Spaccalegna proveniente da un vecchio volano e motore di lavatrice
La spaccatura manuale dei blocchi di legno, soprattutto quelli nodosi, è piuttosto difficoltosa e piuttosto lenta. Oggi questo lavoro fisicamente difficile può essere accelerato trasferendolo sulle spalle di uno spaccalegna meccanico di fabbrica. C'è solo un problema: un tale "taglialegna" con una "carota" costa da 20mila rubli.
Ma l'esperienza degli artigiani dimostra che, anche senza la conoscenza della tornitura, è possibile realizzare una mannaia meccanica con materiali di scarto, adattandola al luogo, alla quantità di lavoro e ai dati antropometrici.
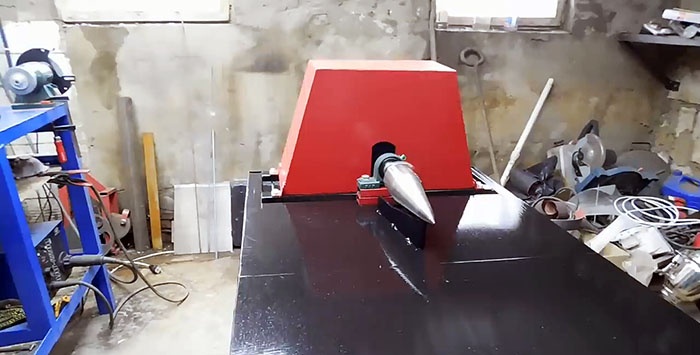
In linea di principio, quasi tutti i materiali e i componenti per l'assemblaggio di una mannaia meccanica possono essere rimossi da vecchie auto, elettrodomestici e trovati nelle discariche. Ma non fa male sapere quanto costa questa o quella "cosa" nel negozio, quanto costerà il motore di una vecchia lavatrice, quanto addebiterà il tornitore per il lavoro, ecc.
Quindi, di cosa dovremmo fare scorta se decidiamo di realizzare una mannaia meccanica:
Degli strumenti e delle attrezzature che dovremmo avere a portata di mano:
Fissiamo il legname tondo in una morsa e contrassegniamo i punti di taglio con nastro adesivo per garantire rapidamente e facilmente la precisione richiesta.
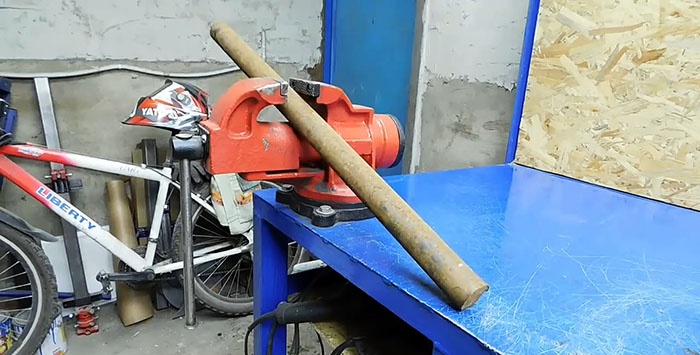
Tagliamo il pezzo grezzo dell'albero dello spaccalegna secondo le marcature utilizzando una smerigliatrice e un disco da taglio da 180 mm.
Segniamo la superficie di una spessa lastra di metallo con due dischi di dimensioni diverse, ma con fori centrali identici.
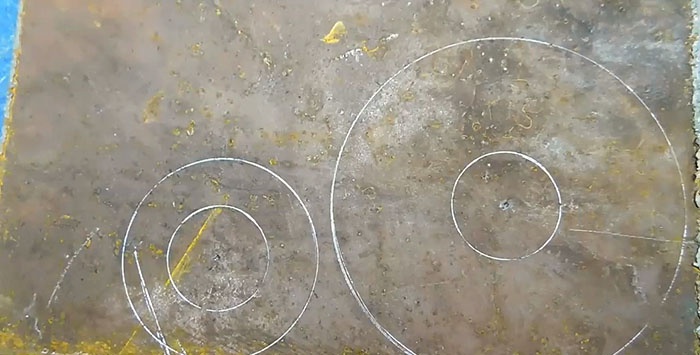
È più comodo e preciso tagliarli con un taglierino al plasma, di conseguenza la quantità di lavorazione successiva è ridotta al minimo.
Portiamo i dischi alla dimensione richiesta con una lima e una smerigliatrice e, per non rimuovere il metallo in eccesso, incolliamo motivi precisi di nastro o carta sulle superfici laterali.
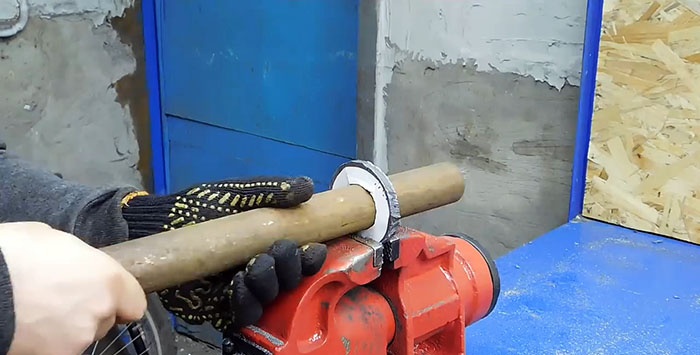
Durante la lavorazione dei dischi, prestiamo l'attenzione principale ai fori centrali: il pezzo dell'albero dovrebbe adattarsi liberamente al loro interno, ma gli spazi dovrebbero essere minimi.
Questa operazione è una delle più importanti: saldiamo un grande disco esattamente a 90 gradi al tondo di legno. Pertanto eseguiamo le saldature con attenzione, controllando costantemente l'angolo tra le parti in modo che non si muovano, e utilizziamo squadre magnetiche. Puliamo le saldature.
Il secondo anello è più facile da installare. È sufficiente premerlo saldamente e fissarlo al primo disco con dei morsetti e saldarlo in questa posizione.
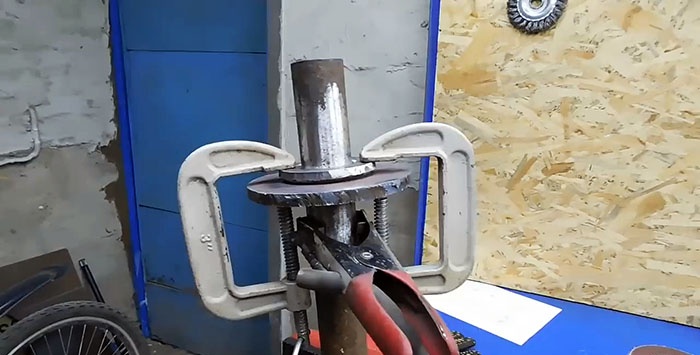
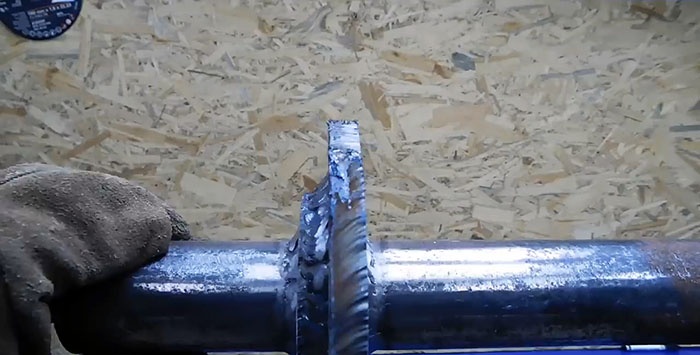
Ora il tornitore lavorerà sul pezzo: girerà il supporto anteriore, che è saldato all'anello più piccolo, molerà a misura le superfici circolari e realizzerà una serie di scanalature dell'anello per la cinghia di trasmissione.
Da un tubo profilato tagliamo pezzi grezzi delle dimensioni richieste e nella quantità richiesta, dai quali saldiamo non solo un desktop, ma anche una base per l'installazione delle unità montate.
