Comment utiliser un compresseur de réfrigérateur comme aérographe
article sur l'utilisation d'un vieux compresseur d'un réfrigérateur pour une utilisation dans un aérographe.
Donc chapitre premier : la production.
En règle générale, sous nos latitudes, l'habitat des compresseurs sauvages ou sauvages est assez petit, bien que des exceptions se produisent. Le plus souvent, on les trouve à proximité des poubelles dans les cours des maisons ou dans les sous-sols où sont stockés toutes sortes de déchets. Habituellement, ils sont fermement vissés sur une grande boîte blanche, communément appelée réfrigérateur, dans laquelle la bière est stockée. Vous ne pourrez pas chasser un compresseur sauvage à mains nues ; il ne vous sera pas simplement offert. En attendant, pendant que vous courez aux armes, le compresseur sauvage pourrait bien devenir domestique, mais déjà étranger.
Vous devez avoir avec vous un ensemble d'armes spécial - pinces, tournevis à tête plate et cruciforme, 2 clés 12x14. Si vous trouvez une grande boîte blanche, vous devez l'inspecter soigneusement ; généralement le compresseur est caché dans sa partie inférieure, à l'arrière. Si le compresseur est trouvé et que vous disposez de l'ensemble d'armes nécessaire, vous pouvez commencer l'exploitation minière.
L'extraction d'un compresseur est un processus simple, mais vous devez l'aborder avec précaution, sinon des problèmes pourraient survenir plus tard. La première chose à faire est d'utiliser une pince ou une pince coupante pour mordre les tubes de cuivre qui vont à la grille de refroidissement, avec une marge d'au moins 10 cm, ou mieux encore, au maximum, alors les tubes supplémentaires vous seront utiles (sur certains types de compresseurs, une plaque métallique avec des chiffres en relief est fixée sur les tubes - ne la jetez pas, elle peut aussi être utile). De plus, il faut arracher les tubes ! Vous ne devez en aucun cas couper, les copeaux vont certainement pénétrer à l'intérieur, et votre compresseur peut alors tomber très malade et mourir. Une fois mordus, les tubes s'aplatiront, vous n'aurez pas à vous en soucier et cela vous aidera également à éviter de vous couvrir d'huile pendant le transport.
A ce stade, je peux recommander de verser une goutte d'huile du compresseur sur un morceau de papier propre et de vérifier la présence de particules métalliques. Si des grains de poussière d’argent sont remarqués dans l’huile, vous n’avez pas besoin de continuer plus loin et d’honorer la mémoire bénie de l’unité décédée par une minute de silence.
Deuxièmement et surtout, le compresseur ne se compose pas seulement de matériel, il possède un autre organe très important - le relais de démarrage. Le relais ressemble à une petite boîte noire (parfois blanche), vissée séparément avec des vis à côté du compresseur, avec des fils entrant et sortant. Il faut dévisser soigneusement le relais du réfrigérateur, et de la même manière débrancher soigneusement le connecteur qui va du relais au corps du compresseur (cela s'applique aux anciens pots ; pour les autres types de compresseurs, le relais peut ne pas être amovible). Il faudra très probablement couper les 2 fils entrants ; ils ne vont toujours pas directement à la prise. Il y a un autre point important - vous devez vous rappeler ou marquer dans quelle position le relais a été vissé, où se trouvent le haut et le bas, c'est parfois signé, mais pas toujours.Pourquoi c’est important – plus d’informations ci-dessous.
Et enfin, troisièmement, à l'aide de 2 clés de 12 mm, dévissez le corps du compresseur du réfrigérateur. Il est généralement fixé avec 4 boulons et écrous à travers des joints en caoutchouc. Il est conseillé d'emporter avec vous l'ensemble de cet ensemble d'attaches et d'élastiques, il pourra être utile lors des préparations ultérieures des travaux.
Chapitre deux : préparation (domestication).
