Making a “marble” table from concrete with a burnt wood base
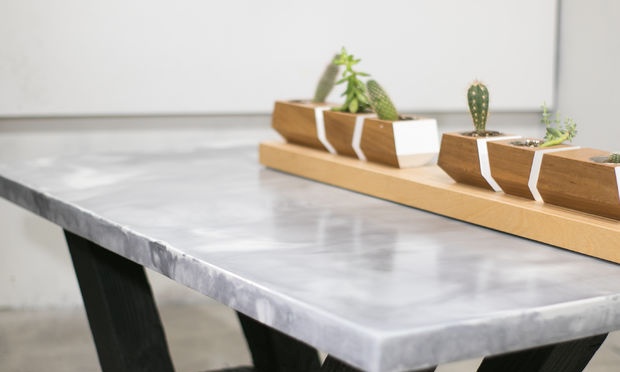
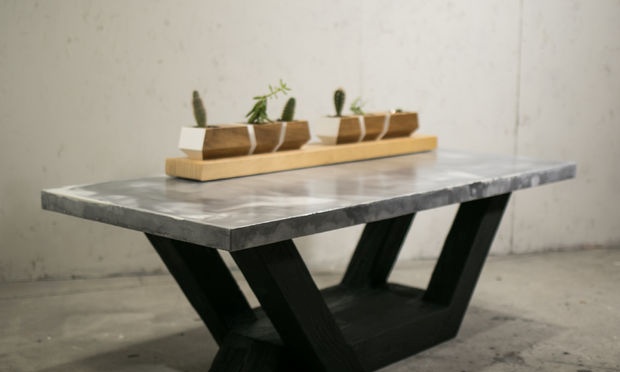
I made a coffee table out of concrete that looks like marble (at least to me). The tabletop is made from a ready-mixed glass fiber reinforced concrete (glass concrete) and cast in a melamine mold. I divided the solution into parts, gave them different colors (from white to dark gray), poured everything into the mold and mixed it lightly with my hand to give the mixture a marbled appearance.
I applied an ancient Japanese technique called "Shou Sugi Ban" to the base. I used a modernized version of it and charred the surface of the wood with a propane torch. This treatment is a natural way to preserve wood. And after applying low-viscosity oil, for example, Danish, the surface will become resistant to wear. The technique works well on any type of wood with a large texture, such as Douglas fir, pine and cedar. I used inexpensive 10 x 10 cm Douglas Fir lumber that I purchased from a local warehouse store.
Materials
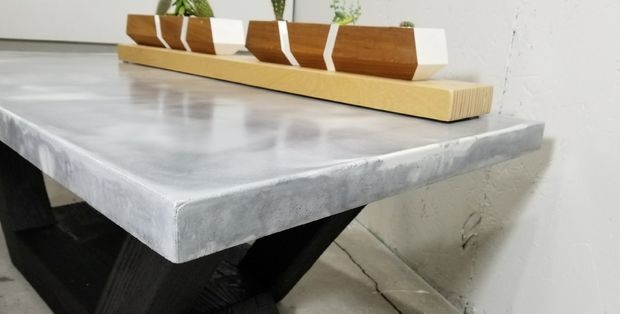
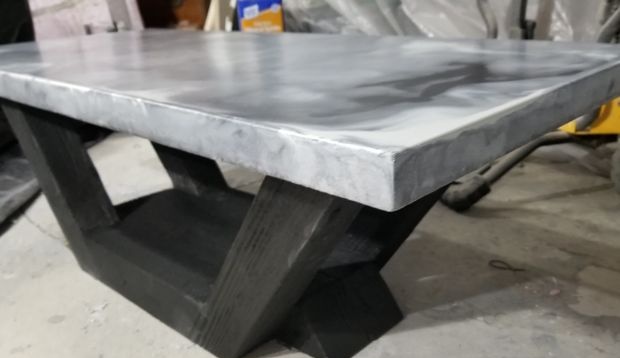
TREE:
- - three beams of Douglas fir, cedar or pine 10 x 10 cm and 2.5 m long;
- - dowel with a diameter of 20 mm;
- - 120 x 250 cm melamine sheet for making concrete molds.
