Divisor de madeira de um antigo volante e motor de máquina de lavar
A divisão manual de blocos de madeira, especialmente os com nós, é bastante difícil e bastante lenta. Hoje, esse trabalho fisicamente difícil pode ser acelerado transferindo-o para os ombros de um rachador mecânico de madeira fabricado na fábrica. Só há um problema: um “lenhador” com uma “cenoura” custa a partir de 20 mil rublos.
Mas a experiência dos artesãos mostra que, mesmo sem conhecimento de torneamento, é possível fazer um cutelo mecânico a partir de sucata, adaptando-o ao local, quantidade de trabalho e dados antropométricos.
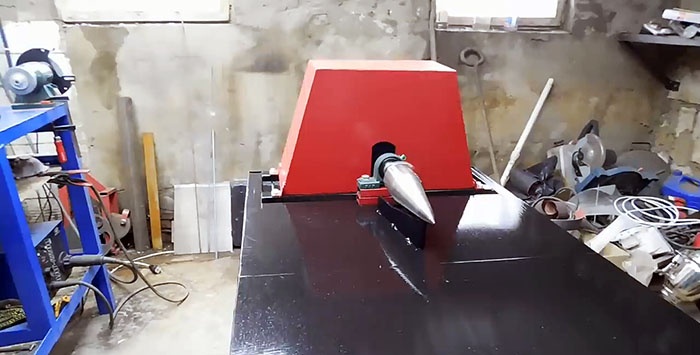
Em princípio, quase todos os materiais e componentes para a montagem de um cutelo mecânico podem ser retirados de carros antigos, eletrodomésticos e encontrados em aterros sanitários. Mas não custa saber quanto custa esta ou aquela “coisa” na loja, quanto custará o motor de uma máquina de lavar velha, quanto o torneiro cobrará pela obra, etc.
Então, o que devemos estocar se decidirmos fazer um cutelo mecânico:
Das ferramentas e equipamentos que devemos ter em mãos:
Fixamos a madeira redonda em um torno e marcamos os locais de corte com fita adesiva para garantir de forma rápida e fácil a precisão necessária.
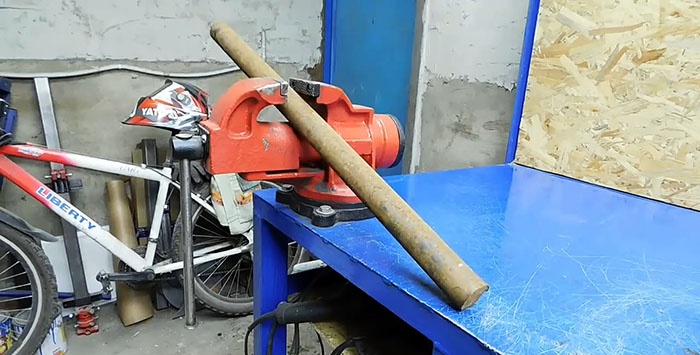
De acordo com as marcações, recortamos o blank do eixo do rachador de madeira com uma esmerilhadeira e um disco de corte de 180 mm.
Marcamos a superfície de uma chapa grossa de metal com dois discos de tamanhos diferentes, mas com furos centrais idênticos.
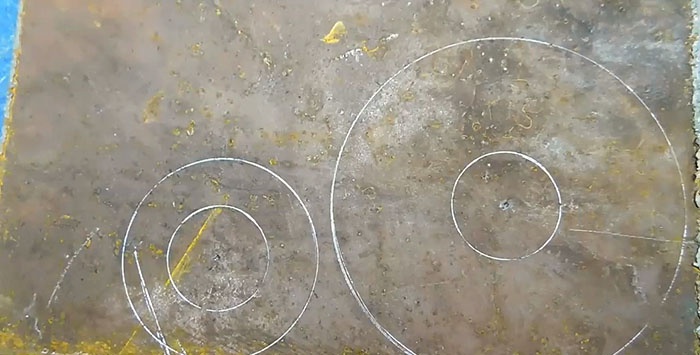
É mais conveniente e preciso cortá-los com um cortador de plasma e, como resultado, a quantidade de processamento subsequente é minimizada.
Levamos os discos ao tamanho desejado com uma lima e uma esmerilhadeira e, para não retirar o excesso de metal, colamos padrões precisos de fita ou papel nas superfícies laterais.
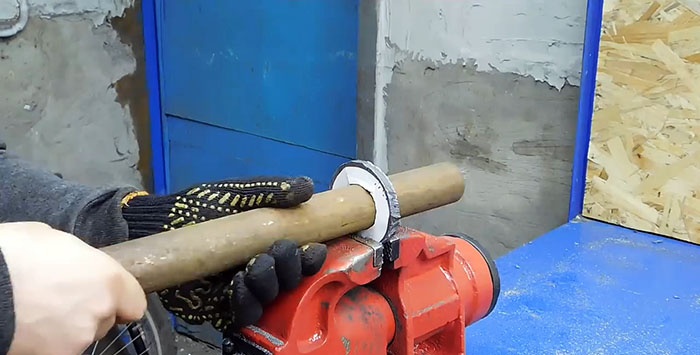
Ao processar discos, prestamos atenção principal aos furos centrais: a peça do eixo deve caber livremente neles, mas as folgas devem ser mínimas.
Esta operação é uma das mais importantes: soldamos um grande disco exatamente a 90 graus na madeira redonda. Por isso, realizamos a soldagem com cuidado, verificando constantemente o ângulo entre as peças para que não se movam, e utilizamos quadrados magnéticos. Limpamos as soldas.
O segundo anel é mais fácil de instalar. Basta pressioná-lo bem e fixá-lo no primeiro disco com pinças e soldá-lo nesta posição.
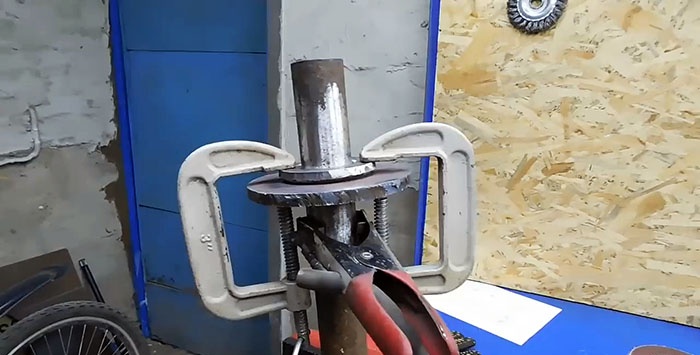
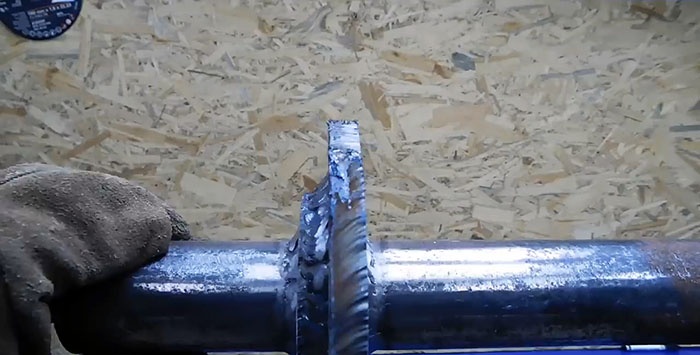
Agora o torneiro trabalhará na peça de trabalho: ele girará o suporte frontal, que é soldado ao anel menor, retificará as superfícies circulares no tamanho certo e fará uma série de ranhuras para a correia de transmissão.
A partir de um tubo perfilado cortamos blanks nos tamanhos e quantidades necessários, dos quais soldamos não apenas uma mesa, mas também uma base para a instalação de unidades montadas.
