Como fazer um afiador complexo para afiar facas simples
Como todas as ferramentas, as facas requerem cuidados adequados, principalmente um afiamento de alta qualidade, no qual é muito importante manter um ângulo de afiação constante ao longo de todo o comprimento da lâmina.
É claro que isso não é difícil para um apontador experiente, mesmo quando trabalha manualmente. Para todos os outros, será bastante difícil manter o ângulo de afiação necessário. O problema das facas cegas permanecerá insolúvel para eles?
Existem três maneiras de sair dessa situação: aprender a afiar facas, mas isso exigirá muito tempo, paciência e esforço; sempre peça ajuda a um profissional e pague por seu serviço caro; faça seu próprio afiador de facas e não se preocupe com o ângulo de afiação.
A seguir consideraremos um método de fabricação de um dispositivo para afiar facas baseado em um afiador elétrico com duas rodas abrasivas.
Para que o trabalho não exija muito esforço e tempo, é bom ter em estoque: máquina de solda, máquinas (furação, fresagem e torneamento), serra pendular, furadeira, retificadora, chaves, ferramentas de marcação, etc.
Além do já mencionado apontador elétrico, é necessário estocar materiais e componentes:
O trabalho consistirá em duas etapas relativamente independentes: montar um afiador elétrico e fabricar um porta-faca que forneça o ângulo de afiação necessário.
Uma das condições necessárias para um afiamento de facas de alta qualidade é a estabilidade da ferramenta de afiação. Portanto, como base para um apontador elétrico, utilizamos uma chapa metálica de tamanho e espessura adequados.
Usando uma fita métrica, um núcleo e um martelo, marcamos os centros de quatro furos, repetindo os furos na placa do apontador elétrico. Fazemos furos de acordo com as marcações de uma furadeira e, com parafusos e porcas, fixamos o apontador elétrico em uma base de metal.
Com uma serra de pêndulo, cortamos dois pedaços de tubos quadrados pré-calculados em comprimento, e um deve caber livremente, mas sem grande folga, no outro.
Em um tubo de seção transversal menor, fresamos um furo passante em uma das extremidades, cujo diâmetro deve ser ligeiramente maior que o diâmetro da haste de metal. No segundo tubo também marcamos e fazemos um furo em uma das extremidades para o parafuso de travamento.
Soldamos um tubo de seção transversal maior no centro à base, em frente ao apontador fixo, de forma que o parafuso de fixação fique voltado para fora e fique para cima.Para evitar que gotas de metal fundido, faíscas e incrustações provenientes da soldagem danifiquem o motor elétrico, cobrimos-o com uma manta de soldagem.
Inserimos a haste no furo perfurado no tubo de seção menor estritamente ao meio e soldamos nesta posição ao tubo, tendo previamente verificado a perpendicularidade dessas partes correspondentes com um triângulo retângulo.
Caso não tenha sido feito com antecedência, retire o apontador elétrico da base e inspecione a caixa elétrica, após o que reinstalamos o apontador no lugar e verificamos seu funcionamento.
Inserimos o tubo com a haste no tubo soldado à base e usando o parafuso você pode definir a altura necessária para afiar uma determinada faca. Esta foi a última etapa do arranjo do apontador elétrico. Vamos iniciar a segunda fase do trabalho.
Para um apontador elétrico, mude o sentido de rotação.
Como já foi observado, a qualidade do afiamento da faca depende, em primeiro lugar, da garantia de um ângulo de afiação constante. O suporte que vamos fazer foi pensado justamente para isso.
Marcamos a peça metálica de acordo com as dimensões pretendidas dos três elementos, o que garantirá a captura e fixação confiável da lâmina da faca em um determinado ângulo em relação à superfície do círculo durante o afiamento.
Cortamos com serra de pêndulo com adição de lubrificante para melhorar a qualidade do corte e a segurança da lâmina da serra.