Alors, vous venez de recevoir votre compresseur, enduit de saleté et d'huile, les mains égratignées et tendues jusqu'aux genoux, fatigué mais heureux, vous êtes finalement arrivé chez lui. Vous pouvez maintenant commencer à préparer le compresseur pour son fonctionnement. La première chose à faire est un lancement de contrôle. Nous connectons le connecteur du relais aux contacts du boîtier du compresseur. Nous orientons et fixons temporairement le relais sur une surface horizontale, vous pouvez même le coller avec du scotch. L'essentiel est de sécuriser le relais tel qu'il était au réfrigérateur, il fonctionne par gravité et par échauffement des plaques. Si vous l'orientez mal, ou si vous le jetez simplement en l'air, il ne fonctionnera pas correctement, ce qui peut être fatal tant pour le relais que pour les enroulements du moteur du compresseur.
Soigneusement et à l'aide de ruban isolant, fixez un fil temporaire avec une fiche aux fils entrant dans le relais. Je recommande fortement d'envelopper la zone de torsion avec du ruban isolant, votre sécurité et votre vie en dépendent. Il existe déjà peu de modélistes, valorisons-les ainsi que nous-mêmes. Les tubes aplatis doivent être sertis avec une pince, ils vont s'écarter et libérer le passage de l'air.
Lorsque tout est prêt et sécurisé, vous pouvez brancher la fiche dans la prise. Cela s'accompagne généralement d'une légère étincelle et d'un pop, mais la charge reste considérable. Si tout est en ordre, le compresseur doit s'allumer et vibrer doucement. L'air doit sortir du tube, vous devez marquer lequel d'entre eux « inspire » et lequel « expire ».Il n'est pas nécessaire de conduire longtemps, l'essentiel est de s'assurer que l'unité assemblée fonctionne correctement. Si ce n’est pas en ordre et que le compresseur ne démarre pas, ou démarre et s’éteint au bout d’un moment, la situation est plutôt mauvaise. Pour une petite inspection, vous devez être familier avec l’électrotechnique et disposer d’un testeur. Si vous n’êtes pas à l’aise avec ces choses, je ne vous recommande pas de fouiller davantage.
Eh bien, si vous êtes amis ou si vous avez une idée, continuons. Vous devez retirer le connecteur du relais du compresseur et faire sonner les enroulements du moteur. Ils devraient sonner avec peu de résistance les uns aux autres, quelle que soit leur combinaison. Si l'un des enroulements ne sonne pas, nous tenons dans nos mains le corps d'une unité morte. Si vous appelez, cela signifie que vous devez inspecter et nettoyer le relais. Ouvrez délicatement la boîte et nettoyez les contacts avec du papier de verre fin. L’essentiel est de ne pas les plier ou de les casser ; il ne faut pas non plus les frotter trop fort.
Ensuite, nous remettons tout en place, le sécurisons comme il se doit et essayons de le rallumer. S'il ne redémarre pas ou s'éteint - hélas, pas de chance... (A condition que le relais soit d'origine et livré avec ce compresseur. Un arrêt d'urgence peut également survenir du fait que le moteur est plus puissant que le celui pour lequel le relais est conçu, vous devrez alors chercher un autre relais, et le signe sur le combiné vous y aidera.) Cependant, ne parlons pas de choses tristes, nous espérons que tout a fonctionné.
Vous devez maintenant assembler votre unité en un appareil plus adapté et plus compact. Bien sûr, je ne prétends pas être la vérité, chacun a ses propres capacités et moyens pour atteindre cet objectif, mais je vais décrire mon approche pour assembler l'ensemble de l'appareil. Pour ce faire, vous devez vous rendre au magasin de pièces automobiles, au marché automobile ou au stand de pièces détachées le plus proche. Là, vous devez acheter :
Un litre d'huile moteur de remplacement, 10w40 ou autre minérale ou semi-synthétique.Habituellement, un litre est le contenant minimum, mais si vous avez de la chance, il arrive au robinet, même 500 grammes suffisent. Au pire, vous pouvez lubrifier toutes les charnières qui grincent de la maison.
Un tube en caoutchouc renforcé résistant à l'huile et à l'essence, d'environ un mètre de long et 4 mm de diamètre interne. C'est une bonne idée d'avoir avec vous un morceau de tube en cuivre provenant du compresseur, vous pouvez y essayer le tube en caoutchouc souhaité.
