Complete disassembly of the brush cutter gearbox to remove wear products and replace lubricant
How to use lubricant to push back the repair of a lawn mower gearbox? Whatever the brand of brush cutter, the second most important component after the engine is the gearbox, consisting of two helical gears, the smaller of which is the drive gear, the larger one is the driven gear.
The gearing, rotating in the bearings, is located in a housing consisting of two symmetrical halves, and tightened together with bolts. The drive gear receives rotation from the engine along a rod that ends with splines (usually there are 7 or 9 of them), the driven gear transmits rotation to the spindle, which serves to attach the working element - a drum with fishing line, cables or a cutting disk.
The gear bearings on the spindle side are sealed with an oil seal that protects the bearings and the lubricant in them from contamination. To replenish it, there is a bolt on the body; by unscrewing it, you can add lubricant during operation of the tool.
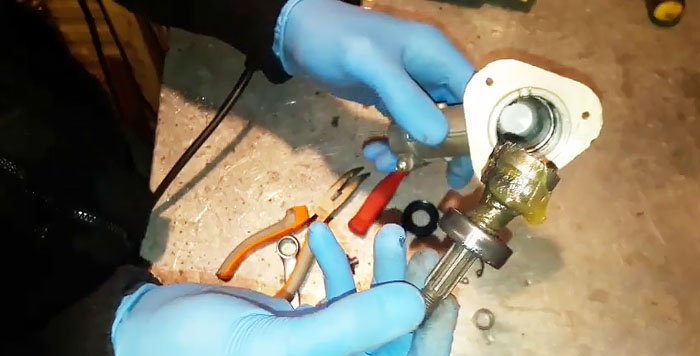
Regular lubrication of the gears of the brush cutter gearbox is so important that it is worth discussing separately.If you exclude working with a cutting disc, when it clings to a stone or curb and sends a counter shock pulse to the gearbox, which leads to breakage of the driven gear tooth, parts of which gradually damage the entire engagement, lubricant can delay the repair of this important unit and extend the service life by several once.
To do this, disconnect the casing and the rod with the shaft inside from the gearbox. We remove the working element from the spindle and wash the gear assembly to make it more convenient to disassemble it.
We unscrew the bolt-plug, but it can be left in place, since it does not carry any power load.
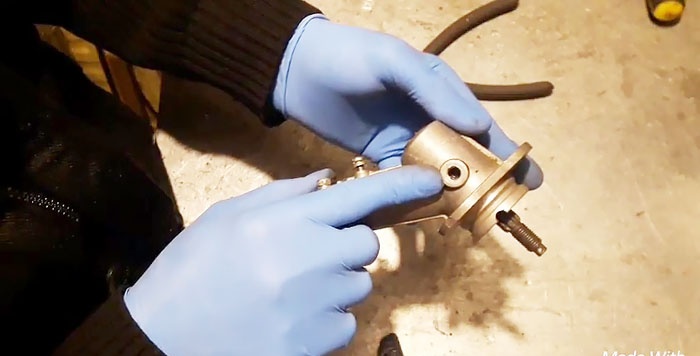
Then we remove the drive gear from the housing. To do this, using a special puller, remove the retaining ring from the annular slot, which holds the drive gear block in the desired position in the housing.
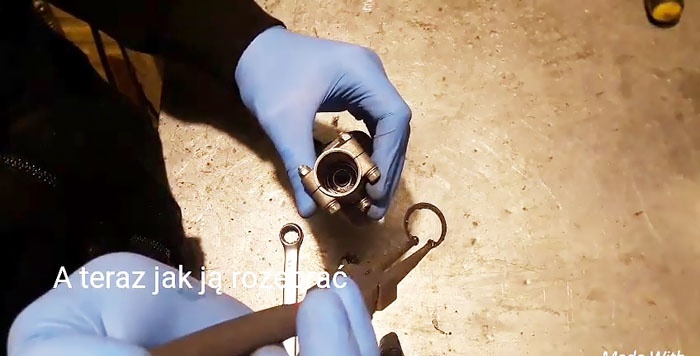
Since the bearings with their outer ring are installed in the seats with interference, they are not easy to remove. To make this task easier, we heat the gearbox housing in the area of the bearings with a hair dryer.
