Como fazer uma extrusora de haste para uma impressora 3D de maneira econômica usando os componentes disponíveis
Com o uso ativo da impressão 3D, grandes somas são gastas na compra de consumíveis. Nesse sentido, faz sentido fabricá-los você mesmo com plástico ABS triturado e garrafas PET. Para isso, é necessário fabricar equipamentos especiais, sendo o mais complexo a extrusora.
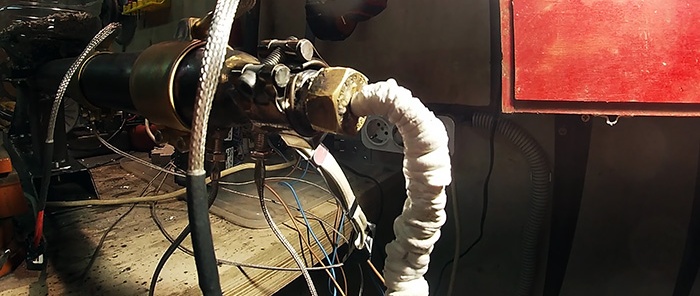
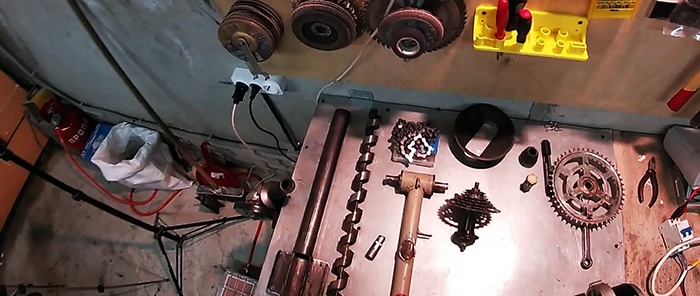
Uma broca espiral para madeira será usada como parafuso extrusor. Um cano de água é selecionado para isso. Nele você precisa desbastar a costura de solda interna com uma lima.Um corte longitudinal é feito a partir da borda do tubo até uma profundidade de 60-80 mm e parte do tubo é cortada ao longo dele. As bochechas da chapa de aço são soldadas na ranhura resultante à esquerda e à direita. Neles será instalado um funil de carregamento para plástico triturado. Pode ser impresso em uma impressora 3D.
Uma placa de aço ou um tubo de perfil maciço pode ser usado como base da extrusora.
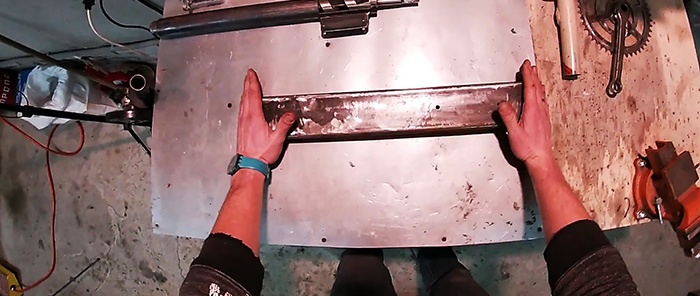
Um suporte é aparafusado à base para fixar a própria extrusora. É feito de um tubo perfilado com saliências. O próprio corpo da extrusora é soldado ao suporte e, em seguida, um parafuso é inserido nele.
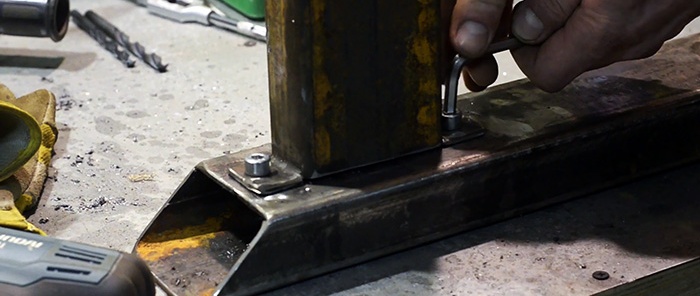
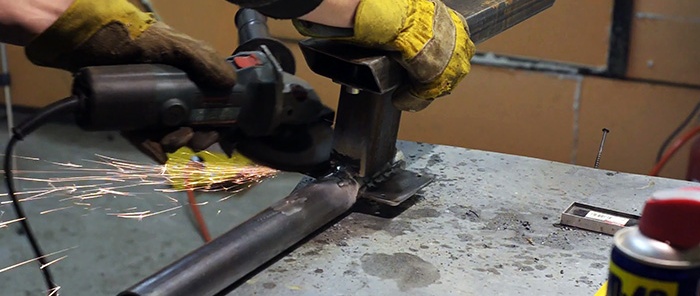
Em seguida, você precisa conectar o sem-fim ao motor por meio de uma caixa de redução.
