Soldagem por fricção
A maioria dos processos de soldagem modernos depende da entrada de calor externo, como uma descarga de arco. Mas o calor pode ser gerado diretamente na zona de soldagem devido ao atrito entre as peças conectadas.
A energia térmica pode ser obtida girando uma parte enquanto a segunda está estacionária ou girando na direção oposta. Além disso, as peças devem ser pressionadas simultaneamente umas contra as outras com uma força constante ou crescente do início ao fim. O processo termina com o deslocamento e a parada rápida da peça rotativa.
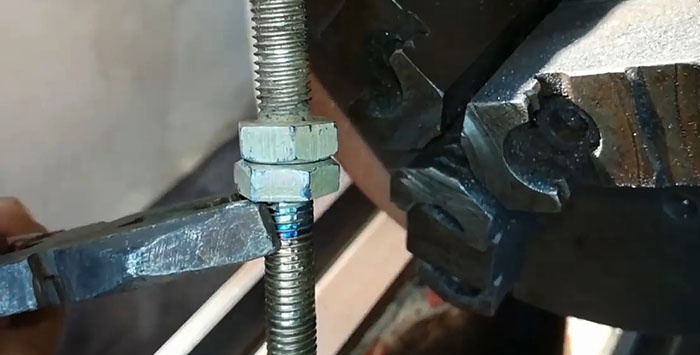
Em comparação, digamos, com a soldagem elétrica de topo, o processo baseado em fricção tem uma série de vantagens operacionais:
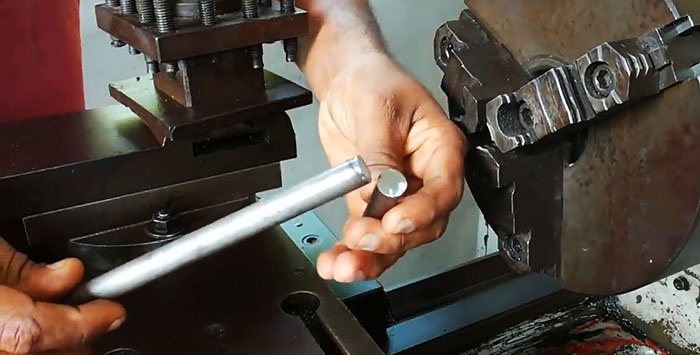
No mandril e cabeçote da máquina fixamos uma haste de metal, cujo diâmetro deve ser superior a 3,5 mm, mas inferior a 200 mm. Eles podem ser aço, alumínio, cobre, bronze ou metais diferentes:
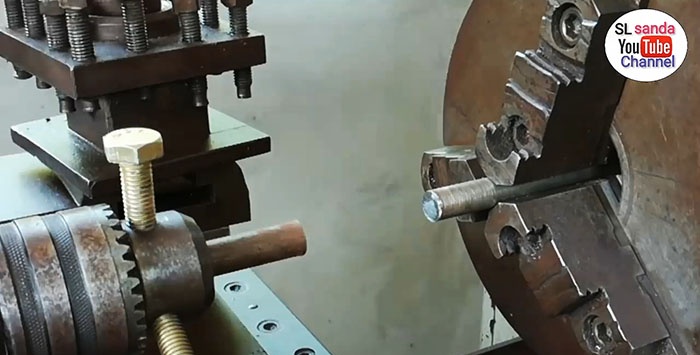
As combinações de materiais podem ser muito diferentes, mesmo aquelas que não podem ser soldadas da forma usual. Não há restrições a este respeito para soldagem por fricção.
No nosso caso, fixamos a haste no cabeçote por meio de três parafusos aparafusados nos orifícios do mandril, espaçados uniformemente em torno da circunferência em 120 graus. Com a ajuda deles, realizamos o alinhamento em relação à haste fixada no mandril, apertando ou afrouxando um ou outro parafuso.
Trazemos o cabeçote até que as hastes parem ponta a ponta e fixamos ou seguramos com a mão para aumentar a força de fixação durante o processo de soldagem, exigida pela tecnologia deste método de soldagem.
