Rocket plate
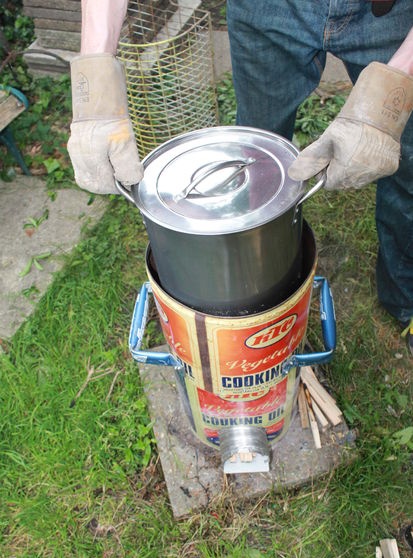
I love rocket stoves... For those who don't know, they are a great wood burning cooking device. The effectiveness of the idea lies in the fact that wood burns quickly and with high heat transfer. This way, you limit the spread of heat and direct it where it needs to go... On the pan!
Materials:
- Two 20-liter tin cans.
- Pot.
- Lots of wood ash.
- Corrugated 10 cm pipe (not aluminum).
- Sheet metal.
- A couple of metal pipes.
Tools:
- Metal scissors.
- Work gloves.
- Drill.
- Tool for installing rivets.
- Angle grinder (not necessary, but it will greatly speed up the work).
- Hacksaw.
It is imperative to wear work gloves when working, since the manufacturing process involves cutting metal, and without them you can injure your hands!
More details about board materials
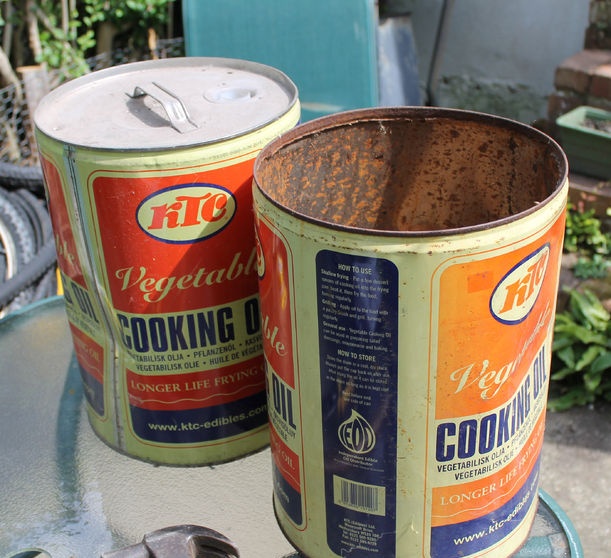
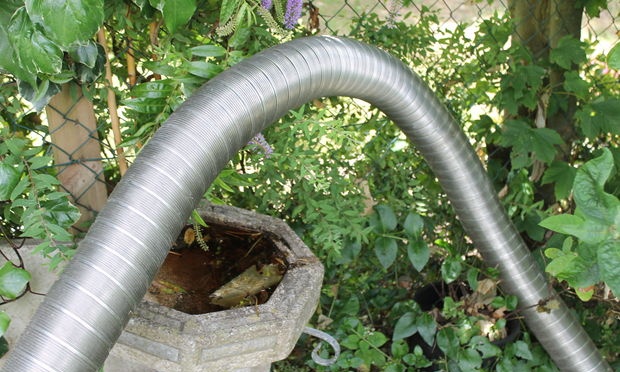
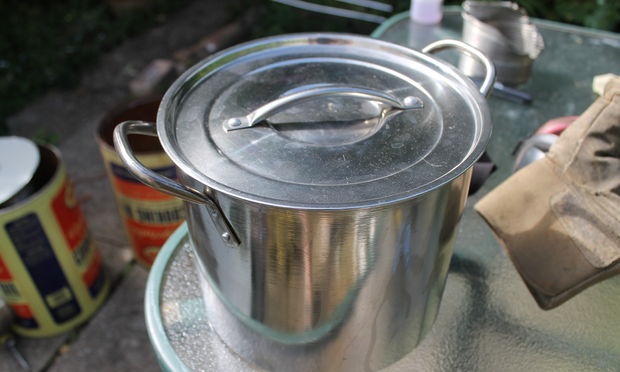
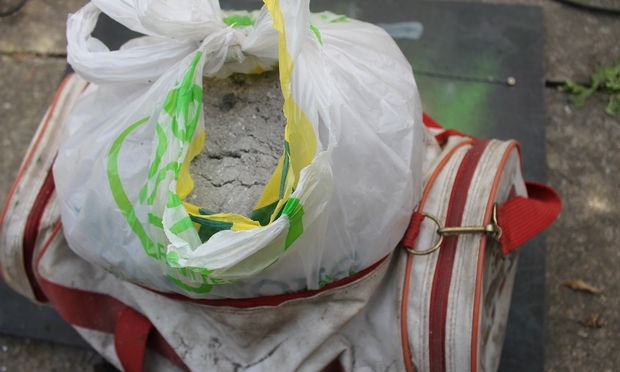
I suppose the rocket plate could be made from anything, but I happened to have some 20 liter tin cans and decided to use them as the body.