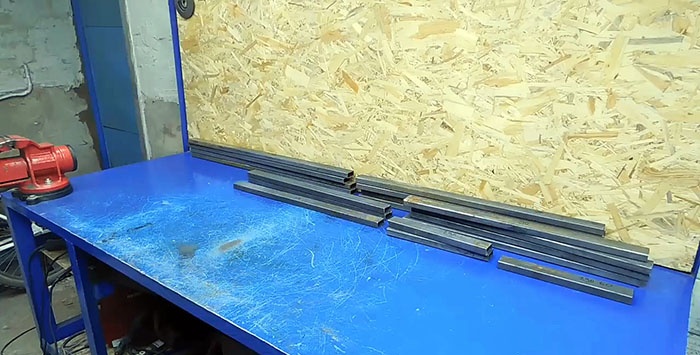
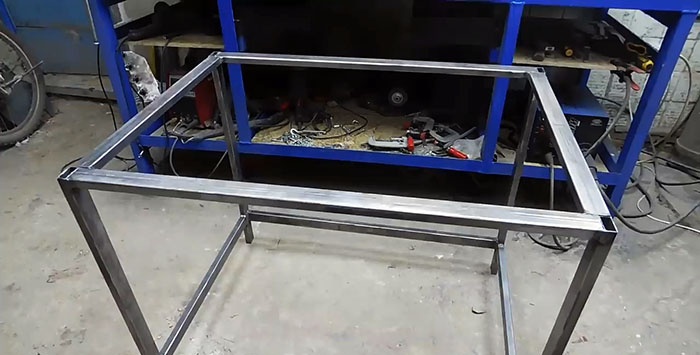
Separadamente, soldamos um chassi auxiliar ao quadro principal sob o tampo da mesa, ao qual será fixado e ajustado o motor elétrico.
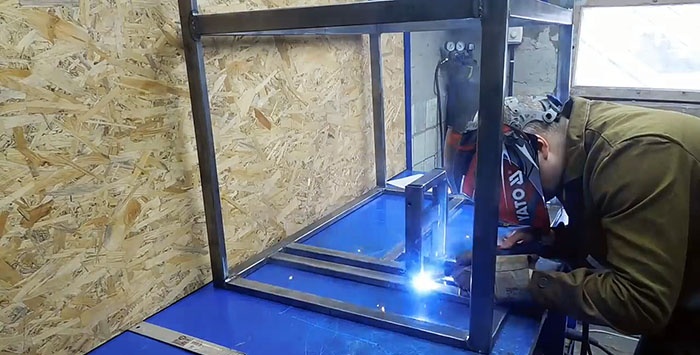
Com uma esmerilhadeira, recortamos duas partes simétricas de uma placa de metal de 6 mm de espessura que, soldadas e fixadas no tampo da mesa, se tornarão uma espécie de suporte da lâmina do rachador de madeira.
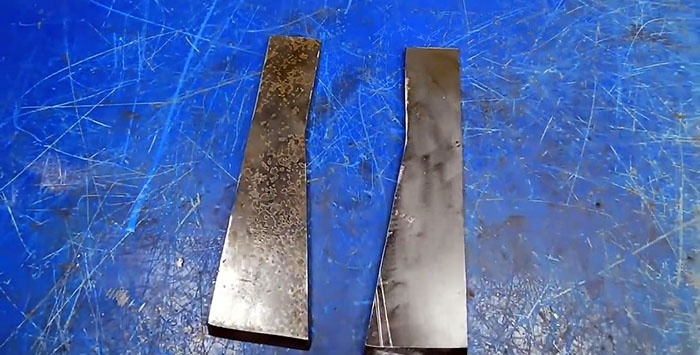
Como a carga em nosso dispositivo muda constantemente, não podemos ficar sem um volante. No nosso caso, em termos de tamanho e peso, o volante mais adequado foi o GAZ-53 com diâmetro externo de 372 mm, furo de montagem de 40 mm e peso de quase 16 kg.
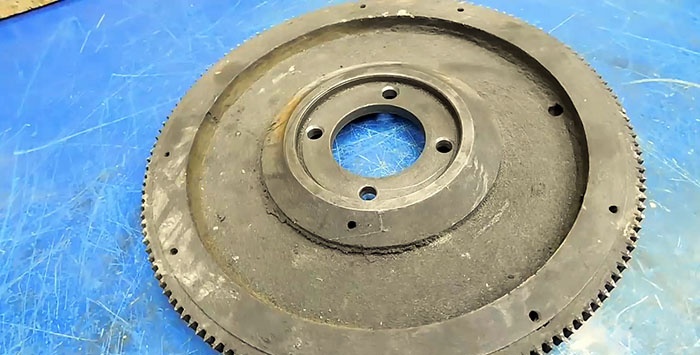
Removemos o anel de engrenagem desta peça e limpamos a sujeira oleosa de muitos anos usando um martelo, uma chave de fenda e um moedor com acessórios.
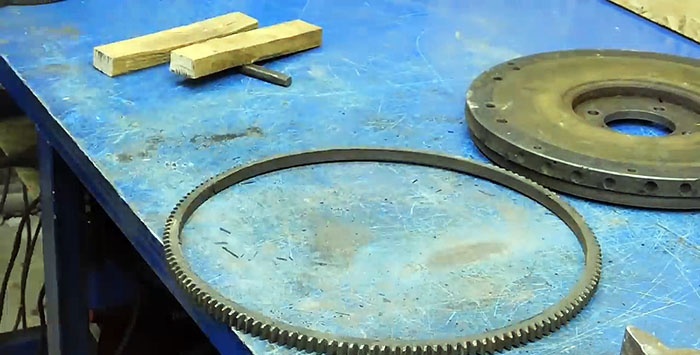
Realizamos o balanceamento estático do eixo e do volante aparafusando-os com parafusos e porcas. Devido à falta de uma máquina de balanceamento, criamos uma usando apenas os recursos disponíveis.
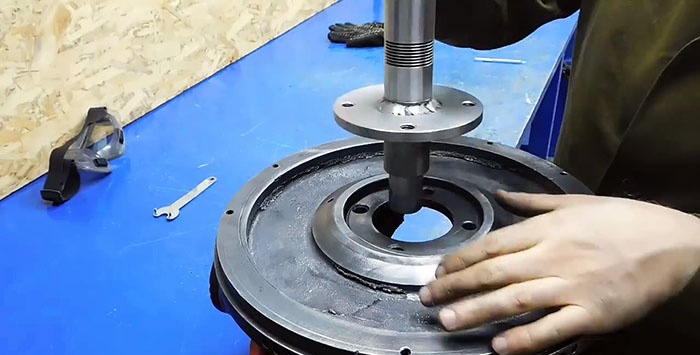
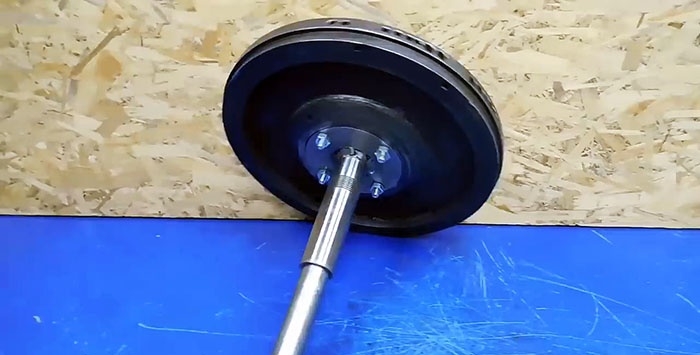
Para fazer isso, coloque temporariamente dois cantos paralelos à moldura da mesa e segure-os levemente. Usando um nível, garantimos que os cantos fiquem o mais planos possíveis e colocamos o eixo com o volante sobre eles.
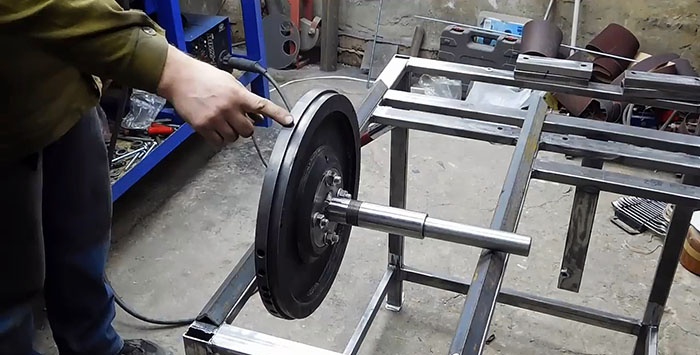
Damos rotação ao volante e monitoramos o momento de parada. Se houver uma massa desequilibrada, ela irá recuar um pouco antes de parar. Além disso, o excesso de massa estará no ponto mais baixo.Marcamos este local e fazemos um furo, retirando assim o excesso de massa.
