How to make a hole of any shape and size in glass
An interesting topic caught my eye and I wanted to share it. Regarding making holes, the first thing that comes to mind is drilling, a common and trivial manufacturing operation that many perform every day without even thinking about it. But it's not that simple. After all, we are talking about holes on GLASS, and not only round ones, but also arbitrary shapes, and even different sizes. Intrigued? Then let's see how and with what this can be done.
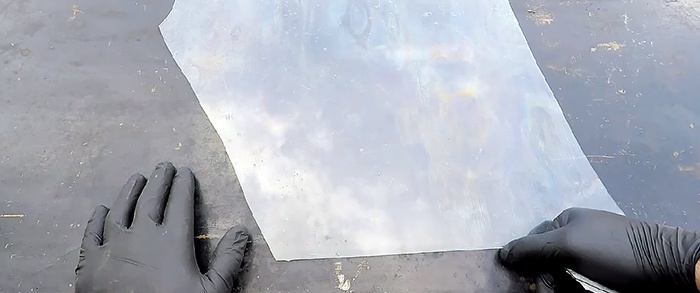
A tool for such work, namely a sandblasting machine. This equipment is mainly used for cleaning metal from rust, slag or old coating.
A primitive homemade installation consists of a compressor, a container with a powder mixture and a hose with a metal nozzle directly for supplying the powder to the surface to be treated.
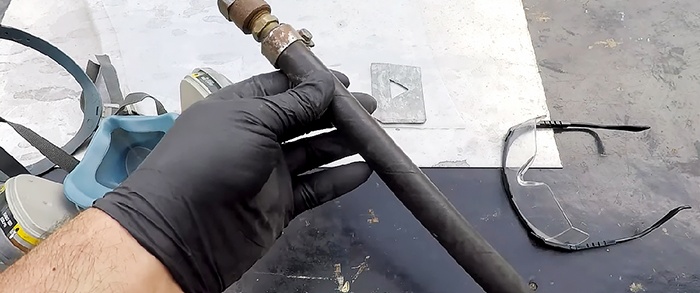
It is better to choose a work table for such processing that is metal or covered with sheet metal.
The process of drilling glass by sandblasting involves treating a given area with an installation nozzle at a distance that is sufficient to remove excess material. It is determined experimentally.
But to form a treated area on the glass, it is necessary to make a template from a material that will withstand this treatment. And sheet steel is perfect for it.
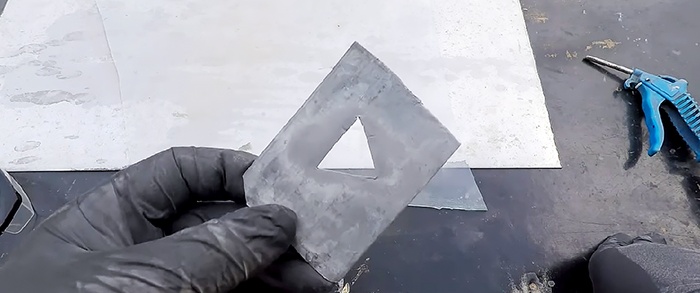
By cutting out any contour in it, regardless of the size of the angles and the smoothness of the lines/transitions, you can easily and quickly repeat it on glass. This trick cannot be repeated with any glass cutter!
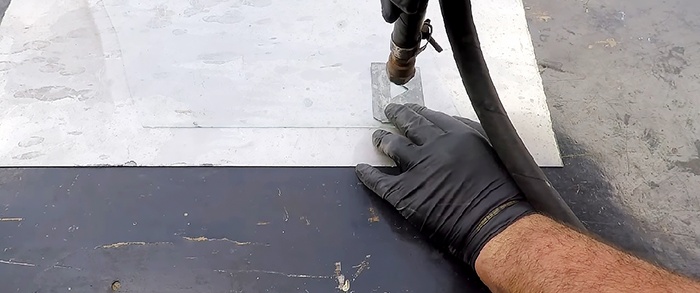
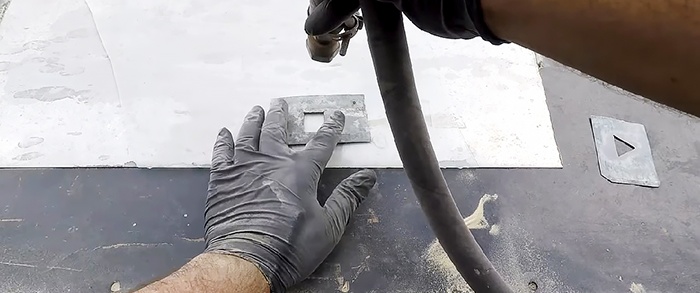
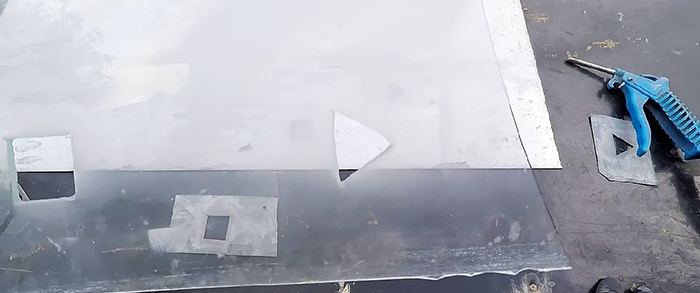
By the way, with this method you can get not only the internal contour, but also the external one, and even try to trim or smooth the edges of the resulting figure. To do this, just cover the proposed element with masking tape, and then cut out its outline directly on the glass with a knife. Fine sand will not be touched by tape, but glass will easily be cut. The edges of the contour are easily trimmed by hand.