Fixamos todos os três elementos em um “pacote” no torno de uma fresadora e processamos as superfícies no tamanho desejado e, a cada mudança de posição, removemos as rebarbas com uma lima manual.
Em dois espaços em branco formamos mandíbulas para agarrar e segurar a lâmina da faca. Para fazer isso, fresamos cada um deles em seu tamanho de um lado.A terceira peça de trabalho é fresada em ambos os lados no tamanho certo. Ele servirá de base para fixar alças laterais com mandíbulas.
Na parte que ficará no meio, na parte fresada fazemos marcações para dois furos, localizados simetricamente ao eixo longitudinal mais próximos das bordas e levemente deslocados em direção à base. Nós os perfuramos em uma furadeira.
Usando esta peça como amostra, marcamos pontos de resposta nas outras duas peças usando uma broca e uma broca fina.
Em seguida, perfuramos os locais marcados com uma broca de grande diâmetro até uma pequena profundidade (fazemos uma espécie de reentrâncias de ninho).
Aparafusamos nos furos do elemento central dois pinos do comprimento necessário e com a mesma saída, que, ao instalar os elementos laterais, vão caber nas reentrâncias e segurá-los, mas não interferem nas mandíbulas, convergem e divergem.
Nos elementos da mandíbula lateral, no centro geométrico, marcamos e fazemos furos do mesmo diâmetro e com um macho manual cortamos os fios.
Fresamos as bordas externas das mandíbulas para completar a aparência do dispositivo e facilidade de uso. Também removemos os chanfros de ambos os lados na extremidade fresada do elemento central para não interferir no ajuste das mandíbulas.
No centro da base do elemento central marcamos e fazemos um furo cego para o mandril.
Misture cola de dois componentes e use-a para fixar um mandril do comprimento necessário no furo cego. Deixe o composto endurecer e endurecer. Para isso, fixamos o elemento central com o mandril em um torno de madeira.
Fixamos uma haste de metal com o diâmetro calculado no mandril do torno e fazemos um furo no centro um pouco maior que o diâmetro do mandril, adicionando lubrificante periodicamente na área de perfuração.
Em seguida, cortamos o cilindro com uma altura de cerca de 10-12 mm e fazemos um furo na superfície lateral, seguido do corte da rosca com uma torneira para o parafuso de travamento.
Num dos elementos laterais, pelo exterior, fazemos um furo central para instalar a cabeça do parafuso embutida.
Finalizamos as superfícies do aparelho processando-o em uma esmerilhadeira, primeiro com uma cinta de lixa sem fim e depois com uma fita adesiva.
Resta montar os elementos do suporte ajustável aparafusando o parafuso de conexão nas mandíbulas e fixando o anel cilíndrico ao mandril, instalando-o no lugar certo por meio de um parafuso de travamento.
Prendemos a lâmina da faca nas mandíbulas do suporte e definimos a altura necessária da haste transversal e o comprimento do mandril movendo o anel cilíndrico para baixo ou para cima e travando-o quando necessário com um parafuso especial.
Para que o ângulo de afiação permaneça o mesmo ao longo de todo o comprimento da lâmina, basta garantir que um anel cilíndrico montado em um mandril deslize ao longo da superfície de uma haste instalada horizontalmente na frente das rodas do afiador elétrico.
Após um breve afiamento sem qualquer tensão, a faca corta facilmente uma folha de papel para escrever em peso, o que confirma seu excelente afiamento.
É claro que isso não é difícil para um apontador experiente, mesmo quando trabalha manualmente. Para todos os outros, será bastante difícil manter o ângulo de afiação necessário. O problema das facas cegas permanecerá insolúvel para eles?
Existem três maneiras de sair dessa situação: aprender a afiar facas, mas isso exigirá muito tempo, paciência e esforço; sempre peça ajuda a um profissional e pague por seu serviço caro; faça seu próprio afiador de facas e não se preocupe com o ângulo de afiação.
A seguir consideraremos um método de fabricação de um dispositivo para afiar facas baseado em um afiador elétrico com duas rodas abrasivas.