Ligamos a máquina e a haste fixada no mandril da máquina começa a girar. No nosso caso, a haste fixada no cabeçote fica imóvel, mas a princípio pode girar no sentido oposto, o que reduziria o tempo do processo.
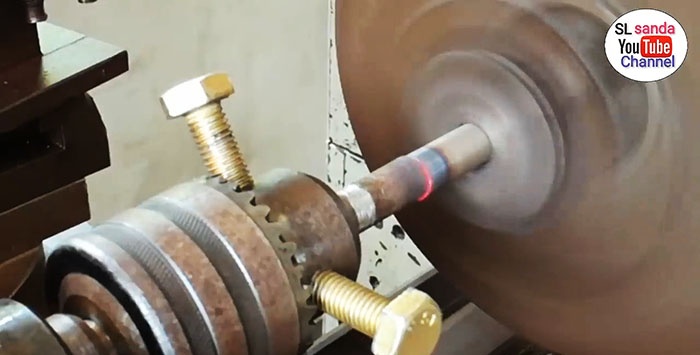
Em breve veremos cores manchadas começando no ponto de contato das hastes e espalhando-se ao longo delas em direções opostas, o que é um sinal direto do rápido aquecimento do metal como resultado do atrito.
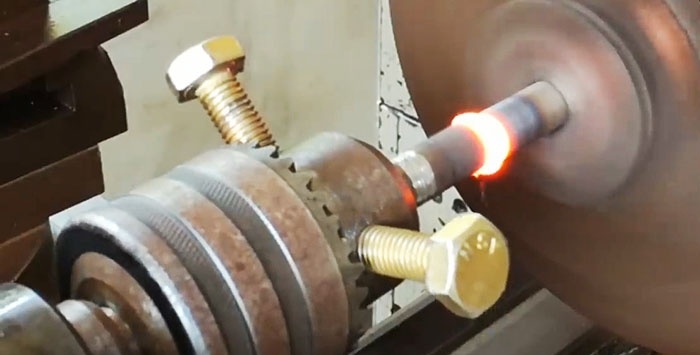
Após outro curto período de tempo, o metal na zona de contato brilhará intensamente e começará a ser espremido na forma de um anel além das dimensões das hastes.Este anel também conterá rebarbas: incrustações, graxa não queimada, inclusões sólidas não metálicas, etc.
No momento do brilho mais forte no ponto de contato, a máquina deve ser desligada bruscamente para que o metal das duas hastes endureça. Ao mesmo tempo, caso o cabeçote não esteja fixado, é necessário aumentar gradativamente a pressão sobre ele para compensar o volume de metal deslocado na zona de contato e obter uma conexão mais forte e de melhor qualidade.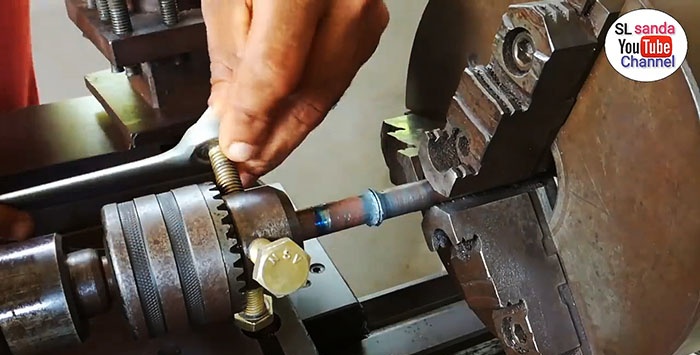
Depois de esperar até que o brilho pare (e isso é um sinal de que o metal está completamente endurecido), você pode afrouxar os parafusos de fixação e remover o cabeçote. Agora só falta verificar a qualidade da soldagem por fricção.
Para isso, ligue a máquina novamente e detecte um leve desvio da haste soldada - consequência do alinhamento impreciso durante a instalação no início. Este defeito pode ser eliminado girando e removendo a rebarba extrudada na área de contato.