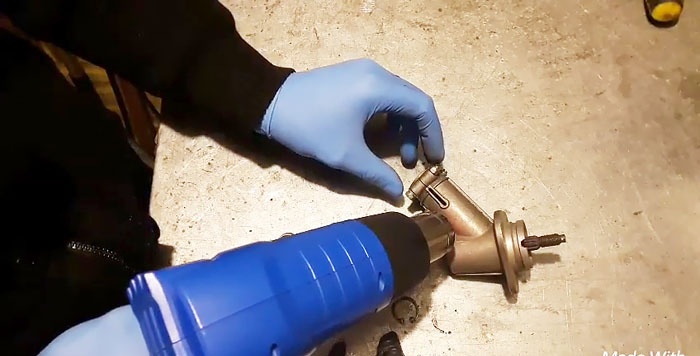
As soon as the metal of the housing heats up, it will expand and the interference will disappear. Now you can easily remove the drive helical gear unit with two identical paired bearings from the housing.
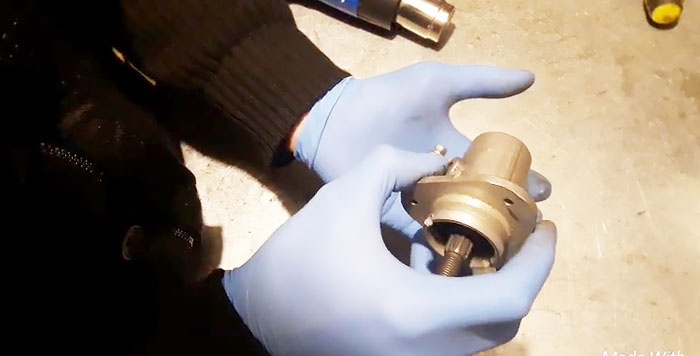
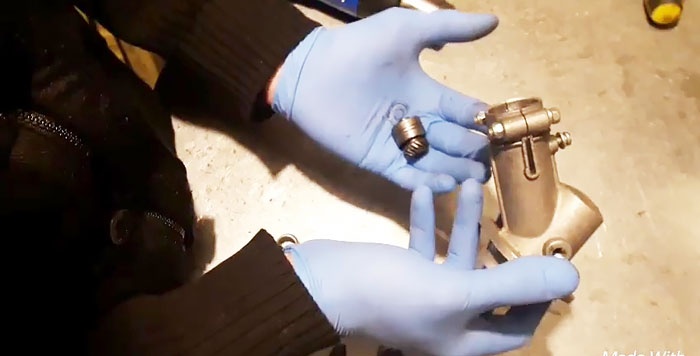
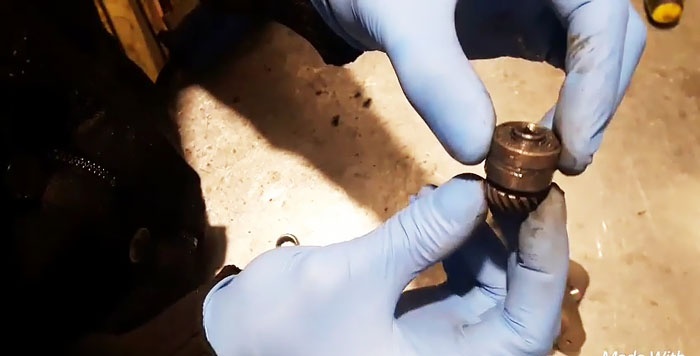
We begin to remove the driven gear unit with the spindle from the gearbox housing. Here, we first remove the centering sleeve using pliers with narrow jaws, then the oil seal, prying it off with a screwdriver or some other suitable tool.
