Car inverter 12-220V
I bought myself a car six months ago. I will not describe all the modernizations made to improve it, I will focus on only one. This is a 12-220V inverter for powering consumer electronics from the vehicle's on-board network.
Of course, you could buy it in a store for $25-30, but I was confused by their power. To power even a laptop, the 0.5-1 ampere current that most car inverters produce is clearly not enough.
Choosing a circuit diagram.
By nature, I am a lazy person, so I decided not to “reinvent the wheel”, but to search the Internet for similar designs, and adapt the circuit of one of them for my own crafts. Time was very pressing, so simplicity and the absence of expensive spare parts were the priority.
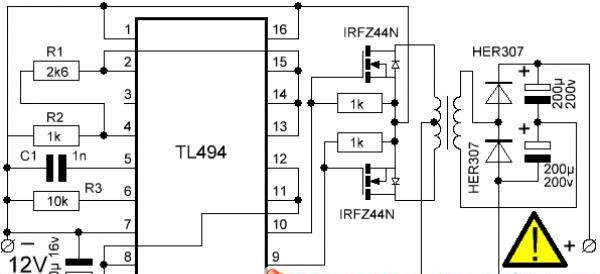
On one of the forums, a simple circuit was chosen using the common PWM controller TL494. The disadvantage of this circuit is that it produces a rectangular voltage of 220 V at the output, but for pulsed power circuits this is not critical.
Selection of parts.
The circuit was chosen because almost all the parts could be taken from a computer power supply. For me this was very critical, because the nearest specialized store is more than 150 km away.
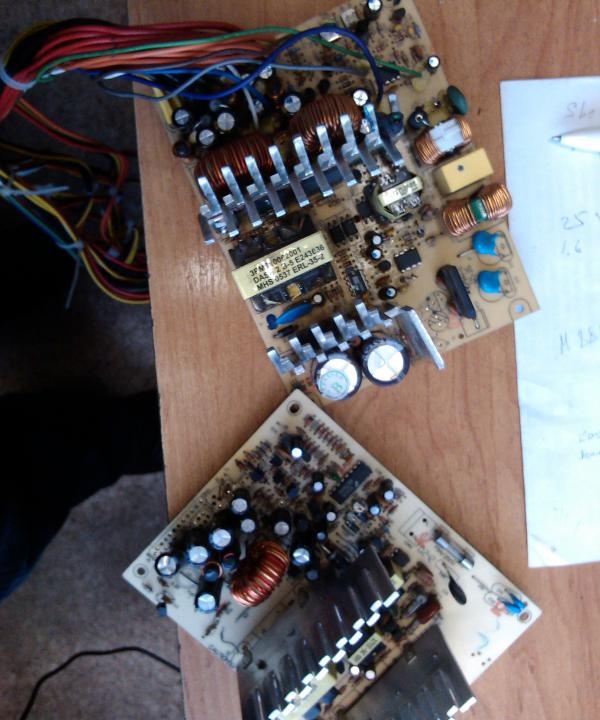
Output capacitors, resistors, and the microcircuit itself were removed from a pair of faulty power supplies of 250 and 350 W.
The difficulty arose only with high-frequency diodes for converting the voltage at the output of the step-up transformer, but here old supplies saved me. The characteristics of the KD2999V suited me quite well.
Assembly of the finished device.
I had to assemble the device within a couple of hours after work, because a long trip was planned.
Since time was very limited, I simply did not look for additional materials and tools. I used only what was at hand. Again, due to speed, I did not use the printed circuit board samples provided on the forums. In 30 minutes, we designed our own printed circuit board on a piece of paper, and its design was transferred to the PCB.
Using a scalpel, one of the foil layers was removed. On the remaining layer, deep grooves were drawn along the applied lines. Using curved tweezers, it turned out to be the most convenient, the grooves were deepened to the non-conducting layer. At the places where the parts were installed using an awl, it was not included in the photo, holes were made.