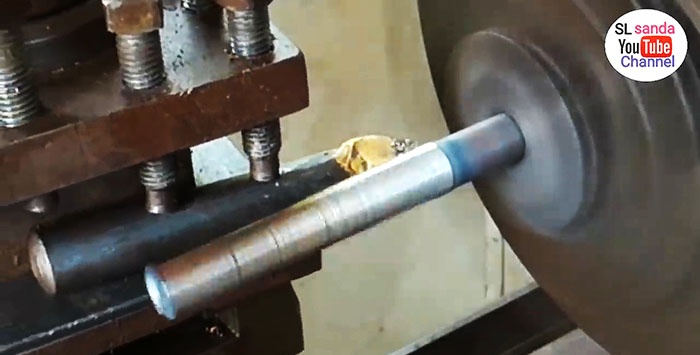
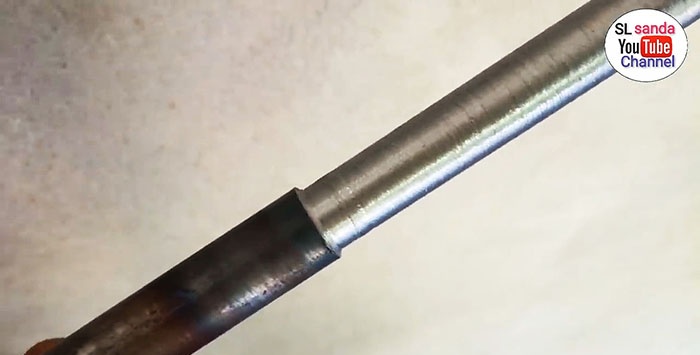
Uma penetração mais profunda do metal mostra que nenhuma característica é visível na área de soldagem das duas hastes. Parece que este não é o ponto de contato entre duas hastes, mas sim o corpo de uma delas.
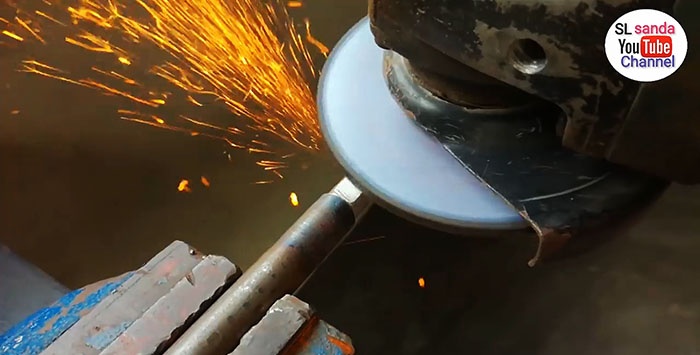
Realizamos o seguinte controle de qualidade da soldagem por fricção. Fixamos as hastes assim conectadas em um torno e usamos um disco triturador para criar uma “prateleira” na zona de contato, e novamente estamos convencidos da homogeneidade do metal, o que também indica a qualidade da soldagem.
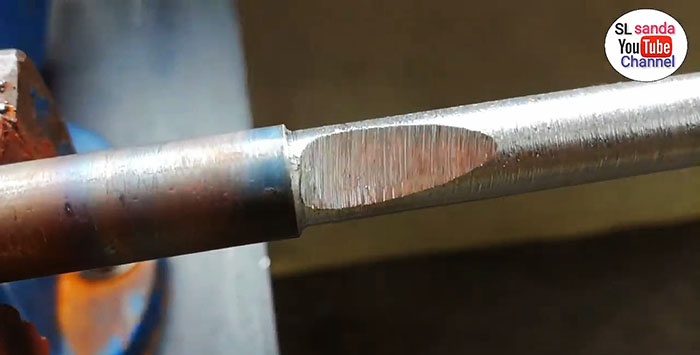
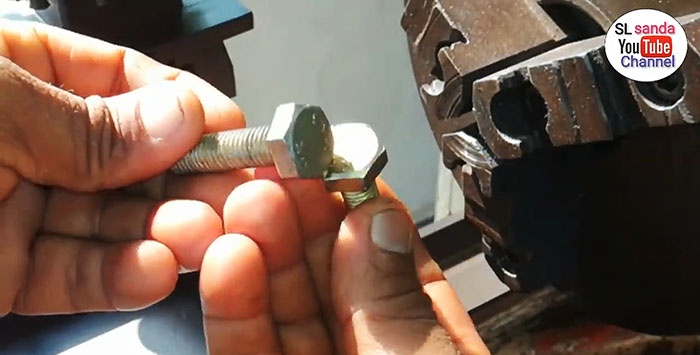
A soldagem por fricção pode ser usada para unir cabeças e parafusos produzidos em massa. O processo não é diferente do processo com hastes: um parafuso é preso no mandril da máquina e o outro no cabeçote.