The firebox can be made from anything, and in fact, a rectangular shape is more efficient... But corrugated pipe is easier to work with.
This is not an aluminum pipe, which will quickly burn, but a stainless steel one, which is used as a chimney. You can use whatever is convenient for you. I've met people who managed to make a firebox out of regular-sized tin cans.
The saucepan for the stove should fit well in size, preferably 2 cm smaller in diameter than the stove body. The handles should not be plastic, otherwise they will melt. It is also important that there is a suitable lid, because we know that everything boils faster with a lid. It would be better to have two small handles on the sides than one long one, because this way it will take up less space.
I used wood ash as an insulating material, but you can use anything that has good thermal insulation properties and does not burn. I've heard that people sometimes use vermiculite. I like wood ash because it's free and makes the stove quite heavy and therefore more stable.
Metal cutting
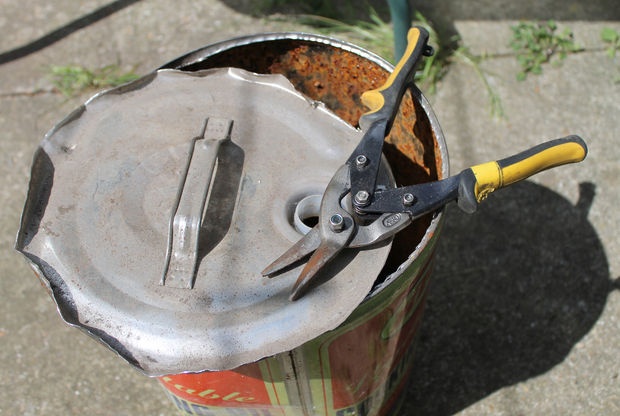
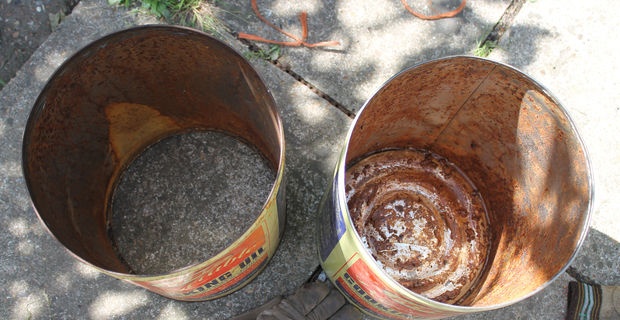
Cut off the top of the tin can. To make a hole you will need a chisel and a hammer, then use metal scissors.
As you work, remember that you are dealing with sharp edges. At all stages of production, I wore protective gloves and constantly filed off anything sharp.
In the second jar, cut off both the top and bottom parts.