CONCRETE (GLASS CONCRETE) MIXTURES:
- - two bags of mixture for the glass concrete base;
- - 0.68 kg package of alkali-resistant fiber glass;
- - cake decorating tool for smoothing edges;
- - construction mixer;
- - impregnation for concrete of your choice;
- - absolutely black silicone sealant;
- - wax-based polishing mixture;
- - paint for concrete.
MORE WHAT YOU NEED:
- - propane burner;
- - Danish oil;
- - respirator;
- - diamond-coated grinding wheel (for processing the bottom of the table);
- - a set of wood drills;
- - level;
- - jig for drilling;
- - casing for an angle grinder with dust extraction.
TOOLS USED IN MANUFACTURING:
- - angle grinder;
- - 18-volt cordless miter saw;
- - a set of 18-volt cordless screwdrivers;
- - sawing machine with a cutting width of 82 cm;
- - hand saw;
- - Miter saw.
We make a wooden base from 10 x 10 cm timber.
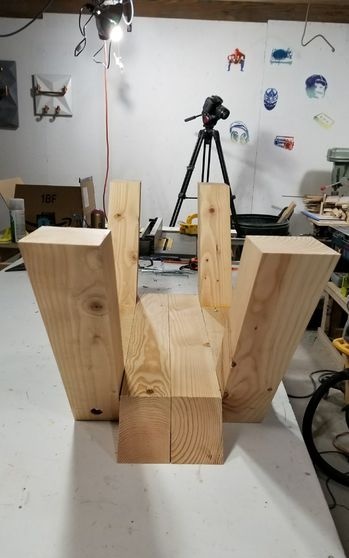
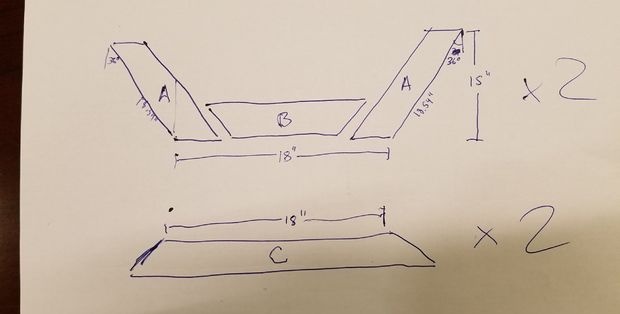
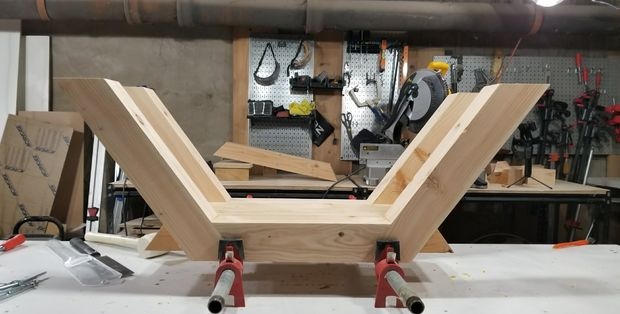
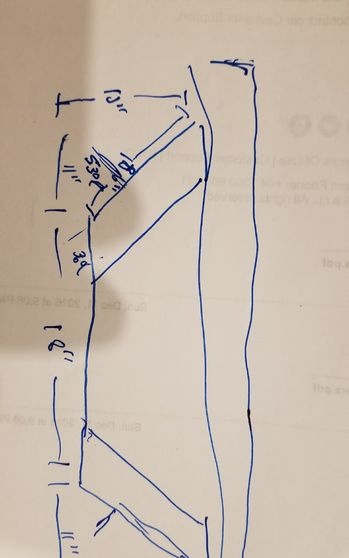
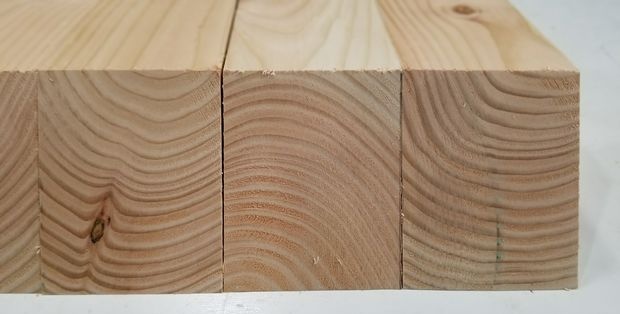
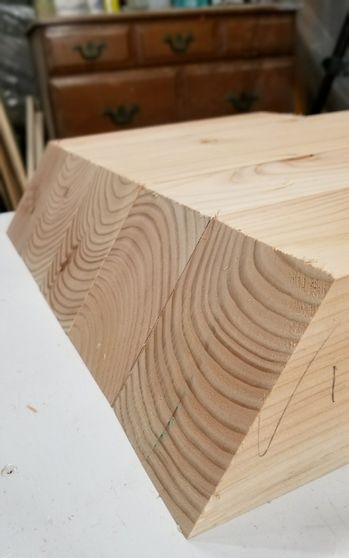
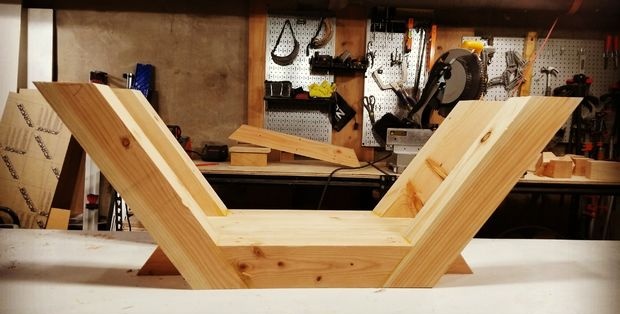
The base is made from 8 pieces of 10 x 10 cm timber. I used only Douglas fir. I processed all the pieces of timber with a plane to get the material to be absolutely the same size. You can make their width at your own discretion, but you can also use standard 10 x 10 bars, just try to choose smooth ones. For the base you will need 3 beams, each 2.5 m long.
Here are the eight elements (shown in the image):
- 4 legs (A);
- 2 external ties (B) - each located between two side legs;
- 2 internal ties (C).
All corners will be cut at 36 degrees.However, I would recommend cutting all the timbers a little longer first (say 10cm or more than needed) and then setting the miter saw to 36 degrees to do the rest of the work.