Vai precisar
Para que o trabalho não exija muito esforço e tempo, é bom ter em estoque: máquina de solda, máquinas (furação, fresagem e torneamento), serra pendular, furadeira, retificadora, chaves, ferramentas de marcação, etc.
Além do já mencionado apontador elétrico, é necessário estocar materiais e componentes:
- chapa metálica com 10 mm de espessura;
- tubos quadrados (duas peças de tamanhos adjacentes);
- uma haste redonda de metal com até 400 mm de comprimento e 15-20 mm de diâmetro;
- fixadores roscados (parafusos, porcas, arruelas), etc.
Fazendo um afiador de faca
O trabalho consistirá em duas etapas relativamente independentes: montar um afiador elétrico e fabricar um porta-faca que forneça o ângulo de afiação necessário.
Disposição do apontador
Uma das condições necessárias para um afiamento de facas de alta qualidade é a estabilidade da ferramenta de afiação. Portanto, como base para um apontador elétrico, utilizamos uma chapa metálica de tamanho e espessura adequados.
Usando uma fita métrica, um núcleo e um martelo, marcamos os centros de quatro furos, repetindo os furos na placa do apontador elétrico. Fazemos furos de acordo com as marcações de uma furadeira e, com parafusos e porcas, fixamos o apontador elétrico em uma base de metal.
Com uma serra de pêndulo, cortamos dois pedaços de tubos quadrados pré-calculados em comprimento, e um deve caber livremente, mas sem grande folga, no outro.
Em um tubo de seção transversal menor, fresamos um furo passante em uma das extremidades, cujo diâmetro deve ser ligeiramente maior que o diâmetro da haste de metal. No segundo tubo também marcamos e fazemos um furo em uma das extremidades para o parafuso de travamento.
Soldamos um tubo de seção transversal maior no centro à base, em frente ao apontador fixo, de forma que o parafuso de fixação fique voltado para fora e fique para cima.Para evitar que gotas de metal fundido, faíscas e incrustações provenientes da soldagem danifiquem o motor elétrico, cobrimos-o com uma manta de soldagem.
Inserimos a haste no furo perfurado no tubo de seção menor estritamente ao meio e soldamos nesta posição ao tubo, tendo previamente verificado a perpendicularidade dessas partes correspondentes com um triângulo retângulo.
Caso não tenha sido feito com antecedência, retire o apontador elétrico da base e inspecione a caixa elétrica, após o que reinstalamos o apontador no lugar e verificamos seu funcionamento.
Inserimos o tubo com a haste no tubo soldado à base e usando o parafuso você pode definir a altura necessária para afiar uma determinada faca. Esta foi a última etapa do arranjo do apontador elétrico. Vamos iniciar a segunda fase do trabalho.
Para um apontador elétrico, mude o sentido de rotação.
Fazendo um porta-faca
Como já foi observado, a qualidade do afiamento da faca depende, em primeiro lugar, da garantia de um ângulo de afiação constante. O suporte que vamos fazer foi pensado justamente para isso.
Marcamos a peça metálica de acordo com as dimensões pretendidas dos três elementos, o que garantirá a captura e fixação confiável da lâmina da faca em um determinado ângulo em relação à superfície do círculo durante o afiamento.
Cortamos com serra de pêndulo com adição de lubrificante para melhorar a qualidade do corte e a segurança da lâmina da serra.
Fixamos todos os três elementos em um “pacote” no torno de uma fresadora e processamos as superfícies no tamanho desejado e, a cada mudança de posição, removemos as rebarbas com uma lima manual.
Em dois espaços em branco formamos mandíbulas para agarrar e segurar a lâmina da faca. Para fazer isso, fresamos cada um deles em seu tamanho de um lado.A terceira peça de trabalho é fresada em ambos os lados no tamanho certo. Ele servirá de base para fixar alças laterais com mandíbulas.