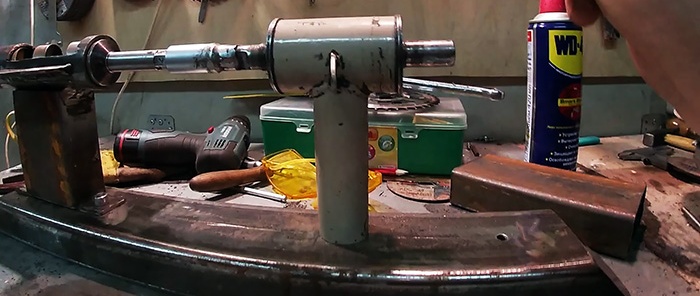
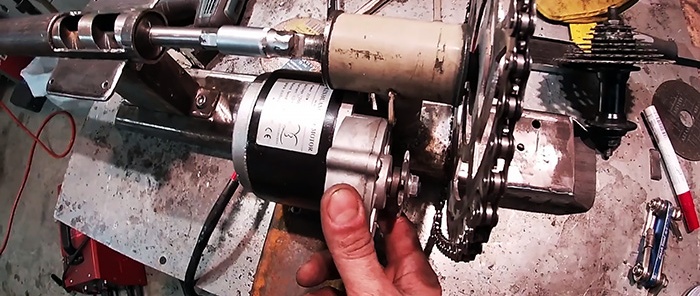
Para fazer isso, um carrinho de bicicleta é conectado a ele através da cabeça do soquete. A cabeça é soldada ao carro e depois colocada na haste do sem-fim. Depois disso, o carro é alinhado coaxialmente com a extrusora e seu suporte é soldado à sola.
Em seguida, a roda dentada da bicicleta é instalada no eixo do carro. Em seguida, você precisa conectar a roda dentada à roda dentada pequena no cassete do cubo por meio de uma corrente de rolos. Depois disso, a mesma corrente conecta a roda dentada grande do cassete com a roda dentada da caixa de engrenagens do motor elétrico. Para isso, outro tubo perfilado é soldado na lateral da moldura para acomodar a bucha e o motor. Neste caso, a roda dentada tem 46 dentes, a pequena tem 11, a do meio tem 30 e a caixa de engrenagens do motor tem 9. Assim, a relação de transmissão do motor para a furadeira será de 1:140. Para maior confiabilidade, todos os racks devem ser reforçados com reforços de soldagem.
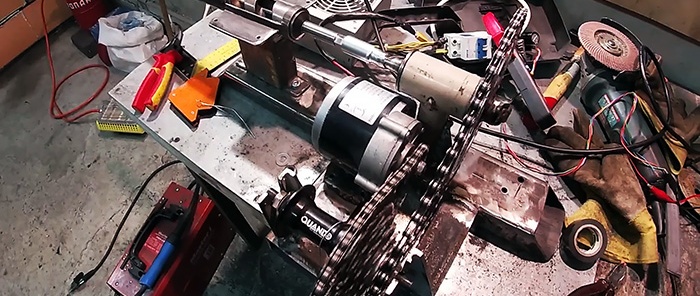
Um adaptador e um pedaço de tubo de 1/2 polegada são soldados na saída do corpo da extrusora. Deve haver uma rosca na borda do tubo para instalar o bico. Ele usa um tampão de encanamento com um furo de 4 mm no centro.
