Cómo convertir un engranaje de distribución en un cortador de madera completo
Todo contribuye a tal metamorfosis: el metal, la proporción de tamaños, la presencia de dientes rectos u oblicuos, etc. En una palabra, un engranaje de distribución de un automóvil de pasajeros puede servir como pieza en bruto ideal para hacer una fresa para madera.
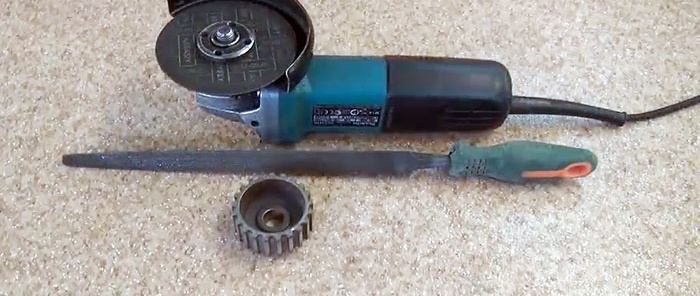
Además del engranaje mencionado, necesitaremos un pequeño trozo de tubo de acero y una conexión atornillada acorde con el tamaño transversal del orificio de montaje del engranaje de distribución.
En nuestro trabajo tendremos que utilizar las siguientes herramientas y equipos:
Para eliminar el descentramiento del engranaje al procesar en un torno, sujetamos un tubo de metal en el mandril y rectificamos su extremo hasta el diámetro del orificio de montaje del engranaje.
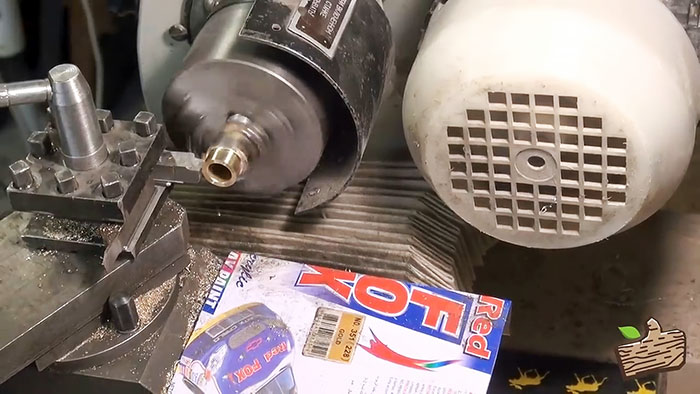
Lo instalamos en el extremo girado del tubo, lo presionamos con el contrapunto y procesamos el extremo de la pieza de trabajo.
Pasemos a la operación más importante: cortar los dientes del engranaje. Para hacer esto, debe fijarse de manera segura en un tornillo de banco, lo cual no es fácil de hacer sin un soporte especial.
No es difícil de hacer. Insertamos un perno de diámetro y longitud adecuados en el orificio de montaje del engranaje, en el otro lado de la pieza de trabajo colocamos una arandela en el perno, luego un casquillo y apretamos el conjunto resultante con una tuerca usando una llave ajustable.
Ahora es posible fijar de forma segura la pieza de trabajo del engranaje al soporte con un tornillo de banco y usar una amoladora para cortar ranuras de la misma profundidad a lo largo de todas las cavidades del engranaje. Ellos determinarán la altura de los dientes y el ángulo de afilado del futuro cortador.
