Serre met een zelfgemaakt frame
Nadat ik verschillende geprefabriceerde kassen had gezien die bij verschillende winkels waren gekocht, vormde ik een zelfverzekerde mening over de kwetsbaarheid van deze constructies. Wat mij vooral aan het lachen maakte, was de montage van dunne gegalvaniseerde platen met schroeven, bijna rechtstreeks uit een kinderbouwdoos. Mijn persoonlijke perceel ligt op een heuvel, er zijn vrijwel geen bomen, geen open ruimte, dus de wind is erg sterk en de "fabrieks" geprefabriceerde structuur van de kas zal zeker niet bestand zijn tegen de windstoten. Later, tijdens de installatie bij winderig weer, was ik ervan overtuigd dat mijn veronderstelling juist was; de toch al bijna vaste polycarbonaatplaat kwam door de windkracht als een veertje los en gooide de ladder van 50 kilogram terug.
De taak was bovendien om een kas te verkrijgen met afmetingen van 3 meter breed en 8 meter lang, met de mogelijkheid voor een persoon van gemiddelde lengte om zich er vrij in te bewegen, d.w.z. tot 1,8 meter. Daarom besloot ik een kas te maken van polycarbonaat met een frame van een metalen profiel naar eigen ontwerp.
Het frame bestond voornamelijk uit lichtgewicht metalen buizen en hoeken. De "dak" -constructie was gemaakt van het noktype, een gewoon zadeldak, getest op betrouwbaarheid.De hoogte van de nok zal variëren afhankelijk van de weersomstandigheden bij jou in de buurt, ik heb gekozen voor een spanthoek van 45 graden zodat de sneeuw er in de winter gemakkelijk vanaf rolt. Tijdens de installatie werden de spanten versterkt met een dwarsbalk, verbonden door een driehoek.
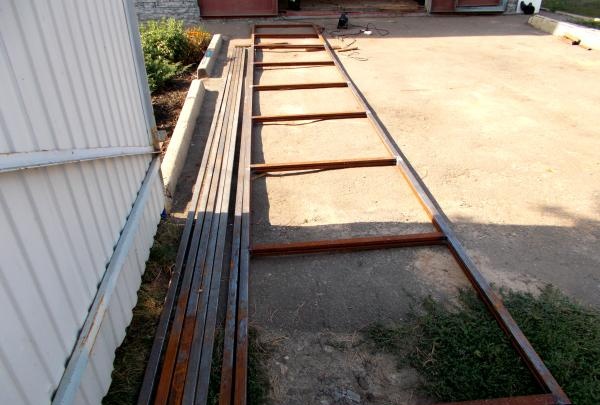
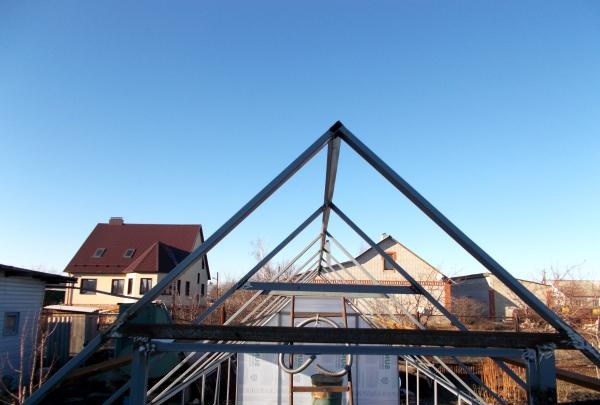
Standaard polycarbonaatplaten hebben de volgende afmetingen: dikte 4 mm, breedte 2,1, lengte 6 meter. Ik vestig de aandacht op de kwaliteit van polycarbonaat, ik heb de Russische fabrikant Sunnex gebruikt, laten we zeggen dat het van gemiddelde kwaliteit is, er is een duurzamer en dichter materiaal, dit is merkbaar in doorbuiging, structuur en gewicht, en ultraviolette transmissie. De keuze is aan jou, maar je moet niet bezuinigen om te voorkomen dat hij kapot gaat onder belasting door sneeuw of wind.