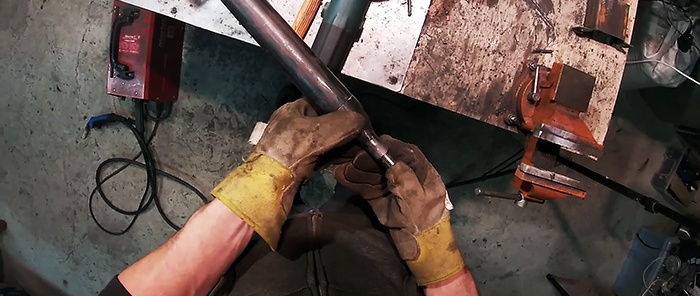
Em seguida, você precisa instalar aquecedores de anel na parte superior da carcaça da extrusora. Se o diâmetro não corresponder, o invólucro pode ser aumentado envolvendo-o com uma tira de aço. Os aquecedores são instalados no nariz da extrusora, no centro e no início do invólucro. Cada um deles está conectado através de um controlador PID separado. Seus sensores térmicos são aparafusados à caixa. Para fazer isso, você precisará soldar porcas nele. É possível que, após o teste, seja necessário adicionar o número de aquecedores.
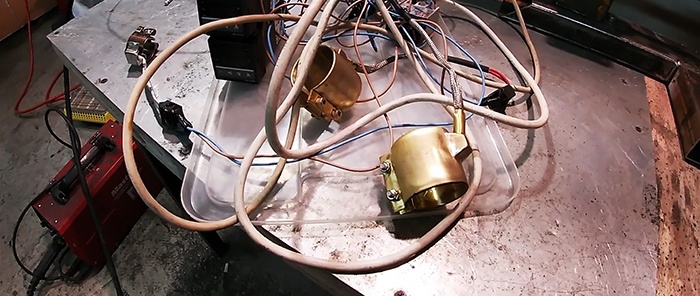
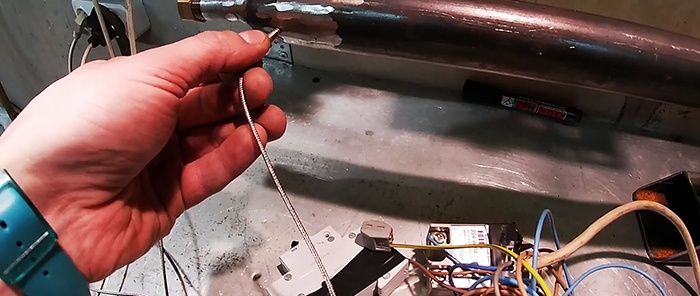
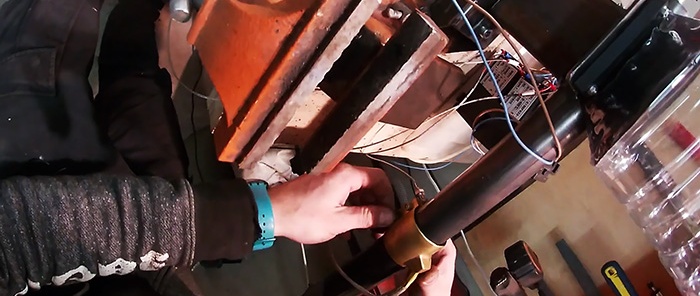
Em seguida, é necessário ligar o aquecimento e ajustar a temperatura dos aquecedores. Para começar, ao usar chips de plástico ABS, o primeiro é ajustado para 120°C, o segundo para 200°C e o terceiro para 180°C. Após o aquecimento, inicia-se a rotação do parafuso. Você precisa configurá-lo para cerca de 5 rpm.
