Voller Kompressor aus einem Kühlschrank
In letzter Zeit erfreuen sich Kompressoren bei Bastlern zunehmender Beliebtheit. Sie basieren auf nahezu jedem Motor und berechnen die Leistung der Basiseinheit in Abhängigkeit von der Anzahl der Verbraucher. Für Heimwerkstätten sind selbstgebaute Kompressoreinheiten gefragt.
Kühlschrankkompressoren bleiben oft betriebsbereit, auch wenn der Kühlschrank selbst kaputt geht oder veraltet ist. Sie haben einen geringen Stromverbrauch, sind aber unprätentiös im Betrieb. Und viele Handwerker machen daraus recht anständige hausgemachte Installationen. Mal sehen, wie Sie das selbst machen können.
Benötigte Teile:
Werkzeuge:
Kühlschrankkompressoren bleiben oft betriebsbereit, auch wenn der Kühlschrank selbst kaputt geht oder veraltet ist. Sie haben einen geringen Stromverbrauch, sind aber unprätentiös im Betrieb. Und viele Handwerker machen daraus recht anständige hausgemachte Installationen. Mal sehen, wie Sie das selbst machen können.
Teile und Materialien
Benötigte Teile:
- 11 kg Propantank;
- 1/2"-Kupplung mit Innengewinde und Stopfen;
- Metallplatten, Breite – 3–4 cm, Dicke – 2–4 mm;
- Zwei Räder mit Montageplattform;
- Kältekompressor aus einem Kühlschrank;
- 1/4 Zoll Adapter;
- Rückschlagventilanschluss aus Messing;
- Kupferrohrverbinder ¼ Zoll – 2 Stück;
- Ausrüstung zum Einstellen des Kompressordrucks;
- Bolzen, Schrauben, Muttern, fumlenta.
Werkzeuge:
- Schweißinverter;
- Schraubendreher oder Bohrer;
- Metallschneider mit Titanbeschichtung;
- Eine Turbine oder Bohrmaschine mit Schleifaufsätzen;
- Metallbürste;
- Rolle für Kupferrohre;
- Rollgabelschlüssel, Zangen.[Liste]
Zusammenbau des Kompressors
Schritt eins – Vorbereiten des Empfängers
Wir spülen die leere Flüssigpropanflasche gründlich mit Wasser aus. Es ist sehr wichtig, auf diese Weise alle verbliebenen explosiven Gasgemische zu entfernen.
Wir überlappen den Adapter um 1/4 Zoll in das Endloch des Zylinders. Wir verbrühen es allseitig durch Schweißen und verschließen es mit einer Schraube.
Wir stellen den Empfänger auf Räder und Stützen. Dazu nehmen wir Metallplattenstücke, biegen sie schräg und schweißen sie von unten an die Karosserie an. An den Ecken schweißen wir Räder mit Montageplattform an. Im vorderen Teil des Empfängers montieren wir eine Stützhalterung.Schritt zwei – Installieren Sie den Kompressor
Auf dem Empfänger platzieren wir Montagerahmen für den Kompressor aus Metallplatten. Wir überprüfen ihre Position mit einer Wasserwaage und verbrühen sie. Wir setzen den Kompressor über stoßdämpfende Gummipolster auf die Klemmschrauben. Dieser Kompressortyp verfügt nur über einen Auslass, durch den Luft in den Empfänger gepumpt wird. Die restlichen beiden, die Luft ansaugen, bleiben unangetastet.Schritt drei – Befestigen Sie das Rückschlagventil und den Adapter am Gerät
Wir wählen einen Metallschneider mit passendem Durchmesser aus und bohren mit einem Schraubendreher oder Bohrer ein Loch in das Gehäuse für die Kupplung. Wenn am Kupplungskörper hervorstehende Formen vorhanden sind, schleifen Sie diese mit einer Bohrmaschine ab (Sie können hierfür ein normales elektrisches Schleifpapier oder eine Schleifmaschine mit Schleifscheibe verwenden).
Setzen Sie die Kupplung in das Loch ein und verschweißen Sie sie rundherum. Sein Innengewinde muss mit der Steigung und dem Durchmesser des Befestigungsgewindes am Rückschlagventil übereinstimmen.
Für kleine Kompressoren verwenden wir ein Messing-Rückschlagventil. Den Druckentlastungsausgang verschließen wir mit einem passenden Bolzen, da die Steuerbaugruppe bereits über ein Entlastungsventil verfügt.
Zum Einbau eines Druckschalters bzw. Druckschalters mit sämtlicher Steuerausrüstung montieren wir einen weiteren 1/4-Zoll-Adapter. Wir machen dafür ein Loch in der Mitte des Empfängers, nicht weit vom Kompressor entfernt.
Wir ziehen das Rückschlagventil mit einem 1/2-Zoll-Adapter fest.
Wir verbinden den Ausgang des Kompressorzylinders und das Rückschlagventil mit einem Kupferrohr. Dazu erweitern wir die Enden der Kupferrohre mit einem Spezialwerkzeug und verbinden sie mit Messing-Gewindeadaptern. Wir ziehen die Verbindung mit verstellbaren Schraubenschlüsseln fest.Schritt vier – Installieren Sie die Steuerausrüstung
Die Steuereinheit besteht aus einem Druckschalter (Pressostat) mit Steuersensor, einem Sicherheitsventil oder Überdruckventil, einer Adapterkupplung mit Außengewinde und mehreren Hähnen und Manometern.
