A second life for an old diamond blade
A worn-out diamond blade for concrete or tile can be converted into a universal tool capable of sawing plexiglass, laminate, boards, plywood, drywall and other materials. The resulting cutting wheel is safe, which distinguishes it from hard-tipped saw blades. For the conversion you only need a grinder and a drill.
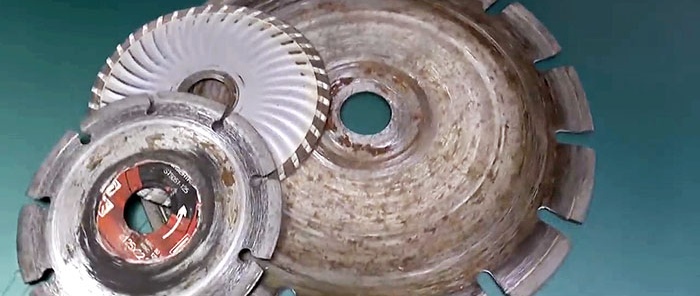
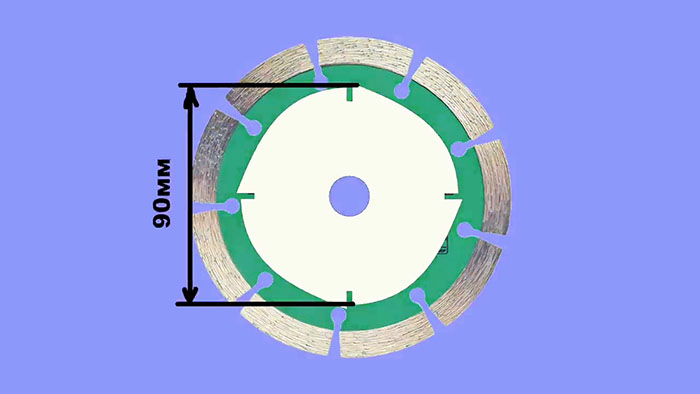
To ensure that the reground old disc does not have runout, you need to apply an exact contour for turning. If symmetry is not maintained, then imbalance will occur, and in the future the grinder will be tossed. It is optimal to print a stencil with the outline of a universal disk, and grind the old circle along it.
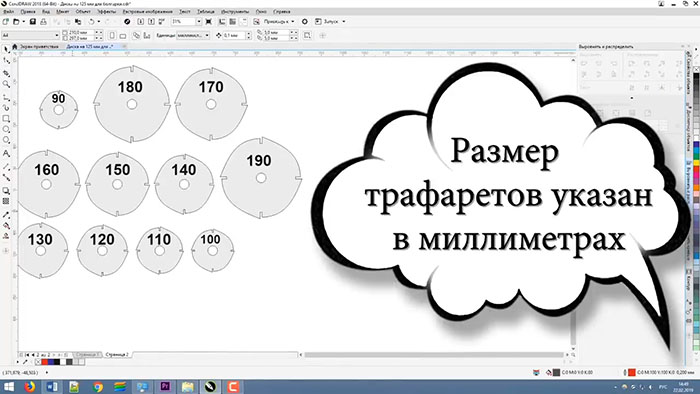
The template can be downloaded under the video - https://www.youtube.com/watch?v=1yKEZBgGUz8
You need to wipe off rust and dust from a worn disk, lubricate it with dry office glue and glue a stencil. The template must be oriented along the mounting hole.
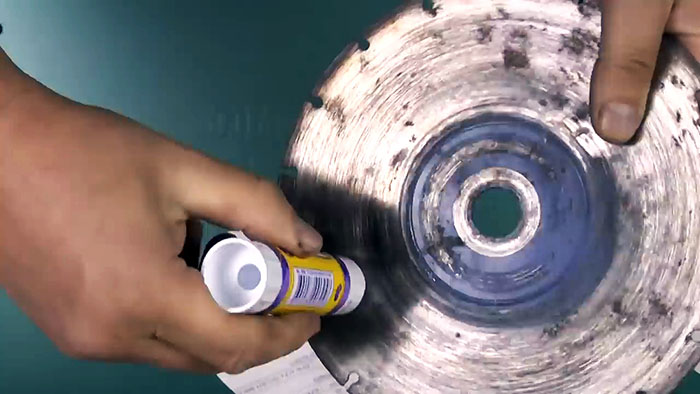
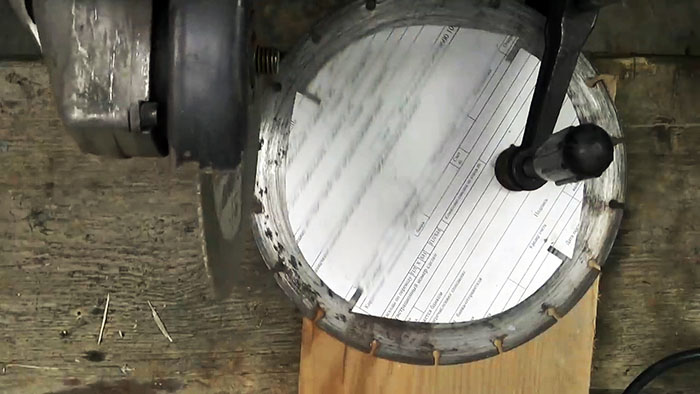
Next, use a grinder with a cutting wheel to cut off the protruding parts of the disk.The remaining metal must be ground off with a sanding disc, reaching the edges of the stencil. Since the metal is not hardened, everything is cut easily and quickly.
