hızla ısınmasının doğrudan bir işaretidir.
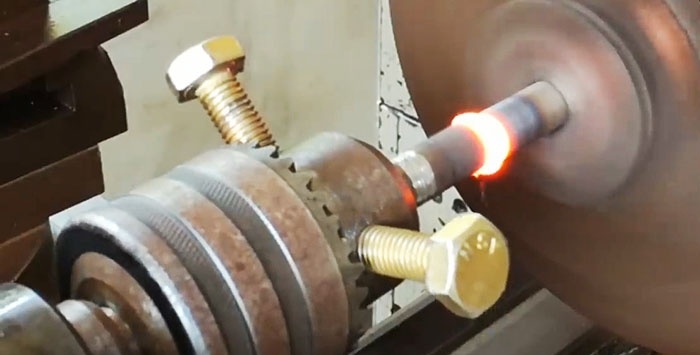
Kısa bir süre sonra temas bölgesindeki metal parlak bir şekilde parlayacak ve çubukların boyutlarının ötesinde bir halka oluşumu şeklinde sıkılmaya başlayacaktır.Bu halka aynı zamanda çapak da içerecektir: kireç, yanmamış gres, katı metalik olmayan kalıntılar, vb.
Temas noktasında en parlak parlama anında, iki çubuğun metalinin sertleşmesi için makine keskin bir şekilde kapatılmalıdır. Aynı zamanda, mesnet sabitlenmemişse, temas bölgesindeki yer değiştiren metalin hacmini telafi etmek ve daha güçlü ve kaliteli bir bağlantı elde etmek için üzerindeki baskıyı kademeli olarak artırmak gerekir.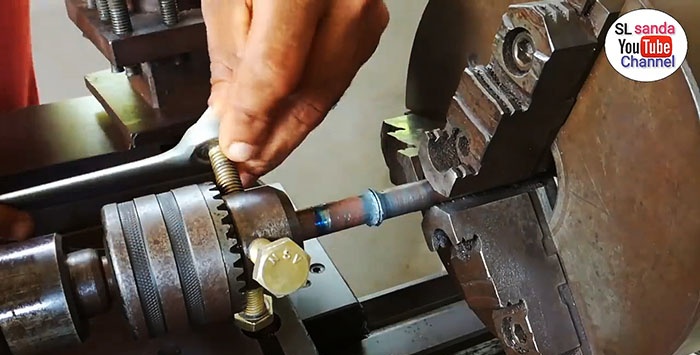
Kızdırma durana kadar bekledikten sonra (ve bu, metalin tamamen sertleştiğinin bir işaretidir), sabitleme cıvatalarını gevşetebilir ve mesneti çıkarabilirsiniz. Artık geriye kalan tek şey sürtünme kaynağının kalitesini kontrol etmektir.
Bunu yapmak için, makineyi tekrar açın ve kaynak çubuğunun hafif bir salgısını tespit edin; bu, başlangıçta kurulum sırasında yanlış hizalamanın bir sonucudur. Bu kusur, temas alanındaki ekstrüde çapakların döndürülmesi ve çıkarılmasıyla giderilebilir.
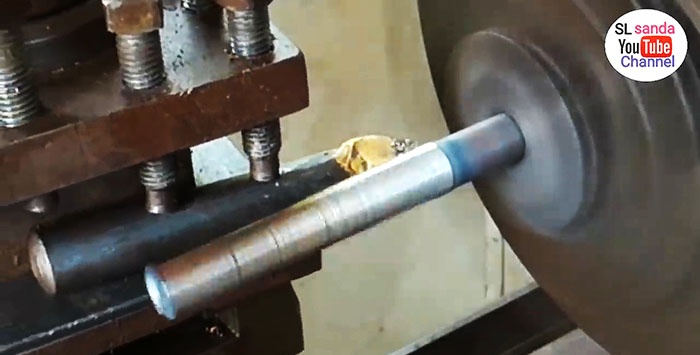
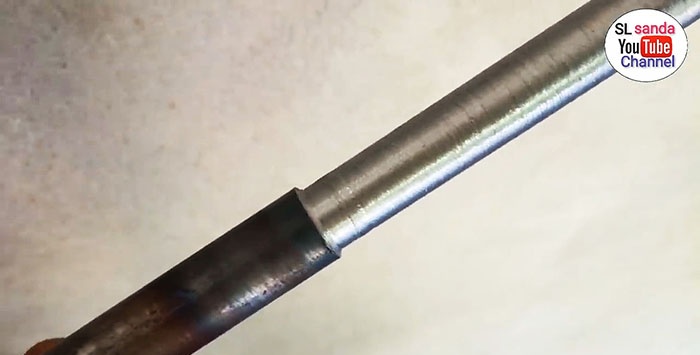
Metalin daha derine nüfuz etmesi, iki çubuğun kaynak bölgesinde hiçbir özelliğin görülmediğini gösterir. Görünüşe göre burası iki çubuğun temas noktası değil, bunlardan birinin gövdesi.