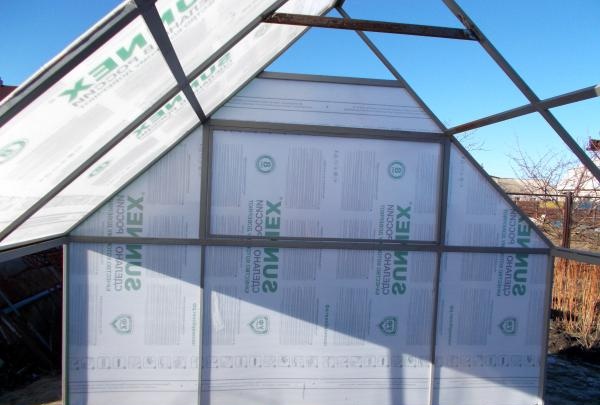
Bouw Traditioneel begon ik met het leggen van een kleine fundering, omdat in mijn geval de kas stevig verankerd moest worden, en ook om vervormingen te voorkomen. Ik heb dunne funderingsblokken en dwarsliggers van gewapend beton gebruikt. In de "standaard" gaten van de dwarsliggers plaatste ik bouten voor krachtige bevestigingen van het frame rond de omtrek van de hele kas. Bij het installeren van de gehele frameconstructie, in delen gelast, dienden deze bevestigingsmiddelen als bevestiging voor de verdere installatie van het bovenste rooster (er waren op dit moment echter assistenten nodig om het frame te ondersteunen).
Caracas maakte het van een metalen profielbuis van 20*40 mm met een rooster van maximaal 1 meter, anders kan het polycarbonaat in de winter bezwijken door ijzige sneeuw. De onderste uiteinden heb ik gemaakt van een hoek van 35*35 mm zodat de deur op de voeg zou sluiten.
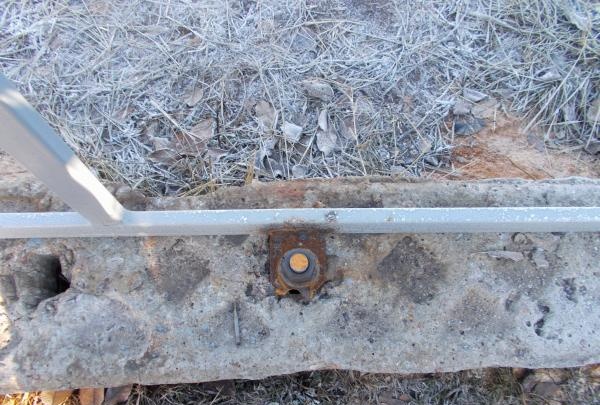
Niet onbelangrijk: we ontwerpen het frame zo dat we het polycarbonaat het meest economisch snijden, namelijk de zijwanden maken we 1,05 meter hoog, waarbij we er rekening mee houden dat de plaat in de lengte doormidden wordt gesneden. Spanten van 2,1 meter lang, zodat twee hele platen aan het dak kunnen worden bevestigd en een extra plaat in stukken van elk 2 meter kan worden gesneden.
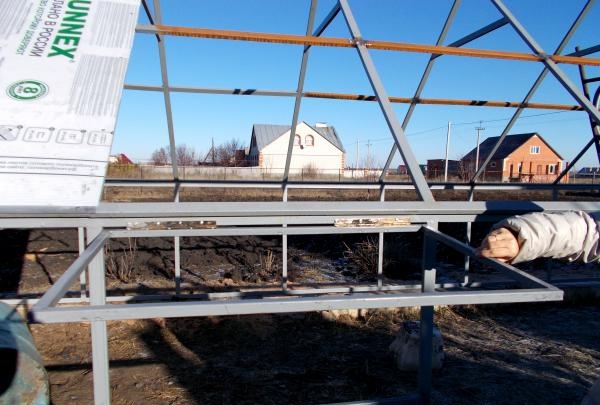
Naast de deur heb ik in de kas twee ramen voorzien voor ventilatie, aan de lijzijde aan het uiteinde en de zijkant van de constructie, gelast uit een lichtgewicht 20*20 mm profiel. Ik heb de ramen op pianoscharnieren geïnstalleerd; ze zijn vrij dun en hinderen niet dat het polycarbonaat stevig op het frame past.
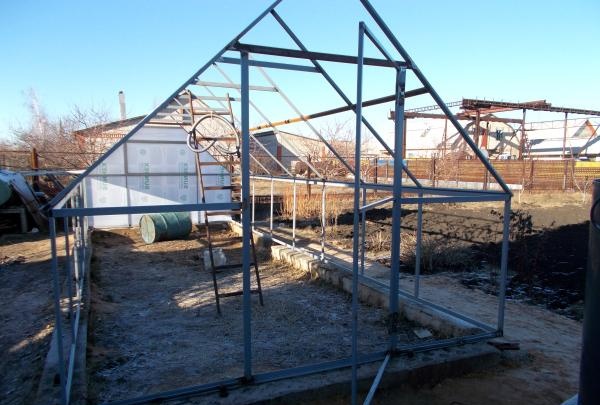
Alle voegen en gaten in het polycarbonaat waren opgevuld met siliconen en de scheuren aan de onderkant waren opgevuld met polyurethaanschuim. Het frame werd op de laspunten geschuurd, geverfd met corrosiewerend middel en verf.