Making the body and pipe
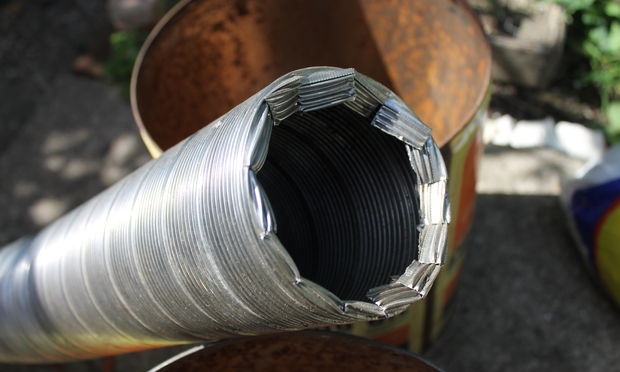
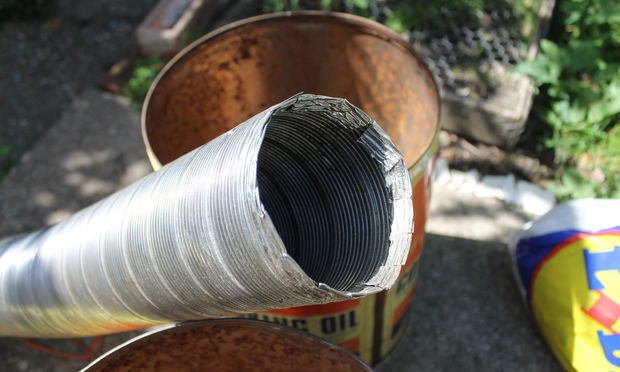
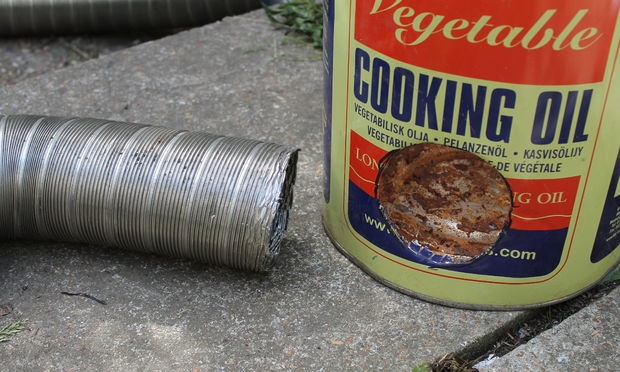
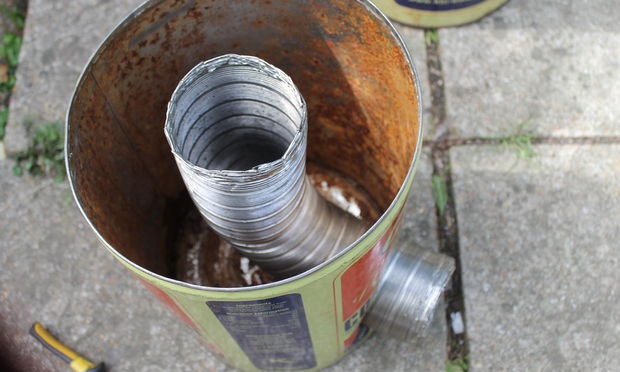
We cut the required length of the corrugated pipe using a hacksaw and metal scissors.
Then we make small cuts on its edge and, using pliers, align the resulting blades and bend them inward (look at the photo).
This is done so that the edges are not sharp and it is difficult to cut yourself on them when lighting a fire.
Now we cut a hole in the bottom of the jar for the corrugated pipe. In the side part 3 cm above the bottom will be enough.
Insert the pipe into the hole and make a bend. The bending angle should be made quite sharp, while the pipe should remain in the center of the can (see photo below).
Making a lid
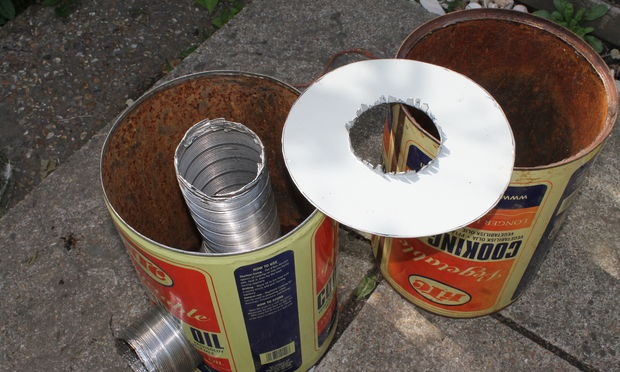
For this purpose, you can use the bottom or top of the can that we cut out earlier. But I used sheet metal that I had on hand.
We cut out a sheet that will exactly follow the shape of the can, with a large hole for the pipe. This can be easily done using an angle grinder or other tool.
