Najprostsza szlifierka bez spawania i toczenia z silnika pralki
Możesz wykonać to narzędzie samodzielnie, nawet jeśli nie masz tokarki ani sprzętu spawalniczego. W rezultacie będzie prosty w projektowaniu i produkcji, a także bez wysokich kosztów.
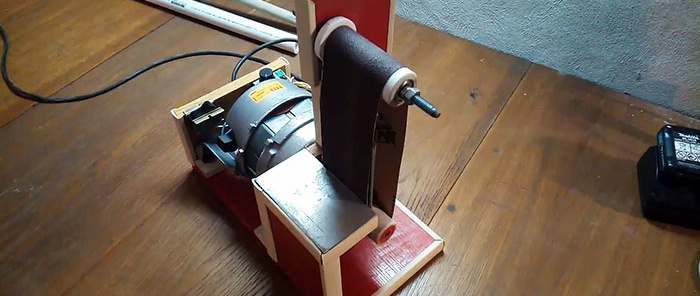
Główne części i podzespoły bierzemy ze starego sprzętu AGD, a niektóre pożyczamy od znajomych lub kupujemy niedrogo w sklepie. Oto ich rejestr:
Korpus wykonany jest z pięciu części wyciętych z płyty wiórowej i skręconych za pomocą wkrętów meblowych. Jego wymiary określa konkretny silnik i nie będziemy ich podawać.
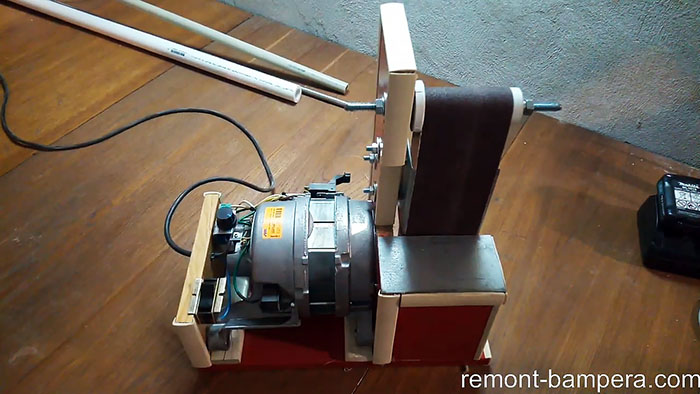
Agregat tworzymy w oparciu o silnik komutatorowy z pralki automatycznej o prędkości obrotowej 14 tys. obr./min. / min. Podłączamy go do sieci poprzez regulator napięcia w celu sterowania obrotami.
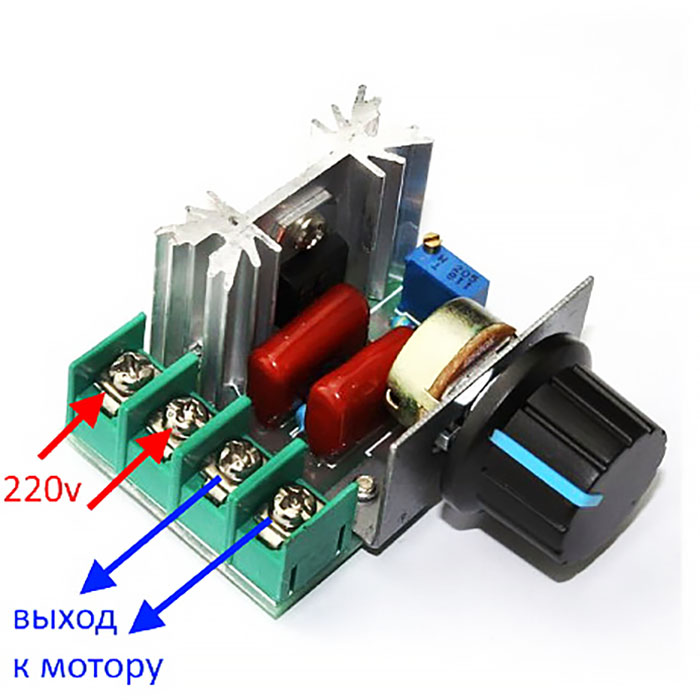
Mocujemy go za pomocą dwóch śrub na blokach.Posiada wejście 220 V i dwa wyjścia na silnik, który posiada zaciski do podłączenia wielu przewodów: do stojana, szczotek twornika, czujnika Halla, tachogeneratora itp.
Do prawidłowego podłączenia znajdziemy po dwa przewody od szczotek stojana i wirnika. Łączymy ze sobą jeden przewód ze szczotek stojana i twornika. Drugą parę przewodów podłączamy do regulatora napięcia. Instalujemy przełącznik przed regulatorem. To kończy podłączenie elektryczne.
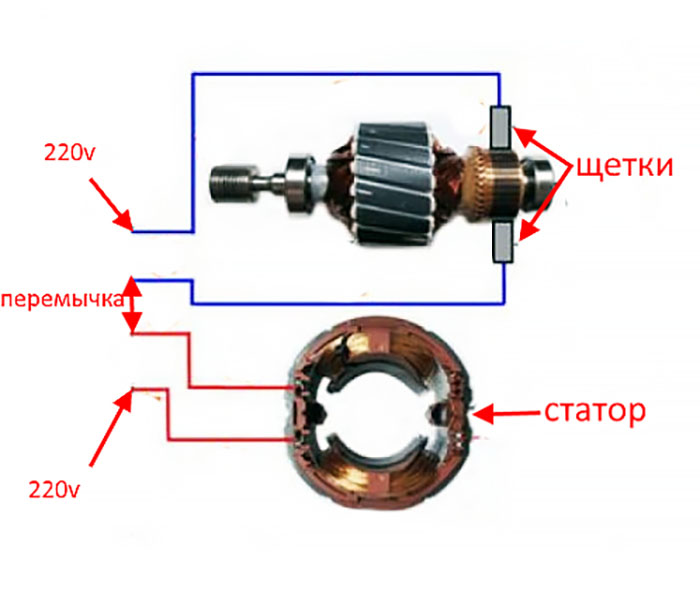
Podpórka pod taśmę szlifierską wykonana jest z kątownika montażowego, którego krawędzie są zaokrąglone, aby zapobiec zaczepianiu się blokady taśmy.
