Comment fabriquer un ventilateur radial pour une hotte d'atelier en contreplaqué et un moteur de machine à laver
La purification de l'air dans un atelier de menuiserie ou un petit atelier de transformation de la pierre à l'aide de systèmes d'aspiration industriels nécessite des investissements considérables. Pour une petite installation de production, un garage ou un atelier à domicile, la ventilation peut être réalisée en quelques heures, ce qui coûte quelques dizaines de dollars. Presque tous les matériaux et outils se trouvent sur les étagères de la plupart des menuisiers.
Ce dont tu auras besoin
Pour le projet dont vous avez besoin :- moteur électrique d'une machine à laver : puissance – 600 W avec condensateur, avec vitesse de rotation de l'arbre – 1600 tr/min ;
- quatre feuilles de contreplaqué de dimensions 400×400 mm, épaisseur 19 mm ;
- une paire de feuilles de contreplaqué de dimensions 300×300 mm, épaisseur ~16 mm ;
- contreplaqué de 6 mm d'épaisseur;
- acier laminé de 0,35 mm d'épaisseur et de dimensions 120×1100 mm ;
- plusieurs dizaines de vis à métal ;
- ruban de masquage étroit;
- Boulons M5 ou M6 avec ailes et rondelles.
- meuleuse (meuleuse d'angle) avec une meule en émeri d'une granulométrie de 80 à 100 grains ;
- crayon, règle et compas ;
- cisailles pour couper la tôle;
- perceuse ou tournevis avec forets à métaux et un embout pour vis autotaraudeuses ;
- fraiseuse à bois manuelle, de préférence intégrée à la table ;
- fraise à rainure droite;
- papier abrasif;
- maillet en bois ou en caoutchouc (maillet);
- colle à bois et pinces;
- une scie circulaire.
Le processus de fabrication d'un ventilateur d'extraction à partir des matériaux disponibles
L'arbre du moteur est débarrassé des écrous, poulies, bouchons, brides et autres accessoires. Un cercle d'un diamètre de 250 mm est découpé dans du contreplaqué mesurant 400x400 mm à l'aide d'une défonceuse à bois manuelle à l'aide d'une table de fraisage universelle.
Un trou est pratiqué à l'intérieur d'un diamètre égal au diamètre de la roue du moteur (50 mm).
Un cercle d'un diamètre de 1 à 2 mm plus petit que le trou est découpé dans les chutes afin qu'il s'y adapte librement.
Des trous sont percés pour le montage du moteur électrique, puis percés de quelques millimètres avec une fraise ou une perceuse épaisse pour cacher les têtes de boulons. Le moteur est vissé au contreplaqué.
Un cylindre plus petit d'une hauteur telle est collé au cercle qu'ils recouvrent ensemble l'arbre du moteur.
Un trou est percé à l'intérieur d'un diamètre égal à l'épaisseur de la tige. La structure est soigneusement pressée sur le fût grâce à une entretoise en bois afin de ne pas se fendre ou s'endommager.
Deux "guitares" identiques sont découpées dans les restes de contreplaqué et une deuxième feuille - le futur corps du purificateur d'air.
Deux cercles sont découpés dans de fines feuilles de contreplaqué d'un diamètre légèrement inférieur à celui d'avant - environ 230 mm.
Sur l'une d'elles, des rainures radiales borgnes sont fraisées à l'aide d'une fraise de 6 mm et d'une profondeur de 3 à 5 mm. Dans ce cas, 8 pièces.
Le résultat est une turbine similaire à celle utilisée dans un aspirateur.
À l'aide d'une scie circulaire manuelle ou fixe, des rectangles sont découpés dans du contreplaqué fin.Leur longueur dépasse la longueur des rainures de quelques millimètres, leur largeur est de 58 mm.