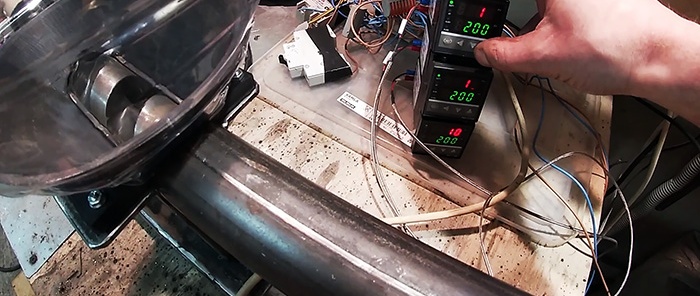
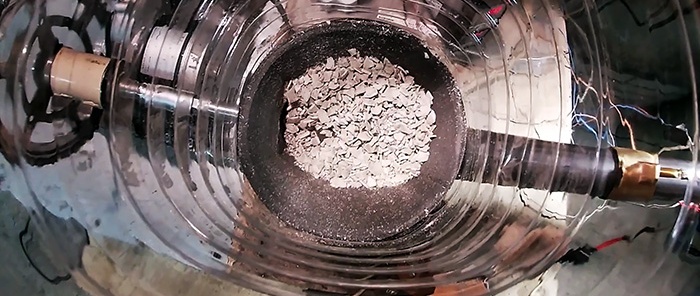
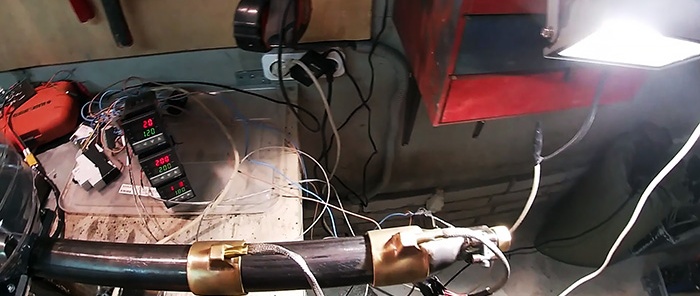
Depois de fazer a extrusora, será necessário montar muito mais dispositivos para organizar a produção da haste, mas eles ficam muito mais fáceis. No mínimo, você também precisará de um banho para resfriar a haste, um rolo receptor e um vibrador para a tremonha para fornecimento ininterrupto de cavacos de plástico ao sem-fim.
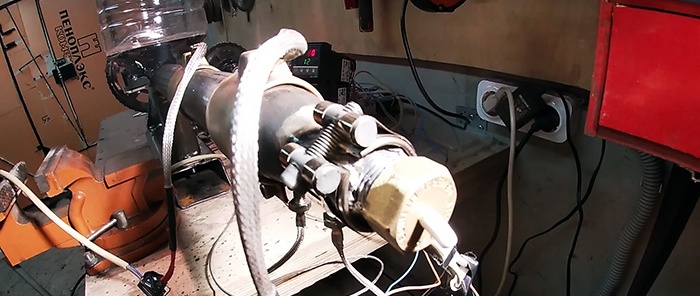
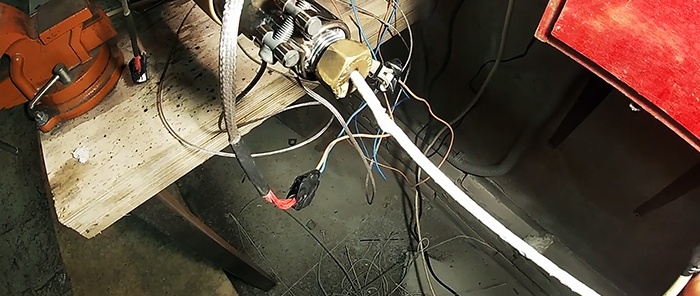
Assista ao vídeo para todos os detalhes:
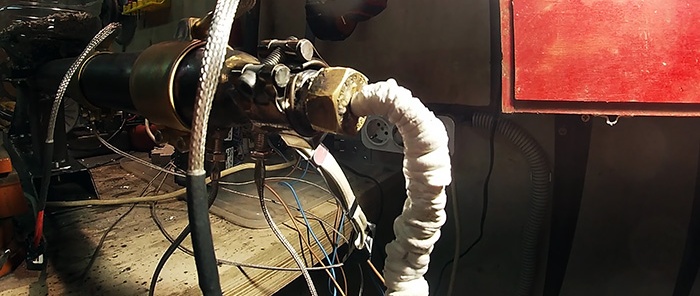
Materiais:
- broca helicoidal para madeira 36 mm;
- tubo de aço com diâmetro interno de 37 mm;
- adaptador para tubo com diâmetro de 1/2 polegada;
- Tubo de 1/2 polegada;
- Plugue de encanamento de 1/2";
- Chapa de aço;
- carrinho de bicicleta no alojamento;
- roda dentada de bicicleta;
- cubo traseiro de bicicleta com cassete;
- corrente de rolos;
- motor elétrico;
- tubos perfilados;
- aquecedores de anel 320 W – 2-3 unidades;
- aquecedor de anel 70 W;
- Controladores PID para cada aquecedor;
- Regulador PWM.
