No worse than the factory one: Knife handle made of polypropylene pipe
Since the blades of modern kitchen knives are made from special grades of steel, which are usually subjected to thermomechanical treatment, they last a long time without losing their strength and cutting qualities. Of course, for this they need to be sharpened correctly and regularly.
Knife handles, unlike blades, are not as durable, especially if they are made of fragile or soft material. But they can be replaced, and this is not at all difficult to do today, given the variety of materials that can be used in this capacity and make the sample no worse than the factory version, and maybe even better and more durable.

Making a new knife handle to replace a broken one does not require any special skills. We can also make do with a remaining piece of polypropylene pipe with a diameter of 32 mm or 40 mm, depending on the size of the blade shank.
To turn a piece of polypropylene pipe into a new and comfortable handle, we will need the most common and affordable tools and devices:
We start by removing the remains of the broken handle from the shank. It would be a good idea to treat it with a degreasing agent, wash it in warm soapy water and wipe dry with a clean cloth.
We lay a piece of polypropylene pipe of the required diameter and length on the slightly spread jaws of a bench vice and begin to heat it with the flame of a gas burner evenly on all sides.
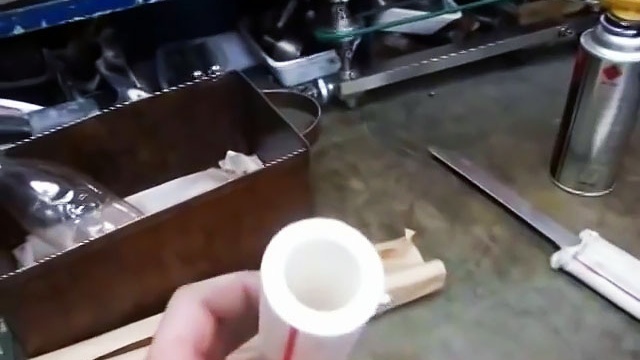
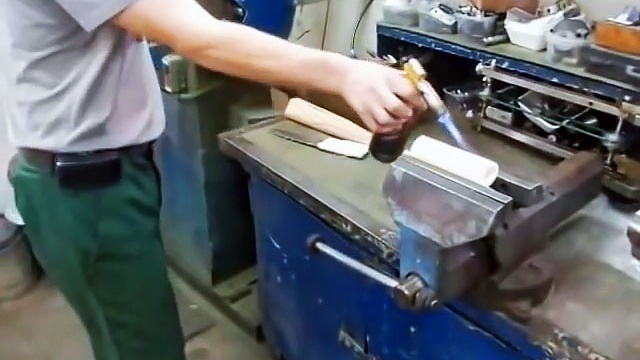
As soon as the workpiece softens enough, but does not yet begin to float and lose its shape, insert the shank of the blade into it, move the jaws of the vice apart so that the tube is between them, and begin to compress the workpiece in the transverse direction.
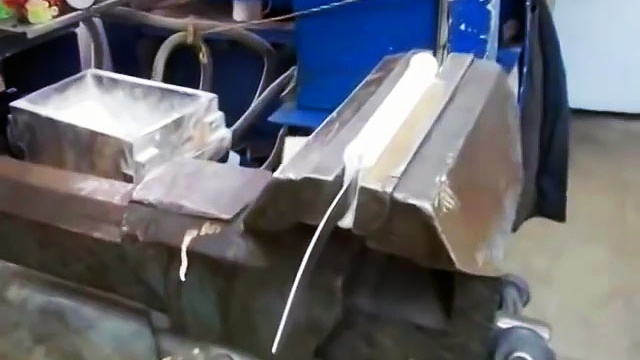
We compress until the specified handle thickness is achieved. In this case, the workpiece will increase in the vertical direction. After that, we leave the handle blank with the shank pressed into it alone for a while until the polypropylene completely hardens.
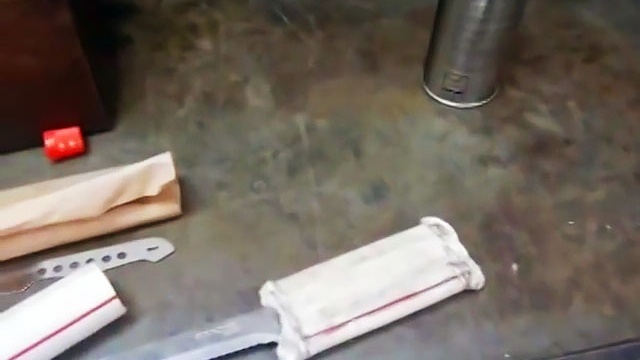
As soon as this happens, we release the workpiece and clamp it in a vice again, but in a vertical position. Then, using a hacksaw, we saw off the excess material along the contour.