Les nervures entre les bords latéraux, avec lesquelles les pièces sont insérées dans les rainures, sont meulées en biais. Ces pentes faciliteront l'installation des pales dans les rainures. Lors du ponçage, vous devez faire attention à ne pas mettre les doigts sous le papier de verre. Les rainures sont lubrifiées avec de la colle à bois et toutes les pièces y sont enfoncées.
Le deuxième cercle est placé coaxialement avec celui du bas et la structure est pressée avec un poids pour le collage.
Après séchage, une entrée d'air d'un rayon de 43 mm est percée à l'intérieur du pied de turbine. Au centre du deuxième cercle d'un diamètre de 230 mm, un trou est percé avec une couronne d'un diamètre égal à l'épaisseur du plus petit cylindre sur l'arbre du moteur.
La structure est posée sur le moteur et vissée avec des vis à travers des trous pré-percés.
Le moteur démarre et le contreplaqué est nivelé à l'aide de papier de verre ou d'une meuleuse avec comme accessoire, en prenant des précautions. Le cercle supérieur est collé aux pales. La structure est sécurisée avec des pinces. Une meuleuse d'angle avec une meule émeri ou une meuleuse s'y adapte.
Si les lames dépassent fortement des cercles, elles doivent être soigneusement coupées avec une scie à main avec une marge de quelques millimètres.
Le moteur fonctionne avec un outil de chiffrement pour aligner les bords et centrer la turbine afin de minimiser les vibrations.
La même chose est faite pour niveler la surface supérieure. Un trou est pratiqué dans la « guitare » supérieure, égal au diamètre du cercle avec le moteur électrique, afin qu'il soit bien ajusté. Une prise d'air d'un rayon de 43 mm est découpée dans la « guitare » inférieure.
Une bande de 110 mm de haut est découpée dans une pièce de tôle d'acier, de circonférence égale à la « guitare » avec une marge.
La largeur est pliée à la longueur indiquée.
À une distance de 10 à 15 mm du bord sur toute la longueur de la tôle, les endroits où les vis sont vissées sont creusés tous les 40 à 50 mm.
Ils sont projetés sur le bord opposé de la bande à l'aide d'un carré ou son équivalent. Pour éviter les espaces le long du périmètre de contact entre le métal et le contreplaqué, du ruban de masquage est collé. Le métal est vissé au bas du socle.
Du côté inférieur du couvercle, 4 trous d'un diamètre de 5 à 6 mm sont percés à une distance de ~ 7 à 8 mm du bord et des boulons M5 ou M6 y sont vissés. À l'aide de morceaux de bois de 81 mm de hauteur, le couvercle est mis en place.
Ensuite, il est vissé avec des vis à métal. L'excès de métal est coupé.
Le bloc avec le moteur est inséré en place. Des rondelles sont placées sur les boulons et des ailes sont vissées pour fixer le bloc à l'intérieur de l'appareil. La conception peut être testée. Après un démarrage réussi, connectez-vous au conduit d'air pour éliminer l'air sale et l'outil via des adaptateurs.
Ne vous inquiétez pas si l'appareil doit être démonté plusieurs fois pour appliquer une deuxième couche de scellant entre le contreplaqué et le métal et un ponçage supplémentaire pour éliminer les vibrations. Il est conseillé de réaliser un carter de protection du moteur en bois ou en tôle d'acier, et d'isoler ses contacts avant le premier démarrage.
Voir la vidéo
Classes de maître similaires
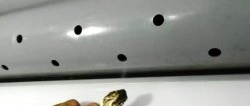
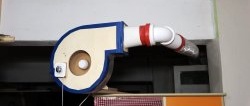
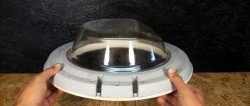
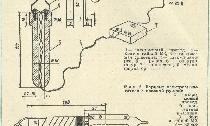
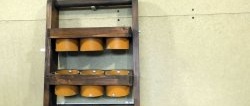
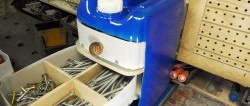