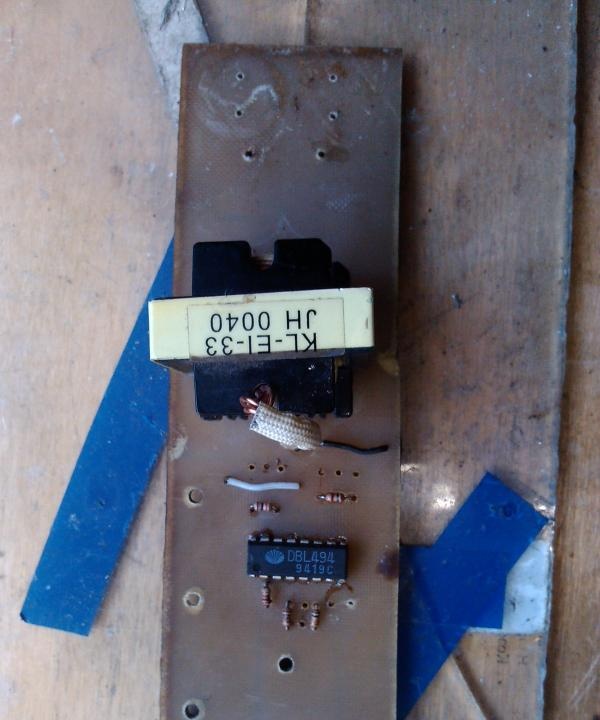
I started the assembly by installing a transformer, I used a step-down one of the blocks, I simply turned it over and instead of lowering the voltage from 400 V to 12 V, it raised it from 12 V to 268 V. By replacing resistors R3 and capacitor C1, it was possible to reduce the output voltage to 220 V, but further experiments showed that this should not be done.
After the transformer, in order of decreasing size, I installed the remaining spare parts.
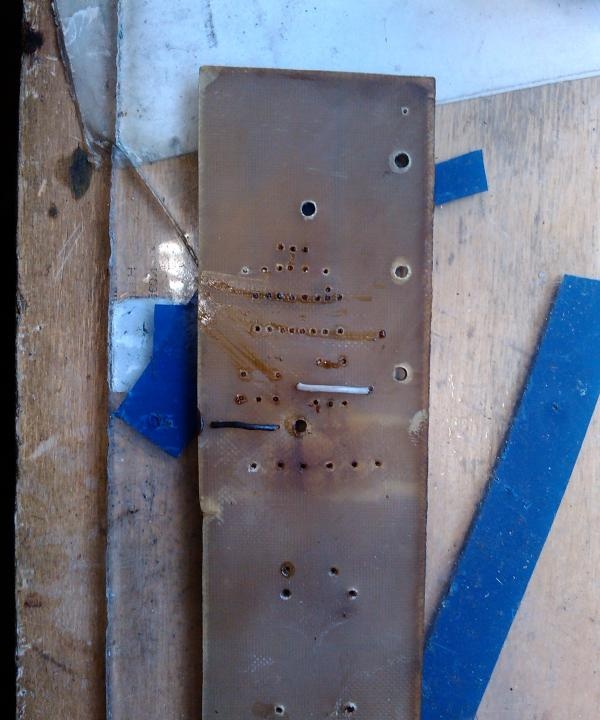
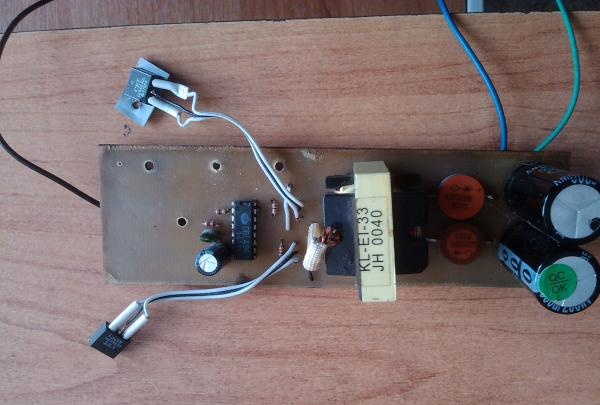
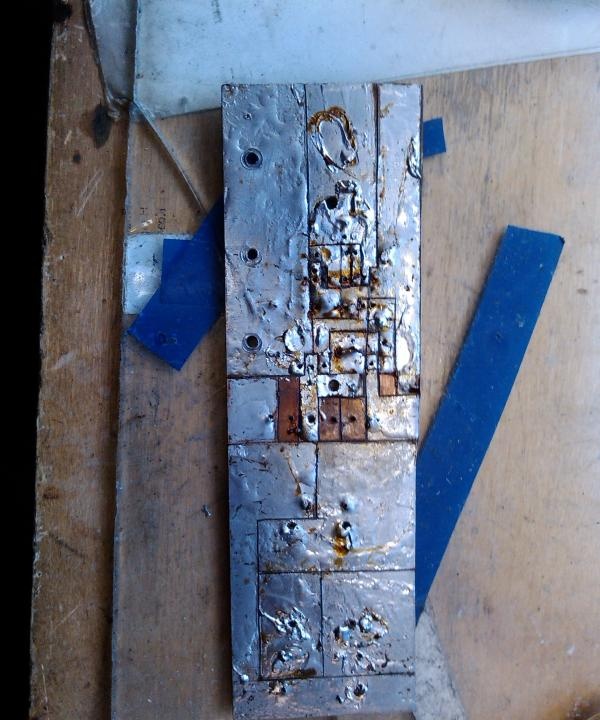
It was decided to install field-effect transistors on elongated inputs so that they are easier to attach to the cooling radiator.