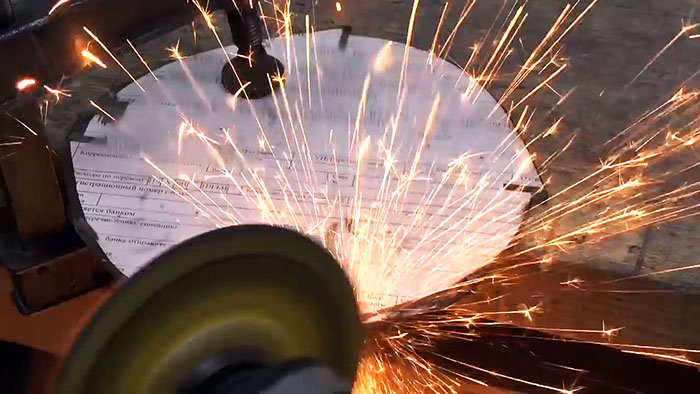
After giving the shape, you need to drill damper holes on the disk along the cuts of the stencil. It is enough to use a 6-8 mm drill. Next, you need to trim the disc to the holes, thereby obtaining 4 teeth. It is better to cut at a slight positive angle so that the formed teeth can quickly bite into materials in the future.
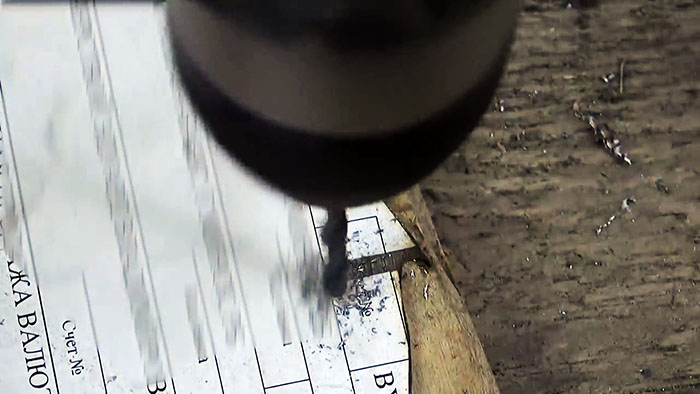
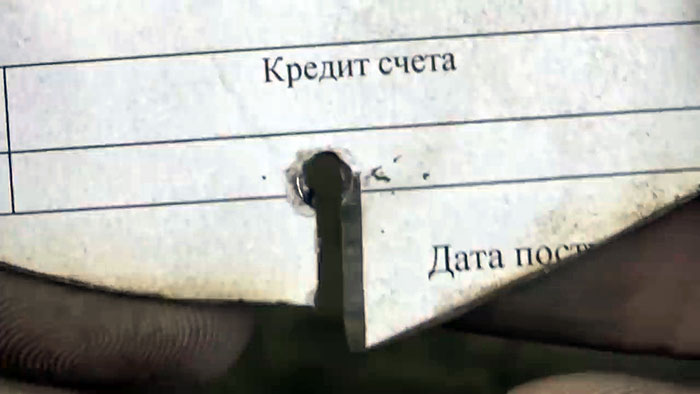
To prevent the saw blade from pinching, you need to set its teeth. If you plan to work only with wood, then it costs more to plant. It is optimal if the width of the resulting cut is 4 mm wider than the cross-section of the disk.
