Lubrication of a maintenance-free computer cooler
In older computers, operating noise increases, which is associated with the grinding noise of the cooler bearing. This is an elementary problem that can be solved without replacing it with regular lubricant - which is what I will do.
Required inventory
To work you will need:
- Silicone Grease;
- crosshead screwdriver;
- drill 1 mm;
- medical syringe with a needle.
As for silicone lubricant for computer fans, it is usually sold in small bottles, such as cold drops. If you do not repair equipment professionally, then it is better to buy it in smaller containers. In stores that sell computer parts, lubricant can often be purchased directly in a syringe.
If specialized silicone grease is too expensive or simply cannot be obtained anywhere, you can use ordinary oil for sewing machines and keyholes. You only need to add a drop.
How to lubricate a cooler
The cooler must be removed from the system unit. The only tool you need is a screwdriver. In addition to lubrication, it is also better to clean the chipset heatsink, and it is advisable to change the thermal paste on it.
As for the cooler itself, there is a round sticker on the back of it, where the diffuser captures air. If you remove it, then in most models you can see an inspection hole for manual lubrication. In my case there is none.
The easiest way is to try to pull out the cooler impeller and coat the bearing on the back side. Sometimes it can be easily removed, but this did not work for me, everything is held very tightly. If you apply excessive force, the plastic will simply break.
In this case, extreme measures are needed. I take an ordinary metal drill with a diameter of 1 mm. For convenience, I built a simple clamp, since I don’t have a miniature collet, which modellers use when assembling copies of ships and airplanes. Using a drill, I cut a miniature hole right in the center of the lid where the sticker was. You need to work carefully so that chips do not get inside.
Next, I simply pour a few drops of silicone grease into the hole and rotate the impeller to evenly lubricate the bearing.
To prevent oil from spilling, the sticker must be glued back, closing the hole. If it no longer sticks, you can use electrical tape or tape instead.
Having done everything correctly, if no chips or grains of dust got inside when drilling a hole, then the noise will go away, as will the heating of the cooler electric motor, since friction and resistance will decrease. After this, you can forget about the grinding noise, at least for several years.
Watch the video
Similar master classes
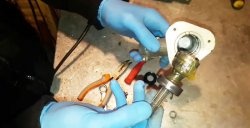
Complete disassembly of the brush cutter gearbox to remove wear products
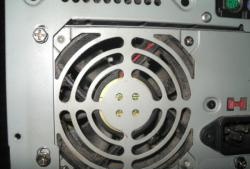
An easy way to eliminate computer noise
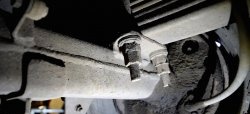
The most powerful penetrating lubricant
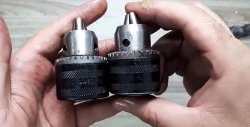
How to disassemble and lubricate a drill chuck
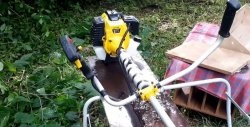
How and with what to lubricate the shafts in the mower bar
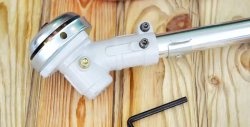
How to lubricate the gearbox of a brush cutter in a simple way
Particularly interesting
Comments (10)