How to Make a Hole in Hardened Steel Without Drilling
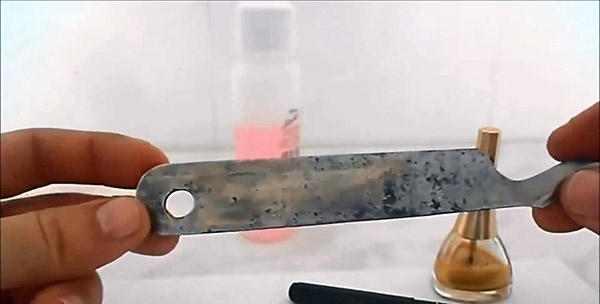
In this simple way, you can make not only a round hole in hardened steel, but also a hole of any other shape without any extra effort. The chemical method will help you out and make the task easier. The method does not require expensive chemicals; all ingredients can be found in any household.
Will need
I offer a simple method for making holes in high-speed steel. To work you will need:
- any product made of high-speed steel;
- marker;
- nail polish;
- nail polish remover (can be replaced with white spirit or acetone. I chose the remover only because of the pleasant smell, and it’s the same acetone);
- cotton wool;
- empty plastic container (bottle);
- salt;
- knife;
- a homemade device made from a charger and two nails.
Making a hole in metal without a drill
Apply nail polish remover to the cotton wool and degrease the surface of our workpiece.
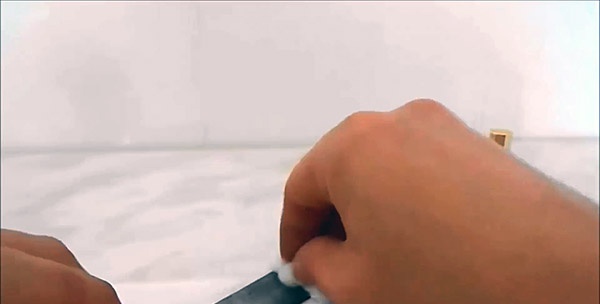
Apply varnish to the desired area. The varnish must be applied in a thick layer on both sides. Don't forget to coat the ends thoroughly. Leave the workpiece for 10-15 minutes to allow the varnish to dry.
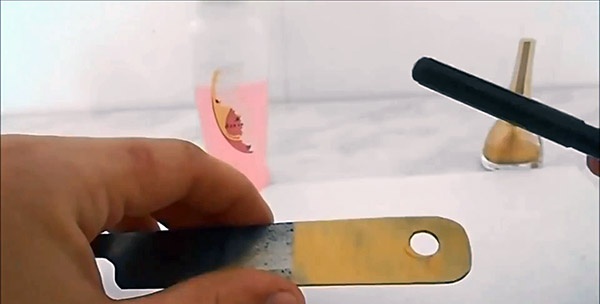
On the dry surface, with a marker on both sides of the workpiece, I mark the place for the hole. I choose the location arbitrarily, now I need to show how you can make a hole using this method. For example, you need to install a regular factory rivet. The diameter of the hole should be slightly smaller than the size of the rivet.
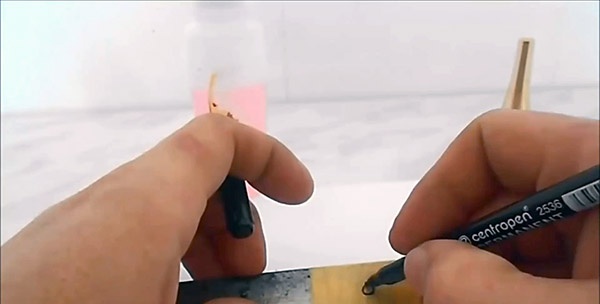
Then use a knife to remove the varnish inside the hole outline. Do this on both sides.
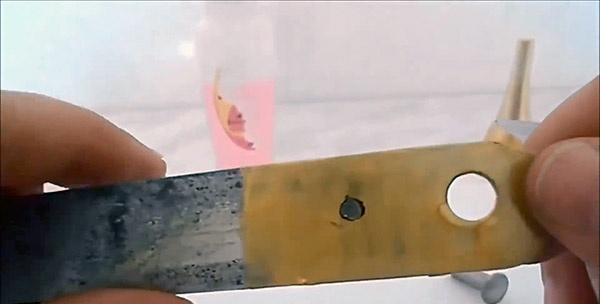
Pour water into a container and add 3 tablespoons of salt. The height of the water in the container should be 10 mm less than the height of the varnished area of the workpiece.
