How to lengthen a short electric motor shaft without welding and lathes
On the back side of most electric motors the shaft is cut off, but there are situations when it is needed. In this case, it can be increased. This is done in an accessible way that does not involve welding or using a lathe. Everything can be done at home, and the result will be more than acceptable with minimal runout.
What you will need:
- threaded rod;
- extended nut for stud;
- epoxy resin.
The process of increasing the electric motor shaft
To extend, you need to drill a hole in the shaft to cut a thread and screw in a stud. You need to drill with the engine turned on, the drill is placed simply for convenience, clamped into the drill, its rotation is not required. For drilling to succeed, the shaft must rotate in the direction of the turns of the drill. If it spins in the opposite direction, then you need to temporarily reverse the polarity of the motor connection to change the direction.
After drilling, the chips are cleared from the hole, and a thread is cut into it for the pin.The tap is held motionless; you need to rotate the shaft by the pulley on the back of the motor. After cutting, the thread is degreased.
A pin coated with epoxy glue is screwed into the shaft.
An elongated nut is screwed onto it until it stops, also applying resin to the threads.
After the epoxy has set, the excess length of the shaft is cut off. Next, you need to start the engine and grind off the edges on the extended nut with a grinder and a grinding wheel. After this, you can install a pulley, disk or flange on the new shaft, and then tighten the equipment with a nut.
If a shaft with a hole for a bolt is required, then a short stud is initially used. It should only reach the middle of the extended nut.
Watch the video
Similar master classes
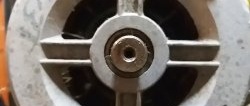
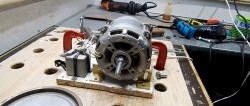
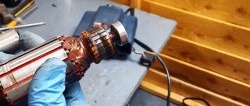
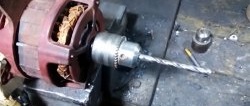
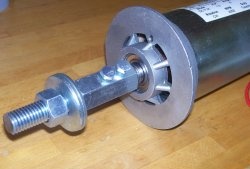
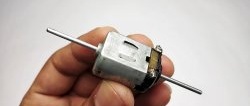