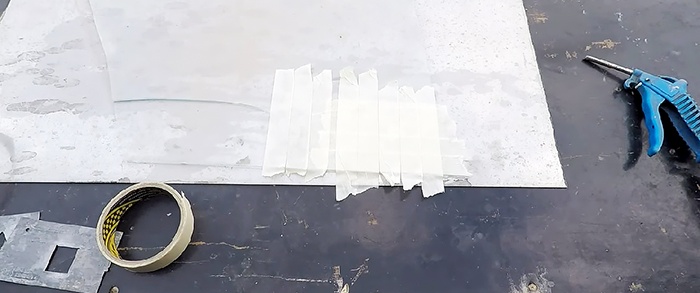
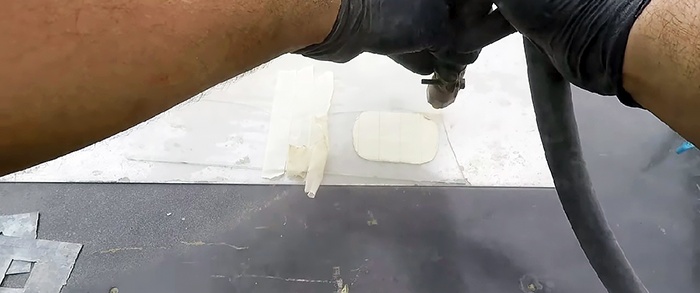
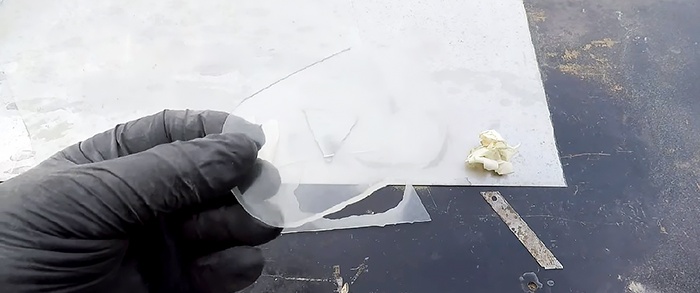
The more accurately the outline of the future hole is cut out on the template, the clearer the sandblasting machine on the glass will make it.
The nozzle sizes differ for different sandblasters. The standard outlet diameter is 3 mm. The larger it is, the more difficult it will be to maintain the clarity of the contour of the selected area on the glass workpiece.
Don't forget about safety precautions too. Dust from sandblasting glass can cause great harm to the mucous membranes of the lungs, eyes, and even damage the skin. In large industries, people work with such equipment in protective overalls. At home, it is necessary to provide ventilation at the work site, and be sure to use safety glasses, a respirator, gloves and protective clothing.
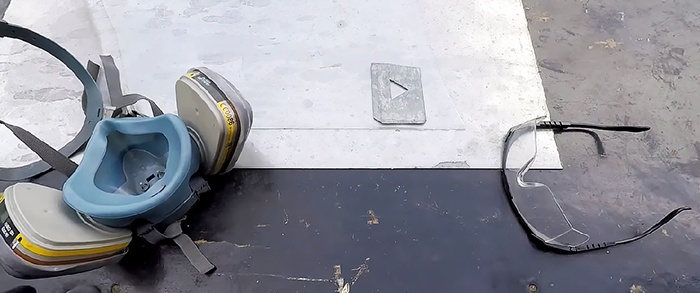
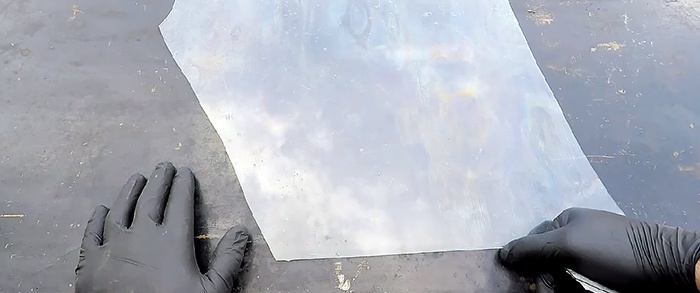
A tool for such work, namely a sandblasting machine. This equipment is mainly used for cleaning metal from rust, slag or old coating.