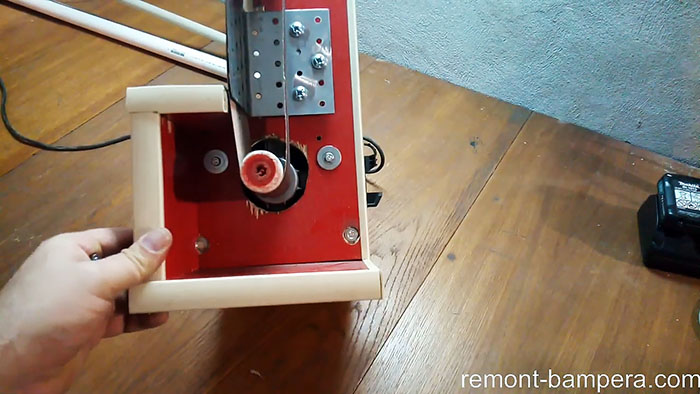
Z blachy wycinamy prostokątną powierzchnię podpórki narzędziowej i przyklejamy ją do płyty wiórowej. Średnica otworów montażowych jest nieco większa niż potrzeba dla śrub. Jest to konieczne, aby wyregulować kąt między ogranicznikiem a resztą.
Rolka napędowa wykonana jest z dwóch rurek polipropylenowych o średnicach 20 i 32 mm.
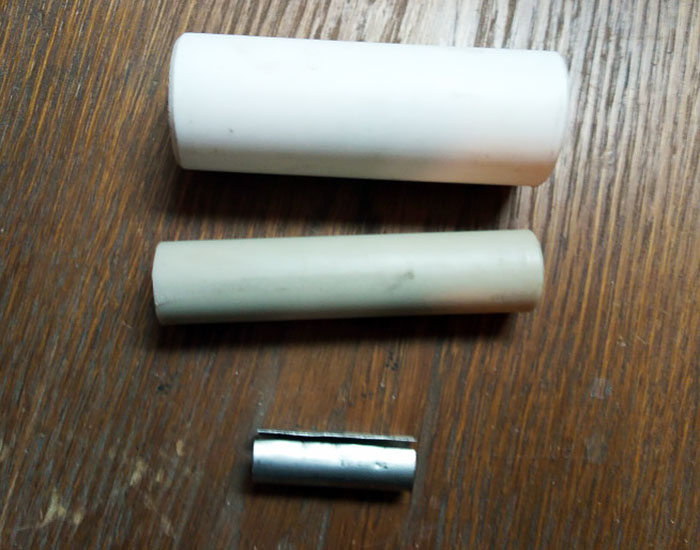
Wybieramy dużą rurę o średnicy wewnętrznej również równej 20 mm. Istnieją dwa sposoby łączenia rur: klejenie lub stapianie.
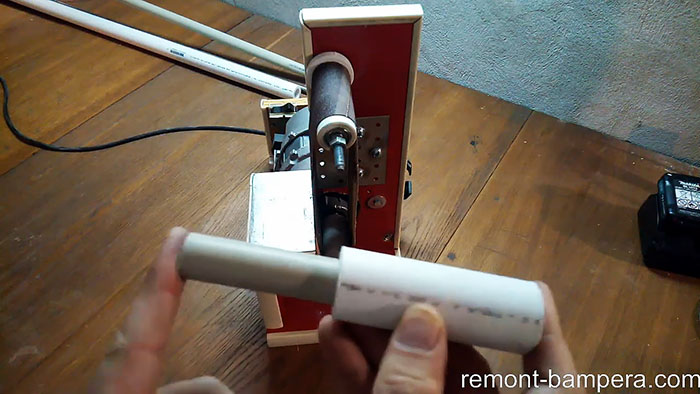
Użyjmy drugiej metody. W tym celu wystarczy docisnąć drewniany klocek do jego końca, jednocześnie obracając wałek.
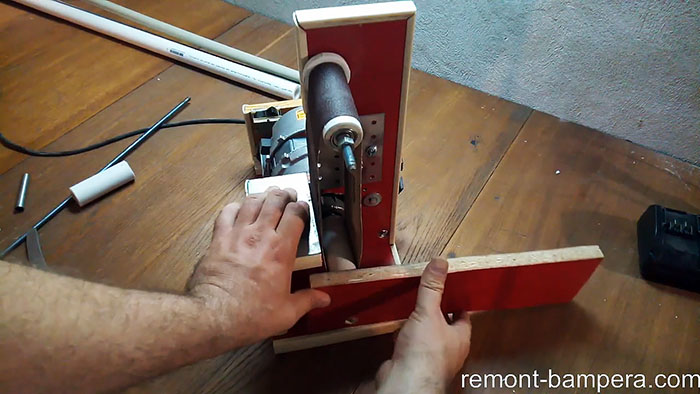
W wyniku wytworzonego ciepła rury są szczelnie stopione.
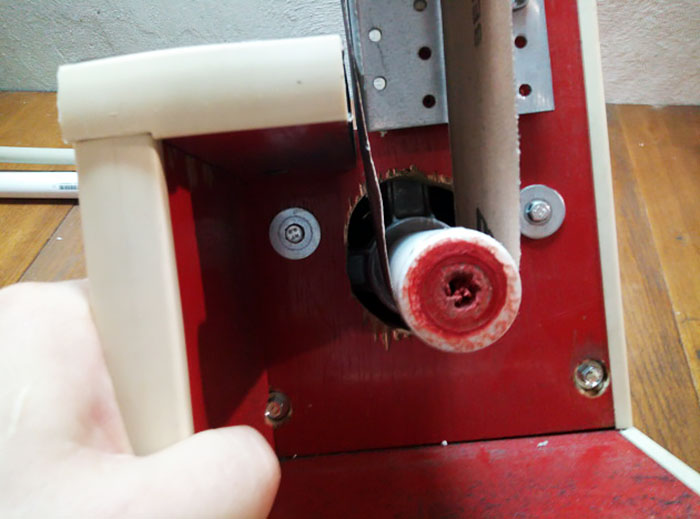
Dodatkowo w wewnętrzny otwór rury podwójnej wkładamy rurkę wygiętą z cyny.