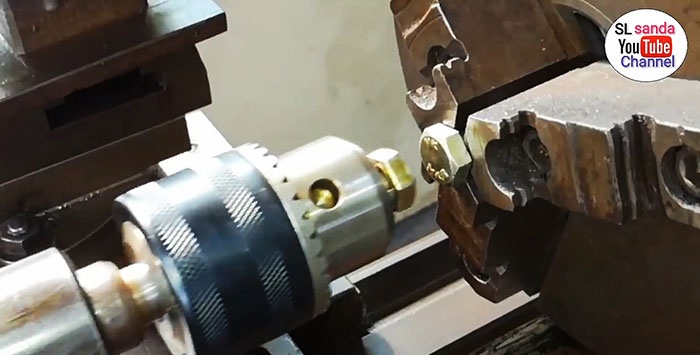
Com a ajuda deste último, os parafusos são colocados em contato com as cabeças e a máquina é acionada. Também é necessário aumentar a força de fixação e captar o momento da soldagem para desligar o acionamento a tempo.
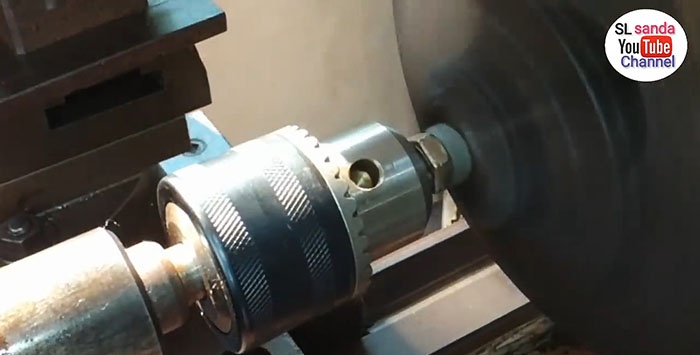
A soldagem por fricção pode ser utilizada para unir materiais difíceis ou impossíveis de soldar com outros tipos: aço e alumínio, aços austeníticos e perlíticos. Também pode ser usado para unir facilmente peças de plástico.
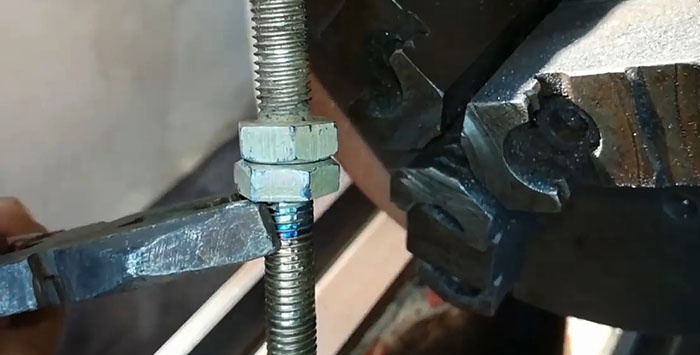
Cálculos e prática usando união por fricção demonstram que este método é mais adequado para peças cujo diâmetro está na faixa de 6 a 100 mm. Varetas de soldagem com diâmetro superior a 200 mm não são economicamente rentáveis, pois o processo exigirá mais potência (0,5 mil kW) e força axial (3 × 106 N). Não será possível conectar hastes com diâmetro inferior a 3,5 mm por este método devido à necessidade de fornecer altas velocidades (200 rpm) e à dificuldade de determinar quando desligar o acionamento.
A energia térmica pode ser obtida girando uma parte enquanto a segunda está estacionária ou girando na direção oposta. Além disso, as peças devem ser pressionadas simultaneamente umas contra as outras com uma força constante ou crescente do início ao fim. O processo termina com o deslocamento e a parada rápida da peça rotativa.
