How to drill a quick cutter - P18 steel
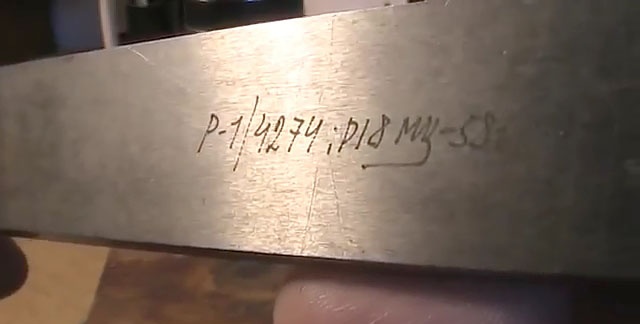
It is possible that a metal processing specialist will have to drill into P18 high-speed steel. To do this, you will need a drill whose characteristics must exceed the material being processed.
Quick cutter P18 is a tool steel that is used for the production of cutters, drills, milling cutters, reamers, broaches, etc. They can be used to process structural steels with a strength of up to 1 thousand MPa.
Materials and tools used
For our practical experiment we will need:
- Detachable turning tool made of P18 steel, manufactured back in 1958.
- Not a new feather drill with a diameter of 5 mm for ceramics and glass.
- Tabletop drilling machine with adjustable spindle speed.
- Emery machine for sharpening tools.
- Calipers.
- Rough file for metal.
- A piece of square rod made of P18 steel.
- Cutter made of steel R6M5.
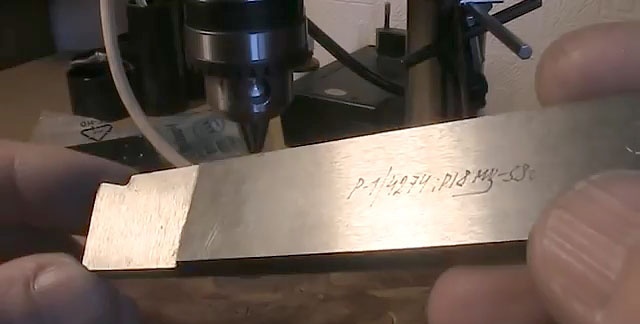
Test process
For the experiment, we settled on a cutting tool made of P18 steel, which was manufactured during the Soviet Union, which is a reliable guarantee of its high quality. This is a fairly durable material.In addition to turning cutters, various tools are made from it, which are used to process structural steels and other metals.
The test tool was a 5mm diameter second-hand point drill bit made in China, which is commonly used on metal, ceramics, glass and stone.
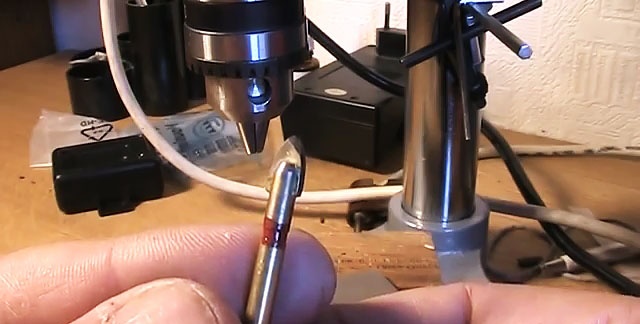
To restore the cutting characteristics of this drill, we will slightly correct it on a mechanically driven grinding wheel.
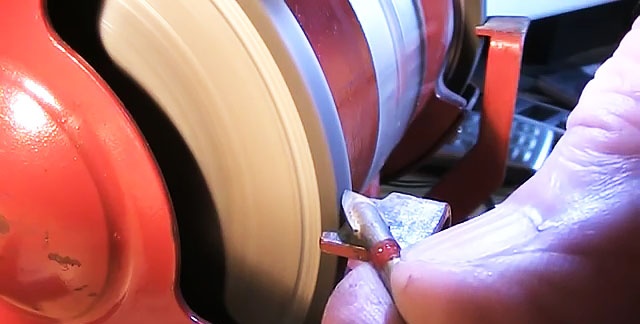
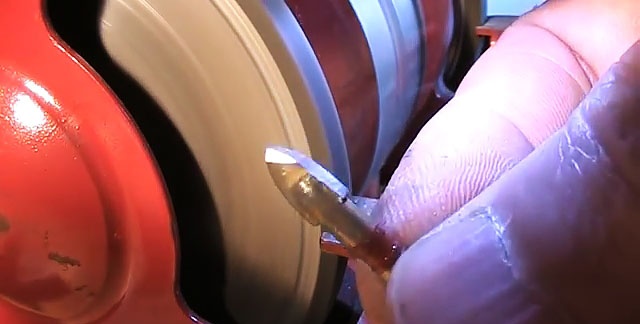
We insert the drill into the chuck of the benchtop drilling machine and clamp it securely with a key.
For reference, use a caliper to measure the thickness of the cutting part of the cutting tool. It turned out to be equal to 3.5 mm.