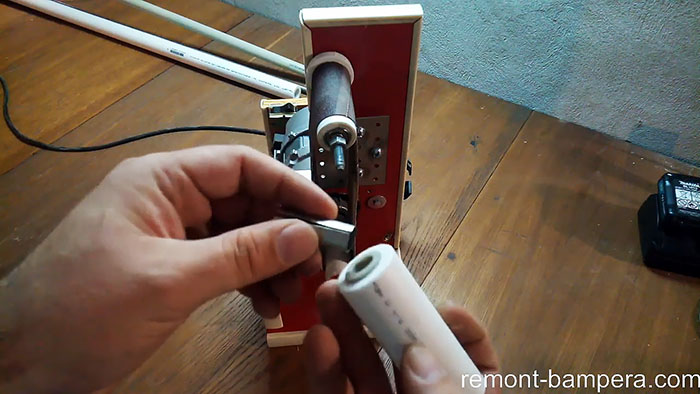
Całą tę konstrukcję napychamy na wielowypustowy wał silnika. Połączenie okazało się niezawodne przy minimalnym bicie.
Do wałka napędzanego dobieramy dwa łożyska oraz w zależności od średnicy zewnętrznej rurkę polipropylenową o dokładnie takim samym rozmiarze wewnętrznym.
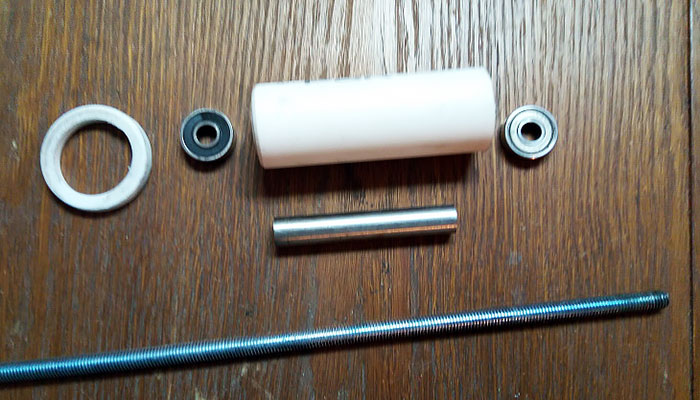
Jeśli okaże się mniejszy, można go wywiercić wiertłem z wiertłem piórowym o wymaganej średnicy.
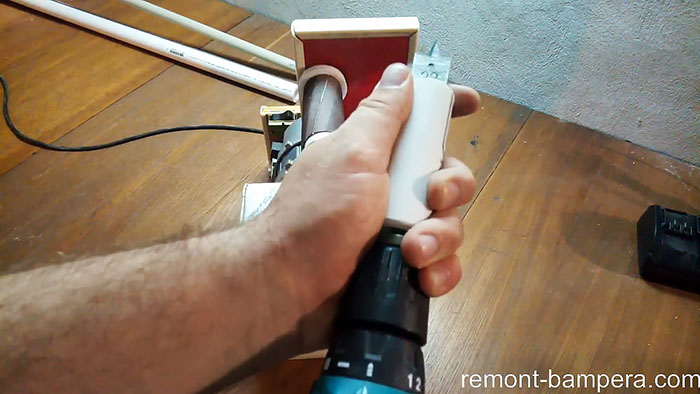
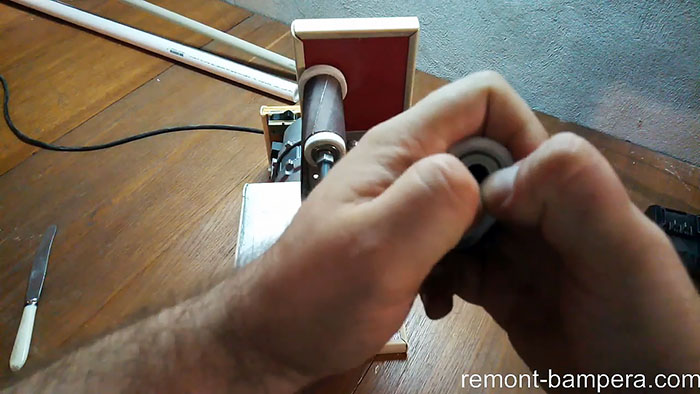
Rozszerzamy łożyska za pomocą stalowej rury, aby odciążyć obciążenie boczne.Na wewnętrznym końcu rolki umieszczamy pierścień wycięty ze złącza tej samej wielkości, który będzie służył jako ogranicznik.