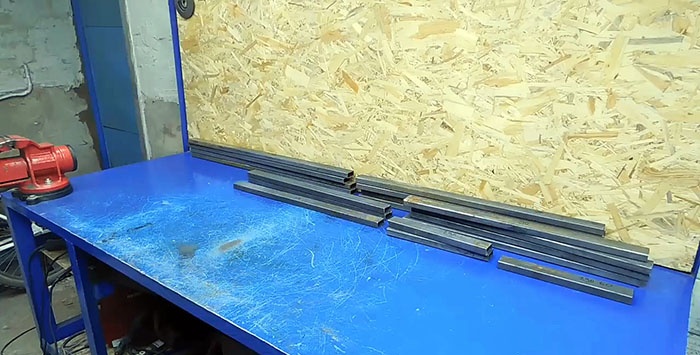
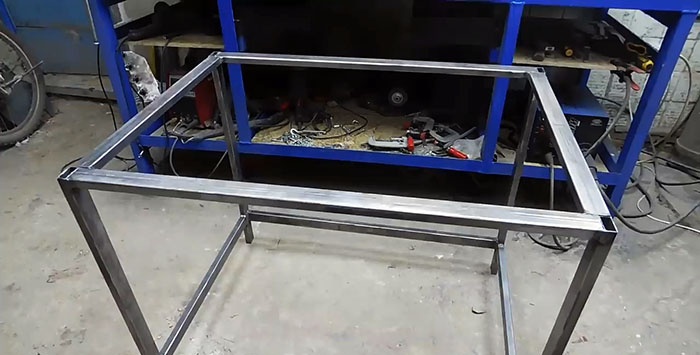
Separatamente, saldiamo un sottotelaio al telaio principale sotto il piano del tavolo, al quale verrà fissato e regolato il motore elettrico.
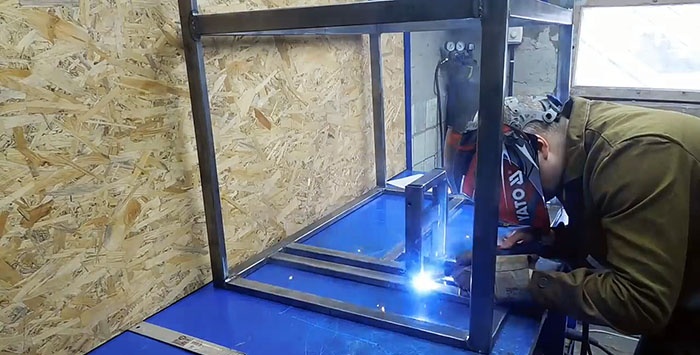
Utilizzando una smerigliatrice, ritagliamo da una piastra metallica di spessore 6 mm due parti simmetriche che, saldate tra loro e fissate al piano del tavolo, diventeranno una sorta di supporto lama sullo spaccalegna.
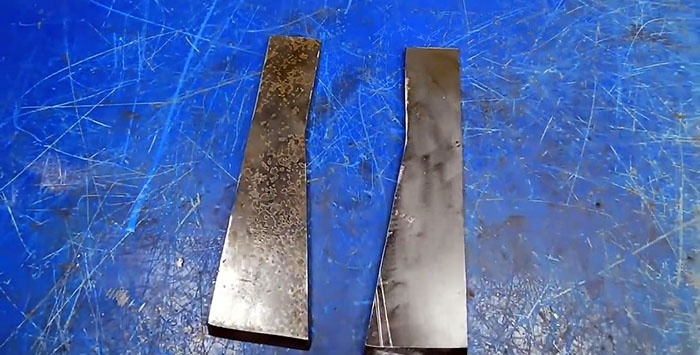
Poiché il carico sul nostro dispositivo cambierà costantemente, non possiamo fare a meno del volano. Nel nostro caso, in termini di dimensioni e peso, il volano più adatto era un GAZ-53 con un diametro esterno di 372 mm, un foro di montaggio di 40 mm e un peso di quasi 16 kg.
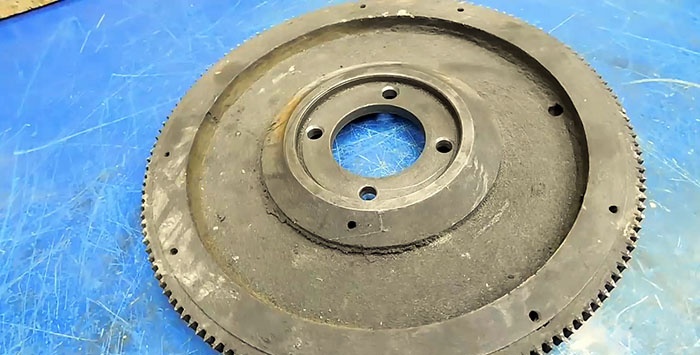
Rimuoviamo la corona dentata da questa parte e la puliamo da molti anni di sporco oleoso utilizzando un martello, un cacciavite e una smerigliatrice con accessori.
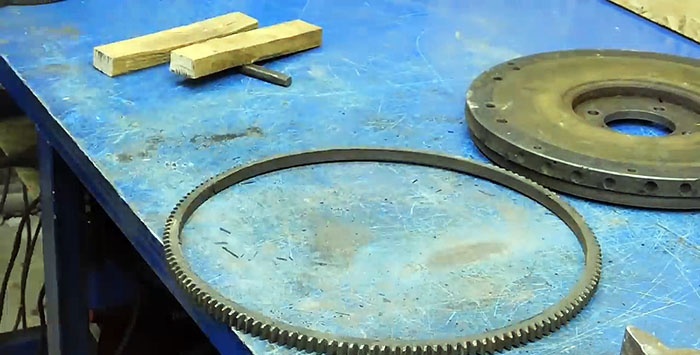
Eseguiamo il bilanciamento statico dell'albero e del volano avvitandoli tra loro con bulloni e dadi. A causa della mancanza di una macchina di bilanciamento, ne abbiamo creata una utilizzando solo le capacità disponibili.
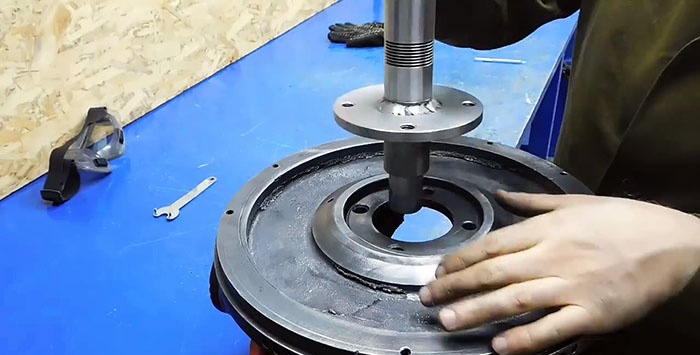
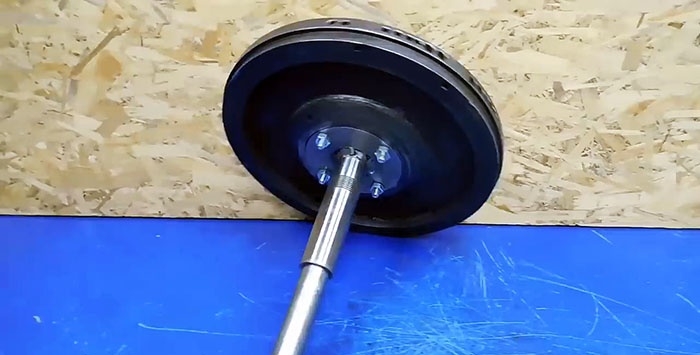
Per fare ciò, posizionare temporaneamente due angoli paralleli al telaio del tavolo e afferrarli leggermente. Utilizzando una livella, ci assicuriamo che gli angoli siano il più piatti possibile e posizioniamo l'albero con sopra il volano.
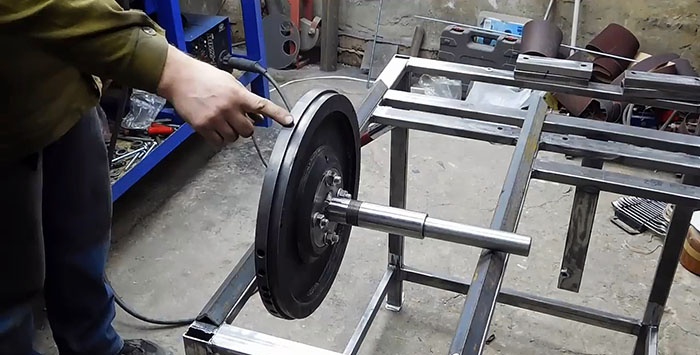
Diamo rotazione al volano e monitoriamo il momento dell'arresto. Se su di esso è presente una massa sbilanciata, rotolerà leggermente indietro prima di fermarsi. Inoltre, la massa in eccesso sarà nel punto più basso.Contrassegniamo questo punto e praticiamo un foro, rimuovendo così la massa in eccesso.