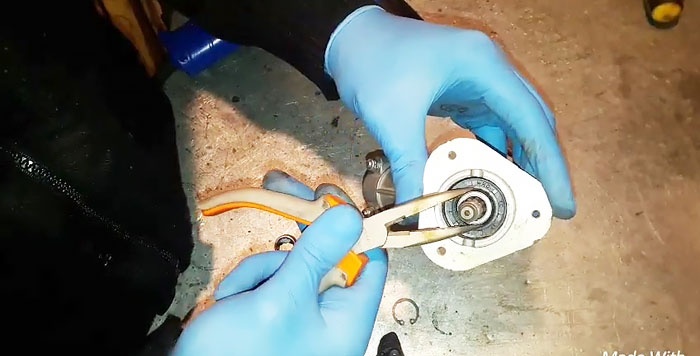
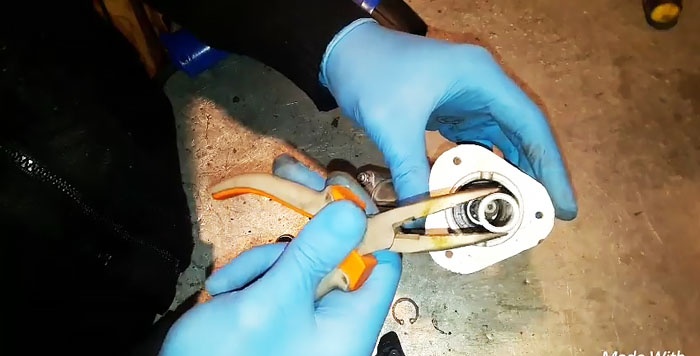
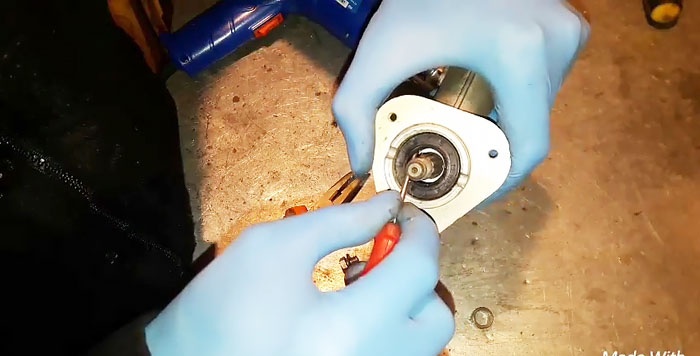
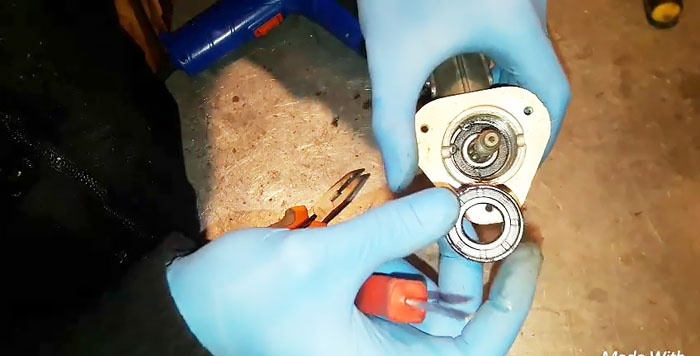
Also, as in the first case, we pull out the retaining part by squeezing it with a snap ring remover, using the holes in the lock for this.
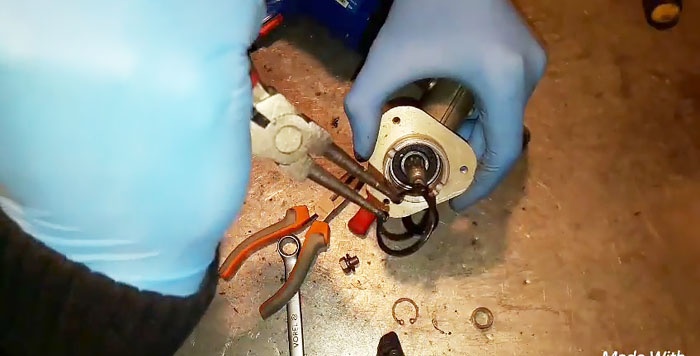
We heat the gear housing with a hairdryer in the area where the bearings of the driven gear block are located and after a while we pull it out by slightly pulling the spindle.