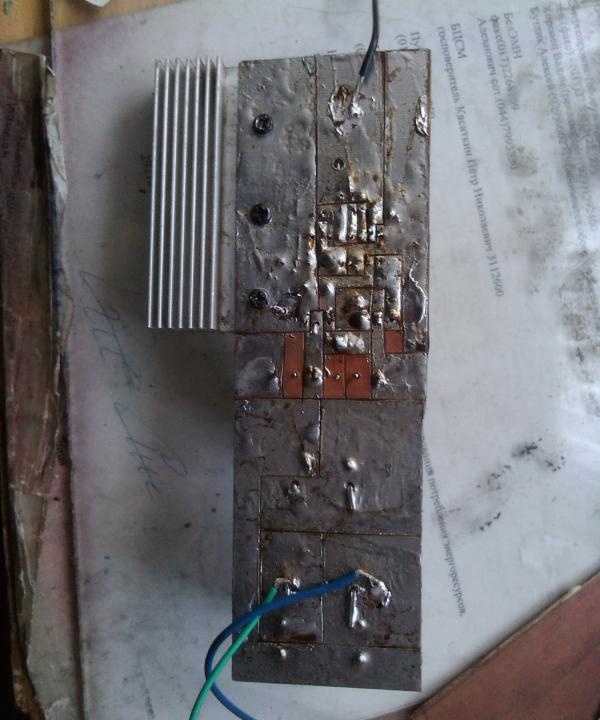
The end result is this device:
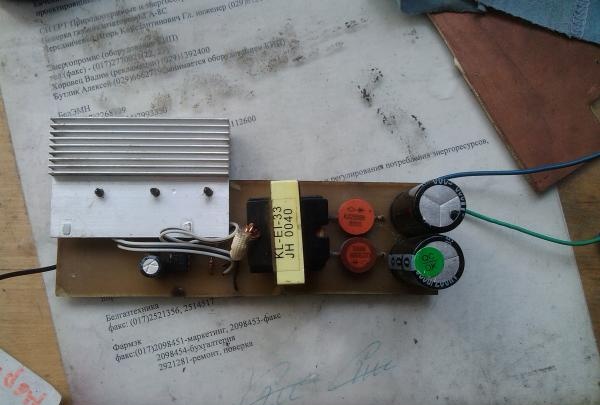
All that remains is the finishing touch - attaching the radiator. There are 4 holes visible on the board, although there are only 3 self-tapping screws; it was just during the assembly process that it was decided to slightly change the position of the radiator for a better appearance. After final assembly this is what we got:
Tests.
There was no time to specifically test the device; it was simply connected to the battery from an uninterruptible power supply. A load in the form of a 30 W light bulb was connected to the output. After it caught fire, the device was simply thrown into my backpack, and I went on a business trip for 2 weeks.
