How to make an extruder for melting plastic from a sealant gun
Many types of plastic are useful raw materials for recycling. By melting them into a plastic mass, you can make homemade filament for a 3D printer or figurines, souvenirs, etc. crafts. Let's look at how you can make a manual compact extruder for plastic processing.
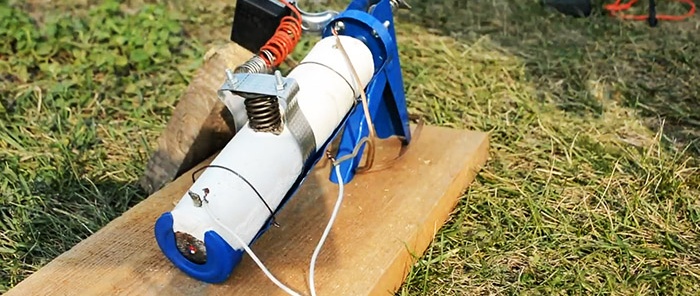
An asbestos cord is wound onto a piece of steel pipe equal in length to a tube for sealants. It is important that the end of the pipe is welded and has a small central hole.
A nichrome thread is wound over the asbestos. It can be obtained from an aligned spiral from an electric stove.
The spiral is then covered with a new winding of asbestos cord.
A mechanical thermostat from the oven is attached to the sealant gun.It must be secured so that the adjustment knob is located on the back of the gun.
A mold for casting in the form of a pipe is made from a plastic detergent bottle. To do this, its bottom and neck are cut off, after which it unfolds lengthwise.
On one side, the workpiece is bent, and notches are cut out on the bend. The resulting sheet is wound onto any tube with a diameter of about 5 cm. Then the workpiece is secured with tape. The notches form its bottom. On the side of the resulting form you need to make a small hole equal to the diameter of the temperature sensor. You need to insert a tube made of rolled up sheet plastic into it.
Then a steel tube with a winding of nichrome thread and asbestos cord is placed into the bottle mold. On one side it is fixed with cut notches. The side tube is pressed close to the winding. The ends of the nichrome thread are brought out into the holes along the edges of the mold.
Next, a heat-resistant solution made from sand and gypsum plaster is poured into the empty space between the plastic shell and the steel core.
After the solution hardens, the top tube is removed from the cut bottle.
A temperature sensor is installed in the side hole free of solution, which is secured with a clamp. The ends of the nichrome thread are connected to an electrical cable with a plug. Plastic chips are poured inside the steel pipe. This can be HDPE plastic from finely chopped caps from PET bottles, or ABS plastic, which can be obtained from the casings of old household appliances.
Next, the pipe filled with plastic is installed in a sealant gun. The gun rod with the plate is launched into it. If the plate turns out to be large, then it must first be sharpened.Now, by plugging in the plug and adjusting the temperature, you can heat up the mass. Then, using the usual movements of the pistol lever, it should be squeezed out.
The resulting extruder can be used in different ways. If you put a thin spout on the end of the pipe, you will be able to get filament for a 3D printer. It is also possible to squeeze the hot mass into various shapes, making figures, handles for furniture, parts for mechanisms, etc.
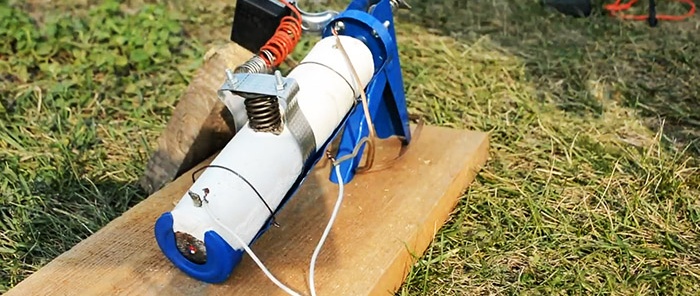
Materials:
- sealant gun;
- steel tube;
- asbestos cord;
- nichrome thread;
- wire with plug;
- mechanical thermostat from an electric oven;
- plastic detergent bottle;
- scotch;
- sand;
- gypsum plaster.
Making an extruder
An asbestos cord is wound onto a piece of steel pipe equal in length to a tube for sealants. It is important that the end of the pipe is welded and has a small central hole.
A nichrome thread is wound over the asbestos. It can be obtained from an aligned spiral from an electric stove.
The spiral is then covered with a new winding of asbestos cord.
A mechanical thermostat from the oven is attached to the sealant gun.It must be secured so that the adjustment knob is located on the back of the gun.
A mold for casting in the form of a pipe is made from a plastic detergent bottle. To do this, its bottom and neck are cut off, after which it unfolds lengthwise.
On one side, the workpiece is bent, and notches are cut out on the bend. The resulting sheet is wound onto any tube with a diameter of about 5 cm. Then the workpiece is secured with tape. The notches form its bottom. On the side of the resulting form you need to make a small hole equal to the diameter of the temperature sensor. You need to insert a tube made of rolled up sheet plastic into it.
Then a steel tube with a winding of nichrome thread and asbestos cord is placed into the bottle mold. On one side it is fixed with cut notches. The side tube is pressed close to the winding. The ends of the nichrome thread are brought out into the holes along the edges of the mold.
Next, a heat-resistant solution made from sand and gypsum plaster is poured into the empty space between the plastic shell and the steel core.
After the solution hardens, the top tube is removed from the cut bottle.
A temperature sensor is installed in the side hole free of solution, which is secured with a clamp. The ends of the nichrome thread are connected to an electrical cable with a plug. Plastic chips are poured inside the steel pipe. This can be HDPE plastic from finely chopped caps from PET bottles, or ABS plastic, which can be obtained from the casings of old household appliances.
Next, the pipe filled with plastic is installed in a sealant gun. The gun rod with the plate is launched into it. If the plate turns out to be large, then it must first be sharpened.Now, by plugging in the plug and adjusting the temperature, you can heat up the mass. Then, using the usual movements of the pistol lever, it should be squeezed out.
The resulting extruder can be used in different ways. If you put a thin spout on the end of the pipe, you will be able to get filament for a 3D printer. It is also possible to squeeze the hot mass into various shapes, making figures, handles for furniture, parts for mechanisms, etc.
Watch the video
Similar master classes
Particularly interesting
Comments (3)