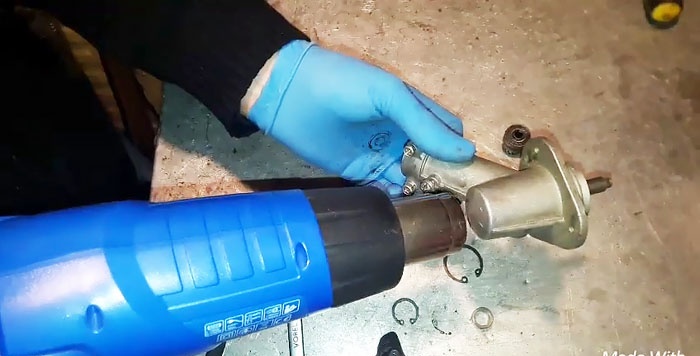
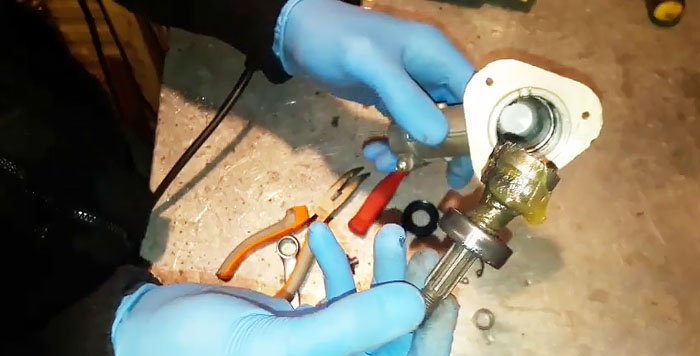
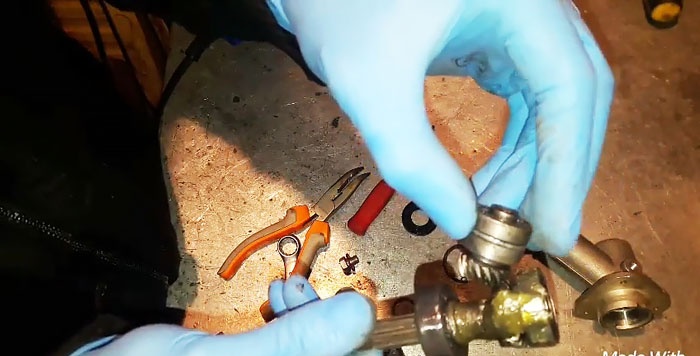
Once you are satisfied that the gears, bearings, circlips and seal are in order, you can begin to completely flush and re-lubricate the gearbox. If damaged parts are found, they must be replaced with similar ones.
Notice how much wear debris is on the sides of the head housing.
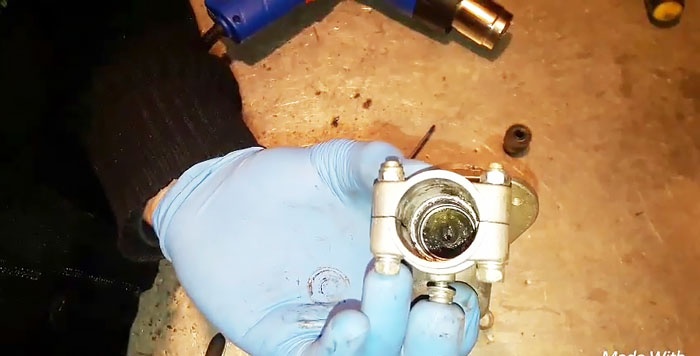
Gearbox design and lubrication
The gearing, rotating in the bearings, is located in a housing consisting of two symmetrical halves, and tightened together with bolts. The drive gear receives rotation from the engine along a rod that ends with splines (usually there are 7 or 9 of them), the driven gear transmits rotation to the spindle, which serves to attach the working element - a drum with fishing line, cables or a cutting disk.