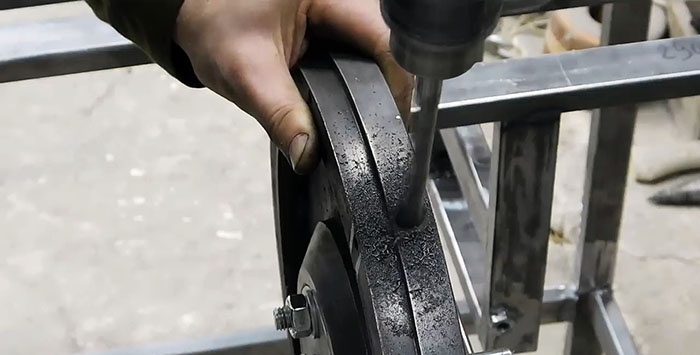
O balanceamento será considerado completo quando o eixo e o volante não rolarem para trás antes de parar.
Por segurança, fazemos uma capa protetora para o volante com os restos do tubo perfilado e da chapa e cozinhamos o tampo da mesa.
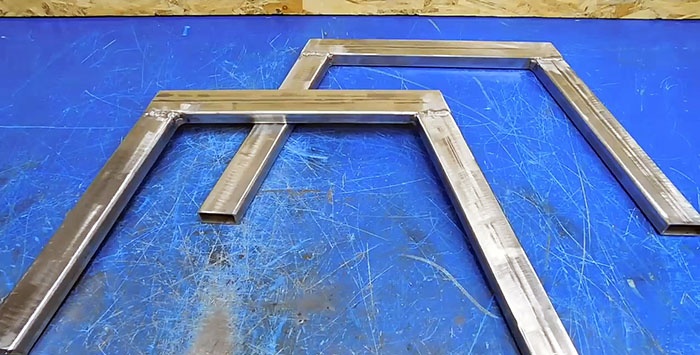
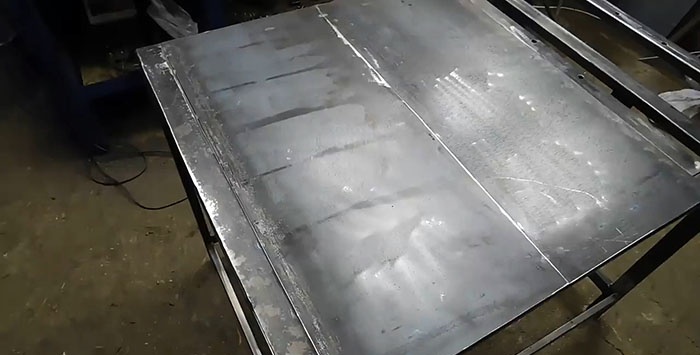
Conectamos duas peças simétricas em ângulo, colocamos um espaçador dentro e soldamos o conjunto resultante ao tampo da mesa.
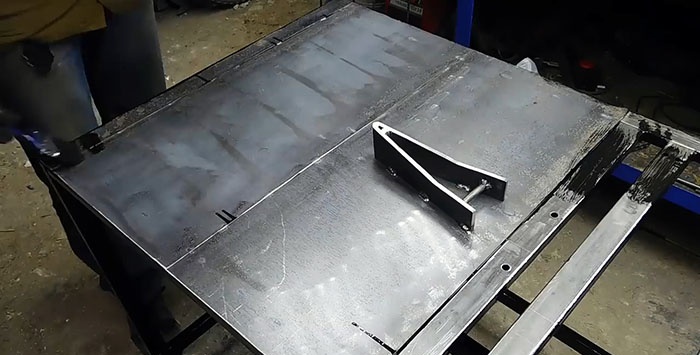
Todos os componentes e peças já foram feitos, então começamos a pintá-los com um pincel comum.
Vamos estimar quanto nos custará um rachador de lenha caseiro:
O total é de cerca de 7 mil rublos. Isso é 3 vezes menos do que o divisor de madeira de fábrica mais barato.
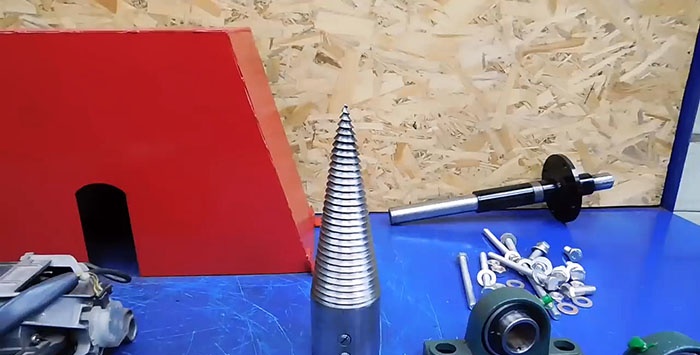
Aparafusamos firmemente o volante ao eixo, colocamos a correia, as unidades de rolamento e fixamos a unidade na estrutura.
Instalamos e fixamos a “cenoura” na extremidade do eixo com dois pinos especiais.
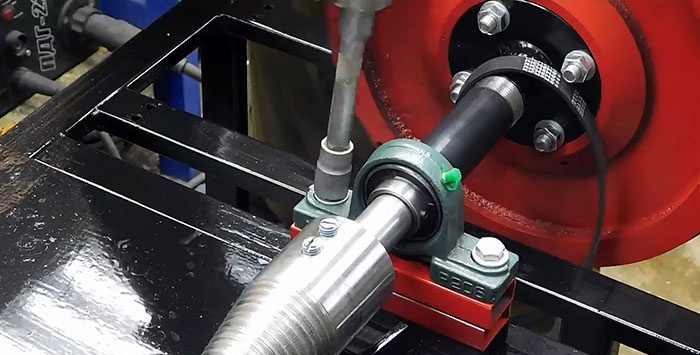
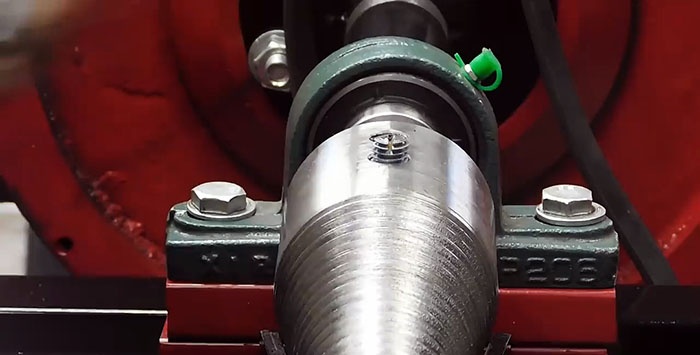
Apertamos a correia apertando o parafuso destinado a esse fim que, apoiado no suporte, movimenta o motor e tensiona a correia.
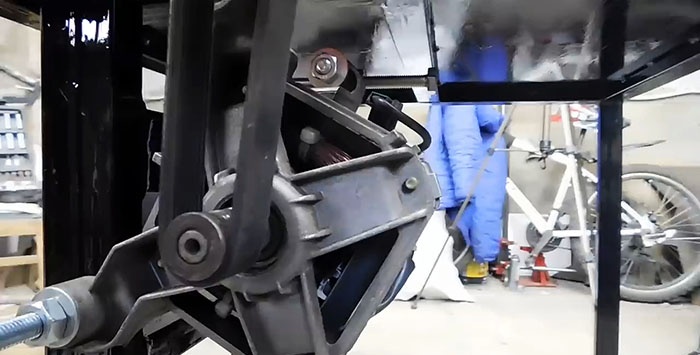
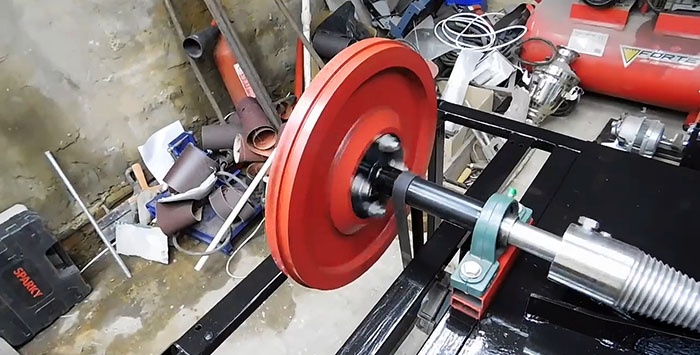
A parte elétrica consiste em um cabo de alimentação, um interruptor e um regulador de tensão do moedor. O sistema de conexão é bastante padrão.