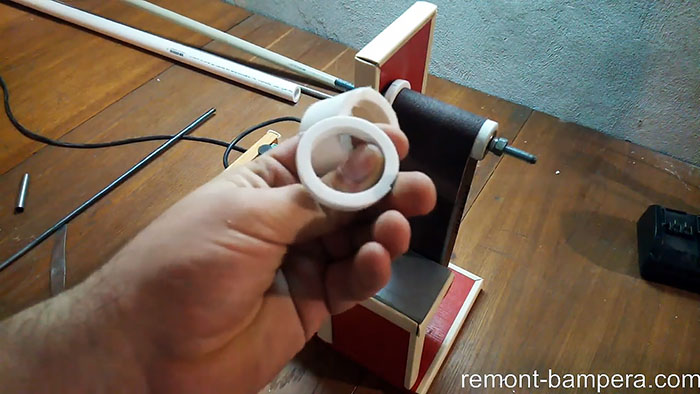
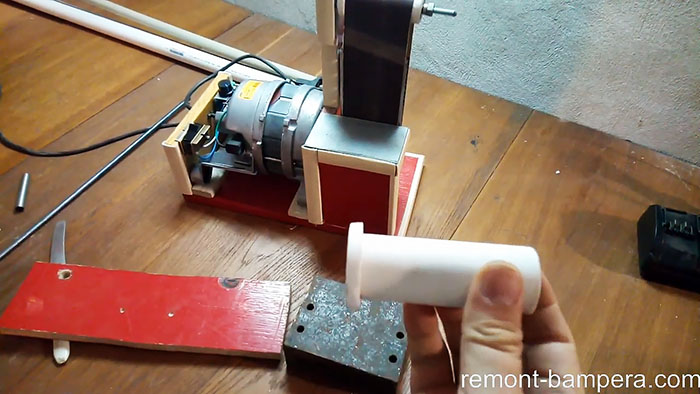
Powstały zespół montujemy na spince do włosów i przykręcamy go do podstawy za pomocą podkładek i nakrętek.
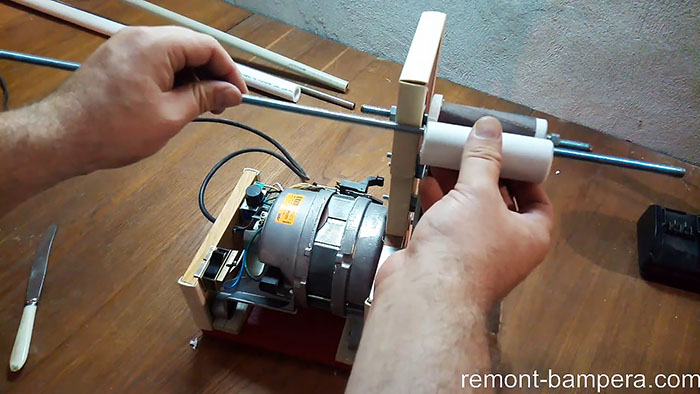
Wykonujemy średnice otworów w korpusie większe niż to, co jest potrzebne do kołka. Rozwiązanie to pozwoli na regulację i naprężenie taśmy szlifierskiej.
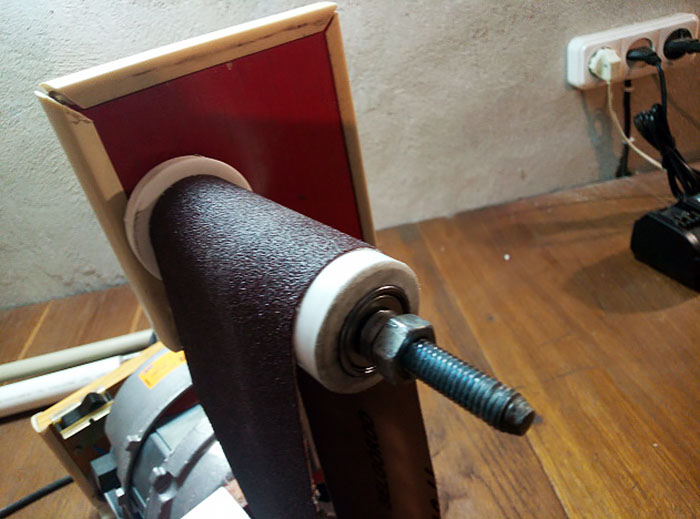
Po zakończeniu montażu całej konstrukcji przystępujemy do napinania taśmy. Podczas obracania może poruszać się wzdłuż rolek w lewo lub w prawo. Aby wyeliminować to zjawisko, obracamy wałek napędzany wokół własnej osi za pomocą obu nakrętek, aż taśma przestanie przesuwać się do jednej lub drugiej krawędzi. W ten sposób znajdziemy pozycję, w której wszystkie elementy oddziałujące na siebie będą na swoim miejscu.
Teraz możemy bezpiecznie włączyć nasz domowy produkt i obrobić metalowy przedmiot. Dbamy o to, aby obróbka przebiegała normalnie, bez szarpnięć i uderzeń, i jesteśmy całkiem zadowoleni z wyniku.
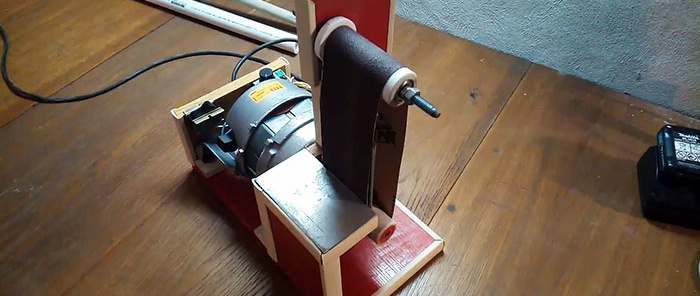
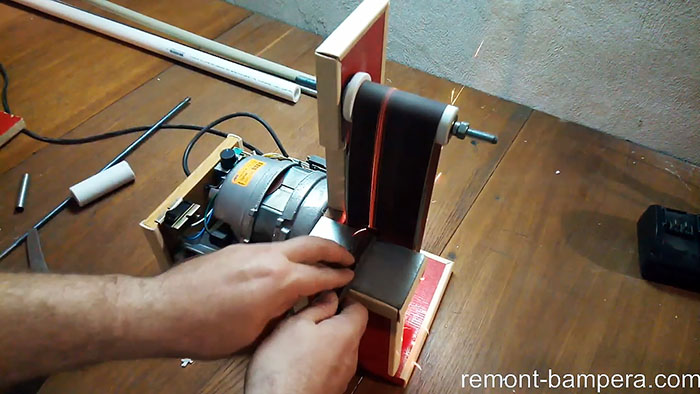
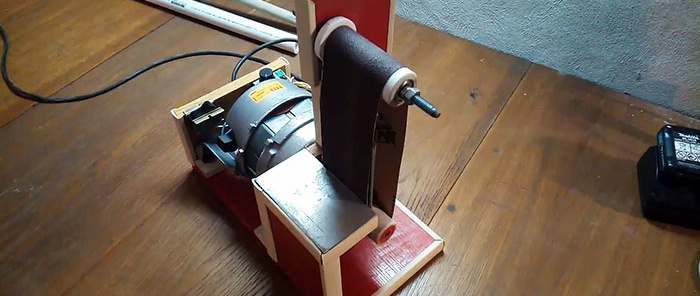
Będzie potrzebował
Główne części i podzespoły bierzemy ze starego sprzętu AGD, a niektóre pożyczamy od znajomych lub kupujemy niedrogo w sklepie. Oto ich rejestr:
- silnik pralki;
- dwa łożyska z odkurzacza;
- fragment arkusza płyty wiórowej;
- Regulator napięcia;
- przełącznik;
- spinka do włosów o długości 150 mm;
- montaż kątownika stalowego;
- dwa fragmenty rur polipropylenowych o średnicach 20 i 32 mm;
- śruby, nakrętki, podkładki i przewody.
