We install a metal profile fence
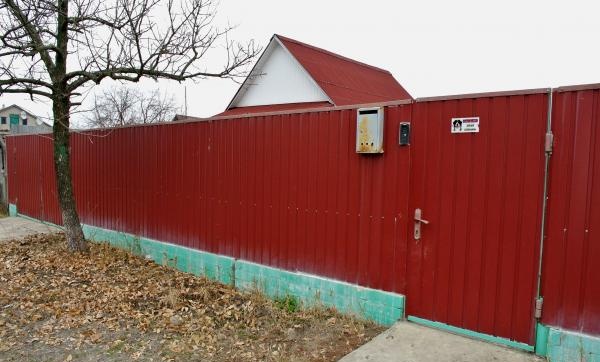
After acquiring the country house, a plan for its reconstruction was drawn up, the first point of which was the installation of a new fence. The old fence with a wicket and gate was wooden and very rickety - it was decided to demolish it. In order not to leave the area without a fence, the old fence was left until the work was completed. The new fence was placed half a meter in front of the old one - there was enough space for this.
Installation of a fence made of metal profiles
When choosing a material for the fence, various options were considered: brick, natural stone and ready-made concrete panels (the so-called Eurofence). The first two technologies were immediately abandoned due to their high cost and labor-intensive installation, and doubts arose about concrete panels about their strength. As a result, the choice fell on a fence made of profiled steel sheet mounted on a supporting frame.
To reduce the cost of reconstruction, most of the work that did not require specific skills was planned to be carried out on our own.Due to the lack of a welding machine at that time, the parts of the structure were connected using studs with nuts and washers. This somewhat complicates and delays the process, but in the end it saved an amount equal to half the cost of materials.
Design and calculation activities
Before starting work, the site was measured, a preliminary design was drawn up and the need for materials was calculated. The total length of the metal profile fence was 23.6 meters, the minimum height was 1700 mm. The plans included the installation of an entrance gate 0.8 - 0.9 m wide and an entrance gate 3.0 m wide. The movable elements of the fence are hinged and open outward.
After the calculations, a list of materials required for the construction of the fence was compiled, which includes the following items:
- Profiled steel sheet C-8x1150, dark red, 1.7 m long - 4 pieces and 1.5 m - 16 pieces.
- White silicate brick – 500 pieces.
- Portland 500 cement – 5 bags of 50 kg each.
- Washed and sifted quarry sand – 5 tons.
- Crushed stone of mixed fractions – 5 tons.
- Profiled steel pipe with a cross-section of 40x40 mm – 60 linear meters (l.m.), with a cross-section of 20x20x1.2 mm – 24 l.m.
- Steel angle 25x25x3.5 mm – 30 linear meters.
- Steel sheet 2 mm thick – 1 piece.
- Channel M12 – 4 pieces, 2.5 m each.
- Canopies - 5 pieces.
- Fasteners: 8 mm studs, M8 nuts, washers, self-tapping screws, aluminum rivets and M8 bolts with a large head for a screwdriver.
To carry out the fence installation work, the following tools were required:
- Bayonet and shovel shovels, buckets for bulk materials and water.
- Trough for mixing concrete.
- Angle grinder with cutting and sharpening wheels.
- Electric drill with a set of metal drills.
- Electric screwdriver.
- Device for installing rivets.
- Locksmith tools: wrenches, pliers, pliers, screwdrivers and nail puller.
- Tape measure, hydraulic level, plumb line, angle, cord and pegs.
- Electric extension cord 50 m long.