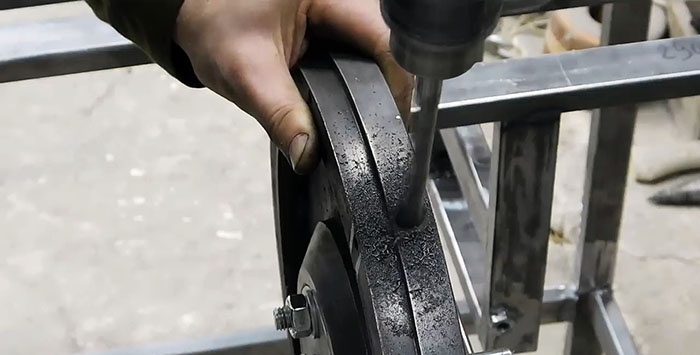
L'equilibratura sarà considerata completa quando l'albero e il volano non tornano indietro prima dell'arresto.
Per sicurezza, realizziamo una copertura protettiva per il volano dai resti del tubo profilato e della lamiera e cuciniamo il piano del tavolo.
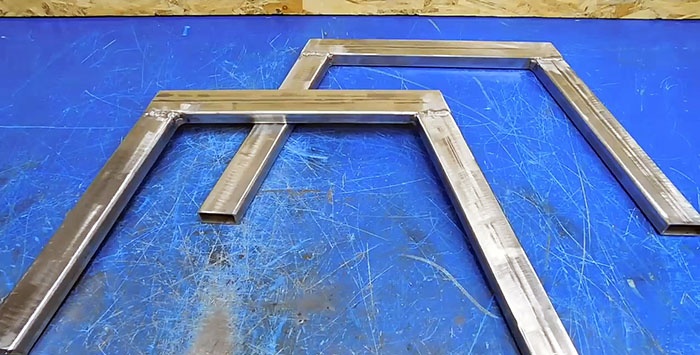
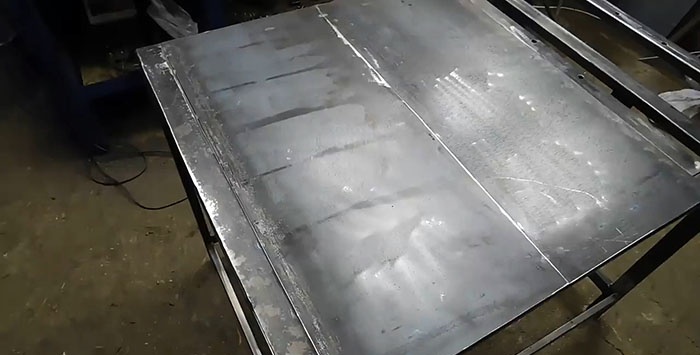
Colleghiamo insieme due parti simmetriche ad angolo, posizioniamo un distanziatore all'interno e saldiamo l'assemblaggio risultante al piano del tavolo.
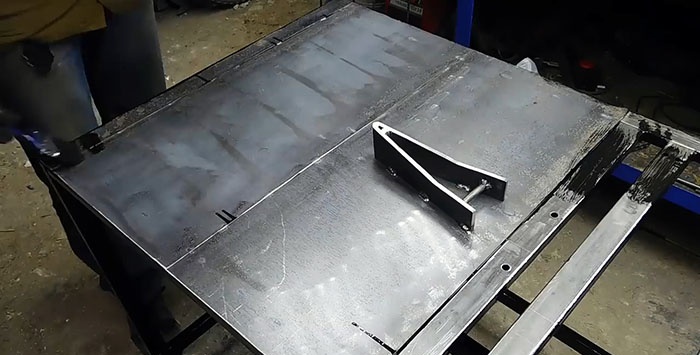
Tutti i componenti e le parti sono stati realizzati, quindi iniziamo a dipingerli utilizzando un normale pennello.
Stimiamo quanto ci costerà uno spaccalegna fatto in casa:
Il totale è di circa 7mila rubli. Questo è 3 volte inferiore rispetto allo spaccalegna di fabbrica più economico.
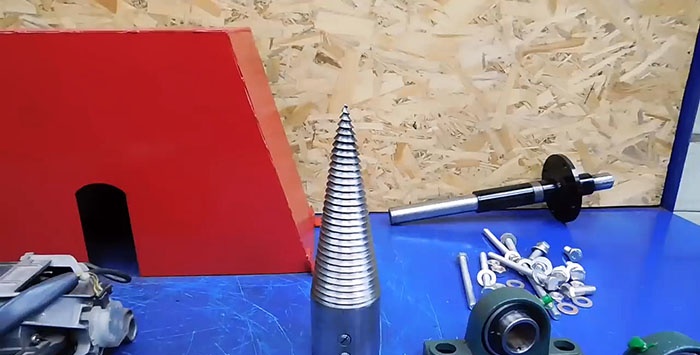
Avvitiamo saldamente il volano all'albero, mettiamo la cinghia, le unità cuscinetto e fissiamo l'unità al telaio.
Installiamo e fissiamo la "carota" all'estremità dell'albero con due perni speciali.
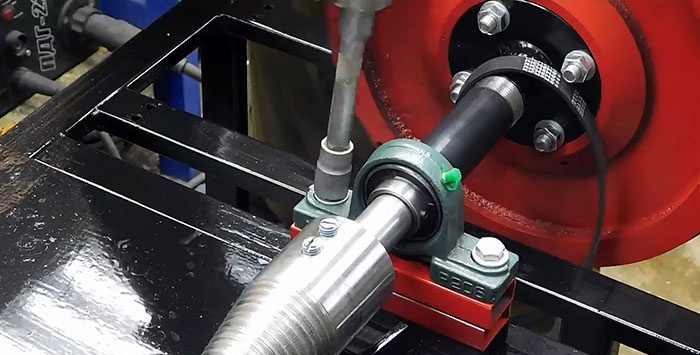
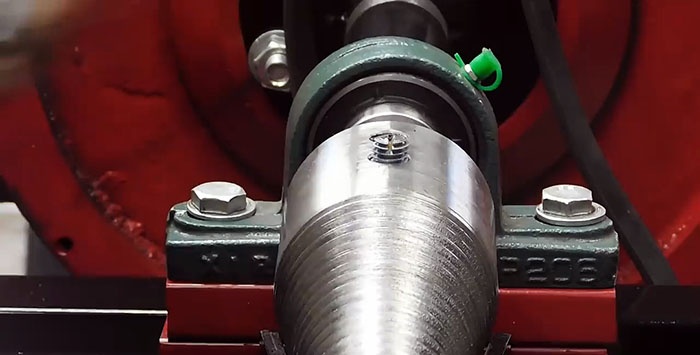
Tendiamo la cinghia stringendo il bullone previsto a tale scopo, che, appoggiato al supporto, muove il motore e mette in tensione la cinghia.
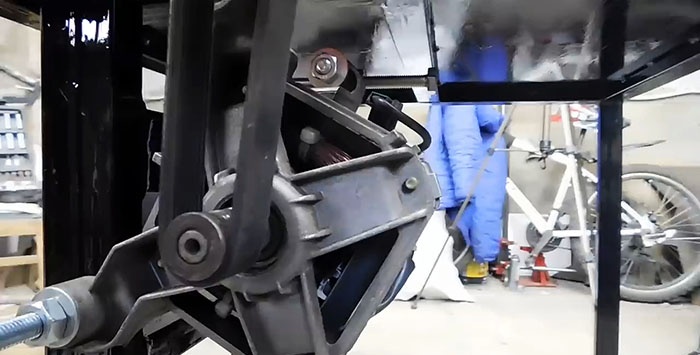
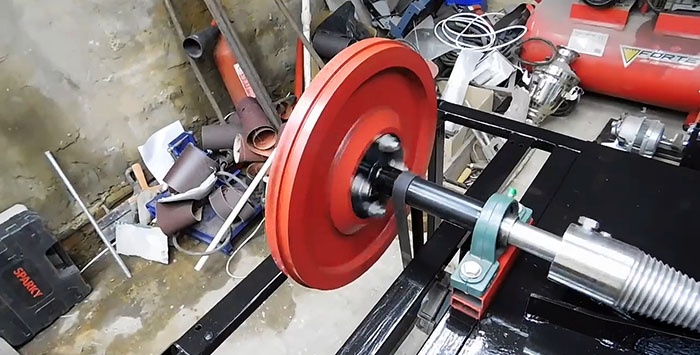
L'impianto elettrico è costituito da un cavo di alimentazione, un interruttore e un regolatore di tensione della smerigliatrice. Il sistema di connessione è abbastanza standard.