First cut off 4 legs (A). In order not to do trigonometry and get their exact length, I recommend cutting the beam at an angle of 36 degrees, then attaching the sawn part to the table surface, measuring 40 cm perpendicular to the table surface upwards (or the height you need), making a mark on the beam and in this place cut it at a 36 degree angle. Then we cut the remaining legs according to the size of the first one.
Next, cut the two outer zip ties (B). To do this, I placed two side legs and supported them with scraps of timber that remained after sawing them off so that they would stand. Then, I spread them in different directions to achieve the required distance between their tops (for me it was 110 cm). Next, I measured the distance between the lower edges of the legs, so I got a shorter length (for the lower part) of the outer struts (B). Then I cut the timber at an angle of 36 degrees in the marked places.
Now we cut off the two internal spacers. To do this, you need to attach the two side legs and the outer brace together (again, scraps will help with this). Place a block of wood next to it for the internal spacer and mark where you want to cut at an angle. All that remains is to work with the miter saw.
After cutting all 8 pieces, I will glue them together. Ideally, using clamps, you need to create a mechanism that would fix the internal angle between each leg and the external spacer at 144 degrees. However, I coated the parts with glue and, using scraps of timber, arranged the parts of the structure by hand.I secured everything with screws until the glue dried.
After the glue dried, I secured the structure with 15 cm wood grouse. They fixed the legs with internal struts. First, I drilled a shallow hole with a diameter of 20 mm so that the head was hidden inside, then a 6 mm preliminary hole and drove the capercaillie into it.
Having hammered a dowel into the holes, I hid the heads of the capercaillie.
After that, I used a belt sander to process the spacer elements to smooth out all the irregularities between them, and ground off the protruding remains of the dowels. Then it was time for firing.