Materiaal voor kassenbouw:
- polycarbonaat 2,1*6 m. – 5 platen;
- metalen profielbuis 20*40 mm – 120 meter;
- metalen profielbuis 20*20 mm – 18 meter;
- parkers met drukring en boor – 1000 stuks;
- funderingsblokken (dwarsliggers) met een totale lengte van 22 meter;
- zand voor het leggen van de fundering;
- bevestigingen en bouten voor het frame;
- corrosiewerende verf;
- deur- en pianoscharnieren, deurklinken;
- laselektroden 3 kg.
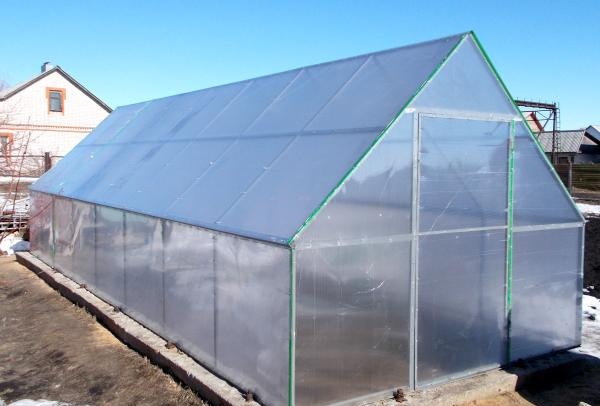
Voordelen van de kas: duurzame gevelconstructie; stijve bevestiging van het frame; vereiste geometrische afmetingen; Makkelijk te gebruiken; mogelijkheid tot economisch snijden van materiaal; weinig gewrichten.
Nadelen: de verbinding van het dak en de zijspant van het frame bleken versterkt te zijn met twee profielen, wat economisch niet rendabel is.
De taak was bovendien om een kas te verkrijgen met afmetingen van 3 meter breed en 8 meter lang, met de mogelijkheid voor een persoon van gemiddelde lengte om zich er vrij in te bewegen, d.w.z. tot 1,8 meter. Daarom besloot ik een kas te maken van polycarbonaat met een frame van een metalen profiel naar eigen ontwerp.
Het frame bestond voornamelijk uit lichtgewicht metalen buizen en hoeken. De "dak" -constructie was gemaakt van het noktype, een gewoon zadeldak, getest op betrouwbaarheid.De hoogte van de nok zal variëren afhankelijk van de weersomstandigheden bij jou in de buurt, ik heb gekozen voor een spanthoek van 45 graden zodat de sneeuw er in de winter gemakkelijk vanaf rolt. Tijdens de installatie werden de spanten versterkt met een dwarsbalk, verbonden door een driehoek.
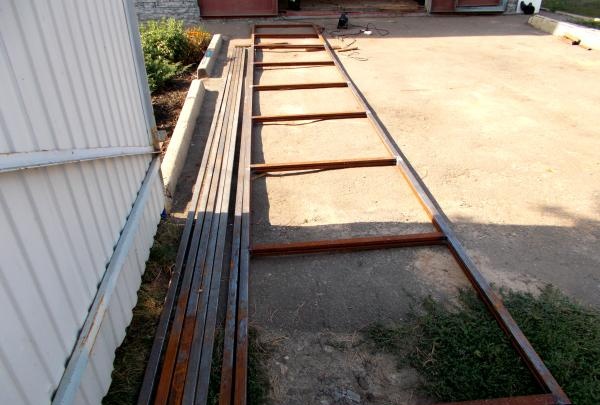
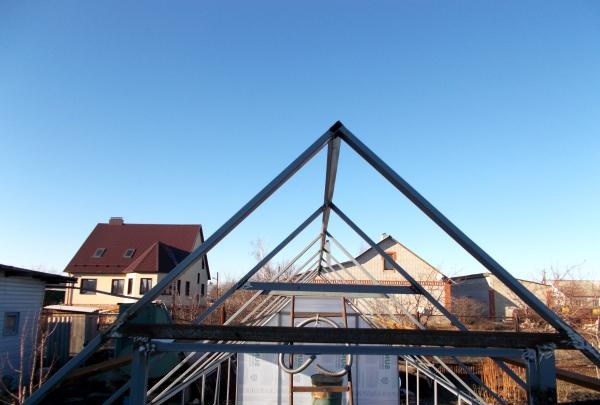
Standaard polycarbonaatplaten hebben de volgende afmetingen: dikte 4 mm, breedte 2,1, lengte 6 meter. Ik vestig de aandacht op de kwaliteit van polycarbonaat, ik heb de Russische fabrikant Sunnex gebruikt, laten we zeggen dat het van gemiddelde kwaliteit is, er is een duurzamer en dichter materiaal, dit is merkbaar in doorbuiging, structuur en gewicht, en ultraviolette transmissie. De keuze is aan jou, maar je moet niet bezuinigen om te voorkomen dat hij kapot gaat onder belasting door sneeuw of wind.