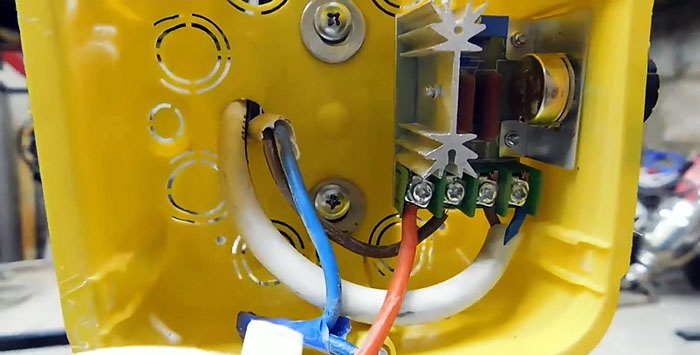
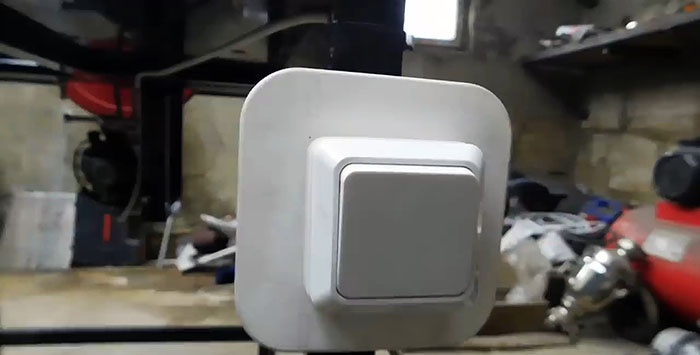
All'avvio, la presenza di un regolatore elimina gli strappi e garantisce un aumento graduale della velocità da parte del volano. Questo è molto importante perché la cinghia non scivola nelle scanalature e quindi durerà più a lungo.
Inoltre, grazie al regolatore di tensione, è possibile modificare la potenza, che senza carico porta immediatamente ad un aumento della velocità.
Installiamo una copertura protettiva sul volano per proteggere noi stessi e le persone vicine da lesioni se il volano vola improvvisamente via dall'albero o si rompe.
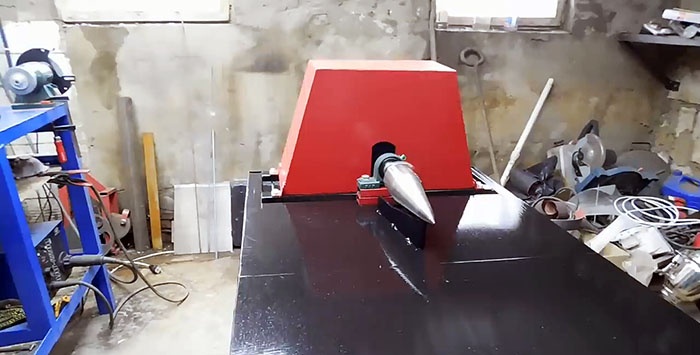
Per prima cosa, proviamo a dividere un piccolo pezzo di tavola. Il nostro prodotto fatto in casa lo affronta senza sforzo. La stessa cosa accade con i tronchi secchi che sono stati immagazzinati sotto una tettoia: lo spaccalegna lavora un ceppo abbastanza massiccio senza alcuno stress.
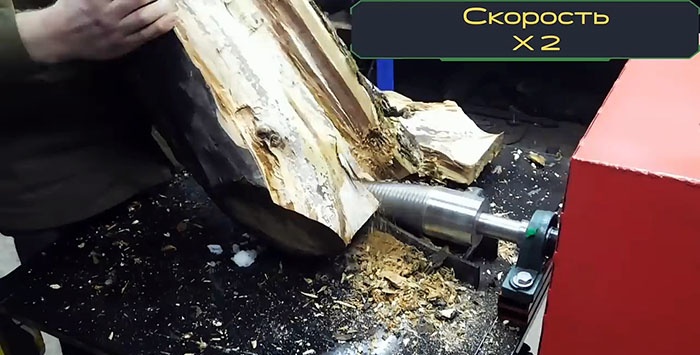
Se all'improvviso la “carota” rimane incastrata in un tronco, spegnendo l'alimentazione, utilizzando la chiave e ruotando la parte posteriore dell'albero, possiamo facilmente liberare l'elemento di lavoro dal tronco in cui è bloccato.
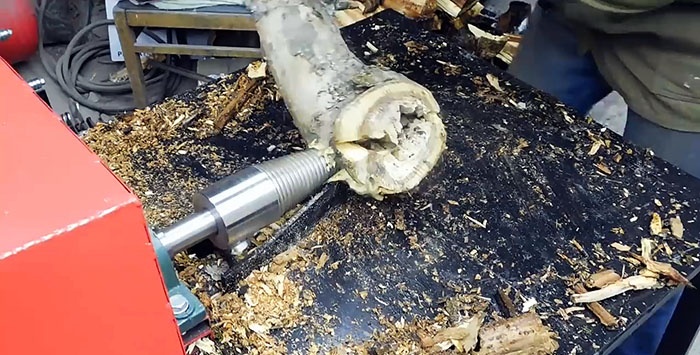
Anche questa piccola pratica ha dimostrato che il fissaggio della “carota” sull'albero deve essere incassato in modo da non creare interferenze durante il taglio della legna da ardere, e il tavolo deve poggiare su una superficie assolutamente orizzontale. Ciò eliminerà anche le piccole vibrazioni durante il funzionamento dello spaccalegna.
Inoltre, non è possibile lavorare su questa unità indossando guanti e muffole, e le maniche degli indumenti non devono essere troppo lunghe e senza lacci, cinture e altri elementi pendenti, in modo che non si attorciglino in una "carota" e danneggino le mani.
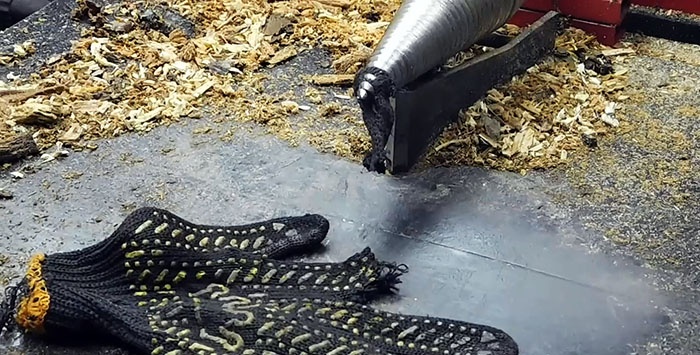
Ma l'esperienza degli artigiani dimostra che, anche senza la conoscenza della tornitura, è possibile realizzare una mannaia meccanica con materiali di scarto, adattandola al luogo, alla quantità di lavoro e ai dati antropometrici.
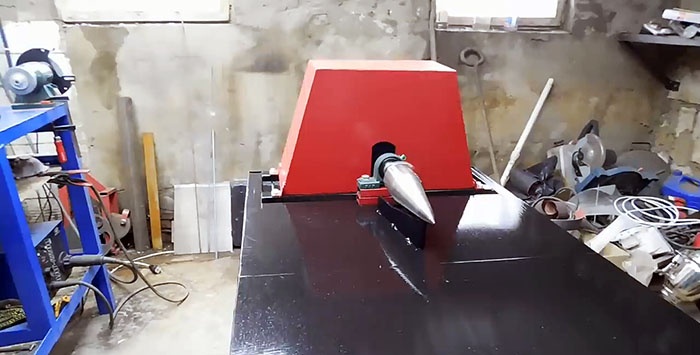
Avrà bisogno
In linea di principio, quasi tutti i materiali e i componenti per l'assemblaggio di una mannaia meccanica possono essere rimossi da vecchie auto, elettrodomestici e trovati nelle discariche. Ma non fa male sapere quanto costa questa o quella "cosa" nel negozio, quanto costerà il motore di una vecchia lavatrice, quanto addebiterà il tornitore per il lavoro, ecc.
