How to make a socket connection with a hair dryer
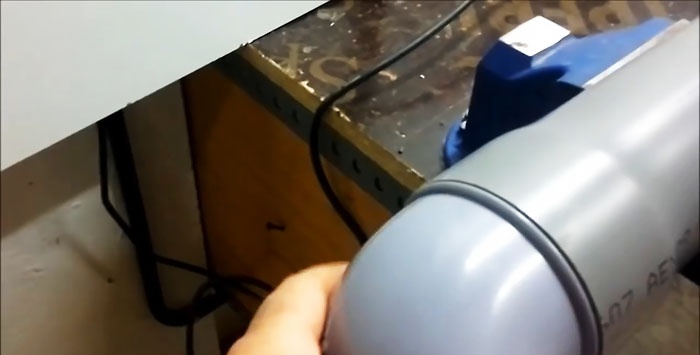
All sewer and waste water systems today are made of plastic pipes. For them you need to buy various corners, triangles, couplings and other additional elements. The connections are bell-shaped, the ends have the so-called “male” and “male”.
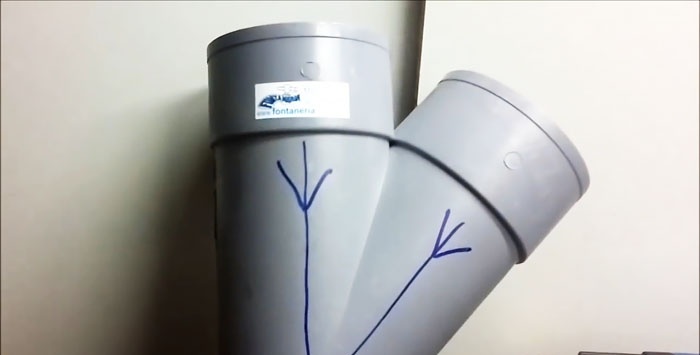
The first has a slightly larger diameter to accommodate the second end.
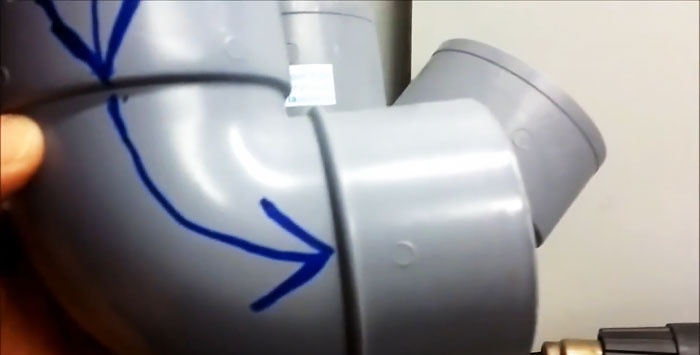
Inexperienced plumbers often make mistakes in calculations, and already during installation they find out that there are not enough additional elements. What to do if it’s too far to go to the store for them or it’s not possible? You can solve the problem yourself.
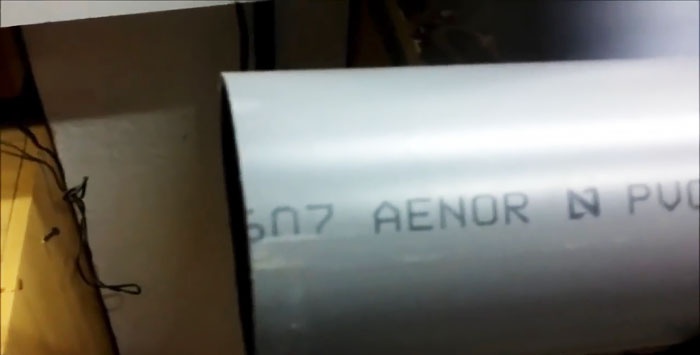
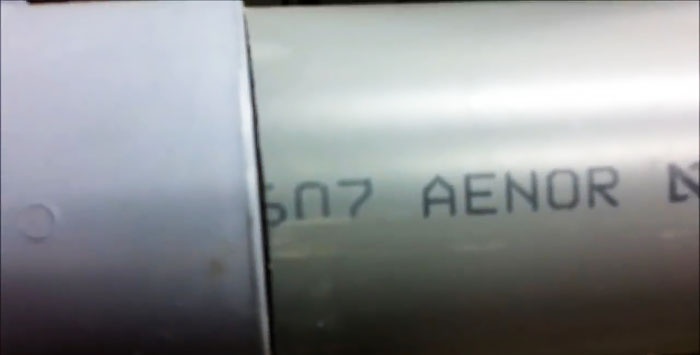
Tools
You will need a construction hair dryer, you can also use a household hair dryer, but with a power of at least 2 kW. Another option is a gas burner. There are bench vices - great, no - you can do without them, but the work will be a little more difficult.
