How to burn a hole in hardened steel
Any hardened steel is not easy to machine. Therefore, it is often tempered in advance, and after processing is completed, it is hardened again, if necessary due to operating conditions.
Hardened alloy steels are especially difficult to process. To make our actions more specific, we will focus on S30V stainless steel, which makes excellent knife blades.
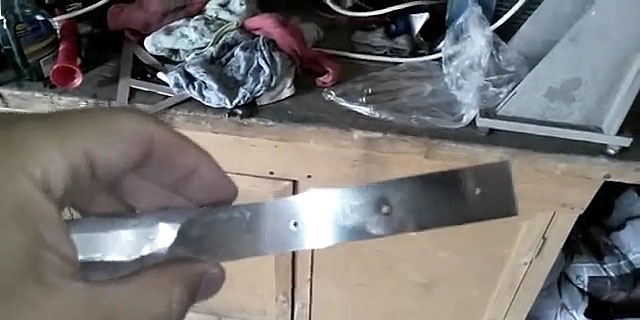
Of course, drilling a hole in steel with such characteristics is much more difficult than in ordinary steels, but in principle it is possible. Below we will look at a method of not so much drilling as burning.
What we need for this:
As the test material, as already defined, we will take a strip of hardened steel grade S30V measuring 5 × 30 × 200 mm.
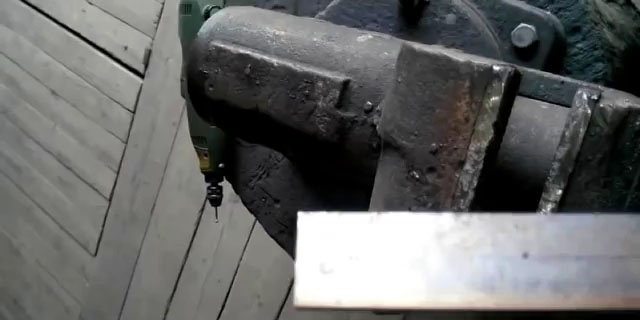
To do this, we clamp the selected strip of steel in a metalworker’s vice, having previously outlined the locations of the upcoming drilling.And so that the planned process proceeds without complications, we make indentations in the places of future holes using a small-diameter diamond drill.
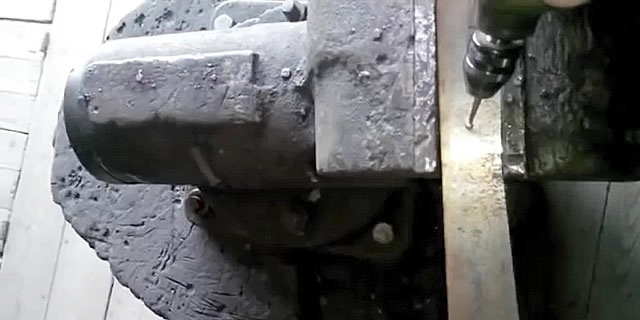
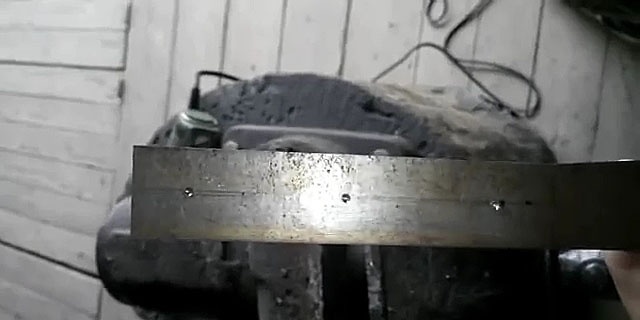
We carry out further actions on a drilling machine using a pre-prepared homemade tool. It can be made from a tungsten electrode with a diameter of 2-4 mm. You can purchase it in stores that sell welding transformers and accessories for this common type of work.
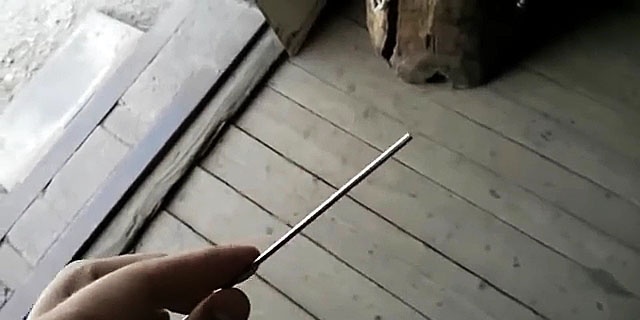
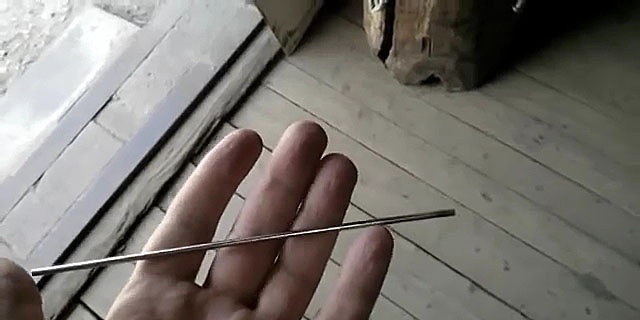
We cut a piece 30-40 mm long from the electrode, for example, using a grinder. We sharpen one end on a suitable abrasive tool so that it fits into the recesses that we made on the test workpiece.