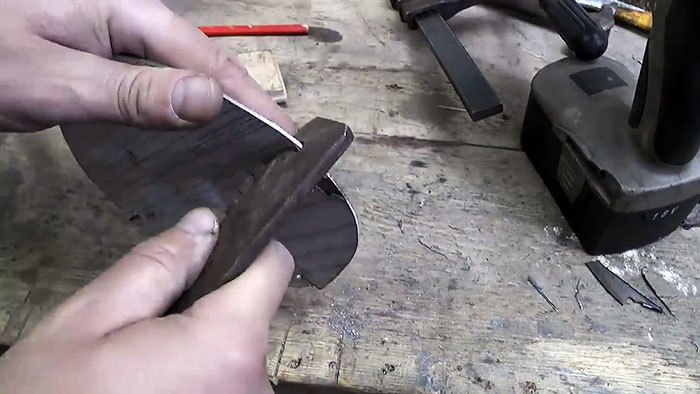
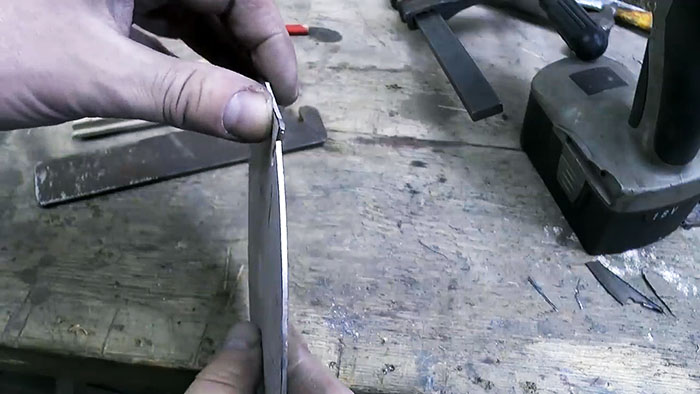
Next you need to sharpen the teeth. An ideal angle would be 3-6 degrees, similar to crosscut saws. In this case, the edge will be more resistant to hard materials and will not wear off in a couple of minutes. If you need to spread the boards lengthwise, then the angle should be increased to 15-25 degrees.
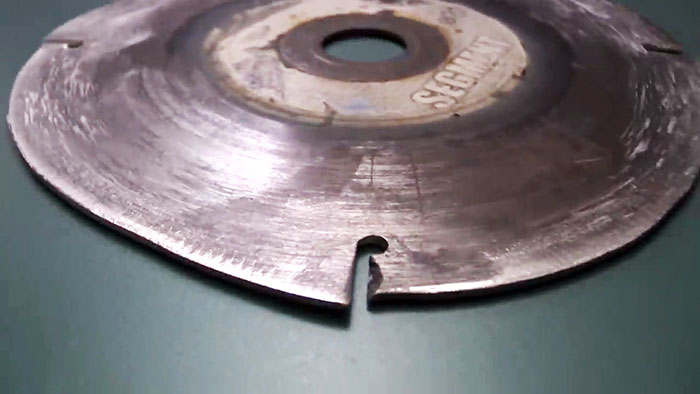
The beauty of the resulting universal disc is that its teeth, although they do not hold an edge for long, do not fly out. If you need to saw a board in a hard-to-reach place, then the tool is ideal. The disk can even make selections in the tree. Its teeth are quickly