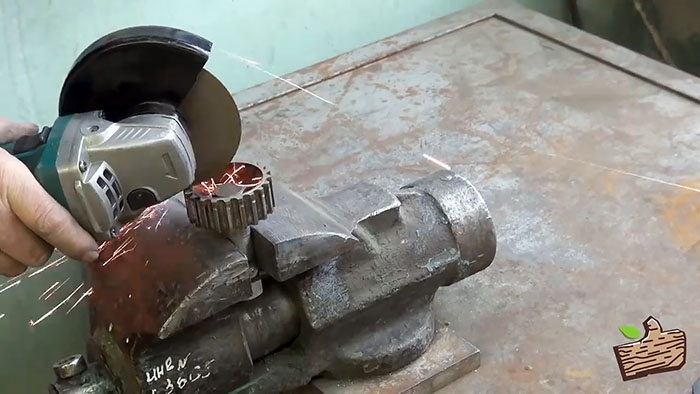
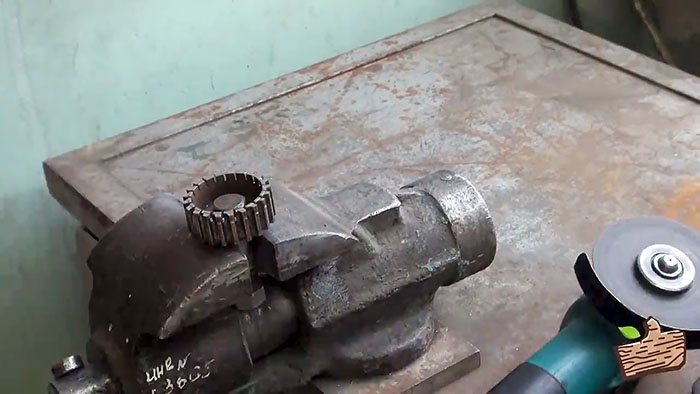
Después de cortar las ranuras en la pieza de trabajo, desmontamos el soporte quitando la tuerca y el casquillo. Sujetamos la varilla del perno en un tornillo de banco para que el engranaje quede de lado y pueda girarse con una llave alrededor del perno ubicado horizontalmente.
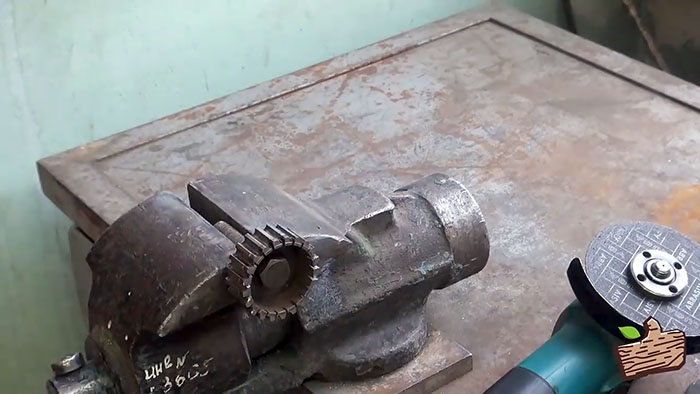
Habiendo establecido el ángulo de afilado calculado, usando una amoladora cortamos los dientes cortantes del futuro cortador en la superficie del extremo del engranaje.
Habiendo colocado el engranaje con el perno plano sobre un tornillo de banco, retiramos las rebabas y le damos a los dientes su forma final, primero con una lima de muesca gruesa y luego con una fina.
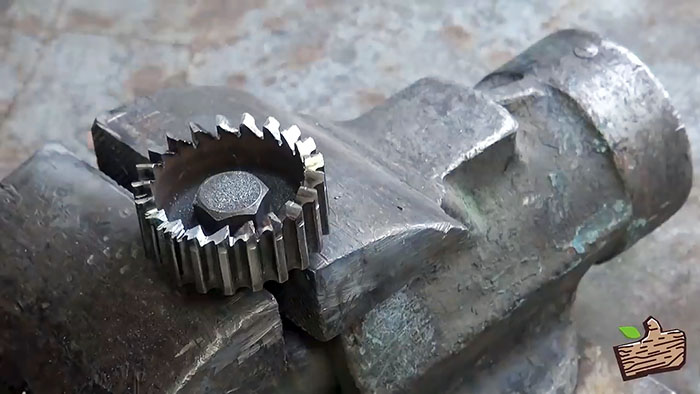
Reinstalamos completamente el soporte en el engranaje de la pieza de trabajo y usamos un cortador de soldadura de gas-acetileno para calentarlo hasta que comience a ponerse rojo, y luego lo bajamos bruscamente a un recipiente con agua.

