How to remove a press-on pulley from an electric motor and install a drill chuck
Even if you have the meager set of simple tools, with some persistence you can remove the pulley pressed onto the electric motor shaft and replace it with a drill chuck. The result is a tool similar to a drill press or drill.
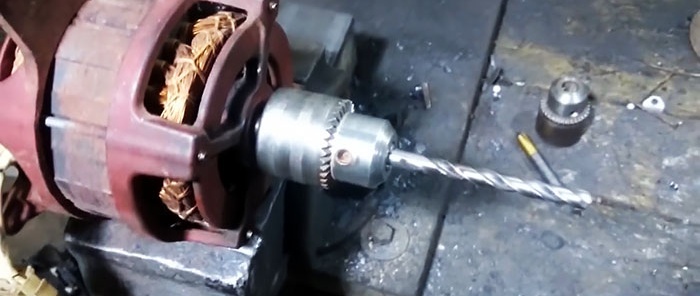
To implement our plans, we still cannot do without the following tools and devices:
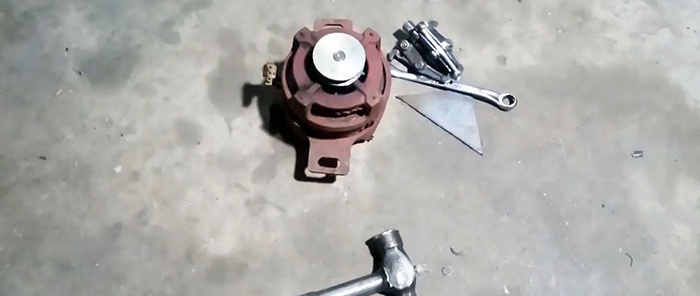
Usually, using one puller, it is not possible to remove a pressed pulley from the electric motor shaft. You can't do without preparatory work. It wouldn't hurt, for example, to add a few drops of liquid oil to the joint area.
Then try to move the pulley from its place. To do this, we rest the second end of the shaft against a round anvil, and around the end of the shaft we place a ring on the pulley, which we hit with a hammer using an attachment.
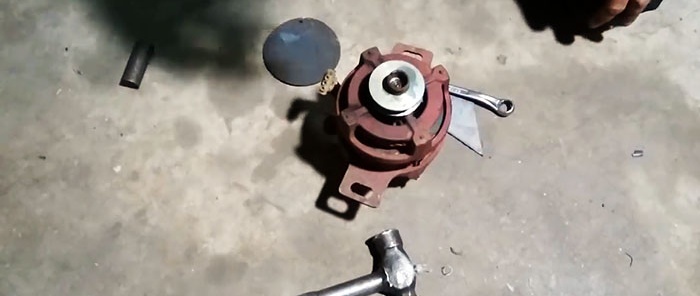
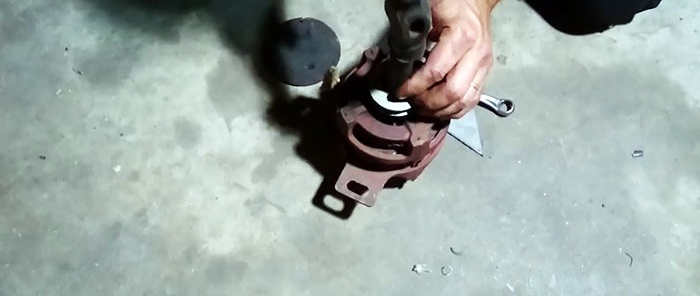
If we manage to move the pulley along the shaft, even just a little, this will make it much easier to remove it using a puller. But you won’t be able to do this by holding everything in your hands.
We clamp the motor housing in a vice and try to thermally influence the press fit using an electric arc discharge, lighting it on the pulley in a circle.