The sheet should cover the jar tightly, but you don't have to worry too much about this, since the wood ash will shrink quite well to maintain the stability of the structure.
Insulation
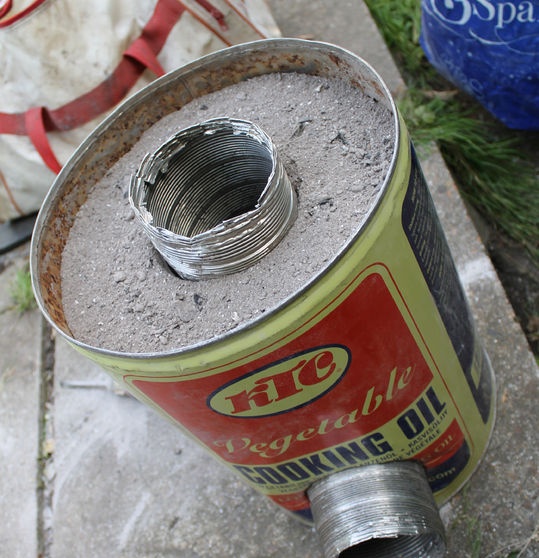
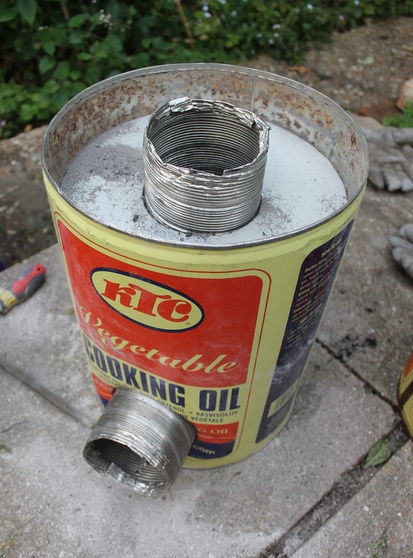
Time to fill the cavities with insulating material.
Especially for these purposes, I collected enough wood ash, which has excellent thermal insulation properties. But it must be dry.
The ashes should lie quite tightly, the main thing is that there are no nails or other heat-conducting materials in it. Compact it and if you come across large pieces of coal, remove them.
Ash may initially seep out from where the corrugated pipe meets the tin, but don't worry about this. Over time, it will lie so tightly that it will no longer get enough sleep.
After filling the oven with insulating material, cover the body with a lid.
We make the heating surface of the furnace
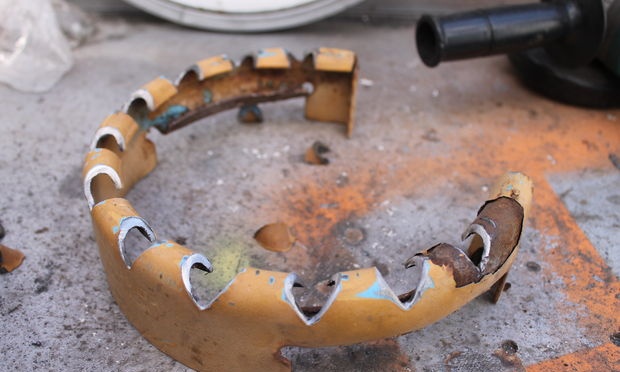
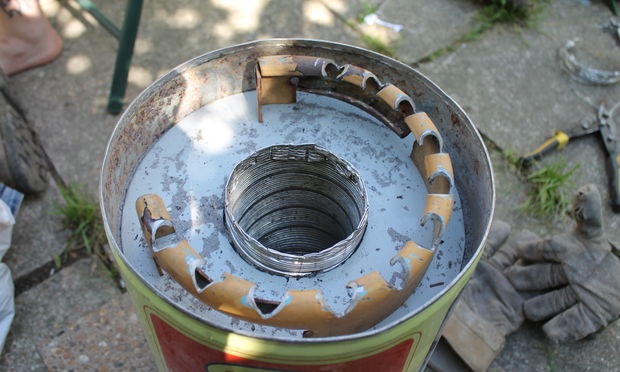
Some people design rocket stoves in such a way that the heated dish is directly on the pipe, to do this, several slits are made on the edge of the pipe so that air can flow freely.
I prefer to make the heating surface from a gas cylinder. I cut off part of it so that there is a space of 20 mm between the top cut of the pipe and the bottom of the pan. Then I make several slits so that air and fire can flow freely and evenly around the pan.