Proces wytwarzania części i montażu szlifierki
Korpus wykonany jest z pięciu części wyciętych z płyty wiórowej i skręconych za pomocą wkrętów meblowych. Jego wymiary określa konkretny silnik i nie będziemy ich podawać.
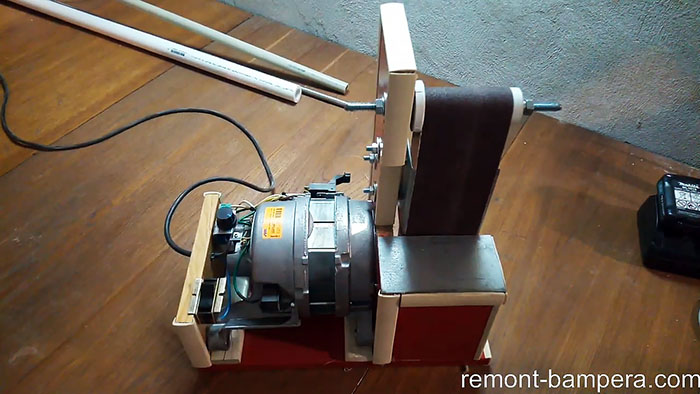
Agregat tworzymy w oparciu o silnik komutatorowy z pralki automatycznej o prędkości obrotowej 14 tys. obr./min. / min. Podłączamy go do sieci poprzez regulator napięcia w celu sterowania obrotami.
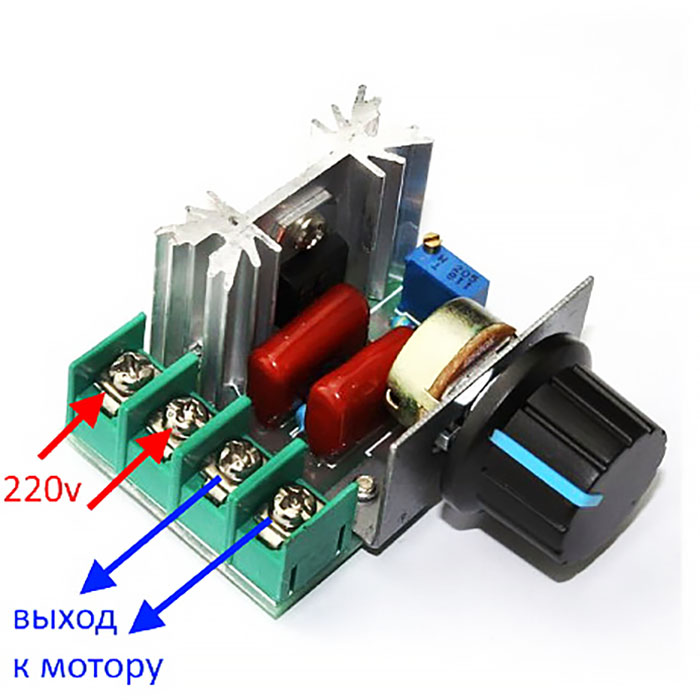
Mocujemy go za pomocą dwóch śrub na blokach.Posiada wejście 220 V i dwa wyjścia na silnik, który posiada zaciski do podłączenia wielu przewodów: do stojana, szczotek twornika, czujnika Halla, tachogeneratora itp.
Do prawidłowego podłączenia znajdziemy po dwa przewody od szczotek stojana i wirnika. Łączymy ze sobą jeden przewód ze szczotek stojana i twornika. Drugą parę przewodów podłączamy do regulatora napięcia. Instalujemy przełącznik przed regulatorem. To kończy podłączenie elektryczne.
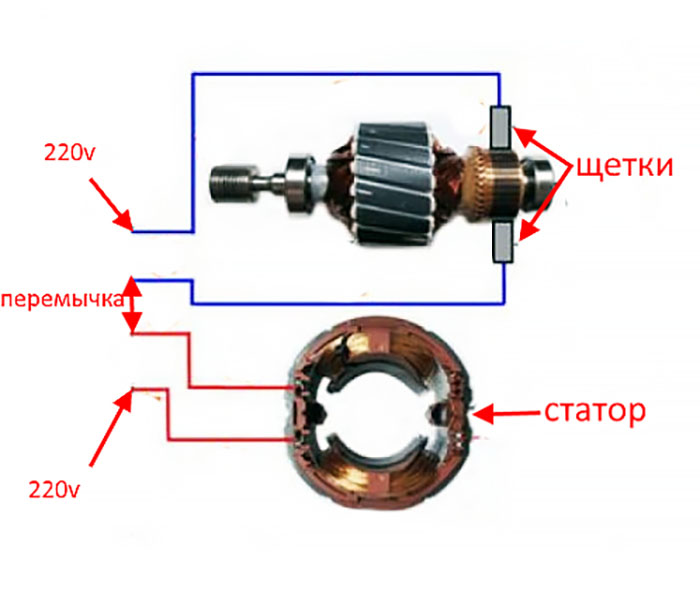
Podpórka pod taśmę szlifierską wykonana jest z kątownika montażowego, którego krawędzie są zaokrąglone, aby zapobiec zaczepianiu się blokady taśmy.