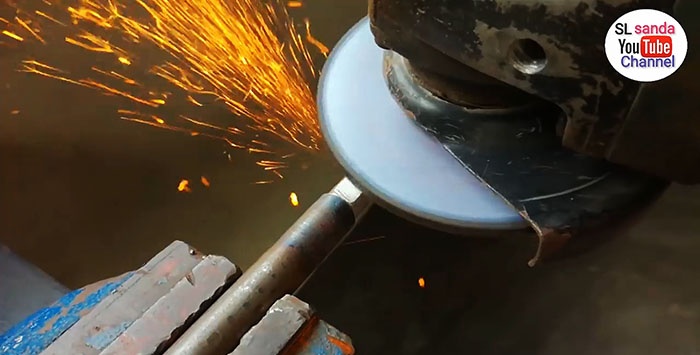
Sürtünme kaynağının aşağıdaki kalite kontrolünü gerçekleştiriyoruz. Bu şekilde bağlanan çubukları bir mengeneye sıkıştırıyoruz ve temas bölgesinde bir "raf" oluşturmak için bir taşlama diski kullanıyoruz ve yine metalin homojenliğine ikna oluyoruz, bu da kaynağın kalitesini de gösteriyor.
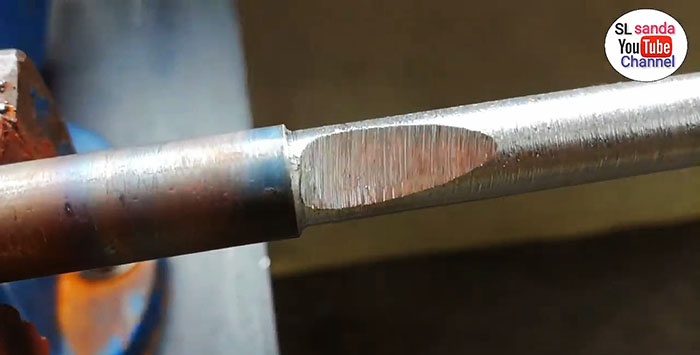
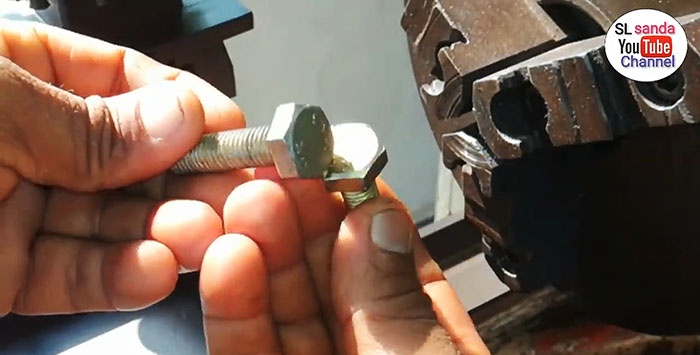
Sürtünme kaynağı seri üretilen kafaları ve cıvataları birleştirmek için kullanılabilir. İşlem, çubuklarla yapılan işlemden farklı değildir: bir cıvata makinenin aynasına, diğeri mesnete sıkıştırılır.