This design will be much stronger than a corrugated pipe. A plus will be the waste-free use of a used gas cylinder if you want to make another stove from the rest of it.
Making the furnace casing
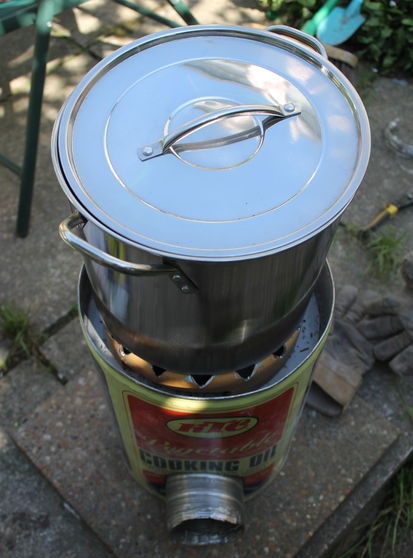
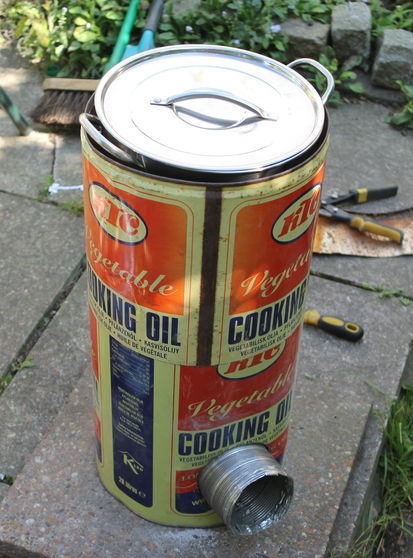
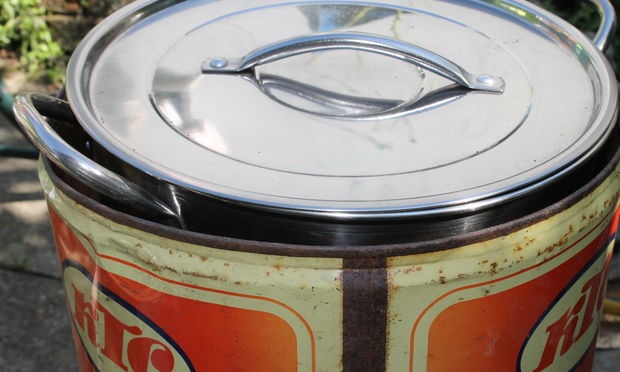
Now we have an insulated fire that will be directed to the bottom of your pan.
To more effectively distribute heat over its surface, we need to make a casing. This will allow the heat escaping from the oven to flow past the sides of the pan, thus increasing heat transfer.
We make the height of the casing in accordance with the size of your pan. We cut off part of the second can so that it fits onto the second, and the handle of the pan rests freely above its upper cut.
Place the second can on top of the first. You may have to use a hammer for this.
Stove handles
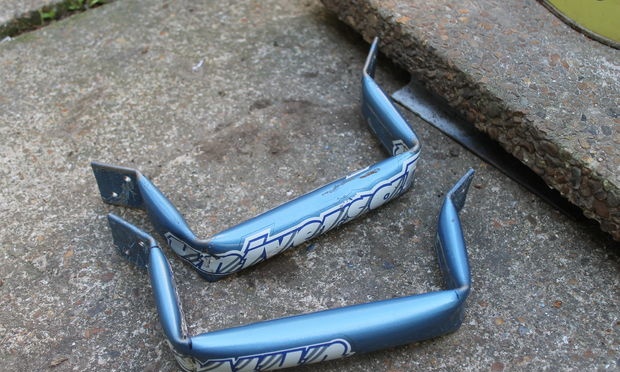
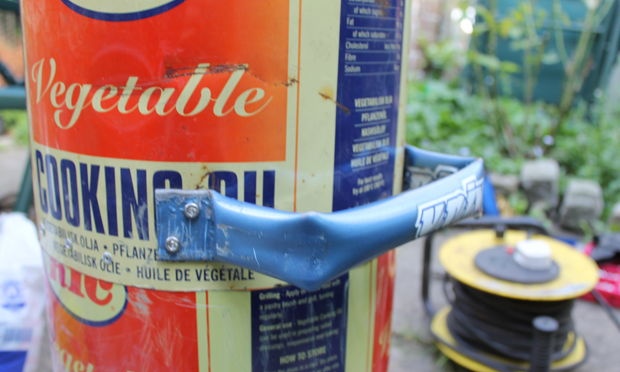
The resulting rocket stove may turn out to be quite heavy, and it will be more convenient to carry it with the help of handles.