Pinces à cravate en métal, 6 pièces. Ils doivent être essayés avec un tube en caoutchouc fraîchement acheté. Ils devraient avoir un diamètre un peu plus grand.
Tube de chlorure de vinyle pour lave-verres. Ils sont translucides, il y en a aussi des renforcés, mais nous n'en avons pas besoin. La longueur doit être choisie en fonction de l'emplacement du compresseur et du confort de fonctionnement, mais pas inférieure à 2 mètres.
2 filtres fins - un pour l'essence, le second pour le diesel. Ils sont visuellement différents - pour l'essence il y a un accordéon en papier à l'intérieur, pour le diesel il y a un maillage synthétique à l'intérieur.
Un tube de mastic silicone résistant au pétrole et au gaz, de consistance épaisse et de couleur grise est préférable, plus de liquide et de noir est pire.
Après avoir acheté tout cela, vous devez vous rendre à la quincaillerie la plus proche. Dans celui-ci, vous devez acheter :
Un cordon avec une fiche à son extrémité pour alimenter le compresseur sur le réseau. Au moins 1,5 mètres de long, de préférence double isolation.
Interrupteur d'éclairage à touche unique dans un boîtier de type fermé, pour installation extérieure.
Vis à bois pour meubles 3,5 x 16 ou 3x16.
Maintenant, tout ce groupe doit être combiné et nous obtiendrons l'unité souhaitée.
Le premier et le plus important point de préparation, dont dépendent le fonctionnement ultérieur et la durabilité du compresseur, est la vidange de l'huile. De nombreux exemplaires ont été cassés à cet égard, il faut changer, il n'est pas nécessaire, quelle huile verser et laquelle non.
Il peut y avoir plusieurs opinions, mais la bonne est la mienne ! Pour que plus tard des questions vides de sens ne se posent pas comme « est-ce que ça marche bien pour moi sur le tournesol ! », j'écrirai mon point de vue sur ce moment.
De l'huile pure "de broche" (fréon, compresseur - comme on ne l'appelait pas) est versée à l'intérieur du compresseur en usine. En fait, elle est minérale. Elle ne contient aucun additif, car le compresseur du réfrigérateur fonctionne dans un environnement fermé et fermé. espace sans air (sans oxygène) et n'est exposé à aucune influence de l'environnement extérieur. Lorsque nous commençons à l'utiliser à nos fins, la situation change radicalement. L'huile commence à être affectée par l'oxygène de l'air, les microparticules de poussière, l'humidité, etc. L'huile minérale s'encrasse et s'oxyde assez rapidement, perdant ses propriétés. Cela entraîne un fort échauffement du compresseur pendant le fonctionnement, du bruit, une usure du système de piston et, finalement, un blocage. Et ce malgré le fait qu'il y avait suffisamment d'huile. De plus, en raison des faibles propriétés liantes et mouillantes de l'huile minérale, elle volera intensément vers la sortie, obstruant les vapeurs d'air et réduisant le niveau de fonctionnement du compresseur.
L'huile automobile (moteur) est dépourvue de la plupart de ces problèmes, principalement en raison du fait qu'elle contient un ensemble d'additifs qui compensent ou éliminent complètement les mauvais facteurs qui affectent la qualité et la durabilité de l'huile. De plus, il est conçu pour des conditions de fonctionnement beaucoup plus sévères que celles qui seront présentes dans votre compresseur. Par exemple, j'utilise un moteur semi-synthétique 10w40, car il reste après avoir changé l'huile de ma voiture. Vous pouvez utiliser de l'huile minérale et semi-synthétique avec d'autres indices, mais je ne recommande pas d'utiliser des huiles synthétiques.Premièrement, ils sont nettement plus chers et, deuxièmement, ils sont plus liquides et moins durables.
J'espère avoir écrit de manière convaincante, même si, bien sûr, il y aura des non-croyants qui s'obstineront à verser toute l'huile sur laquelle ils pourront mettre la main et, enfin, le drapeau pour eux.