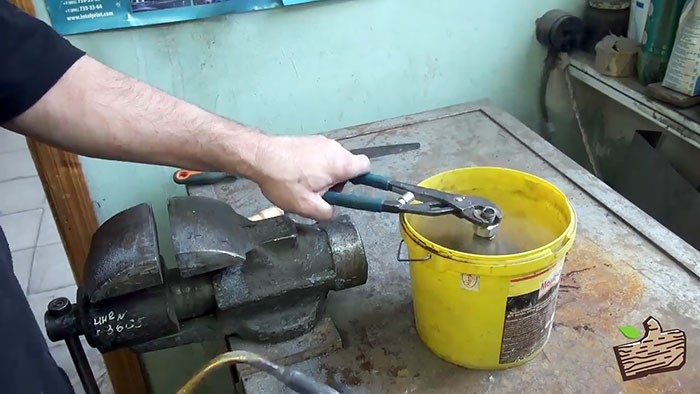
Comprobamos la dureza del endurecimiento y notamos que el metal no está lo suficientemente endurecido, ya que se puede procesar con una lima finamente cortada.
Calentamos la pieza de trabajo nuevamente, pero a una temperatura más alta, y llevamos el metal a un brillo rojo brillante, después de lo cual sumergimos el cortador casi terminado en un recipiente con agua para templarlo.
Rectificamos uno más pequeño del casquillo del soporte para compensar el diámetro del orificio de montaje de nuestro cortador, 16 mm, y el diámetro del husillo de la amoladora angular, 14 mm.
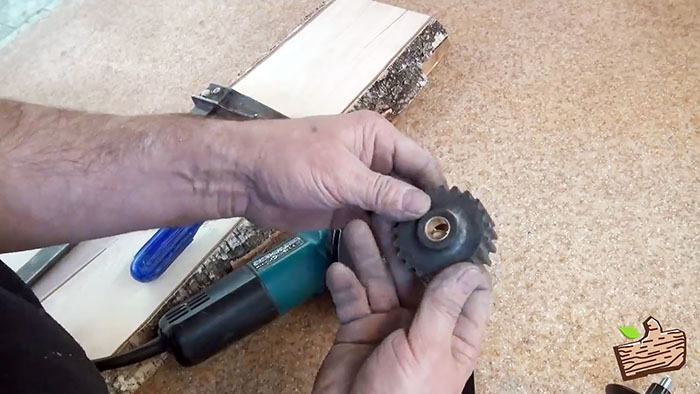
Retiramos el disco de corte del husillo de la amoladora angular, instalamos el manguito adaptador y sobre él un cortador casero hecho con el engranaje de distribución, y aseguramos todo con una tuerca de apriete.
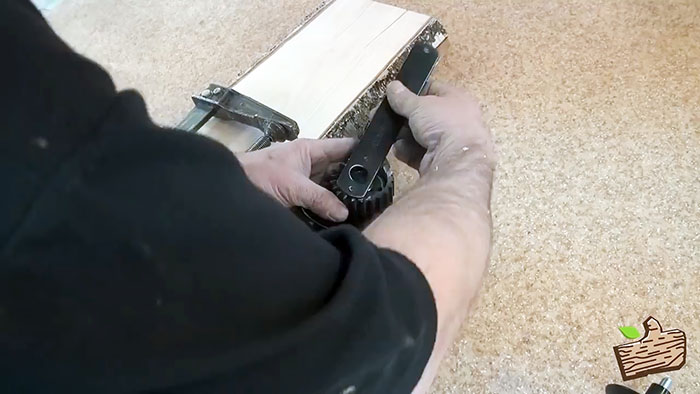
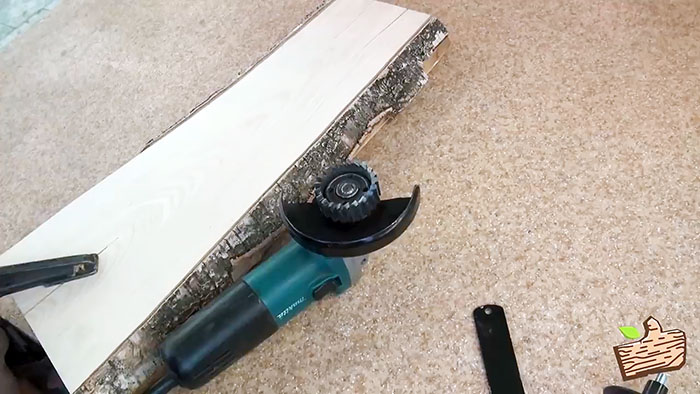
Presionamos de forma segura un trozo de tabla contra la mesa del banco de trabajo con una abrazadera, encendemos la amoladora y la verificamos al ralentí sin carga. La herramienta funciona sin problemas y no se siente ninguna vibración.