Some people prefer the cover to be removable. This way you can put a frying pan and other utensils on the fire. I chose to use just my chosen pan. This made it possible to secure the casing to the stove body and screw the handles to it.
To make the handles, I used a bicycle frame, gave the pipes the required shape, drilled several holes and screwed them to the stove. To attach the handles, I chose a place where two cans overlap each other to make the structure more durable. In addition, I fastened the cans with rivets.
Shelf for firewood
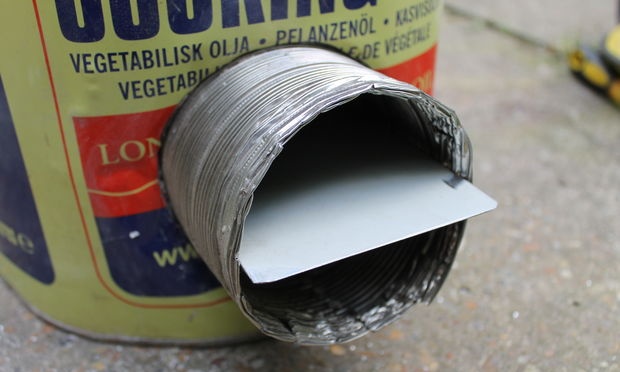
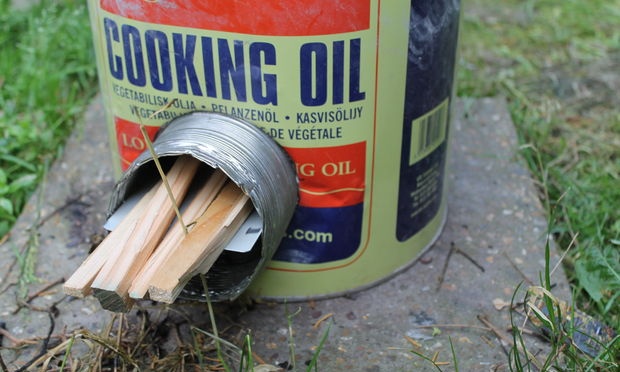
When I made my first stove, I left out this detail because I thought it wasn't needed. Wrong. It is necessary.
You need to cut a plate from a sheet of metal that will be inserted into the corrugated pipe and stick out a little from it.
This way, the wood will be fed above the top of the plate, and the air will flow from below, allowing the wood to burn well.
Very simple, but very important.
Testing the finished slab
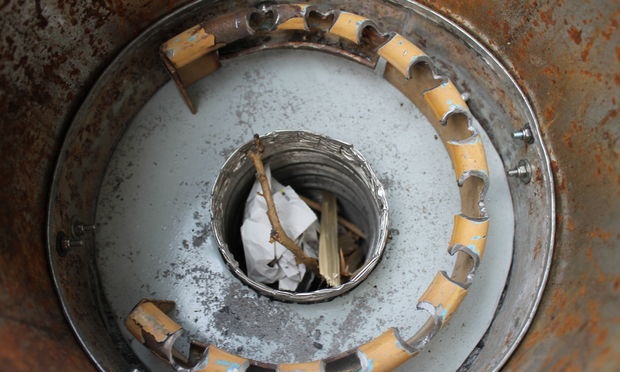

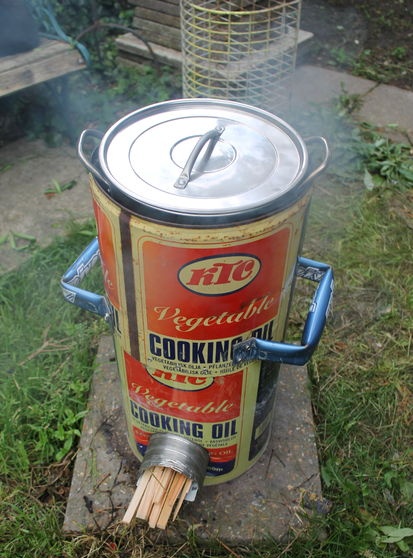
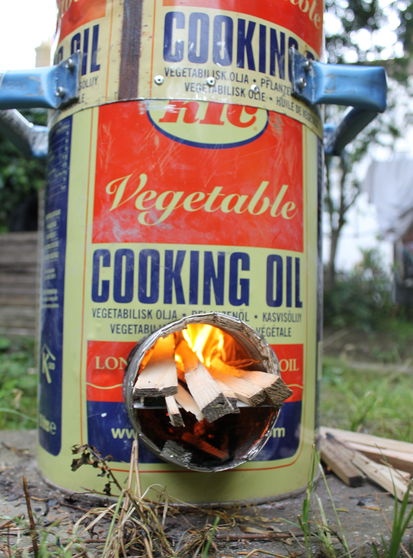