Revenons à notre ami de fer. Ici se pose un certain point technique, à savoir quel type de compresseur vous avez entre les mains. Visuellement, ils sont divisés en 2 types principaux - un cylindre et un pot (ressemble à un vase de nuit recouvert d'un couvercle convexe). Les premiers sont une espèce presque éteinte ; ils étaient utilisés dans des types de réfrigérateurs très anciens et ont cessé d'être produits à la fin des années 70. Mais si vous avez réussi à faire vivre ce type de compresseur, vous avez beaucoup de chance. Ils peuvent fournir une pression de sortie beaucoup plus élevée que les autres. Le plus souvent, c'est le deuxième type de compresseur qui nous tombe entre les mains : les pots.
La principale différence pour nous à ce stade est de savoir où changer l'huile. Dans les cylindres, le plus souvent un énorme boulon est vissé sur le côté du boîtier ; il ferme le goulot de remplissage. Vous devez le dévisser avec une clé, vidanger l'ancienne huile du compresseur dans un récipient jetable. Il est conseillé de mesurer la quantité de cette huile. Selon le type de cylindre, il faut les remplir de 300 à 500 grammes d'huile. Revissez ensuite soigneusement le boulon, en le recouvrant de préférence d'un produit d'étanchéité résistant à l'huile et à l'essence.
Le pot est un peu plus compliqué. Il y a généralement 3 tubes qui en sortent : l'inspiration, l'expiration et un tube de remplissage scellé. Il est conseillé de changer l'huile par celui-ci. Pour ce faire, il faut ouvrir ce tube, on peut le couper un peu avec une lime aiguille en cercle au-dessous de l'endroit aplati, mais en aucun cas le couper à travers. Ensuite, le long de la coupe, vous devez casser le tube et le casser complètement en le balançant sur les côtés.La bavure formée le long du bord doit être légèrement battue avec un marteau. Ensuite, vidangez simplement l'huile du pot, en l'inclinant vers les tubes, dans n'importe quel récipient jetable. N'oubliez pas qu'après avoir vidangé l'huile, n'allumez en aucun cas le compresseur !
Vous devrez remplir le compresseur avec une seringue en versant progressivement de l'huile dans le tube de remplissage ; vous pouvez mettre un tube en caoutchouc en forme d'entonnoir improvisé. Environ 250 à 350 grammes d'huile par pot sont nécessaires. Après le ravitaillement, le tube doit être bouché, sinon l'air s'en échappera (ou vice versa - entrera par le filtre, selon le type de compresseur). Vous pouvez bien sûr l'aplatir, mais ce n'est pas pratique, car il faudra alors changer l'huile. Je recommande de visser une petite vis autotaraudeuse d'un diamètre adapté, sous la tête de laquelle se trouvera une rondelle-entretoise en caoutchouc.
Comme dans le cas de l'huile, il y aura des camarades désespérés ou paresseux qui tenteront d'alimenter le compresseur en huile en déplacement, en l'ajoutant au tube d'aspiration - je ne recommande fortement pas de le faire. Tout d'abord, il est conseillé de changer l'huile en une seule fois, mais allumer le compresseur avec l'huile vidangée signifie le tuer. Deuxièmement, il existe un tel phénomène dans les appareils à piston - les coups de bélier. C'est lorsque le liquide pénètre dans l'espace au-dessus du piston dans un volume supérieur à celui de la chambre de compression. Les liquides, comme nous le savons, ne sont presque pas comprimés, mais le moteur du compresseur essaiera de le faire. En conséquence, nous pourrions subir une destruction du système de piston. J'espère que je vous ai également convaincu de cela.
Et donc nous continuerons. Nous allons maintenant tout mettre en tas, selon le schéma donné.
Ce schéma est destiné aux aérographes à simple action, comme notre bien-aimé « Eton » - alias biélorusse, ou aux aérographes à double action convertis en simple action.