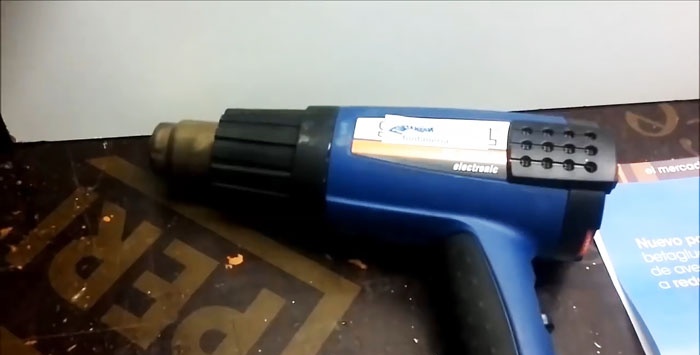
Manufacturing process
Wrap the paper around the “dad” and press it as tightly as possible to the surface. 1-2 turns are enough, it all depends on its density. Bend long pieces inside the pipe, make a neat hem.
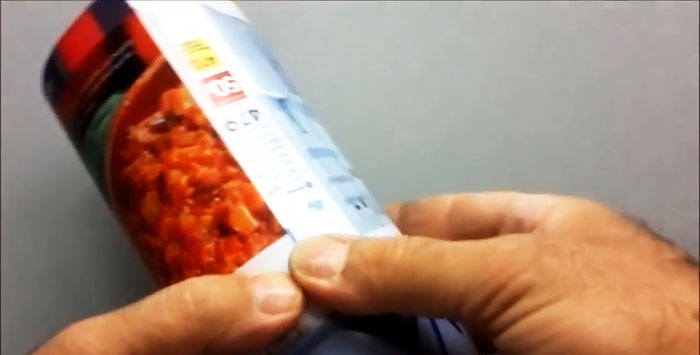
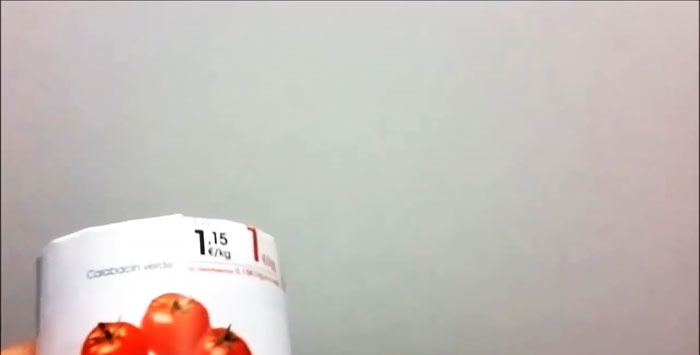
Secure a piece of pipe of the required length in a vice, do not tighten it too much, it cannot withstand heavy loads.
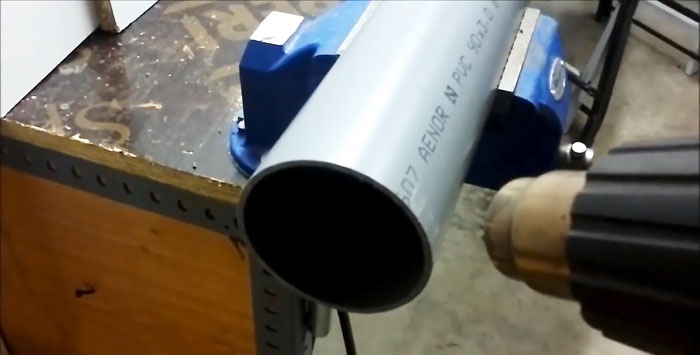
Use a hairdryer to warm it up. The nozzle movements should be uniform around the perimeter of the circle. The heating length is 2–3 cm longer than the “mother” size. Keep in mind that PVC pipes become deformed or ignite at the slightest violation of the recommended heating regime; it is very difficult to correct problems.
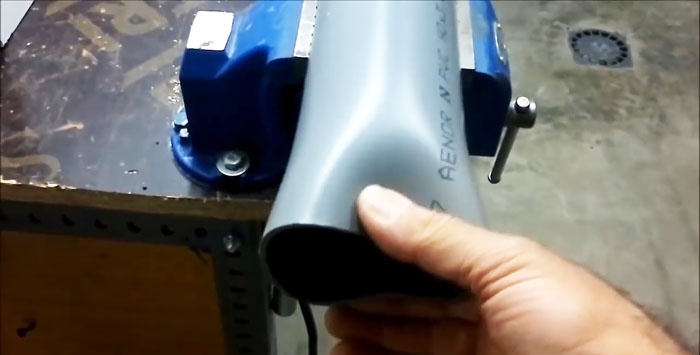
Constantly check the condition of the plastic with your hand; in places where it is heated, it should become soft throughout the entire length of heating, but not deform under its own weight.
