Dobrador de tubos faça você mesmo - simples e quase grátis
A necessidade de dobrar um tubo de aço em um determinado ângulo com o raio desejado não surge com muita frequência. Mas, se tal tarefa surgir, então, na ausência de equipamento especial, ela inevitavelmente se tornará um problema difícil de resolver.
No caso de tubos redondos, às vezes os acessórios ajudam. Não existem tais soluções para tubos retangulares e quadrados. Somente montagem aparafusada é oferecida.
Dobrar um tubo soldando-o em segmentos separados não é a melhor saída para a situação. É difícil e geralmente não confiável.
A opção mais avançada tecnologicamente e comprovada há décadas foi e continua sendo um dobrador de tubos, que permite dobrar um tubo de qualquer seção transversal sem comprometer suas características de qualidade e desempenho.
Você pode fazer uma máquina tão compacta com acionamento mecânico com suas próprias mãos. Vai dar um pouco de trabalho, mas vale a pena. Você não conseguirá comprar um dobrador de tubos barato. O preço mínimo nas lojas para um dispositivo que parece mais ou menos valioso começa em vários milhares de rublos. Ao mesmo tempo, só podemos adivinhar sua qualidade e vida útil.
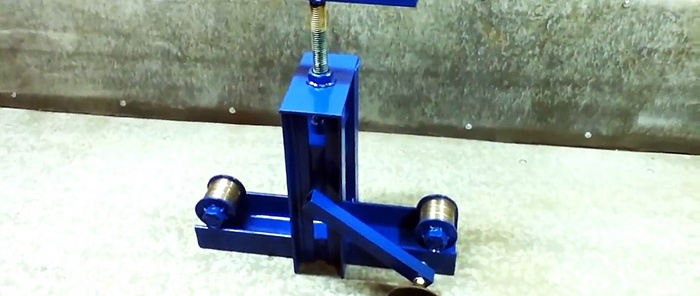
Uma máquina caseira será composta por pelo menos 50% dos materiais disponíveis. Definitivamente, algo será encontrado em residências particulares, algo nas garagens dos vizinhos. Muito provavelmente você só precisará comprar 8 rolamentos da série 303. Eles são projetados para desempenhar a função de eixos, o que elimina a necessidade de trabalhos de torneamento. Esses rolamentos são baratos e, se você olhar, poderá encontrá-los por alguns centavos. Se você precisar comprar algum ferro adicional, não será quase nada comparado ao preço de loja de um dobrador de tubos.
Definitivamente, você precisará de uma seção de canal de 80x40 mm, um ângulo de aço de 25x25 mm, um tubo de perfil de 20x20 mm, um pino de construção com diâmetro de 18 mm, 6 arruelas M18 com diâmetro externo aumentado de 56 mm, 9 porcas para 18 e algumas outras pequenas coisas, mas mais sobre isso no processo.
As principais ferramentas são uma retificadora, uma máquina de solda e uma furadeira.
1. Tomamos como base para o desenho um canal de 80x40 mm, marcamos e cortamos uma peça com aproximadamente 40 cm de comprimento.
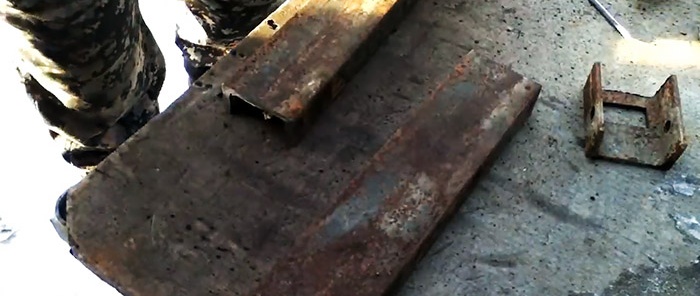
2. Limpe com uma escova de metal.
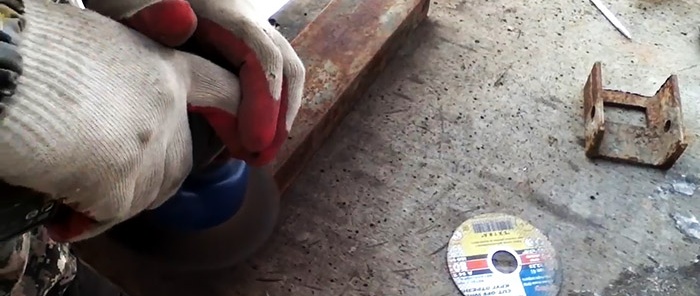
3. Use uma esmerilhadeira para remover parcialmente a rosca do pino, de modo que os rolamentos, cujo diâmetro interno é de 17 mm, se encaixem nele com folga, mas com firmeza.
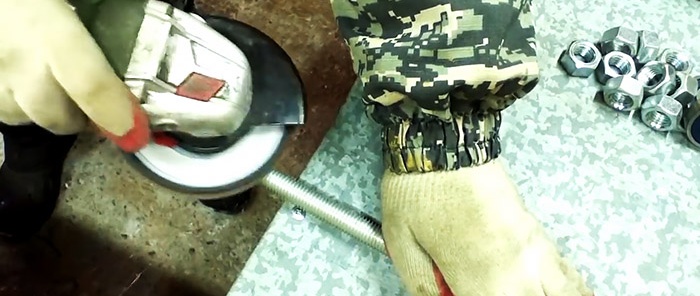
4. Usando uma serra circular ou esmerilhadeira, corte três seções do pino - elas serão usadas para fazer rolos. Tomamos o comprimento dos segmentos com margem (aproximadamente 100-120 mm), levando em consideração a largura das arruelas, rolamentos e porcas. Retiraremos o excesso mais tarde.
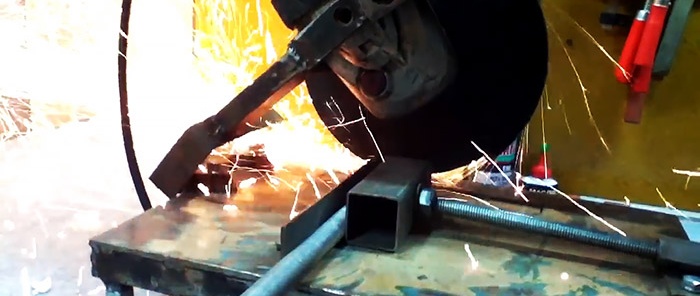
5. Usando um mandril e um martelo, ajuste uma leve conicidade para as arruelas - dentro de 1 mm, o que garantirá a rotação livre dos rolos.