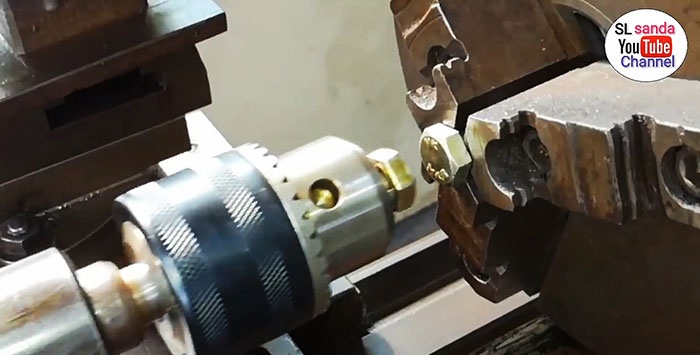
İkincisinin yardımıyla cıvatalar kafalara temas ettirilir ve makine çalıştırılır. Sürücüyü zamanında kapatmak için sıkma kuvvetini arttırmak ve kaynak anını yakalamak da gereklidir.
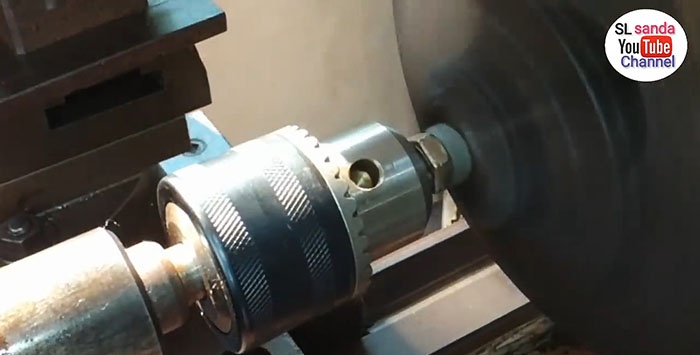
Sürtünme kaynağı, diğer türlerle kaynaklanması zor veya imkansız olan malzemeleri birleştirmek için kullanılabilir: çelik ve alüminyum, östenitik çelikler ve perlitik olanlar. Ayrıca plastik iş parçalarını kolaylıkla birleştirmek için de kullanılabilir.
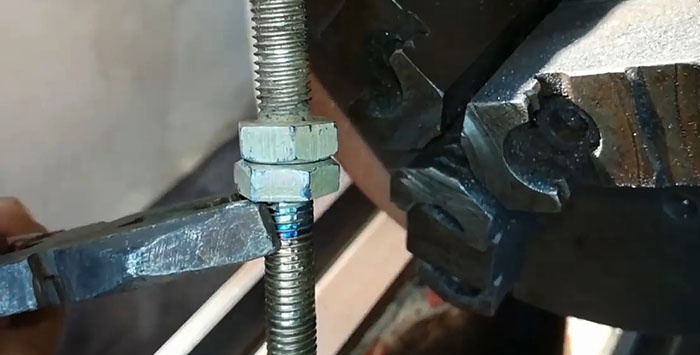
Sürtünmeli birleştirme kullanılarak yapılan hesaplamalar ve uygulamalar, bu yöntemin çapı 6-100 mm aralığında olan iş parçaları için daha uygun olduğunu göstermektedir. Çapı 200 mm'den büyük olan kaynak çubukları, işlem daha fazla güç (0,5 bin kW) ve eksenel kuvvet (3 × 106 N) gerektireceğinden ekonomik olarak karlı değildir. Yüksek hızlar (200 rpm) sağlama ihtiyacı ve sürücünün ne zaman kapatılacağını belirlemenin zorluğu nedeniyle çapı 3,5 mm'den küçük olan çubukların bu yöntemle bağlanması mümkün olmayacaktır.
Isıl enerji, bir parçanın sabit iken ikinci parçanın döndürülmesiyle veya ters yönde döndürülmesiyle elde edilebilir. Ayrıca parçaların baştan sona sabit veya artan bir kuvvetle aynı anda birbirine bastırılması gerekir. İşlem, dönen parçanın sarsılması ve hızla durmasıyla sona erer.