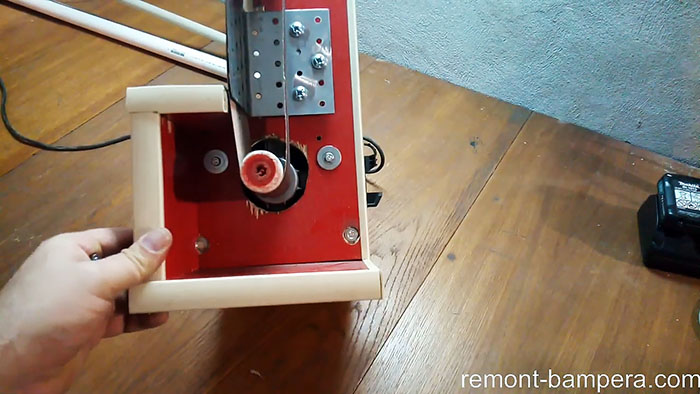
Z blachy wycinamy prostokątną powierzchnię podpórki narzędziowej i przyklejamy ją do płyty wiórowej. Średnica otworów montażowych jest nieco większa niż potrzeba dla śrub. Jest to konieczne, aby wyregulować kąt między ogranicznikiem a resztą.
Rolka napędowa wykonana jest z dwóch rurek polipropylenowych o średnicach 20 i 32 mm.
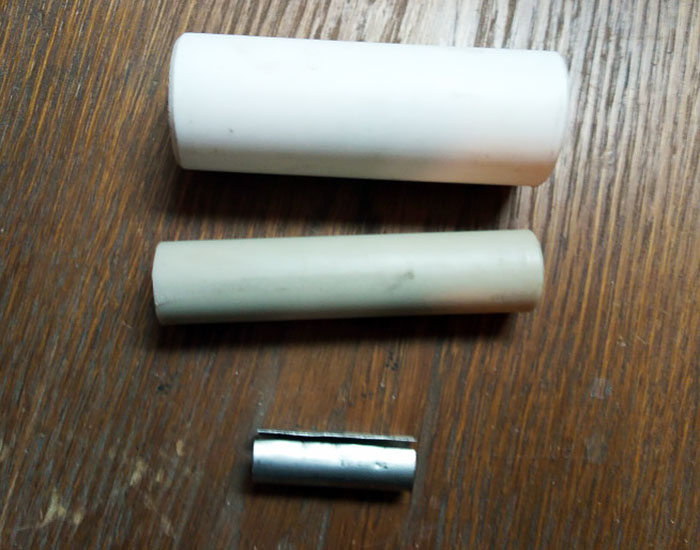
Wybieramy dużą rurę o średnicy wewnętrznej również równej 20 mm. Istnieją dwa sposoby łączenia rur: klejenie lub stapianie.
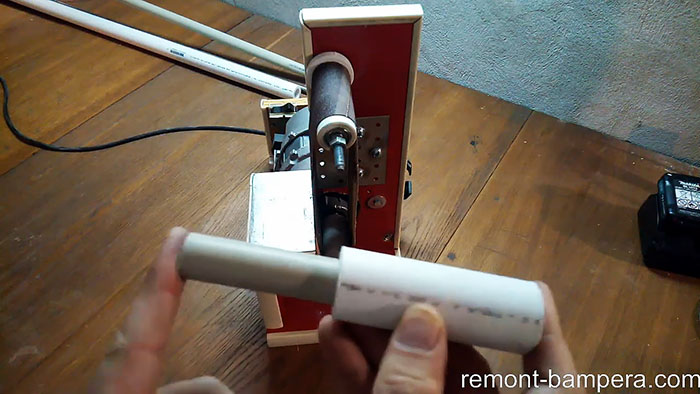
Użyjmy drugiej metody. W tym celu wystarczy docisnąć drewniany klocek do jego końca, jednocześnie obracając wałek.
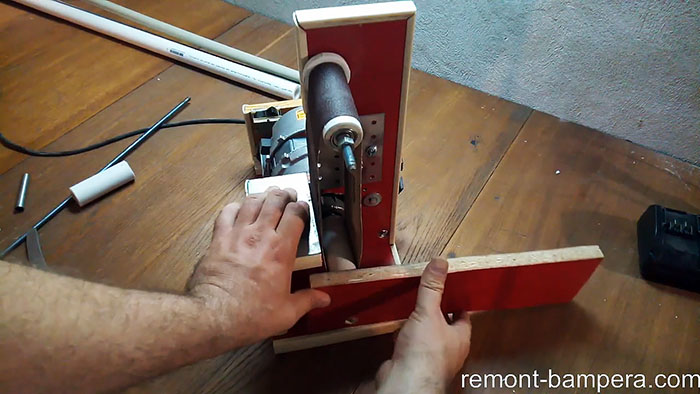
W wyniku wytworzonego ciepła rury są szczelnie stopione.
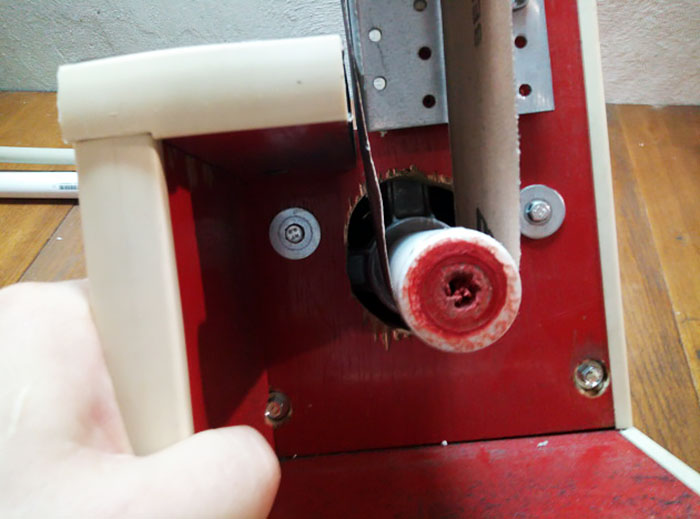
Dodatkowo w wewnętrzny otwór rury podwójnej wkładamy rurkę wygiętą z cyny.