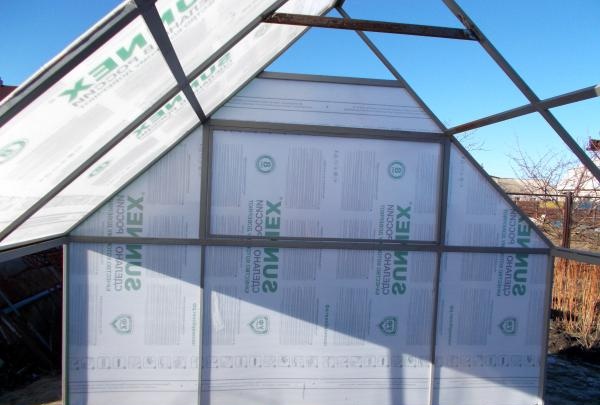
Bouw Traditioneel begon ik met het leggen van een kleine fundering, omdat in mijn geval de kas stevig verankerd moest worden, en ook om vervormingen te voorkomen. Ik heb dunne funderingsblokken en dwarsliggers van gewapend beton gebruikt. In de "standaard" gaten van de dwarsliggers plaatste ik bouten voor krachtige bevestigingen van het frame rond de omtrek van de hele kas. Bij het installeren van de gehele frameconstructie, in delen gelast, dienden deze bevestigingsmiddelen als bevestiging voor de verdere installatie van het bovenste rooster (er waren op dit moment echter assistenten nodig om het frame te ondersteunen).
Caracas maakte het van een metalen profielbuis van 20*40 mm met een rooster van maximaal 1 meter, anders kan het polycarbonaat in de winter bezwijken door ijzige sneeuw. De onderste uiteinden heb ik gemaakt van een hoek van 35*35 mm zodat de deur op de voeg zou sluiten.
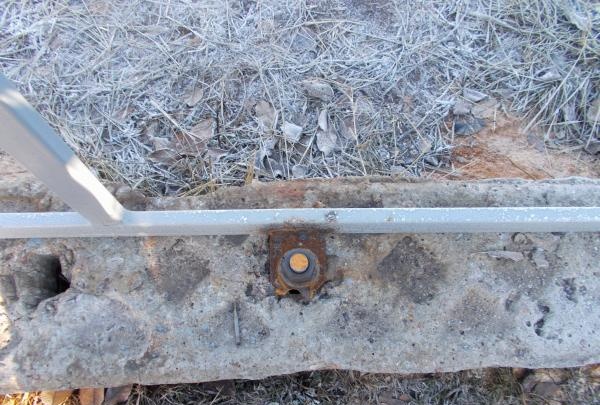
Niet onbelangrijk: we ontwerpen het frame zo dat we het polycarbonaat het meest economisch snijden, namelijk de zijwanden maken we 1,05 meter hoog, waarbij we er rekening mee houden dat de plaat in de lengte doormidden wordt gesneden. Spanten van 2,1 meter lang, zodat twee hele platen aan het dak kunnen worden bevestigd en een extra plaat in stukken van elk 2 meter kan worden gesneden.
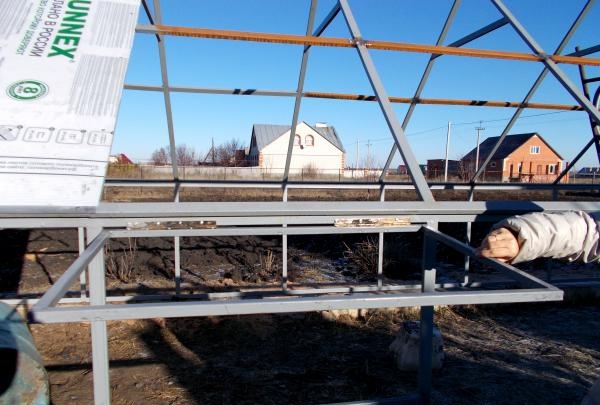
Naast de deur heb ik in de kas twee ramen voorzien voor ventilatie, aan de lijzijde aan het uiteinde en de zijkant van de constructie, gelast uit een lichtgewicht 20*20 mm profiel. Ik heb de ramen op pianoscharnieren geïnstalleerd; ze zijn vrij dun en hinderen niet dat het polycarbonaat stevig op het frame past.