sharpened, and if you put the circle in the opposite direction and cut towards yourself, the grinder almost does not jump. This is a good alternative to a purchased tool for solving small household tasks.
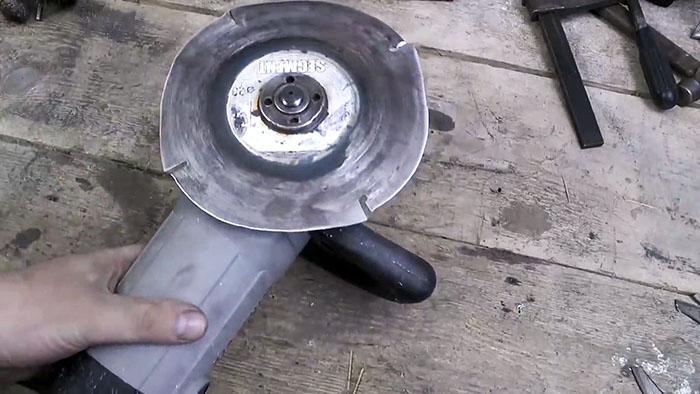
We cut plexiglass:
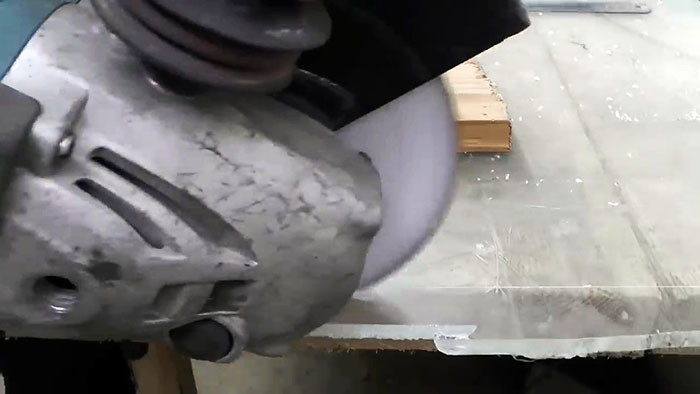
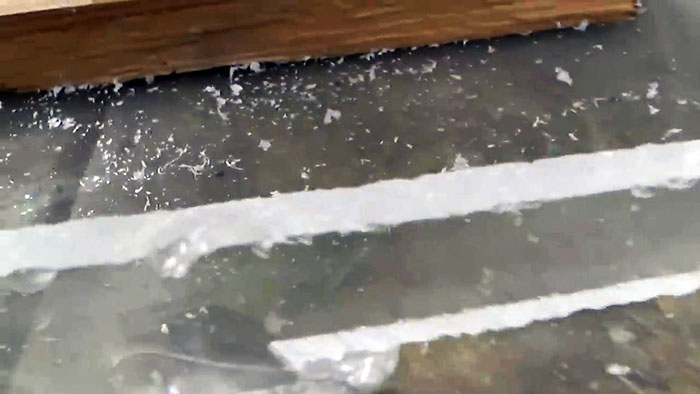
We saw and process wood:
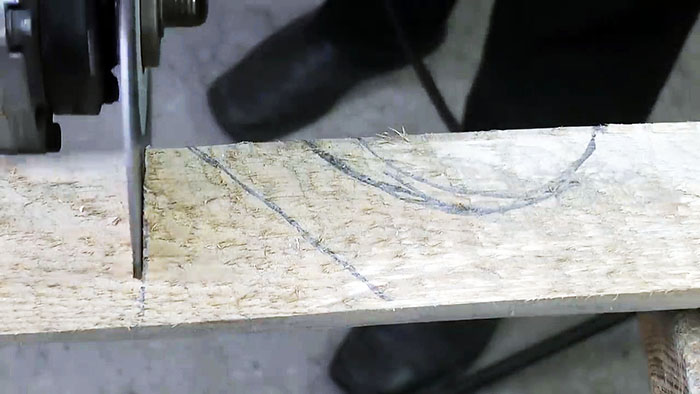
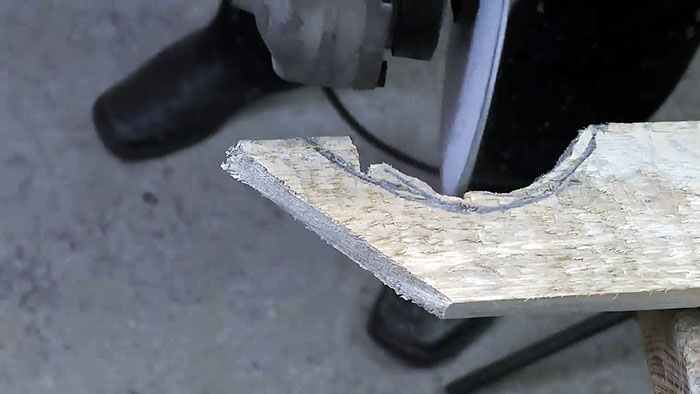
Chipboard and multi-layer waterproof plywood:
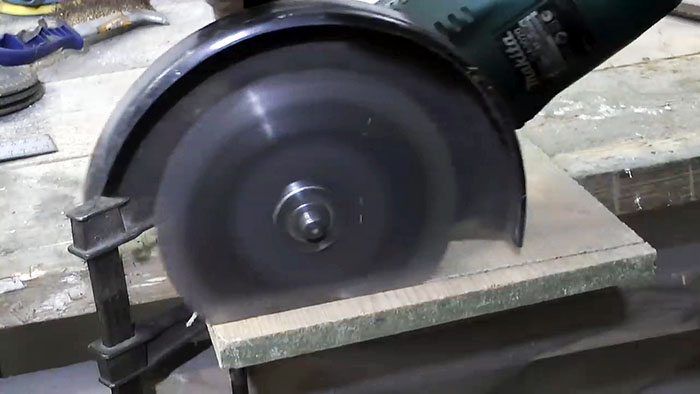
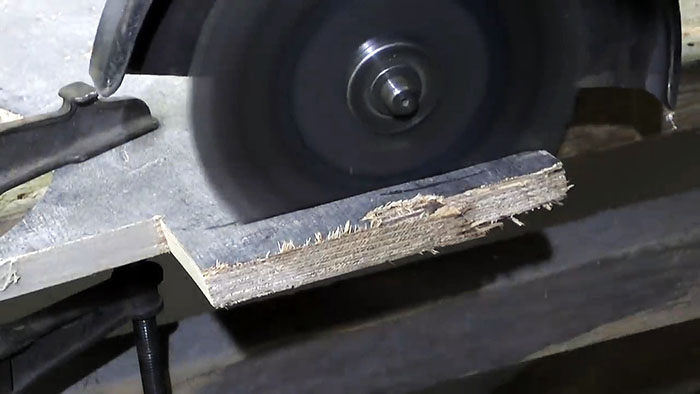
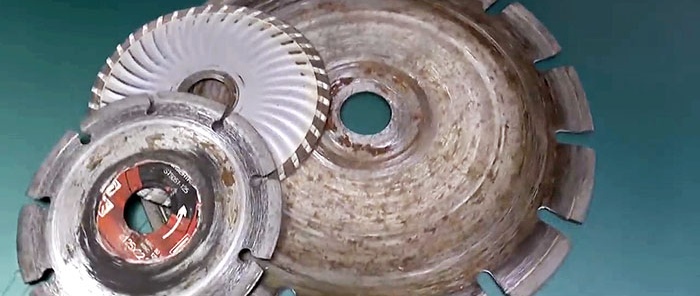
Materials:
- worn diamond disc;
- office glue;
- stencil for cutting the disk shape.