Aumentamos la velocidad y comenzamos a fresar la superficie del tablero. Inmediatamente sentimos una carga notable en nuestras manos, lo que indica que se está quitando mucha madera. Para mayor comodidad y seguridad en el trabajo, atornillamos el mango lateral en el cuerpo de la amoladora angular.
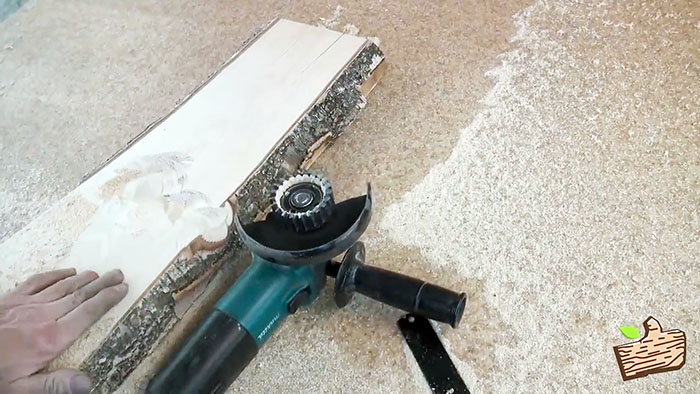
Si el trabajo a realizar es delicado, entonces el ángulo de afilado de los dientes de un cortador casero conviene reducirlo, para aumentar la productividad, por el contrario, conviene hacerlo mayor.
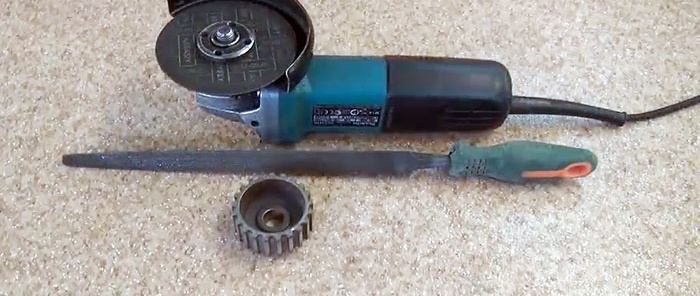
Necesitará
Además del engranaje mencionado, necesitaremos un pequeño trozo de tubo de acero y una conexión atornillada acorde con el tamaño transversal del orificio de montaje del engranaje de distribución.
En nuestro trabajo tendremos que utilizar las siguientes herramientas y equipos:
- torno y amoladora;
- calibrador;
- limas de metal con cortes gruesos y finos;
- tornillo de banco y abrazadera;
- llave ajustable y martillo;
- soldadura de gas-acetileno;
- recipiente con agua.
El procedimiento para hacer un cortador de madera a partir de un engranaje de distribución.
Para eliminar el descentramiento del engranaje al procesar en un torno, sujetamos un tubo de metal en el mandril y rectificamos su extremo hasta el diámetro del orificio de montaje del engranaje.
