Wie man aus Altmetall einen Langzeitofen baut
Zum Heizen der Garage können Sie einen Ofen aus einem 200-Liter-Eisenfass verwenden, der sowohl effizient als auch wirtschaftlich ist. Um es herzustellen, benötigen Sie einige Kenntnisse im Umgang mit Metall.
Wird benötigt
Material:
- zwei 200-Liter-Stahlfässer;
- Armaturen;
- Ecken 45×45 mm und 30×30 mm;
- 3 verlängerte Muttern M10;
- 3 M10-Schrauben mit Muttern;
- Eisenblech;
- Stahlband 20 mm breit;
- Rohre mit einem Durchmesser von 60 und 115 mm;
- Teil aus einem Propantank;
- 2 Scharniere und 2 Metallhalterungen;
- Satz Muttern, Schrauben usw.
Werkzeuge: Markierungs- und Messzubehör, Schleifer, Schweißgerät, Pendelsäge, Bohrer, Matrize usw.
Der Prozess der Herstellung eines Festbrennstoffofens mit langer Brenndauer aus Altmetall
Wir schneiden den Deckel vom Fass ab und formen daraus einen Gitterrost aus Bewehrung, schneiden ihn auf die Größe des Deckels zu und legen ihn im Abstand von 10 mm auseinander. Wir schweißen die Querstangen oben an den Kreuzungspunkten an jede Stange. Auch die Beine für den 100 mm hohen Rost bestehen aus Armierung.
Legen Sie den Rost auf den Boden des Fasses.
An drei Ecken 45x45 mm mit einer Länge von 620 mm auf einer Seite jedes Endes 30 Grad messen und mit einer Schleifmaschine abschneiden. Indem wir die Ecken entlang der Schnittlinien falten, erhalten wir ein gleichseitiges Dreieck. Nach der Anpassung verbrühen wir alle Gelenke.
Wir platzieren verlängerte M10-Muttern in den Ecken des Dreiecks und verschweißen sie. Wir schrauben Schrauben und Muttern hinein. Wir platzieren das Stativ mit Bolzen auf dem Boden, legen den Deckel darauf und schweißen 3 Anschläge aus Verstärkung an das Stativ, um den Lauf zu stabilisieren.
Aus einem Blech schneiden wir einen Kreis mit einem Durchmesser von 530 mm. Aus einer 30x30 mm großen Ecke fertigen wir 3 Stücke mit einer Länge von 210 mm. Wir schweißen sie an die Unterseite des Deckels, auf den wir einen Kreis legen und diesen ebenfalls anschweißen. Wir schweißen auch das Loch aus dem Korken.
Wir fertigen die Deckelgriffe aus zwei Metallstreifen, schneiden die Markierungen auf die Hälfte der Dicke und biegen sie um 90 Grad. Zur Stärkung kochen und reinigen wir die Biegungen. Wir legen sie auf den Deckel und verschweißen sie.
Um der Verbrennungszone Luft zuzuführen, nehmen Sie ein 60-mm-Rohr. Wir fertigen 2 Abschnitte mit einer Länge von 230 mm und einem 45-Grad-Beschnitt und 500 mm mit einem vorgefertigten Beschnitt. Wir entfernen die Fasen an den Enden, befestigen alles sauber und schweißen es.
Um das Rohr im Fass zu installieren, schneiden Sie 190 mm von der Oberseite entfernt ein Loch. Führen Sie von der Innenseite des Laufs ein kurzes Rohrstück bis zum Anschlag in das Loch ein und schweißen Sie es kreisförmig zusammen.
Aus dem zylindrischen Teil der Propanflasche schneiden wir ein 500 mm langes Fragment. Wir zeichnen darauf 5 Linien mit gleichem Abstand voneinander. Wir bohren 10 mm große Löcher 30 mm von den Enden entfernt. Verbinden Sie die Ränder der Löcher und schneiden Sie 5 Streifen aus. Wir platzieren diesen Rost senkrecht entlang des Rohrs, ruhen auf dem unteren und schweißen ihn an das Fass. Dieses Seitengitter schützt die Luftzufuhr beim Befüllen des Feuerraums mit Holz.
Das nächste Teil fertigen wir aus einem 115 mm Rohr mit einer Länge von 90 mm.Wir legen es gegen den Lauf und machen Markierungen darauf, um überschüssiges Metall abzuschneiden. Wir drücken das Teil an den Lauf, schneiden ein Loch im Durchmesser und brühen es kreisförmig aus. Es wird für die Sekundärluftversorgung zur Verbrennung von Pyrolysegasen benötigt.
