Wie man aus Schrott einen zuverlässigen Holzhacker macht
In Gärten und Sommerhäusern bilden sich nach dem Beschneiden von Bäumen und dem Ausdünnen von Büschen, der Gemüseernte und der Reinigung des Geländes viele Äste, Wipfel und Unkraut. Um sie zu entsorgen, gibt es teure Fabrik-Schredder. Um kein Geld zu verschwenden, können Sie es selbst aus Abfallmaterialien herstellen.
Wird benötigt
Material:- Flansch-Elektromotor;
- zwei quadratische Stahlplatten;
- altes Sägeblatt;
- verschiedene Schrauben, Muttern und Unterlegscheiben;
- Buchse mit abgestufter Außenfläche;
- gebogene Ecke;
- Stahlstreifen;
- geschweißtes Stahlrohr;
- Rundrohr;
- Sprühfarbe in zwei Farben usw.
Herstellungsprozess eines Holzhackers
Unter Berücksichtigung der Leistung und Abmessungen des angeflanschten Elektromotors schneiden wir zwei Stahlplatten aus, ermitteln deren Mittelpunkte und bohren Löcher passend zum Durchmesser der Motorachse.
Auf einer Platte bohren wir entsprechend dem Durchmesser und der Lage der Löcher am Flansch des Elektromotors passende Löcher.
Wir befestigen die Platte in einem Schraubstock und wandeln die runden Löcher mit einer Feile in quadratische um, um sie mit Schrauben mit einer quadratischen Kopfstütze am Motorflansch zu befestigen.
Wir schneiden aus einem alten Sägeblatt eine Platte mit den angegebenen Maßen aus und bohren in der Mitte ein Loch.
In die Platten auf den Diagonalen entlang der Markierungen gegenüber den Ecken bohren wir vier Löcher für lange Bolzen.
Dazwischen bohren wir drei weitere Löcher im gleichen Abstand von der Mitte wie die vier zuvor gebohrten. In einem etwas größeren Radius von der Mitte bohren wir sieben weitere Löcher.
Wir setzen eine Buchse auf die Welle des Elektromotors, wobei eine Platte mit der größeren Außenfläche nach oben am Flansch befestigt wird.
Darauf legen wir ein geschärftes Messer der gewünschten Form und zwei Spannringe auf.
In die vier Löcher in den Ecken der Platte, die sich in einem kleineren Radius von der Mitte befinden, stecken wir von unten Schrauben ein, die wir mit Muttern oben auf der Platte befestigen. Wir schrauben die hohen auf diese Standardmuttern und ziehen sie auch fest.
Wir legen eine zweite Platte auf die vier langen Schrauben und die Motorwelle, sodass sie auf den Enden der hohen Muttern aufliegt.
Wir befestigen es mit einer Unterlegscheibe und einer Sechskantschraube an der Welle, wobei wir das zentrale Gewindeloch am Ende der Welle sowie Muttern verwenden, die auf die langen Schrauben geschraubt werden.
Um das Messer relativ zur Oberplatte einzustellen, werden Unterlegscheiben zwischen die Muttern der Bolzen gelegt.
Die Bolzenstangen oberhalb der Muttern schneiden wir mit einer Schleifmaschine ab.
Für den Motorsockel fertigen wir durch Schweißen einen Rahmen aus einem gebogenen Winkel und befestigen ihn mit Schrauben am Sockel.
Wir bedecken sieben Bolzen, die sich in einem kleineren Radius von der Mitte der Platten befinden, mit einem Stahlstreifen, dessen Breite dem Abstand zwischen den Platten entspricht.
Wir stecken sieben weitere Schrauben in die Löcher, die sich in einem größeren Radius von der Mitte befinden, und ziehen sie mit Muttern fest.Das Band liegt am gesamten Umfang zwischen den Bolzen und kann sich daher weder nach außen noch nach innen bewegen.
Auf der Außenplatte zwischen der Welle des Elektromotors und den Schrauben schneiden wir ein quadratisches Loch aus, an das wir ein geschweißtes Stahlrohr (Empfänger) mit abgeschrägtem Ende anschweißen, durch das wir dem Zerkleinerer Materialien zum Mahlen zuführen.
In vier gleich lange Abschnitte eines Rundrohrs bohren wir an einem Ende Schlitze, stecken sie zur Stabilität nach unten und leicht seitlich ausgerichtet in die Ablage der gebogenen Ecke und verschweißen sie.
Wir lackieren das selbstgemachte Produkt in zwei Farben, entsprechend der Funktionalität (Sicherheit) der zu lackierenden Teile, und es ist gebrauchsfertig.
Schau das Video
Ähnliche Meisterkurse
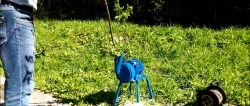
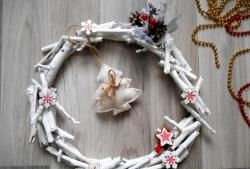
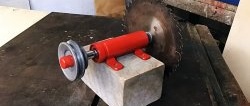
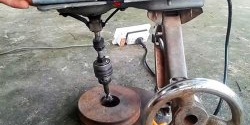
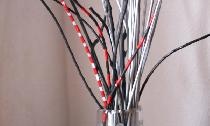
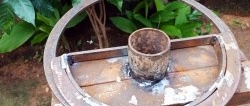
Besonders interessant
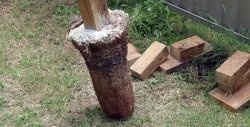
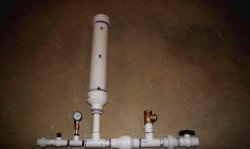
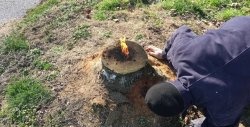
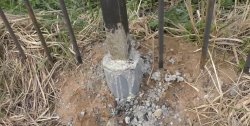
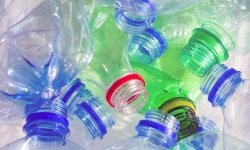
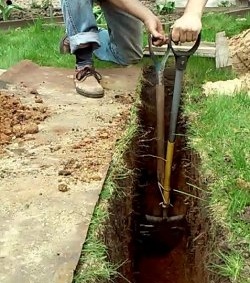