Disc conversion
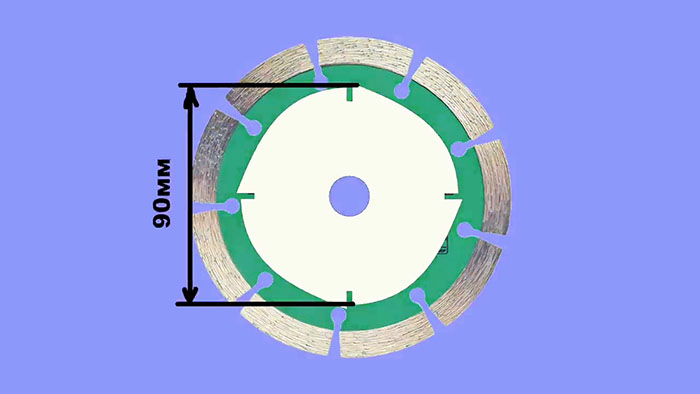
To ensure that the reground old disc does not have runout, you need to apply an exact contour for turning. If symmetry is not maintained, then imbalance will occur, and in the future the grinder will be tossed. It is optimal to print a stencil with the outline of a universal disk, and grind the old circle along it.
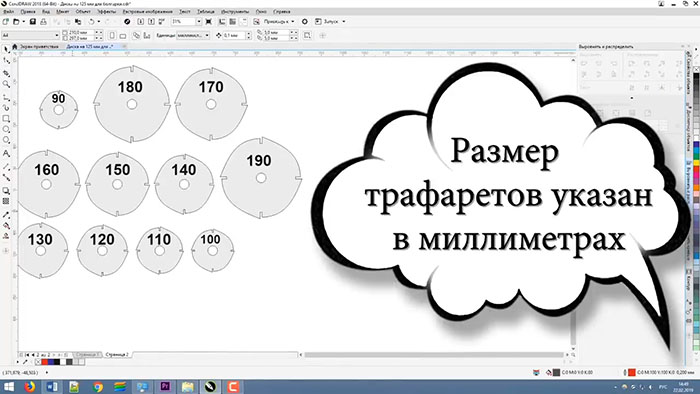
The template can be downloaded under the video - https://www.youtube.com/watch?v=1yKEZBgGUz8
You need to wipe off rust and dust from a worn disk, lubricate it with dry office glue and glue a stencil. The template must be oriented along the mounting hole.
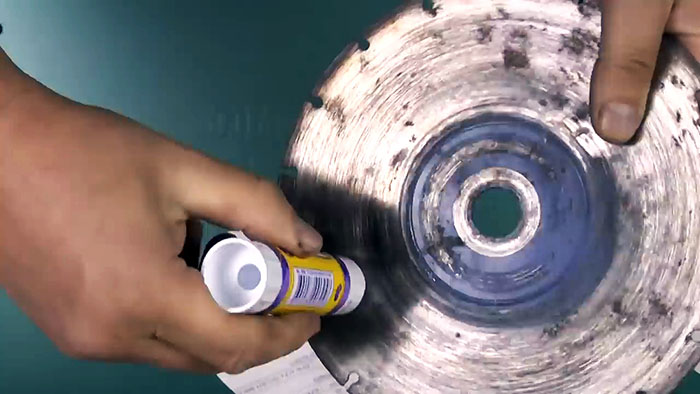
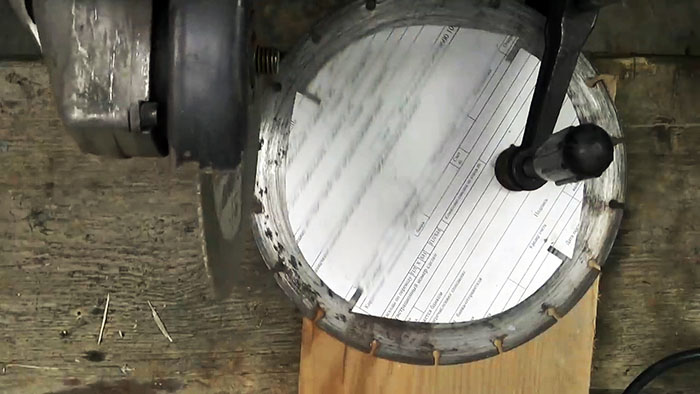
Next, use a grinder with a cutting wheel to cut off the protruding parts of the disk.The remaining metal must be ground off with a sanding disc, reaching the edges of the stencil. Since the metal is not hardened, everything is cut easily and quickly.