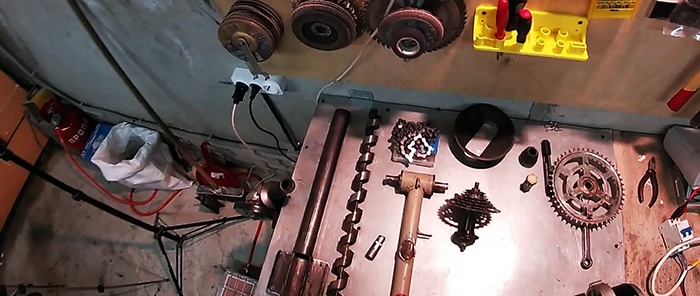
Processo de fabricação de extrusora
Uma broca espiral para madeira será usada como parafuso extrusor. Um cano de água é selecionado para isso. Nele você precisa desbastar a costura de solda interna com uma lima.Um corte longitudinal é feito a partir da borda do tubo até uma profundidade de 60-80 mm e parte do tubo é cortada ao longo dele. As bochechas da chapa de aço são soldadas na ranhura resultante à esquerda e à direita. Neles será instalado um funil de carregamento para plástico triturado. Pode ser impresso em uma impressora 3D.
Uma placa de aço ou um tubo de perfil maciço pode ser usado como base da extrusora.
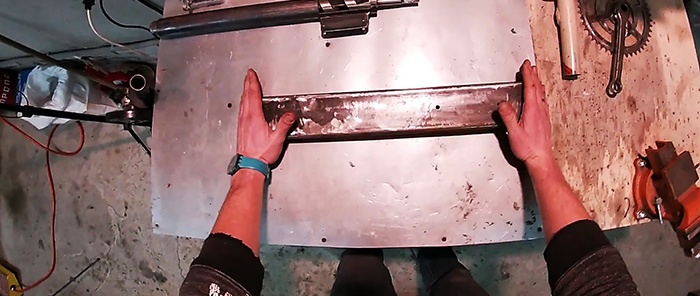
Um suporte é aparafusado à base para fixar a própria extrusora. É feito de um tubo perfilado com saliências. O próprio corpo da extrusora é soldado ao suporte e, em seguida, um parafuso é inserido nele.
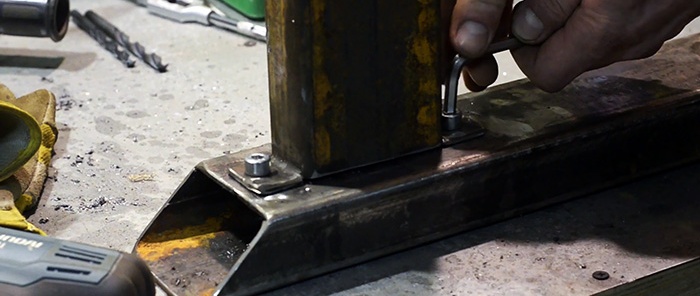
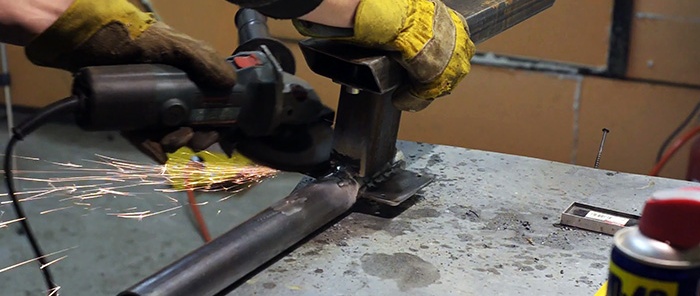
Em seguida, você precisa conectar o sem-fim ao motor por meio de uma caixa de redução.