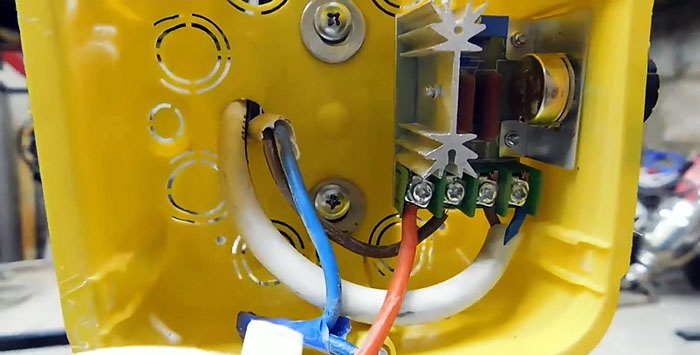
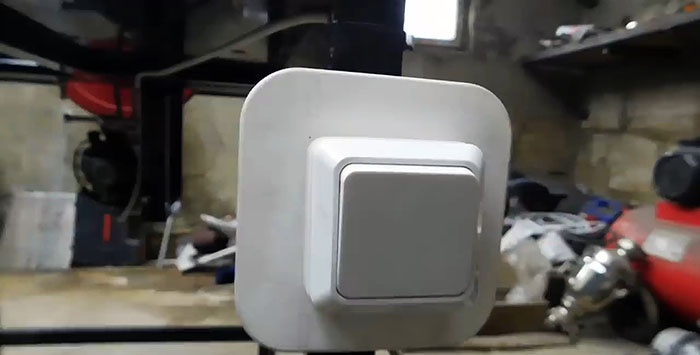
Na partida, a presença de um regulador elimina solavancos e garante um aumento suave da velocidade pelo volante. Isto é muito importante porque a correia não escorrega nas ranhuras, o que significa que durará mais.
Além disso, graças ao regulador de tensão, você pode alterar a potência, o que sem carga leva imediatamente a um aumento na velocidade.
Instalamos uma capa protetora no volante para proteger a nós mesmos e às pessoas próximas contra ferimentos se o volante sair repentinamente do eixo ou rachar.
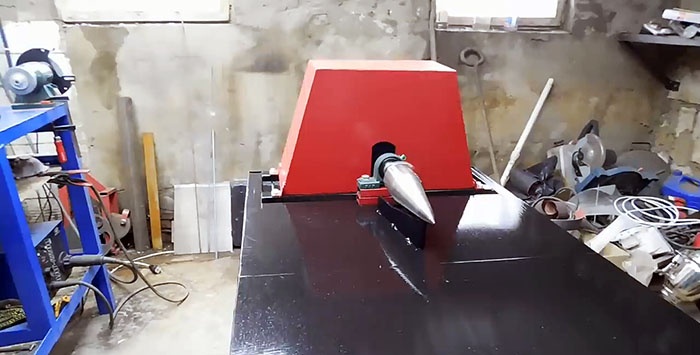
Primeiro, vamos tentar dividir um pequeno pedaço de tabuleiro. Nosso produto caseiro lida com isso sem esforço. O mesmo acontece com toras secas que foram armazenadas sob um dossel.O rachador de lenha lida com um toco bastante grande sem qualquer estresse.
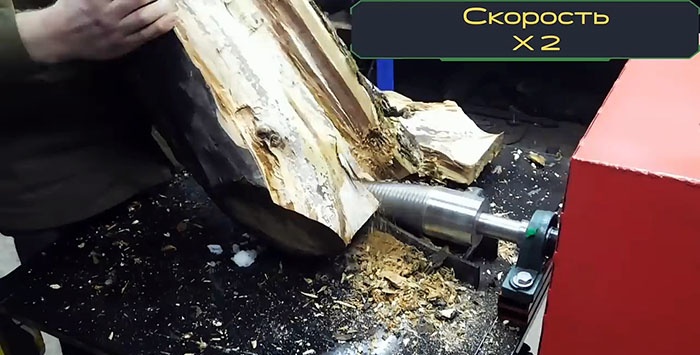
Se de repente a “cenoura” ficar presa em uma tora, então desligando a energia, usando a chave e girando a parte traseira do eixo, podemos facilmente liberar o elemento de trabalho da tora em que está preso.
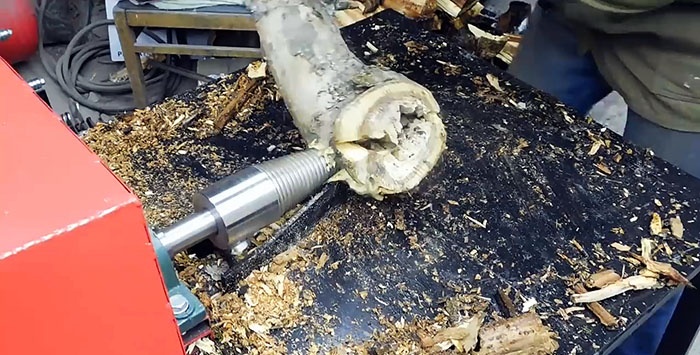
Mesmo esta pequena prática mostrou que a fixação da “cenoura” no eixo deveria ser recuada para não interferir no corte da lenha, e a mesa deveria ficar sobre uma superfície absolutamente horizontal. Isso eliminará até mesmo pequenas vibrações durante a operação do rachador de madeira.
Além disso, você não pode trabalhar nesta unidade com luvas e mitenes, e as mangas das roupas não devem ser muito longas e sem cadarços, cintos e outros elementos pendurados, para que não se torçam em forma de “cenoura” e machuquem suas mãos.
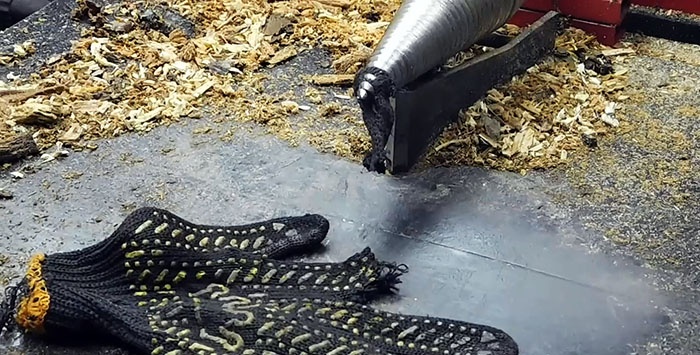
Mas a experiência dos artesãos mostra que, mesmo sem conhecimento de torneamento, é possível fazer um cutelo mecânico a partir de sucata, adaptando-o ao local, quantidade de trabalho e dados antropométricos.
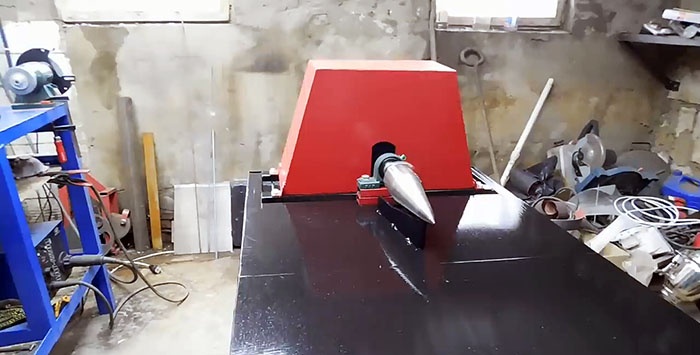
Vai precisar
Em princípio, quase todos os materiais e componentes para a montagem de um cutelo mecânico podem ser retirados de carros antigos, eletrodomésticos e encontrados em aterros sanitários. Mas não custa saber quanto custa esta ou aquela “coisa” na loja, quanto custará o motor de uma máquina de lavar velha, quanto o torneiro cobrará pela obra, etc.
