Homemade super bright mini LED flashlight 3 W
LEDs Today they are built into everything - into toys, lighters, household appliances and even stationery. But the most useful invention with them is, of course, a flashlight. Most of them are autonomous and produce a powerful glow from small batteries. You won’t get lost in the dark with it, and when working in a dimly lit room, this tool is simply irreplaceable.
Small copies of a wide variety of LED flashlights can be bought in almost any store. They are inexpensive, but the build quality can sometimes be disappointing. Or maybe it’s homemade devices that can be made using the simplest parts. It is interesting, educational and has a developing effect on those who love to make things.
Today we will look at another homemade product - an LED flashlight, made literally from scrap parts. Their cost is no more than a few dollars, and the efficiency of the device is higher than that of many factory models. Interesting? Then do it with us.
This time Light-emitting diode connected to the battery only through a 3 ohm resistor.Since it contains a ready source of energy, it does not require a storage thyristor and transistor to distribute the voltage, as is the case with the Faraday Eternal Flashlight. An electronic charging module is used to charge the battery. A tiny micromodule provides protection against voltage surges and prevents the battery from overcharging. The device is charged from a USB connector, and on the module itself there is a micro USB connector.
The tools you will need are: a soldering iron with flux, a glue gun, a drill, a lighter and a painting knife.
We take a plastic cap with lenses and mark the circumference of the radiator. It is needed for cooling LED. We mark the mounting grooves and holes on the aluminum plate and cut out the radiator according to the markings. This can be done, for example, using a drill.
We take out the magnifying lenses for a while, they won’t be needed now. Glue the radiator plate onto the back of the cap with superglue. The holes and grooves in the cap and radiator must match.
Contacts LED Tin and solder with copper wiring. We protect the contacts with heat-shrinkable casings and warm them up with a lighter. Insert from the front side of the cap Light-emitting diode with wiring.
We unlock the piston with the handle of the syringe; we will no longer need them.We cut the needle cone with a painting knife.
We completely clean the end of the syringe, making holes in it for the LED contacts of the flashlight.
We attach the lantern cap to the end surface of the syringe using any suitable glue, for example, epoxy resin or liquid nails. Don’t forget to place the LED contacts inside the syringe.
We attach terminals with contacts to the lithium battery and insert it into the syringe body. We tighten the copper contacts to clamp them with the battery body.
The syringe has only a few centimeters of free space, which is not enough for the charging module. Therefore, it will have to be divided into two parts.
We run a paint knife in the middle of the module board and break it along the cut line. Using double tape we connect both halves of the board together.
We tin the open contacts of the module and solder them with copper wiring.
We solder a resistor to the module board and connect it to the micro-button, insulating the contacts with heat shrink.
We solder the remaining three contacts to the module according to its connection diagram. We connect the micro button last, checking the operation of the LED.
We place the electronic content of our device in the body of the syringe so that the micro USB connector and micro button remain on the surface. We insulate the rest of the space with hot glue. We install the LED lenses back into their place on the front side of the cap.
We put the battery on charge, and after a while the LED on the charging module will let you know that our flashlight can already be used. By the way, according to the author, such a flashlight can work for about 10 hours on one charge!
Small copies of a wide variety of LED flashlights can be bought in almost any store. They are inexpensive, but the build quality can sometimes be disappointing. Or maybe it’s homemade devices that can be made using the simplest parts. It is interesting, educational and has a developing effect on those who love to make things.
Today we will look at another homemade product - an LED flashlight, made literally from scrap parts. Their cost is no more than a few dollars, and the efficiency of the device is higher than that of many factory models. Interesting? Then do it with us.
How the device works
This time Light-emitting diode connected to the battery only through a 3 ohm resistor.Since it contains a ready source of energy, it does not require a storage thyristor and transistor to distribute the voltage, as is the case with the Faraday Eternal Flashlight. An electronic charging module is used to charge the battery. A tiny micromodule provides protection against voltage surges and prevents the battery from overcharging. The device is charged from a USB connector, and on the module itself there is a micro USB connector.
Required Parts
- Plastic syringe 20 ml;
- 3.4V/3W LED;
- Lenses for LED flashlight with housing;
- Micro button switch;
- 3 Ohm/0.25 W resistor;
- Micro charging module TP4056;
- A piece of aluminum plate for the radiator;
- Several copper wires;
- 3.7 V battery;
- Superglue, epoxy resin or liquid nails.
The tools you will need are: a soldering iron with flux, a glue gun, a drill, a lighter and a painting knife.
Assembling a powerful LED flashlight
Preparing an LED with lenses
We take a plastic cap with lenses and mark the circumference of the radiator. It is needed for cooling LED. We mark the mounting grooves and holes on the aluminum plate and cut out the radiator according to the markings. This can be done, for example, using a drill.
We take out the magnifying lenses for a while, they won’t be needed now. Glue the radiator plate onto the back of the cap with superglue. The holes and grooves in the cap and radiator must match.
Contacts LED Tin and solder with copper wiring. We protect the contacts with heat-shrinkable casings and warm them up with a lighter. Insert from the front side of the cap Light-emitting diode with wiring.
Processing the flashlight body from a syringe
We unlock the piston with the handle of the syringe; we will no longer need them.We cut the needle cone with a painting knife.
We completely clean the end of the syringe, making holes in it for the LED contacts of the flashlight.
We attach the lantern cap to the end surface of the syringe using any suitable glue, for example, epoxy resin or liquid nails. Don’t forget to place the LED contacts inside the syringe.
Connecting the charging micromodule and battery
We attach terminals with contacts to the lithium battery and insert it into the syringe body. We tighten the copper contacts to clamp them with the battery body.
The syringe has only a few centimeters of free space, which is not enough for the charging module. Therefore, it will have to be divided into two parts.
We run a paint knife in the middle of the module board and break it along the cut line. Using double tape we connect both halves of the board together.
We tin the open contacts of the module and solder them with copper wiring.
Final assembly of the flashlight
We solder a resistor to the module board and connect it to the micro-button, insulating the contacts with heat shrink.
We solder the remaining three contacts to the module according to its connection diagram. We connect the micro button last, checking the operation of the LED.
We place the electronic content of our device in the body of the syringe so that the micro USB connector and micro button remain on the surface. We insulate the rest of the space with hot glue. We install the LED lenses back into their place on the front side of the cap.
We put the battery on charge, and after a while the LED on the charging module will let you know that our flashlight can already be used. By the way, according to the author, such a flashlight can work for about 10 hours on one charge!
Watch the video
Similar master classes
Particularly interesting
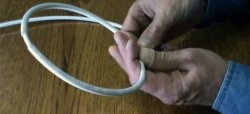
Cable antenna for digital TV in 5 minutes
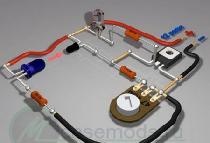
A selection of simple and effective schemes.
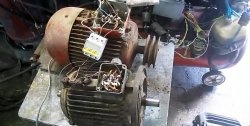
Three-phase voltage from single-phase in 5 minutes
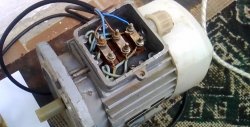
Starting a three-phase motor from a single-phase network without a capacitor
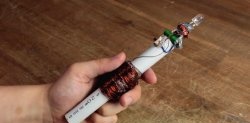
Eternal flashlight without batteries
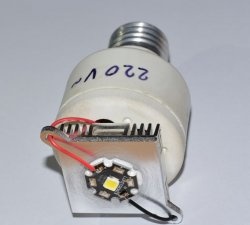
How to make an inexpensive but very powerful LED lamp
Comments (4)