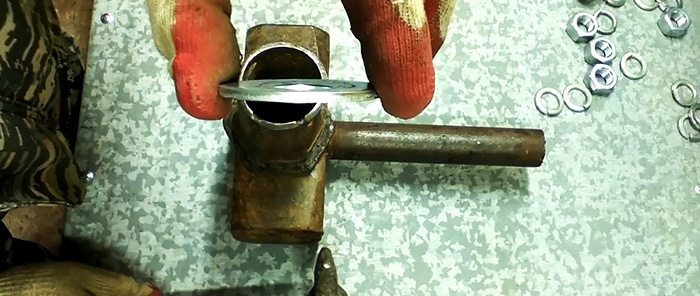
6. Monte o rolo e aperte as porcas.
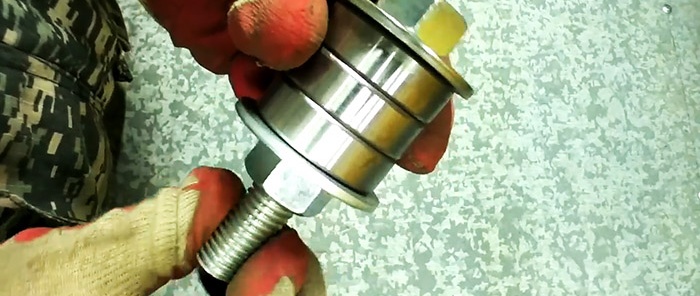
7. Remova a parte do pino que se projeta além da porca.
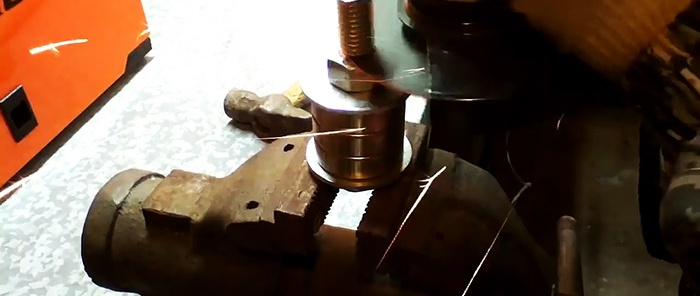
8. Usando soldagem elétrica, fixamos os elementos do rolo.
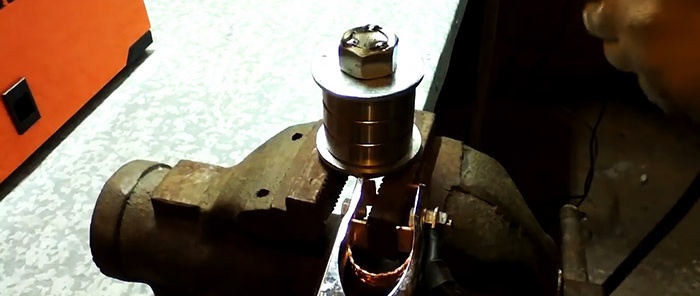
9. Verifique se o rolo gira livremente.
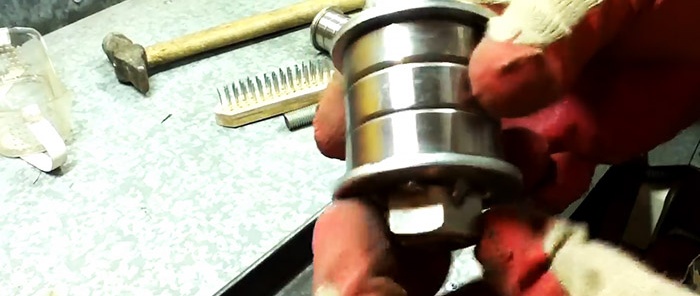
10.Marcamos e cortamos quatro segmentos de 25 cm de comprimento de um canto de 25x25 mm para fazer guias para os rolos de acionamento e pressão.
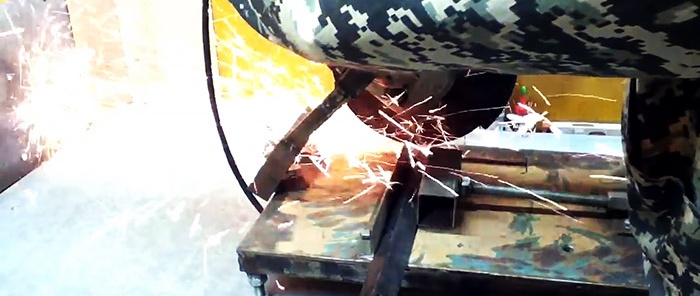
11. Soldamos os pedaços de cantos na base do canal, mantendo uma folga para o eixo do rolo de acionamento (eixo).
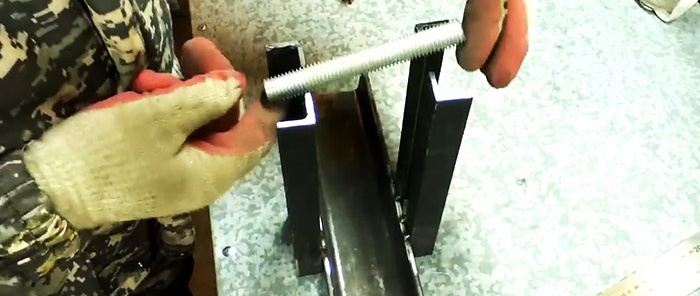
12. Em uma das partes já preparadas do pino colocamos um pedaço de tubo com diâmetro de 27 mm e comprimento de 40 mm. Preencha a lacuna interna com pregos de 40 mm sem cabeça.