Então, o que devemos estocar se decidirmos fazer um cutelo mecânico:
- aço laminado redondo (madeira redonda);
- fita adesiva;
- chapas metálicas de diferentes espessuras;
- tubo perfilado com cerca de 14 m;
- volante do GAZ-53;
- parafusos, porcas, arruelas;
- motor com polia e correia;
- tinta e pincel;
- cutelo de cenoura com parafuso cônico.
Das ferramentas e equipamentos que devemos ter em mãos:
- moedor com discos;
- cortador de plasma;
- lima metálica;
- equipamento de solda;
- tornos e pinças;
- furar com brocas.
Fabricação de componentes e peças do rachador de madeira
Fixamos a madeira redonda em um torno e marcamos os locais de corte com fita adesiva para garantir de forma rápida e fácil a precisão necessária.
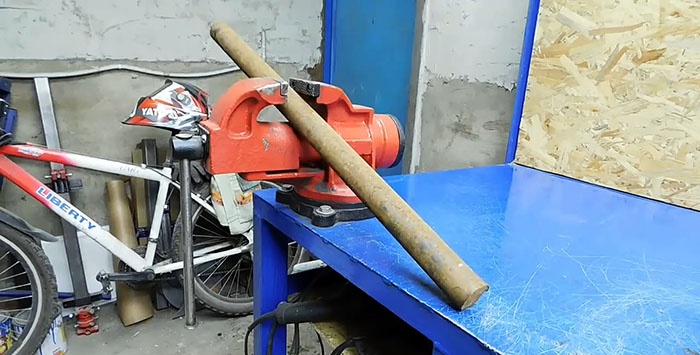
De acordo com as marcações, recortamos o blank do eixo do rachador de madeira com uma esmerilhadeira e um disco de corte de 180 mm.
Marcamos a superfície de uma chapa grossa de metal com dois discos de tamanhos diferentes, mas com furos centrais idênticos.
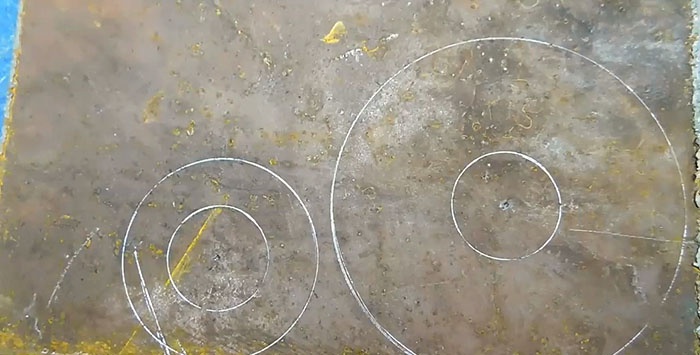
É mais conveniente e preciso cortá-los com um cortador de plasma e, como resultado, a quantidade de processamento subsequente é minimizada.
Levamos os discos ao tamanho desejado com uma lima e uma esmerilhadeira e, para não retirar o excesso de metal, colamos padrões precisos de fita ou papel nas superfícies laterais.
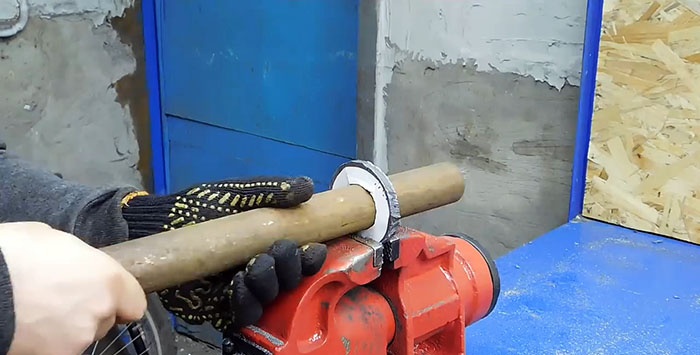
Ao processar discos, prestamos atenção principal aos furos centrais: a peça do eixo deve caber livremente neles, mas as folgas devem ser mínimas.
Esta operação é uma das mais importantes: soldamos um grande disco exatamente a 90 graus na madeira redonda. Por isso, realizamos a soldagem com cuidado, verificando constantemente o ângulo entre as peças para que não se movam, e utilizamos quadrados magnéticos. Limpamos as soldas.
O segundo anel é mais fácil de instalar. Basta pressioná-lo bem e fixá-lo no primeiro disco com pinças e soldá-lo nesta posição.
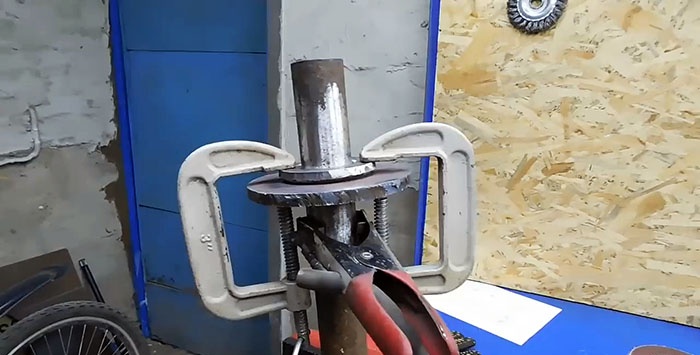
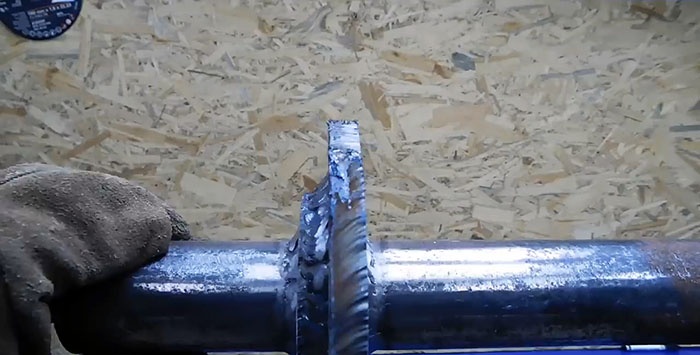
Agora o torneiro trabalhará na peça de trabalho: ele girará o suporte frontal, que é soldado ao anel menor, retificará as superfícies circulares no tamanho certo e fará uma série de ranhuras para a correia de transmissão.
A partir de um tubo perfilado cortamos blanks nos tamanhos e quantidades necessários, dos quais soldamos não apenas uma mesa, mas também uma base para a instalação de unidades montadas.
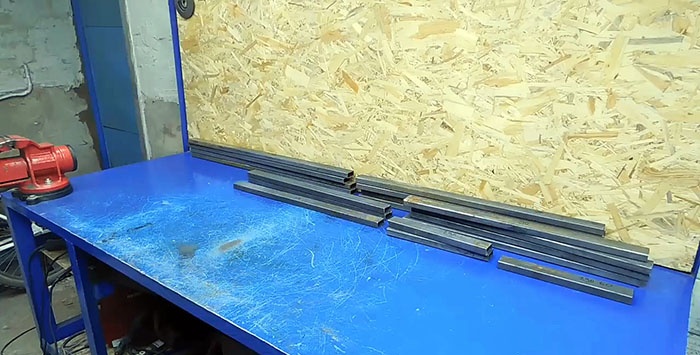
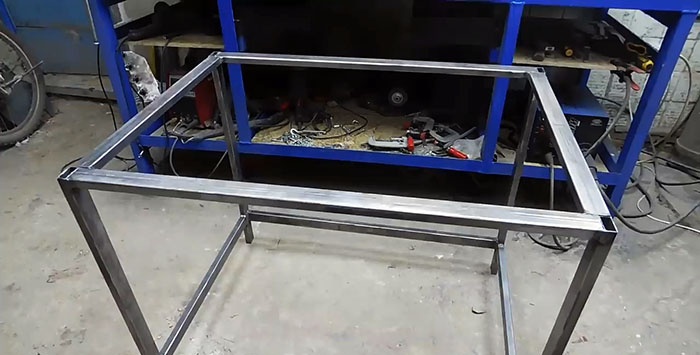
Separadamente, soldamos um chassi auxiliar ao quadro principal sob o tampo da mesa, ao qual será fixado e ajustado o motor elétrico.