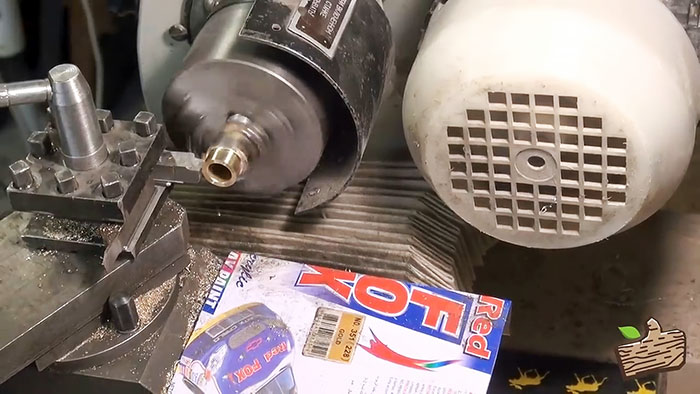
Lo instalamos en el extremo girado del tubo, lo presionamos con el contrapunto y procesamos el extremo de la pieza de trabajo.
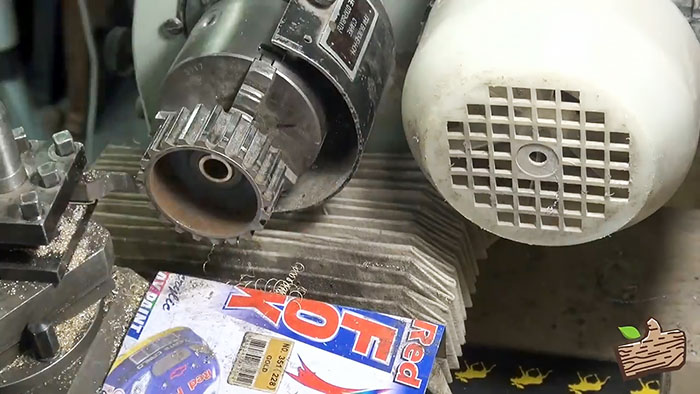
Pasemos a la operación más importante: cortar los dientes del engranaje. Para hacer esto, debe fijarse de manera segura en un tornillo de banco, lo cual no es fácil de hacer sin un soporte especial.
No es difícil de hacer. Insertamos un perno de diámetro y longitud adecuados en el orificio de montaje del engranaje, en el otro lado de la pieza de trabajo colocamos una arandela en el perno, luego un casquillo y apretamos el conjunto resultante con una tuerca usando una llave ajustable.
Ahora es posible fijar de forma segura la pieza de trabajo del engranaje al soporte con un tornillo de banco y usar una amoladora para cortar ranuras de la misma profundidad a lo largo de todas las cavidades del engranaje. Ellos determinarán la altura de los dientes y el ángulo de afilado del futuro cortador.
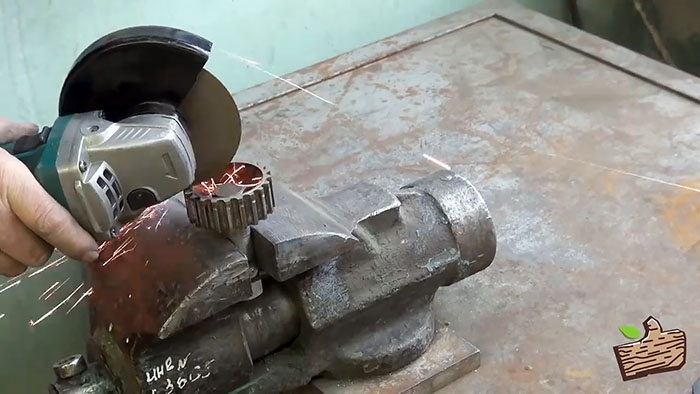
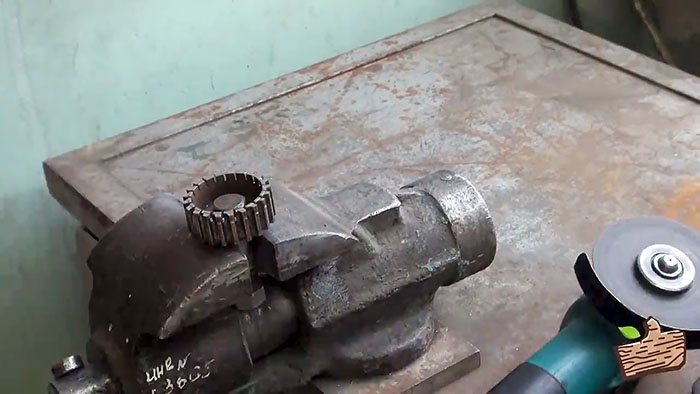
Después de cortar las ranuras en la pieza de trabajo, desmontamos el soporte quitando la tuerca y el casquillo. Sujetamos la varilla del perno en un tornillo de banco para que el engranaje quede de lado y pueda girarse con una llave alrededor del perno ubicado horizontalmente.