A primitive homemade installation consists of a compressor, a container with a powder mixture and a hose with a metal nozzle directly for supplying the powder to the surface to be treated.
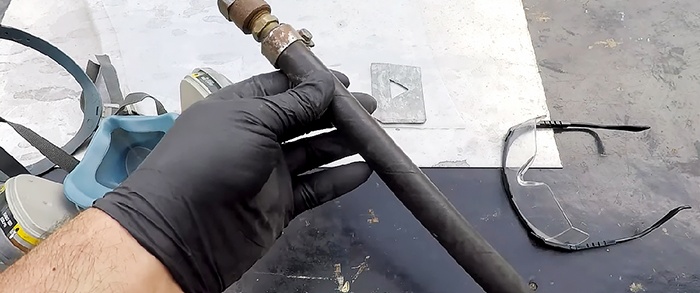
It is better to choose a work table for such processing that is metal or covered with sheet metal.
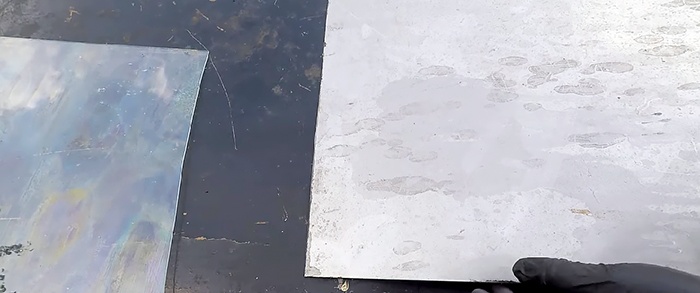
Sandblasting technology for making holes on glass
The process of drilling glass by sandblasting involves treating a given area with an installation nozzle at a distance that is sufficient to remove excess material. It is determined experimentally.
But to form a treated area on the glass, it is necessary to make a template from a material that will withstand this treatment. And sheet steel is perfect for it.
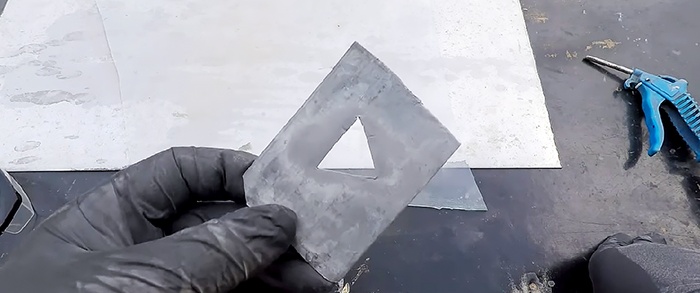
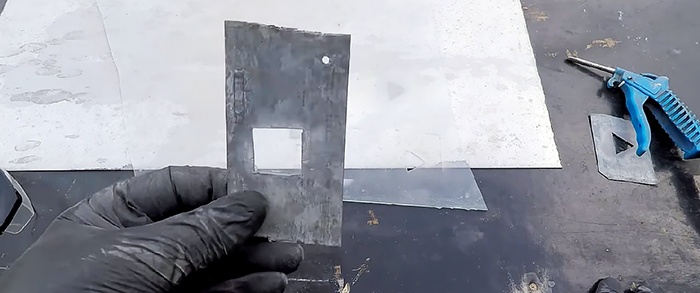
By cutting out any contour in it, regardless of the size of the angles and the smoothness of the lines/transitions, you can easily and quickly repeat it on glass. This trick cannot be repeated with any glass cutter!