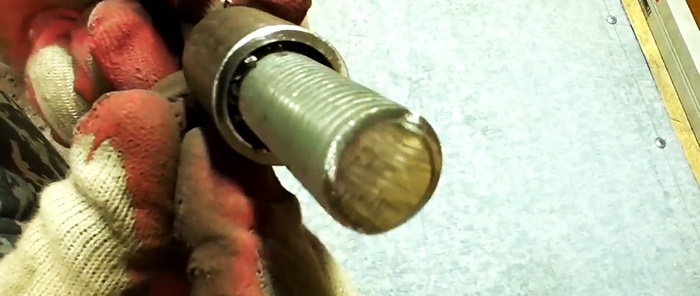
13. Soldamos todos os elementos ao redor da circunferência por meio de soldagem elétrica e obtemos um eixo acabado.
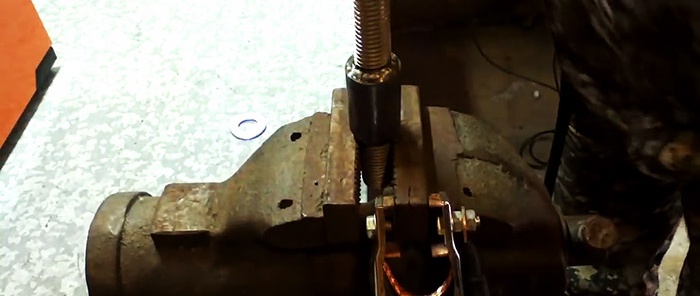
14. Colocamos rolamentos nas bordas do eixo.
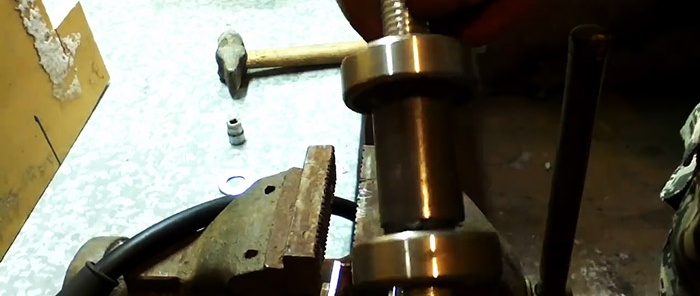
15. Fazemos um carro móvel soldando duas seções de um tubo perfilado 20x40x30 mm, uma placa de aço retangular 80x50 mm e um eixo com rolamentos em uma única estrutura.
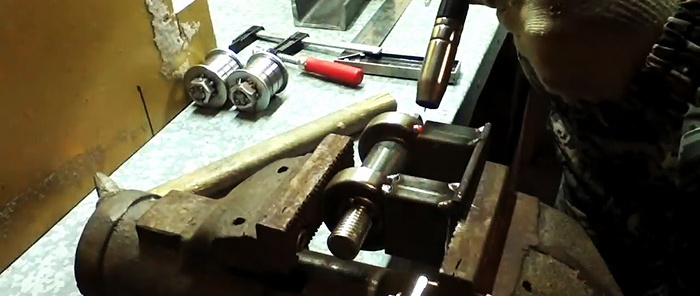
16. Na intersecção das diagonais, marque o centro com um núcleo e faça um furo com diâmetro de 18 mm para o pino na parte superior do carro usando uma broca e um alargador.
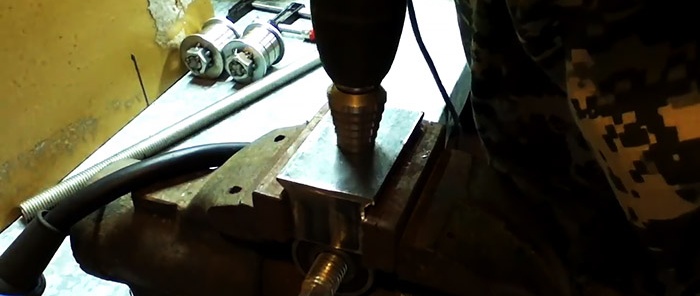
17. Montamos o mecanismo de elevação, composto por um pino e três porcas M18, duas das quais soldadas por pontos ao pino rosqueado no orifício da plataforma do carro.
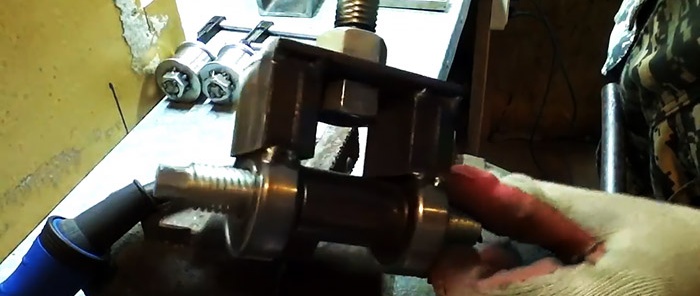
18. Recorte um retângulo de aproximadamente 70x130 mm de uma chapa de aço de 5 mm de espessura, que servirá de batente para o mecanismo de elevação. Marque o meio e faça um furo de 18 mm semelhante à base do carro.
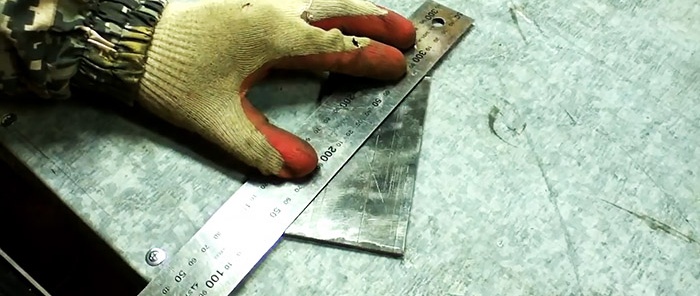
19. Montamos os elementos fabricados em uma única estrutura. Para isso, instale o carro com o eixo de transmissão nas guias.