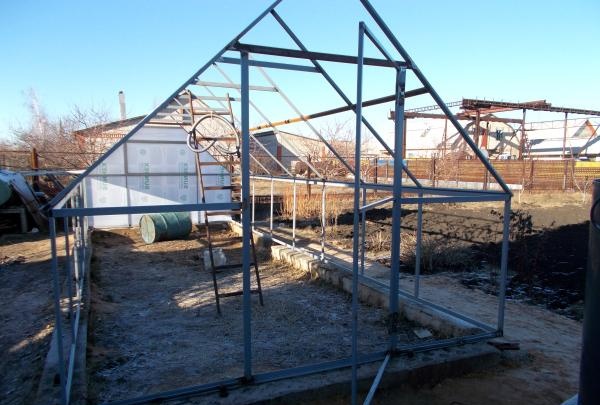
Alle voegen en gaten in het polycarbonaat waren opgevuld met siliconen en de scheuren aan de onderkant waren opgevuld met polyurethaanschuim. Het frame werd op de laspunten geschuurd, geverfd met corrosiewerend middel en verf.
Materiaal voor kassenbouw:
- polycarbonaat 2,1*6 m. – 5 platen;
- metalen profielbuis 20*40 mm – 120 meter;
- metalen profielbuis 20*20 mm – 18 meter;
- parkers met drukring en boor – 1000 stuks;
- funderingsblokken (dwarsliggers) met een totale lengte van 22 meter;
- zand voor het leggen van de fundering;
- bevestigingen en bouten voor het frame;
- corrosiewerende verf;
- deur- en pianoscharnieren, deurklinken;
- laselektroden 3 kg.
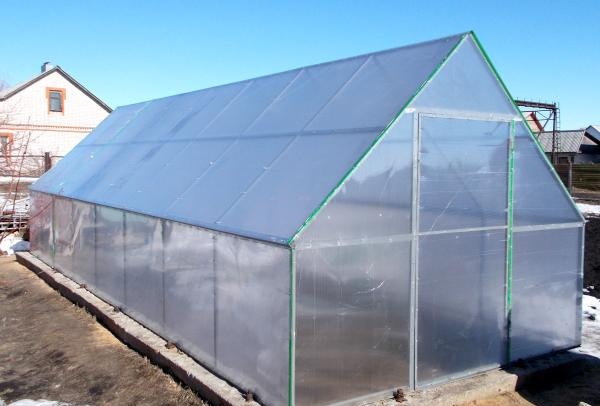
Voordelen van de kas: duurzame gevelconstructie; stijve bevestiging van het frame; vereiste geometrische afmetingen; Makkelijk te gebruiken; mogelijkheid tot economisch snijden van materiaal; weinig gewrichten.
Nadelen: de verbinding van het dak en de zijspant van het frame bleken versterkt te zijn met twee profielen, wat economisch niet rendabel is.
Soortgelijke masterclasses
Bijzonder interessant
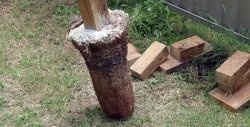
Hoe je gemakkelijk een paal uit de grond trekt
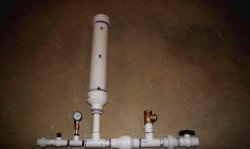
Waterpomp zonder stroom
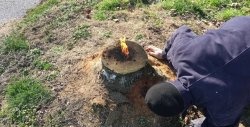
Hoe u eenvoudig een stronk kunt verwijderen zonder te ontwortelen
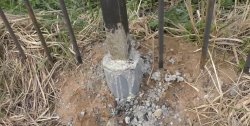
Hoe u een hekpaal tot het laatst installeert
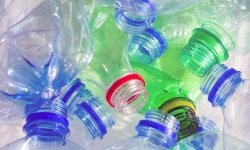
Ongebruikelijk gebruik van plastic flessen op het platteland
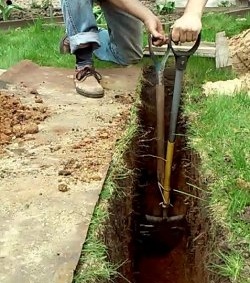
Hoe je water naar een huis brengt zonder een graafmachine en een team van gravers
Opmerkingen (0)