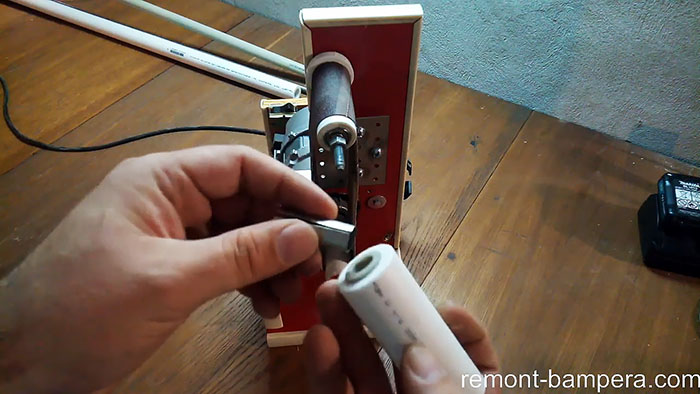
Całą tę konstrukcję napychamy na wielowypustowy wał silnika. Połączenie okazało się niezawodne przy minimalnym bicie.
Do wałka napędzanego dobieramy dwa łożyska oraz w zależności od średnicy zewnętrznej rurkę polipropylenową o dokładnie takim samym rozmiarze wewnętrznym.
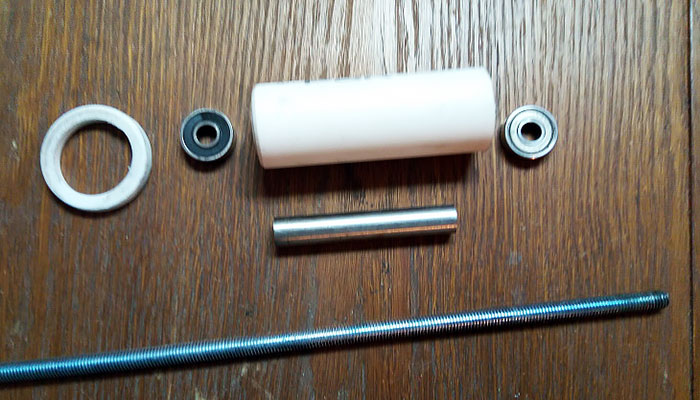
Jeśli okaże się mniejszy, można go wywiercić wiertłem z wiertłem piórowym o wymaganej średnicy.
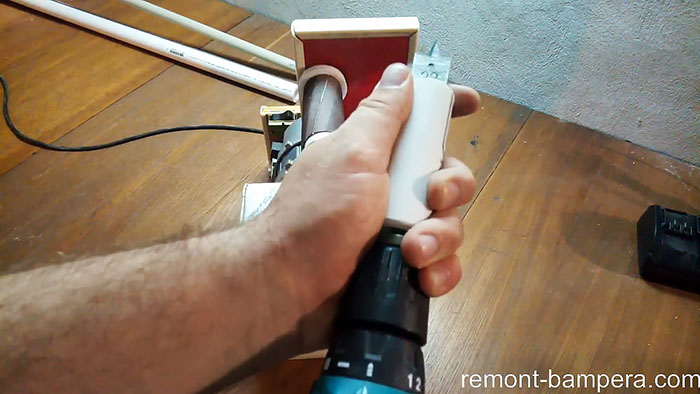
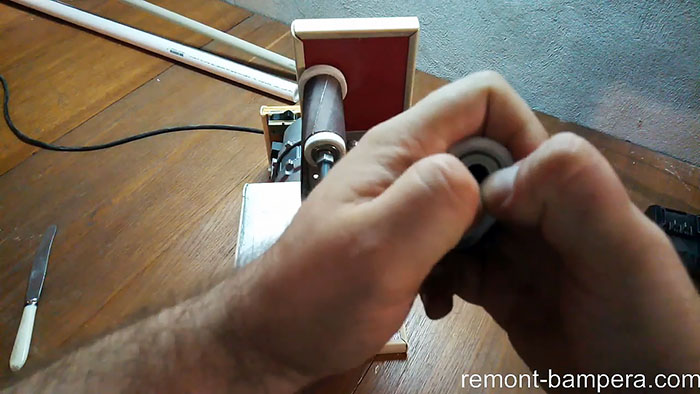
Rozszerzamy łożyska za pomocą stalowej rury, aby odciążyć obciążenie boczne.Na wewnętrznym końcu rolki umieszczamy pierścień wycięty ze złącza tej samej wielkości, który będzie służył jako ogranicznik.