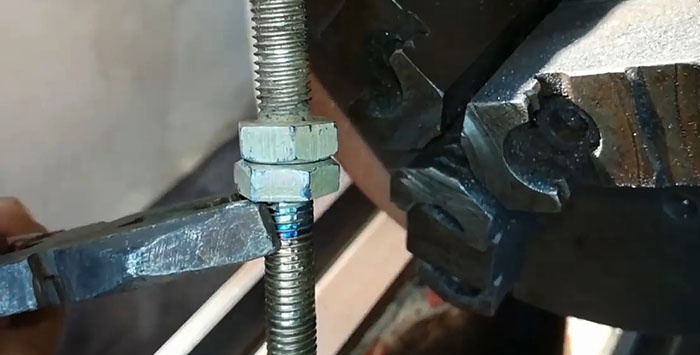
Örneğin elektrikli alın kaynağıyla karşılaştırıldığında, sürtünmeye dayalı işlemin bir takım operasyonel avantajları vardır:
- enerji maliyetleri büyük ölçüde azalır;
- kaynaklı bağlantı her zaman güvenilirdir, çünkü yalnızca kaynak yapılan ürünlerin termofiziksel özelliklerine bağlıdır;
- işlemin başlangıcında kireç, pas, gres ve gres yandığı veya bir anda sıkışıp kaldığı için, bağlanacak bağlantı için özel bir hazırlığa gerek yoktur;
- 6±1 dereceye kadar açılara kadar iş parçalarının paralelliğinin ihlali durumunda bile bağlantının kalitesi etkilenmez;
- ultraviyole radyasyon ve zararlı gaz emisyonları şeklinde olumsuz faktörlerin olmaması;
- teknolojik ekipmanın basitliği, rutin bakıma, mekanizasyona ve otomasyona kolayca uyum sağlaması.
Tornada sürtünme kaynağı işlemi
Çelik çubukların kaynaklanması
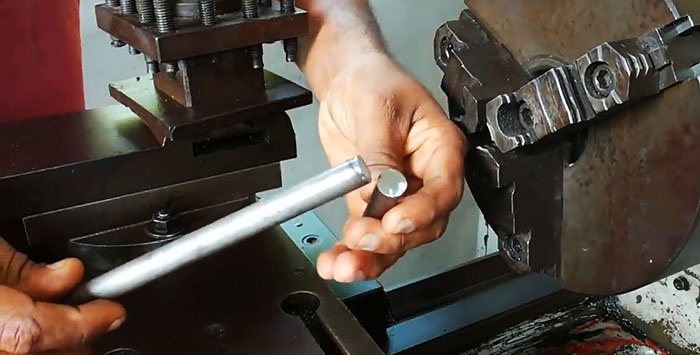
Makinenin aynasına ve mesnetine, çapı 3,5 mm'den fazla, ancak 200 mm'den az olması gereken metal bir çubuğu kelepçeliyoruz. Hem çelik, alüminyum, bakır, bronz hem de farklı metaller olabilirler:
- çelik ve alüminyum;
- çelik ve bakır;
- alüminyum ve bronz vb.
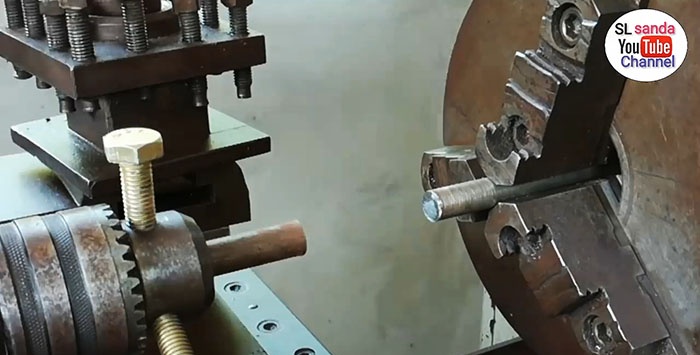
Malzeme kombinasyonları, olağan şekilde kaynak yapılamayanlar bile çok farklı olabilir. Sürtünme kaynağında bu konuda herhangi bir kısıtlama yoktur.
Bizim durumumuzda, aynanın deliklerine vidalanmış, çevre etrafında 120 derecelik eşit aralıklarla yerleştirilmiş üç cıvatayı kullanarak çubuğu mesnete sabitliyoruz. Onların yardımıyla, bir veya daha fazla cıvatayı sıkarak veya gevşeterek aynaya kenetlenen çubuğa göre hizalama yapıyoruz.
Bu kaynak yönteminin teknolojisinin gerektirdiği kaynak işlemi sırasında bağlama kuvvetini arttırmak için mesneti çubuklar uç uca kadar getirip sabitliyoruz veya elle tutuyoruz.
Makineyi açıyoruz, bunun sonucunda makine aynasına kenetlenen çubuk dönmeye başlıyor. Bizim durumumuzda, mesnete sabitlenen çubuk hareketsizdir ancak prensipte ters yönde dönebilir, bu da işlem süresini kısaltacaktır.