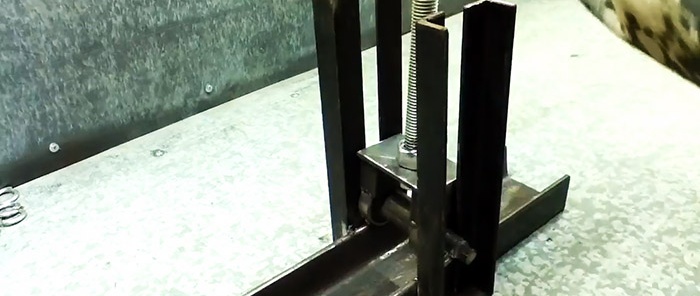
20. Colocamos no pino e instalamos a placa de suporte.
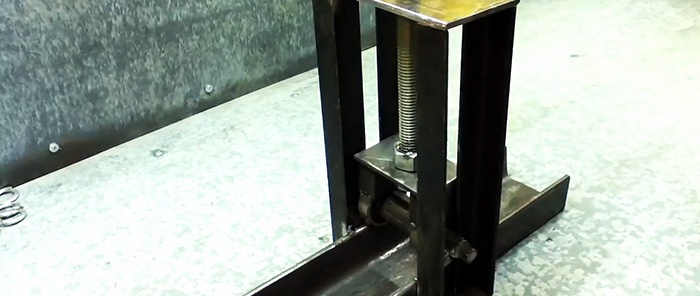
21. Aparafuse a porca no pino até parar e aperte as juntas com solda elétrica.
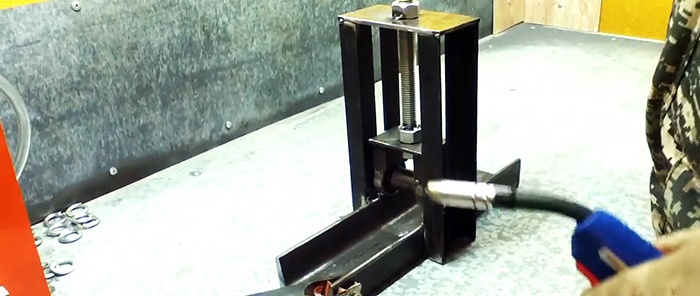
22. Soldamos os rolos previamente confeccionados ao longo das bordas da base do canal.
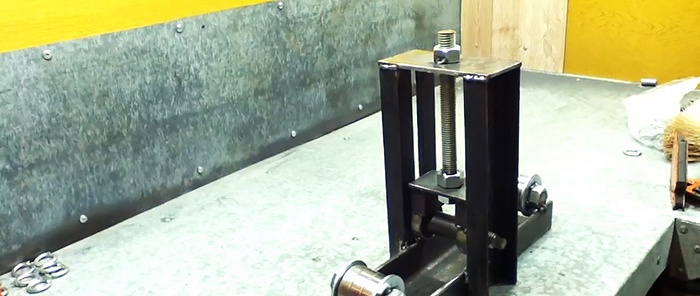
23. Soldamos uma alça de 25-30 cm de um tubo perfilado de 20x20 mm ao mecanismo de elevação e fixação.
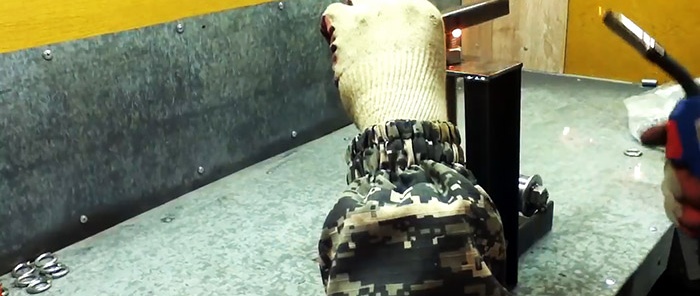
24.Fazemos uma alavanca de acionamento mecânico a partir de uma seção de 20-25 cm de um tubo perfilado de 20x20 mm e soldamos ao rolo de acionamento (pino). A alça de acionamento pode ser emprestada de qualquer ferramenta elétrica antiga, primeiro fazendo um furo para ela. Se não estiver disponível, você pode soldar um pedaço de tubo redondo de 12 a 14 cm na alavanca.

25. O dobrador de tubos está pronto, vamos fazer o teste.
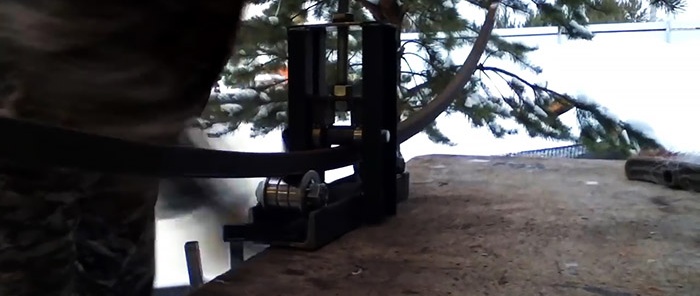
26. E por fim, a última etapa é pintar nosso dobrador de tubos. Como pode uma obra-prima técnica tão montada à mão não ter uma aparência respeitável?
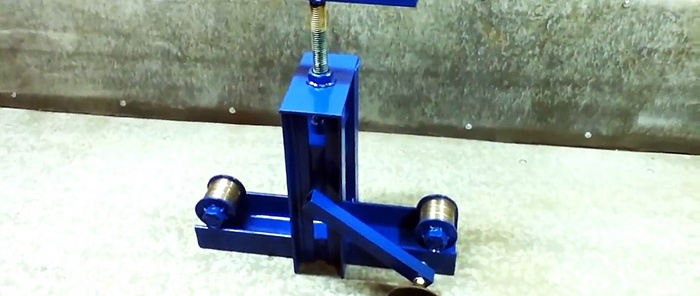
No entanto, esta é uma questão puramente individual e não nos deteremos nela em detalhes. Observamos apenas que primeiro é necessário remover toda a rugosidade com uma lima ou esmeril, desengordurar bem com solvente e cobrir com primer. Mas em qualquer caso, embora agrade à alma, não afeta em nada o resultado.
No caso de tubos redondos, às vezes os acessórios ajudam. Não existem tais soluções para tubos retangulares e quadrados. Somente montagem aparafusada é oferecida.
Dobrar um tubo soldando-o em segmentos separados não é a melhor saída para a situação. É difícil e geralmente não confiável.
A opção mais avançada tecnologicamente e comprovada há décadas foi e continua sendo um dobrador de tubos, que permite dobrar um tubo de qualquer seção transversal sem comprometer suas características de qualidade e desempenho.
