How to make a knife from broken scissors
Scissors are made from the same steel as knives. Thanks to this, fairly large scissors can be sharpened into a narrow blade, which is equipped with a Japanese universal utility knife. This tool is used for precise cutting of wood, cardboard, and leather. It is lightweight, convenient and reaches hard-to-reach places, so everyone can find a use for it.
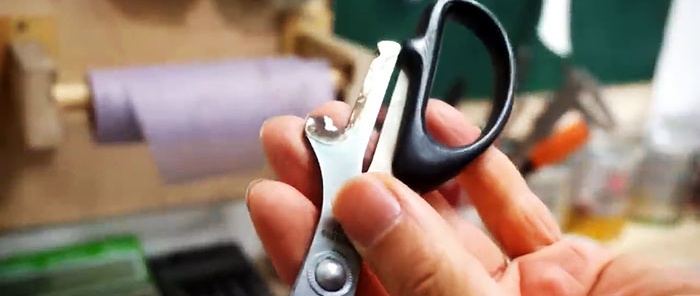
Materials:
- old scissors;
- textolite, caprolon or other sheet material;
- ordinary rivet;
- thin tube for rivet;
- epoxy adhesive.
Making a knife from scissors
Large scissors made of good steel are suitable for sharpening into a blade. You shouldn’t bother with cheap office scissors, since they won’t make a working tool that will retain its sharpness.
The scissors are disassembled; only one half with the most suitable bend shape is required for the blade.
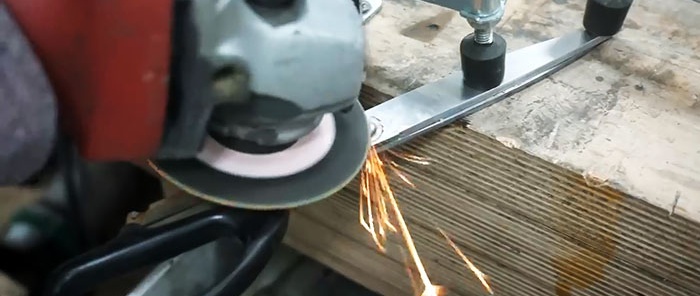
A blade is drawn right along it.
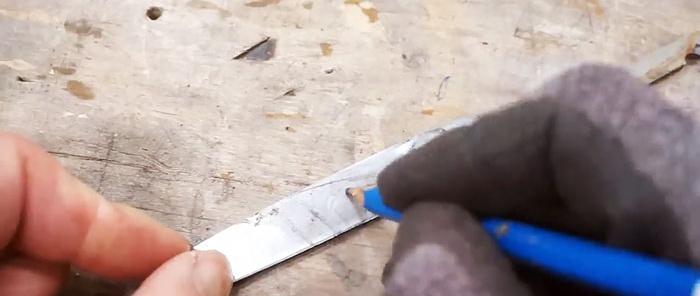
It can have a variety of shapes, the main thing is to make a beveled blade and a groove for the finger at the transition between the cutting part and the handle. The shank is a handle, which for convenience needs to be equipped with pads or wrapped with a cord, so when drawing you need to take this into account.
The workpiece is cut with a grinder or drill with a cutting disc.
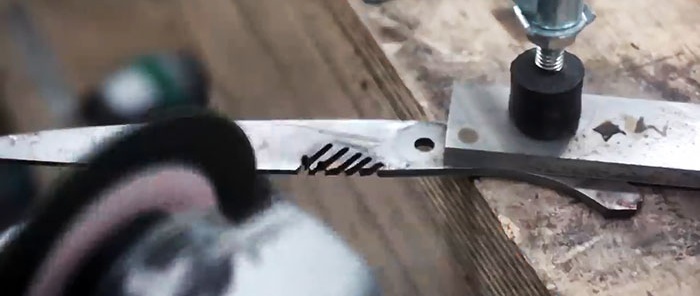
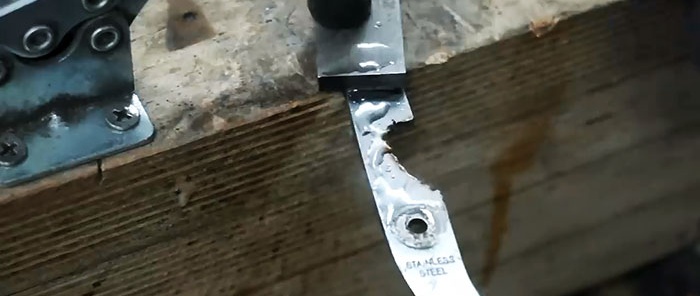
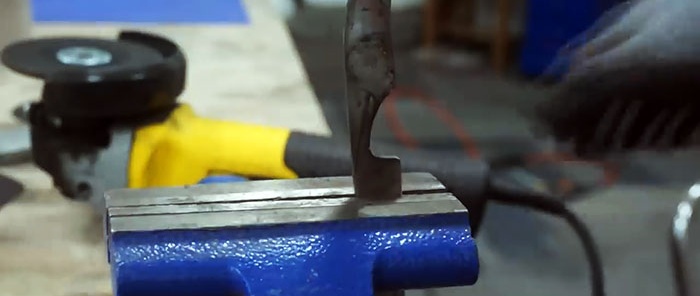
After this, the edges are smoothed using an emery machine. Next, a trigger is brought out on the right side, which will allow you to make precise cuts with the knife in the future; for a left-handed person, it is ground off on the left.