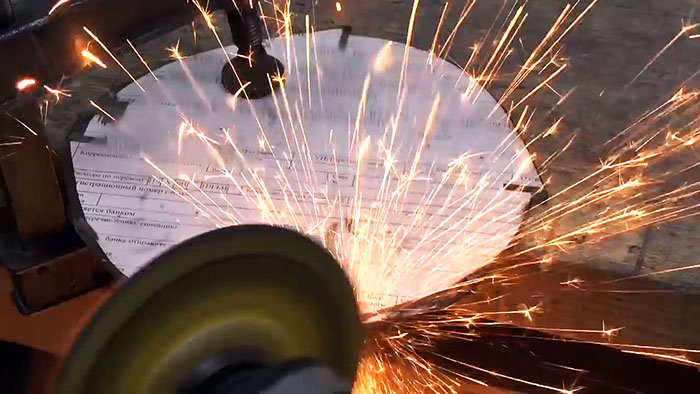
After giving the shape, you need to drill damper holes on the disk along the cuts of the stencil. It is enough to use a 6-8 mm drill. Next, you need to trim the disc to the holes, thereby obtaining 4 teeth. It is better to cut at a slight positive angle so that the formed teeth can quickly bite into materials in the future.
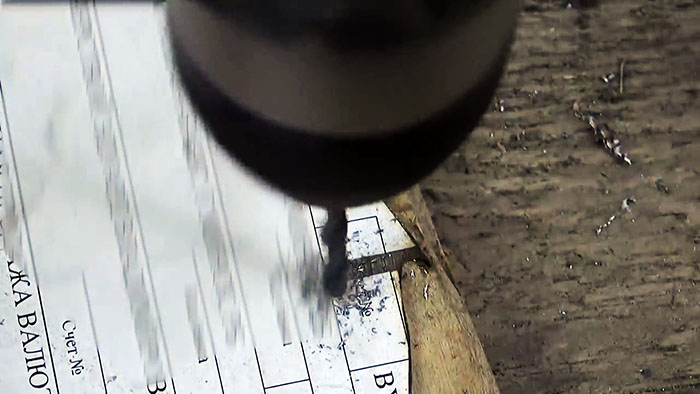
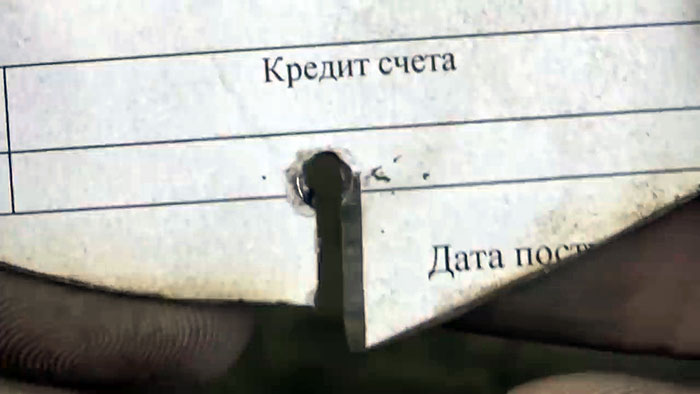
To prevent the saw blade from pinching, you need to set its teeth. If you plan to work only with wood, then it costs more to plant. It is optimal if the width of the resulting cut is 4 mm wider than the cross-section of the disk.