Você pode fazer uma máquina tão compacta com acionamento mecânico com suas próprias mãos. Vai dar um pouco de trabalho, mas vale a pena. Você não conseguirá comprar um dobrador de tubos barato. O preço mínimo nas lojas para um dispositivo que parece mais ou menos valioso começa em vários milhares de rublos. Ao mesmo tempo, só podemos adivinhar sua qualidade e vida útil.
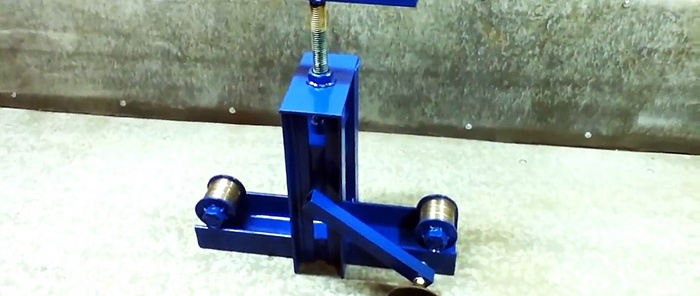
O que você precisa para um dobrador de tubos caseiro
Uma máquina caseira será composta por pelo menos 50% dos materiais disponíveis. Definitivamente, algo será encontrado em residências particulares, algo nas garagens dos vizinhos. Muito provavelmente você só precisará comprar 8 rolamentos da série 303. Eles são projetados para desempenhar a função de eixos, o que elimina a necessidade de trabalhos de torneamento. Esses rolamentos são baratos e, se você olhar, poderá encontrá-los por alguns centavos. Se você precisar comprar algum ferro adicional, não será quase nada comparado ao preço de loja de um dobrador de tubos.
Definitivamente, você precisará de uma seção de canal de 80x40 mm, um ângulo de aço de 25x25 mm, um tubo de perfil de 20x20 mm, um pino de construção com diâmetro de 18 mm, 6 arruelas M18 com diâmetro externo aumentado de 56 mm, 9 porcas para 18 e algumas outras pequenas coisas, mas mais sobre isso no processo.
As principais ferramentas são uma retificadora, uma máquina de solda e uma furadeira.
Ordem de operações
1. Tomamos como base para o desenho um canal de 80x40 mm, marcamos e cortamos uma peça com aproximadamente 40 cm de comprimento.
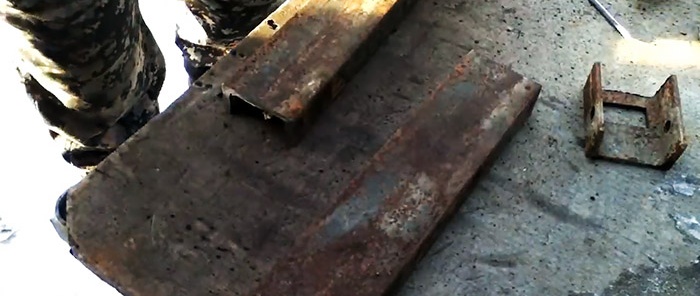
2. Limpe com uma escova de metal.
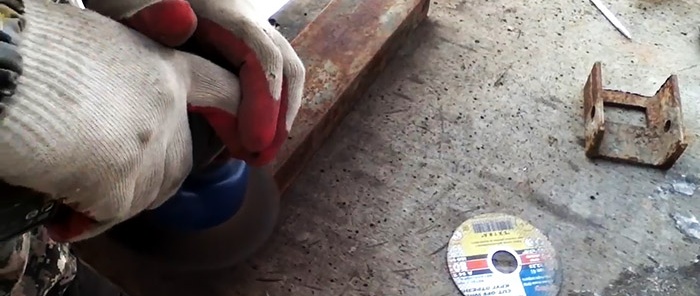
3. Use uma esmerilhadeira para remover parcialmente a rosca do pino, de modo que os rolamentos, cujo diâmetro interno é de 17 mm, se encaixem nele com folga, mas com firmeza.
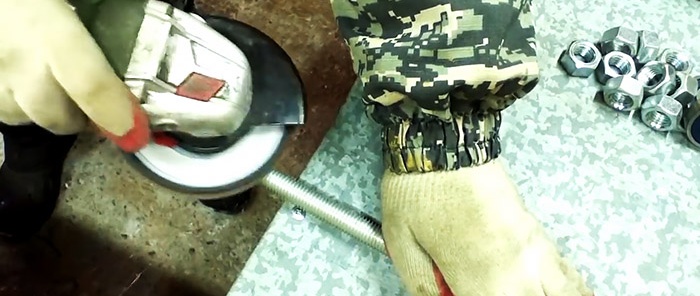
4. Usando uma serra circular ou esmerilhadeira, corte três seções do pino - elas serão usadas para fazer rolos. Tomamos o comprimento dos segmentos com margem (aproximadamente 100-120 mm), levando em consideração a largura das arruelas, rolamentos e porcas. Retiraremos o excesso mais tarde.
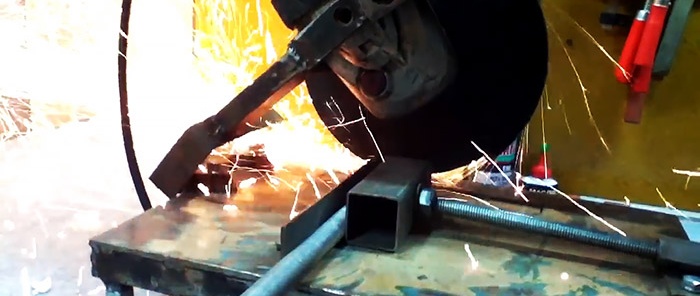
5. Usando um mandril e um martelo, ajuste uma leve conicidade para as arruelas - dentro de 1 mm, o que garantirá a rotação livre dos rolos.