Treating wood with fire
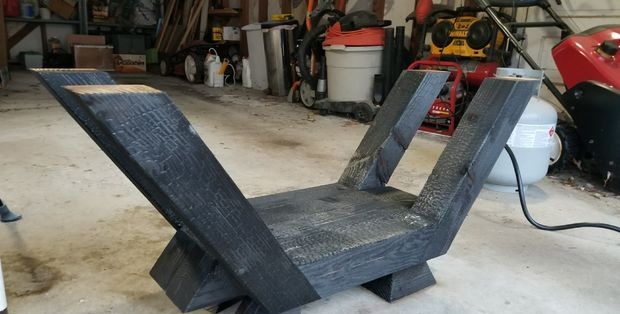
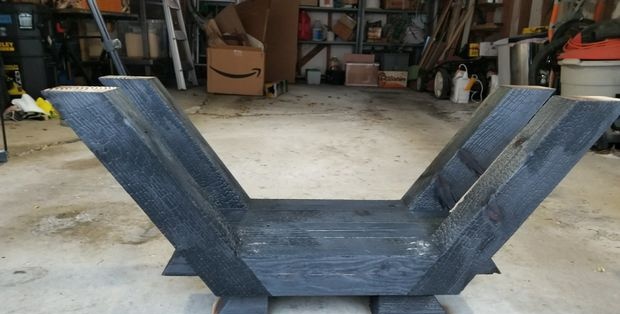
Watch the video on fire treatment
This part of the work leaves a positive impression. Prepare the gas burner according to its instructions. The process itself is quite safe, but it is better to have a fire extinguisher nearby. Just in case.
It's hard to overdo it here. Point the torch nozzle at the wood. The hottest part of the flame (the blue end) should lightly touch the wood surface. The tree turns brown and then turns black. When this part of the job is done, turn off the burner and wet the wood surfaces with water (I used a spray bottle). After this, using a brush, you need to lightly remove the burnt, ashen-colored parts.
Once the wood has cooled, apply polishing oil to it. I used Danish oil because it penetrates and hardens into the wood. This makes the charred “alligator skin” on the wood more durable and resistant to wear and tear. You will need a large amount of oil because this technique thoroughly dries out the wood and opens its pores for absorption. I gave it three coats and then had to do it again.
Make a mold for pouring concrete from melamine
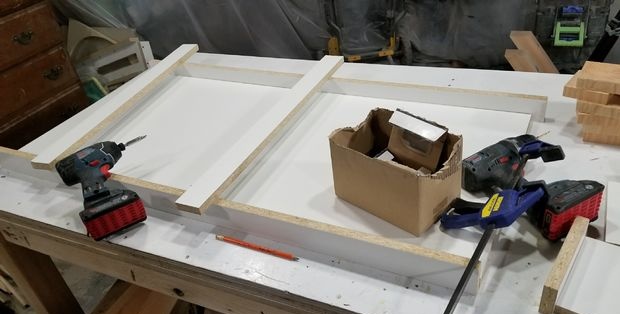
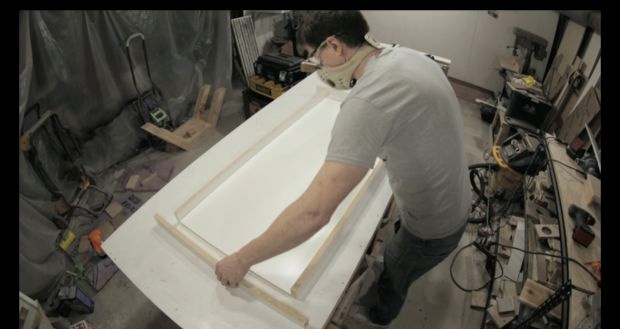
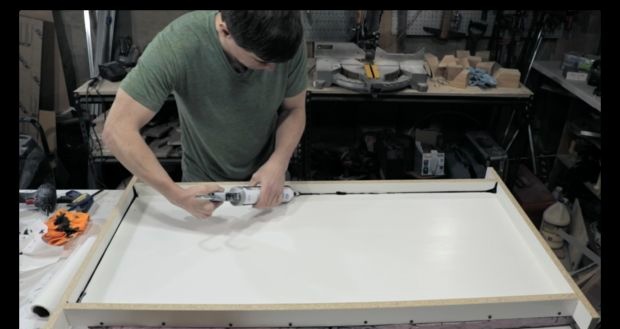
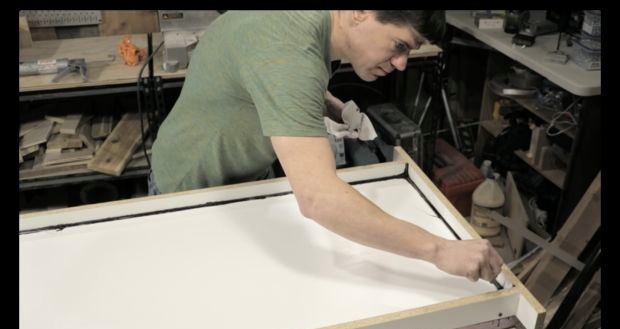
This is a mold, so the tabletop will be cast with the top down.