Quindi, di cosa dovremmo fare scorta se decidiamo di realizzare una mannaia meccanica:
- acciaio laminato tondo (legno tondo);
- nastro adesivo;
- lamiere di diverso spessore;
- tubo profilato circa 14 m;
- volano da GAZ-53;
- bulloni, dadi, rondelle;
- motore con puleggia e cinghia;
- vernice e pennello;
- mannaia per carote a vite conica.
Degli strumenti e delle attrezzature che dovremmo avere a portata di mano:
- smerigliatrice con dischi;
- taglierina al plasma;
- lima metallica;
- attrezzature per la saldatura;
- morse e fascette;
- forare con trapani.
Produzione di componenti e parti dello spaccalegna
Fissiamo il legname tondo in una morsa e contrassegniamo i punti di taglio con nastro adesivo per garantire rapidamente e facilmente la precisione richiesta.
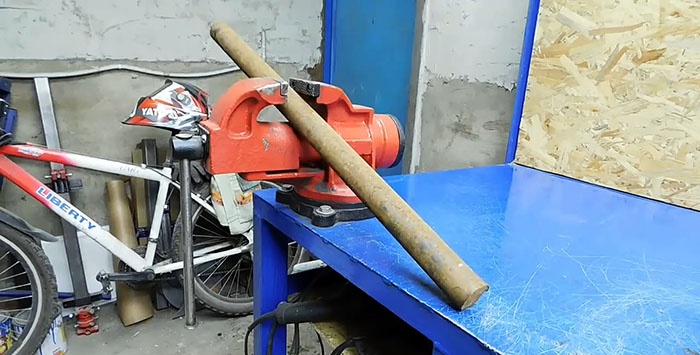
Tagliamo il pezzo grezzo dell'albero dello spaccalegna secondo le marcature utilizzando una smerigliatrice e un disco da taglio da 180 mm.
Segniamo la superficie di una spessa lastra di metallo con due dischi di dimensioni diverse, ma con fori centrali identici.
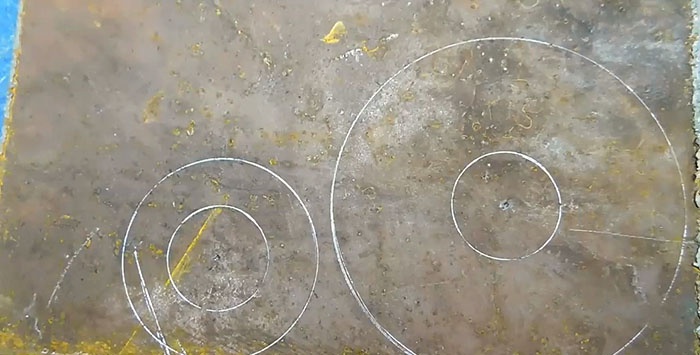
È più comodo e preciso tagliarli con un taglierino al plasma, di conseguenza la quantità di lavorazione successiva è ridotta al minimo.
Portiamo i dischi alla dimensione richiesta con una lima e una smerigliatrice e, per non rimuovere il metallo in eccesso, incolliamo motivi precisi di nastro o carta sulle superfici laterali.
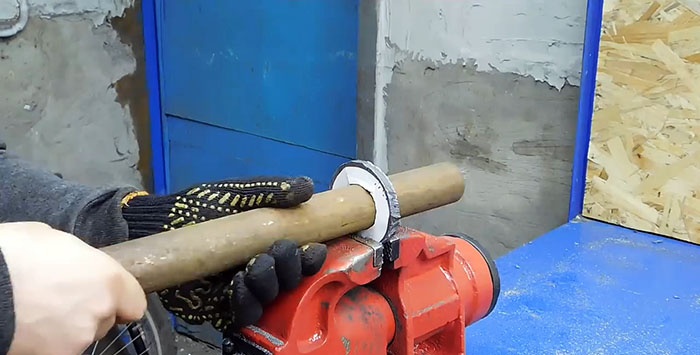
Durante la lavorazione dei dischi, prestiamo l'attenzione principale ai fori centrali: il pezzo dell'albero dovrebbe adattarsi liberamente al loro interno, ma gli spazi dovrebbero essere minimi.
Questa operazione è una delle più importanti: saldiamo un grande disco esattamente a 90 gradi al tondo di legno. Pertanto eseguiamo le saldature con attenzione, controllando costantemente l'angolo tra le parti in modo che non si muovano, e utilizziamo squadre magnetiche. Puliamo le saldature.
Il secondo anello è più facile da installare. È sufficiente premerlo saldamente e fissarlo al primo disco con dei morsetti e saldarlo in questa posizione.
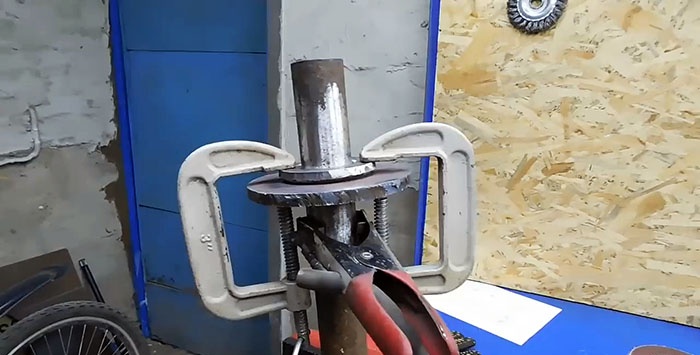
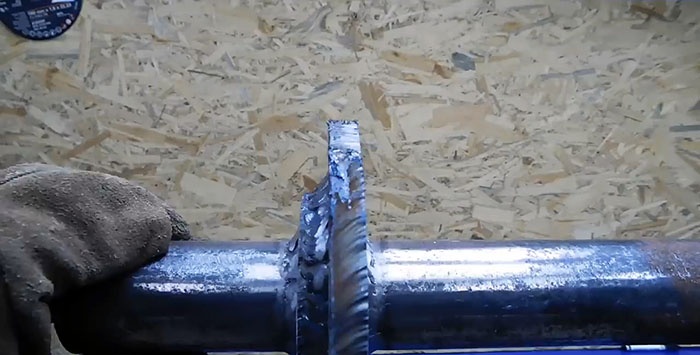
Ora il tornitore lavorerà sul pezzo: girerà il supporto anteriore, che è saldato all'anello più piccolo, molerà a misura le superfici circolari e realizzerà una serie di scanalature dell'anello per la cinghia di trasmissione.
Da un tubo profilato tagliamo pezzi grezzi delle dimensioni richieste e nella quantità richiesta, dai quali saldiamo non solo un desktop, ma anche una base per l'installazione delle unità montate.
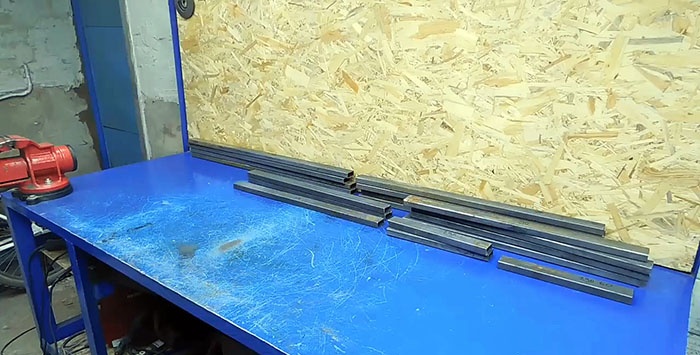
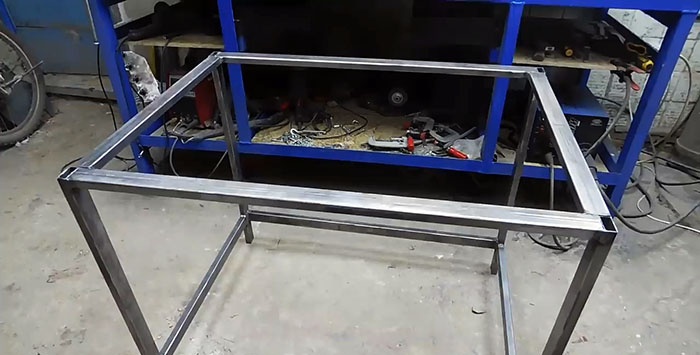
Separatamente, saldiamo un sottotelaio al telaio principale sotto il piano del tavolo, al quale verrà fissato e regolato il motore elettrico.