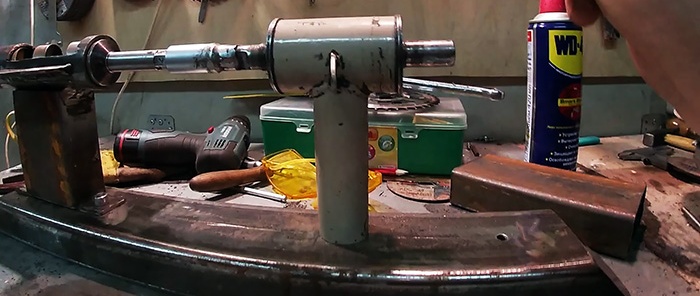
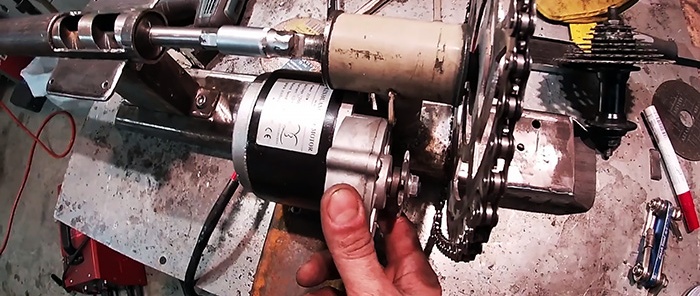
Para fazer isso, um carrinho de bicicleta é conectado a ele através da cabeça do soquete. A cabeça é soldada ao carro e depois colocada na haste do sem-fim. Depois disso, o carro é alinhado coaxialmente com a extrusora e seu suporte é soldado à sola.
Em seguida, a roda dentada da bicicleta é instalada no eixo do carro. Em seguida, você precisa conectar a roda dentada à roda dentada pequena no cassete do cubo por meio de uma corrente de rolos. Depois disso, a mesma corrente conecta a roda dentada grande do cassete com a roda dentada da caixa de engrenagens do motor elétrico. Para isso, outro tubo perfilado é soldado na lateral da moldura para acomodar a bucha e o motor. Neste caso, a roda dentada tem 46 dentes, a pequena tem 11, a do meio tem 30 e a caixa de engrenagens do motor tem 9. Assim, a relação de transmissão do motor para a furadeira será de 1:140. Para maior confiabilidade, todos os racks devem ser reforçados com reforços de soldagem.
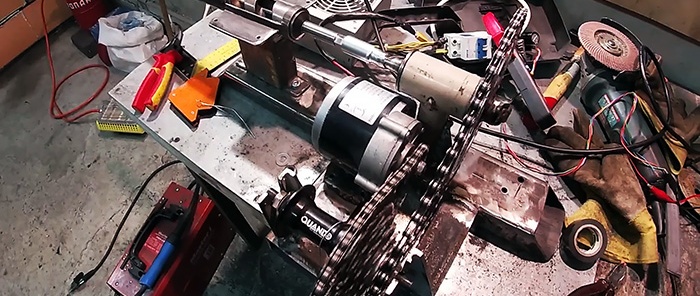
Um adaptador e um pedaço de tubo de 1/2 polegada são soldados na saída do corpo da extrusora. Deve haver uma rosca na borda do tubo para instalar o bico. Ele usa um tampão de encanamento com um furo de 4 mm no centro.