The gear bearings on the spindle side are sealed with an oil seal that protects the bearings and the lubricant in them from contamination. To replenish it, there is a bolt on the body; by unscrewing it, you can add lubricant during operation of the tool.
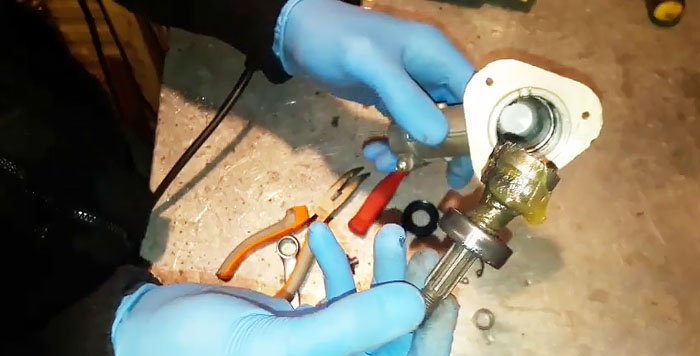
Regular lubrication of the gears of the brush cutter gearbox is so important that it is worth discussing separately.If you exclude working with a cutting disc, when it clings to a stone or curb and sends a counter shock pulse to the gearbox, which leads to breakage of the driven gear tooth, parts of which gradually damage the entire engagement, lubricant can delay the repair of this important unit and extend the service life by several once.
Disassembling the gearbox to check it and replace lubricant and wear particles
To do this, disconnect the casing and the rod with the shaft inside from the gearbox. We remove the working element from the spindle and wash the gear assembly to make it more convenient to disassemble it.
We unscrew the bolt-plug, but it can be left in place, since it does not carry any power load.
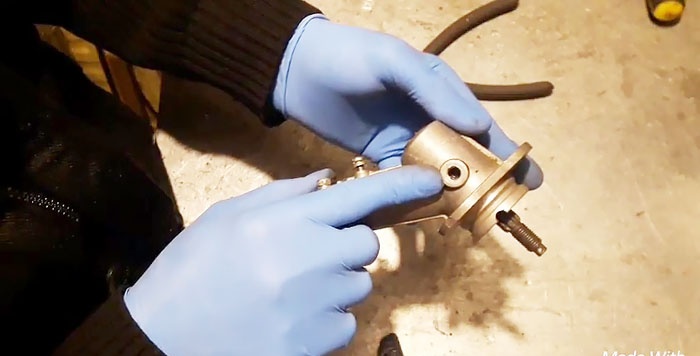
Then we remove the drive gear from the housing. To do this, using a special puller, remove the retaining ring from the annular slot, which holds the drive gear block in the desired position in the housing.
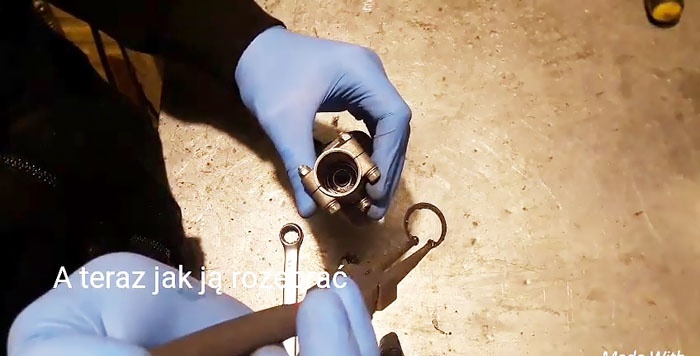
Since the bearings with their outer ring are installed in the seats with interference, they are not easy to remove. To make this task easier, we heat the gearbox housing in the area of the bearings with a hair dryer.
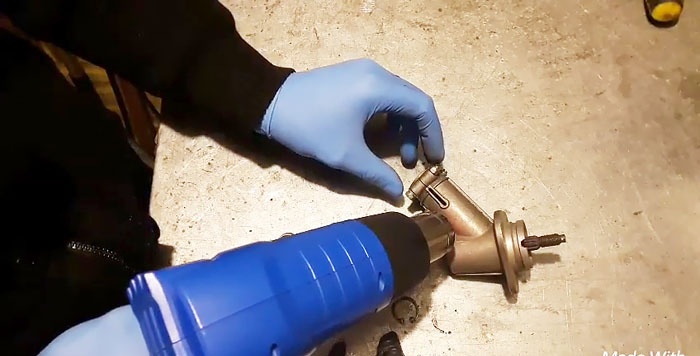
As soon as the metal of the housing heats up, it will expand and the interference will disappear. Now you can easily remove the drive helical gear unit with two identical paired bearings from the housing.