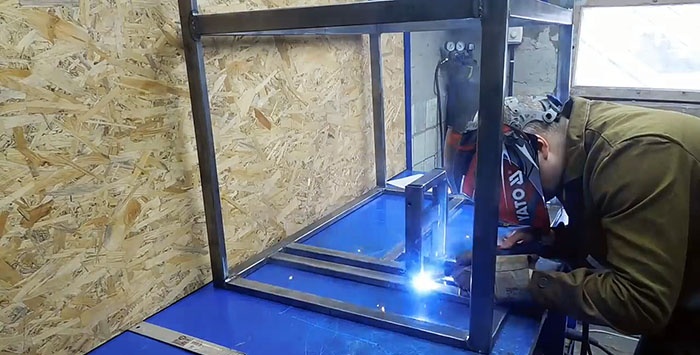
Utilizzando una smerigliatrice, ritagliamo da una piastra metallica di spessore 6 mm due parti simmetriche che, saldate tra loro e fissate al piano del tavolo, diventeranno una sorta di supporto lama sullo spaccalegna.
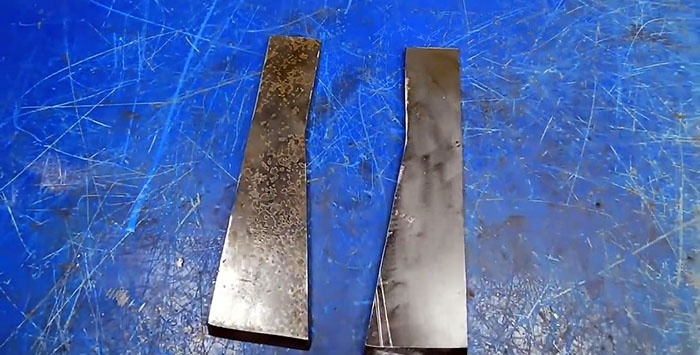
Poiché il carico sul nostro dispositivo cambierà costantemente, non possiamo fare a meno del volano. Nel nostro caso, in termini di dimensioni e peso, il volano più adatto era un GAZ-53 con un diametro esterno di 372 mm, un foro di montaggio di 40 mm e un peso di quasi 16 kg.
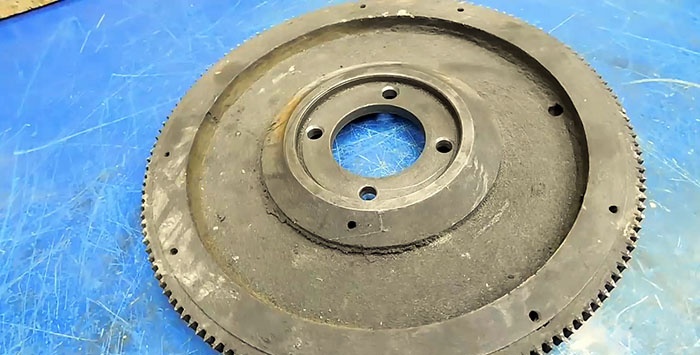
Rimuoviamo la corona dentata da questa parte e la puliamo da molti anni di sporco oleoso utilizzando un martello, un cacciavite e una smerigliatrice con accessori.
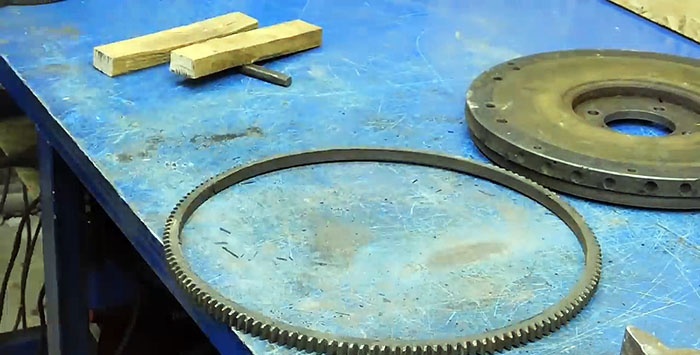
Eseguiamo il bilanciamento statico dell'albero e del volano avvitandoli tra loro con bulloni e dadi. A causa della mancanza di una macchina di bilanciamento, ne abbiamo creata una utilizzando solo le capacità disponibili.
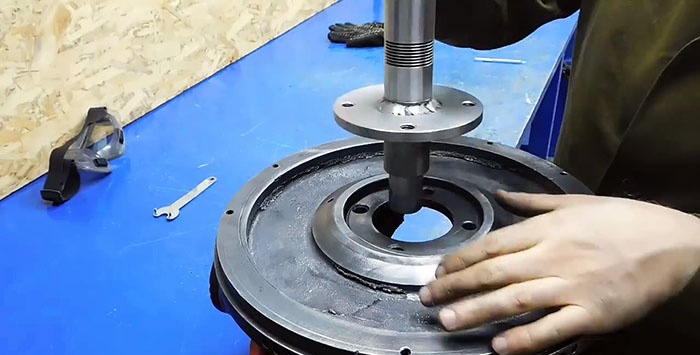
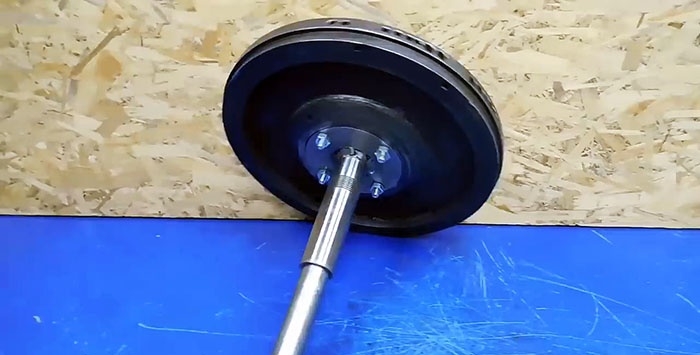
Per fare ciò, posizionare temporaneamente due angoli paralleli al telaio del tavolo e afferrarli leggermente. Utilizzando una livella, ci assicuriamo che gli angoli siano il più piatti possibile e posizioniamo l'albero con sopra il volano.
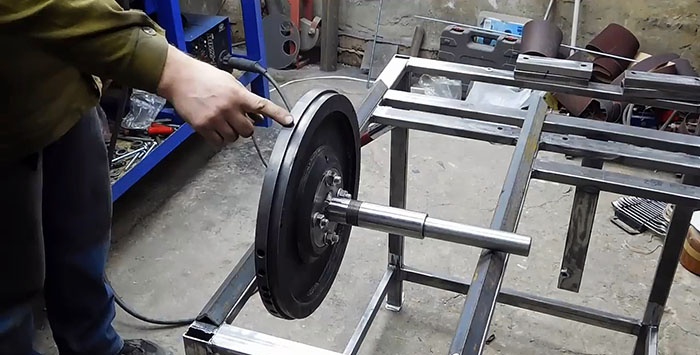
Diamo rotazione al volano e monitoriamo il momento dell'arresto. Se su di esso è presente una massa sbilanciata, rotolerà leggermente indietro prima di fermarsi. Inoltre, la massa in eccesso sarà nel punto più basso.Contrassegniamo questo punto e praticiamo un foro, rimuovendo così la massa in eccesso.
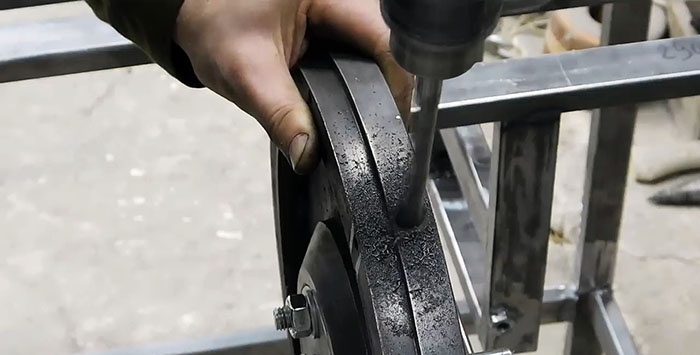
L'equilibratura sarà considerata completa quando l'albero e il volano non tornano indietro prima dell'arresto.
Per sicurezza, realizziamo una copertura protettiva per il volano dai resti del tubo profilato e della lamiera e cuciniamo il piano del tavolo.