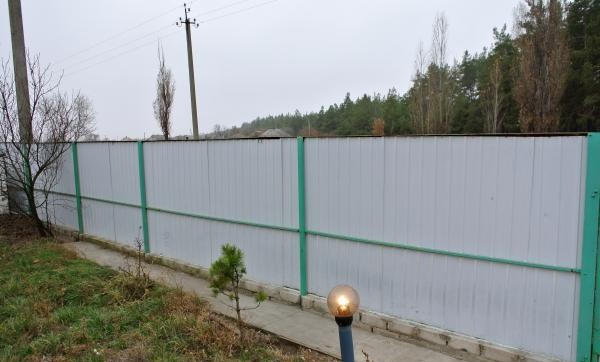
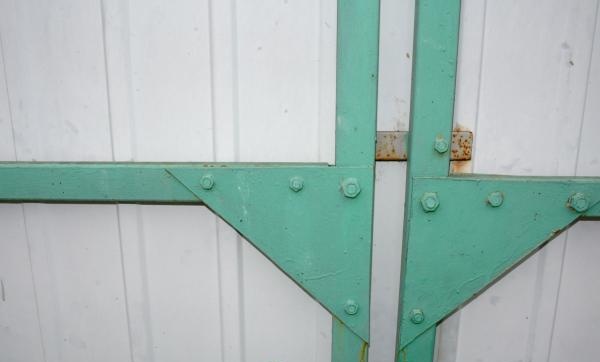
The materials were purchased from one company, which allowed us to reduce time and receive a small bonus in the form of delivery at the expense of the seller. Storage was carried out in the yard under a canopy to avoid getting wet in case of precipitation.
Site preparation and marking
The area in front of the old fence was cleared of vegetation and debris. At the extreme points, pegs were installed, connected to each other by a cord. Using a hydraulic level, zero marks were made, from which the height of the fence being built was measured. Additional pegs are installed in the places where the gates and wickets are installed. The spaces between them were divided into equal parts and also marked for the installation of pillars.
The next item in the work plan included preparing a trench for a sand and gravel bed and pits. The depth of the ditch should be at least 20 cm, and the depth of the holes for the posts should be about 80 - 90 cm. The excavated soil was evenly distributed over the area in front of the yard and leveled. The pillow was filled in two layers of equal thickness: first gravel, then sand flush with the earth's surface.
Support pillars 2.5 m long were installed in the two outer pits, so that their height was at least 1750 mm. After concreting the pits was completed, the vertical position of the pillars was checked using a plumb line.Crushed stone was added to the sand-cement mortar to increase strength. All posts were previously coated with a primer to protect against corrosion.
Cords were stretched between the installed posts at a level of 25 cm from the ground, indicating the height of the supports and brickwork. At this point, the preparatory activities were completed and it became possible to proceed directly to the installation of the fence.
Installation of posts and brickwork
At this stage, an assistant was needed whose tasks included mixing the solution and supplying materials. First of all, the columns were installed and concreted. The work was simplified by stretched cords. They marked the plane of the fence, and it was necessary to control the verticality of the installation only in one direction. In the places where the gates were installed, channels were installed and concreted.
In the spaces between the posts, brickwork was done at the level indicated by the bottom cord. The basis for it was the sand cushion poured and compacted at the previous stage. During the masonry process, a trowel and a special mason's hammer were used. The spaces for installing gates and wickets were left empty.
Installation of the load-bearing frame of the fence and covering with corrugated sheets
A corner was secured on top of the support posts using scraps of tubes with a diameter of 10 mm and a length of 15 mm, as well as M8 bolts and nuts. A profiled steel pipe was installed at a level of 50 cm from the brickwork. The installation of these elements with studs and nuts was carried out after preliminary drilling.
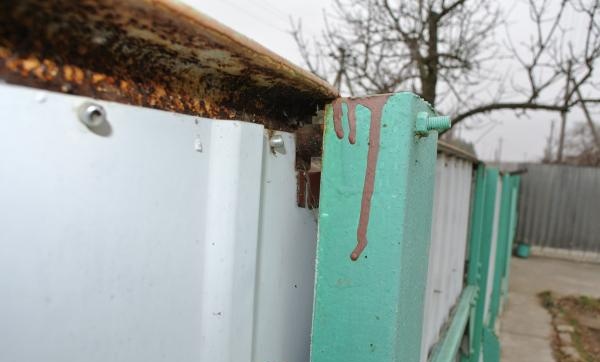
The corrugated sheeting was attached to the frame installed at the previous stage using rivets and self-tapping screws. This operation was carried out as follows: the sheet was wound around the corner and raised all the way up.In this position, it was fixed with the help of wooden wedges, which were installed spaced between the masonry and the corrugated sheet. Holes were drilled in the required places and the sheet was riveted to the corner and profile.