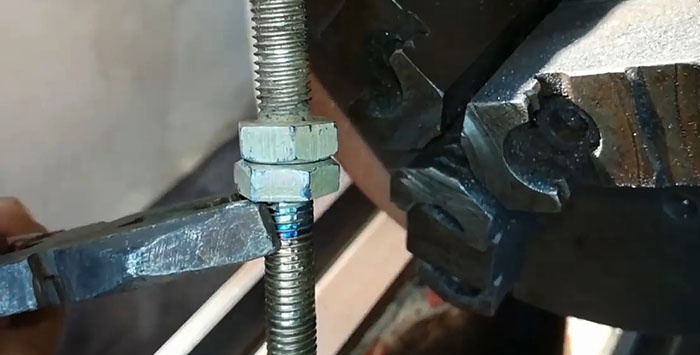
Em comparação, digamos, com a soldagem elétrica de topo, o processo baseado em fricção tem uma série de vantagens operacionais:
- os custos de energia são bastante reduzidos;
- a junta soldada é sempre confiável, pois depende apenas das características termofísicas dos produtos a serem soldados;
- nenhuma preparação especial é necessária para a conexão da junta, pois incrustações, ferrugem, graxa e graxa queimam ou são espremidas rapidamente no início do processo;
- a qualidade da conexão não é afetada mesmo pela violação do paralelismo das peças até ângulos de 6±1 graus;
- ausência de fatores negativos na forma de radiação ultravioleta e emissões de gases nocivos;
- simplicidade dos equipamentos tecnológicos, facilmente passíveis de manutenção de rotina, mecanização e automação.
Processo de soldagem por fricção em torno
Soldagem de hastes de aço
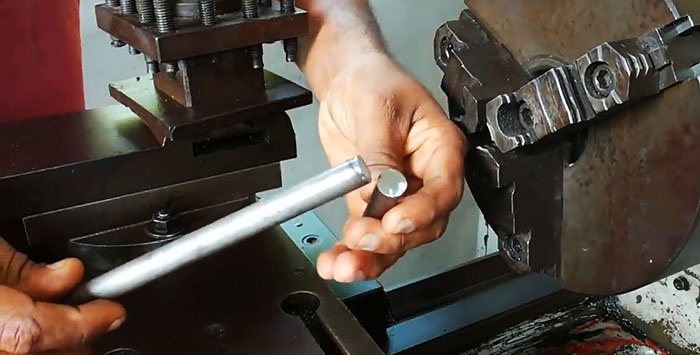
No mandril e cabeçote da máquina fixamos uma haste de metal, cujo diâmetro deve ser superior a 3,5 mm, mas inferior a 200 mm. Eles podem ser aço, alumínio, cobre, bronze ou metais diferentes:
- aço e alumínio;
- aço e cobre;
- alumínio e bronze, etc.
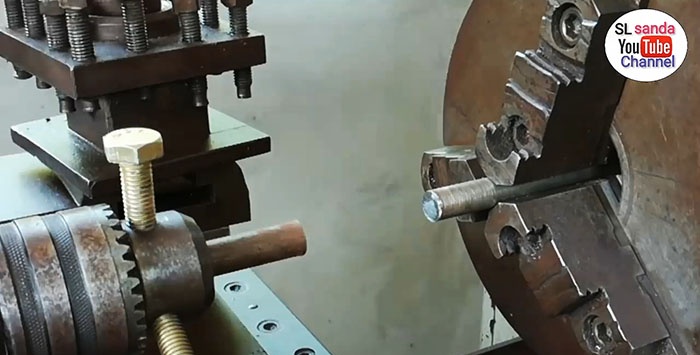
As combinações de materiais podem ser muito diferentes, mesmo aquelas que não podem ser soldadas da forma usual. Não há restrições a este respeito para soldagem por fricção.
No nosso caso, fixamos a haste no cabeçote por meio de três parafusos aparafusados nos orifícios do mandril, espaçados uniformemente em torno da circunferência em 120 graus. Com a ajuda deles, realizamos o alinhamento em relação à haste fixada no mandril, apertando ou afrouxando um ou outro parafuso.