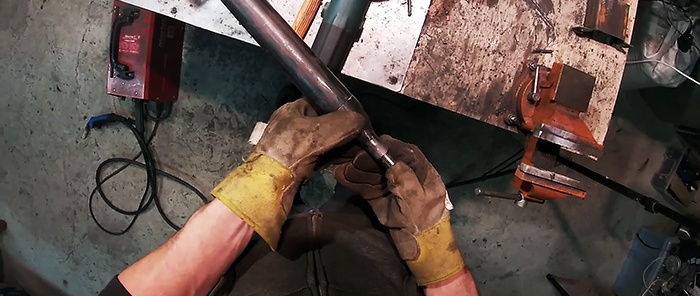
Em seguida, você precisa instalar aquecedores de anel na parte superior da carcaça da extrusora. Se o diâmetro não corresponder, o invólucro pode ser aumentado envolvendo-o com uma tira de aço. Os aquecedores são instalados no nariz da extrusora, no centro e no início do invólucro. Cada um deles está conectado através de um controlador PID separado. Seus sensores térmicos são aparafusados à caixa. Para fazer isso, você precisará soldar porcas nele. É possível que, após o teste, seja necessário adicionar o número de aquecedores.
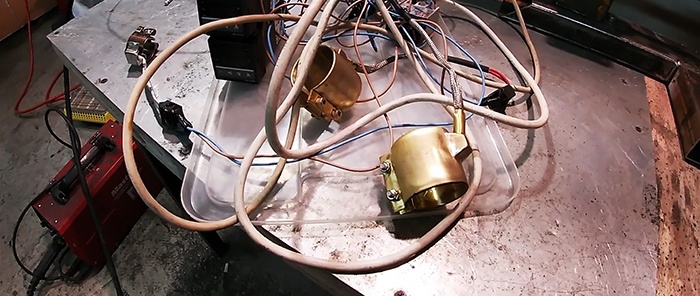
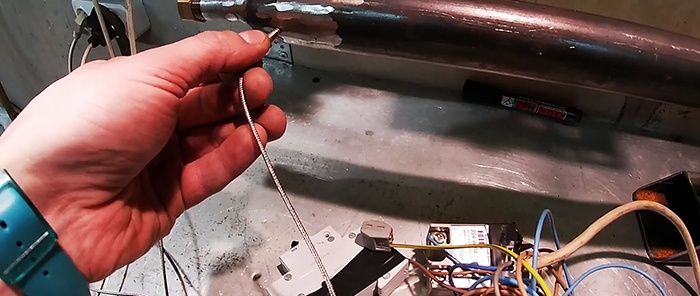
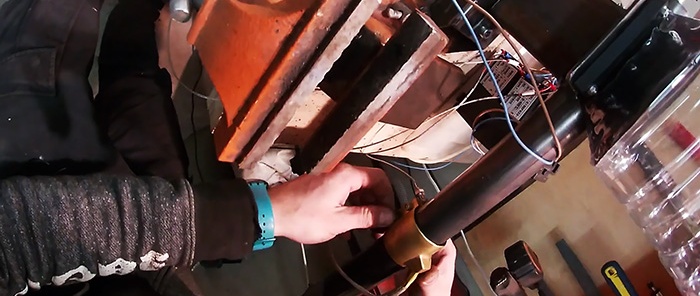
Em seguida, é necessário ligar o aquecimento e ajustar a temperatura dos aquecedores. Para começar, ao usar chips de plástico ABS, o primeiro é ajustado para 120°C, o segundo para 200°C e o terceiro para 180°C. Após o aquecimento, inicia-se a rotação do parafuso. Você precisa configurá-lo para cerca de 5 rpm.