Vous pouvez, bien sûr, tout connecter et le laisser suspendu, mais cette structure se brisera et s'effondrera constamment. Je pense que si vous faites un petit effort et combinez le tout sur une plate-forme ou dans un boîtier, cela sera plus fiable et vous procurera plus de plaisir de travailler. Je n’ai pas la prétention de standardiser, mais mon type d’assemblage ne nécessite absolument pas l’utilisation de machines, de soudures ou d’outils spéciaux. Tous les matériaux sont également disponibles et leur coût est faible. Pour le résultat le plus simple et le plus fiable, vous pouvez assembler la structure sur une feuille de contreplaqué ou d'aggloméré. Les dimensions de cette feuille dépendent principalement du type de récepteur choisi ou obtenu. Le récepteur est nécessaire pour au moins deux fonctions : il atténue les pulsations de pression d'air inévitables pendant le fonctionnement du compresseur et sert de piège à vapeur et à gouttelettes d'huile. Pour les aérographes à simple action bon marché, parmi lesquels le très utilisé "Eton" - également connu sous le nom de biélorusse - un récepteur de grande capacité est totalement inutile ; un volume d'environ 1 à 2 litres est suffisant.
Comme le montre la pratique, presque tous les conteneurs hermétiquement fermés sont utilisés comme récepteurs - des bouteilles en plastique pour boissons et bières aux récepteurs industriels de camions et d'équipements. À mon avis, l'utilisation de bouteilles en plastique, et plus encore en verre, est quelque peu dangereuse : ces matériaux n'ont pas une bonne résistance mécanique, et même une légère pression dans le récipient peut le rompre s'il est endommagé et provoquer des blessures.Vous pouvez bien sûr utiliser des éléments tels qu'un cylindre d'extincteur, mais cela agrandit quelque peu et alourdit l'ensemble de la structure.
Les conteneurs les plus optimaux pour le récepteur sont de petits bidons de nourriture pour l'eau en polyéthylène blanc translucide ou, comme dans mon exemple, un vase d'expansion d'une voiture Lada. Le polyéthylène à partir duquel ces conteneurs sont fabriqués est assez épais et visqueux, ne craint pas les dommages mécaniques causés par la chute de petits objets et conserve ses propriétés assez longtemps. Même si une rupture se produit, elle ne produit pas de fragments ou de chutes de matière. Pour ceux qui ne souhaitent pas utiliser de tels matériaux sous pression, je peux vous conseiller de regarder de plus près les petits bidons d'essence en métal soudé d'un volume de 5 litres.
Adapter un bidon ou un réservoir pour un récepteur est assez simple : il faut prendre 2 tubes, par exemple en cuivre, découpés dans un compresseur, chacun d'environ 15 cm de long. N’oubliez pas qu’il doit y avoir des tubes d’au moins 10 cm de long sur le compresseur. 2 trous sont percés dans le couvercle du bidon dans lesquels ces tubes doivent s'insérer étroitement. Ensuite, depuis l'intérieur du couvercle, l'endroit où entrent les tubes est rempli de résine époxy, il n'est pas nécessaire de le remplir complètement, il faut laisser un peu plus d'espace pour le vissage du col. Lorsque tout sèche, vous devez lubrifier le col et le bouchon avec du mastic et les visser fermement. À ce stade, il est important de placer correctement les tubes : leurs extrémités ne doivent pas être côte à côte et le tube sortant doit être plus haut que celui entrant (comme sur le schéma).
Maintenant que tout est préparé, vous pouvez déterminer la taille de feuille de contreplaqué dont vous avez besoin. Vous ne devez pas l’assembler de manière serrée, car il sera plus difficile à entretenir, et le compresseur doit disposer d’un espace autour de lui pour la circulation de l’air et le refroidissement.Dans mon cas, un morceau de 30 x 40 cm suffisait. Le contreplaqué devait avoir au moins 9 mm d'épaisseur, une feuille de panneaux de fibres de 15 mm. Couper les coins et traiter avec du papier de verre grossier est déjà un avant-goût. Mais les éclats dans les doigts ne feront pas plaisir.
Aux coins de la tôle sur sa future partie inférieure, il faut fixer les pattes, en caoutchouc ou, par exemple, les bouchons des bouteilles en plastique avec des vis (une bonne raison de prendre 4 bières « une et demie »). L'essentiel est de ne pas le visser jusqu'au sol ou à la table. Les pieds sont nécessaires pour réduire le bruit lorsque le compresseur fonctionne, l'empêcher de « ramper » et rayer le sol est également désagréable.