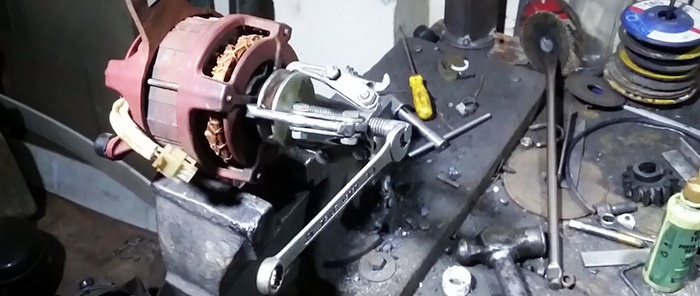
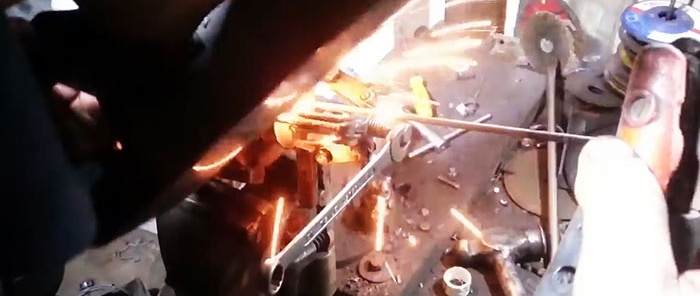
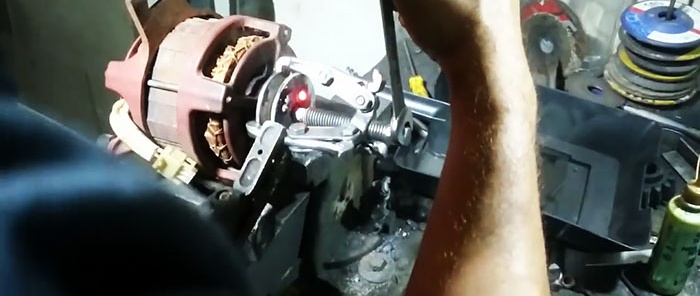
After this, use a screwdriver to lock the puller’s grips relative to the engine housing and begin to rotate the screw with a wrench. It is very important, as they say, to tear the pulley out of place. When this succeeds, things will go easier.

After removing the pulley from the shaft, it is clear that the pressing was carried out along shallow triangular splines, which strengthened the fastening of the mating parts.
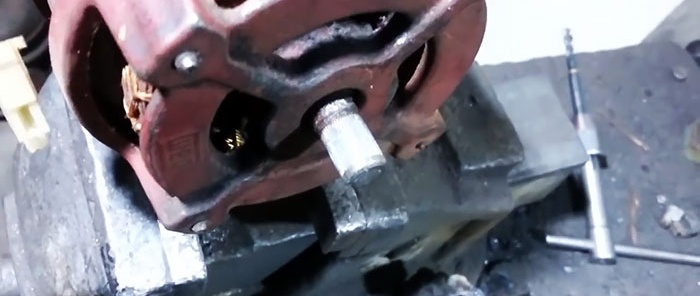
It cannot be fitted onto a shaft with splines and a larger diameter than the mounting hole of the drill chuck. The end of the shaft needs to be machined. To do this, we disassemble the engine housing and clamp the rotor into the lathe chuck.
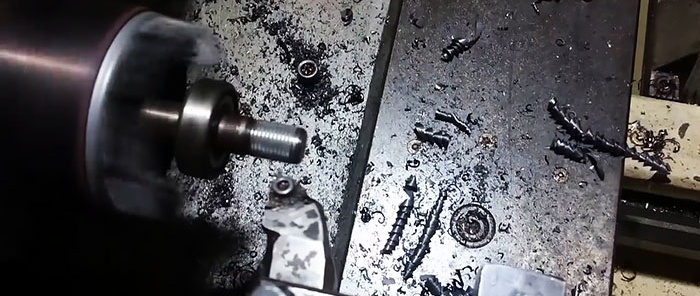
We gradually remove the rotor runout by lightly hitting the end of the shaft with a massive roller. We grind the shaft in several passes, constantly trying on the mounting hole of the drill chuck.
After obtaining the required fit, the rotor, together with the drill chuck mounted on the shaft, is reinstalled into the housing. If you now clamp a drill into the chuck and connect the motor to the mains, then such a tool can be used as a drilling machine or drill.
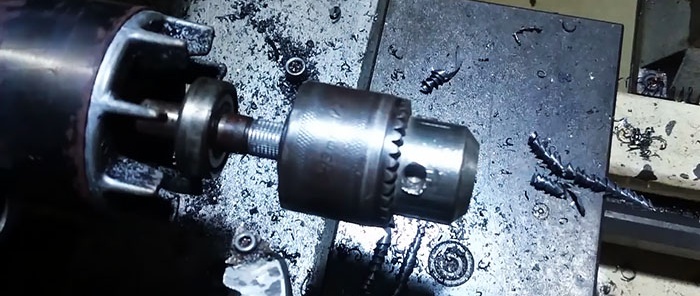
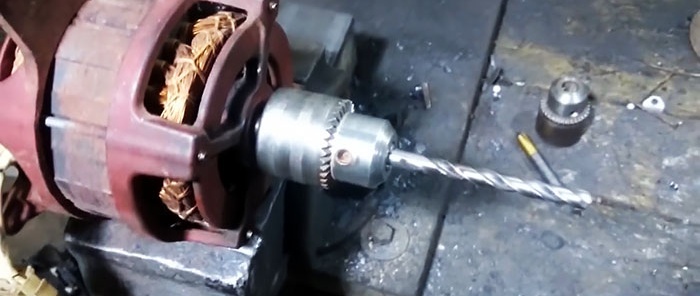
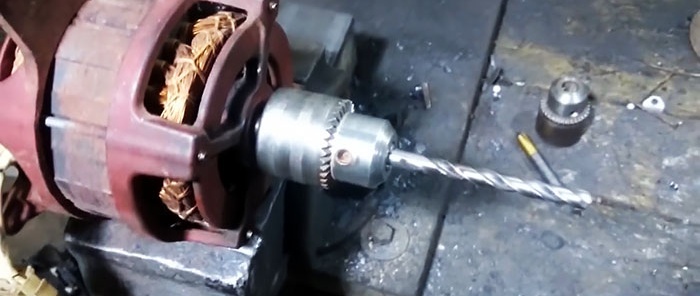
Will need
To implement our plans, we still cannot do without the following tools and devices:
- puller and vice;
- lathe;
- welding machine;
- wrench;
- hammer;
- hand screwdriver;
- anvils, attachments and power bushings.