We insert our homemade tool into the chuck of a drilling machine, which is able to provide quite a significant vertical force on the spindle with our drill clamped in it.
As a result, a large frictional force will be provided between the test plate and the rotating tool, releasing a huge amount of thermal energy.
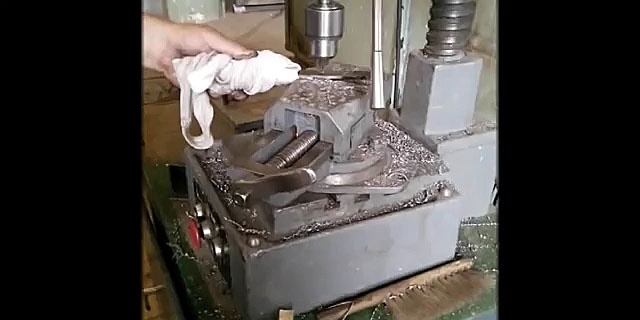
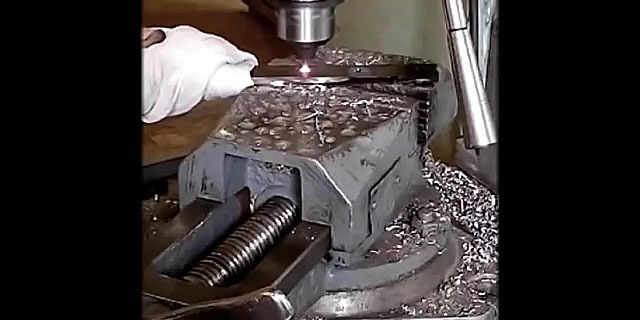
As a result, both the drill and the area of the plate around the future hole will become red hot. To intensify the process, the spindle speed must be maximum.
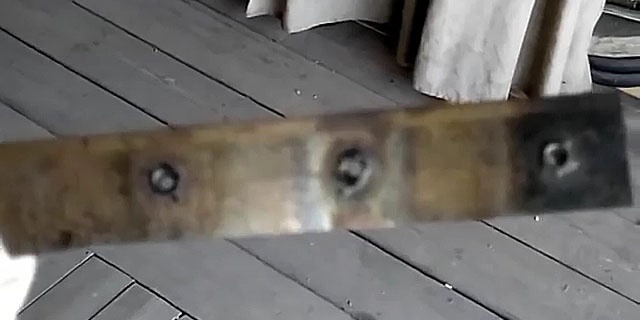
If you then process the plate with drilled holes on both sides on a grinder, then they will look quite presentable.
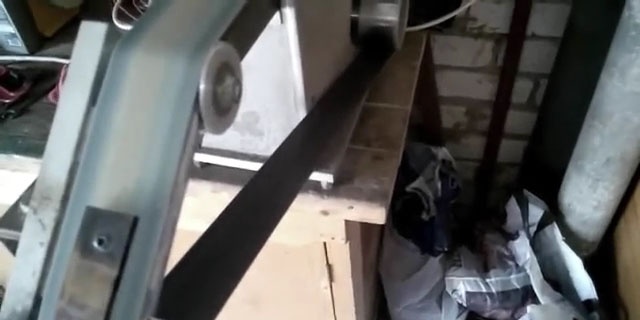
In this form they can be used for the intended purposes. If necessary, the holes can be expanded using a regular drill, since after burning the metal around them is released.
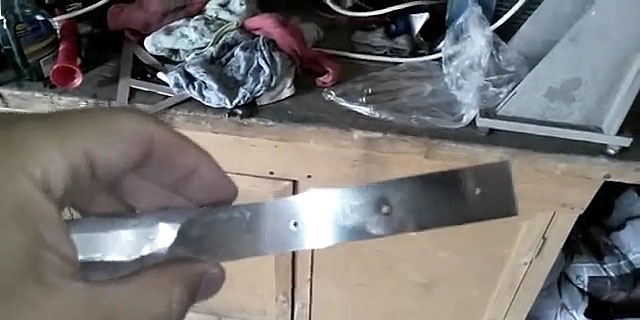
[media=https://www.youtube.com/watch?v=tTs4Kdf33A8]
Hardened alloy steels are especially difficult to process. To make our actions more specific, we will focus on S30V stainless steel, which makes excellent knife blades.