Trazemos o cabeçote até que as hastes parem ponta a ponta e fixamos ou seguramos com a mão para aumentar a força de fixação durante o processo de soldagem, exigida pela tecnologia deste método de soldagem.
Ligamos a máquina e a haste fixada no mandril da máquina começa a girar. No nosso caso, a haste fixada no cabeçote fica imóvel, mas a princípio pode girar no sentido oposto, o que reduziria o tempo do processo.
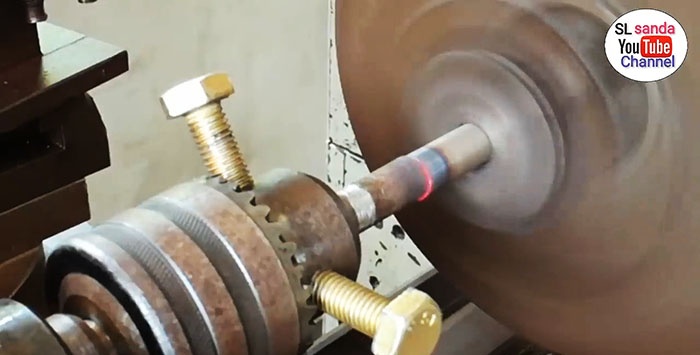
Em breve veremos cores manchadas começando no ponto de contato das hastes e espalhando-se ao longo delas em direções opostas, o que é um sinal direto do rápido aquecimento do metal como resultado do atrito.
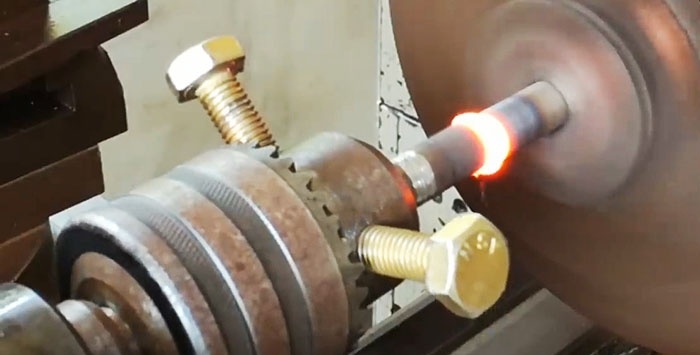
Após outro curto período de tempo, o metal na zona de contato brilhará intensamente e começará a ser espremido na forma de um anel além das dimensões das hastes.Este anel também conterá rebarbas: incrustações, graxa não queimada, inclusões sólidas não metálicas, etc.
No momento do brilho mais forte no ponto de contato, a máquina deve ser desligada bruscamente para que o metal das duas hastes endureça. Ao mesmo tempo, caso o cabeçote não esteja fixado, é necessário aumentar gradativamente a pressão sobre ele para compensar o volume de metal deslocado na zona de contato e obter uma conexão mais forte e de melhor qualidade.
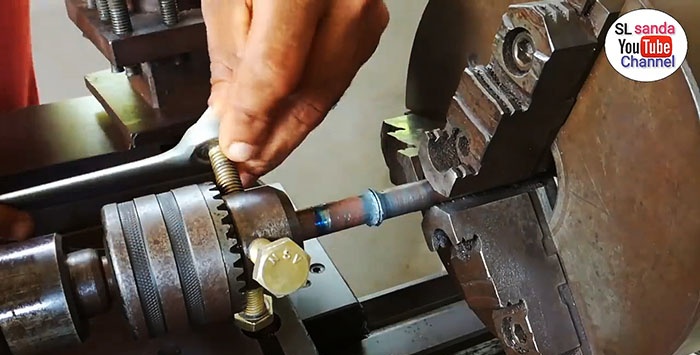
Depois de esperar até que o brilho pare (e isso é um sinal de que o metal está completamente endurecido), você pode afrouxar os parafusos de fixação e remover o cabeçote. Agora só falta verificar a qualidade da soldagem por fricção.
Para isso, ligue a máquina novamente e detecte um leve desvio da haste soldada - consequência do alinhamento impreciso durante a instalação no início. Este defeito pode ser eliminado girando e removendo a rebarba extrudada na área de contato.