To make the shape you gently do the following:
a) Cut strips of melamine for the sides of the mold to the height of your table top + 2 cm. In my case, the table top was 4 cm high, so I cut the strips 6 cm wide. This is easier to do on a sawing machine, but you can use a miter saw if you will do everything consistently and accurately. Cut all the strips at the same time so they are the same width. Then we cut the strips to length. Each should be a few centimeters longer than the base. With this protruding part, the side strip will be easier to remove after the concrete has hardened.
b) Cut the base of the melanin mold to the size of the tabletop. In my case it was 120 x 55 cm.
c) Make preliminary holes in the sides, then screw them to the base. I used 30mm self-tapping screws for this.
d) Coat the inside of your mold with the wax mixture.
e) Apply silicone sealant to the internal seams and use a cake decorating tool (in the form of a small ball on a stick) to even them out. After the sealant has dried, you need to remove its excess.
IMPORTANT POINT I MISSED: You will need blocks to hold the foam inserts in the solution. They can be attached to the sides of the mold at the last stage of pouring the solution.
Cut foam inserts into concrete
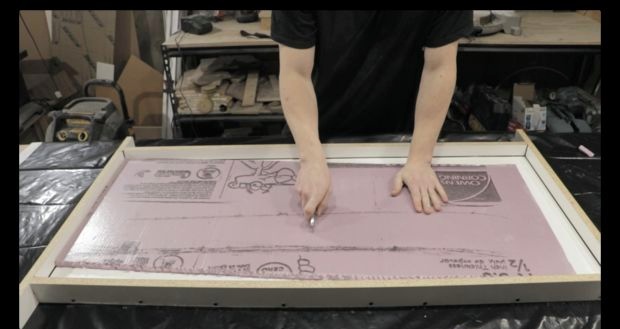
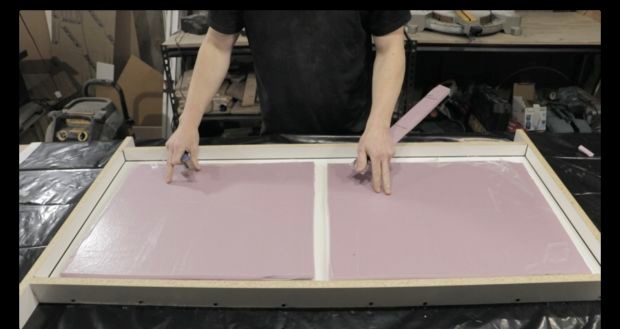
You need to cut foam inserts from 15mm thick sheet that will be dipped into the solution. In these places the tabletop will be 2.5 cm thick (unlike the edges, where the thickness will be 4 cm).Using a knife, we cut out two foam plastic plates of the required sizes so that they are placed 7-10 cm from each edge of the tabletop. The plate can only be cut, after which it can easily be broken by hand. If you need precision, you can use a miter saw or cut the inserts on a sawing machine.