In 2 weeks, the device never failed. Various devices were powered from it. When measured with a multimeter, the maximum current obtained reached 2.7 A.
Of course, you could buy it in a store for $25-30, but I was confused by their power. To power even a laptop, the 0.5-1 ampere current that most car inverters produce is clearly not enough.
Choosing a circuit diagram.
By nature, I am a lazy person, so I decided not to “reinvent the wheel”, but to search the Internet for similar designs, and adapt the circuit of one of them for my own crafts. Time was very pressing, so simplicity and the absence of expensive spare parts were the priority.
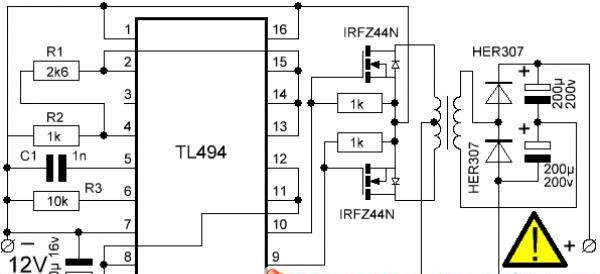
On one of the forums, a simple circuit was chosen using the common PWM controller TL494. The disadvantage of this circuit is that it produces a rectangular voltage of 220 V at the output, but for pulsed power circuits this is not critical.
Selection of parts.
The circuit was chosen because almost all the parts could be taken from a computer power supply. For me this was very critical, because the nearest specialized store is more than 150 km away.
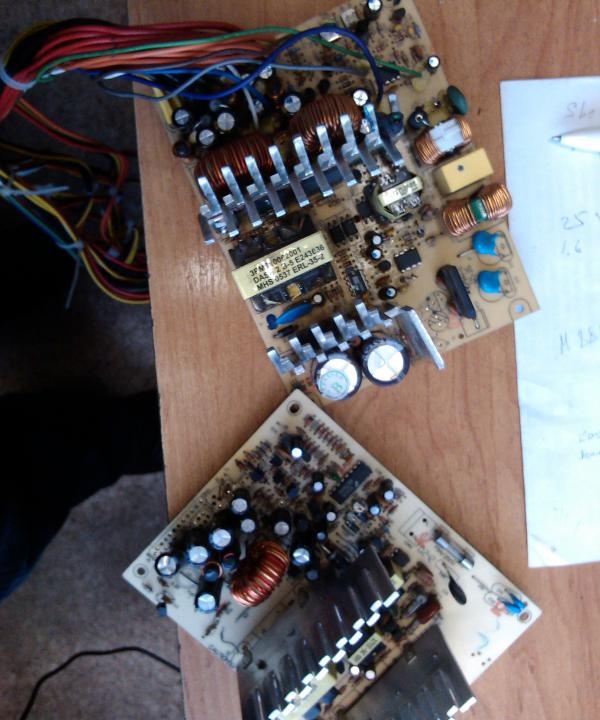
Output capacitors, resistors, and the microcircuit itself were removed from a pair of faulty power supplies of 250 and 350 W.
The difficulty arose only with high-frequency diodes for converting the voltage at the output of the step-up transformer, but here old supplies saved me. The characteristics of the KD2999V suited me quite well.
Assembly of the finished device.
I had to assemble the device within a couple of hours after work, because a long trip was planned.
Since time was very limited, I simply did not look for additional materials and tools. I used only what was at hand. Again, due to speed, I did not use the printed circuit board samples provided on the forums. In 30 minutes, we designed our own printed circuit board on a piece of paper, and its design was transferred to the PCB.
Using a scalpel, one of the foil layers was removed. On the remaining layer, deep grooves were drawn along the applied lines. Using curved tweezers, it turned out to be the most convenient, the grooves were deepened to the non-conducting layer. At the places where the parts were installed using an awl, it was not included in the photo, holes were made.