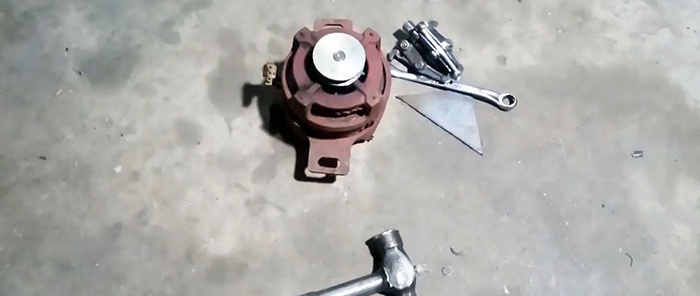
The process of removing the pulley and installing the drill chuck
Usually, using one puller, it is not possible to remove a pressed pulley from the electric motor shaft. You can't do without preparatory work. It wouldn't hurt, for example, to add a few drops of liquid oil to the joint area.
Then try to move the pulley from its place. To do this, we rest the second end of the shaft against a round anvil, and around the end of the shaft we place a ring on the pulley, which we hit with a hammer using an attachment.
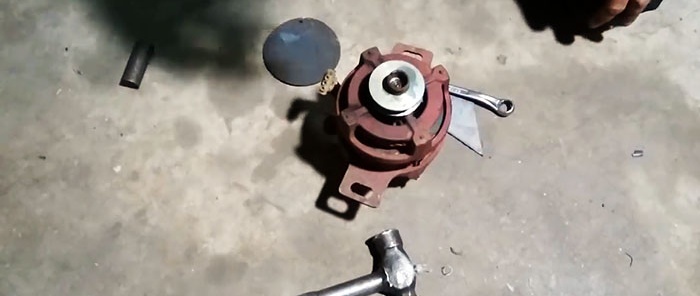
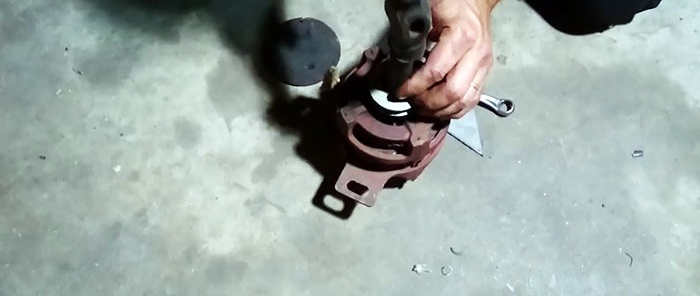
If we manage to move the pulley along the shaft, even just a little, this will make it much easier to remove it using a puller. But you won’t be able to do this by holding everything in your hands.
We clamp the motor housing in a vice and try to thermally influence the press fit using an electric arc discharge, lighting it on the pulley in a circle.