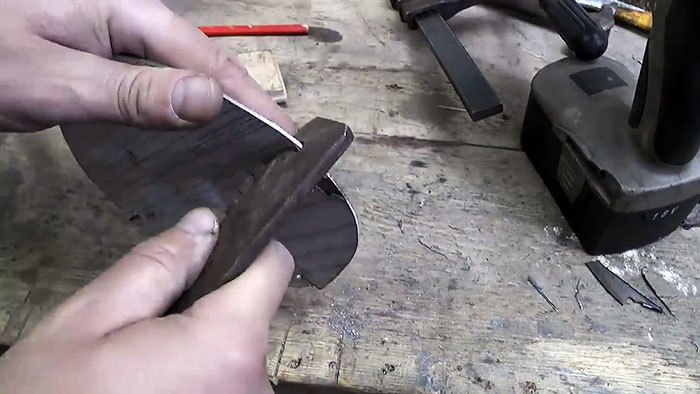
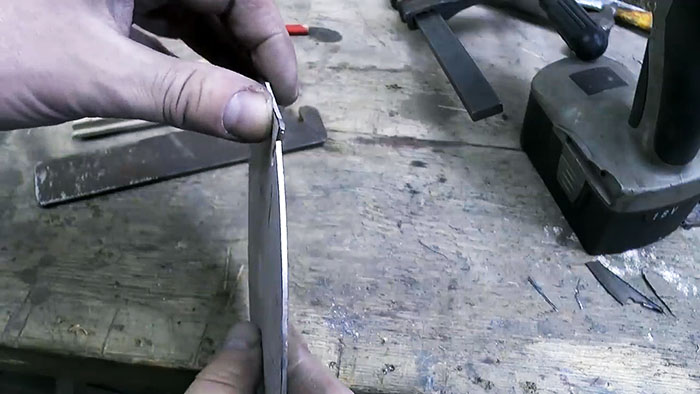
Next you need to sharpen the teeth. An ideal angle would be 3-6 degrees, similar to crosscut saws. In this case, the edge will be more resistant to hard materials and will not wear off in a couple of minutes. If you need to spread the boards lengthwise, then the angle should be increased to 15-25 degrees.
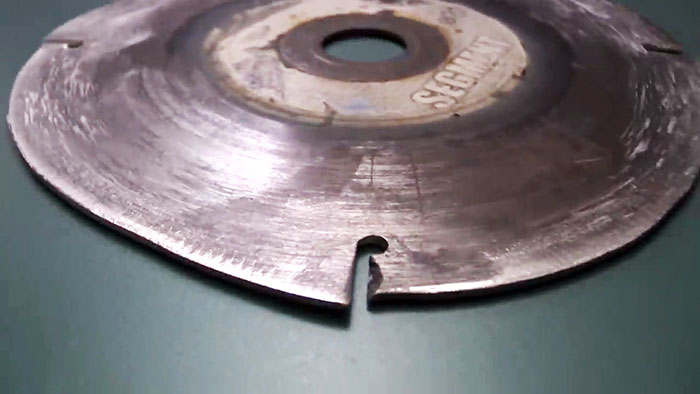
The beauty of the resulting universal disc is that its teeth, although they do not hold an edge for long, do not fly out. If you need to saw a board in a hard-to-reach place, then the tool is ideal. The disk can even make selections in the tree. Its