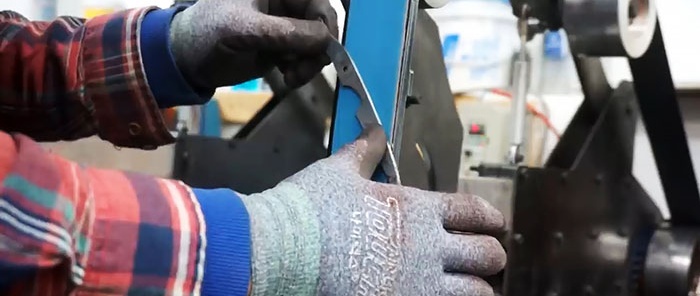
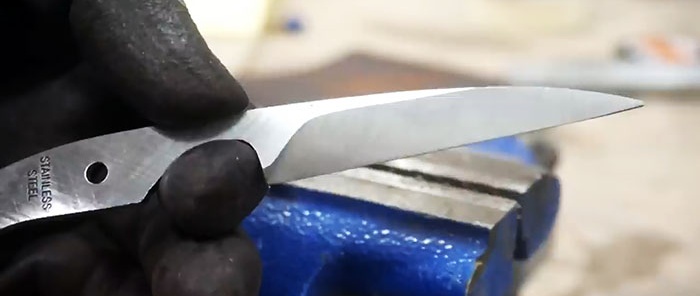
The knife handle is made of textolite or caprolon linings.
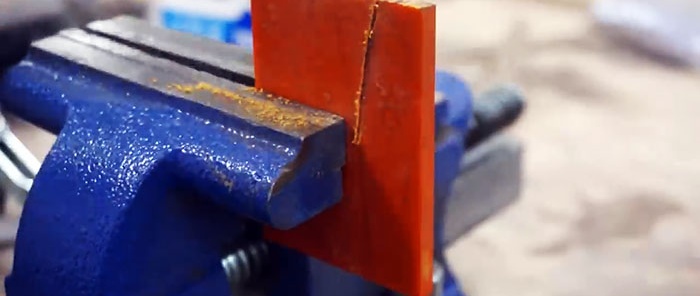
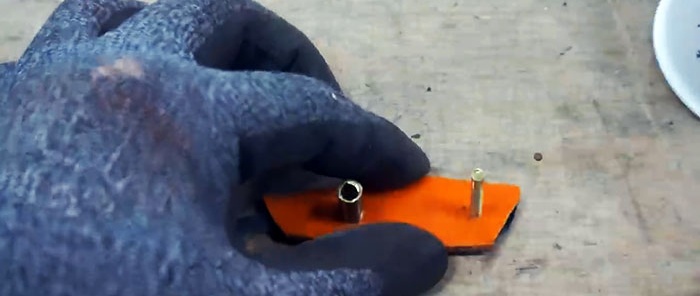
You can also make an additional insert from sheet plastic. The pads will stick to the shank, so for better glue adhesion they need to be sanded with coarse sandpaper. It is also necessary to immediately drill holes for rivets in them, as on the shank.
For gluing it is better to use epoxy glue. First, a plastic insert is glued to the shank, then a textolite one. Only textolite can be used. To prevent the linings from moving relative to the holes, you must immediately insert the rivets. Until the glue hardens, the handle is compressed in a vice or tightened with clamps.

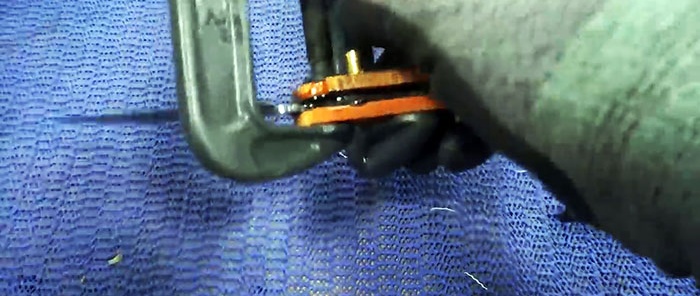
After drying, you need to splash the rivets. The handle is given the required shape using a file and sandpaper.
