Drill-based push drilling machine for home workshop
Drilling involves precision work. The hole in the workpiece must be drilled evenly. Otherwise, the parts will not match correctly and you will have to redo everything all over again. In a home workshop, not everyone can afford to have a drilling machine. But anyone can make a homemade device for precision drilling. A conventional drill is installed in such an auxiliary device and can be used to produce high-quality work.
Will need
For work you will need the following material:- A sheet of metal 6 mm thick with dimensions (with a margin) of 300 by 300 mm;
- Profile pipe 40 by 40 mm 300 long;
- A piece of pipe with an internal diameter similar to a drill mount 1 pc. height 20 mm;
- Door spring 1 pc.;
- Hexagon socket bolt M10 9 pieces.
Manufacturing process of drill press machine
In a section of a 40x40 mm profile pipe, 300 mm long, a through hole of 8.5 mm is drilled in the center at a distance of 15 mm from one edge.
Then, using an M10 tap, a thread is cut on both sides of the pipe hole.A 40*40 square is cut from sheet metal 6 mm thick - this will be the plug. Once installed on the pipe from the side of the holes, it will be necessary to weld it.
To make a platform that will be screwed to the base, 6 mm thick metal with dimensions of 100 by 60 mm is cut.
We retreat 15 by 15 mm from each corner side and drill 4 holes by 10 mm. Then we place the resulting workpiece on the other unplugged side of the profile pipe in the middle and scald it.
It's time to make a working base. To do this, take a sheet of metal with a thickness of 6 mm and dimensions of 100 by 200 mm.
From the 100 mm side, it is necessary to mirror the holes from the platform and drill them into the base with an 8.5 mm drill. Then you should cut M10 threads in these four holes.
From the other edge of 100 mm where there are no holes, you should retreat 80 mm and drill a hole in the center with a Pobedit drilling head of 50 mm.
The platform is screwed to the base using four M10 internal hexagon bolts 20 mm long.
We proceed to the manufacture of a moving element in which the drill will be fixed. To do this, 4 blanks with dimensions of 47 by 70 mm are cut out of a 6 mm sheet of metal.
Having fastened the workpieces with an overlap so that in the middle you get a 40 by 40 square, scalding should be done.
In the resulting workpiece, stepping back 15 mm from the edge in the center, we drill a hole of 8.5 mm on both sides.
We cut the M10 thread. We cut a 40 by 30 mm blank from a 6 mm sheet of metal. To make fasteners for a drill, take a pipe with an approximate internal diameter like that of a drill near the chuck.
The workpiece is cut and, if necessary, the dimensional accuracy is adjusted on a lathe by boring. Next, an 8.5 hole is drilled in the middle of the round workpiece and an M10 thread is cut.
A 40 by 30 piece and a machined workpiece are welded to the driving element on the side opposite to the holes. The chassis is placed on the stand, a drill is inserted into the mount and secured with a bolt.
To make a reverse mechanism, you need to cut the springs. To do this, take a door spring and cut two 100 mm sections from it. On each side of the spring, rings are bent with pliers for fixation. Bolts are screwed into the upper part of the main rod, onto which the springs are placed.
While the second part of the springs is fixed to the chassis with bolts. Now you can install the appropriate tool and perform precise drilling.
Helpful information
Remember, when performing any mechanical processing of metal, personal safety rules must be observed. When operating an angle grinder, you must use safety glasses, a respirator, ear protection and gloves. Wear goggles when operating lathes and drilling machines.
There is no doubt that the jig works and drills holes accurately. But it is necessary to make such a thing when the need for drilling holes through the squint is great.
By following these simple rules of work, your health will be fine for many years to come.
Watch the video
Similar master classes
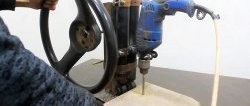
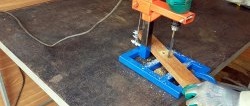
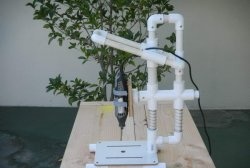
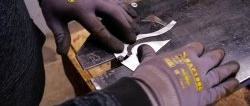
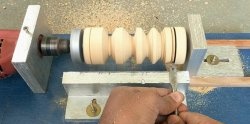
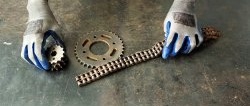