Angolo magnetico per saldatura
Quando si eseguono lavori di saldatura, si verificano momenti in cui è necessario afferrare contemporaneamente una parte e tenerla ad una certa angolazione. Questo lavoro richiede due persone o uno strumento speciale. Il più comunemente usato è un morsetto. Con il suo aiuto, la parte viene fissata nella posizione desiderata. Tuttavia, il morsetto presenta molti svantaggi. Pertanto, hai bisogno di un supporto magnetico speciale che ti aiuti a svolgere questo lavoro rapidamente e senza problemi inutili.
Vantaggi di un angolo magnetico per la saldatura
- In grado di sostenere entrambe le parti metalliche, liberando le mani per svolgere il lavoro principale.
- Non blocca l'accesso al punto di connessione, il che lo rende migliore di un morsetto.
- Consente di creare diverse opzioni di angolazione.
- Facile da usare.
- Non richiede grandi costi di produzione.
Processo di produzione degli angoli magnetici
Per prima cosa abbiamo bisogno di un disco magnetico con un diametro di ~15 cm e un diametro interno di ~5 cm. Inoltre ci servono dei quadrati di lamiera spessi 3 mm, con un lato di 20 cm. È molto importante che i lati della piazza sono perfettamente uniformi.È consigliabile che lo spessore del magnete non superi il materiale maggiormente utilizzato nel lavoro. L'opzione migliore è 1-1,5 cm.
Posiziona il magnete al centro del quadrato e traccialo con un pennarello per creare un segno. Successivamente, applichiamo le linee di taglio al metallo che devono essere realizzate per creare il motivo.
Blocchiamo il pezzo in una morsa e utilizziamo una turbina per tagliare gli elementi in eccesso.
Applichiamo la parte risultante al secondo quadrato per delinearne i contorni. Successivamente, rimuoviamo anche l'eccesso con una turbina.
Colleghiamo insieme i due pezzi grezzi risultanti e li fissiamo mediante saldatura. Ora possiamo eseguire un'operazione su due parti contemporaneamente.
Successivamente abbiamo bisogno di due giunti filettati. Installiamo un magnete sul pezzo, applicandolo nella posizione precedentemente designata. Quindi distribuiamo gli accoppiamenti lungo il suo perimetro, alla stessa distanza l'uno dall'altro. Contrassegniamo la loro posizione con un pennarello.
Rimuoviamo gli accoppiamenti. Contrassegniamo i fori al centro della posizione dei giunti. Successivamente, utilizzando un trapano corrispondente al diametro del foro nell'accoppiamento, realizziamo dei fori nel nostro pezzo. È attraverso di loro che verranno installati i bulloni per il fissaggio.
Successivamente, saldiamo un pezzo di tubo al pezzo, il diametro del foro interno del magnete. Lo sistemiamo esattamente in questo posto. Di conseguenza, abbiamo ottenuto una parte che può essere bloccata nel mandrino del tornio.
Utilizzando un trapano e una fresa su una macchina, creiamo un foro uguale al diametro interno dell'anello magnetico.
Rimuoviamo il tubo saldato e puliamo la nostra parte. In questo caso è molto importante ottenere bordi perfettamente lisci pur mantenendo il rispetto degli angoli. Pertanto, dovrai lavorare non solo con una rettificatrice, ma anche con una lima. Stiamo realizzando una sorta di strumento di misura, il che significa che la precisione del lavoro deve essere ottimale.
Nella fase successiva avremo bisogno di giunti e bulloni per loro.
I pezzi vengono separati e puliti. Successivamente, installa un magnete e dei giunti su uno di essi.
Sono coperti con un secondo pezzo grezzo sulla parte superiore, fissando la posizione con bulloni attraverso i giunti, ma senza serrarli completamente.
Nella fase finale, la struttura viene livellata e controllata per il rispetto degli angoli. Solo dopo vengono serrati i bulloni. La sagoma magnetica è pronta per l'uso.
Guarda il video
Masterclass simili
Particolarmente interessante
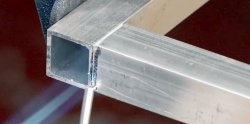
Un modo semplice per saldare l'alluminio
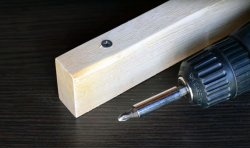
Come restaurare un pipistrello
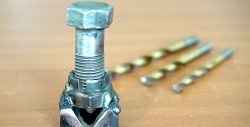
Dispositivo per l'affilatura del trapano
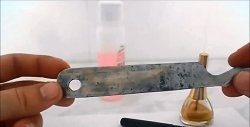
Come realizzare un foro nell'acciaio temprato senza forare
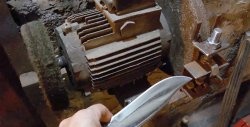
Il dispositivo più semplice per affilare i coltelli a 30 gradi
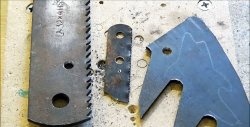
Come forare qualsiasi acciaio rapido con un trapano per piastrelle
Commenti (3)