Aus einem Blech schneiden wir eine Tropfenform mit einem runden Teildurchmesser von 115 mm aus. Mit einer an der Sekundärseite angeschweißten Schraube und Mutter befestigen wir einen „Tropfen“, um die Luftzufuhr zu regulieren. Am Hauptfeuerraum nehmen wir genau die gleichen Luftzufuhreinstellungen vor.
Wir fertigen eine Luke für den Aschekasten, indem wir zunächst ein Muster anfertigen, das der Biegung des Fasses folgt. Mit seiner Hilfe schneiden wir alle Teile der Luke aus einem Blech aus. Wir schweißen sie zusammen und befestigen die Tür am Scharnier. Wir befestigen den T-förmigen Türriegel mit zwei Halterungen an der Luke. Wir schneiden ein Loch für die Luke in den Lauf, probieren es an und schweißen es.
Die Feuerraumluke fertigen wir nach dem gleichen Prinzip wie die Aschenkastenluke. Nur um den Halterungshalter zu sichern, ersetzen wir ihn durch 2 Muttern und nehmen eine größere Schlaufe. Wir schweißen die Luke unter die Versteifungsrippe.
Das nächste Teil fertigen wir aus dem zweiten Lauf, wobei wir das Teil mit einer Drehung abschneiden, da es stark verbeult ist. Dann schneiden wir einen 50 mm breiten Ring und schneiden ihn ab. Dieser dient als Rand am ersten Fass, sodass der Deckel an seine Stelle treten kann. Dazu den Ring um 20 mm nach oben verlängern und verschweißen. Wir schneiden den überschüssigen Streifen ab und schweißen auch die Verbindung.
Wir bauen einen Schornstein aus einem 115-mm-Rohr. Schneiden Sie zunächst ein Stück von 260 mm im 45-Grad-Winkel ab. Aus dem Restrohr mit vorgefertigtem 45-Grad-Winkel schneiden wir eine Länge von 1430 mm ab und verschweißen es miteinander.
Markieren Sie hingegen auf Höhe des Lochs für die Sekundärluftzufuhr den Landeplatz 50 mm von oben und schneiden Sie ein Loch von 115 mm. Nach der Montage montieren und verschweißen wir den Schornstein.
Wir setzen den Deckel mit der Stoßstange auf und der Herd ist fast betriebsbereit.Für eine bessere Wärmeabfuhr von der Oberfläche fertigen wir jedoch einen Konvektionsmantel aus 60-mm-Rohren, nachdem wir zuvor das Fass und den Schornstein gereinigt haben.
Wir schweißen das erste Leuchtfeuerrohr mit einer Länge von 790 mm und konzentrieren uns dabei auf die Naht des Laufs. Die Schweißpunkte sind die Versteifungen und der untere Rand. Zusätzlich zu den Topflappen für den Feuerraum befestigen wir auch die folgenden Rohre miteinander.
Richten Sie zunächst den dreibeinigen Ständer aus, indem Sie die Länge der Schrauben anpassen und die Sicherungsmuttern festziehen. Wir stellen den Ofen an seinen Platz auf dem Ständer. Wir platzieren ein Ventil am Schornstein. Wir laden Brennholz vertikal entlang der Oberkante des Seitengitters, jedoch unterhalb der Stoßstange.
Wir testen den Ofen bei einer Außentemperatur und in der teilweise isolierten Garage von 7 Grad Celsius. Brennstoff ist nicht vollständig getrocknetes Brennholz aus Ahorn und Kiefernholz. Nach dem Anzünden stieg die Temperatur in der Garage auf 27 Grad, obwohl sich der Ofen weiterhin mit einer Geschwindigkeit von 1 Grad pro 5 Sekunden aufheizte. Einen Tag später betrug die Temperatur in der Garage 17 Grad Celsius.
Schau das Video
Ähnliche Meisterkurse
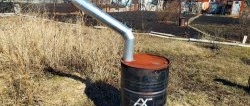
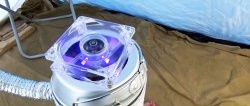
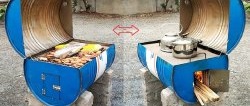
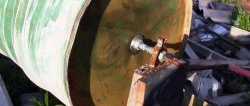
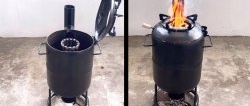
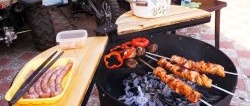