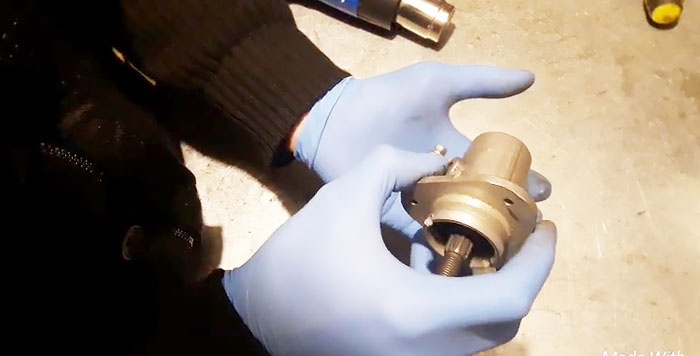
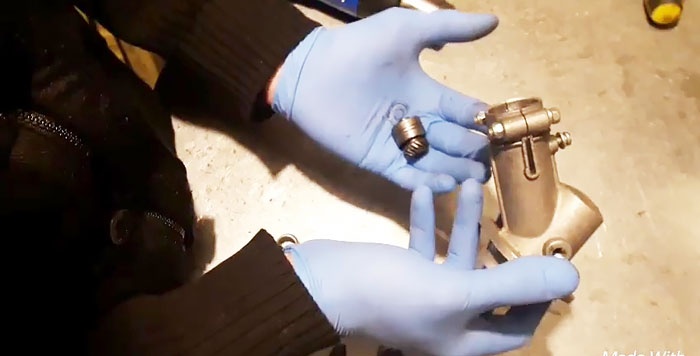
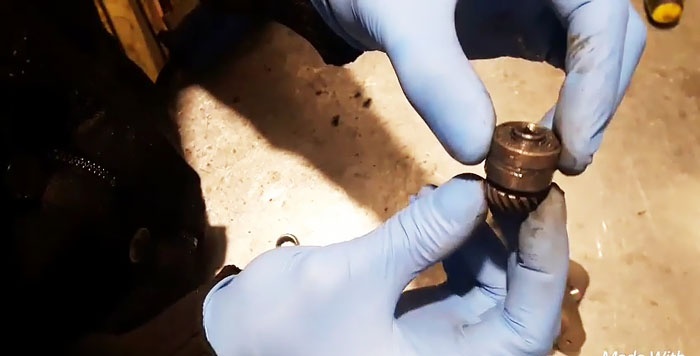
We begin to remove the driven gear unit with the spindle from the gearbox housing. Here, we first remove the centering sleeve using pliers with narrow jaws, then the oil seal, prying it off with a screwdriver or some other suitable tool.