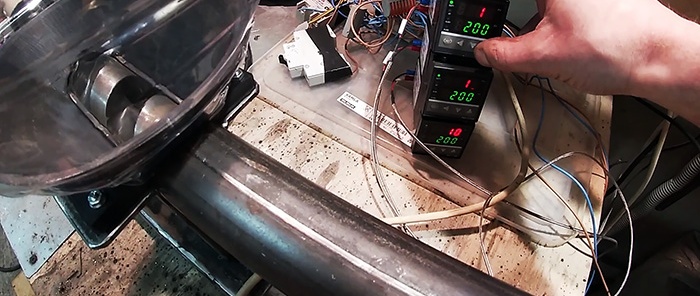
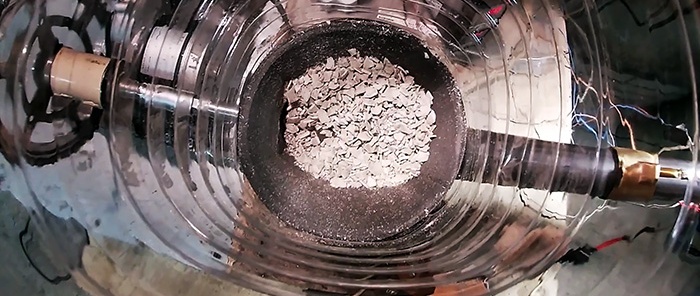
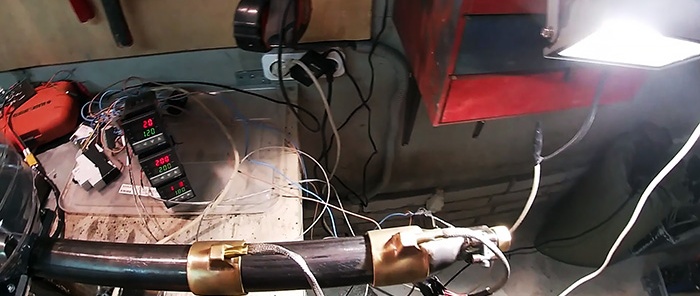
Depois de fazer a extrusora, será necessário montar muito mais dispositivos para organizar a produção da haste, mas eles ficam muito mais fáceis. No mínimo, você também precisará de um banho para resfriar a haste, um rolo receptor e um vibrador para a tremonha para fornecimento ininterrupto de cavacos de plástico ao sem-fim.
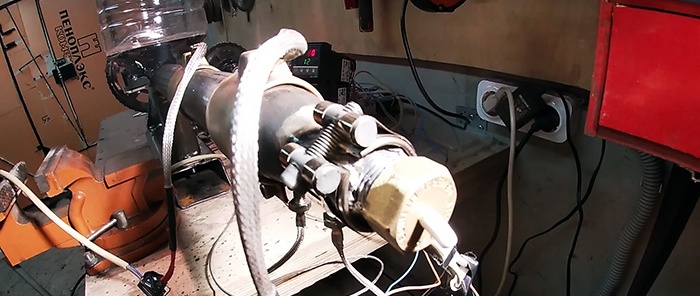
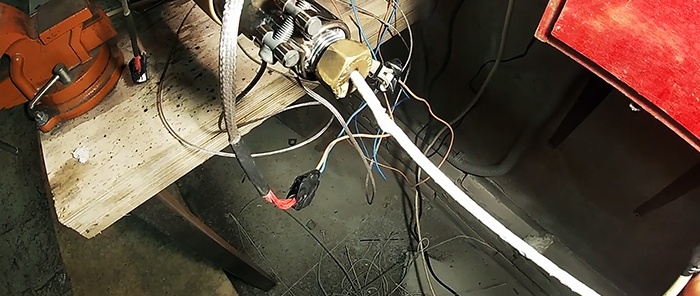
Assista o vídeo
Assista ao vídeo para todos os detalhes:
Master classes semelhantes
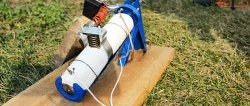
Como fazer uma extrusora para derreter plástico com uma pistola para
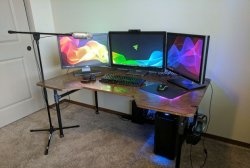
Mesa de computador simples
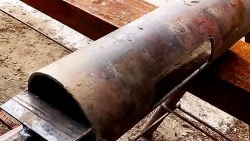
Furadeira para tubos faça você mesmo
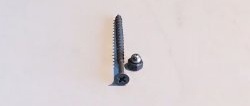
Como fazer uma broca a partir de um rolamento para furar aço temperado
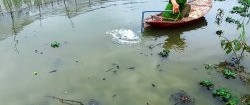
Motor elétrico de barco de 12 V faça você mesmo
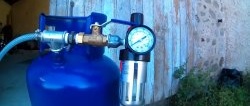
Como fazer um jato de areia com um pequeno cilindro de gás
Particularmente interessante
Comentários (0)