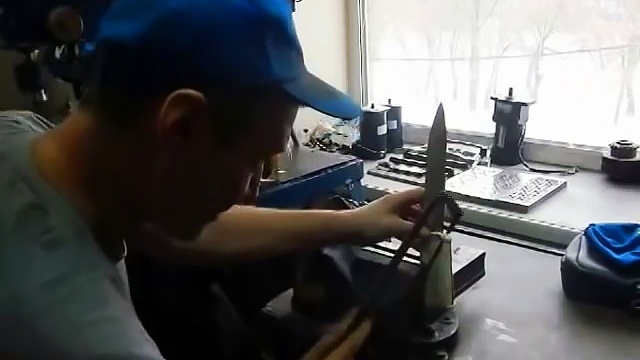
After completing this operation, the handle blank acquires the overall dimensions that were planned.
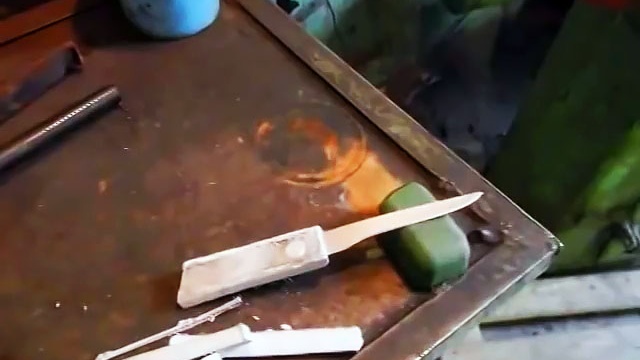
Its length is determined by the dimensions of the shank, and its width and height are determined by the comfort of the grip, ensuring the efficiency and safety of working with a knife.
The rough shape of the handle is obtained by turning it on mechanical sandpaper, first on a coarse-grained stone, then on a fine-grained one.
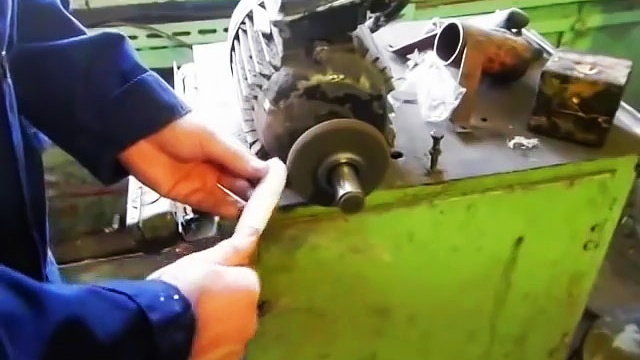

The final finishing is carried out using a set of sandpaper, processing successively with coarse, then medium, and finally with “zero” sandpaper.
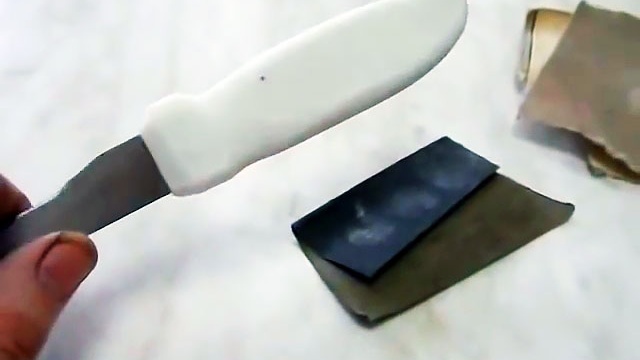
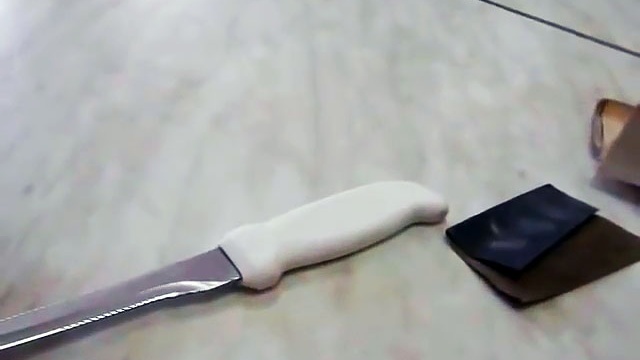
Knife handles, unlike blades, are not as durable, especially if they are made of fragile or soft material. But they can be replaced, and this is not at all difficult to do today, given the variety of materials that can be used in this capacity and make the sample no worse than the factory version, and maybe even better and more durable.