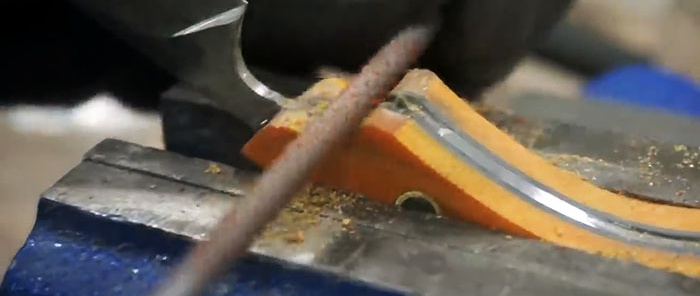
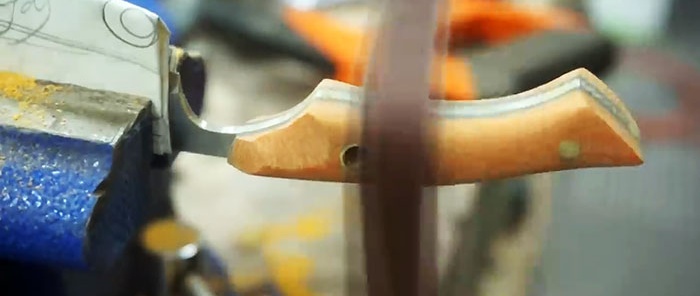
This is a delicate, unhurried job, so it’s better not to use sandpaper. To later remove the whitish roughness of the PCB, the handle can be wiped with oil.
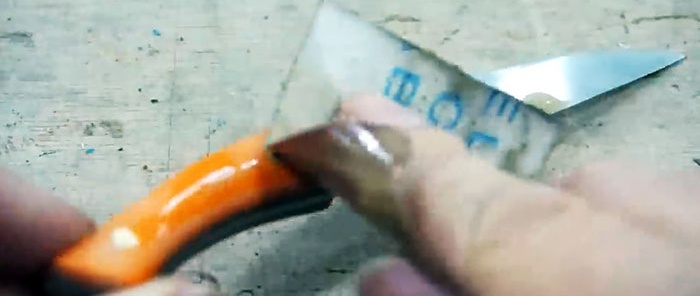
After finishing the handle, the blade is finally sharpened to a razor sharpness.
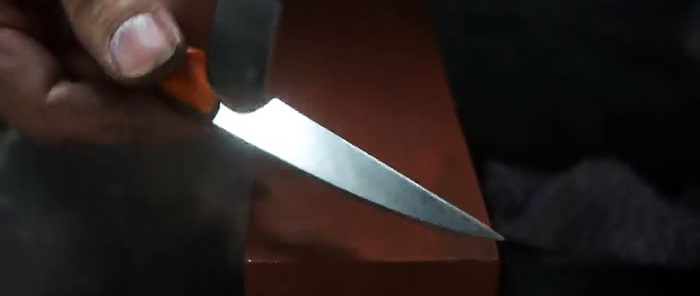
A knife with one trigger dulls slowly and is easy to sharpen. A thin knife made from scissors can work when cutting almost any soft materials.
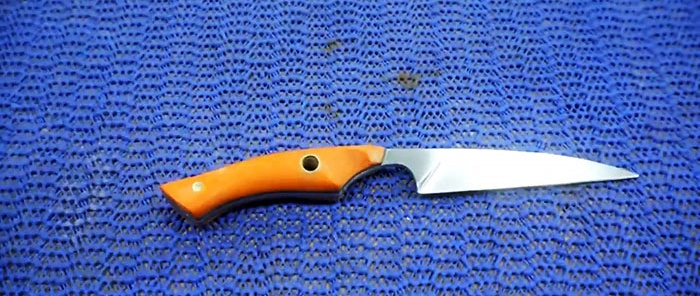
The main thing is not to put too much pressure on it, since the blade is thin. A Japanese knife should cut using sharpness, not pressure.
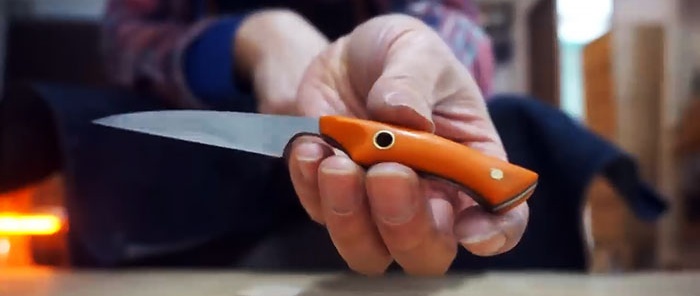
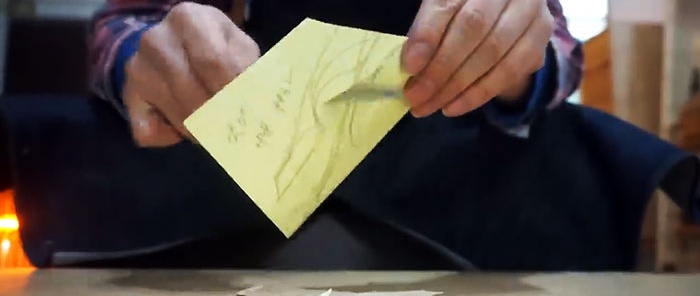