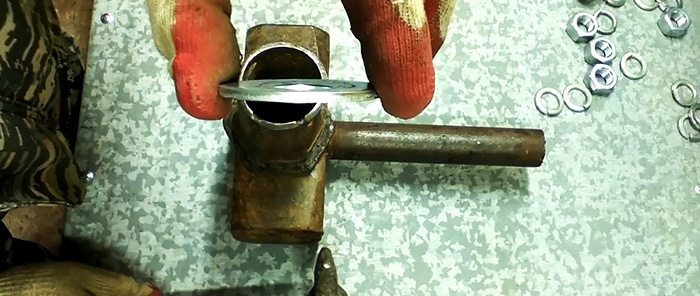
6. Monte o rolo e aperte as porcas.
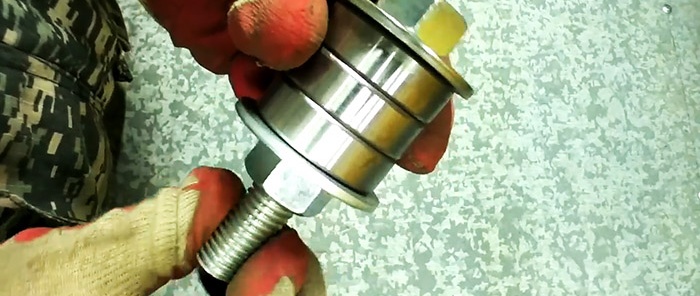
7. Remova a parte do pino que se projeta além da porca.
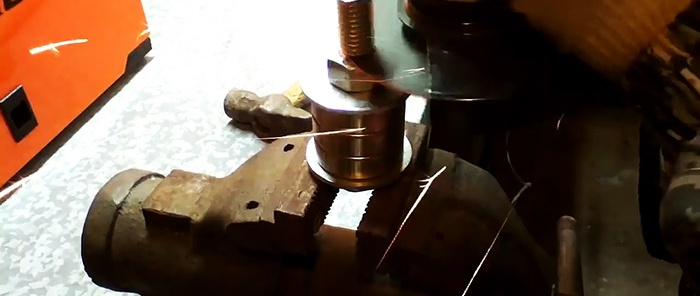
8. Usando soldagem elétrica, fixamos os elementos do rolo.
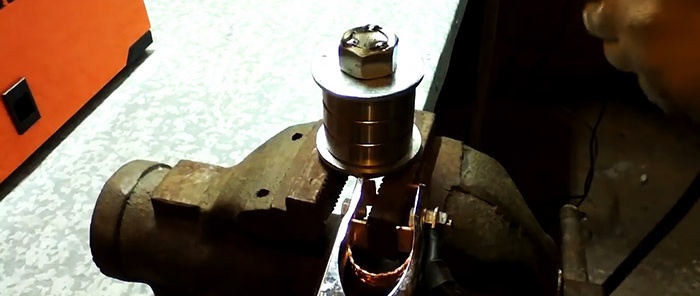
9. Verifique se o rolo gira livremente.
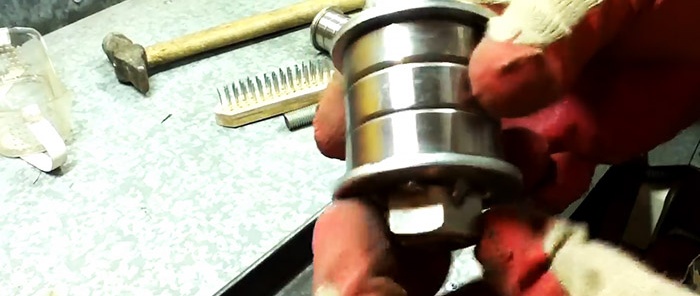
10.Marcamos e cortamos quatro segmentos de 25 cm de comprimento de um canto de 25x25 mm para fazer guias para os rolos de acionamento e pressão.
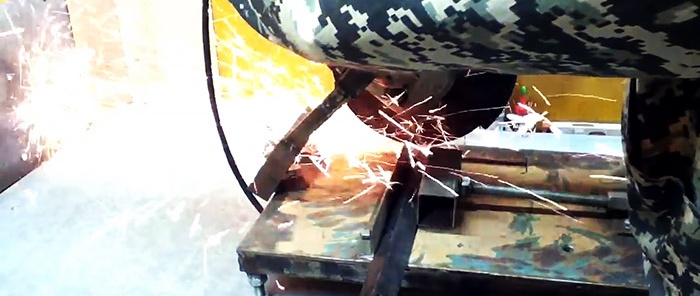
11. Soldamos os pedaços de cantos na base do canal, mantendo uma folga para o eixo do rolo de acionamento (eixo).
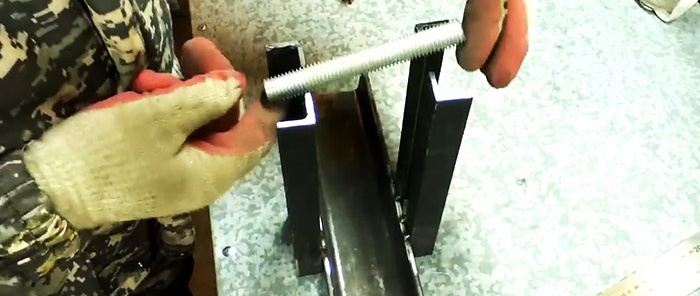
12. Em uma das partes já preparadas do pino colocamos um pedaço de tubo com diâmetro de 27 mm e comprimento de 40 mm. Preencha a lacuna interna com pregos de 40 mm sem cabeça.