Ensuite, 4 trous sont percés pour les supports du compresseur ; j'espère que vous n'avez pas oublié de prendre les boulons avec vous ? Il est possible que lors de l'utilisation d'une épaisse feuille de contreplaqué ou de panneaux de particules, la longueur des boulons standard ne soit pas suffisante, vous devrez alors en acheter des plus longs avec des écrous dans une quincaillerie ou un magasin automobile.
Le plus difficile est de sécuriser le récepteur. Il doit être installé en premier afin que d'autres parties de l'unité n'interfèrent pas plus tard. Il n'est pas nécessaire de percer le récepteur de part en part avec des attaches ; une approche créative est ici nécessaire - par exemple, utiliser un tube ou une bande en caoutchouc, un tissu ou du cuir durable, du ruban perforé pour emballer de lourdes charges, etc. Un bord du ruban de fixation est vissé au contreplaqué avec une vis, jeté sur le récepteur et fermement vissé de l'autre côté.
Le compresseur est fixé avec des boulons, de préférence avec des tubes, au bord d'une feuille de contreplaqué, cela facilitera la vidange d'huile à l'avenir. Lors du vissage, il est conseillé de lubrifier les filetages des boulons avec du mastic, afin qu'ils ne se dévissent pas par la suite à cause des vibrations. Nous vissons le relais de démarrage à côté avec des vis, en l'orientant correctement. Vient ensuite l'interrupteur d'éclairage : nous connectons un relais et un cordon d'alimentation à ses contacts.Il est conseillé de fixer le cordon lui-même avec une attache ou une boucle à une feuille de contreplaqué afin qu'il ne se détache pas de l'interrupteur.
Une fois la partie électrique terminée, nous procédons à l'installation du reste du système pneumatique. A l'entrée du compresseur, à l'aide d'un morceau de tube en caoutchouc et de 2 colliers, on fixe un filtre fin pour essence. Peut-être que cette pièce peut sembler inutile à quelqu'un, mais elle n'est pas chère et toutes sortes de poussières ne pénétreront pas à l'intérieur du compresseur, il ne sera alors pas possible de l'enlever. L'essentiel lors de toutes les opérations ultérieures est de ne pas remplir ce filtre d'huile, car cela lui ferait perdre ses propriétés. Ensuite, utilisez un morceau de tube en caoutchouc et 2 pinces pour connecter la sortie du compresseur à l'entrée du récepteur. Vous devez agir avec précaution afin de ne pas casser les tubes du couvercle. Nous tendons également un tube en caoutchouc avec 2 pinces sur la sortie du récepteur et fixons un filtre pour carburant diesel. Ce filtre peut être rempli de gel de silice, il remplira alors 2 fonctions : un piège à humidité et un adaptateur pour fixer les tubes en caoutchouc et en chlorure de vinyle. Vous pouvez bien sûr vous en passer, tirer le tube de chlorure de vinyle directement sur la sortie du récepteur, mais une telle connexion ne sera pas complètement étanche et durable, le tuyau se détachera du tube de cuivre lisse.
Le tube de chlorure de vinyle a généralement un diamètre plus petit que celui du filtre et du raccord de l'aérographe, ne s'étire pas très bien et est assez difficile à installer. Il existe une petite astuce pour cela : l'extrémité du tube est immergée dans le solvant 647 pendant plusieurs minutes. Il ne doit pas être profond, il ne doit pas dépasser 5 mm, sinon il sera trop souple et il n'y aura pas de support pour le fixer sur le raccord. Il est conseillé de fixer le filtre et le tube de chlorure de vinyle sur une feuille de contreplaqué, afin qu'ils ne pendent pas et ne desserrent pas les tubes récepteurs.
Eh bien, c'est pratiquement tout.Vous pouvez l'allumer et écouter le sifflement de l'air. Ne vous précipitez pas au travail tout de suite si vous avez utilisé du mastic silicone : il doit sécher pendant quelques jours.
Chapitre trois : Fonctionnement.