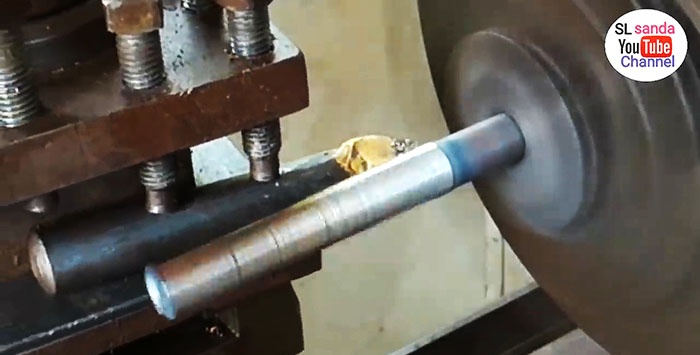
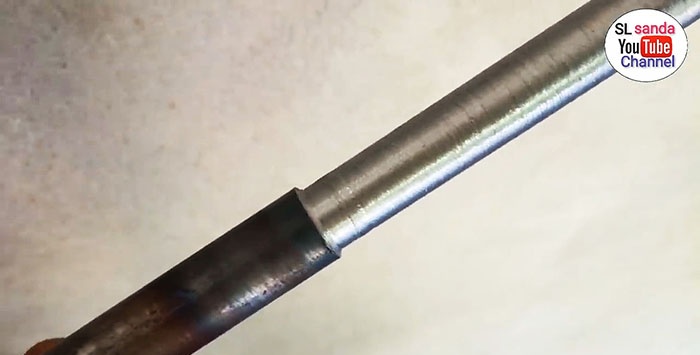
Uma penetração mais profunda do metal mostra que nenhuma característica é visível na área de soldagem das duas hastes. Parece que este não é o ponto de contato entre duas hastes, mas sim o corpo de uma delas.
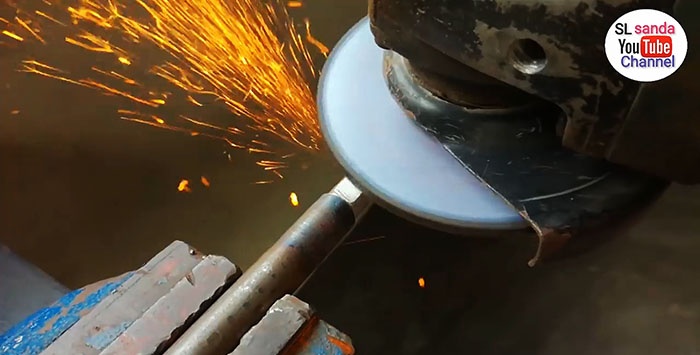
Realizamos o seguinte controle de qualidade da soldagem por fricção. Fixamos as hastes assim conectadas em um torno e usamos um disco triturador para criar uma “prateleira” na zona de contato, e novamente estamos convencidos da homogeneidade do metal, o que também indica a qualidade da soldagem.
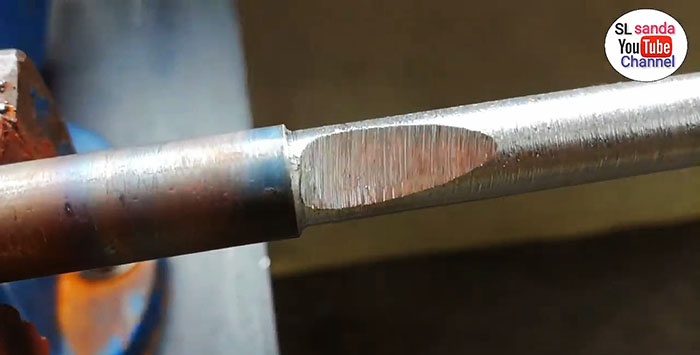
Conexão de parafuso
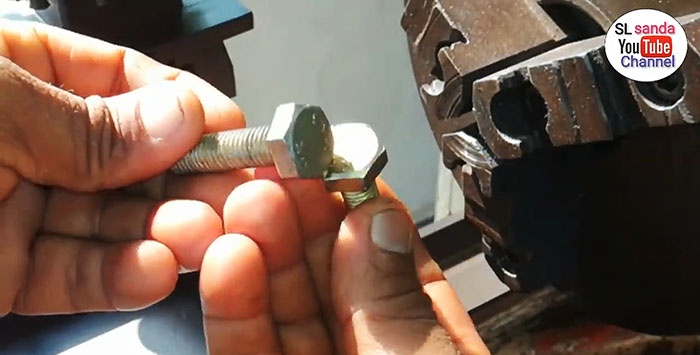
A soldagem por fricção pode ser usada para unir cabeças e parafusos produzidos em massa. O processo não é diferente do processo com hastes: um parafuso é preso no mandril da máquina e o outro no cabeçote.