Manufacturing and installation of wickets and gates
This operation was carried out in two stages: the frames of the wicket and gate were assembled on an improvised slipway, and then hung and sheathed with corrugated sheets. The supporting structures consist of two vertical and two horizontal profiles with a cross-section of 40x40 mm, connected to each other using triangular-shaped overhead slopes. The corners were installed below using bolts and tubes.
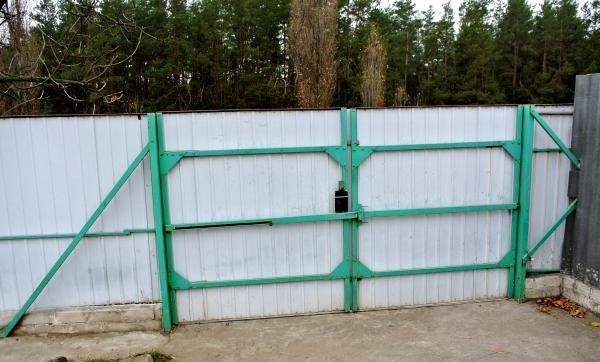
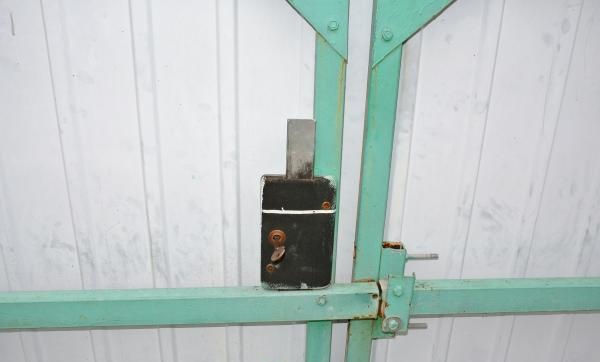
The wickets and gates were hung on ready-made separate canopies, one part of which was pre-mounted to the posts. The frames were installed and fixed using wedges. The edge of the sheet was wound around the lower corner, after which it was pressed against the upper corner that had been removed at that time and riveted to them. After this, the gate was equipped with a deadbolt, and the gate was equipped with a conventional mortise lock.
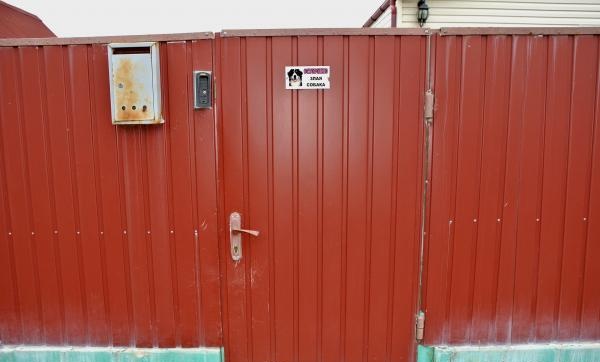
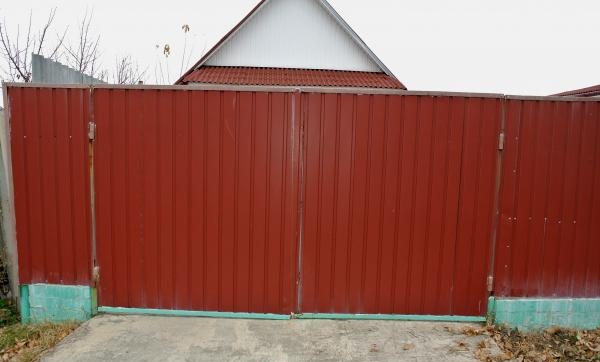
Subsequently, an intercom and a mailbox were installed at the entrance. During the work, the old fence was dismantled in parts, which made it possible not to expose the yard until the new fence was installed. As a result of almost ten days of effort, a pleasant-looking and, most importantly, very functional protective structure was obtained. A metal profile fence is one of the most affordable and reliable types of fencing.
Similar master classes
Particularly interesting
Comments (1)