Zunächst installieren wir den Druckschalter. Es muss leicht auf das Niveau des Kompressors angehoben werden. Wir verwenden eine Verlängerungskupplung mit Außengewinde und schrauben das Relais durch das Dichtungsband.
Durch den Adapter installieren wir einen Druckregulierungssensor mit Manometern. Wir vervollständigen die Montage mit einem Überdruckventil und zwei Hähnen für die Schlauchabgänge.Schritt fünf – Elektrik anschließen
Mit einem Schraubendreher zerlegen wir das Gehäuse des Druckschalters und öffnen so den Zugang zu den Kontakten. Wir schließen das 3-adrige Kabel an die Kontaktgruppe an und verteilen die einzelnen Adern gemäß Anschlussplan (inkl. Erdung).
Ebenso schließen wir das Netzkabel an, das mit einem Stecker für eine Steckdose ausgestattet ist. Schrauben Sie die Relaisabdeckung wieder fest.Schritt sechs – Überarbeitung und Testlauf
Zum Tragen der Kompressoreinheit befestigen wir einen speziellen Griff am Kompressorrahmen. Wir stellen es aus Resten von quadratischen und runden Profilrohren her. Wir befestigen es an den Spannschrauben und lackieren es in der Farbe des Kompressors.
Wir schließen die Anlage an ein 220-V-Netz an und prüfen ihre Funktionsfähigkeit. Nach Angaben des Autors benötigt dieser Kompressor 10 Minuten, um einen Druck von 90 psi oder 6 atm zu erreichen. Mithilfe eines Einstellsensors wird außerdem die Aktivierung des Kompressors nach einem Druckabfall anhand einer bestimmten Anzeige auf dem Manometer geregelt. In seinem Fall hat der Autor die Installation so konfiguriert, dass sich der Kompressor ab 60 psi oder 4 atm wieder einschaltet.
Der letzte verbleibende Arbeitsschritt ist ein Ölwechsel. Dies ist ein wichtiger Teil der Wartung solcher Anlagen, da diese über kein Sichtfenster verfügen. Und ohne Öl können solche Maschinen nur kurze Zeit arbeiten.
Wir schrauben die Ablassschraube an der Unterseite des Kompressors ab und lassen den Abfall in eine Flasche ab. Drehen Sie den Kompressor auf die Seite, füllen Sie etwas sauberes Öl ein und schrauben Sie den Stopfen wieder fest. Jetzt ist alles in Ordnung, Sie können unsere Kompressoreinheit nutzen!Abschluss
Kompressorgeräte gelten als stromsparend und praktisch haushaltsüblich. Es ist unwahrscheinlich, dass es die Arbeit mehrerer Druckluftwerkzeuge gleichzeitig bewältigen kann. Es kann aber auch für Geräte mit geringem Stromverbrauch verwendet werden, beispielsweise zum Airbrushen oder Reifenpumpen. Es ist auch eine großartige Möglichkeit, einen nicht mehr benötigten Kühlkompressor wiederzuverwenden und ihm in Ihrer Heimwerkstatt ein zweites Leben zu geben.Schau das Video
Ähnliche Meisterkurse
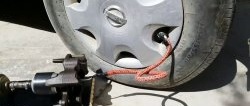
12V-Kompressor vom Kühlschrankkompressor
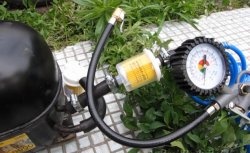
Kühlschrankkompressor zum Aufpumpen von Reifen
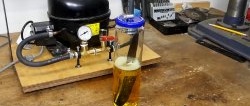
So wandeln Sie einen Kühlschrankkompressor in eine Vakuumpumpe um
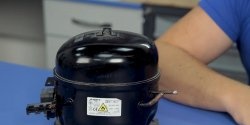
Kolbenkompressoren für Kühlschränke – Typen und Funktionsprinzipien
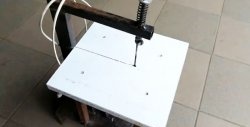
Stichsäge von einem Kompressor aus einem Kühlschrank
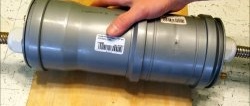
So bauen Sie einen einfachen Kühlschrank für eine Brennerei zusammen
Besonders interessant
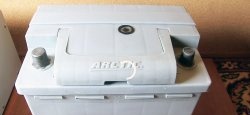
Der effektivste Weg, Ihre Batterie wiederherzustellen
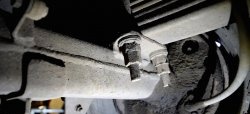
Das stärkste Kriechschmiermittel
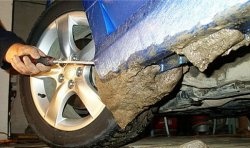
Eine einfache Möglichkeit, an den Kotflügelverkleidungen haftenden Schmutz zu entfernen
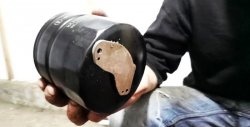
Lohnt es sich, einen Magneten am Ölfilter anzubringen?
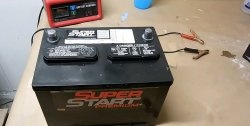
So restaurieren Sie eine Autobatterie mit Backpulver
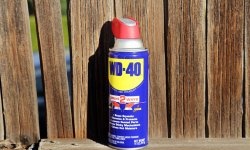
Ungewöhnliche Verwendungen von WD-40
Kommentare (11)