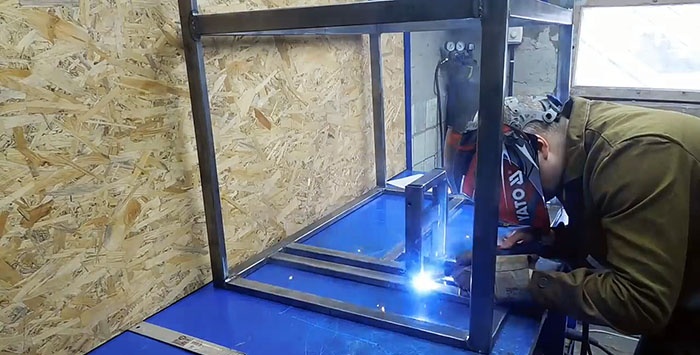
Com uma esmerilhadeira, recortamos duas partes simétricas de uma placa de metal de 6 mm de espessura que, soldadas e fixadas no tampo da mesa, se tornarão uma espécie de suporte da lâmina do rachador de madeira.
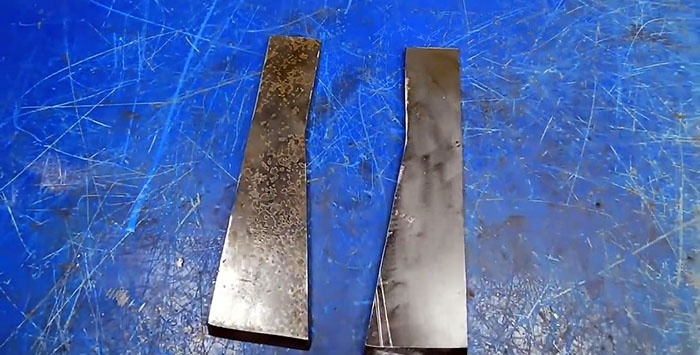
Como a carga em nosso dispositivo muda constantemente, não podemos ficar sem um volante. No nosso caso, em termos de tamanho e peso, o volante mais adequado foi o GAZ-53 com diâmetro externo de 372 mm, furo de montagem de 40 mm e peso de quase 16 kg.
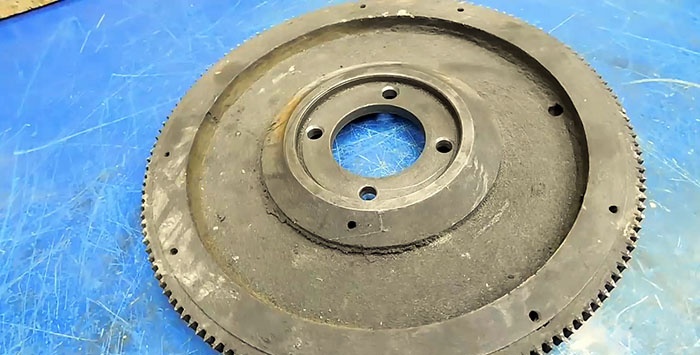
Removemos o anel de engrenagem desta peça e limpamos a sujeira oleosa de muitos anos usando um martelo, uma chave de fenda e um moedor com acessórios.
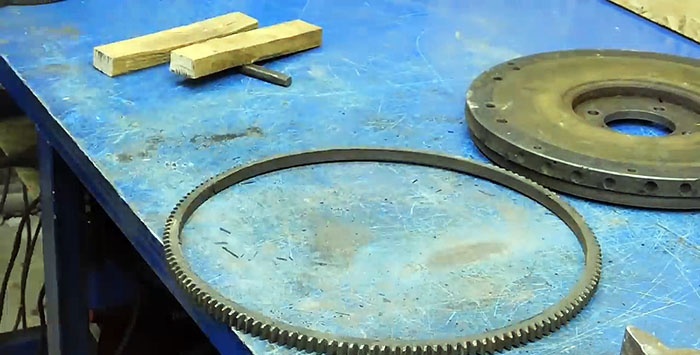
Realizamos o balanceamento estático do eixo e do volante aparafusando-os com parafusos e porcas. Devido à falta de uma máquina de balanceamento, criamos uma usando apenas os recursos disponíveis.
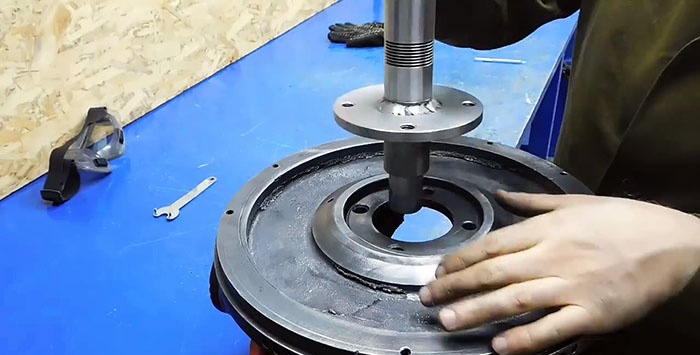
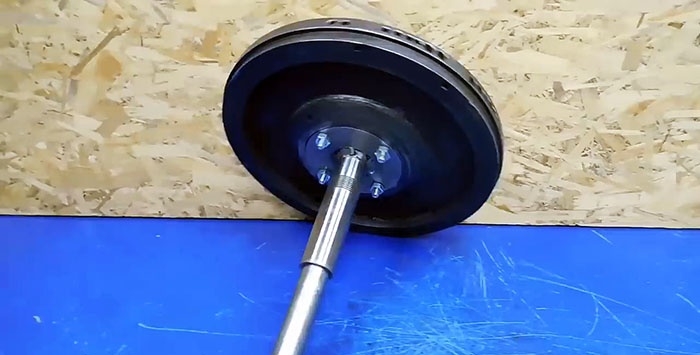
Para fazer isso, coloque temporariamente dois cantos paralelos à moldura da mesa e segure-os levemente. Usando um nível, garantimos que os cantos fiquem o mais planos possíveis e colocamos o eixo com o volante sobre eles.
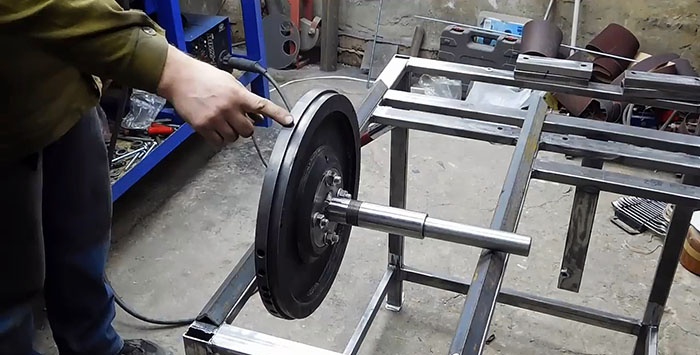
Damos rotação ao volante e monitoramos o momento de parada. Se houver uma massa desequilibrada, ela irá recuar um pouco antes de parar. Além disso, o excesso de massa estará no ponto mais baixo.Marcamos este local e fazemos um furo, retirando assim o excesso de massa.