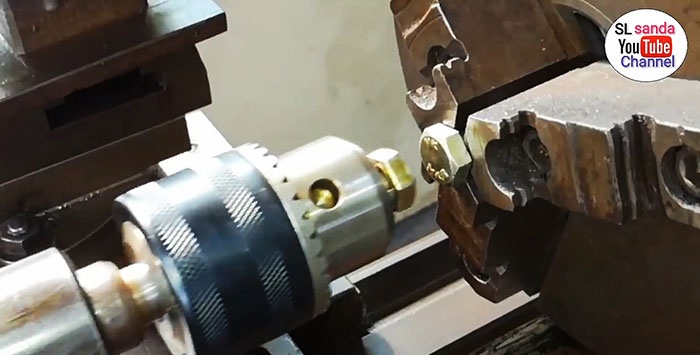
Com a ajuda deste último, os parafusos são colocados em contato com as cabeças e a máquina é acionada. Também é necessário aumentar a força de fixação e captar o momento da soldagem para desligar o acionamento a tempo.
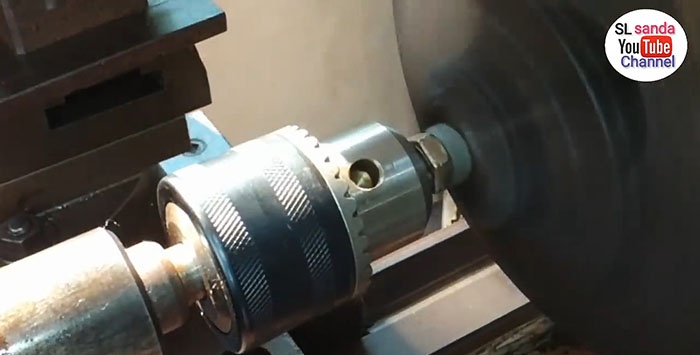
A soldagem por fricção pode ser utilizada para unir materiais difíceis ou impossíveis de soldar com outros tipos: aço e alumínio, aços austeníticos e perlíticos. Também pode ser usado para unir facilmente peças de plástico.
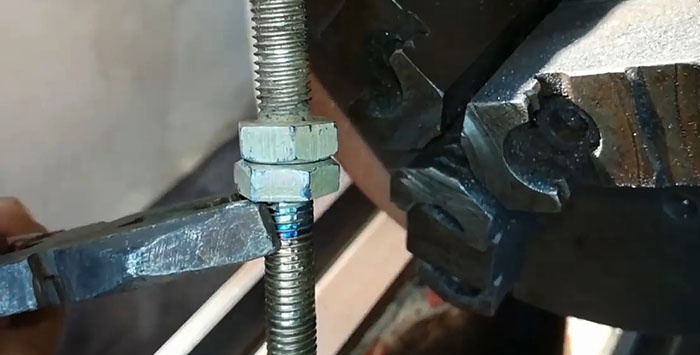
Cálculos e prática usando união por fricção demonstram que este método é mais adequado para peças cujo diâmetro está na faixa de 6 a 100 mm. Varetas de soldagem com diâmetro superior a 200 mm não são economicamente rentáveis, pois o processo exigirá mais potência (0,5 mil kW) e força axial (3 × 106 N). Não será possível conectar hastes com diâmetro inferior a 3,5 mm por este método devido à necessidade de fornecer altas velocidades (200 rpm) e à dificuldade de determinar quando desligar o acionamento.
Assista o vídeo
Master classes semelhantes
Particularmente interessante
Comentários (1)