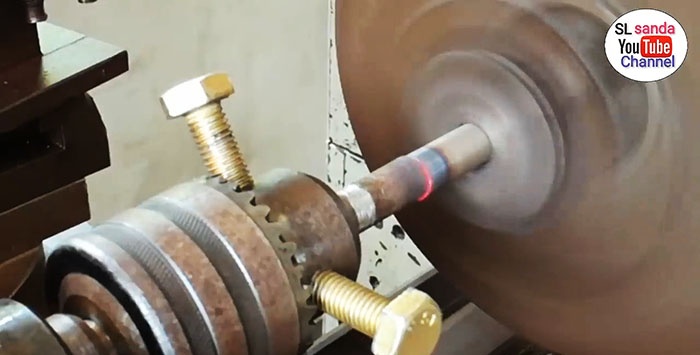
Yakında çubukların temas noktasında başlayan ve bunlar boyunca zıt yönlere yayılan kararmış renkleri göreceğiz; bu, metalin sürtünme sonucu hızla ısınmasının doğrudan bir işaretidir.
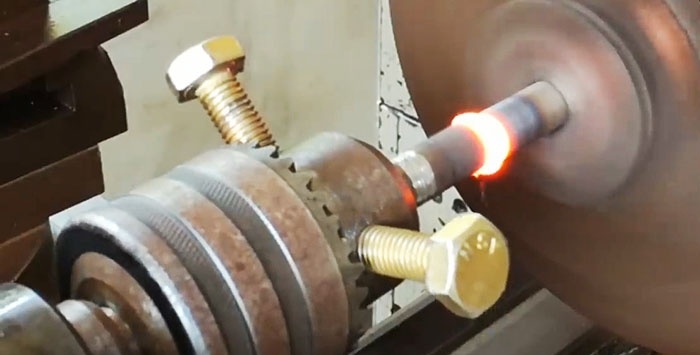
Kısa bir süre sonra temas bölgesindeki metal parlak bir şekilde parlayacak ve çubukların boyutlarının ötesinde bir halka oluşumu şeklinde sıkılmaya başlayacaktır.Bu halka aynı zamanda çapak da içerecektir: kireç, yanmamış gres, katı metalik olmayan kalıntılar, vb.
Temas noktasında en parlak parlama anında, iki çubuğun metalinin sertleşmesi için makine keskin bir şekilde kapatılmalıdır. Aynı zamanda, mesnet sabitlenmemişse, temas bölgesindeki yer değiştiren metalin hacmini telafi etmek ve daha güçlü ve kaliteli bir bağlantı elde etmek için üzerindeki baskıyı kademeli olarak artırmak gerekir.
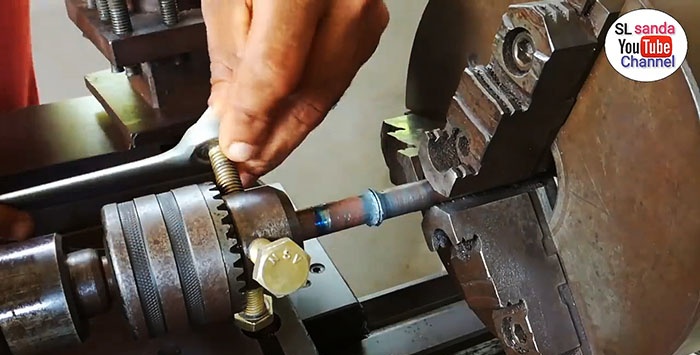
Kızdırma durana kadar bekledikten sonra (ve bu, metalin tamamen sertleştiğinin bir işaretidir), sabitleme cıvatalarını gevşetebilir ve mesneti çıkarabilirsiniz. Artık geriye kalan tek şey sürtünme kaynağının kalitesini kontrol etmektir.
Bunu yapmak için, makineyi tekrar açın ve kaynak çubuğunun hafif bir salgısını tespit edin; bu, başlangıçta kurulum sırasında yanlış hizalamanın bir sonucudur. Bu kusur, temas alanındaki ekstrüde çapakların döndürülmesi ve çıkarılmasıyla giderilebilir.