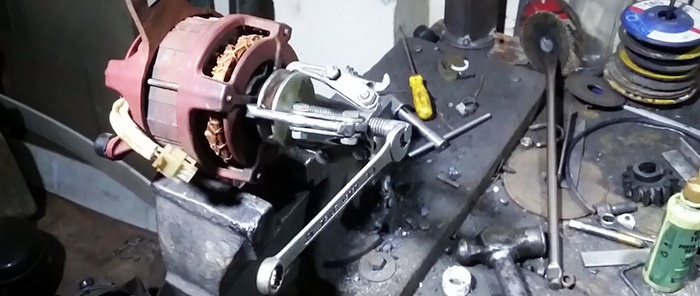
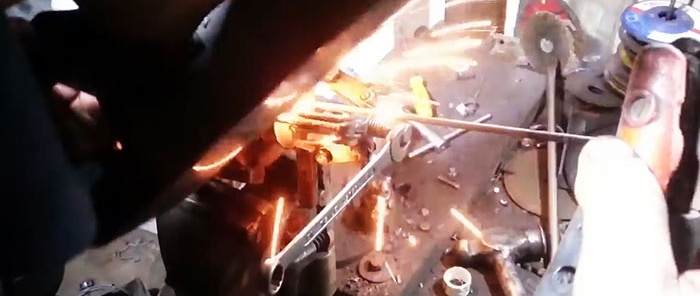
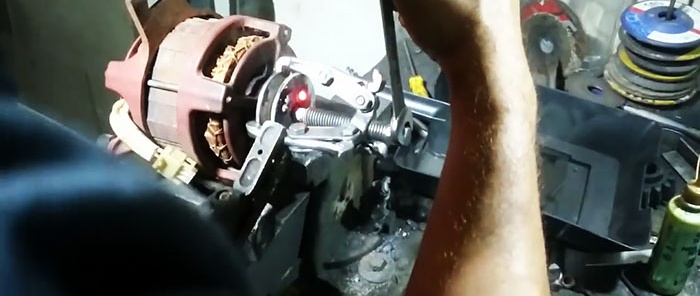
After this, use a screwdriver to lock the puller’s grips relative to the engine housing and begin to rotate the screw with a wrench. It is very important, as they say, to tear the pulley out of place. When this succeeds, things will go easier.

After removing the pulley from the shaft, it is clear that the pressing was carried out along shallow triangular splines, which strengthened the fastening of the mating parts.
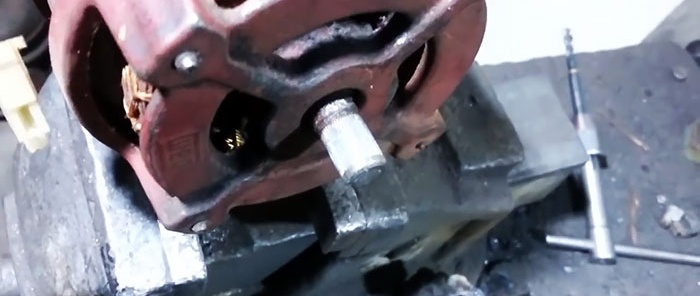
It cannot be fitted onto a shaft with splines and a larger diameter than the mounting hole of the drill chuck. The end of the shaft needs to be machined. To do this, we disassemble the engine housing and clamp the rotor into the lathe chuck.
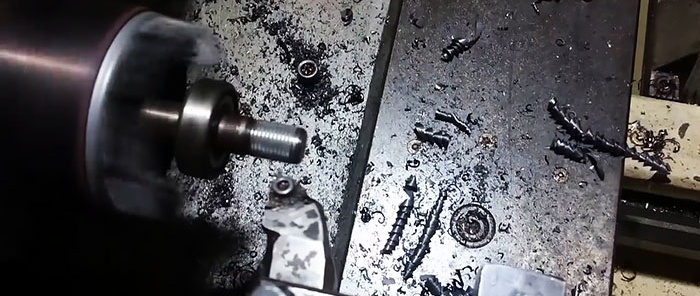
We gradually remove the rotor runout by lightly hitting the end of the shaft with a massive roller. We grind the shaft in several passes, constantly trying on the mounting hole of the drill chuck.
After obtaining the required fit, the rotor, together with the drill chuck mounted on the shaft, is reinstalled into the housing. If you now clamp a drill into the chuck and connect the motor to the mains, then such a tool can be used as a drilling machine or drill.
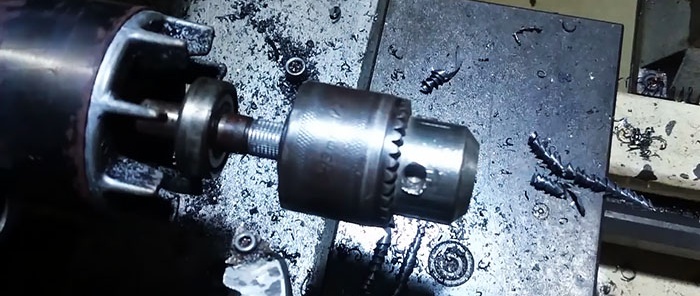
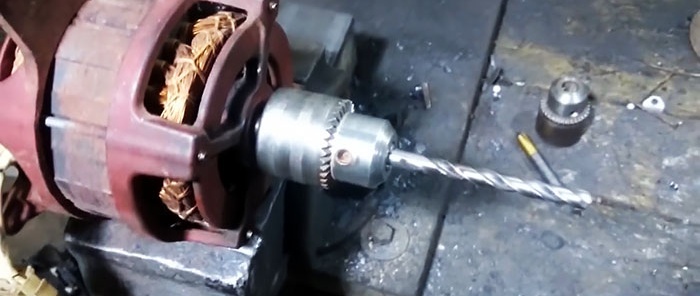
Watch the video
Similar master classes
Particularly interesting
Comments (3)