Wie man ein elektrisches Holzkohlegebläse für einen Grill herstellt
Der Frühling ist bereits in vollem Gange. Noch ein bisschen und der Schnee schmilzt und die Grillsaison steht vor der Tür. Wieder das endlose Wedeln eines Stücks Pappe über der Kohle, rote, tränende Augen, versengte Bärte und Schnurrbärte! Manche Amateure finden einen Ausweg aus der Situation; Schließen Sie Ventilatoren, Haartrockner und sogar alte Staubsauger an! Das ist natürlich alles wunderbar, aber wenn Sie Fleisch gerne im Freien braten, wo es keinen Strom gibt, müssen Sie die Kohlen selbst anzünden. Außerdem kann aufgrund bestimmter Umstände nicht jeder ein Picknick in einem Auto machen, das über eine große Batterie verfügt, an die man ein geeignetes Gerät anschließen kann. Auch hier können Sie ein spezielles Gerät zum Anfächern der Kohlen kaufen. Mittlerweile gibt es eine riesige Vielfalt davon, in unterschiedlichen Typen und Modifikationen! Es gibt manuelle Geräte (Sie müssen den Griff drehen, um den Propeller anzutreiben), es gibt elektrische, batteriebetriebene. Aber Sie können dieses einfache Gerät selbst herstellen. Das Design ist nicht kompliziert.
Wird benötigt
- Leere Blechdose (ich habe sie unter der Farbe hervorgeholt).
- Motor (9 bis 12 Volt).
- Kühlerer Propeller.
- Graveur mit Trennscheibe, Schleifstein und Bohrer.
- Das Rohr besteht aus Metall mit einem Durchmesser von 20 mm und einer Länge von 7–8 cm.
- Das Rohr besteht aus Kunststoff, ist 7–8 cm lang und der Durchmesser entspricht der Dicke des Motors.
- Lötkolben mit Lot.
- Sekundärkleber.
- Schalten.
- Zwei Schrauben mit Gewinde oben am Motor.
- Zange.
- Marker.
- Schere.
- Datei.
- Schreibwarenmesser.
- Schraubendreher.
- Batterie passend zu den Bedürfnissen des Motors.
- Sprühfarbe (Farbe Ihrer Wahl).
Zusammenbau eines Kohlegebläses
Zuerst müssen Sie die Parameter des Blechdosenkörpers vorbereiten und berechnen. Dazu müssen Sie die ungefähre Dicke der zukünftigen Lufteinlasstrommel abschätzen. Unsere Dicke ergibt sich aus der dicksten Stelle, nämlich dem Auslassrohr.
Vergessen Sie dabei nicht die Reserve. 5 Millimeter auf beiden Seiten reichen aus. Zeichnen Sie mit einem Marker eine Schnittlinie und schneiden Sie das gewünschte Stück ab.
Werfen Sie die Reste der Blechdose nicht weg – sie landen am Ende der Trommel. Wir schneiden ein Stück Blech von der Dose ab, das das Ende der Trommel vollständig bedeckt, befestigen das Ende, skizzieren es mit einem Marker und schneiden das runde Stück aus.
Als nächstes schneiden wir eine Aussparung am Rohr aus, die der Wölbung der Seite der Trommel entspricht, und an der Seite der Trommel befindet sich ein Loch, in das das angepasste Rohr passt. So:
Nun bohren wir an einer der Endplatten drei Löcher für den Motor; ein großes für den Hals mit der Welle und zwei kleinere an den Seiten für die Schrauben, mit denen es am Motor befestigt ist.
Probieren wir den Motor auf dem Teller aus:
Kommen wir nun zum Einstellen des Griffs. Wir messen den Abstand der Motorlänge von der Oberseite des Kunststoffrohrs zuzüglich des Randes und schneiden ein Loch für den Schalter. Versuchen wir es mit dem Schalter:Als nächstes probieren wir den Motor an.Wenn sich herausstellt, dass es für das Rohrkaliber klein ist, können Sie es durch Aufwickeln von Isolierband dicker machen.
Nun schneiden wir an der zweiten Endplatte ein Loch für den Lufteinlass aus.