Mix and pour the solution into the mold
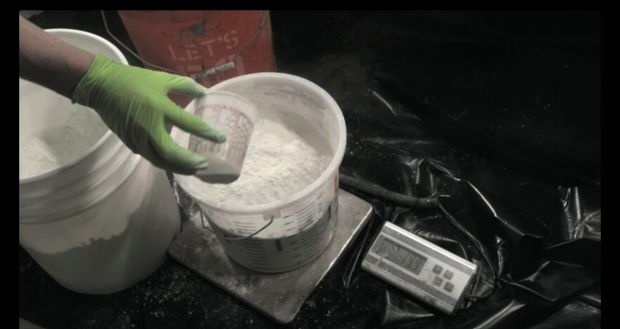
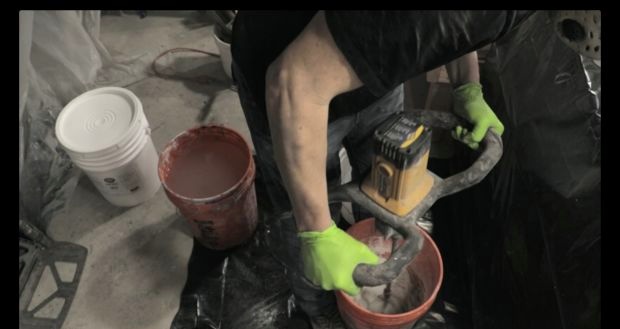
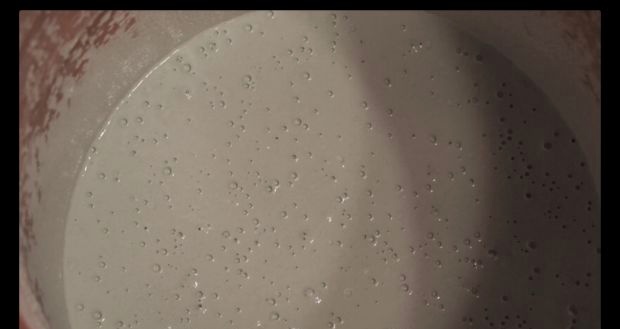
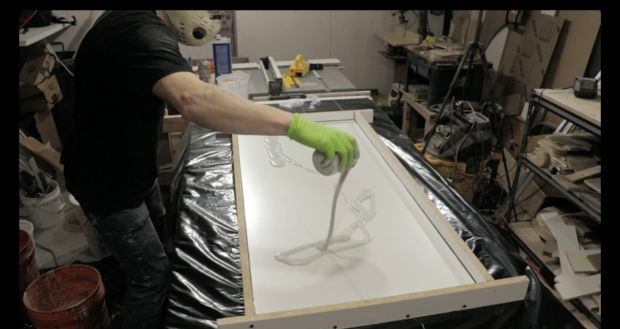
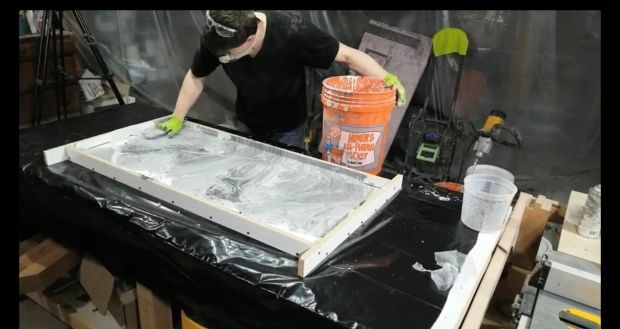
In my project, I used a ready-made glass concrete mixture to which you only need to add water. Add water according to instructions. Estimate how much solution you will need.
I ended up with almost 45 kg of dry mixture. I separated about 10kg for the cladding (without fibreglass) and used the remaining 35kg for the base (with fibreglass). For 35 kg of mixture I used 0.7 kg of fiberglass.
When preparing the facing mortar (and for the base), slowly add the mixture to the water. For example, add one third, stir, another third, etc. You can add a little more water (but not too much) if you want to make the solution more fluid. It should pour out like whipped batter.
To achieve the marbled look, I selected three small buckets of mortar. I added a lot of paint to one, after which its color became dark gray (almost black). I poured a small amount of dye into the rest of the lining solution in the main bucket, and stirred it only a little so that the color was uneven. Then I poured all three color options of the solution into the mold one by one and stirred with my hand until the entire mixture completely covered the bottom with a thin (about 5 mm) layer. The poured facing part should stand for 30 to 60 minutes (depending on the hardening time), after which, when touched, it should seem slightly damp, but quite durable.When pouring mortar for the bottom of the countertop, the facing should not be damaged.
PLEASE NOTE: glass concrete mortar should not be subjected to vibration.
Prepare the solution for the base of the tabletop in a similar way, but after it is ready, add fiberglass to it. Adding fiberglass should be done in parts, for example, a third per mixing. If the solution is too thick, you can add a little water. Pour it into the mold. You can help it spread into all corners with your hand. Again, vibrations are not needed. If the solution is made more fluid, it will distribute itself evenly throughout the form. First, pour in part of the solution without dye (for example, white), then add paint to the rest and mix, leaving it uneven. At this stage, we immerse the foam inserts and secure them inside the solution using bars screwed to the sides of the mold. Then pour in the rest of the solution until the mold is filled.