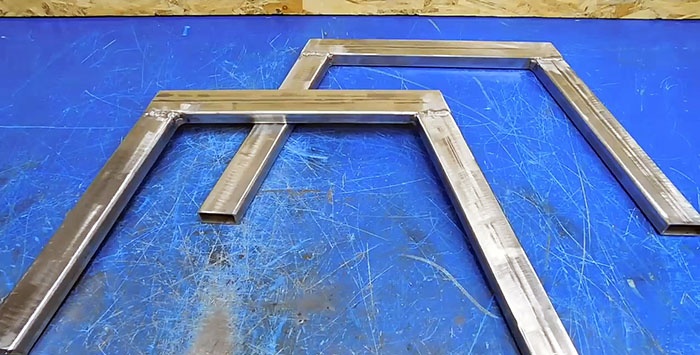
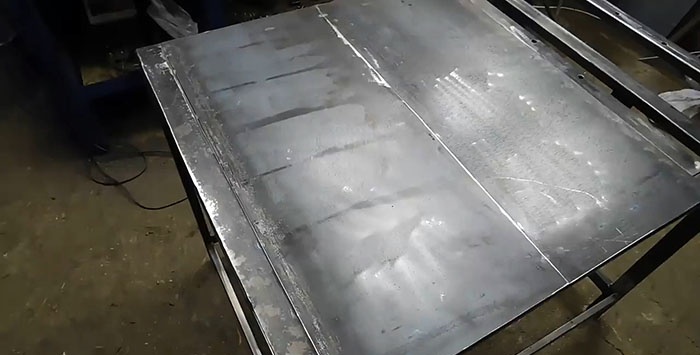
Colleghiamo insieme due parti simmetriche ad angolo, posizioniamo un distanziatore all'interno e saldiamo l'assemblaggio risultante al piano del tavolo.
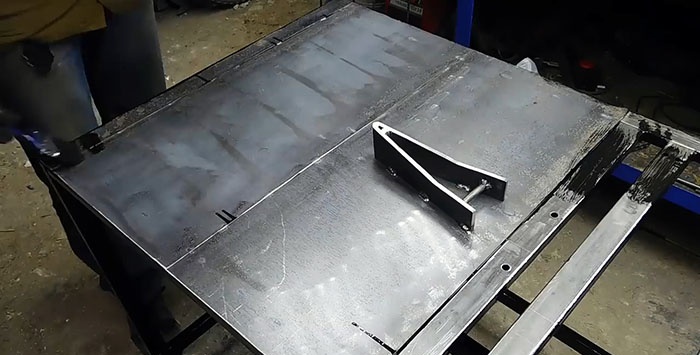
Tutti i componenti e le parti sono stati realizzati, quindi iniziamo a dipingerli utilizzando un normale pennello.
Costi approssimativi
Stimiamo quanto ci costerà uno spaccalegna fatto in casa:
- volano – 1200 rub.;
- tubo profilato 14 m – 1200 sfregamenti;
- motore della lavatrice (730 W, 8mila giri/min) – 530 rubli;
- “carota” (diametro base – 70 mm, altezza – 250 mm) – 1300 rubli;
- due cuscinetti da 206 in un alloggiamento – 600 rubli;
- lavoro di tornitura - 1650 rubli;
- hardware e cinghia di trasmissione – 530 rub.
Il totale è di circa 7mila rubli. Questo è 3 volte inferiore rispetto allo spaccalegna di fabbrica più economico.
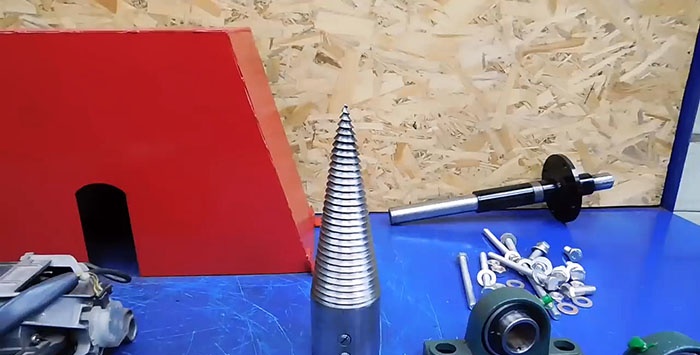
Assemblaggio di componenti e parti dello spaccalegna
Avvitiamo saldamente il volano all'albero, mettiamo la cinghia, le unità cuscinetto e fissiamo l'unità al telaio.
Installiamo e fissiamo la "carota" all'estremità dell'albero con due perni speciali.
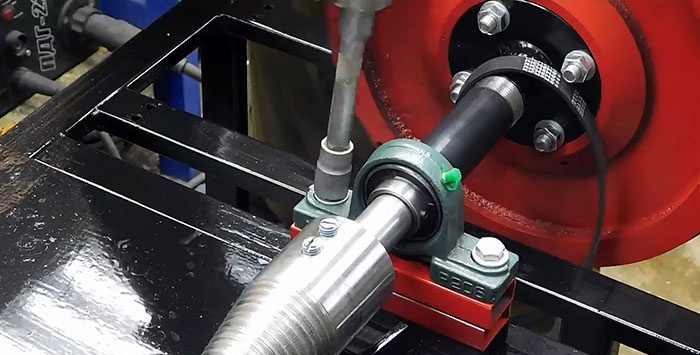
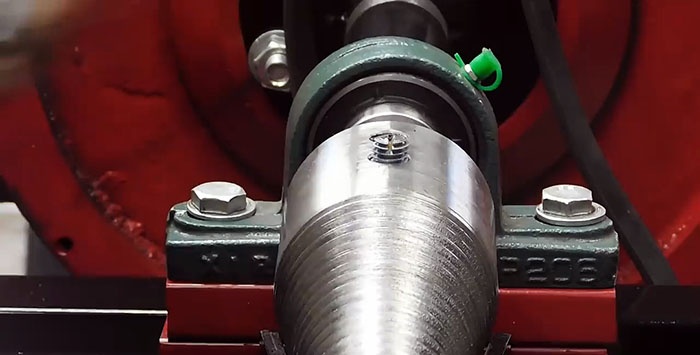
Tendiamo la cinghia stringendo il bullone previsto a tale scopo, che, appoggiato al supporto, muove il motore e mette in tensione la cinghia.
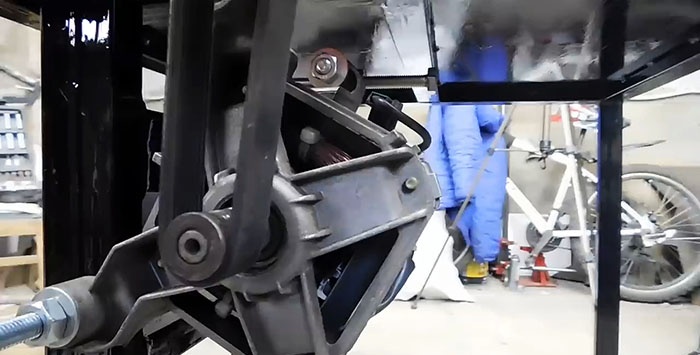
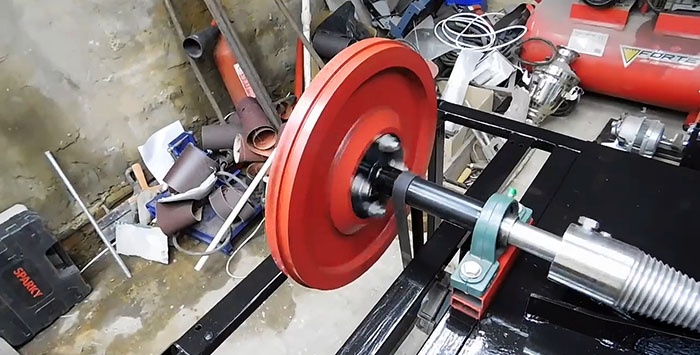
L'impianto elettrico è costituito da un cavo di alimentazione, un interruttore e un regolatore di tensione della smerigliatrice. Il sistema di connessione è abbastanza standard.