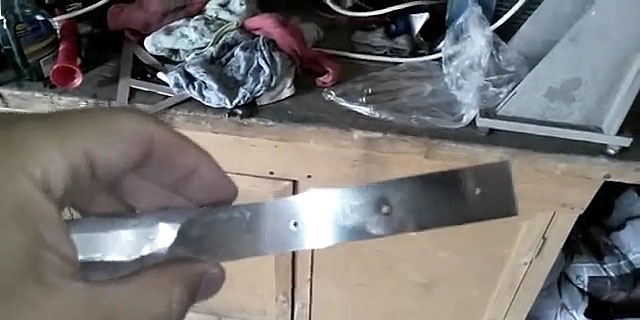
Of course, drilling a hole in steel with such characteristics is much more difficult than in ordinary steels, but in principle it is possible. Below we will look at a method of not so much drilling as burning.
What we need for this:
- powerful drilling machine;
- grinder with endless abrasive belt;
- bench vice for metal;
- diamond drill;
- tungsten electrode.
As the test material, as already defined, we will take a strip of hardened steel grade S30V measuring 5 × 30 × 200 mm.
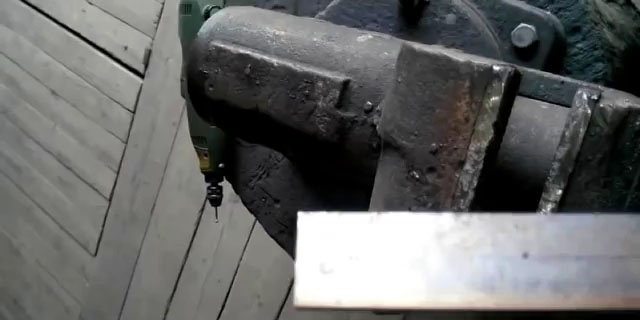
Steps for drilling/burning holes in hardened steel
To do this, we clamp the selected strip of steel in a metalworker’s vice, having previously outlined the locations of the upcoming drilling.And so that the planned process proceeds without complications, we make indentations in the places of future holes using a small-diameter diamond drill.
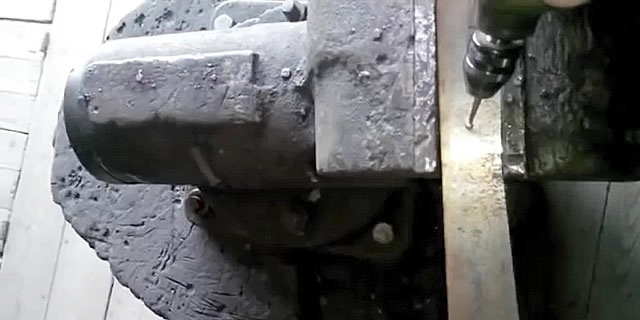
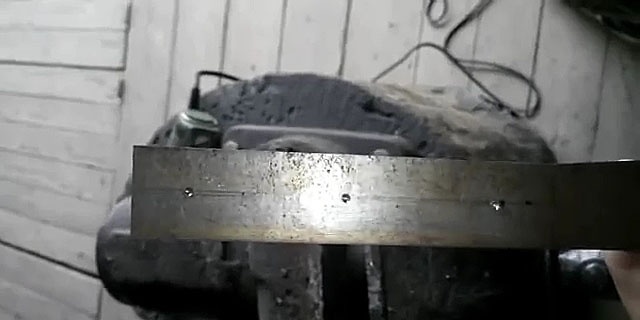
We carry out further actions on a drilling machine using a pre-prepared homemade tool. It can be made from a tungsten electrode with a diameter of 2-4 mm. You can purchase it in stores that sell welding transformers and accessories for this common type of work.
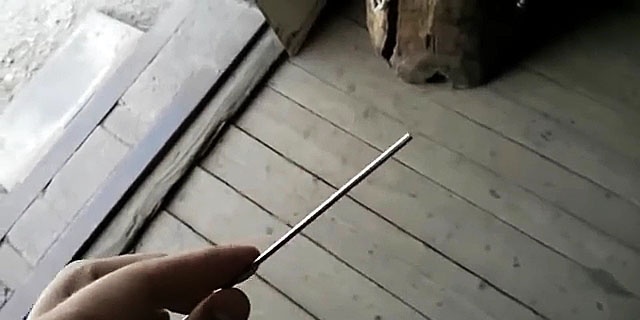
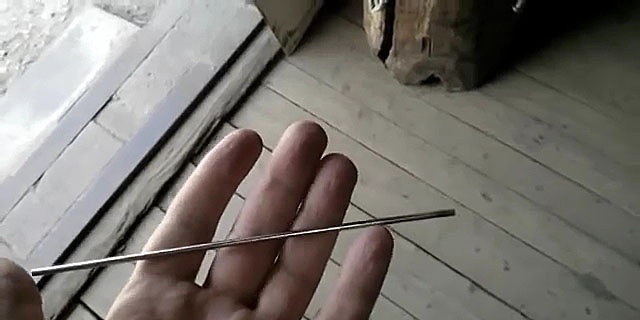
We cut a piece 30-40 mm long from the electrode, for example, using a grinder. We sharpen one end on a suitable abrasive tool so that it fits into the recesses that we made on the test workpiece.