Na parte que ficará no meio, na parte fresada fazemos marcações para dois furos, localizados simetricamente ao eixo longitudinal mais próximos das bordas e levemente deslocados em direção à base. Nós os perfuramos em uma furadeira.
Usando esta peça como amostra, marcamos pontos de resposta nas outras duas peças usando uma broca e uma broca fina.
Em seguida, perfuramos os locais marcados com uma broca de grande diâmetro até uma pequena profundidade (fazemos uma espécie de reentrâncias de ninho).
Aparafusamos nos furos do elemento central dois pinos do comprimento necessário e com a mesma saída, que, ao instalar os elementos laterais, vão caber nas reentrâncias e segurá-los, mas não interferem nas mandíbulas, convergem e divergem.
Nos elementos da mandíbula lateral, no centro geométrico, marcamos e fazemos furos do mesmo diâmetro e com um macho manual cortamos os fios.
Fresamos as bordas externas das mandíbulas para completar a aparência do dispositivo e facilidade de uso. Também removemos os chanfros de ambos os lados na extremidade fresada do elemento central para não interferir no ajuste das mandíbulas.
No centro da base do elemento central marcamos e fazemos um furo cego para o mandril.
Misture cola de dois componentes e use-a para fixar um mandril do comprimento necessário no furo cego. Deixe o composto endurecer e endurecer. Para isso, fixamos o elemento central com o mandril em um torno de madeira.
Fixamos uma haste de metal com o diâmetro calculado no mandril do torno e fazemos um furo no centro um pouco maior que o diâmetro do mandril, adicionando lubrificante periodicamente na área de perfuração.
Em seguida, cortamos o cilindro com uma altura de cerca de 10-12 mm e fazemos um furo na superfície lateral, seguido do corte da rosca com uma torneira para o parafuso de travamento.
Num dos elementos laterais, pelo exterior, fazemos um furo central para instalar a cabeça do parafuso embutida.
Finalizamos as superfícies do aparelho processando-o em uma esmerilhadeira, primeiro com uma cinta de lixa sem fim e depois com uma fita adesiva.
Resta montar os elementos do suporte ajustável aparafusando o parafuso de conexão nas mandíbulas e fixando o anel cilíndrico ao mandril, instalando-o no lugar certo por meio de um parafuso de travamento.
Teste de fixação
Prendemos a lâmina da faca nas mandíbulas do suporte e definimos a altura necessária da haste transversal e o comprimento do mandril movendo o anel cilíndrico para baixo ou para cima e travando-o quando necessário com um parafuso especial.
Para que o ângulo de afiação permaneça o mesmo ao longo de todo o comprimento da lâmina, basta garantir que um anel cilíndrico montado em um mandril deslize ao longo da superfície de uma haste instalada horizontalmente na frente das rodas do afiador elétrico.
Após um breve afiamento sem qualquer tensão, a faca corta facilmente uma folha de papel para escrever em peso, o que confirma seu excelente afiamento.
Assista o vídeo
Master classes semelhantes
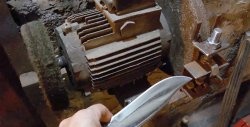
O dispositivo mais simples para afiar facas a 30 graus
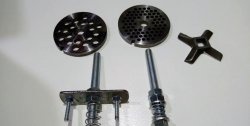
Dispositivo para afiar facas de moedor de carne
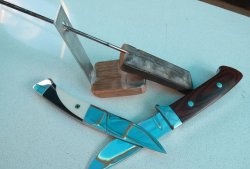
Uma ferramenta simples para afiar facas em um ângulo fixo

Como afiar facilmente facas de moedor de carne
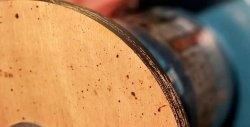
Usamos um disco de madeira para afiar facas rapidamente
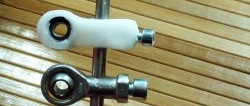
Como fazer rapidamente uma dobradiça para um amolador de facas
Particularmente interessante
Comentários (5)