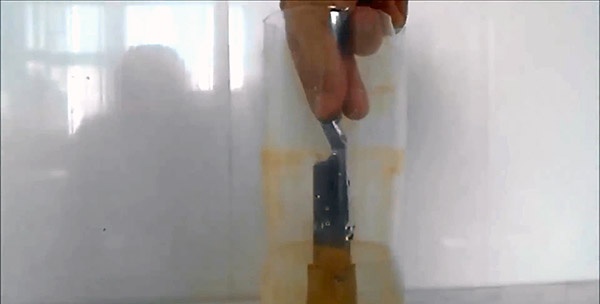
I take a device made from a hair clipper charger and two nails. The nails will serve as electrodes - I connected them to one contact. The other contact is simply bare, stripped wire. I use a 12V charger, but a regular cell phone charger will do the job.
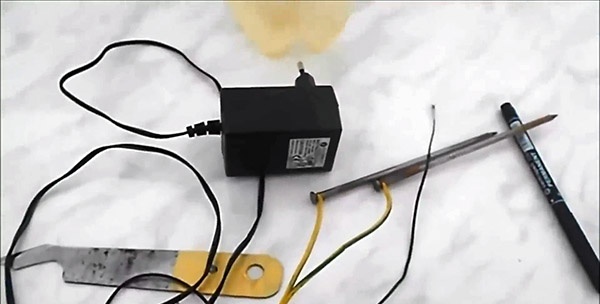
The stripped wire should be positive, the electrodes should be negative. We attach the positive wire to our workpiece using a clothespin. Then we lower the nails into the water.
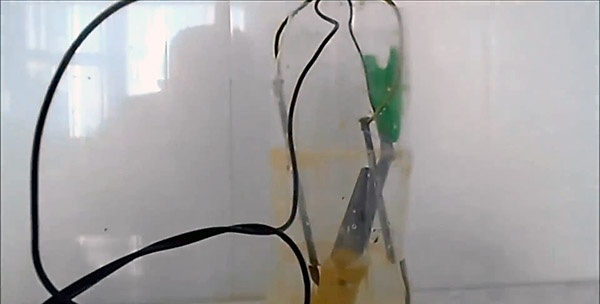
You can make slits in the container to fix the position of the nails. Plugging the charger into a power outlet. After switching on, the water around the electrode nails begins to bubble, and the cleaned hole mark turns black.
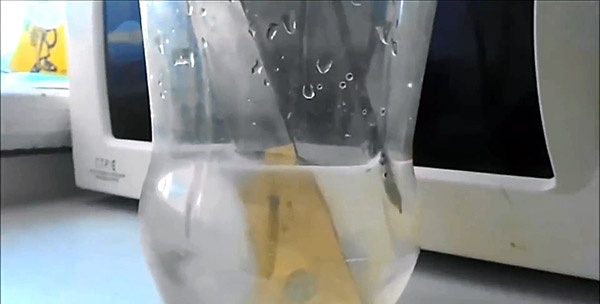
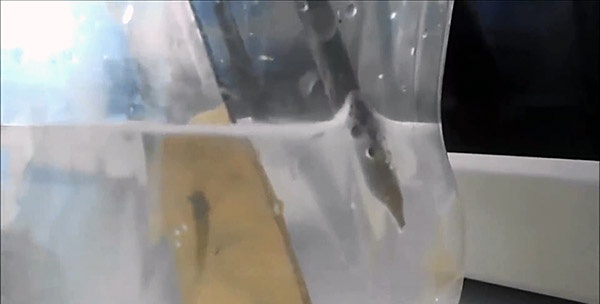
Note: to check the polarity of the wires, you must connect the charger. If water starts to bubble around the nails, it means it's a minus and you connected correctly. The appearance of bubbles in the water around the workpiece indicates that the minus is connected to it and the wires need to be reconnected. The negative must always be connected to the electrodes, the positive to the workpiece being etched!
Leave the container for one hour, 30 minutes after the start of the process you need to change the water.I turn off the charger and take out the workpiece.
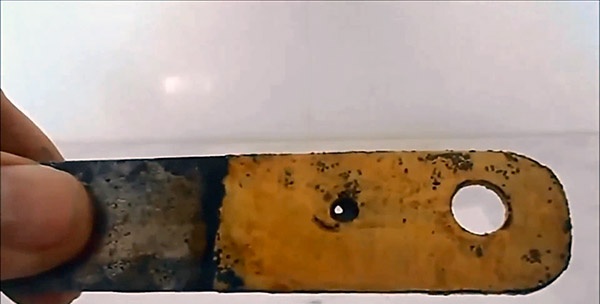
A through hole appeared in the intended location. In order to make the hole diameter larger, the process can be continued. Or file uneven edges with a file.
This is how you can make the desired hole in a workpiece by etching high-speed steel using the most ordinary objects.

Watch the video
Similar master classes
Particularly interesting
Comments (28)