We insert our homemade tool into the chuck of a drilling machine, which is able to provide quite a significant vertical force on the spindle with our drill clamped in it.
As a result, a large frictional force will be provided between the test plate and the rotating tool, releasing a huge amount of thermal energy.
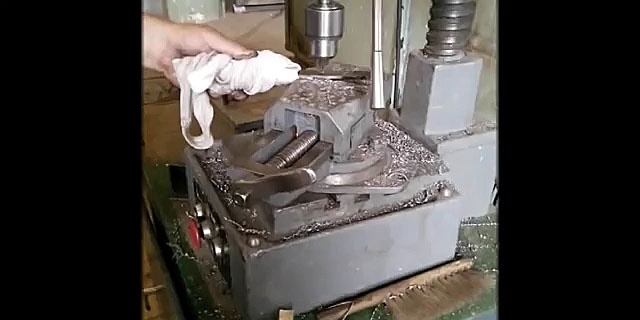
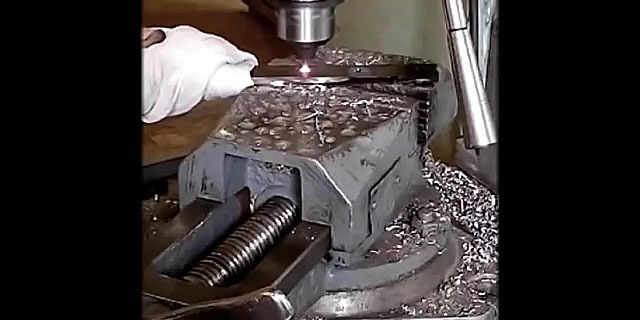
As a result, both the drill and the area of the plate around the future hole will become red hot. To intensify the process, the spindle speed must be maximum.
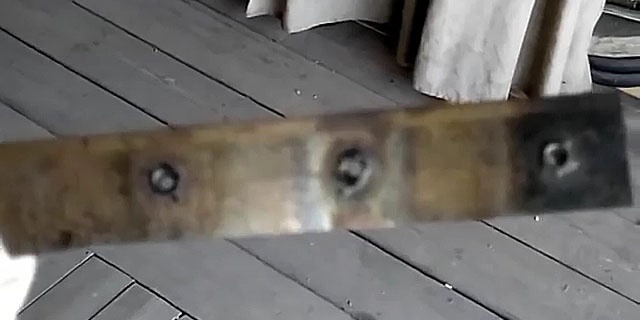
If you then process the plate with drilled holes on both sides on a grinder, then they will look quite presentable.
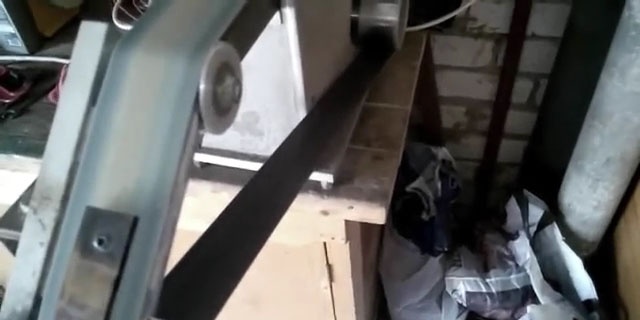
In this form they can be used for the intended purposes. If necessary, the holes can be expanded using a regular drill, since after burning the metal around them is released.
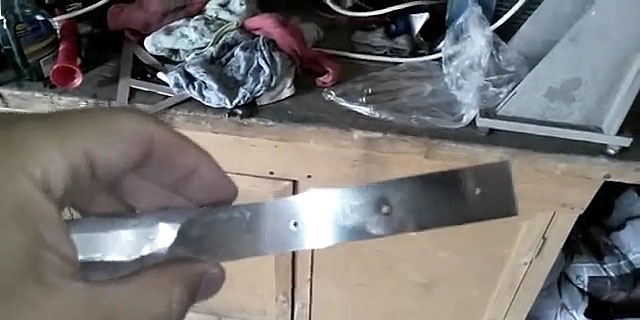
Watch the video
[media=https://www.youtube.com/watch?v=tTs4Kdf33A8]
Similar master classes
Particularly interesting
Comments (0)