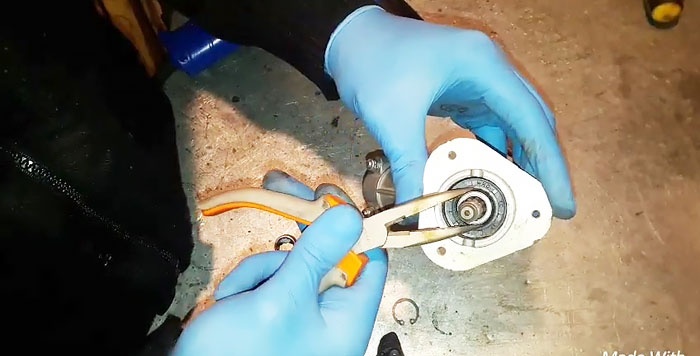
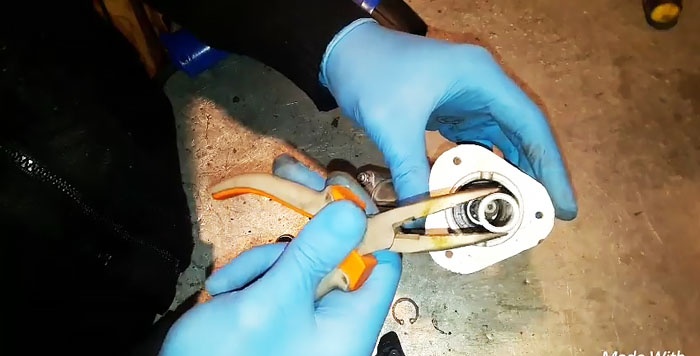
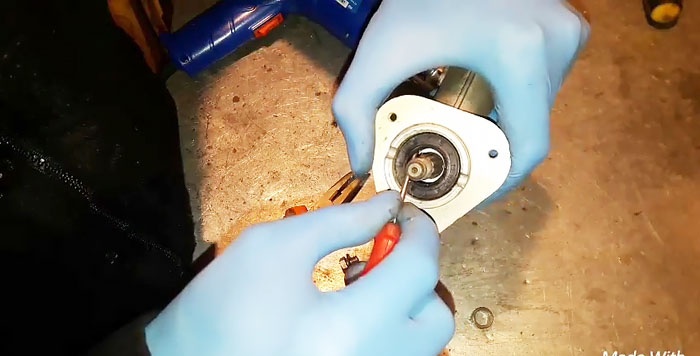
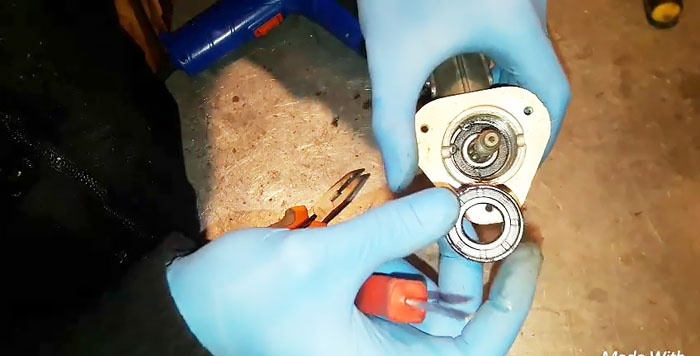
Also, as in the first case, we pull out the retaining part by squeezing it with a snap ring remover, using the holes in the lock for this.
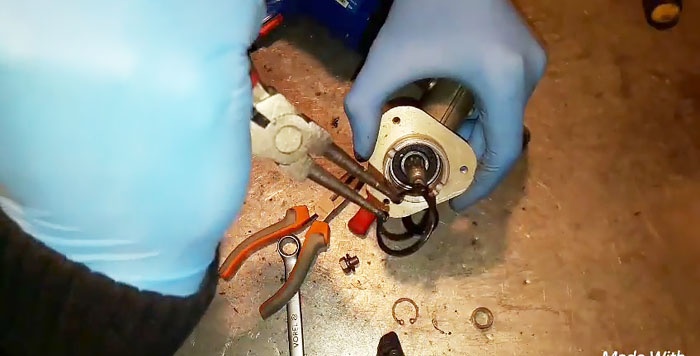
We heat the gear housing with a hairdryer in the area where the bearings of the driven gear block are located and after a while we pull it out by slightly pulling the spindle.