teeth are quickly sharpened, and if you put the circle in the opposite direction and cut towards yourself, the grinder almost does not jump. This is a good alternative to a purchased tool for solving small household tasks.
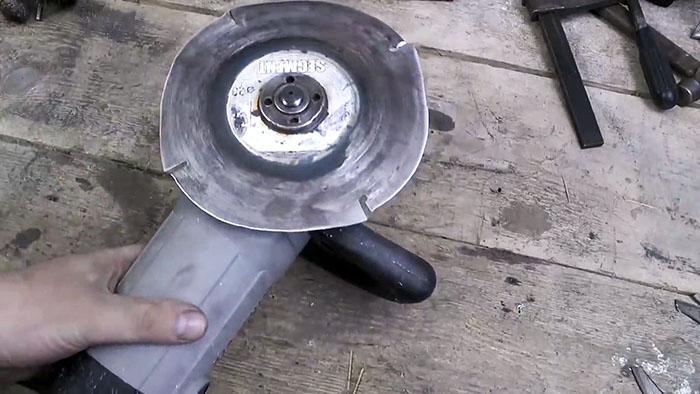
We cut plexiglass:
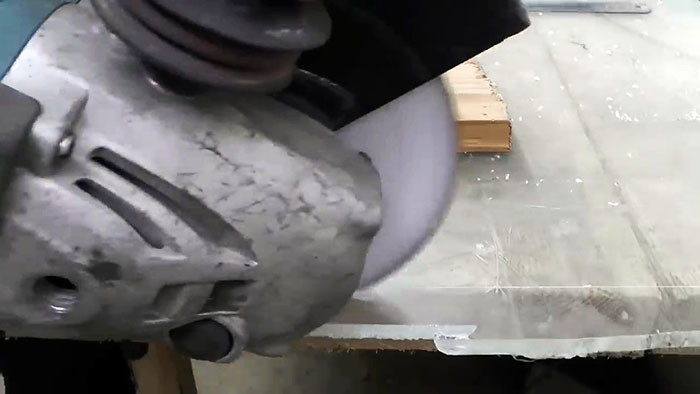
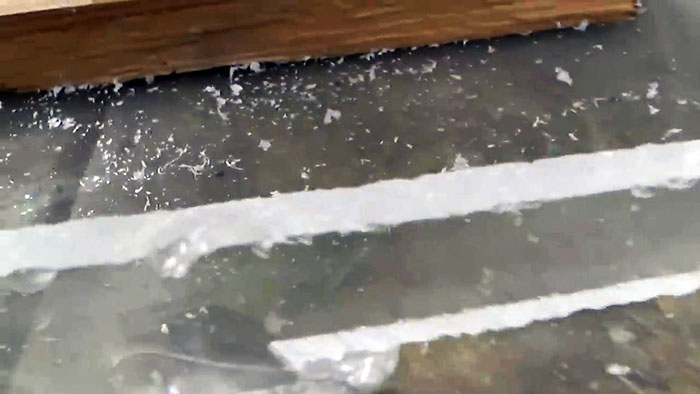
We saw and process wood:
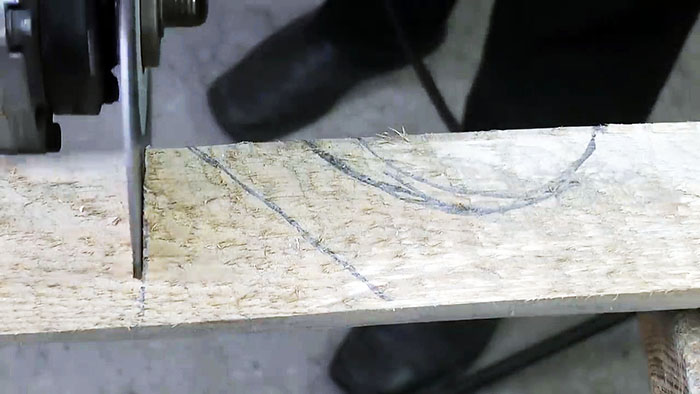
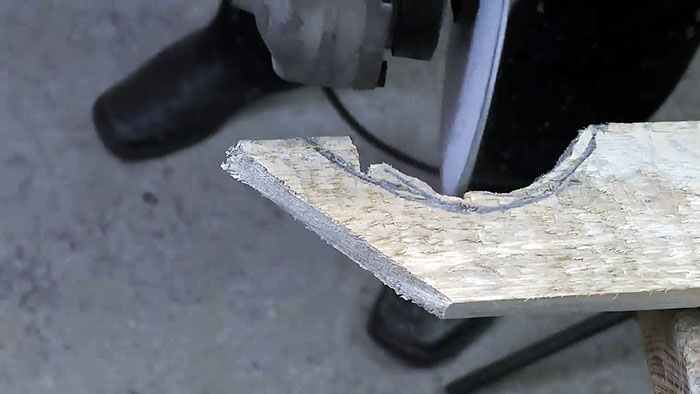
Chipboard and multi-layer waterproof plywood:
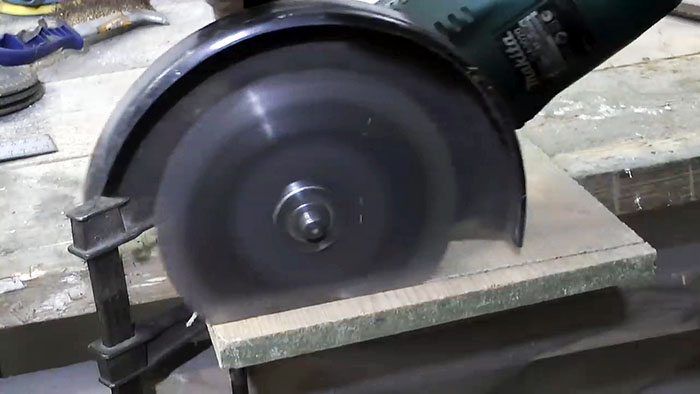
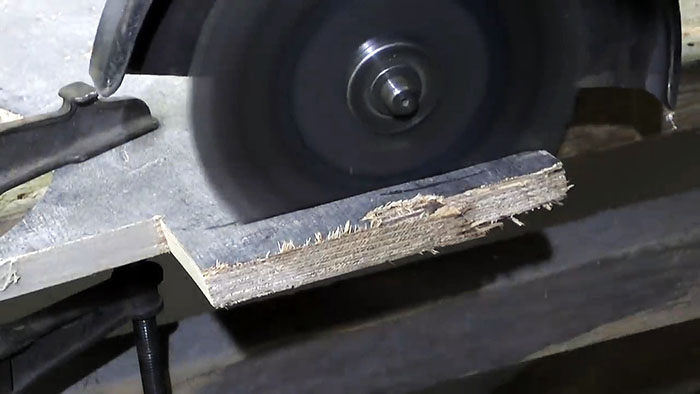
Watch the video
Similar master classes
Particularly interesting
Comments (4)