Sanding the bottom of the mold
Hardening should last at least 24 hours (36 at temperatures below 20 ºC). If the solution has risen above the foam inserts, the excess can be removed with an angle grinder fitted with a diamond-coated disc. Then remove the foam inserts. At this stage it is important not to disassemble the mold, because when sanding it is convenient to align the bottom with its sides.
Removal of mold elements, grinding and impregnation
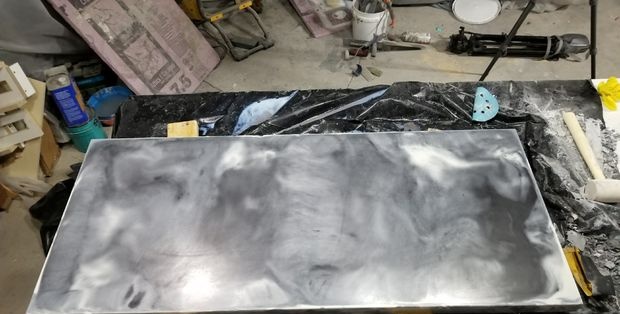
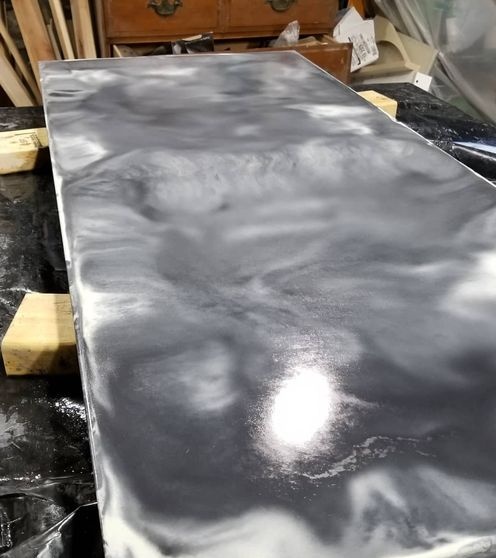
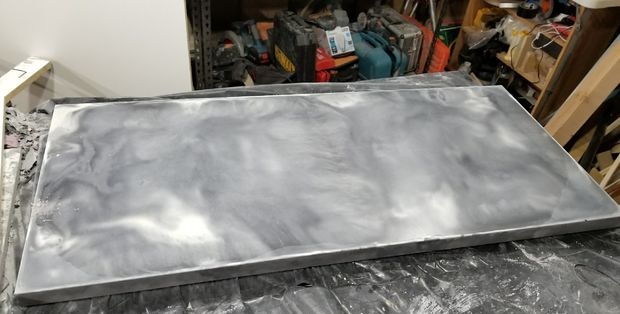

Once all the edges of the bottom of the table top are aligned, it's time to take the mold apart. We unscrew all the screws and separate all its parts.
If the sides do not come off very well, you can lightly tap them with a rubber hammer. If you turn the tabletop over, it will be easier to separate the bottom of the mold (now the top).To do this, you can use a plastic spatula (but not a metal one, so as not to leave scratches). If the base of the mold is strongly adhered to the concrete, then most likely the vacuum is preventing release. In this case, a compressor gun will help, the end of which must be inserted between the plastic and concrete. This will break the seal created by the vacuum and the plastic will come off easily.
Then we wet the entire concrete surface of the table with water and sand it by hand with P400 sandpaper. When you feel that the surface has become smooth, sanding is enough.
After this, apply impregnation to the concrete. This can be done according to the instructions.
We place the tabletop on a wooden base - and that’s it!