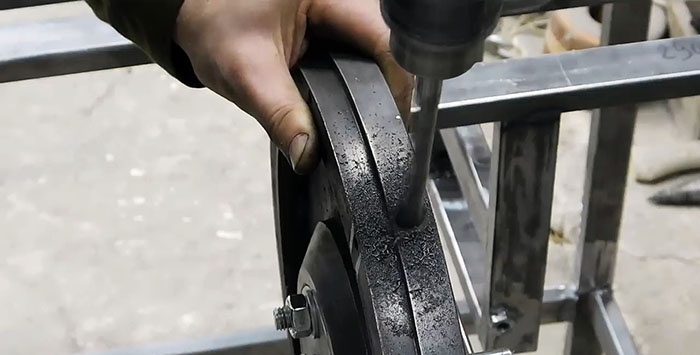
O balanceamento será considerado completo quando o eixo e o volante não rolarem para trás antes de parar.
Por segurança, fazemos uma capa protetora para o volante com os restos do tubo perfilado e da chapa e cozinhamos o tampo da mesa.
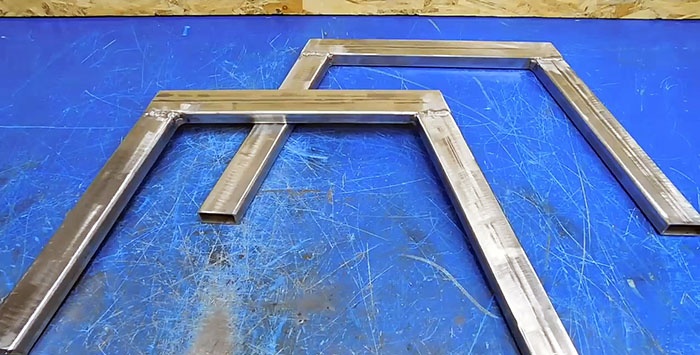
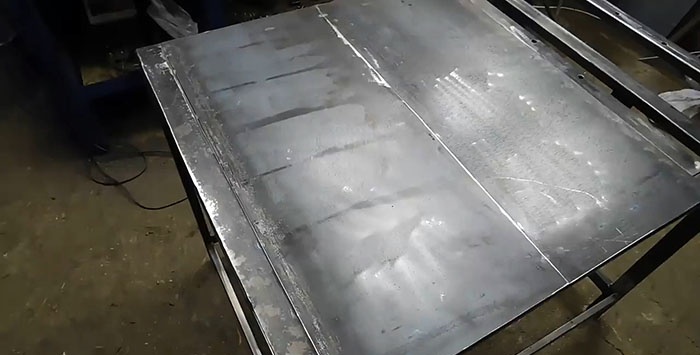
Conectamos duas peças simétricas em ângulo, colocamos um espaçador dentro e soldamos o conjunto resultante ao tampo da mesa.
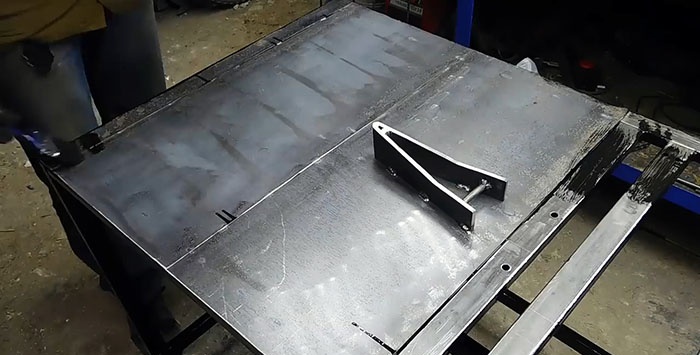
Todos os componentes e peças já foram feitos, então começamos a pintá-los com um pincel comum.
Custos aproximados
Vamos estimar quanto nos custará um rachador de lenha caseiro:
- volante – 1200 rublos;
- tubo de perfil 14 m – 1200 rublos;
- motor da máquina de lavar (730 W, 8 mil rpm) – 530 rublos;
- “cenoura” (diâmetro da base – 70 mm, altura – 250 mm) – 1300 rublos;
- dois rolamentos 206 em uma caixa – 600 rublos;
- trabalho de torneiro - 1.650 rublos;
- hardware e correia de transmissão – 530 esfregar.
O total é de cerca de 7 mil rublos. Isso é 3 vezes menos do que o divisor de madeira de fábrica mais barato.
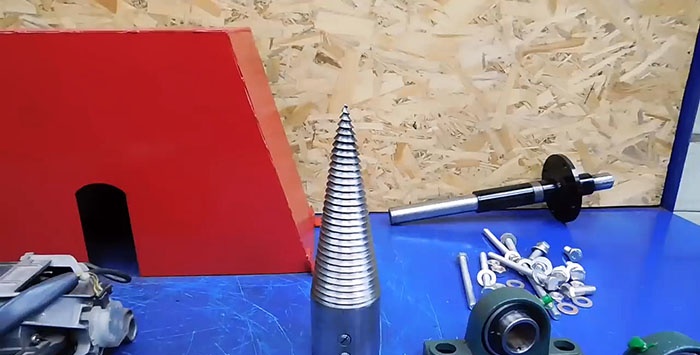
Montagem de componentes e peças do rachador de madeira
Aparafusamos firmemente o volante ao eixo, colocamos a correia, as unidades de rolamento e fixamos a unidade na estrutura.
Instalamos e fixamos a “cenoura” na extremidade do eixo com dois pinos especiais.
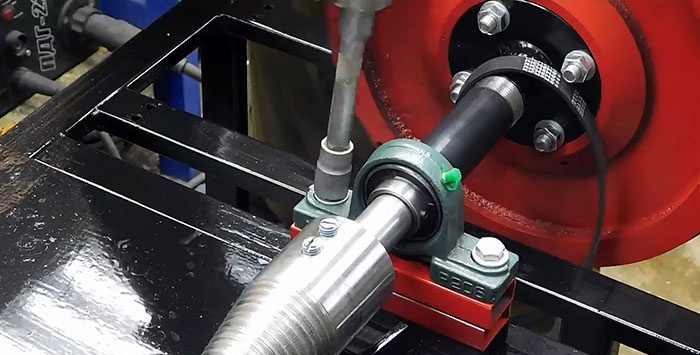
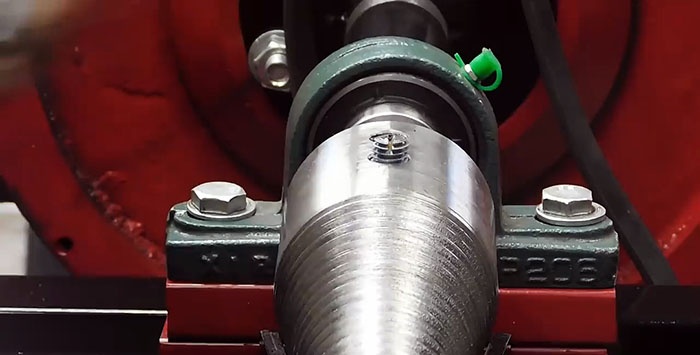
Apertamos a correia apertando o parafuso destinado a esse fim que, apoiado no suporte, movimenta o motor e tensiona a correia.
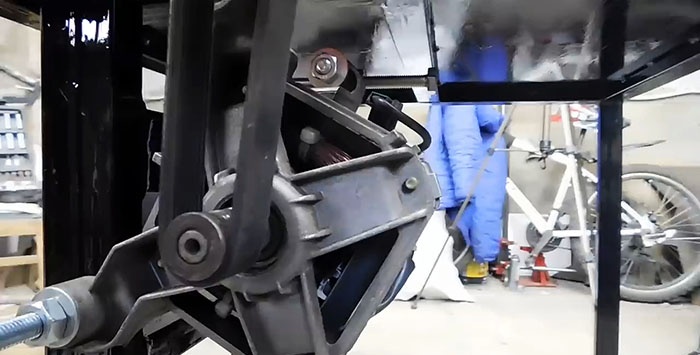
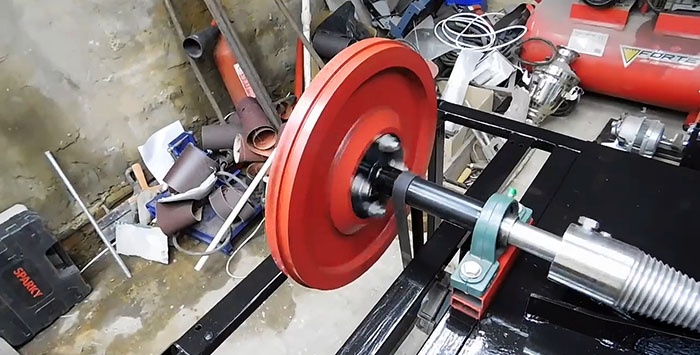
A parte elétrica consiste em um cabo de alimentação, um interruptor e um regulador de tensão do moedor. O sistema de conexão é bastante padrão.