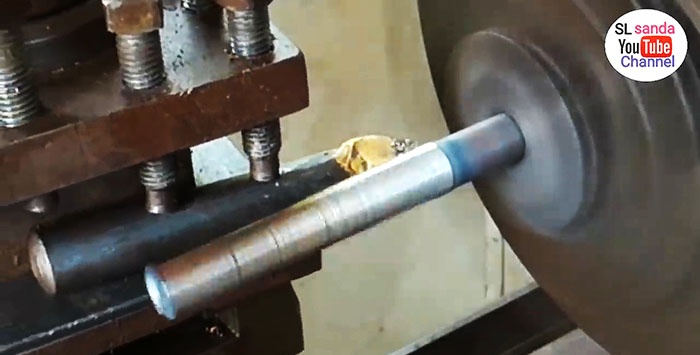
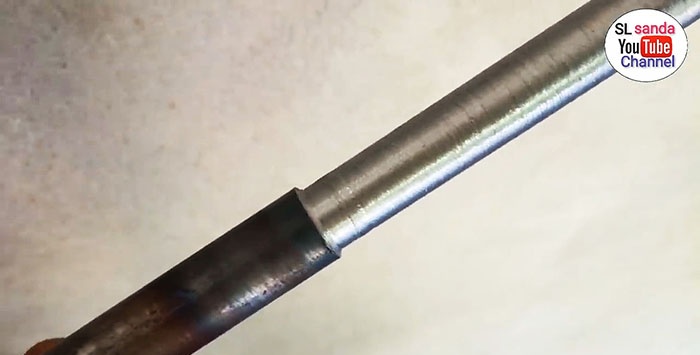
Metalin daha derine nüfuz etmesi, iki çubuğun kaynak bölgesinde hiçbir özelliğin görülmediğini gösterir. Görünüşe göre burası iki çubuğun temas noktası değil, bunlardan birinin gövdesi.
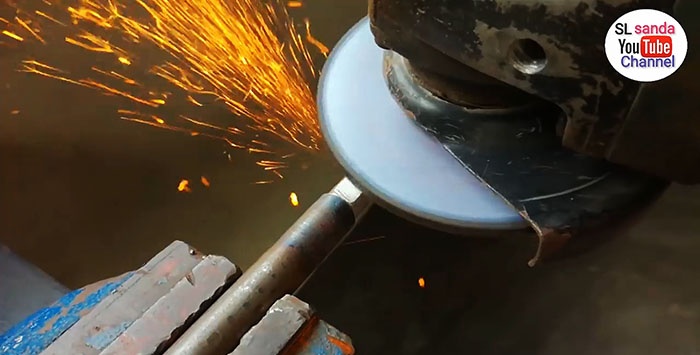
Sürtünme kaynağının aşağıdaki kalite kontrolünü gerçekleştiriyoruz. Bu şekilde bağlanan çubukları bir mengeneye sıkıştırıyoruz ve temas bölgesinde bir "raf" oluşturmak için bir taşlama diski kullanıyoruz ve yine metalin homojenliğine ikna oluyoruz, bu da kaynağın kalitesini de gösteriyor.
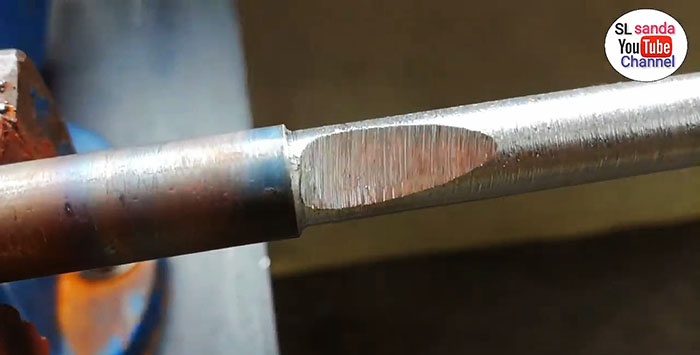
Cıvata bağlantısı
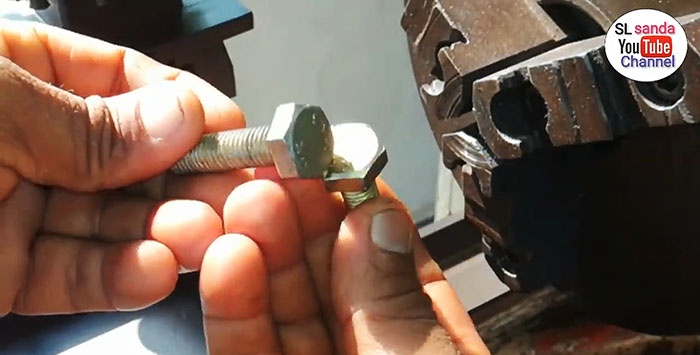
Sürtünme kaynağı seri üretilen kafaları ve cıvataları birleştirmek için kullanılabilir. İşlem, çubuklarla yapılan işlemden farklı değildir: bir cıvata makinenin aynasına, diğeri mesnete sıkıştırılır.