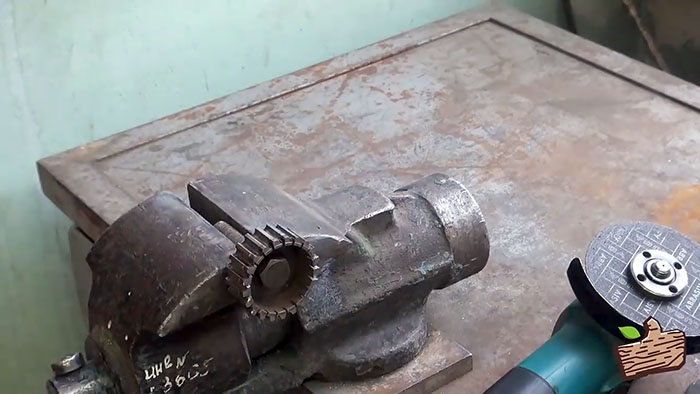
Habiendo establecido el ángulo de afilado calculado, usando una amoladora cortamos los dientes cortantes del futuro cortador en la superficie del extremo del engranaje.
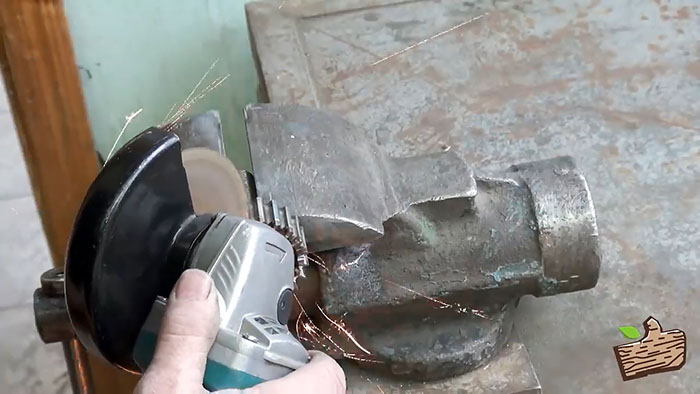
Habiendo colocado el engranaje con el perno plano sobre un tornillo de banco, retiramos las rebabas y le damos a los dientes su forma final, primero con una lima de muesca gruesa y luego con una fina.
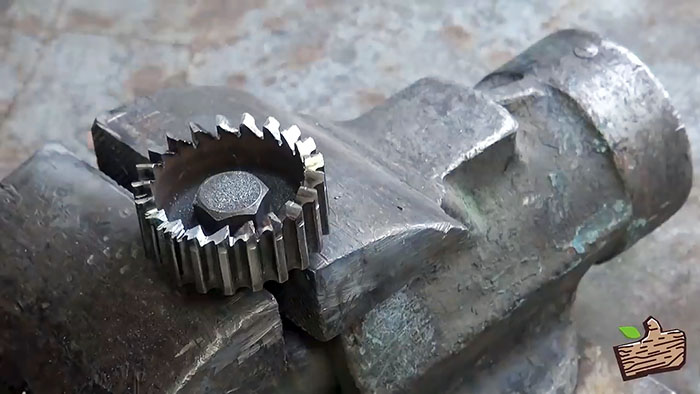
Reinstalamos completamente el soporte en el engranaje de la pieza de trabajo y usamos un cortador de soldadura de gas-acetileno para calentarlo hasta que comience a ponerse rojo, y luego lo bajamos bruscamente a un recipiente con agua.