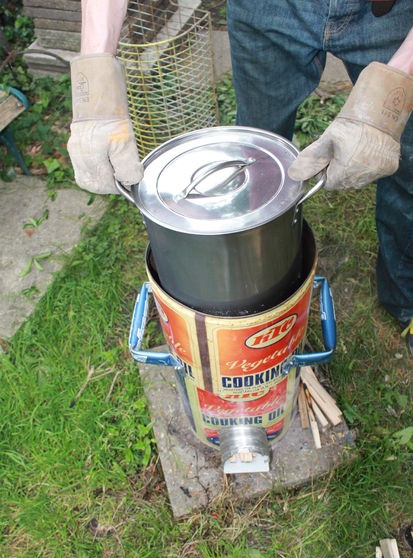
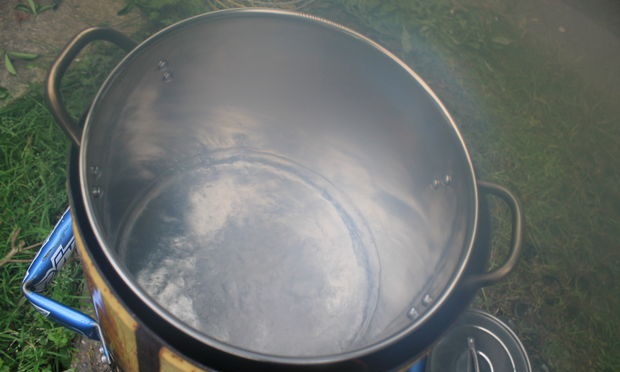
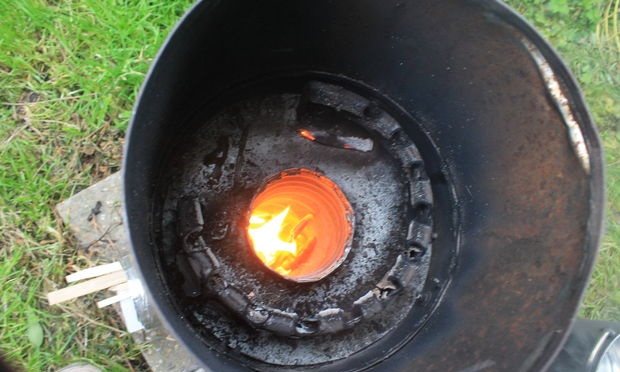
First, position the stove so that the firewood chamber faces the wind. The wind will allow the fire to burn better.
To begin, the stove is filled with fuel through the top of the pipe. You can use some paper and thin dry wood chips.
We bring the fire, let it burn for about a minute.
Then we feed the firewood over the shelf through the side pipe. Tree above, air below.
We put a pan, it will limit the air flow, which will create better draft.
Firewood in such a stove burns quickly, and it is better to use small pieces of wood. They can be pushed inside with a stick.
The bark does not burn well, so it is better not to use it as fuel. Dry pine wood will be just right.
On the first test, the water boiled in three minutes and required some firewood. The result can be considered successful.
No smoke, no ash - burns well.
P.S. It may be obvious, but only dry wood ash serves as a heat insulator.Therefore, you should not leave the stove in the rain.
Original article in English
Similar master classes
Particularly interesting
Comments (1)