Will need
Making a new knife handle to replace a broken one does not require any special skills. We can also make do with a remaining piece of polypropylene pipe with a diameter of 32 mm or 40 mm, depending on the size of the blade shank.
To turn a piece of polypropylene pipe into a new and comfortable handle, we will need the most common and affordable tools and devices:
- gas-burner;
- bench vice;
- hacksaw for metal;
- mechanical emery;
- sandpaper set.
The process of turning a piece of polypropylene pipe into a knife handle
We start by removing the remains of the broken handle from the shank. It would be a good idea to treat it with a degreasing agent, wash it in warm soapy water and wipe dry with a clean cloth.
We lay a piece of polypropylene pipe of the required diameter and length on the slightly spread jaws of a bench vice and begin to heat it with the flame of a gas burner evenly on all sides.
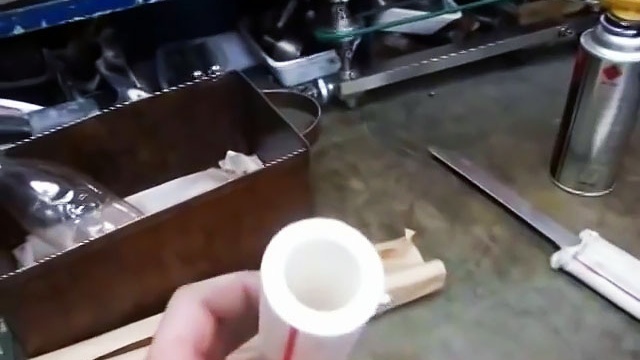
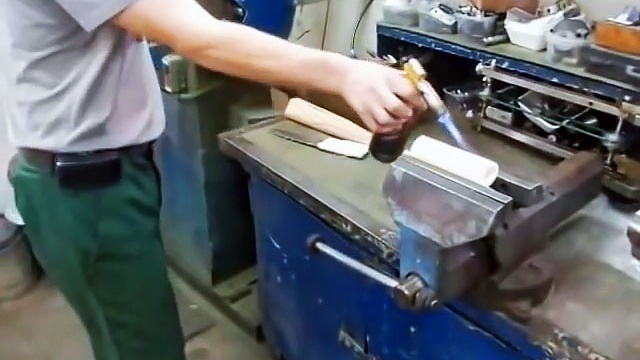
As soon as the workpiece softens enough, but does not yet begin to float and lose its shape, insert the shank of the blade into it, move the jaws of the vice apart so that the tube is between them, and begin to compress the workpiece in the transverse direction.
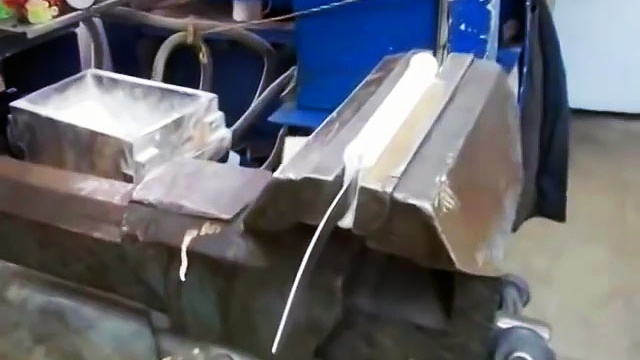
We compress until the specified handle thickness is achieved. In this case, the workpiece will increase in the vertical direction. After that, we leave the handle blank with the shank pressed into it alone for a while until the polypropylene completely hardens.
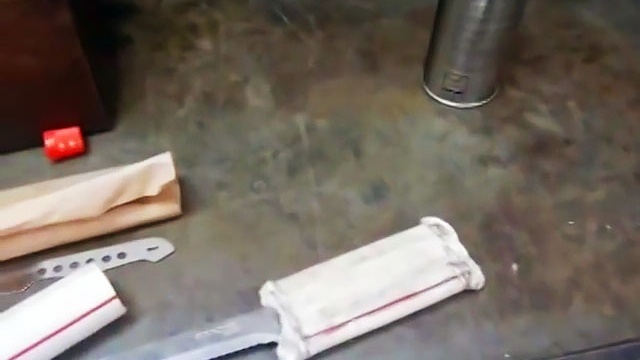
As soon as this happens, we release the workpiece and clamp it in a vice again, but in a vertical position. Then, using a hacksaw, we saw off the excess material along the contour.