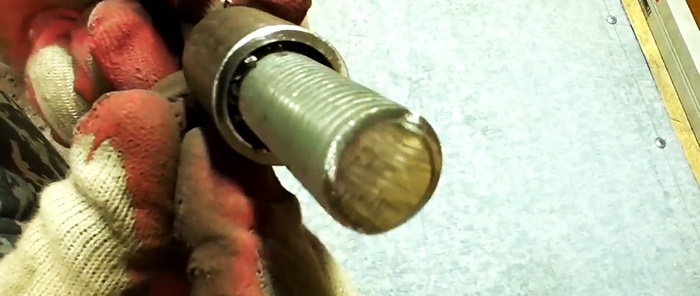
13. Soldamos todos os elementos ao redor da circunferência por meio de soldagem elétrica e obtemos um eixo acabado.
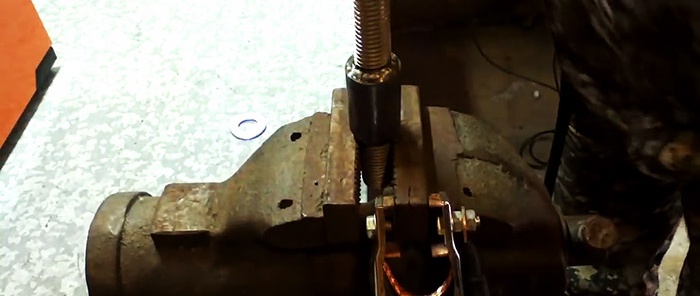
14. Colocamos rolamentos nas bordas do eixo.
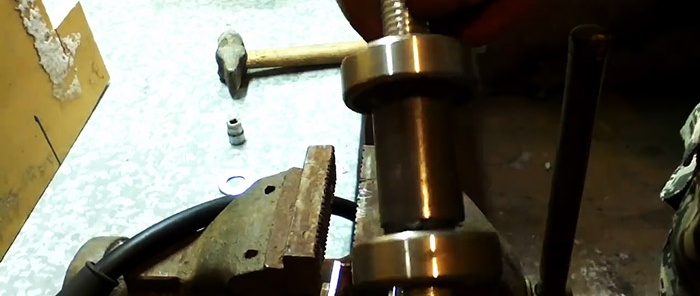
15. Fazemos um carro móvel soldando duas seções de um tubo perfilado 20x40x30 mm, uma placa de aço retangular 80x50 mm e um eixo com rolamentos em uma única estrutura.
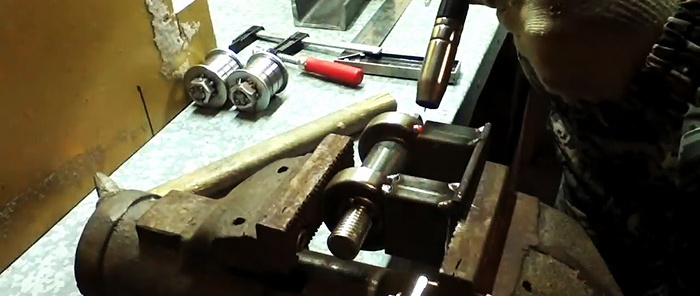
16. Na intersecção das diagonais, marque o centro com um núcleo e faça um furo com diâmetro de 18 mm para o pino na parte superior do carro usando uma broca e um alargador.
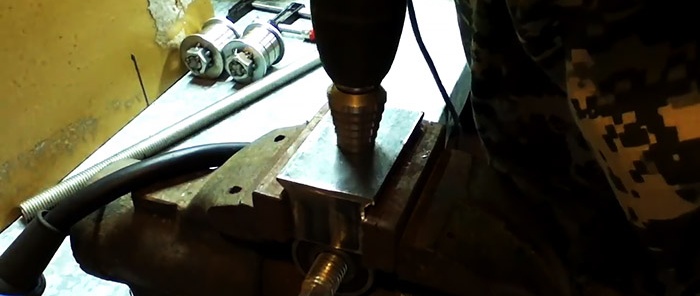
17. Montamos o mecanismo de elevação, composto por um pino e três porcas M18, duas das quais soldadas por pontos ao pino rosqueado no orifício da plataforma do carro.
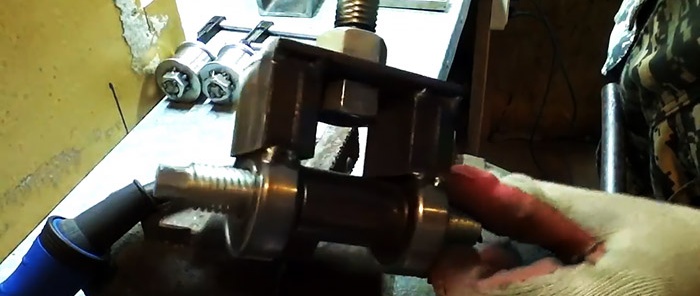
18. Recorte um retângulo de aproximadamente 70x130 mm de uma chapa de aço de 5 mm de espessura, que servirá de batente para o mecanismo de elevação. Marque o meio e faça um furo de 18 mm semelhante à base do carro.
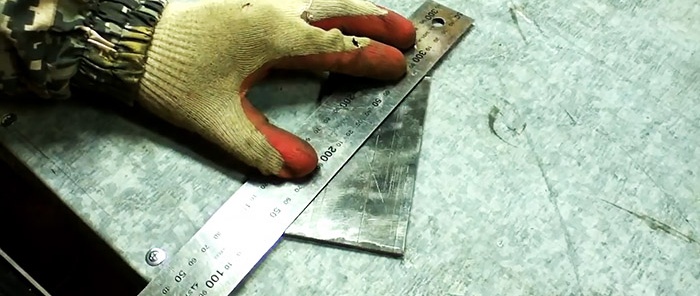
19. Montamos os elementos fabricados em uma única estrutura. Para isso, instale o carro com o eixo de transmissão nas guias.