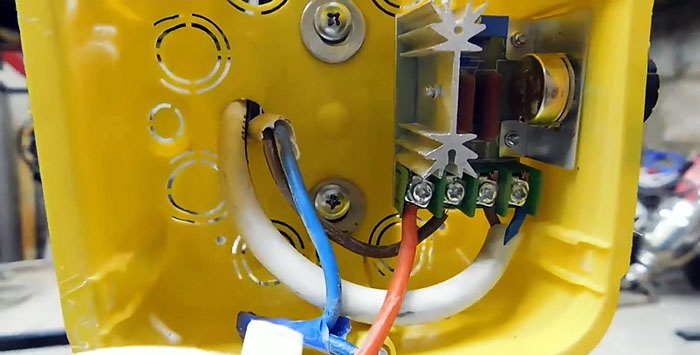
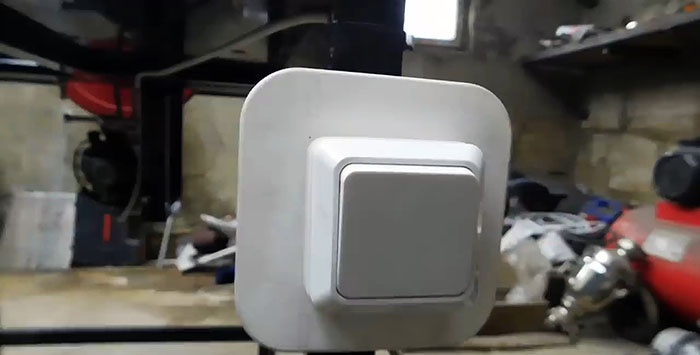
All'avvio, la presenza di un regolatore elimina gli strappi e garantisce un aumento graduale della velocità da parte del volano. Questo è molto importante perché la cinghia non scivola nelle scanalature e quindi durerà più a lungo.
Inoltre, grazie al regolatore di tensione, è possibile modificare la potenza, che senza carico porta immediatamente ad un aumento della velocità.
Installiamo una copertura protettiva sul volano per proteggere noi stessi e le persone vicine da lesioni se il volano vola improvvisamente via dall'albero o si rompe.
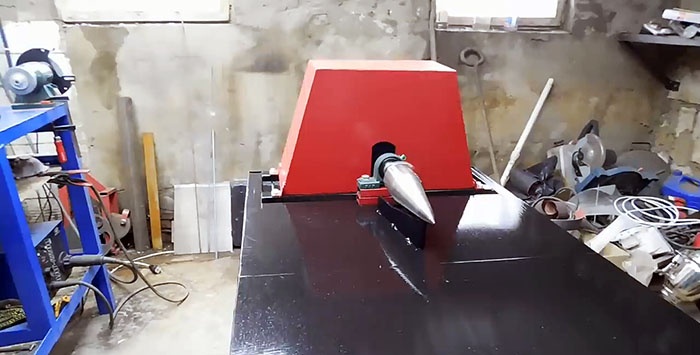
Testare uno spaccalegna in azione
Per prima cosa, proviamo a dividere un piccolo pezzo di tavola. Il nostro prodotto fatto in casa lo affronta senza sforzo. La stessa cosa accade con i tronchi secchi che sono stati immagazzinati sotto una tettoia: lo spaccalegna lavora un ceppo abbastanza massiccio senza alcuno stress.
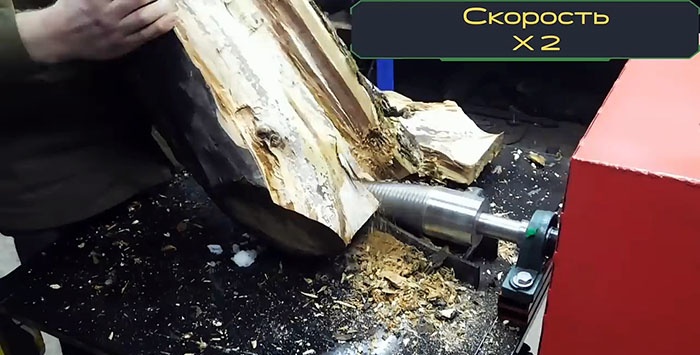
Se all'improvviso la “carota” rimane incastrata in un tronco, spegnendo l'alimentazione, utilizzando la chiave e ruotando la parte posteriore dell'albero, possiamo facilmente liberare l'elemento di lavoro dal tronco in cui è bloccato.
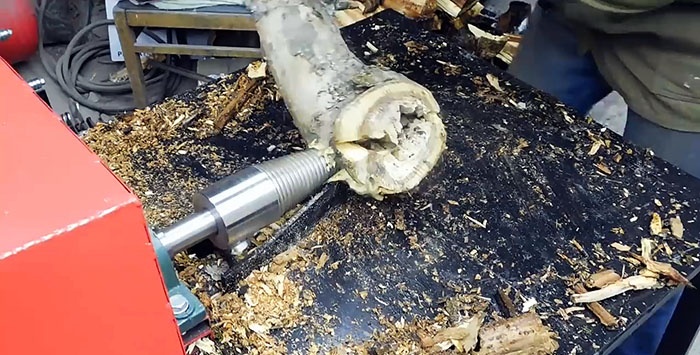
Anche questa piccola pratica ha dimostrato che il fissaggio della “carota” sull'albero deve essere incassato in modo da non creare interferenze durante il taglio della legna da ardere, e il tavolo deve poggiare su una superficie assolutamente orizzontale. Ciò eliminerà anche le piccole vibrazioni durante il funzionamento dello spaccalegna.
Inoltre, non è possibile lavorare su questa unità indossando guanti e muffole, e le maniche degli indumenti non devono essere troppo lunghe e senza lacci, cinture e altri elementi pendenti, in modo che non si attorciglino in una "carota" e danneggino le mani.
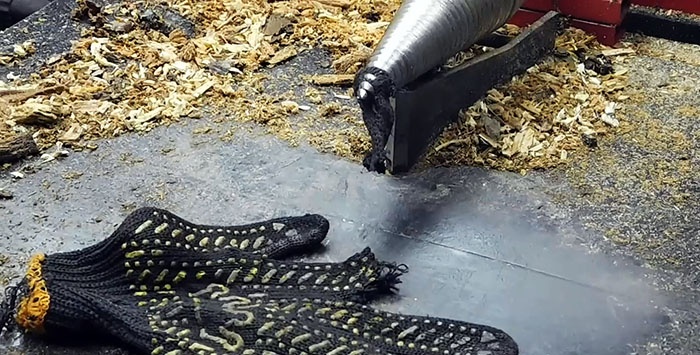
Guarda il video
Masterclass simili
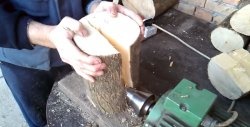
Progettazione e principio di funzionamento di uno spaccalegna a vite
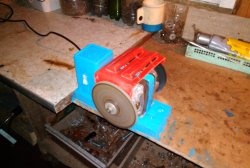
Affilatore dal motore di una lavatrice
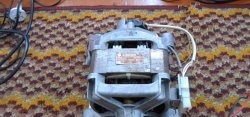
Come collegare il motore di una lavatrice a 220 V
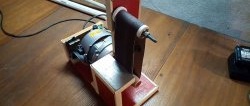
La smerigliatrice più semplice senza saldatura e rotazione dal motore di una lavatrice
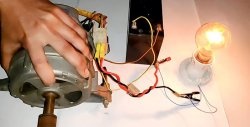
Come trasformare il motore della lavatrice in un generatore da 220 V
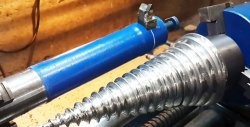
Come realizzare uno spaccalegna "carota" in garage
Particolarmente interessante
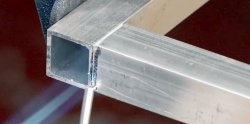
Un modo semplice per saldare l'alluminio
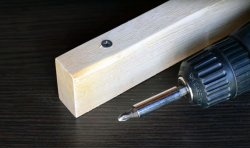
Come restaurare un pipistrello
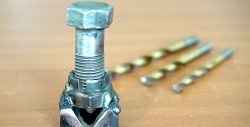
Dispositivo per l'affilatura del trapano
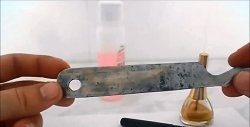
Come realizzare un foro nell'acciaio temprato senza forare
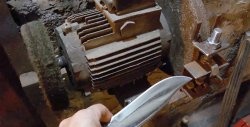
Il dispositivo più semplice per affilare i coltelli a 30 gradi
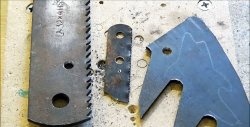
Come forare qualsiasi acciaio rapido con un trapano per piastrelle
Commenti (0)