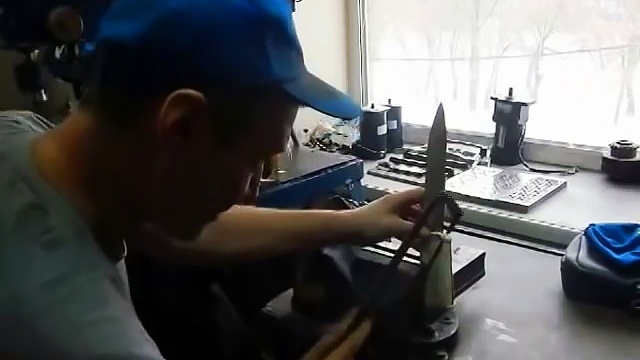
After completing this operation, the handle blank acquires the overall dimensions that were planned.
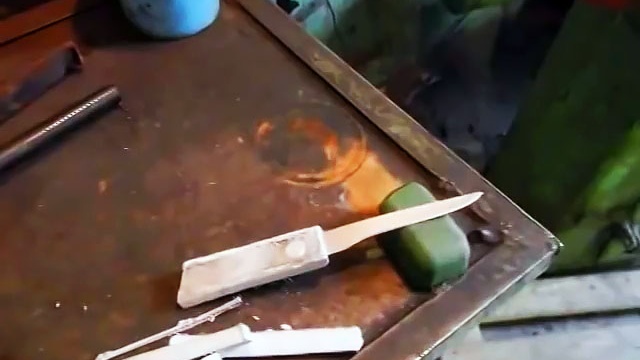
Its length is determined by the dimensions of the shank, and its width and height are determined by the comfort of the grip, ensuring the efficiency and safety of working with a knife.
The rough shape of the handle is obtained by turning it on mechanical sandpaper, first on a coarse-grained stone, then on a fine-grained one.
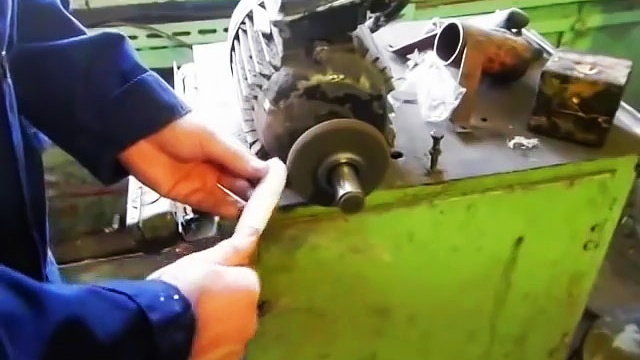

The final finishing is carried out using a set of sandpaper, processing successively with coarse, then medium, and finally with “zero” sandpaper.
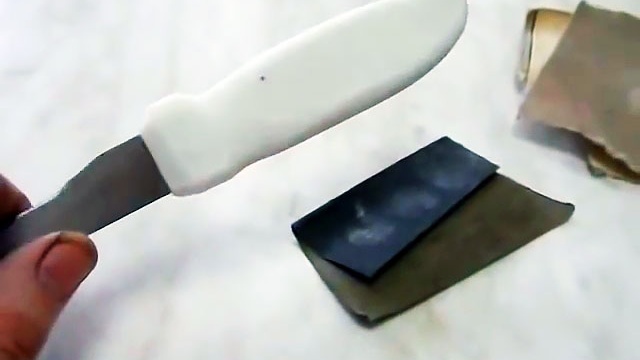
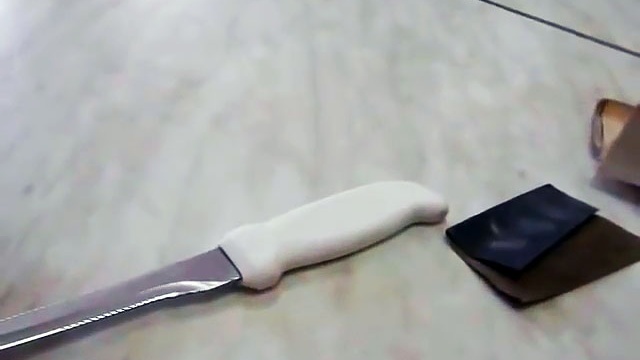
Watch the video
Similar master classes
Particularly interesting
Comments (0)