Il n'y a rien de compliqué ici. L’essentiel lors du fonctionnement d’un compresseur est d’éviter qu’il ne surchauffe. Généralement, le compresseur chauffe jusqu'à une température de 40 à 45 °C en 25 à 30 minutes de fonctionnement continu. Cela ne vaut pas la peine de travailler plus longtemps, cela pourrait avoir un impact négatif sur ses ressources et la qualité du travail.
Au cours d'une opération ultérieure, vous devrez peut-être ajuster la pression de l'air. Par exemple, certains types de compresseurs peuvent produire une quantité d’air beaucoup plus importante que celle nécessaire à un aérographe, ou cela est dû à des problèmes de peinture. Dans ce cas, le compresseur créera une pression excessivement élevée dans les tubes, les filtres et le récepteur, et lui-même fonctionnera en surcharge et chauffera rapidement. Dans ce cas, nous avons besoin d'une boîte de vitesses. Le plus important est que la boîte de vitesses de ce système doit être installée à l'ENTRÉE du compresseur ; si elle est installée à la sortie, cela provoquera également une surcharge du compresseur et son échauffement rapide.
En installant un réducteur à l'entrée, on limite la quantité d'air traversant le compresseur, régulant ainsi la pression. Le réducteur le plus simple et le plus accessible est constitué de tubes calibrés, qui peuvent être fixés à l'entrée du filtre via un tube en caoutchouc, provenant par exemple de recharges de stylo, ou d'aiguilles épaisses de seringues. Vous pouvez le percer vous-même avec différentes perceuses. Vous pouvez également vous rendre dans l'animalerie la plus proche ; dans les produits pour aquariums, vous trouverez de petits robinets et réducteurs très adaptés. Et selon les diamètres de montage, ce ne sont que cela, et ils coûtent quelques centimes. Contrairement aux tubes calibrés, ils vous permettront de réguler la pression dans certaines limites au fur et à mesure de votre travail.
Chapitre quatre : Entretien.
L'entretien du compresseur n'est pas difficile, même si pour ce faire, vous devrez retirer partiellement certaines pièces. Bien sûr, vous ne pouvez pas du tout entretenir l'unité, mais croyez-moi, elle répondra en nature.
La prestation comprend :
Changement d'huile.
Remplacement des filtres.
Videz l’huile accumulée du récepteur.
Le pétrole, aussi bon soit-il, perd ses propriétés avec le temps et est contaminé. Dans un compresseur, quels que soient le mode et la durée de fonctionnement, il est conseillé de changer l'huile au moins une fois par an.
Pour ce faire, vous devez en retirer tous les tubes, dévisser le bouchon - vis - du tube de remplissage, incliner le compresseur, en vider toute l'huile. N'oubliez pas qu'après cela, vous ne pourrez en aucun cas l'allumer ! Ensuite, comme lors de la première vidange, utilisez une seringue pour verser la quantité d'huile requise à l'intérieur. Pendant que les tubes sont retirés, vous pouvez en même temps retirer les anciens filtres et vider l'huile accumulée du récepteur. Cela ne sert à rien de remettre cette huile dans le compresseur.
Installez ensuite tous les nouveaux filtres en place et remettez les tubes au compresseur. Les pinces métalliques y contribuent, elles vous permettent d'effectuer des opérations similaires à plusieurs reprises.
Eh bien, cela semble être tout, bonne chance. Je pense que toutes les questions supplémentaires qui ont surgi peuvent être résolues sur le forum.
Classes de maître similaires
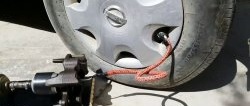
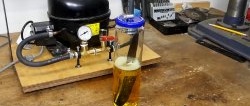
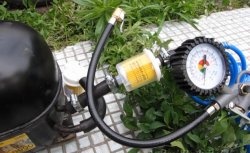
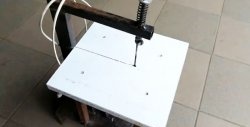
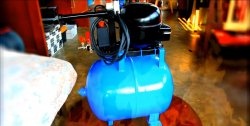
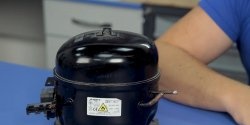