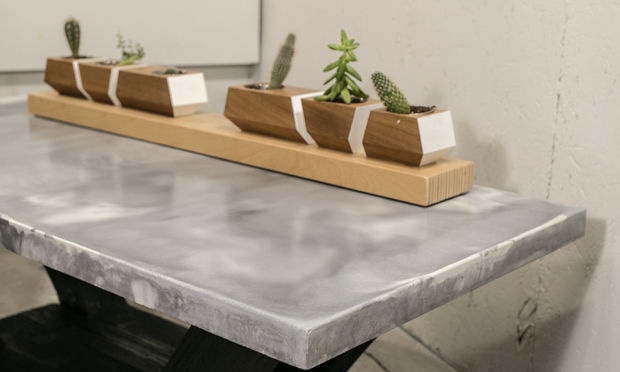
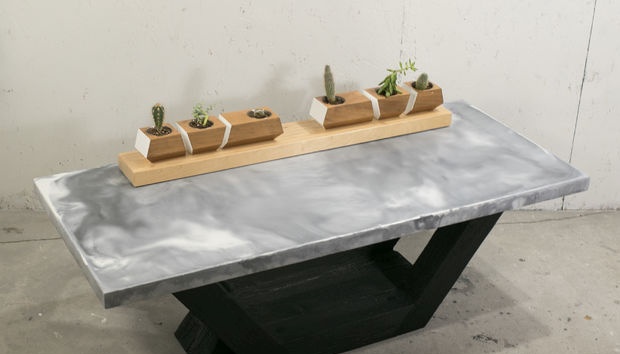
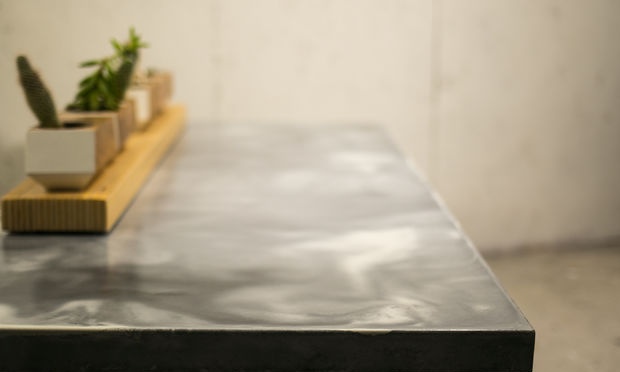
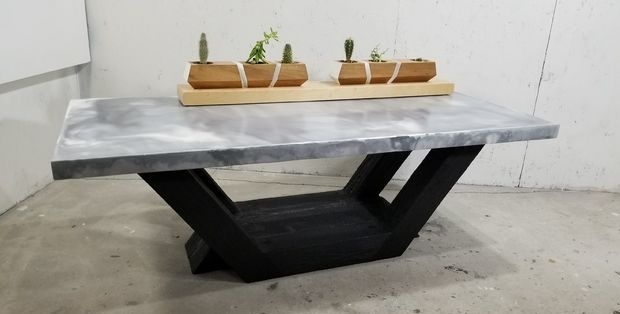
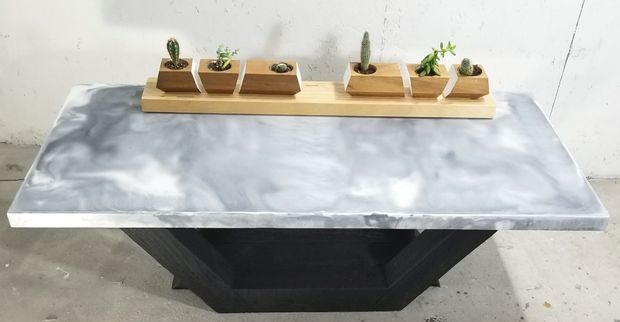

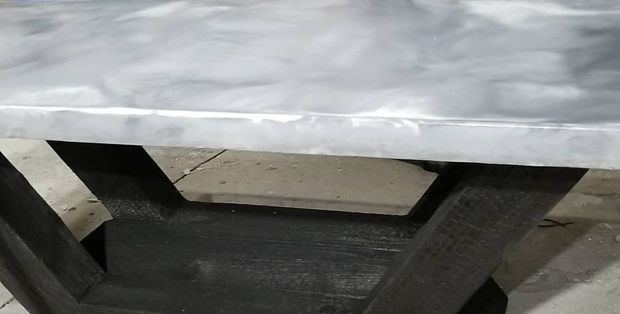
Lay the tabletop on top of the wood base, leveling it so that it lies perfectly in the center. Carefully lift the sides of the tabletop one by one to apply adhesive to the surfaces of the legs. Before the glue dries, make sure the tabletop is perfectly level.
Watch the video on making a table
Original article in English
Similar master classes
Particularly interesting
Comments (0)