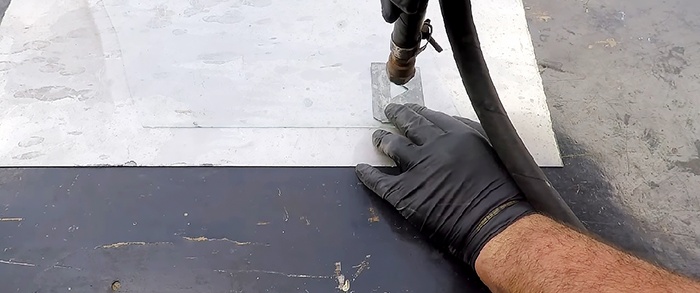
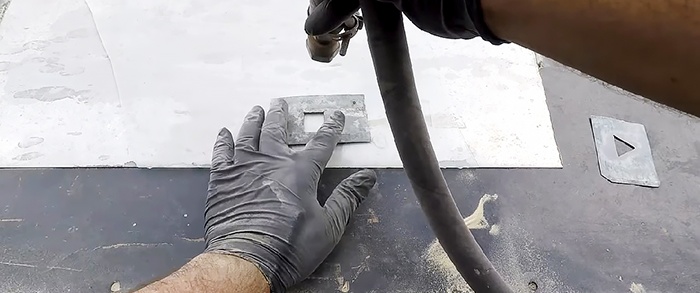
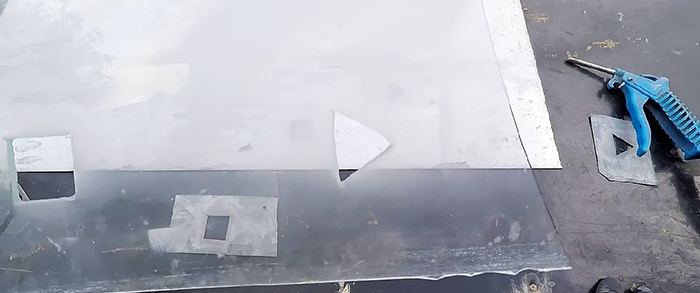
By the way, with this method you can get not only the internal contour, but also the external one, and even try to trim or smooth the edges of the resulting figure. To do this, just cover the proposed element with masking tape, and then cut out its outline directly on the glass with a knife. Fine sand will not be touched by tape, but glass will easily be cut. The edges of the contour are easily trimmed by hand.
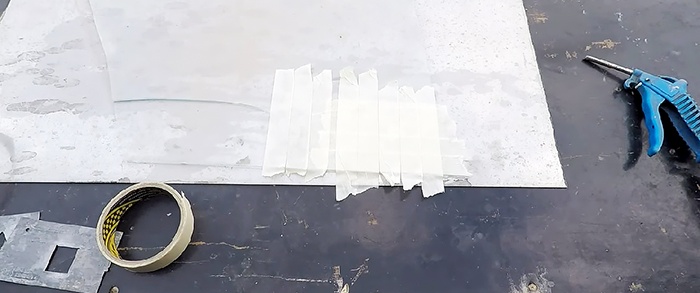
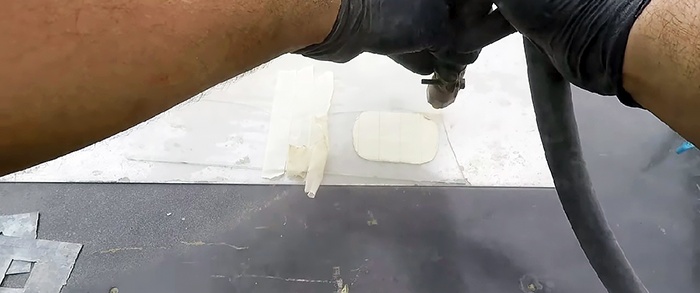
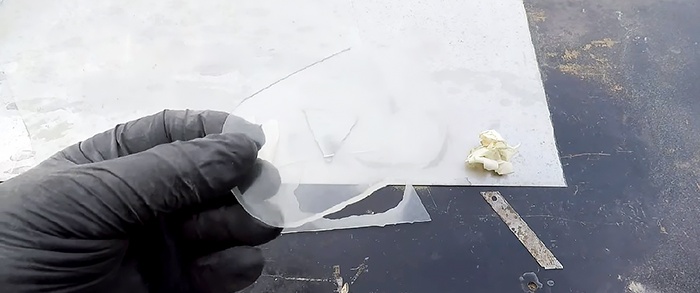
Practical advice
The more accurately the outline of the future hole is cut out on the template, the clearer the sandblasting machine on the glass will make it.
The nozzle sizes differ for different sandblasters. The standard outlet diameter is 3 mm. The larger it is, the more difficult it will be to maintain the clarity of the contour of the selected area on the glass workpiece.
Don't forget about safety precautions too. Dust from sandblasting glass can cause great harm to the mucous membranes of the lungs, eyes, and even damage the skin. In large industries, people work with such equipment in protective overalls. At home, it is necessary to provide ventilation at the work site, and be sure to use safety glasses, a respirator, gloves and protective clothing.
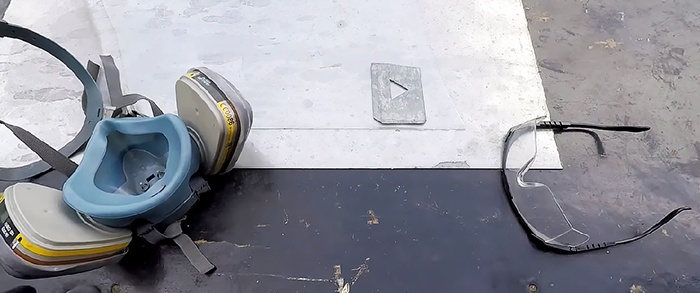
Watch the video
Similar master classes
Particularly interesting
Comments (1)