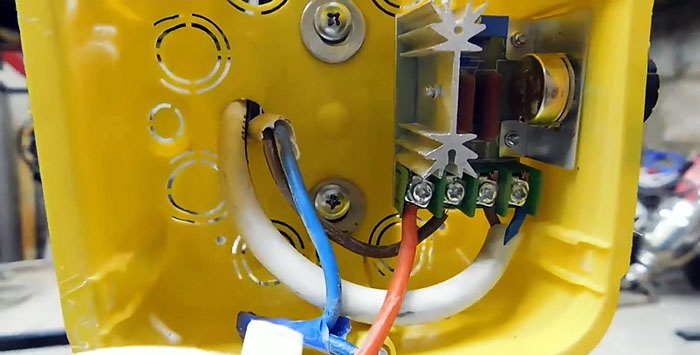
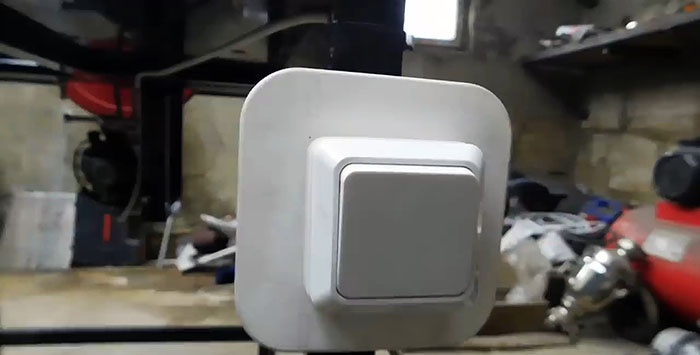
Na partida, a presença de um regulador elimina solavancos e garante um aumento suave da velocidade pelo volante. Isto é muito importante porque a correia não escorrega nas ranhuras, o que significa que durará mais.
Além disso, graças ao regulador de tensão, você pode alterar a potência, o que sem carga leva imediatamente a um aumento na velocidade.
Instalamos uma capa protetora no volante para proteger a nós mesmos e às pessoas próximas contra ferimentos se o volante sair repentinamente do eixo ou rachar.
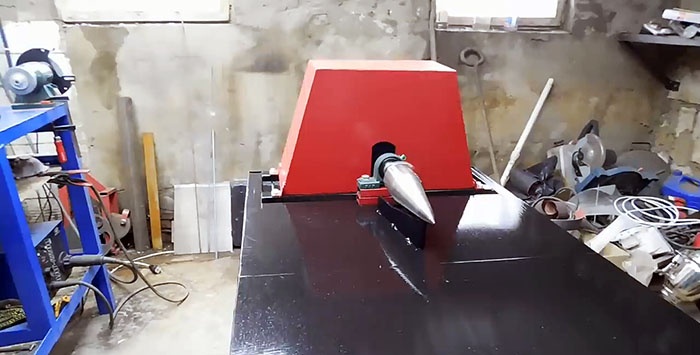
Testando um divisor de madeira em ação
Primeiro, vamos tentar dividir um pequeno pedaço de tabuleiro. Nosso produto caseiro lida com isso sem esforço. O mesmo acontece com toras secas que foram armazenadas sob um dossel.O rachador de lenha lida com um toco bastante grande sem qualquer estresse.
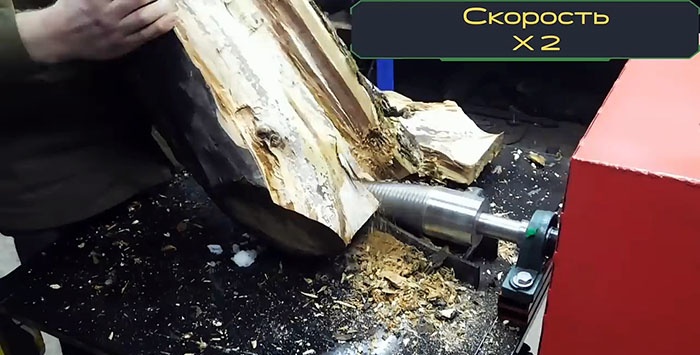
Se de repente a “cenoura” ficar presa em uma tora, então desligando a energia, usando a chave e girando a parte traseira do eixo, podemos facilmente liberar o elemento de trabalho da tora em que está preso.
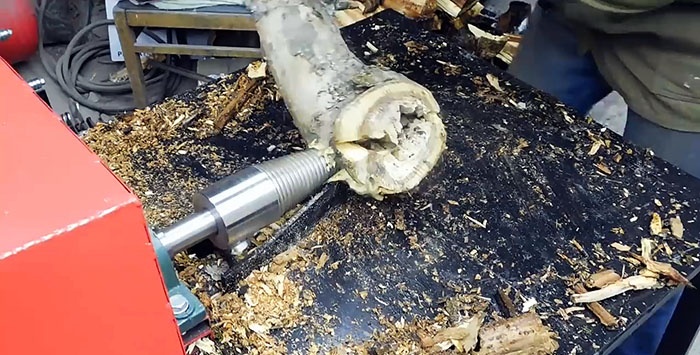
Mesmo esta pequena prática mostrou que a fixação da “cenoura” no eixo deveria ser recuada para não interferir no corte da lenha, e a mesa deveria ficar sobre uma superfície absolutamente horizontal. Isso eliminará até mesmo pequenas vibrações durante a operação do rachador de madeira.
Além disso, você não pode trabalhar nesta unidade com luvas e mitenes, e as mangas das roupas não devem ser muito longas e sem cadarços, cintos e outros elementos pendurados, para que não se torçam em forma de “cenoura” e machuquem suas mãos.
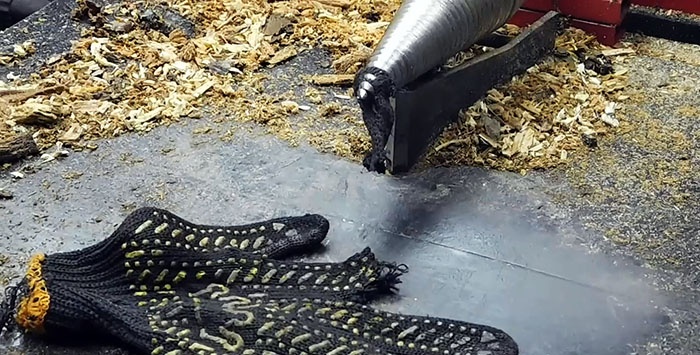
Assista o vídeo
Master classes semelhantes
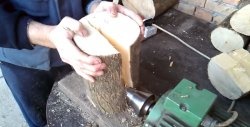
Projeto e princípio de funcionamento de um rachador de madeira aparafusado
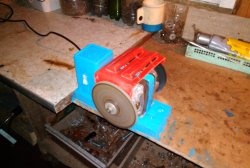
Afiador de motor de máquina de lavar
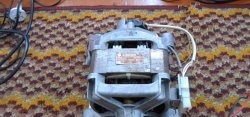
Como conectar o motor de uma máquina de lavar a 220 V
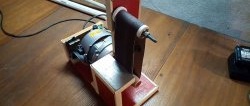
O moedor mais simples sem soldar e girar do motor de uma máquina de lavar
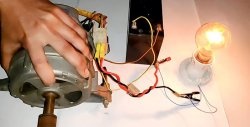
Como transformar o motor de uma máquina de lavar em um gerador de 220 V
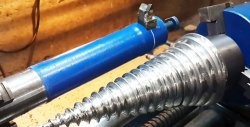
Como fazer um rachador de toras “cenoura” na garagem
Particularmente interessante
Comentários (0)