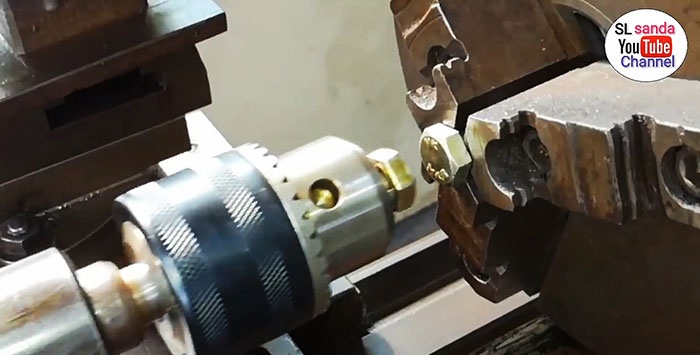
İkincisinin yardımıyla cıvatalar kafalara temas ettirilir ve makine çalıştırılır. Sürücüyü zamanında kapatmak için sıkma kuvvetini arttırmak ve kaynak anını yakalamak da gereklidir.
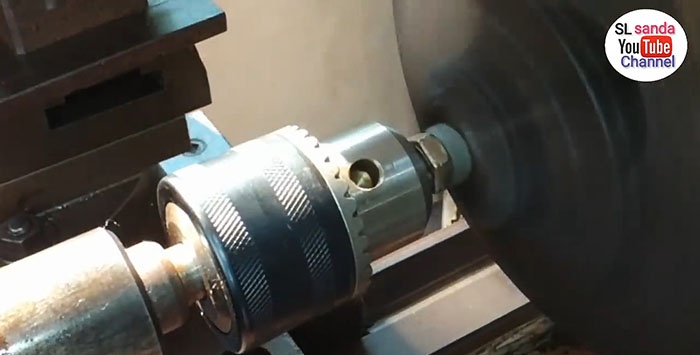
Sürtünme kaynağı, diğer türlerle kaynaklanması zor veya imkansız olan malzemeleri birleştirmek için kullanılabilir: çelik ve alüminyum, östenitik çelikler ve perlitik olanlar. Ayrıca plastik iş parçalarını kolaylıkla birleştirmek için de kullanılabilir.
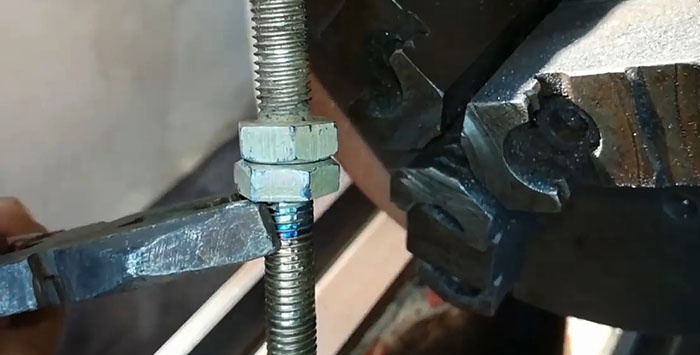
Sürtünmeli birleştirme kullanılarak yapılan hesaplamalar ve uygulamalar, bu yöntemin çapı 6-100 mm aralığında olan iş parçaları için daha uygun olduğunu göstermektedir. Çapı 200 mm'den büyük olan kaynak çubukları, işlem daha fazla güç (0,5 bin kW) ve eksenel kuvvet (3 × 106 N) gerektireceğinden ekonomik olarak karlı değildir. Yüksek hızlar (200 rpm) sağlama ihtiyacı ve sürücünün ne zaman kapatılacağını belirlemenin zorluğu nedeniyle çapı 3,5 mm'den küçük olan çubukların bu yöntemle bağlanması mümkün olmayacaktır.
Videoyu izle
Benzer ana sınıflar
Özellikle ilginç
Yorumlar (1)