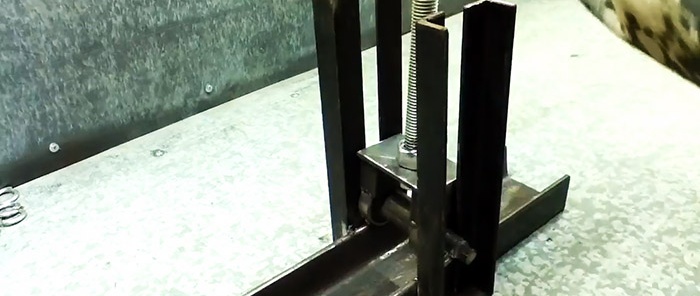
20. Colocamos no pino e instalamos a placa de suporte.
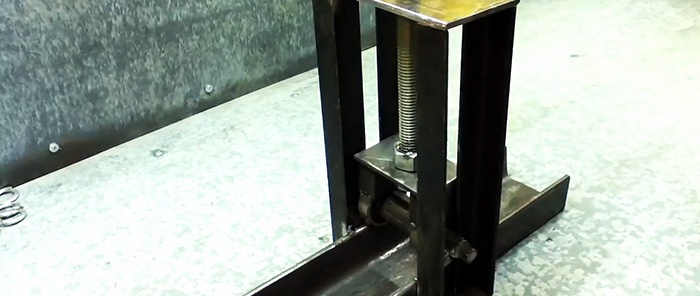
21. Aparafuse a porca no pino até parar e aperte as juntas com solda elétrica.
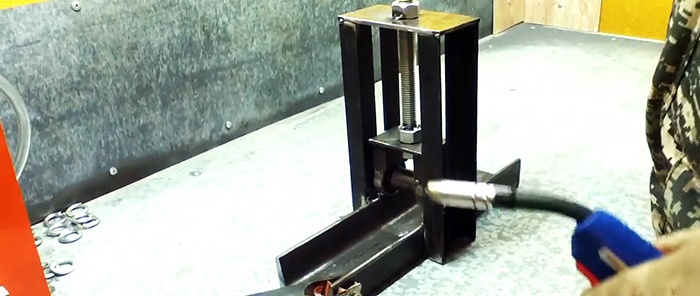
22. Soldamos os rolos previamente confeccionados ao longo das bordas da base do canal.
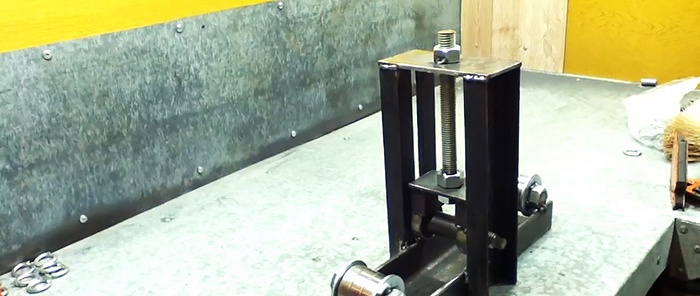
23. Soldamos uma alça de 25-30 cm de um tubo perfilado de 20x20 mm ao mecanismo de elevação e fixação.
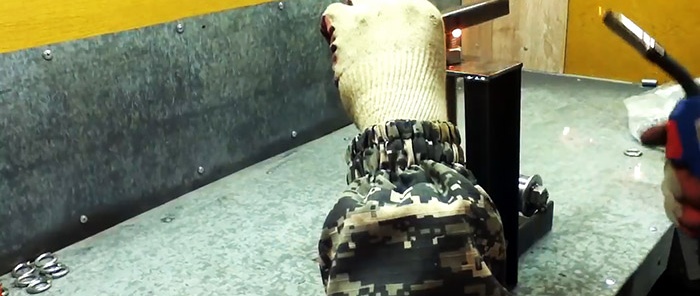
24.Fazemos uma alavanca de acionamento mecânico a partir de uma seção de 20-25 cm de um tubo perfilado de 20x20 mm e soldamos ao rolo de acionamento (pino). A alça de acionamento pode ser emprestada de qualquer ferramenta elétrica antiga, primeiro fazendo um furo para ela. Se não estiver disponível, você pode soldar um pedaço de tubo redondo de 12 a 14 cm na alavanca.

25. O dobrador de tubos está pronto, vamos fazer o teste.
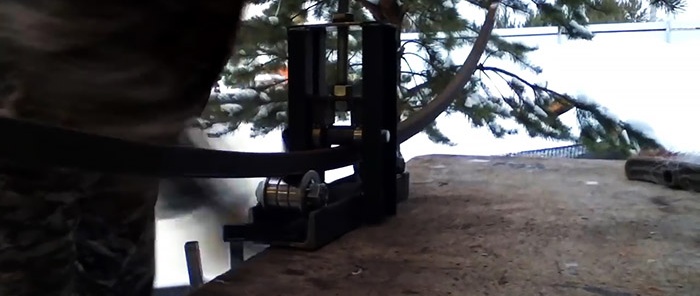
26. E por fim, a última etapa é pintar nosso dobrador de tubos. Como pode uma obra-prima técnica tão montada à mão não ter uma aparência respeitável?
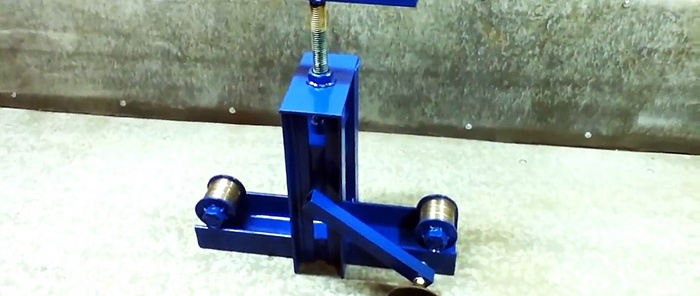
No entanto, esta é uma questão puramente individual e não nos deteremos nela em detalhes. Observamos apenas que primeiro é necessário remover toda a rugosidade com uma lima ou esmeril, desengordurar bem com solvente e cobrir com primer. Mas em qualquer caso, embora agrade à alma, não afeta em nada o resultado.
Assista o vídeo
Master classes semelhantes
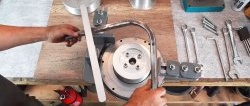
Como fazer um dobrador de tubos a partir do volante de um carro e de um motor de arranque Bendix
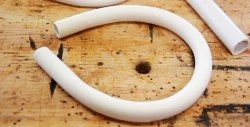
Como dobrar tubos de plástico corretamente
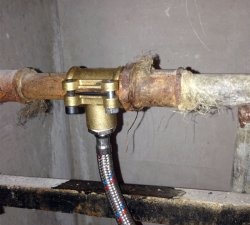
Como fazer um corte simples em um tubo de aço
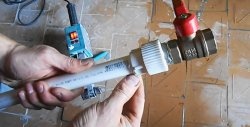
Como soldar um tubo de polipropileno quando a água está fluindo
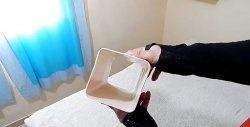
Como transformar um tubo de PVC redondo em quadrado
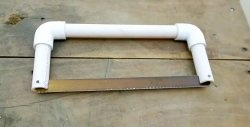
Como fazer uma serra para metal
Particularmente interessante
Comentários (0)