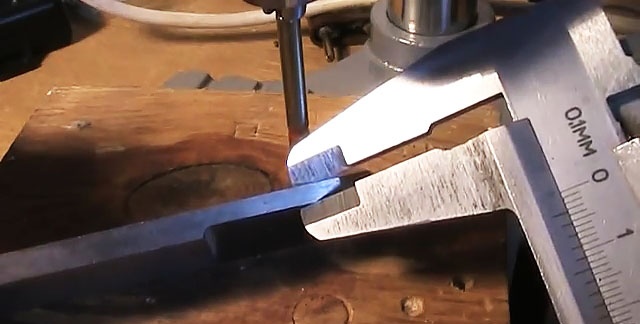
We make sure that the vertical stroke of the spindle is sufficient to carry out through drilling of the cutter. To do this, you need to make sure that the end of the drill reaches the plane of the base and there is still some power reserve.
We begin drilling, releasing pressure on the tool from time to time. This is necessary to at least partially cool it and clean it from chips and metal particles formed during drilling.
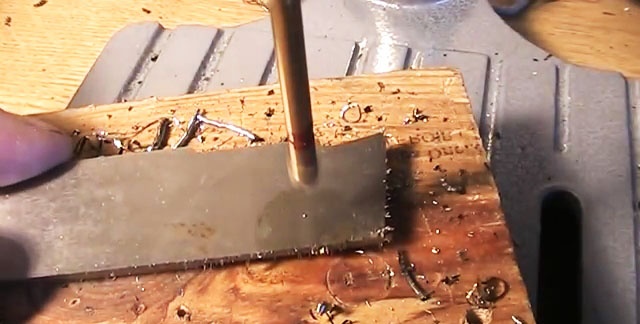
At the moment when the top of the tool comes out from the opposite side, we stop the process and turn the cutter over to the other side. We place the drill on the mark and complete the process.
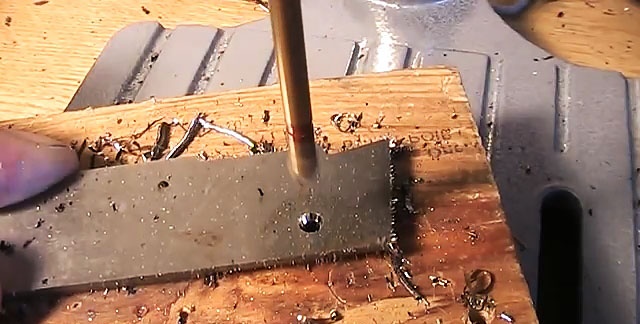
The through hole in the area of the cutting part of the cutting tool made of P18 steel is ready! We spent no more than 2-3 minutes on this, without making much effort, without complications, and with just one sharpening of the drill.
A rough hand file for metal, of course, is not suitable for processing P18 steel, unless it can be used to remove burrs formed during the drilling process.
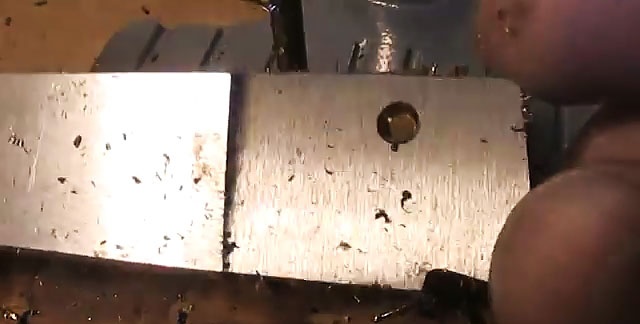
To check the results obtained, we take a square rod made of P18 steel, drill it and make sure that the processing process and its results remain the same, no different from the first time.
Let's try using the same drill without regrinding to drill a square, or better yet, a cutter made of high-speed steel R6M5, which has higher cutting properties than tools made of steel R18, especially in terms of the permissible operating temperature. And the drill copes well with this material.
Surprisingly, an ordinary cheap Chinese 5-mm tip drill, which is designed primarily for working with ceramics and glass, easily drills not only high-speed tool steel P18, but also more durable grade P6M5.
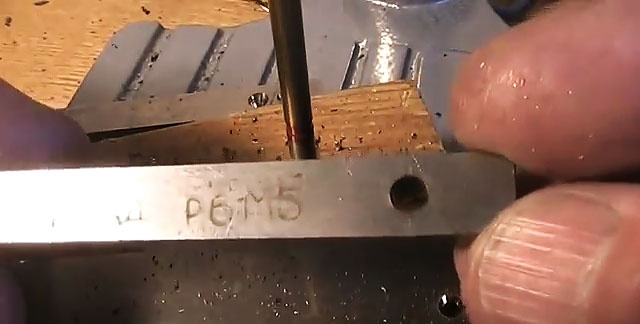
Final conclusions
We believe that with a slightly greater investment of time and effort, the same result can be achieved using a drill made of the same P18 steel. Moreover, choosing the optimal speed, which clearly should be lower.
Periodic lubrication of the drill will also facilitate the process, which will facilitate better metal processing and somewhat cool the tool during drilling. Several sharpenings may be needed.
Of course, making one hole is not difficult. There is no need for special scrupulosity; the main thing is to have enough persistence and patience. But when it is necessary to drill at least a dozen holes in this quick cutter, then all the shortcomings of sharpening, drilling mode, lack of lubrication and cooling of the tool will play a decisive role.
Watch the video
Similar master classes
Particularly interesting
Comments (8)