How to convert an angle grinder to 12 V
If your small-power angle grinder is out of order, then you can take this opportunity to convert it to a constant supply voltage of 12 V. At some points, it will be an indispensable assistant for you, in the sense that it will work anywhere from a battery.
For the conversion you will need a 775 series motor (). Electric motors of this series are high-speed and very powerful. They operate on direct current, at a voltage of 12, 24 or 36 V, depending on the design.
We open the body of the angle grinder by unscrewing the screws securing the gearbox.
And the rear casing screw.
We take out the gearbox with the rotor.
We remove the stator from the housing; it will no longer be needed.
It would be a good idea to disassemble the gearbox and lubricate it with new grease.
Then we close it back. Next, we saw off the rotor shaft from the gearbox with a hacksaw.
The impeller, which was used for forced cooling of the motor, can be removed with pliers
We fix the gearbox and drill the shaft in the center, with a drill of a diameter slightly larger than the shaft of the new electric motor.
Now we drill a hole on the side and cut a thread for the screw.
We insert the motor shaft and fix the screws.
We wrap the engine with electrical tape, increasing its diameter to fit the inside of the housing.
We insert it tightly into the body.First remove all the brushes from the old motor.
We assemble the tool in reverse order.
Solder the contacts to the new motor.
The grinder is ready to work.
We try to cut something off with a cutting disc.
Of course, the power has changed a little for the worse, but it is still quite possible to work.
For the conversion you will need a 775 series motor (). Electric motors of this series are high-speed and very powerful. They operate on direct current, at a voltage of 12, 24 or 36 V, depending on the design.
We convert the grinder from 220 V to 12 V
We open the body of the angle grinder by unscrewing the screws securing the gearbox.
And the rear casing screw.
We take out the gearbox with the rotor.
We remove the stator from the housing; it will no longer be needed.
It would be a good idea to disassemble the gearbox and lubricate it with new grease.
Then we close it back. Next, we saw off the rotor shaft from the gearbox with a hacksaw.
The impeller, which was used for forced cooling of the motor, can be removed with pliers
We fix the gearbox and drill the shaft in the center, with a drill of a diameter slightly larger than the shaft of the new electric motor.
Now we drill a hole on the side and cut a thread for the screw.
We insert the motor shaft and fix the screws.
We wrap the engine with electrical tape, increasing its diameter to fit the inside of the housing.
We insert it tightly into the body.First remove all the brushes from the old motor.
We assemble the tool in reverse order.
Solder the contacts to the new motor.
The grinder is ready to work.
We try to cut something off with a cutting disc.
Of course, the power has changed a little for the worse, but it is still quite possible to work.
Watch the video
Similar master classes
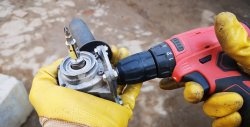
A device for a screwdriver from the gearbox of a broken angle grinder
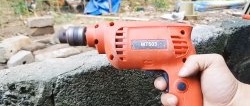
How to restore a burnt out drill by converting it from 220 V to 12 V
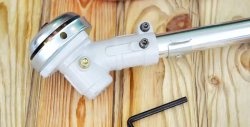
How to lubricate the gearbox of a brush cutter in a simple way
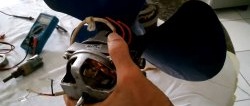
How to convert a fan motor into a generator
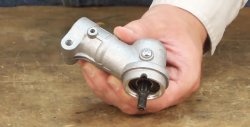
Replacing the lower gearbox of a brush cutter (trimmer)
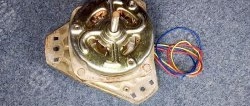
How to convert any asynchronous motor into a generator
Particularly interesting
Comments (7)