Hier habe ich die Stärke und Geschwindigkeit des Motors etwas falsch eingeschätzt und die Löcher zu klein gemacht. Dann musste ich ein großes Loch in die Mitte schneiden.
Wenn Ihr Motor hohe Drehzahlen hat, können die Löcher so geschnitten werden, wie ich es zuerst gemacht habe – gemustert. So ist es schöner. Das reicht für einen hochdrehenden Motor. Jetzt kommt der lustige Teil; Alle Teile verlöten! Aufgrund seiner geringen Dicke lässt sich das Zinn einfach und schnell ohne Vorwärmen löten. Kein Löten, sondern pures Vergnügen! Mit Flussmittel und Lot verzinnen wir die Abschnitte auf dem Metall. Wir löten das Rohr für den Luftauslass.
Auf die gleiche Weise löten wir die untere Endplatte, auf der der Motor montiert wird. Wir befestigen den Motor.
Wir setzen den Propeller auf die Welle.
Löten Sie die obere Endplatte mit Löchern.
Als nächstes löten Sie die Drähte an den Schalter.
Installieren Sie den Schalter im Gehäuse. Nun löten wir einen Draht vom Schalter an einen der Kontakte des Motors und einen freien langen Draht an den zweiten Kontakt des Motors.
Wir entfernen die Drähte von der Unterseite des Griffs und befestigen den Griff mit Sekundenkleber am Motor und an der Trommel.
Wir achten sorgfältig darauf, dass der Kleber nicht in das Motorinnere gelangt! Hier ist es besser, dicken Sekundenkleber auf Gelbasis zu verwenden. Jetzt muss nur noch die Buchse für den Netzteilstecker angelötet werden. Löten Sie die Buchse an ein zweiadriges Stück Draht.
Schneiden Sie ein Loch in die Griffabdeckung.
Wir legen eine Abdeckung auf das Kabel und löten das Kabel an die Ausgangskontakte.
Wir überwachen die Polarität, damit sich der Propeller in die richtige Richtung dreht! Kleben Sie den Deckel auf den Griff.
Als Abdeckung oder Stopfen für den Griff können Sie jedes runde Stück mit passendem Durchmesser verwenden. Es bleibt nur noch, dem fertigen Produkt ein anständiges Aussehen zu verleihen. Wir decken alle vorhandenen Löcher in der Trommel ab, wickeln den Griff mit einer Art Schutz ein und lackieren die Trommel.
Jetzt bleibt nur noch, es auszuprobieren. Alles funktioniert super!
Sie können den Inflator natürlich leistungsstärker machen. Wenn Sie beispielsweise einen Zwölf-Volt-Motor darin einbauen, verwenden Sie einen Schraubendreher. Dieser kann auch an eine Autobatterie angeschlossen werden. Aber ich denke, dass eine solche Kraft nicht nötig ist – sie wird eine Menge Asche aufwirbeln, die sich auf dem Essen absetzt. Ich habe einem kaputten Spielzeug einen Neun-Volt-Motor entnommen. Das ist völlig ausreichend. Auch die Stromversorgung ist selbstgebaut und besteht aus drei 18650-Akkus und einem schützenden Lademodul.
Und noch ein Punkt – warum ich Zinn und nicht Plastik verwendet habe, das einfacher zu verarbeiten ist. Nicht jeder Kunststoff hält den Temperaturen stand, die beim Verbrennen von Kohlen entstehen. Und für mich persönlich ist die Arbeit mit Löten viel angenehmer als die Arbeit mit Kunststoff und Kleber.
Schau das Video
Ähnliche Meisterkurse
Besonders interessant
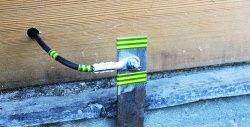
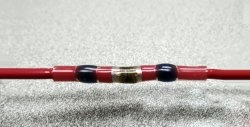
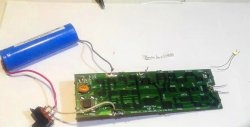
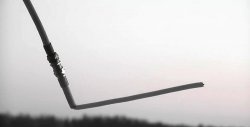
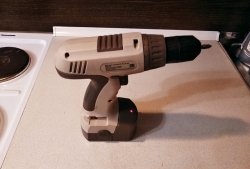