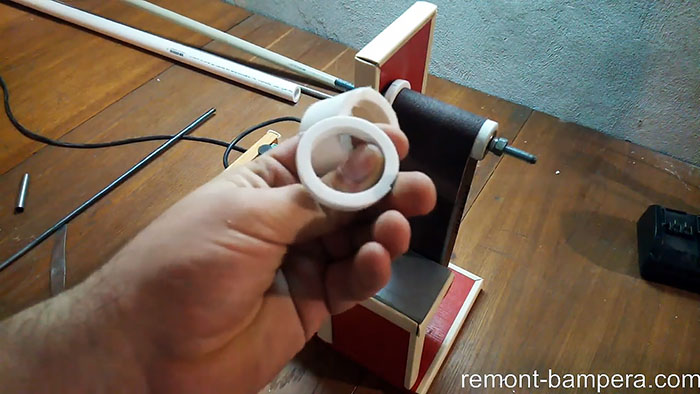
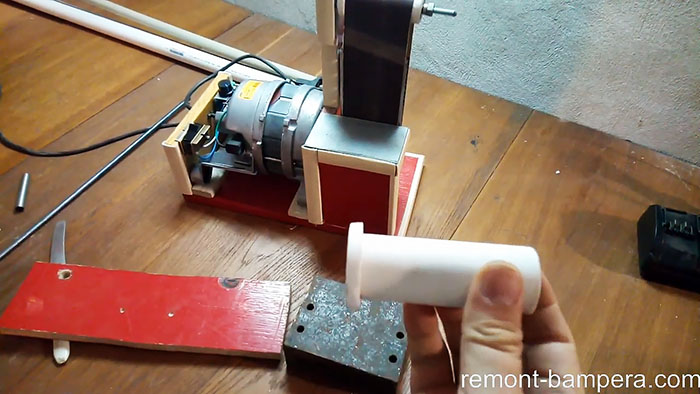
Powstały zespół montujemy na spince do włosów i przykręcamy go do podstawy za pomocą podkładek i nakrętek.
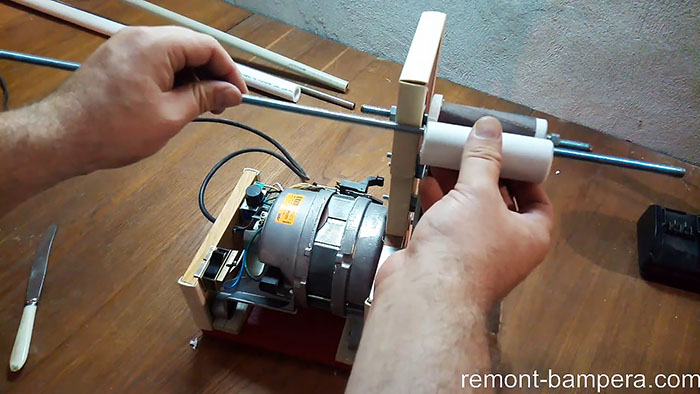
Wykonujemy średnice otworów w korpusie większe niż to, co jest potrzebne do kołka. Rozwiązanie to pozwoli na regulację i naprężenie taśmy szlifierskiej.
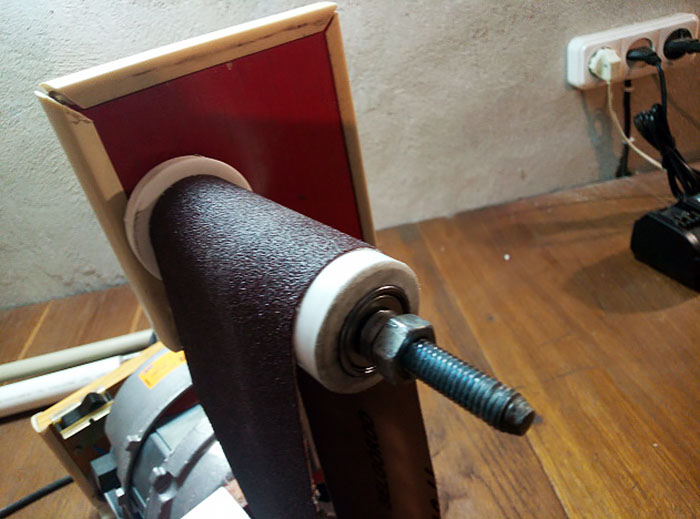
Ustawianie i sprawdzanie szlifierki w działaniu
Po zakończeniu montażu całej konstrukcji przystępujemy do napinania taśmy. Podczas obracania może poruszać się wzdłuż rolek w lewo lub w prawo. Aby wyeliminować to zjawisko, obracamy wałek napędzany wokół własnej osi za pomocą obu nakrętek, aż taśma przestanie przesuwać się do jednej lub drugiej krawędzi. W ten sposób znajdziemy pozycję, w której wszystkie elementy oddziałujące na siebie będą na swoim miejscu.
Teraz możemy bezpiecznie włączyć nasz domowy produkt i obrobić metalowy przedmiot. Dbamy o to, aby obróbka przebiegała normalnie, bez szarpnięć i uderzeń, i jesteśmy całkiem zadowoleni z wyniku.
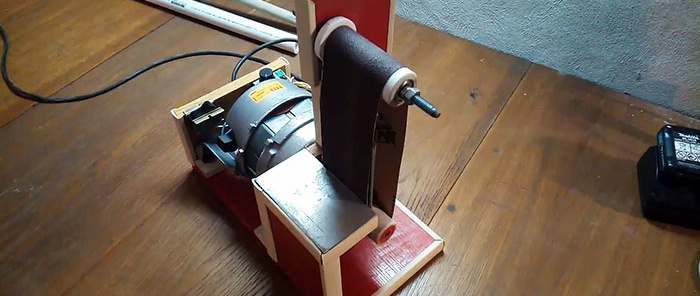
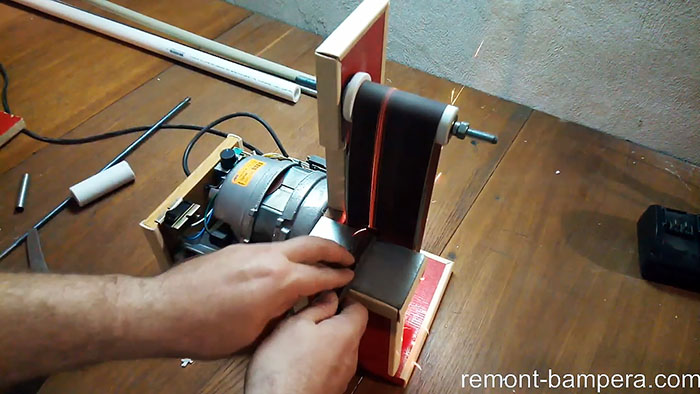
Obejrzyj wideo
Podobne klasy mistrzowskie
Szczególnie interesujące
Komentarze (3)