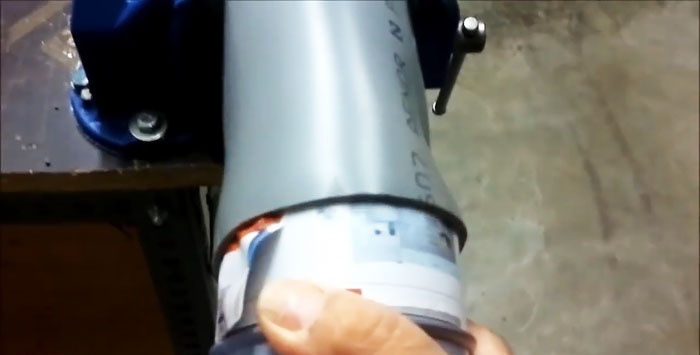
Carefully begin to insert the male into the heated section of the pipe. Keep both parts on the same axis as much as possible. First, press the male edge down a little, this will enlarge the hole.
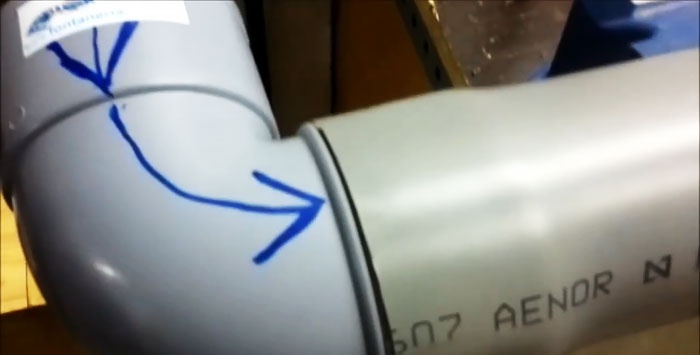
Then level the position and constantly turn left/right. Avoid creasing. As soon as 2–3 cm of the pipe has reached the end, further press the part with great force and constant turns until it stops. Leave the part in place and cool the plastic; to speed up the process, you can wrap it with a damp cloth.
Separate the elements, remove the paper and check the connection. If you do everything carefully, it will work out the first time.
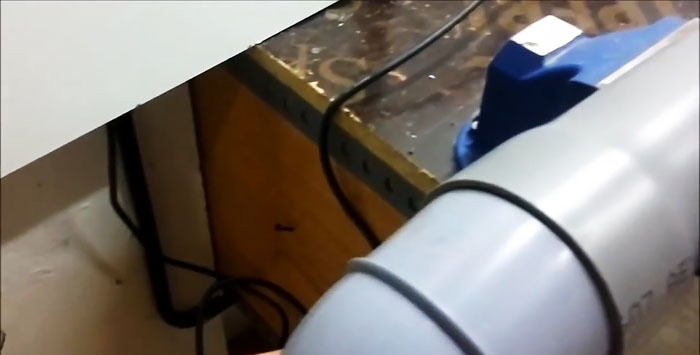
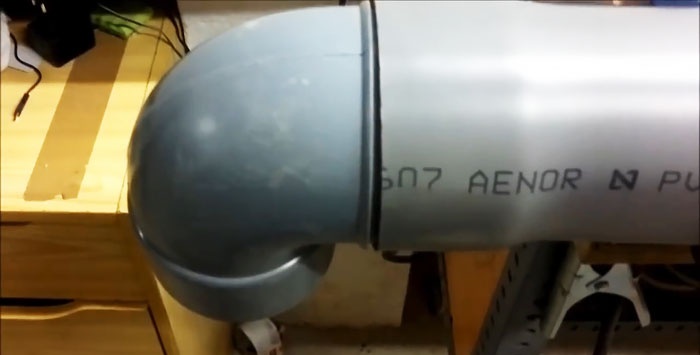
Conclusion
Using this method, socket joints of various diameters can be made. If the socket is made on both sides, you will get an excellent coupling. The only drawback is that the system can only be mounted vertically or at large angles - it does not have a rubber gasket. It is difficult to lay horizontally; you need to use seals, but they do not provide a 100% guarantee of tightness and durability.
Watch the video
Similar master classes
Particularly interesting
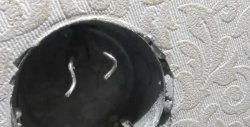
How to install a socket if there are short wires left
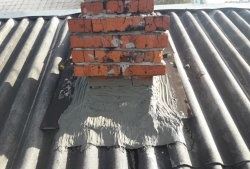
How to eliminate gaps between the chimney and slate
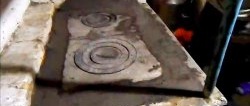
How to mix an ultra-reliable solution for the oven that does not give
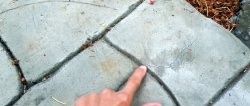
There will be no more cracks: What to add to concrete to make it
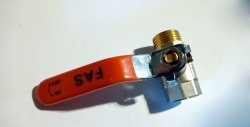
Never buy ball valves without checking with me
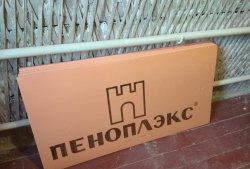
New technology for floor insulation with penoplex
Comments (1)