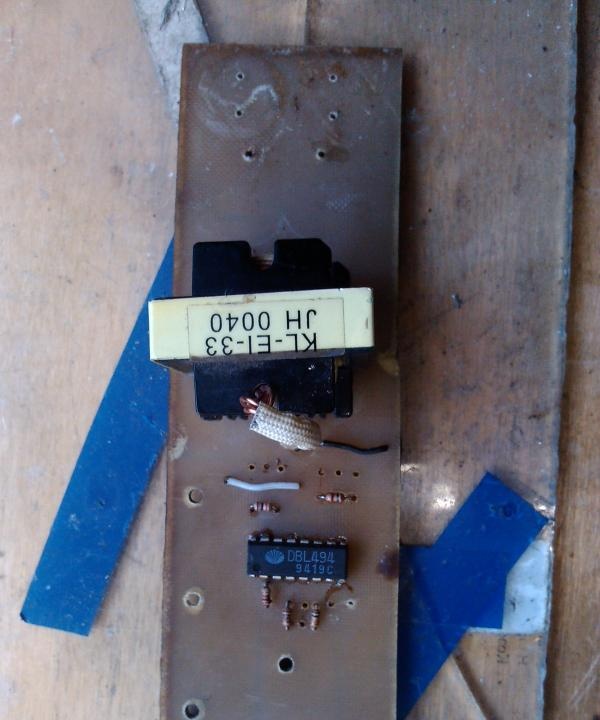
I started the assembly by installing a transformer, I used a step-down one of the blocks, I simply turned it over and instead of lowering the voltage from 400 V to 12 V, it raised it from 12 V to 268 V. By replacing resistors R3 and capacitor C1, it was possible to reduce the output voltage to 220 V, but further experiments showed that this should not be done.
After the transformer, in order of decreasing size, I installed the remaining spare parts.
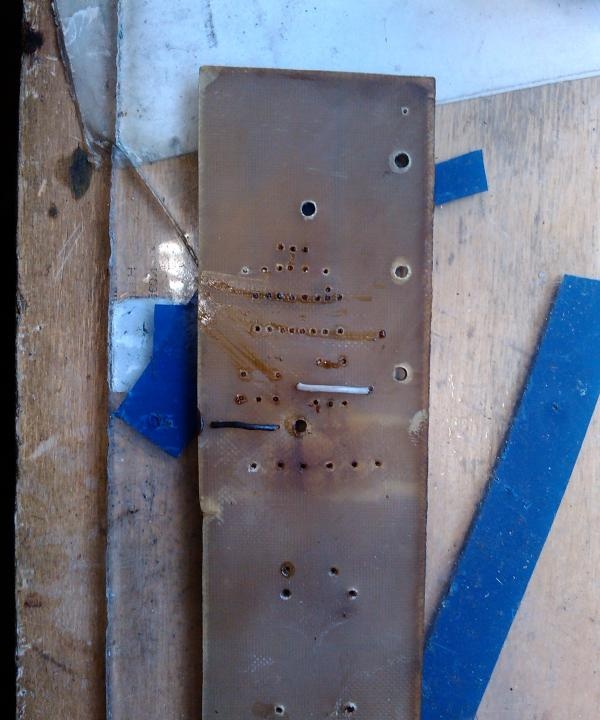
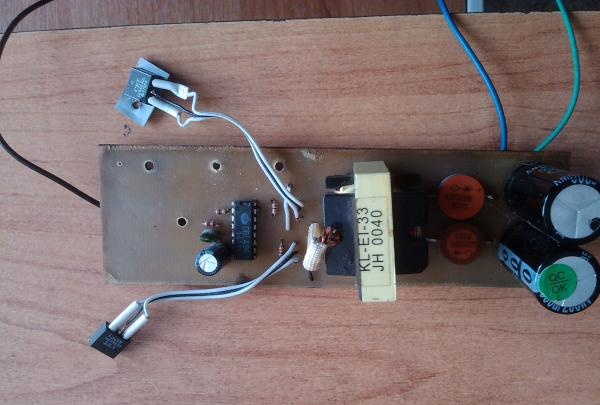
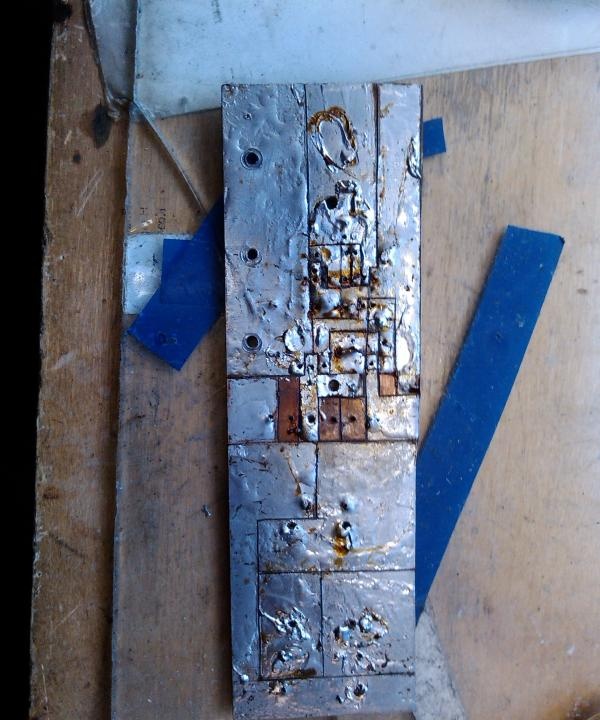
It was decided to install field-effect transistors on elongated inputs so that they are easier to attach to the cooling radiator.