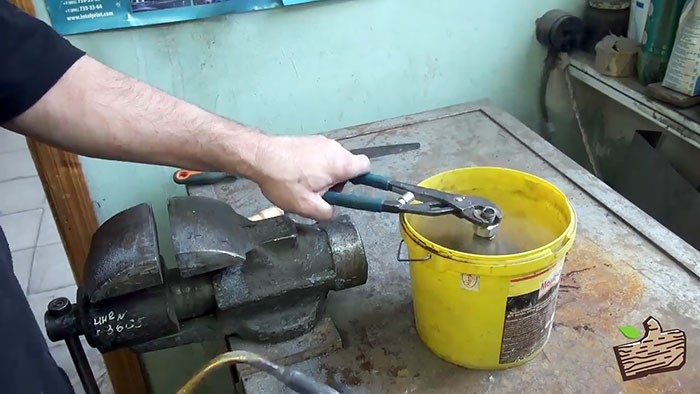
Comprobamos la dureza del endurecimiento y notamos que el metal no está lo suficientemente endurecido, ya que se puede procesar con una lima finamente cortada.
Calentamos la pieza de trabajo nuevamente, pero a una temperatura más alta, y llevamos el metal a un brillo rojo brillante, después de lo cual sumergimos el cortador casi terminado en un recipiente con agua para templarlo.
Rectificamos uno más pequeño del casquillo del soporte para compensar el diámetro del orificio de montaje de nuestro cortador, 16 mm, y el diámetro del husillo de la amoladora angular, 14 mm.
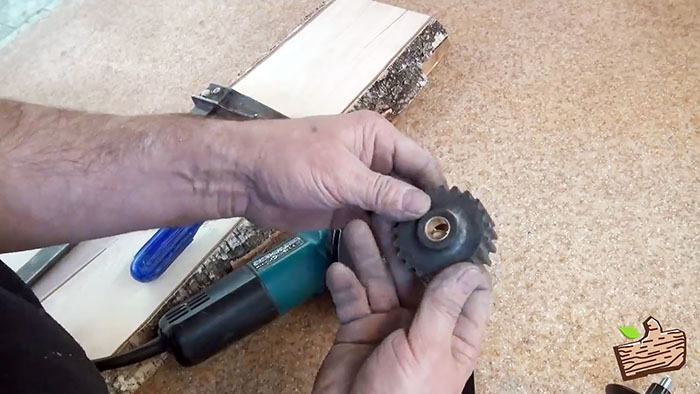
Probando un cortador de madera casero
Retiramos el disco de corte del husillo de la amoladora angular, instalamos el manguito adaptador y sobre él un cortador casero hecho con el engranaje de distribución, y aseguramos todo con una tuerca de apriete.