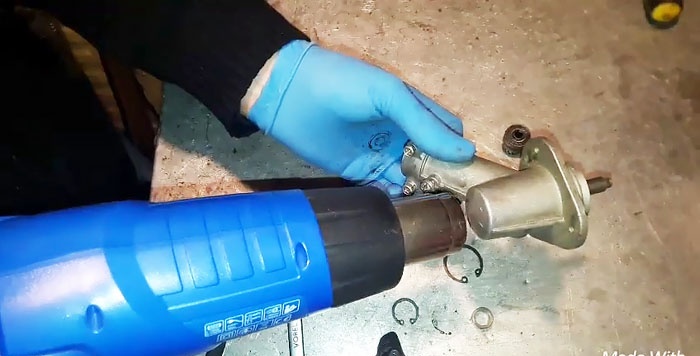
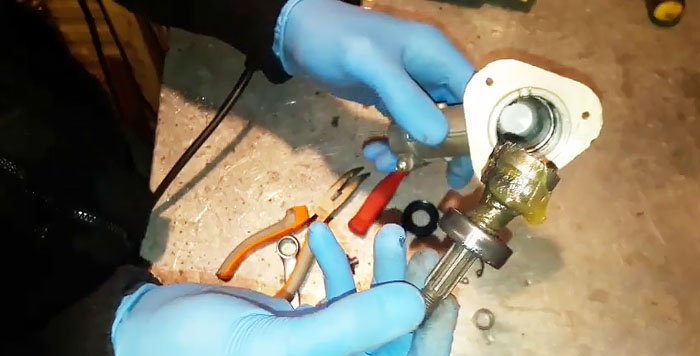
In custody…
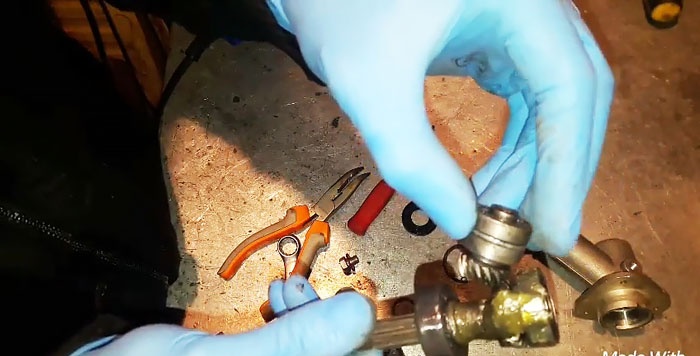
Once you are satisfied that the gears, bearings, circlips and seal are in order, you can begin to completely flush and re-lubricate the gearbox. If damaged parts are found, they must be replaced with similar ones.
Notice how much wear debris is on the sides of the head housing.
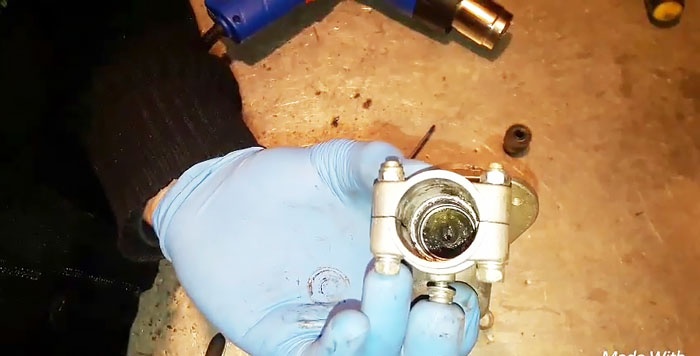
Watch the video
Similar master classes
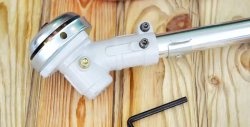
How to lubricate the gearbox of a brush cutter in a simple way
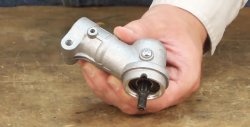
Replacing the lower gearbox of a brush cutter (trimmer)
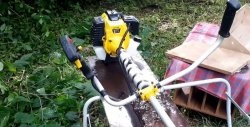
How and with what to lubricate the shafts in the mower bar
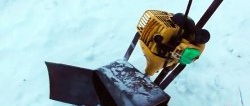
Do-it-yourself snow blower from a brush cutter
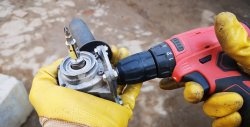
A device for a screwdriver from the gearbox of a broken angle grinder
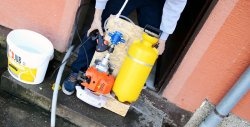
Homemade motorized sprayer from a brush cutter
Particularly interesting
Comments (0)