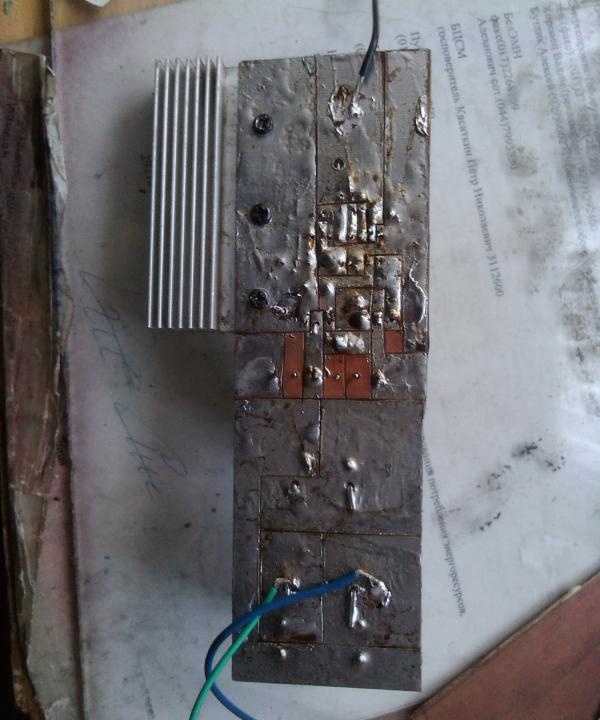
The end result is this device:
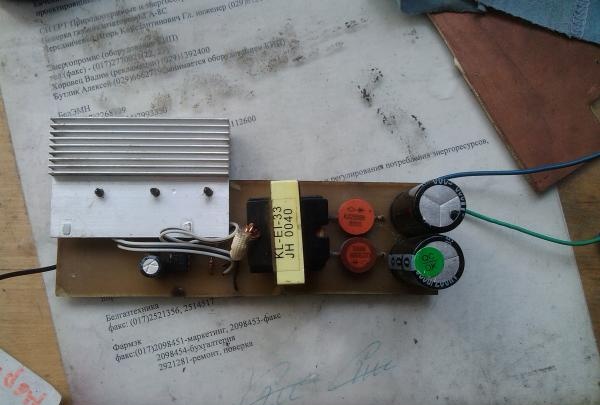
All that remains is the finishing touch - attaching the radiator. There are 4 holes visible on the board, although there are only 3 self-tapping screws; it was just during the assembly process that it was decided to slightly change the position of the radiator for a better appearance. After final assembly this is what we got:
Tests.
There was no time to specifically test the device; it was simply connected to the battery from an uninterruptible power supply. A load in the form of a 30 W light bulb was connected to the output. After it caught fire, the device was simply thrown into my backpack, and I went on a business trip for 2 weeks.
In 2 weeks, the device never failed. Various devices were powered from it. When measured with a multimeter, the maximum current obtained reached 2.7 A.
Similar master classes
Particularly interesting
Comments (24)