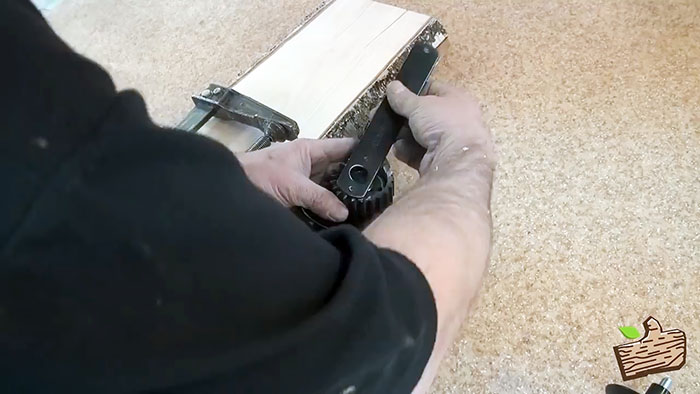
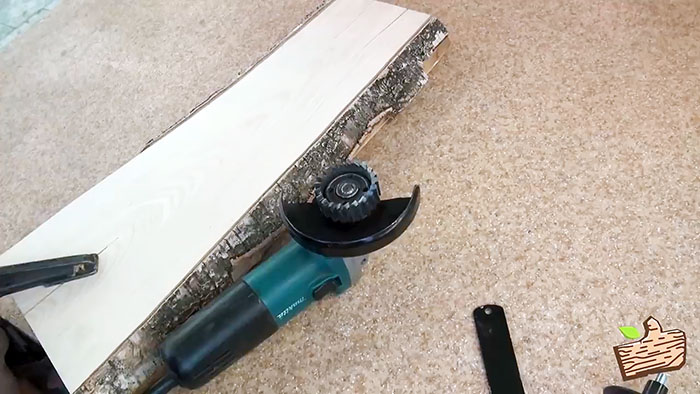
Presionamos de forma segura un trozo de tabla contra la mesa del banco de trabajo con una abrazadera, encendemos la amoladora y la verificamos al ralentí sin carga. La herramienta funciona sin problemas y no se siente ninguna vibración.
Aumentamos la velocidad y comenzamos a fresar la superficie del tablero. Inmediatamente sentimos una carga notable en nuestras manos, lo que indica que se está quitando mucha madera. Para mayor comodidad y seguridad en el trabajo, atornillamos el mango lateral en el cuerpo de la amoladora angular.
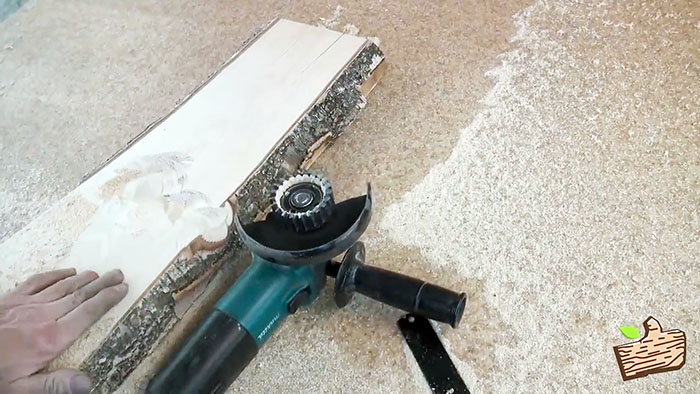
Si el trabajo a realizar es delicado, entonces el ángulo de afilado de los dientes de un cortador casero conviene reducirlo, para aumentar la productividad, por el contrario, conviene hacerlo mayor.
Ver el vídeo
Clases magistrales similares
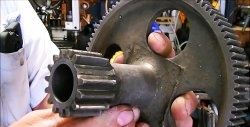
Cómo reparar un diente de engranaje roto
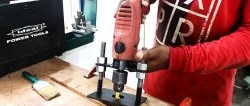
Cómo convertir un taladro en un enrutador usando un equipo simple
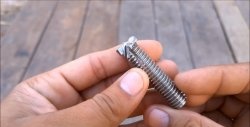
Cortador de madera para agujeros pasantes y ciegos de pernos
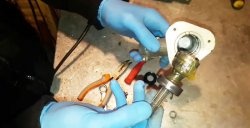
Desmontaje completo de la caja de cambios de la desbrozadora para eliminar los productos de desgaste.
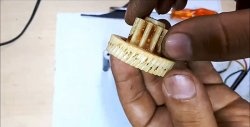
Restauración de dientes de engranajes de plástico mediante moleteado
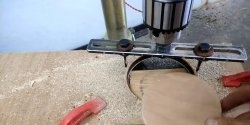
Cortante bailarina regulable para madera
Particularmente interesante
Comentarios (6)